机械设计制造及其自动化专业自动生产线PLC自动送料站控制毕业论文外文文献翻译及原文
机械设计制造及自动化中英文对照外文翻译文献
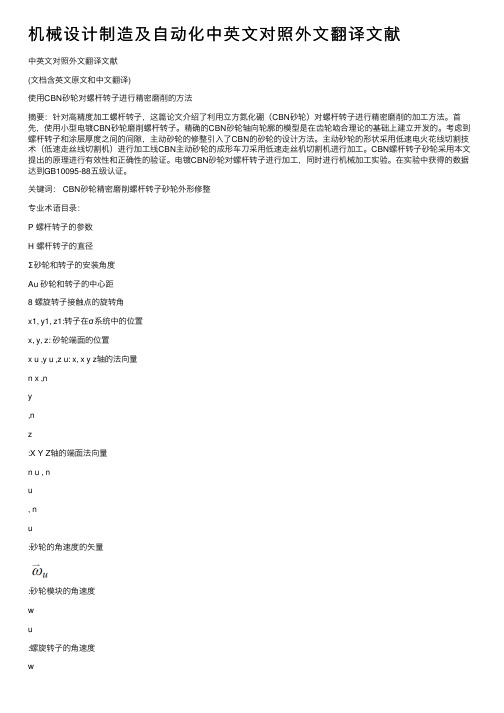
机械设计制造及⾃动化中英⽂对照外⽂翻译⽂献中英⽂对照外⽂翻译⽂献(⽂档含英⽂原⽂和中⽂翻译)使⽤CBN砂轮对螺杆转⼦进⾏精密磨削的⽅法摘要:针对⾼精度加⼯螺杆转⼦,这篇论⽂介绍了利⽤⽴⽅氮化硼(CBN砂轮)对螺杆转⼦进⾏精密磨削的加⼯⽅法。
⾸先,使⽤⼩型电镀CBN砂轮磨削螺杆转⼦。
精确的CBN砂轮轴向轮廓的模型是在齿轮啮合理论的基础上建⽴开发的。
考虑到螺杆转⼦和涂层厚度之间的间隙,主动砂轮的修整引⼊了CBN的砂轮的设计⽅法。
主动砂轮的形状采⽤低速电⽕花线切割技术(低速⾛丝线切割机)进⾏加⼯线CBN主动砂轮的成形车⼑采⽤低速⾛丝机切割机进⾏加⼯。
CBN螺杆转⼦砂轮采⽤本⽂提出的原理进⾏有效性和正确性的验证。
电镀CBN砂轮对螺杆转⼦进⾏加⼯,同时进⾏机械加⼯实验。
在实验中获得的数据达到GB10095-88五级认证。
关键词: CBN砂轮精密磨削螺杆转⼦砂轮外形修整专业术语⽬录:P 螺杆转⼦的参数H 螺杆转⼦的直径Σ砂轮和转⼦的安装⾓度Au 砂轮和转⼦的中⼼距8 螺旋转⼦接触点的旋转⾓x1, y1, z1:转⼦在σ系统中的位置x, y, z: 砂轮端⾯的位置x u ,y u ,z u: x, x y z轴的法向量n x ,ny,nz:X Y Z轴的端⾯法向量n u , nu, nu:砂轮的⾓速度的⽮量:砂轮模块的⾓速度wu:螺旋转⼦的⾓速度w1螺旋转⼦模块的⾓速度转⼦接触点的⾓速度转⼦表⾯接触点的初始速度砂轮表⾯接触点的⾓速度砂轮表⾯接触点的初始速度l砂轮的理论半径砂轮轴的理想位置砂轮表⾯的修改半径砂轮轴的修改位置砂轮表⾯的法向量1.引⾔螺旋转⼦是螺杆压缩机、螺钉、碎纸机以及螺杆泵的关键部分。
转⼦的加⼯精度决定了机械性能。
⼀般来说,铣⼑⽤于加⼯螺旋转⼦。
许多研究者,如肖等⼈[ 1 ]和姚等⼈[ 2 ],对⽤铣⼑加⼯螺旋转⼦做了⼤量的⼯作。
该⽅法可以提⾼加⼯效率。
然⽽,加⼯精度低和表⾯粗糙度不⾼是其主要缺点。
自动化制造系统与PLC论文中英文资料外文翻译文献

中英文资料外文翻译文献外文原文Automating Manufacturing Systems with PLCs2.1 INTRODUCTIONControl engineering has evolved over time. In the past humans were the main method for controlling a system. More recently electricity has been used for control and early electrical control was based on relays. These relays allow power to be switched on and off without a mechanical switch. It is common to use relays to make simple logical control decisions. The development of low cost computer has brought the most recent revolution,the Programmable Logic Controller (PLC). The advent of the PLC began in the1970s, and has become the most common choice for manufacturing controls.PLCs have been gaining popularity on the factory floor and will probably remain predominant for some time to come. Most of this is because of the advantages they offer. • Cost effective for controlling complex systems.• Flexible and can be reapplied to control other systems quickly and easily.• Computational abilities allow more sophisticated control.• Tr ouble shooting aids make programming easier and reduce downtime.• Reliable components make these likely to operate for years before failure.2.1.1 Ladder logicLadder logic is the main programming method used for PLCs. As mentioned before, ladder logic has been developed to mimic relay logic. logic diagrams was a strategic one. By selecting ladder logic as the main programming method, the amount of retraining needed forengineers and trades people was greatly reduced.Modern control systems still include relays, but these are rarely used for logic. A relay is a simple device that uses a magnetic field to control a switch, as pictured in Figure 2.1. When a voltage is applied to the input coil, the resulting current creates a magnetic field. The magnetic field pulls a metal switch (or reed) towards it and the contacts touch, closing the switch. The contact that closes when the coil is energized is called normally open. The normally closed contacts touch when the input coil is not energized. Relays are normally drawn in schematic form using a circle to represent the input coil. The output contacts are shown with two parallel lines. Normally open contacts are shown as two lines, and will be open (non-conducting) when the input is not energized. Normally closed contacts are shown with two lines with a diagonal line through them. When the input coil is not energized the normally closed contacts will be closed (conducting).Figure 2.1 Simple Relay Layouts and SchematicsRelays are used to let one power source close a switch for another (often high current) power source, while keeping them isolated. An example of a relay in a simple control application is shown in Figure 2.2. In this system the first relay on the left is used as normally closed, and will allow current to flow until a voltage is applied to the input A. The second relay is normally open and will not allow current to flow until a voltage is applied to the input B. If current is flowing through the first two relays then current will flow through the coil in the third relay, and close the switch for output C. This circuit would normally be drawn in the ladder logic form. This can be read logically as C will be on if A is off and B is on.Figure 2.2 A Simple Relay ControllerThe example in Figure 2.2 does not show the entire control system, but only the logic. When we consider a PLC there are inputs, outputs, and the logic. Figure 2.3 shows a more complete representation of the PLC. Here there are two inputs from push buttons.We can imagine the inputs as activating 24V DC relay coils in the PLC. This in turn drives an output relay that switches 115V AC, that will turn on a light. Note, in actual PLCs inputs are never relays, but outputs are often relays. The ladder logic in the PLC is actually a computer program that the user can enter and change. Notice that both of the input push buttons are normally open, but the ladder logic inside the PLC has one normally open contact, and one normally closed contact. Do not think that the ladder logic in the PLC need so match the inputs or outputs. Many beginners will get caught trying to make the ladder logic match the input types.Figure 2.3 A PLC Illustrated With RelaysMany relays also have multiple outputs (throws) and this allows an output relay to also be an input simultaneously. The circuit shown in Figure 1.4 is an example of this, it is called a seal in circuit. In this circuit the current can flow through either branch of the circuit, through the contacts labelled A or B. The input B will only be on when the output B is on. If B is off, and A is energized, then B will turn on. If B turns on then the input B will turn on, and keep output B on even if input A goes off. After B is turned on the output B will not turn off.Figure 2.4 A Seal-in Circuit2.1.2 ProgrammingThe first PLCs were programmed with a technique that was based on relay logic wiring schematics. This eliminated the need to teach the electricians, technicians and engineers how to program a computer - but, this method has stuck and it is the most common technique for programming PLCs today. An example of ladder logic can be seen in Figure 2.5. To interpret this diagram imagine that the power is on the vertical line on the left hand side, we call this the hot rail. On the right hand side is the neutral rail. In the figure there are two rungs, and on each rung there are combinations of inputs (two vertical lines) and outputs (circles). If the inputs are opened or closed in the right combination the power can flow from the hot rail, through the inputs, to power the outputs, and finally to the neutral rail. An input can come from a sensor, switch, or any other type of sensor. An output will be some device outside the PLC that is switched on or off, such as lights or motors. In the top rung the contacts are normally open and normally closed. Which means if input A is on and input B is off, then power will flow through the output and activate it. Any other combination of input values will result in the output X being off.Figure 2.5 A Simple Ladder Logic DiagramThe second rung of Figure 2.5 is more complex, there are actually multiple combinations of inputs that will result in the output Y turning on. On the left most part of the rung, power could flow through the top if C is off and D is on. Power could also (and simultaneously) flow through the bottom if both E and F are true. This would get power half way across the rung, and then if G or H is true the power will be delivered to output Y. In later chapters we will examine how to interpret and construct these diagrams.There are other methods for programming PLCs. One of the earliest techniques involved mnemonic instructions. These instructions can be derived directly from the ladderlogic diagrams and entered into the PLC through a simple programming terminal. An example of mnemonics is shown in Figure 2.6. In this example the instructions are read one line at a time from top to bottom. The first line 00000 has the instruction LDN (input load and not) for input A. . This will examine the input to the PLC and if it is off it will remember a 1 (or true), if it is on it will remember a 0 (or false). The next line uses an LD (input load) statement to look at the input. If the input is off it remembers a 0, if the input is on it remembers a 1 (note: this is the reverse of the LD). The AND statement recalls the last two numbers remembered and if the are both true the result is a 1, otherwise the result is a 0. This result now replaces the two numbers that were recalled, and there is only one number remembered. The process is repeated for lines 00003 and 00004, but when these are done there are now three numbers remembered. The oldest number is from the AND, the newer numbers are from the two LD instructions. The AND in line 00005 combines the results from the last LD instructions and now there are two numbers remembered. The OR instruction takes the two numbers now remaining and if either one is a 1 the result is a 1, otherwise the result is a 0. This result replaces the two numbers, and there is now a single number there. The last instruction is the ST (store output) that will look at the last value stored and if it is 1, the output will be turned on, if it is 0 the output will be turned off.Figure 2.6 An Example of a Mnemonic Program and Equivalent Ladder LogicThe ladder logic program in Figure 2.6, is equivalent to the mnemonic program. Even ifyou have programmed a PLC with ladder logic, it will be converted to mnemonic form before being used by the PLC. In the past mnemonic programming was the most common, but now it is uncommon for users to even see mnemonic programs.Sequential Function Charts (SFCs) have been developed to accommodate the programming of more advanced systems. These are similar to flowcharts, but much more powerful. The example seen in Figure 2.7 is doing two different things. To read the chart, start at the top where is says start. Below this there is the double horizontal line that says follow both paths. As a result the PLC will start to follow the branch on the left and right hand sides separately and simultaneously. On the left there are two functions the first one is the power up function. This function will run until it decides it is done, and the power down function will come after. On the right hand side is the flash function, this will run until it is done. These functions look unexplained, but each function, such as power up will be a small ladder logic