长材直接轧制铸坯保温设备、生产线及方法的制作技术
长钢H型钢生产线的装备技术及应用

长钢H型钢生产线的装备技术及应用长钢H型钢生产线是一种重要的金属加工设备,主要用于生产H型钢、I型钢等长条铁材料。
其装备技术及应用是现代工业生产领域的重要组成部分。
本文将从以下几个方面进行阐述。
1. 加工工艺流程长钢H型钢生产线的加工工艺流程主要包括:原材料预处理、轧制成型、冷却控制、精整修整、打标喷码以及出库包装等步骤。
其中,轧制成型是整个生产流程中最为关键的环节。
2. 关键设备长钢H型钢生产线的关键设备包括:加热炉、轧机、冷却设备、切割机、抛丸清理机、喷漆机等。
其中,轧机是整个生产线中最为重要的设备,其自动化程度、轧制效果直接关系到产品的质量和产量。
3. 控制技术长钢H型钢生产线的控制技术主要包括PLC控制、电气控制、液压控制等。
这些控制技术可以实现对轧机、切割机、抛丸清理机等设备的精确控制,使得产品质量更为稳定。
长钢H型钢生产线广泛应用于建筑、桥梁、工程机械等领域。
具体来说:1. 建筑领域长钢H型钢生产线生产的H型钢广泛应用于建筑领域,比如各类工业厂房的结构支撑、顶部悬挑、大跨度梁架、钢框架结构等。
这些用途都需要长钢H型钢具备较好的承载能力,使得在建筑领域中,长钢H型钢生产线是不可或缺的装备之一。
2. 桥梁领域之所以长钢H型钢生产线被广泛应用于桥梁领域,是因为其长条材料具有较好的强度和刚度,能够满足桥梁建设的需要。
比如,现代高速公路、城市快速路、铁路等铁路建设过程都需要大量的长钢H型钢,使得长钢H型钢生产线在桥梁领域得到了大力推广和应用。
3. 工程机械领域工程机械是一个需要使用大量长条材料的领域,比如各类挖掘机、推土机、装载机等。
这些机械需要具备较强的承载能力和抗压能力,因此选用长钢H型钢作为机械材料便成为了一个必然的选择。
长钢H型钢生产线就成为了这些工程机械生产领域中一个不可或缺的装备之一。
三、长钢H型钢生产线面临的挑战1. 钢材精度的不断提高,要求设备精度也要相应提高。
2. 模具的使用寿命和模具精度的保证是长钢H型钢生产线经常面临的问题。
首钢2250mm热连轧机技术规格
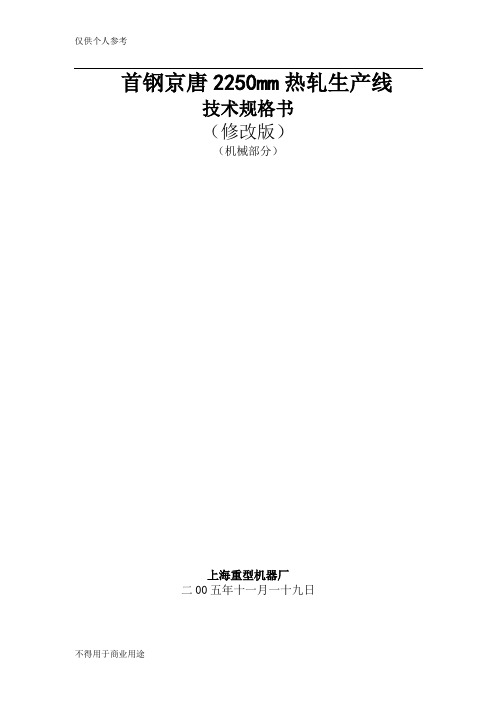
首钢京唐2250mm热轧生产线技术规格书(修改版)(机械部分)上海重型机器厂二00五年十一月一十九日目录一、原料与产品二、设备与技术参数三、设备清单一.原料与产品1.原料规格(100%连铸坯)所有原料全部为连铸坯,由相邻的连铸车间通过辊道送入热轧车间。
板坯规格如下:板坯厚度:230、250mm(以230mm为主)板坯宽度:1100mm~2180mm板坯长度:9000~12000mm(长尺)4500~5800mm(短尺)板坯重量:42t(max.)2.钢种2250mm热轧带钢生产线生产的产品品种为:生产的主要钢种有碳素结构钢、优质碳素结构钢、锅炉及压力容器用钢、造船用钢、桥梁用钢、管线用钢、耐候钢、IF钢、双相(DP)和多相(MP)及相变诱导塑性钢(TRIP)、超微细品粒高强度钢等。
3.成品规格带钢厚度: 1.2~25.4mm带钢宽度:830~2130mm钢卷内径:%%c762mm;钢卷外径:%%c2200mm(max)最大卷重:42t;最大单位卷重:24kg/mm年产钢卷量:550万吨二.设备及技术参数1. 除鳞机前辊道作用输送板坯位置位于加热炉与除鳞机之间。
技术参数类型单独传动辊道长度约4320mm辊间距约1080mm辊子数 5个辊径 450mm辊身长 2250mm辊道速度 0±1.5m/s设计辊类型实心锻钢,轴颈冷却辊轴承调心滚子轴承辊传动通过电机减速机和联轴器传动润滑辊道轴承和集中干油润滑系统相连2. 除鳞机辊道作用输送板坯位置位于除鳞机内部技术参数类型单独传动辊道长度约6860mm辊间距不等辊子数 8个辊径 450mm辊身长 2250mm辊道速度 0±1.5m/s设计辊类型实心锻钢辊辊轴承调心滚子轴承润滑辊道轴承和集中干油润滑系统相连3. 初级除鳞机作用去除板坯表面氧化铁皮位置除鳞机位于除鳞机辊道上技术参数除鳞箱的长度约5600mm水压喷嘴处的最大压力180—190bar190bar时水消耗总量 max710m3/h喷水宽度约2300mm集管数量上部 2下部 2喷嘴数量每个集管37个设计喷嘴扁平喷嘴除鳞箱罩装有收集水槽集水槽集中在罩的上部链帘在出入口侧、钢制4. 定宽机前辊道作用输送板坯通过定宽机。
轧钢机械设备