program. This method is much different from flowcharts because it does not have to follow a single path through the flowchart..Figure 2.7 An Example of a Sequential Function CharStructured Text programming has been developed as a more modern programming language. It is quite similar to languages such as BASIC. A simple example is shown in Figure 2.8. This example uses a PLC memory location i. This memory location is for an integer, as will be explained later in the book. The first line of the program sets the value to 0. The next line begins a loop, and will be where the loop returns to. The next line recalls thevalue in location i, adds 1 to it and returns it to the same location. The next line checks to see if the loop should quit. If i is greater than or equal to 10, then the loop will quit, otherwise the computer will go back up to the REPEAT statement continue from there. Each time the program goes through this loop i will increase by 1 until the value reaches 10.Figure 2.8 An Example of a Structured Text Program2.1.3 PLC ConnectionsWhen a process is controlled by a PLC it uses inputs from sensors to make decisions and update outputs to drive actuators, as shown in Figure 2.9. The process is a real process that will change over time. Actuators will drive the system to new states (or modes of operation). This means that the controller is limited by the sensors available, if an input is not available, the controller will have no way to detect a condition.Figure 2.9 The Separation of Controller and ProcessThe control loop is a continuous cycle of the PLC reading inputs, solving the ladder logic, and then changing the outputs. Like any computer this does not happen instantly. Figure 2.10 shows the basic operation cycle of a PLC. When power is turned on initially the PLC does a quick sanity check to ensure that the hardware is working properly.If there is a problem the PLC will halt and indicate there is an error. For example, if the PLC power is dropping andabout to go off this will result in one type of fault. If the PLC passes the sanity check it will then scan (read) all the inputs. After the inputs values are stored in memory the ladder logic will be scanned (solved) using the stored values not the current values. This is done to prevent logic problems when inputs change during the ladder logic scan. When the ladder logic scan is complete the outputs will be scanned (the output values will be changed). After this the system goes back to do a sanity check, and the loop continues indefinitely. Unlike normal computers, the entire program will be run every scan. Typical times for each of the stages is in the order of milliseconds.Figure 2.10 The Scan Cycle of a PLC2.1.4 Ladder Logic InputsPLC inputs are easily represented in ladder logic. In Figure 2.11 there are three types of inputs shown. The first two are normally open and normally closed inputs, discussed previously. The IIT (Immediate InpuT) function allows inputs to be read after the input scan, while the ladder logic is being scanned. This allows ladder logic to examine input values more often than once every cycle.Figure 2.11 Ladder Logic Inputs2.1.5 Ladder Logic OutputsIn ladder logic there are multiple types of outputs, but these are not consistently available on all PLCs. Some of the outputs will be externally connected to devices outside the PLC, but it is also possible to use internal memory locations in the PLC. Six types of outputs are shown in Figure 2.12. The first is a normal output, when energized the output will turn on, and energize an output. The circle with a diagonal line through is a normally on output. When energized the output will turn off. This type of output is not available on all PLC types. When initially energized the OSR (One Shot Relay) instruction will turn on for one scan, but then be off for all scans after, until it is turned off. The L (latch) and U (unlatch) instructions can be used to lock outputs on. When an L output is energized the output will turn on indefinitely, even when the output coil is deenergized. The output can only be turned off using a U output. The last instruction is the IOT (Immediate OutpuT) The last instruction is the IOT (Immediate OutpuT)that will allow outputs to be updated without having to wait for the ladder logic scan to be completed.3.1 INPUTS AND OUTPUTSInputs to, and outputs from, a PLC are necessary to monitor and control a process. Both inputs and outputs can be categorized into two basic types: logical or continuous. Considerthe example of a light bulb. If it can only be turned on or off, it is logical control. If the light can be dimmed to different levels, it is continuous. Continuous values seem more intuitive, but logical values are preferred because they allow more certainty, and simplify control. As a result most controls applications (and PLCs) use logical inputs and outputs for most applications. Hence, we will discuss logical I/O and leave continuous I/O for later.Outputs to actuators allow a PLC to cause something to happen in a process. A short list of popular actuators is given below in order of relative popularity.Solenoid Valves - logical outputs that can switch a hydraulic or pneumatic flow. Lights - logical outputs that can often be powered directly from PLC output boards.Motor Starters - motors often draw a large amount of current when started, so they require motor starters, which are basically large relays.Servo Motors - a continuous output from the PLC can command a variable speed or position.Outputs from PLCs are often relays, but they can also be solid state electronics such as transistors for DC outputs or Triacs for AC outputs. Continuous outputs require special output cards with digital to analog converters.Inputs come from sensors that translate physical phenomena into electrical signals. Typical examples of sensors are listed below in relative order of popularity.Proximity Switches - use inductance, capacitance or light to detect an object logically. Switches - mechanical mechanisms will open or close electrical contacts for a logical signal. Potentiometer - measures angular positions continuously, using resistance.LVDT (linear variable differential transformer) - measures linear displacement continuously using magnetic coupling.Inputs for a PLC come in a few basic varieties, the simplest are AC and DC inputs. Sourcing and sinking inputs are also popular. This output method dictates that a device does not supply any power. Instead, the device only switches current on or off, like a simple switch. Sinking - When active the output allows current to flow to a common ground. This is best selected when different voltages are supplied. Sourcing - When active, current flows from asupply, through the output device and to ground. This method is best used when all devices use a single supply voltage. This is also referred to as NPN (sinking) and PNP (sourcing). PNP is more popular. This will be covered in detail in the chapter on sensors.3.1.1 InputsIn smaller PLCs the inputs are normally built in and are specified when purchasing the PLC. For larger PLCs the inputs are purchased as modules, or cards, with 8 or 16 inputs of the same type on each card. For discussion purposes we will discuss all inputs as if they have been purchased as cards. The list below shows typical ranges for input voltages, and is roughly in order of popularity. PLC input cards rarely supply power, this means that an external power supply is needed to supply power for the inputs and sensors. The example in Figure 3.1 shows how to connect an AC input card.Figure 3.1 An AC Input Card and Ladder LogicIn the example there are two inputs, one is a normally open push button, and the second is a temperature switch, or thermal relay. (NOTE: These symbols are standard and will be discussed later in this chapter.) Both of the switches are powered by the positive/ hot output ofthe 24Vac power supply - this is like the positive terminal on a DC supply. Power is supplied to the left side of both of the switches. When the switches are open there is no voltage passed to the input card. If either of the switches are closed power will be supplied to the input card. In this case inputs 1 and 3 are used - notice that the inputs start at 0. The input card compares these voltages to the common. If the input voltage is within a given tolerance range the inputs will switch on. Ladder logic is shown in the figure for the inputs. Here it uses Allen Bradley notation for PLC-5 racks. At the top is the location of the input card I:013 which indicates that the card is an Input card in rack 01 in slot 3. The input number on the card is shown below the contact as 01 and 03.Many beginners become confused about where connections are needed in the circuit above. The key word to remember is circuit, which means that there is a full loop that the voltage must be able to follow. In Figure 3.1 we can start following the circuit (loop) at the power supply. The path goes through the switches, through the input card, and back to the power supply where it flows back through to the start. In a full PLC implementation there will be many circuits that must each be complete. A second important concept is the common. Here the neutral on the power supply is the common, or reference voltage. In effect we have chosen this to be our 0V reference, and all other voltages are measured relative to it. If we had a second power supply, we would also need to connect the neutral so that both neutrals would be connected to the same common. Often common and ground will be confused. The common is a reference, or datum voltage that is used for 0V, but the ground is used to prevent shocks and damage to equipment. The ground is connected under a building to a metal pipe or grid in the ground. This is connected to the electrical system of a building, to the power outlets, where the metal cases of electrical equipment are connected. When power flows through the ground it is bad. Unfortunately many engineers, and manufacturers mix up ground and common. It is very common to find a power supply with the ground and common mislabeled.One final concept that tends to trap beginners is that each input card is isolated. This means that if you have connected a common to only one card, then the other cards are not connected. When this happens the other cards will not work properly. You must connect acommon for each of the output cards.3.1.2.Output ModulesAs with input modules, output modules rarely supply any power, but instead act as switches. External power supplies are connected to the output card and the card will switch the power on or off for each output. Typical output voltages are listed below, and roughly ordered by popularity.120 Vac24 Vdc12-48 Vac12-48 Vdc5Vdc (TTL)230 VacThese cards typically have 8 to 16 outputs of the same type and can be purchased with different current ratings. A common choice when purchasing output cards is relays, transistors or triacs. Relays are the most flexible output devices. They are capable of switching both AC and DC outputs. But, they are slower (about 10ms switching is typical), they are bulkier, they cost more, and they will wear out after millions of cycles. Relay outputs are often called dry contacts. Transistors are limited to DC outputs, and Triacs are limited to AC outputs. Transistor and triac outputs are called switched outputs. Dry contacts - a separate relay is dedicated to each output.This allows mixed voltages (AC or DC and voltage levels up to the maximum), as well as isolated outputs to protect other outputs and the PLC. Response times are often greater than 10ms. This method is the least sensitive to voltage variations and spikes. Switched outputs - a voltage is supplied to the PLC card, and the card switches it to different outputs using solid state circuitry (transistors, triacs, etc.) Triacs are well suited to AC devices requiring less than 1A. Transistor outputs use NPN or PNP transistors up to 1A typically. Their response time is well under 1ms.