(5)连续式轧机
第44页/共81页
第45页/共81页
(6)串(顺)列往复式(跟踪式、越野式)轧机
第46页/共81页
(7)布棋式轧机
第47页/共81页
(8)复二重式轧机
第48页/共81页
1.4 主机列的构成及各部分的作用
二辊冷轧机
第49页/共81页
第50页/共81页
第51页/共81页
飞轮:轧制时,冲击负荷作用下,系统减速,负载的一部 分有飞轮放出储存的动能来克服。轧件轧出后(空载), 负载突减,主电机带动飞轮加速,飞轮储存能量。
1.3 轧钢机分类 1.3.1 轧钢机按用途分类:可直观显现轧机的主要性能参数 和所生产的产品形状、尺寸。
第7页/共81页
第8页/共81页
1.3.2 按结构分类:根据轧辊在机座中的布置形式 1.3.2.1轧辊水平布置
(1)二辊式轧钢机
第9页/共81页
第10页/共81页
(2)三辊式轧机
第11页/共81页
(5)板形控制:板形控制主要是通过变更轧辊凸度来控制。 为了增大轧辊凸度调整效果,开发了多种新型轧机。主要 有三种:1)横移工作辊:HC、CVC轧机;2)三菱重工及 新日铁开发的PC轧机,通过调整工作辊交叉角来形成不同 凸度辊缝;3)石川岛播磨开发的,在支撑辊中间设置液压 油腔,在其中注入高压油从而调整支撑辊凸度的VC轧机。
1.7.2 热轧板带轧钢机技术的新进展
(1)连铸坯连续铸轧直接将金属熔体“轧制”成半成品带坯 或成品带材的工艺称为连续铸轧。这种工艺的显著特点是其 结晶器为两个带水冷系统的旋转铸轧辊,熔体在其辊缝间完 成凝固和热轧两个过程,而且在很短的时间内(2—3s)完成的。
直接轧制即“连铸一切断一加热或补热一轧制”方式的组
包钢2250mm热轧生产线工艺流程

包钢2250mm热轧生产线工艺流程1. 原料准备在热轧生产线上,主要的原料是热轧坯和燃料。
热轧坯是通过连铸机将液态钢浇铸成坯,在坯料冷却后送至热轧车间。
燃料主要是煤炭、焦炭和焦粉,用于热轧炉的加热。
2. 热轧工艺热轧工艺是将热轧坯通过一系列的轧制工序,使其形成所需的钢材产品。
热轧工艺包括加热、粗轧、精轧、冷却等工序。
加热:热轧坯进入炉内进行加热,将坯料加热至适合热轧的温度,以便于后续的轧制工序。
粗轧:加热后的坯料通过粗轧机进行轧制,将坯料压制成厚度适中的钢板。
精轧:粗轧后的钢板再经过精轧机进行轧制,使其变得更加平整、光滑,并且使钢材的厚度更加精确。
冷却:经过精轧后的钢板,通过冷却设备,迅速冷却至室温,以获得理想的组织和性能。
3. 质量控制热轧生产线上的质量控制是非常重要的,其关键是控制热轧工艺中的各项参数,以确保生产出合格的产品。
温度控制:热轧时,通过监测和控制炉内温度,保证钢坯达到理想的热轧温度,确保热轧过程中的均匀性。
轧制力控制:通过控制轧机的轧制力和速度,保证轧制过程中的稳定性,避免产生过大的轧制应力,保证产品的表面光洁度和尺寸精度。
冷却控制:通过控制冷却设备,保证产品的冷却速度和温度均匀性,确保产品的组织和性能达到要求。
4. 辅助设备热轧生产线上还配备了各种辅助设备,如切割机、卷取机、探伤机等,用于对热轧钢材进行后续加工和检测。
切割机:用于将热轧钢板切割成所需的长度和宽度。
卷取机:用于将热轧钢板卷取成卷材,以便于运输和储存。
探伤机:用于对热轧钢材进行探伤,检测产品的质量和表面缺陷。
5. 成品检验最后,热轧钢材经过生产线上的各项工艺后,需要进行全面的成品检验,以确保产品的质量符合要求。
尺寸检验:通过测量设备对产品的尺寸精度进行检验。
化学成分检验:通过化学分析仪器对产品的化学成分进行检验。
机械性能检验:通过拉伸试验、冲击试验等手段对产品的机械性能进行检验。
表面质量检验:通过目视和仪器检测对产品表面质量进行检验。
连铸生产复合金属板坯、方坯的方法及其连铸机与制作流程