中文翻译自动化制造系统与PLC2.1介绍控制工程随着时间的推移在不断发展。
机械设计制造及自动化专业英语翻译
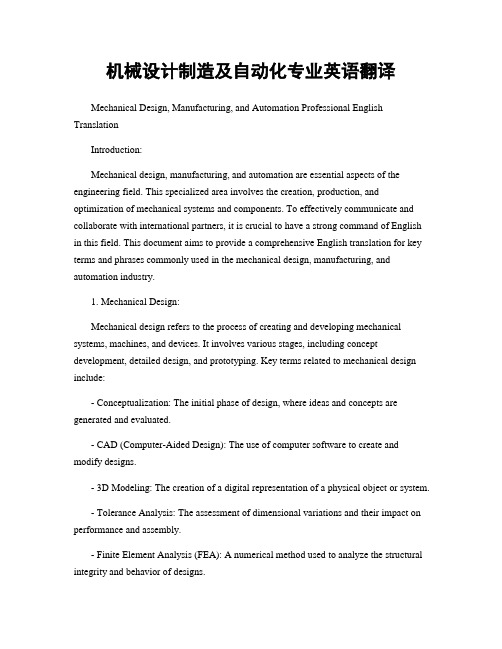
机械设计制造及自动化专业英语翻译Mechanical Design, Manufacturing, and Automation Professional English TranslationIntroduction:Mechanical design, manufacturing, and automation are essential aspects of the engineering field. This specialized area involves the creation, production, and optimization of mechanical systems and components. To effectively communicate and collaborate with international partners, it is crucial to have a strong command of English in this field. This document aims to provide a comprehensive English translation for key terms and phrases commonly used in the mechanical design, manufacturing, and automation industry.1. Mechanical Design:Mechanical design refers to the process of creating and developing mechanical systems, machines, and devices. It involves various stages, including concept development, detailed design, and prototyping. Key terms related to mechanical design include:- Conceptualization: The initial phase of design, where ideas and concepts are generated and evaluated.- CAD (Computer-Aided Design): The use of computer software to create and modify designs.- 3D Modeling: The creation of a digital representation of a physical object or system.- Tolerance Analysis: The assessment of dimensional variations and their impact on performance and assembly.- Finite Element Analysis (FEA): A numerical method used to analyze the structural integrity and behavior of designs.- Design Optimization: The process of improving designs to achieve desired performance, efficiency, or cost-effectiveness.2. Manufacturing:Manufacturing involves the production of goods through various processes, such as machining, casting, forging, and assembly. Key terms related to manufacturing include:- CNC (Computer Numerical Control): The automation of machine tools through the use of computers to control machining operations.- Machining: The process of shaping or altering materials through cutting, drilling, milling, or grinding.- Casting: The manufacturing process of pouring molten material into a mold to obtain a desired shape.- Forging: The process of shaping metal through the application of localized compressive forces.- Assembly: The process of joining individual components to create a final product.3. Automation:Automation refers to the use of technology and control systems to operate and control machinery and processes with minimal human intervention. Key terms related to automation include:- PLC (Programmable Logic Controller): A digital computer used to control industrial processes and machines.- Robotics: The design, construction, and operation of robots to perform tasks autonomously or with human assistance.- Sensors: Devices that detect and measure physical or chemical properties and convert them into signals for control systems.- HMI (Human-Machine Interface): The interface that allows humans to interact with machines or systems.- SCADA (Supervisory Control and Data Acquisition): A system used to monitor and control industrial processes remotely.Conclusion:The mechanical design, manufacturing, and automation industry requires a deep understanding of technical terms and concepts. This English translation provides a comprehensive overview of key terms and phrases in this field. By familiarizing yourself with these terms, you will be better equipped to communicate effectively and collaborate with international partners in the mechanical design, manufacturing, and automation industry.。
机械制造及自动化毕业设计---外语文献翻译

攀枝花学院本科毕业设计(论文)外文译文院(系):机电工程学院专业:机械设计制造及其自动化姓名:**************学号:ZJD02043外语文献翻译摘自: 《制造工程与技术(机加工)》(英文版)《Manufacturing Engineering and Technology—Machining》机械工业出版社2004年3月第1版页P560—564美s. 卡尔帕基安(Serope kalpakjian)s.r 施密德(Steven R.Schmid) 著原文:20.9 MACHINABILITYThe machinability of a material usually defined in terms of four factors:1、Surface finish and integrity of the machined part;2、Tool life obtained;3、Force and power requirements;4、Chip control.Thus, good machinability good surface finish and integrity, long tool life, and low force And power requirements. As for chip control, long and thin (stringy) cured chips, if not broken up, can severely interfere with the cutting operation by becoming entangled in the cutting zone.Because of the complex nature of cutting operations, it is difficult to establish relationships that quantitatively define the machinability of a material. In manufacturing plants, tool life and surface roughness are generally considered to be the most important factors in machinability. Although not used much any more, approximate machinability ratings are available in the example below.20.9.1 Machinability Of SteelsBecause steels are among the most important engineering materials (as noted in Chapter 5), their machinability has been studied extensively. The machinability of steels has been mainly improved by adding lead and sulfur to obtain so-calledfree-machining steels.Resulfurized and Rephosphorized steels. Sulfur in steels forms manganese sulfide inclusions (second-phase particles), which act as stress raisers in the primaryshear zone. As a result, the chips produced break up easily and are small; this improves machinability. The size, shape, distribution, and concentration of these inclusions significantly influence machinability. Elements such as tellurium and selenium, which are both chemically similar to sulfur, act as inclusion modifiers in resulfurized steels.Phosphorus in steels has two major effects. It strengthens the ferrite, causing increased hardness. Harder steels result in better chip formation and surface finish. Note that soft steels can be difficult to machine, with built-up edge formation and poor surface finish. The second effect is that increased hardness causes the formation of short chips instead of continuous stringy ones, thereby improving machinability.Leaded Steels. A high percentage of lead in steels solidifies at the tip of manganese sulfide inclusions. In non-resulfurized grades of steel, lead takes the form of dispersed fine particles. Lead is insoluble in iron, copper, and aluminum and their alloys. Because of its low shear strength, therefore, lead acts as a solid lubricant (Section 32.11) and is smeared over the tool-chip interface during cutting. This behavior has been verified by the presence of high concentrations of lead on thetool-side face of chips when machining leaded steels.When the temperature is sufficiently high-for instance, at high cutting speeds and feeds (Section 20.6)—the lead melts directly in front of the tool, acting as a liquid lubricant. In addition to this effect, lead lowers the shear stress in the primary shear zone, reducing cutting forces and power consumption. Lead can be used in every grade of steel, such as 10xx, 11xx, 12xx, 41xx, etc. Leaded steels are identified by the letter L between the second and third numerals (for example, 10L45). (Note that in stainless steels, similar use of the letter L means “low carbon,” a condition that improves their corrosion resistance.)However, because lead is a well-known toxin and a pollutant, there are serious environmental concerns about its use in steels (estimated at 4500 tons of lead consumption every year in the production of steels). Consequently, there is a continuing trend toward eliminating the use of lead in steels (lead-free steels). Bismuth and tin are now being investigated as possible substitutes for lead in steels.Calcium-Deoxidized Steels. An important development is calcium-deoxidized steels, in which oxide flakes of calcium silicates (CaSo) are formed. These flakes, in turn, reduce the strength of the secondary shear zone, decreasing tool-chip interfaceand wear. Temperature is correspondingly reduced. Consequently, these steels produce less crater wear, especially at high cutting speeds.Stainless Steels. Austenitic (300 series) steels are generally difficult to machine. Chatter can be s problem, necessitating machine tools with high stiffness. However, ferritic stainless steels (also 300 series) have good machinability. Martensitic (400 series) steels are abrasive, tend to form a built-up edge, and require tool materials with high hot hardness and crater-wear resistance. Precipitation-hardening stainless steels are strong and abrasive, requiring hard and abrasion-resistant tool materials.The Effects of Other Elements in Steels on Machinability. The presence of aluminum and silicon in steels is always harmful because these elements combine with oxygen to form aluminum oxide and silicates, which are hard and abrasive. These compounds increase tool wear and reduce machinability. It is essential to produce and use clean steels.Carbon and manganese have various effects on the machinability of steels, depending on their composition. Plain low-carbon steels (less than 0.15% C) can produce poor surface finish by forming a built-up edge. Cast steels are more abrasive, although their machinability is similar to that of wrought steels. Tool and die steels are very difficult to machine and usually require annealing prior to machining. Machinability of most steels is improved by cold working, which hardens the material and reduces the tendency for built-up edge formation.Other alloying elements, such as nickel, chromium, molybdenum, and vanadium, which improve the properties of steels, generally reduce machinability. The effect of boron is negligible. Gaseous elements such as hydrogen and nitrogen can have particularly detrimental effects on the properties of steel. Oxygen has been shown to have a strong effect on the aspect ratio of the manganese sulfide inclusions; the higher the oxygen content, the lower the aspect ratio and the higher the machinability.In selecting various elements to improve machinability, we should consider the possible detrimental effects of these elements on the properties and strength of the machined part in service. At elevated temperatures, for example, lead causes embrittlement of steels (liquid-metal embrittlement, hot shortness; see Section 1.4.3), although at room temperature it has no effect on mechanical properties.Sulfur can severely reduce the hot workability of steels, because of the formation of iron sulfide, unless sufficient manganese is present to prevent such formation. Atroom temperature, the mechanical properties of resulfurized steels depend on the orientation of the deformed manganese sulfide inclusions (anisotropy). Rephosphorized steels are significantly less ductile, and are produced solely to improve machinability.20.9.2 Machinability of Various Other MetalsAluminum is generally very easy to machine, although the softer grades tend to form a built-up edge, resulting in poor surface finish. High cutting speeds, high rake angles, and high relief angles are recommended. Wrought aluminum alloys with high silicon content and cast aluminum alloys may be abrasive; they require harder tool materials. Dimensional tolerance control may be a problem in machining aluminum, since it has a high thermal coefficient of expansion and a relatively low elastic modulus.Beryllium is similar to cast irons. Because it is more abrasive and toxic, though, it requires machining in a controlled environment.Cast gray irons are generally machinable but are. Free carbides in castings reduce their machinability and cause tool chipping or fracture, necessitating tools with high toughness. Nodular and malleable irons are machinable with hard tool materials.Cobalt-based alloys are abrasive and highly work-hardening. They require sharp, abrasion-resistant tool materials and low feeds and speeds.Wrought copper can be difficult to machine because of built-up edge formation, although cast copper alloys are easy to machine. Brasses are easy to machine, especially with the addition pf lead (leaded free-machining brass). Bronzes are more difficult to machine than brass.Magnesium is very easy to machine, with good surface finish and prolonged tool life. However care should be exercised because of its high rate of oxidation and the danger of fire (the element is pyrophoric).Molybdenum is ductile and work-hardening, so it can produce poor surface finish. Sharp tools are necessary.Nickel-based alloys are work-hardening, abrasive, and strong at high temperatures. Their machinability is similar to that of stainless steels.Tantalum is very work-hardening, ductile, and soft. It produces a poor surfacefinish; tool wear is high.Titanium and its alloys have poor thermal conductivity (indeed, the lowest of all metals), causing significant temperature rise and built-up edge; they can be difficult to machine.Tungsten is brittle, strong, and very abrasive, so its machinability is low,although it greatly improves at elevated temperatures.Zirconium has good machinability. It requires a coolant-type cutting fluid,however, because of the explosion and fire.20.9.3 Machinability of Various MaterialsGraphite is abrasive; it requires hard, abrasion-resistant, sharp tools.Thermoplastics generally have low thermal conductivity, low elastic modulus, and low softening temperature. Consequently, machining them requires tools with positive rake angles (to reduce cutting forces), large relief angles, small depths of cut and feed, relatively high speeds, andproper support of the workpiece. Tools should be sharp.External cooling of the cutting zone may be necessary to keep the chips from becoming “gummy” and sticking to the tools. Cooling can usually be achieved w ith a jet of air, vapor mist, or water-soluble oils. Residual stresses may develop during machining. To relieve these stresses, machined parts can be annealed for a period of time at temperatures ranging from C ︒80 to C ︒160 (F ︒175to F ︒315), and then cooled slowly and uniformly to room temperature.Thermosetting plastics are brittle and sensitive to thermal gradients duringcutting. Their machinability is generally similar to that of thermoplastics.Because of the fibers present, reinforced plastics are very abrasive and aredifficult to machine. Fiber tearing, pulling, and edge delamination are significant problems; they can lead to severe reduction in the load-carrying capacity of the component. Furthermore, machining of these materials requires careful removal of machining debris to avoid contact with and inhaling of the fibers.The machinability of ceramics has improved steadily with the development of nanoceramics (Section 8.2.5) and with the selection of appropriate processing parameters, such as ductile-regime cutting (Section 22.4.2).Metal-matrix and ceramic-matrix composites can be difficult to machine, depending on the properties of the individual components, i.e., reinforcing or whiskers, as well as the matrix material.20.9.4 Thermally Assisted MachiningMetals and alloys that are difficult to machine at room temperature can be machined more easily at elevated temperatures. In thermally assisted machining (hot machining), the source of heat—a torch, induction coil, high-energy beam (such as laser or electron beam), or plasma arc—is forces, (b) increased tool life, (c) use of inexpensive cutting-tool materials, (d) higher material-removal rates, and (e) reduced tendency for vibration and chatter.It may be difficult to heat and maintain a uniform temperature distribution within the workpiece. Also, the original microstructure of the workpiece may be adversely affected by elevated temperatures. Most applications of hot machining are in the turning of high-strength metals and alloys, although experiments are in progress to machine ceramics such as silicon nitride.SUMMARYMachinability is usually defined in terms of surface finish, tool life, force and power requirements, and chip control. Machinability of materials depends not only on their intrinsic properties and microstructure, but also on proper selection and controlof process variables.译文:20.9 可机加工性一种材料的可机加工性通常以四种因素的方式定义:1、分的表面光洁性和表面完整性。
生产自动化毕业论文中英文资料外文翻译文献
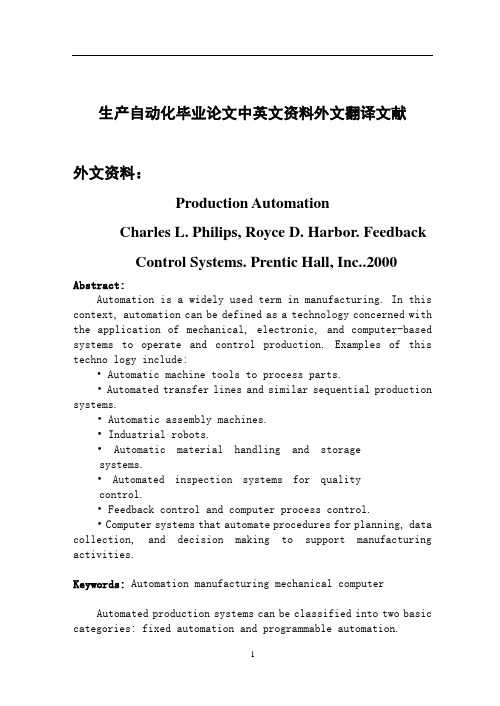
生产自动化毕业论文中英文资料外文翻译文献外文资料:Production AutomationCharles L. Philips, Royce D. Harbor. FeedbackControl Systems. Prentic Hall, Inc..2000Abstract:Automation is a widely used term in manufacturing. In this context, automation can be defined as a technology concerned with the application of mechanical, electronic, and computer-based systems to operate and control production. Examples of this techno logy include:• Automatic machine tools to process parts.• Automated transfer lines and similar sequential production systems.• Automatic assembly machines.• Industrial robots.• Automatic material handling and storagesystems.• Automated inspection systems for qualitycontrol.• Feedback control and computer process control.• Computer systems that automate procedures for planning, data collection, and decision making to support manufacturing activities.Keywords: Automation manufacturing mechanical computerAutomated production systems can be classified into two basic categories: fixed automation and programmable automation.Fixed AutomationFixed automation is what Harder was referring to when he coined the word automation. Fixed automation refers to production systems in which the sequence of processing or assembly operations is fixed by the equipment configuration and cannot be readily changed without altering the equipment. Although each operation in the sequence is usually simple, the integration and coordination of many simple operations into a single system makes fixed automation complex. Typical features of fixed automation include 1. high initial investment for custom-engineered equipment, 2. high production rates, 3. application to products in which high quantities are to be produced, and 4. relative inflexibility in accommodating product changes.Fixed automation is economically justifiable for products with high demand rates. The high initial investment in the equipment can be divided over a large number of units, perhaps millions, thus making the unit cost low compared with alternative methods of production. Examples of fixed automation include transfer lines for machining, dial indexing machines, and automated assembly machines. Much of the technology in fixed automation was developed in the automobile industry; the transfer line (dating to about (1920) is an example.Programmable AutomationFor programmable automation, the equipment is designed in such a way that the sequence of production operations is controlled by a program, i. e., a set of coded instructions that can be read and interpreted by the system. Thus the operation sequence can be readily changed to permit different product configurations to be produced on the same equipment. Some of the features that characterize programmable automation include 1. high investment in general-purpose programmable equipment, 2. lower production rates than fixed automation, 3. flexibility to deal with changes in product configuration, and 4. suited to low and / or medium production of similar products or parts (e. g. part families). Examples of programmable automation include numerically controlled machine tools, industrial robots, and programmable logic controllers.Programmable production systems are often used to produceparts or products in batches. They are especially appropriate when repeat orders for batches of the same product are expected. To produce each batch of a new product, the system must be programmed with the set of machine instructions that correspond to that product. The physical setup of the equipment must also be changed; special fixtures must be attached to the machine, and the appropriate tools must be loaded. This changeover procedure can be time-consuming. As a result, the usual production cycle for a given batch includes 1. a (3 period during which the setup and reprogramming is accomplished and 2. a period in which the batch is processed. The setup-reprogramming period constitutes nonproductive time of the automated system.The economics of programmable automation require that as the setup-reprogramming time increases, the production batch size must be made larger so as to spread the cost of lost production time over a larger number of units. Conversely, if setup and reprogramming time can be reduced to zero, the batch size can be reduced to one. This is the theoretical basis for flexible automation, an extension of programmable automation. A flexible automated system is one that is capable of producing a variety of products (or parts) with minimal lost time for changeovers from one product to the next. The time toreprogram the system and alter the physical setup is minimal and results in virtually no lost production time. Consequently, the system is capable of producing various combinations and schedules of products in a continuous flow, rather than batch production with interruptions between batches. The features of flexible automation are 1. high investment for a custom-engineered system, 2. continuous production of mixtures of products, 3. ability to change product mix to accommodate changes in demand rates for the different products made, 4. medium production rates, and 5- flexibility to deal with product design variations.Flexible automated production systems operate in practice by one or more of the following approaches: 1. using part family concepts, by which the parts made on the system are limited in variety; 2. reprogramming the system in advance and /or off-line, so that reprogramming does not interrupt production; 3. downloading existing programs to the system to produce previouslymade parts for which programs are already prepared;) 4. using quick-change fixtures so that physical setup time is minimized;5. using a family of fixtures that have been designed for a limited number of part styles; and6. equipping the system with a large number of quick-change tools that include the variety of processing operations needed to produce the part family. For these approaches to be successful, the variation in the part styles produced on a flexible automated production system is usually) more limited than a batch-type programmable automation system. Examples of flexible automation are the flexible manufacturing systems for performing machining operations that date back to the late 1960s.Automation StrategiesA number of fundamental strategies exist for improving productivity in manufacturing operations. These strategies often involve the use of automation technology and are, therefore, called automation strategies. Indicating the likely effects of each strategy on operating factors such as cycle time, nonproductive time, manufacturing lead time, and other production parameters.Numerical controlNumerical control (often abbreviated NC) can be defined as a form of programmable automation in which the process is controlled by numbers, letters, and symbols. In NC, the numbers form a program of instructions designed for a particular workpart or job. When the job changes, the program of instructions is changed. This capability to change the program for each new job is what gives NC its flexibility. It is much easier to write new programs than to make major changes in the production equipment.NC equipment is used in all areas of metal parts fabrication and comprises roughly 15% of the modern machine tools in industry today. Since numerically controlled machines are considerably more expensive than their conventional counterparts, the asset value of industrial NC machine tools is proportionally much larger than their numbers. Equipment utilizing numerical control has been designed to perform such diverse operations as drilling, milling, turning, grinding, sheet metal press working, spot welding, arcwelding, riveting, assembly, drafting, inspection, and parts handling. And this is by no means a complete list. Numerical control should be considered as a possible mode of controlling the operation for any production situation possessing the following characteristics:1. Similar workparts in terms of raw material (e. g., metal stock for machining).2. The workparts are produced in various sizes and geometries.3. The workparts are produced in batches of small to medium-sized quantities.4. A sequence of similar processing steps is required to complete the operation on each workpiece.Many machining jobs meet these conditions. The machined workparts are metal, they are specified in many different sizes and shapes, and most machined parts produced in industry today are made in small to medium-size lot sizes. To produce each part, a sequence of drilling operations may be required, or a series of turning or milling operations. The suitability of NC for these kinds of jobs is the reason for the tremendous growth of numerical control in the metalworking industry over the last 25 years.Basic Components of an NC SystemAn operational numerical control system consists of the following three basic components:1. Program of instructions.2. Controller unit, also called machine control unit (MCU).3. Machine tool or other controlled process.The general relationship among the three components is illustrated. The program of instructions serves as the input to the controller unit, which in turn commands) the machine tool or other process to be controlled.Program of instructionsThe program of instructions is the detailed step-by-step set of directions which tell the Wm machine tool what to do. It is coded in numerical or symbolic form on some type of input medium that can be interpreted by the controller unit. The most common input medium is i-inch-wide punched tape. Over the years, other forms of input media have (been used, including punched cards, magnetic tape, and even 35-mm motion picture film.There are two other methods of input to the NC system which should be mentioned. The first is by manual entry of instructional data to the controller unit. This is time-consuming and is rarely used except as an auxiliary means of control or when only one or a very limited number of parts are to be made. The second method of input is by means of a direct link with a computer. This is called direct numerical control, or DNC.The program of instructions is prepared by someone called a part programmer. The programmer's job is to provide a set of detailed instructions by which the sequence of processing steps is to be performed. For a machining operation, the processing steps 4 involve the relative movement of the machine tool table and the cutting tool.Controller unitThe second basic component of the NC system is the controller unit. This consists of the electronics and hardware that read and interpret the program of instructions and convert it into mechanical actions of the machine tool. The typical elements of the controller unit include the tape reader, a data buffer, signal output channels to the machine tool, feedback channels from the machine tool, and the sequence controls to coordinate the overall operation of the foregoing elements.The tape reader is an electrical-mechanical device for winding and reading the punched tape containing the program of instructions. The data contained on the tape are read into the data buffer. The purpose of this device is to store the input instructions in logical blocks of information. A block of information usually represents one complete step in the sequence of processing elements. For example, one block may be the data required to move the machine table to a certain position and drill a hole at that location.The signal output channels are connected to the servomotors and other controls in the machine tool. Through these channels, the instructions are sent to the machine tool from the controller unit. To make certain that the instructions have been properly executed by the machine, feedback data are sent back to the controller via the feedback channels. The most important function of this return loop is to assure that the table and workpart have$ been properly located with respect to the tool. Most NC machine tools in use today are provided with position feedback controls for this purpose and are referred to as closed-loop systems. However, in recent years there has been a growth in the use of open-loop systems, which do not make use of feedback signals to the controller unit. The advocates of the open-loop concept claim that the reliability of the system is great enough that feedback controls are not needed and are an unnecessary extra cost.Sequence controls coordinate the activities of the other elements of the controller unit. The tape reader is actuated to read data into the buffer from the tape, signals are sent to and from the machine tool, and so on. These types of operations must be synchronized and this is the function of the sequence controls.Another element of the NC system, which may be physically part of the controller unit or part of the machine tool, is the control panel. The control panel or control console contains the dials and switches by which the machine operator runs the NC system. It may also contain data displays to provide information to the operator. Although the NC system is an automatic system, the human operator is still needed to turn the machine on and off, to change tools (some NC systems have automatic tool changers), to load and unload the machine, and to perform various other duties. To be able to discharge these duties, the operator must be able to control the system, and this is done through the control panel.Machine toolThe third basic component of an NC system is the machine tool or other controlled process. It is the part of the NC system which performs useful work. In the most common example of an NC system, one designed to perform machining operations, the machine tool consists of the worktable and spindle as well as the motors and controls necessary to drive them. It also includes the cutting tools, work fixtures, and other auxiliary equipment needed in the machining operation.Transfer MachinesThe highest degree of automation obtainable with special-purpose, multifunction machines is achieved by using transfer machines. Transfer machines are essentially acombination of individual workstations arranged in the required sequence, connected by work transfer devices, and integrated with interlocked controls. Workpieces are automatically transferred between the stations, which are equipped with horizontal, vertical, or angular units to perform machining, gagging, workpiece repositioning, assembling, washing, or other operations. The two major classes of transfer machines are rotary and in-line types.An important advantage of transfer machines is that they permit the maximum number of operations to be performed simultaneously. There is relatively no limitation on (the number of workpiece surfaces or planes that can be machined, since devices can be interposed in transfer machines at practically any point for inverting, rotating, or orienting the workpiece, so as to complete the machining operations. Work repositioning also minimizes the need for angular machining heads and allows operations to be performed in optimum time. Complete processing from rough castings or forgings to finished parts is often possible.One or more finished parts are produced on a transfer machine with each index of the transfer system that moves the parts from station to station. Production efficiencies of such machines generally range from 50% for a machine producing a variety of different parts to 85% for a machine producing one part, in high production, depending upon the workpiece and how the machine is operated (materials handling method, maintenance procedures, etc.)All types of machining operations, such as drilling, tapping, reaming, boring, and milling, are economically combined on transfer machines. Lathe-type operations such as turning and facing are also being performed on in-line transfer machine, with the workpieces being rotated in selected machining stations. Turning operations are performed in lathe-type segments in which multiple tool holders are fed on slides mounted on tunnel-type bridge units. Workpieces are located on centers and rotated by chucks at each turning station. Turning stations with CNC are available for use on in-line transfer machines. The CNC units allow the machine cycles to be easily altered to accommodate changes in workpiece design and can also be used for automatic tooladjustments.Maximum production economy on transfer lines is often achieved by assembling parts to the workpieces during their movement through the machine. Such items as bushings, seals, Welch plugs, and heat tubes can be assembled and then machined or tested during the transfer machining sequence. Automatic nut torturing following the application of part subassemblies can also be carried out.Gundrilling or reaming on transfer machines is an ideal application provided that proper machining units are employed and good bushing practices are followed. Contour boring and turning of spherical seats and other surfaces can be done with tracer controlled single-point inserts, thus eliminating the need for costly special form tools. In-process gaging of reamed or bored holes and automatic tool setting are done on transfer machines to maintain close tolerances.Less conventional operations sometimes performed on transfer machines include grinding, induction heating of ring gears for shrink-fit pressing on flywheels, induction hardening of valve seats, deep rolling to apply compressive preloads, and burnishing.Transfer machines have long been used in the automotive industry for producing identical components at high production rates with a minimum of manual part handling. In addition to decreasing labor requirements, such machines ensure consistently uniform high-quality parts at lower cost. They are no longer confined just to rough machining and now often eliminate the need for subsequent operations such as grinding and honing.More recently, there has been an increasing demand for transfer machines to handle lower volumes of similar or even different parts in smaller sizes, with means for quick changeover between production runs. Built-in flexibility, the ability to rearrange and interchange machining units, and the provision of idle stations increases the cost of any transfer machine, but such features are economically feasible when product redesigns are common. Many such machines are now being used in no automotive applications for lower production requirements.Special features now available to reduce the time required for part changeover include I standardized dimensions, modularconstruction, interchangeable fixtures mounted on master pallets that remain on the machine, interchangeable fixture components, the ability to lock out certain stations for different parts by means of selector switches, and programmable controllers. Product design is also important and common transfer and clamping surfaces should be provided on different parts whenever possible.Programmable Logic ControllersA programmable logic controller (PLC) is a solid-state device used to control machine motion or process operation by means of a stored program. The PLC sends output control signals and receives input signals through input/output (I/O) devices. A PLC controls outputs in response to stimuli at the inputs according to the logic prescribed by the stored program. The inputs are made up of limit switches, pushbuttons, and thumbwheels switches, pulses, analog signals, ASCII serial data, and binary or BCD data from absolute position encoders. The outputs are voltage or current levels to drive end devices such as solenoids, motor starters, relays, lights, and so on. Other output devices include analog devices, digital BCD displays, ASCII compatible devices, servo variable-speed drives, and even computers.Programmable controllers were developed (circa in 1968) when General Motors Corp, and other automobile manufacturers were experimenting to see if there might be an alternative to scrapping all their hardwired control panels of machine tools and other production equipment during a model changeover. This annual tradition was necessary because rewiring of the panels was more expensive than buying new ones.The automotive companies approached a number of control equipment manufacturers and asked them to develop a control system that would have a longer productive life without major rewiring, but would still be understandable to and repairable by plant personnel. The new product was named a "programmable controller".The processor part of the PLC contains a central processing unit and memory. The central processing unit (CPU) is the "traffic director" of the processor, the memory stores information. Coming into the processor are the electrical signals from the input devices, as conditioned by the input module to voltage levelsacceptable to processor logic. The processor scans the state of I / O and updates outputs based on instructions stored in the memory of the PLC. For example, the processor may be programmed so that if an input connected to a limit switch is true (limit switch closed), then a corresponding output wired to an output module is to be energized. This output might be a solenoid, for example.The processor remembers this command through its memory and compares on each scan to see if that limit switch is, in fact, closed. If it is closed, the processor energizes the solenoid by turning on the output module.The output device, such as a solenoid or motor starter, is wired to an output module's terminal, and it receives its shift signal from the processor, in effect, the processor is performing a long and complicated series of logic decisions. The PLC performs such decisions sequentially and in accordance with the stored program. Similarly, analog I / O allows the processor to make decisions based on the magnitude of a signal, rather than just if it is on or off. For example, the processor may be programmed to increase or decrease the steam flow to a boiler (analog output) based on a comparison of the actual temperature in the boiler {analog input) to the desired temperature. This is often performed by utilizing the built-in PID (proportional, integral, derivative) capabilities of the processor.Because a PLC is "software based", its control logic functions can be changed by reprogramming its memory. Keyboard programming devices facilitate entry of the revised program, which can be designed to cause an existing machine or process to operate in a different sequence or to respond to different levels of, or combinations of stimuli. Hardware modifications are needed only if additional, changed, or relocated input / output devices are involved.中文翻译:生产自动化摘要:自动化是一个在制造业中广泛使用的术语。
机械设计制造及其自动化毕业设计外文翻译

机械设计制造及其自动化毕业设计外文翻译英文原文名Automatic production line PLC control of automatic feeding station中文译名基于PLC的自动化生产线自动上料站的控制中文译文:自动化生产线自动上料站的PLC控制自动生产线是由工件传送系统和控制系统,将一组自动机床和辅助设备按照工艺顺序联结起来,自动完成产品全部或部分制造过程的生产系统,简称自动线。
二十世纪20年代,随着汽车、滚动轴承、小电机和缝纫机和其他工业发展,机械制造业开始出现在自动生产线,第一个是组合机床自动线。
在20世纪20年代,第一次出现在汽车工业流水生产线和半自动生产线,然后发展成自动生产线。
第二次世界大战后,在机械制造工业发达国家,自动生产线的数量急剧增加。
采用自动生产线生产的产品应该足够大,产品设计和技术应该是先进的、稳定的和可靠的,基本上保持了很长一段时间维持不变。
自动线用于大,大规模生产可以提高劳动生产率,稳定和提高产品质量,改善劳动条件,降低生产区域,降低生产成本,缩短生产周期,保证生产平衡、显著的经济效益。
自动生产线的一个干预指定的程序或命令自动操作或控制的过程,我们的目标是稳定、准确、快速。
自动化技术广泛用于工业、农业、军事、科学研究、交通运输、商业、医疗、服务和家庭,等自动化生产线不仅可以使人们从繁重的体力劳动、部分脑力劳动以及恶劣、危险的工作环境,能扩大人的器官功能,极大地提高劳动生产率,提高人们认识世界的能力,可以改变世界。
下面我说下它的应用范围:机械制造业中有铸造、锻造、冲压、热处理、焊接、切削加工和机械装配等自动线,也有包括不同性质的工序,如毛坯制造、加工、装配、检验和包装等的综合自动线。
加工自动线发展最快,应用最广泛的机械制造。
主要包括:用于处理盒、外壳、各种各样的部件,如组合机床自动线;用于加工轴、盘部分,由通用、专业化、或自动机器自动专线;转子加工自动线;转子自动线加工过程简单、小零件等。
生产自动化毕业论文中英文资料外文翻译文献
生产自动化毕业论文中英文资料外文翻译文献随着科技的不断进步和人们对效率的追求,生产自动化已经成为现代工业的重要组成部份。
生产自动化通过引入先进的机械和电子设备,以及自动化控制系统,实现了生产过程的自动化和智能化。
本文将介绍一些关于生产自动化的研究和应用的外文翻译文献。
1. 文献一:《生产自动化的发展与趋势》这篇文献介绍了生产自动化的发展历程和未来的趋势。
文章指出,生产自动化的发展可以追溯到20世纪初,随着电子技术和计算机技术的不断进步,生产自动化得到了快速发展。
未来,生产自动化将更加注重智能化和柔性化,以适应不断变化的市场需求。
2. 文献二:《生产自动化在汽车创造业中的应用》这篇文献探讨了生产自动化在汽车创造业中的应用。
文章指出,汽车创造业是生产自动化的典型应用领域之一。
通过引入机器人和自动化生产线,汽车创造商可以大大提高生产效率和产品质量。
此外,生产自动化还可以减少人力成本和人为错误。
3. 文献三:《生产自动化对工作环境和员工的影响》这篇文献研究了生产自动化对工作环境和员工的影响。
文章指出,尽管生产自动化可以提高生产效率,但它也带来了一些负面影响。
例如,自动化设备的噪音和振动可能对员工的健康造成影响。
此外,自动化还可能导致一些工人失去工作机会。
因此,为了最大限度地发挥生产自动化的优势,必须采取适当的安全措施和培训计划。
4. 文献四:《生产自动化在食品加工行业中的应用》这篇文献讨论了生产自动化在食品加工行业中的应用。
文章指出,食品加工是一个复杂而繁琐的过程,生产自动化可以大大提高生产效率和产品质量。
通过引入自动化设备和控制系统,食品加工商可以减少人为错误和污染风险。
此外,生产自动化还可以实现对食品生产过程的精确控制和监测。
5. 文献五:《生产自动化在医药创造业中的应用》这篇文献探讨了生产自动化在医药创造业中的应用。
文章指出,医药创造是一个高度精细和复杂的过程,生产自动化可以提高生产效率和产品质量的同时,确保药品的安全和一致性。
PLC毕设相关英文文献翻译
翻译对应文章Programmable Logic Controllers可编程序逻辑控制器1.1动力1968年,Richard E. Morley创造出了新一代工业控制装置可编程逻辑控制器(PLC),现在,PLC已经被广泛应用于工业领域,包括机械制造也、运输系统、化学过程设备、等许多其他领域。
初期可编程控制器只是用一种类似于语言的软件逻辑于代替继电器硬件逻辑,并且使开发时间由6个月缩短到6天。
虽然计算机控制技术已经产生,但是PLC控制因为它的高性能、成本低、并且对恶劣的环境有很强的适应能力而在工业控制的广泛应用中保持优势。
而且,尽管硬件的价格在逐渐下跌,据估计,根据Frost和Sullivan对PLC市场的调查研究表明,每年销售硬件的价格要比销售PLC的价格(一千五百万)至少多出八十亿美元。
PLC的创造者Richard E. Morley十分肯定的认为目前PLC市场是一个价值五十亿的工业虽然PLC广泛应用于工业控制中,PLC控制系统的程序依然和语法有关。
和软件过程一样,PLC的软件设计也以同样的方式会遇到软件错误或危机。
Morley在演讲中着重强调了这个方面。
如果房子建造的像软件过程一样,那么仅仅一只啄木鸟就可以摧毁文明。
特别的,PLC程序要解决的实际问题是消除软件错误和减少老式梯形逻辑语言的花费。
尽管PLC的硬件成本在继续下降,但是在工业控制上减少梯形逻辑的扫描时间仍然是一个问题,以至于可以用到低耗时的PLC。
一般来说,和其他领域相比生产PLC的周期要短很多。
例如,在实践中,VISI设计是一种有效的计算机辅助设计。
PLC不需要使用目前的以软件设计为基础软件工程方法论,因为PLC程序要求对软件和硬件搜都要考虑到。
因此,软件设计越来越成为花费动力。
在许多的工业设计工程中,超过的人力分配给了控制系统设计和安装,并且他们要对。
PLC程序测试和排除错误,再者,PLC控制系统不适合设计对适应性和重构有越来越多要求的生产系统。
自动化生产线外文翻译
English Translation Material1. Transfer MachineThe highest degree of automation with special-purpose, multifunction machines is achieved by using transfer machines. Transfer machine are essentially a combination of individual workstations arranged in the required sequence, connected by work transfer devices, and integrated with interlocked controls. Workplaces are automatically transferred between the stations, which are equipped with horizontal, vertical, or angular units to perform machining , gaging ,workplace repositioning, assembling, washing, or other operation. The two major classes of transfer machines are rotary and in-line types. An important advantage of transfer machines is that they permit the maximum number of operations to be performed simultaneously. There is relatively no limitation on the number of workplace surface or planes that can be machined, since devices can be interposed in transfer machines at practically any point for inverting, rotating, or orienting the workplace, so as to complete the machining operations. Work repositioning alsominimizes the need for angular machining heads and allows operations to be performed in optimum time. Complete processing from rough casting or forging to finished parts is often possible.One or more finished parts are produced on a transfer machine with each index of the transfer system that moves the parts from stations to stations. Production efficiencies of such machines generally range from 50% for a machine variety of different parts to 85% for a machine producing one part, in high production, depending upon the workplace and how the machine is operated(material handling method, maintenance procedures, etc. )All types of machining operations, such as drilling, tapping, reaming, boring, and milling, are economically combined on transfer machines. Lathe-type operations such as turning and facing are also being performed on in-line transfer machine, with the workplace being rotated in selectedmachining stations. Turning operations are performed in lathe-type segments in which toolholders are fed on slides mounted on tunnel-type bridge units. Workplaceare located on centers and rotated by chucks at each turning station. Turning stations with CNC are available for use on in-line transfer machine. The CNC units allow the machine cycles to be easily altered to accommodate changes in workplace design and can also be used for automatic tool adjustments.Maximum production economy on transfer lines is often achieved by assembling parts to the workplaces during their movement through the machine. such items as bushings, seals, welch plugs, and heat tubes can be assembled and then machine or tested during the transfer machining sequence. Automatic nut torquing following the application of part subassemblies can also be carried out.Gundrilling or reaming on transfer machines is an ideal application provided that proper machining units are employed and good bushing practices are followed. Contour boring and turning of spherical seats and other surface can be done with tracer-controlled single-point inserts, thus eliminating the need for costly special form tools. In-process gaging of reamed or bored holes and automatic tool setting are done on transfer machines tomaintain close tolerances.Less conventional operations sometimes performed on transfer machines include grinding, induction heating of ring gears for shrink-fit pressing on flywheels, induction hardening of valve seats, deep rolling to apply compressive preloads, and burnishing.Transfer machines have long been used in the automotive industry for production rates with a minimum of manual part handling. In addition to decreasing labor requirements, such machines ensure consistently uniform, high-quality parts at lower cost. They are no longer confined just to rough machining and now often eliminate the need for subsequent operations such as grinding and honing.More recently, there has been an increasing demand for transfer machines to handle lower volumes of similar or even different parts in smaller sizes, with means for quick changeover between production runs. Built-in flexibility, the ability to rearrange and interchange machine units, and the provision of idle stations increases the cost of any transfer machine, but such feature are economically feasible when product redesignsare common. Many such machines are now being used in nonautomotive applications for lower production requirements.Special feature now available to reduce the time required for part changeover include standardized dimensions, modular construction, interchangeable fixtures mounted on master pallets that remain on the machine, interchangeable fixture components, the ability to lock out certain stations for different parts by means of selector switches, and programmable controllers. Product design is also important, and common transfer and clamping surfaces should be provided on different parts whenever possible.2. Programmable Logic ControllersA programmable logic controller (PLC) is a solid-state device used to control machine motion or process operation by means of a stored program. The PLC sends output control signals output and receive input signals through input/output (I/O) devices. A PLC controls output in response to stimuli at the inputs according to the logic prescribed by the stored program. The inputs are made up of limit switches, pushbuttons,thumbwheels, switches, pulses, analog signal, ASCII serial data, and binary or BCD data from absolute position encoders. The output are voltage or current level to drive end devices such as solenoids, motor starters, relays, lights, and so on. Other output device include analog devices, digital BCD displays, ASCII compatible devices, servo variable-speed drives, and even computers.Programmable controllers were developed (circa in 1968) when General Motors Corps, and other automobile manufacturers were experimenting to see if there might be an alternative to scrapping all their hardwired control panel of machine tools and other production equipment during a model changeover. This annual tradition was necessary because rewriting of the panels was more expensive than buying new ones.The automotive companies approached a number of control equipment manufacturers and asked them to develop a control system that would have a longer productive life without major rewriting, but would still be understandable to and repairable by the plant personnel. The new product was named a “programmablecontroller”.The processor part of the PLC contains a central processing unit and memory. The central processing unit (CPU) is the “traffic direction” of the processor, the memory stores information. Coming into the processor are the electrical signals from the input devices, as conditioned by the input module to voltage levels acceptable to processor logic. The processor scans the state of I/O and updates outputs stored in the memory of the PLC. For example, the processor may be programmed so that if an input connected to a limit switch is true (limit switch closed), then a corresponding output wired to an output module is to be energized. This processor remembers this command through its memory and compares on each scan to see if that limit switch is, in fact, closed. If it is closed ,the processor energizes the solenoid by turning on the output module.The output device, such as a solenoid or motor starter, is wired to an output module’s terminal, and it receives its shift signal from the processor, in effect, the processor is performing a long and complicated series of logic decisions. The PLC performs such decisions sequentiallyand in according with the stored program. Similarly, analog I/O allows the processor to make decisions based on the magnitude of a signal, rather than just if it is on or off. For example, the processor may be programmed to increase or decrease the steam flow to a boiler (analog output) based on a comparison of the actual temperature in the boiler (analog input ) This is often performed by utilizing the built-in PID (proportional, integral, derivative) capabilities of the processor.Because a PLC is “software based”, its control logic functions can be changed by reprogramming its memory. Keyboard programming devices facilitate entry of the revised program, which can be design to cause an existing machine or process to operate in a different sequence or to different level of, or combinations of stimuli. Hardware modifications are needed only if additional, changed, or relocated input/output device are involved.3. Automated AssemblyAssembly in the manifacturing process consists of putting together all the component parts and sub-assemblies of a given product, fastening, performinginspections and function tests, labeling, separating good assembly from bad, and packaging and or preparing them for final use. Assembly is unique compared to the methods of manufacturing such as machining, grinding, and welding in that most of these processes invovle only a few disciplines and possibly only one. Most of these nonassembly operations cannot be performed weithout the aid of equipment; thus the development of automatic methods has been necessary rather than optional. Assembly, on the other hand, may involve in one machine many of the fastening methods,such as riveting, welding, screwdriving,and adhesive application,as well as automatic parts seletion, proding, gaging, functional testing, labeling,and packaging. The state of the art in assembly operations has not reached the level of standardization; much manual work is stillbeing performed in this area.Assembly has traditionally been one of the highest areas of direct labor costs. In some cases, assembly accounts for 50% or more of manufacturing csosts and typically 20% ~50%. However, closer cooperation between design and manufacturing engineers hasresulted in reducing and in a few cases eliminating altogether the need for assembly. When asssembly is required, improved design or products has simplified automated (semiautomatic or automatic) assembly. Considerations for Automated AssemblyBefore automated assembly is adopted, several factors should be considerd. These include practicality of the process for automation, simulation for economic considerations and justification, management involvement, and labor relations.Determining the practicality of automated assembly required careful evaluation of the following:a)The number of parts in assembly.b)Design of the parts with respect to producibility, assembility, automatic handling, and testability (materials, forms, dimensional tolerances, and weights).c)Quality of parts to be assembled. Out-of-tolerance or defective parts can cause production losses and increase costs because of stoppages.d)Availablity of qualiyied, technically competent personal to be responsible for equipment operation.e) Total production and production-rate requipments.Product variations and frequency of design changes.f)Joining methods required.g)Assembly times and costs.h)Assembly lines or system configuration, using simulation, including material handling.译文1. 自动生产线使用自动生产线可以利用专用、多功能机床来实现最大程度的自动化。
PLC-文献翻译-英文-中文-自动化
附件1:外文资料翻译译文人机界面系统的探讨超过60000人致力于相同的目标:增加你的竞争力,这就是西门子自动化和驱动。
我们在你的行业,无论是关于自动化工程、驱动或是电气安装系统,都让您拥有一个综合组合可持续性成功。
全集成自动化(TIA)和全集成能源(TIP)形成我们提供的核心形式。
TIA和TIP是关于产品和系统集成的范围制造业和流程工业以及楼宇自动化的基础。
这种投资组合在您的发电厂的整个生命周期中变得更加完善。
请您了解我们产品和系统为您提供的潜能。
并发现您如何和我们一起永久性的提高您的生产力。
你的西门子区域联系商可以提供更多的信息,他或她会很高兴为您提供帮助。
Windows XP嵌入式或Windows XP专业版允许客户选择一个标准的操作系统或使用嵌入式系统来增强安全性,这与闪存的结合在实践中开辟了新的视角。
操作系统和应用程序在一个受保护的闪存卡提供一个安全的和短的稳定系统启动。
额外的硬盘可以保存临时数据(数据跟踪、产品跟踪、临时图像文件或植物状态),或者内存密集型数据库SQL服务器。
即使在硬盘故障时,手动模式仍可以继续生产。
创新WinCC flexile的可视化软件和自动化软件基于WinAC RTX是理想的配置。
pc477b OEM可以根据要求提供个人硬件,软件以及设计的扩充和修改。
对于SIMATIC WinCC flexile和SIMATIC WinCC产品系列,SIMATIC HIM等应用软件的可视化和软件配置我们将提供完整的范围。
SIMATIC WinCC flexile包括应用程序直接在机器从基于pc的人机界面解决方案基于WinCC flexible Runtime通过SIMATIC HMI操作面板的单用户系统,。
配置上位机WinCC flexile运行时对电脑以及SIMATIC HMI控制单元、WinCC flexile的家庭也提供集成和可扩展的配置工具WinCC flexible Micro, WinCC flexible Compact, WinCC flexible Standard and WinCC flexible Advanced.SIMATIC WinCC是可视化或SCADA系统(基于pc机的HMI系统) 的过程,用于可视化和控制过程,生产流程,机器和设备的所有部门——从简单的单用户系统到分布式多用户系统的冗余服务器和Web客户端的一种解决方案。
- 1、下载文档前请自行甄别文档内容的完整性,平台不提供额外的编辑、内容补充、找答案等附加服务。
- 2、"仅部分预览"的文档,不可在线预览部分如存在完整性等问题,可反馈申请退款(可完整预览的文档不适用该条件!)。
- 3、如文档侵犯您的权益,请联系客服反馈,我们会尽快为您处理(人工客服工作时间:9:00-18:30)。
毕业设计(论文)外文文献翻译文献、资料中文题目:自动生产线PLC自动送料站控制文献、资料英文题目:文献、资料来源:文献、资料发表(出版)日期:院(部):专业:机械设计制造及其自动化班级:姓名:学号:指导教师:翻译日期: 2017.02.14英文原文名Automatic production line PLC control中文译文:自动化生产线自动上料站的PLC控制自动生产线是由工件传送系统和控制系统,将一组自动机床和辅助设备按照工艺顺序联结起来,自动完成产品全部或部分制造过程的生产系统,简称自动线。
二十世纪20年代,随着汽车、滚动轴承、小电机和缝纫机和其他工业发展,机械制造业开始出现在自动生产线,第一个是组合机床自动线。
在20世纪20年代,第一次出现在汽车工业流水生产线和半自动生产线,然后发展成自动生产线。
第二次世界大战后,在机械制造工业发达国家,自动生产线的数量急剧增加。
采用自动生产线生产的产品应该足够大,产品设计和技术应该是先进的、稳定的和可靠的,基本上保持了很长一段时间维持不变。
自动线用于大,大规模生产可以提高劳动生产率,稳定和提高产品质量,改善劳动条件,降低生产区域,降低生产成本,缩短生产周期,保证生产平衡、显著的经济效益。
自动生产线的一个干预指定的程序或命令自动操作或控制的过程,我们的目标是稳定、准确、快速。
自动化技术广泛用于工业、农业、军事、科学研究、交通运输、商业、医疗、服务和家庭,等自动化生产线不仅可以使人们从繁重的体力劳动、部分脑力劳动以及恶劣、危险的工作环境,能扩大人的器官功能,极大地提高劳动生产率,提高人们认识世界的能力,可以改变世界。
下面我说下它的应用范围:机械制造业中有铸造、锻造、冲压、热处理、焊接、切削加工和机械装配等自动线,也有包括不同性质的工序,如毛坯制造、加工、装配、检验和包装等的综合自动线。
加工自动线发展最快,应用最广泛的机械制造。
主要包括:用于处理盒、外壳、各种各样的部件,如组合机床自动线;用于加工轴、盘部分,由通用、专业化、或自动机器自动专线;转子加工自动线;转子自动线加工过程简单、小零件等。
1.确保节拍时间:无论什么样的产品,都必须完成的时间生产。
2.单元过程:只有一个产品,单位部分处理、组装、加工和材料。
3.先导器:理解为视觉设备节拍时间。
4.U型生产线:校准设备按照项目订单逆时针方向,和一个人负责出口和入口。
5.AB控制:只有当没有产品工程,工程的产品,使项目。
6.灯光:传达我们的产品线过程变化的装置。
7.后工程领取:在产品的生产线,以满足项目需求。
设备联接:自动线中设备的联结方式有刚性联接和柔性联接两种。
在刚性联接自动线中,没有装载装置,工件加工和传播过程有严格的节奏。
当暂停设备故障,将导致政府关门。
因此,刚性连接自动生产线的工作需要高可靠性的各种设备。
在自动生产线柔性连接,每个工序(或部分)之间的加载装置,比不必严格在每个过程是一致的,短暂的停顿,一个设备可以由存储设备在一定时间来调整平衡,从而不会影响其他设备的正常工作。
集成自动生产线、装配、自动线路和时间组合机床自动线通常采用柔性连接。
组成部分:自动线路传输系统一般包括机床和工件装载装置,传动装置和加载装置。
在转子加工自动线,传动装置,包括重力式输送机或迫使槽或进料输送机,推广、传输和配电装置等。
有时,机械手完成转运装置的功能。
在组合机床自动线工件有合适的输送机基础,采用直接传输方式,传输设备有各种步进式输送机、传输装置和翻转装置形状不规则,没有适当的传输的基础表面的工件,通常在托盘的位置和运输,这种情况将增加托盘返回设备。
自动生产线控制系统主要是用于确保机床的传动系统,工件,依照有关规定和辅助设备的正常工作的工作周期和联锁要求,检验设备和信号设备和麻烦。
适应的要求自动生产线的调试和正常运行,控制系统有三种工作状态:,半自动和自动调整。
的调整可以手动操作和调整,实现单机每个行动;在半自动可实现单机单工作;在自动传输机可以连续工作。
控制系统有其“停止”控制功能、停车、传送机在正常工作条件下需要完成一个工作循环,每个机床的运动部件上停车后回到原来的位置。
自动设置的其他辅助设备按照流程和自动化程度的要求,比如洗衣机工件自动检测装置,自动工具改变装置,自动芯片系统和冷却系统,等。
为了提高生产力,自动行必须确保自动生产线的工作可靠性。
主要影响因素自动生产线的可靠性工作是加工质量和设备的稳定运行的可靠性。
自动生产线的发展方向主要是提高生产率和增加通用性和灵活性。
为了适应多种生产的需要,调整开发可以快速可调自动生产线。
这生产线是一套基于PLC控制的教学系统,也是一套模块化的生产实训系统。
它集电气控制、PLC应用、传感器和气动等多种技术于一体, 由自动上料、传输检测、真空分拣、颜色分拣、位置调整、配件供给和装配下料等七个工作站组成。
自动上料站的功能是为其它工作站提供工件。
工件由气动机械手抓取,经平移,升降,摆动等动作,放到输送带上,然后回归原位。
1.系统的硬件设计自动上料模块是整个自动生产线系统的起始单元,主要由工件装料管和推出装置,支架,阀组,终端组件、PLC、按钮、槽底板,等。
主要功能是被放置在一个掩体工件自动推到材料板,以便运输单元的机械手抓取和输送。
有手动和自动两种操作方式。
操作前应确保进料板材料。
1.1 动作过程上料单元主体是一个转动的料盘,料盘上设置两个管形料仓。
在料盘口对应上料的位置安装了漫反射光电开关,功能是检测材料装在盘子里。
当工件将达到位置,光电开关检测工件的存在,然后系统提供本单位圆盘材料工件的信号。
在输送单元控制程序中,您可以使用信号状态的构件驱动机械手装置,去旅游。
本在重力的作用下工件自动向下移动工件,准备下一个抓取工件。
如果当前盘没有工件,材料板将在程序控制下的预期位置继续测试。
直到两个菜没有工件,材料板停止转动。
1.2 气动回路设计气动控制回路是本工作单元的执行机构,由气动机械手和上料转盘组成,完成上料和取料。
机械手在结构上由两个直线气缸、一个摆动气缸和气爪组成。
归位状态为:气爪闭,平移缸退,升降缸落,摆缸0°。
一个工作循环:气爪闭→气爪开→升降缸升→平移缸进→气爪闭→平移缸退→摆缸180°→平移缸进→升降缸落→ 气爪开→平移缸退→升降缸升→摆缸0°。
机械手可以完成翻译,举重和摆动臂爪抓取动作,由磁性接近开关安装在每个气缸的缸测试极限位置,然后由PLC实现位置控制。
五两位五通双电动电磁阀安装在收集器板,控制机械臂的平移、起重和摆动控制和上料盘的旋转动作。
1.3 PLC控制在上料单元中,检测磁开关、位置缸材料盘没有光电开关的工件,传输拥塞检测传感器和控制按钮,PLC,总共14个输入终端接收信号。
电磁阀来控制运动的输出,故障信号和信号,共13个输出终端。
可以选择西门子s7 - 300的主要单位和从站之间的信息交换。
2.系统的软件设计PLC梯形图程序的设计方法有经验法和顺序控制法两种。
顺序控制设计法的基本思想是将系统的一个工作周期划分为若干个顺序相连的步,用编程元件(例如存储器位M)来代表,在任何一步内各输出量的状态不变。
使系统由当前步进入下一步的信号称为转换条件,它可以是外部的输入信号,如按钮、限位开关的通断等。
也可以是PLC内部产生的信号,如定时器和计数器的触点信号。
使用顺序控制设计方法时,首先根据系统的工艺流程,所示的顺序功能图,再根据顺序功能图画出梯形图来完成程序设计。
The original textAutomatic production line PLC control of automatic feeding station Automatic production line is composed of the workpiece transmission system and control system, a set of automatic machine and auxiliary equipment in accordance with the process sequence, completion of all or part of the manufacturing process production system, automatic line for short.The 20th century 20 s, as car, rolling bearings, small motor and sewing machines and other industrial development, machinery manufacturing industry began to appear in automatic production line, the first is the modular machine tool automatic line. In the 1920 s, first appeared in the automotive industry running water production line and semi-automatic production lines, and then developed into the automatic production line. After the second world war, in the machinery manufacturing industry in developed countries, the number of automatic production line has increased dramatically. Adopt the products of the automatic production line should be large enough, the product design and technology should be advanced, stable and reliable, remained largely unchanged for a long time. Automatic line for large, mass production can improve labor productivity, stability and improve product quality, improve labor condition, reduce the production area, reduce the production cost, shorten production cycle, guarantee the production of balance, significant economic benefits.Automatic production line of an intervention in a specified program or command automatic operation or control of process, our goal is to be stable, accurate and fast. Automation technology is widely used in industry, agriculture, military, scientific research, transportation, business, health, services, and family, such as automatic production line can not only make people from heavy manual labor, parts of mental Labour and bad, dangerous working conditions, can expand human organ function, greatly improve the labor productivity, improve the ability of people to know the world, can change the world.Below I say under its scope of application:In mechanical manufacturing casting, forging, stamping, heat treatment, welding, machining and mechanical assembly, automatic line, also to have the process including different properties, such as blank manufacturing, machining, assembly, testing and packaging of integrated automatic line.Processing and automatic line fastest growing, most widely used machinery manufacturing.Mainly includes: used for processing box, shell, all kinds of parts, such as the combination machine tools automatic line; Used for machining shaft, plate part, by gm, specialization, or automatic machine automatic line; Rotor processing automatic line; Rotor automatic line, such as simple process, small parts.1. Ensure the takt time: no matter what kind of products, are required to complete the time of production.2. Unit process: only a product, the unit parts processing, assembly, processing and materials.3. The guide: understand the takt time for visual devices.4. U-shaped line: calibration equipment in accordance with the project order counterclockwise, and a person in charge of export and entry.5. AB control: only when there is no product engineering, product engineering, make the project.6. Lighting: convey our product process change device.7. After the engineering drawing: in the product line, in order to meet project requirements.Equipment connection:Automatic line of the connection device has two kinds of rigid connection and flexible connection.In rigid connection automatic line, there is no loading device, processing and transmission process has strict rhythm. When the suspension of equipment failure, will lead to shut down the government. Therefore, rigid connection of automatic production line work need high reliability of various equipment.In the automatic production line of flexible connections, each working procedure (or parts) between the loading device, than don't have to be strict in each process is consistent, a brief pause, a device can be made by a storage device in a certain time to adjust the balance, thus will not affect the normal work of the other devices. Integrated automatic production line, assembly, automatic line and time combination machine tools automatic line usually adopt flexible connection.Components:Automatic line transmission system generally includes machine tools and the workpiece loading device, transmission device and load device. In rotor machining automatic line, transmission device, including gravity conveyor or force or feed conveyor trough, the promotion,。