本技术涉及到连铸生产复合金属板坯、方坯的方法。
将1550℃的普通钢水加入连铸机的普通钢水中间包中,经出钢口过滤砖过滤后由浸入式出钢口送入普通钢水结晶器,经冷却得到普通板坯或方坯钢坯,由普通钢坯大面及小面夹送辊护送向下运动,穿过高频中间加热器,对普通钢坯外表面加热至1250℃-1300℃,然后再穿过感应式复合钢水中间包,使普通钢坯外表面加热至1300℃-1350℃,与复合钢水一起进入复合钢坯结晶器,使普通钢坯外表面复合10-20mm复合钢金属层,复合钢与普通钢坯熔焊成一体成为复合钢坯,在复合钢坯大面及小面夹送辊拉拔下经二次冷却后定尺切断即制成复合金属板坯或方坯产品。
该技术具有工艺简单、设备投资少、生产成本低、产品质量好、适合大规模生产的优点及效果。
权利要求书1.一种连铸生产复合金属板坯、方坯的方法,其特征在于它按下述步骤进行:先将1550℃的普通钢水加入连铸机的普通钢水中间包(1)中,经出钢口过滤砖(2)过滤后的普通钢水由浸入式出钢口(3)送入板坯或方坯的普通钢水结晶器(4),经冷却后得到普通板坯或方坯钢坯(5),从普通钢水结晶器的出钢口出来的普通钢坯由普通钢坯大面夹送辊(6)和普通钢坯小面夹送辊(7)护送向下运动,直到普通钢坯完全结晶后进入高频中间加热器(9),快速对普通钢坯外表面高频加热至1250℃-1300℃,然后再穿过感应式复合钢水中间包(10),该中间包装有复合钢水(11),钢水深度为600-700mm,温度为1650℃-1680℃,感应式复合钢水中间包的感应加热和钢水导热使被复合的普通钢坯外表面加热至1300℃-1350℃,与复合钢水一起从包底进入复合钢坯结晶器(13),使普通钢坯外表面复合10-20mm 复合钢金属层(15),复合钢与普通钢坯熔焊成一体成为复合钢坯,在复合钢坯大面夹送辊(16)、复合钢坯小面夹送辊(17)的拉拔下经二次冷却后定尺寸切断即制成复合金属板坯或方坯产品。
2.一种连铸生产复合金属板坯、方坯的连铸机,它由普通钢水中间包(1)、普通钢水结晶器(4)、普通钢坯大面夹送辊(6)、普通钢坯小面夹送辊(7)、主机架(8)、高频中间加热器(9)、感应式复合钢水中间包(10)、复合钢水结晶器(13)、复合钢坯大面夹送辊(16)、复合钢坯小面夹送辊(17)组成,其特征在于:a)高频中间加热器由外壳(18)、托盘(19)和支架(20)组成,外壳由耐火材料和感应线圈组成,托盘为水冷式结构,通过支架固定在主机架上;b)感应式复合钢水中间包由壳体(21)、内腔(22)、托盘(23)、出渣口(24)和出钢口插板(12)组成,壳体由耐火材料和感应线圈组成,壳体上方为出渣口,在内腔的下出口装有出钢口插板,通过调整四块插板的距离来控制复合钢水的流量,托盘为水冷式结构,通过支架固定在主机架上。
安钢1780mm热连轧生产线的工艺及设备

2011.0280安钢1780mm 热连轧生产线的工艺及设备魏宏武(安阳钢铁股份有限公司第二炼轧厂,河南 安阳 455004)摘要:安阳钢铁股份有限公司建设了一跳集炼钢,炉外精炼,连铸和轧钢四位一体的先进生产线,取得良好的效果,文章基于此介绍了安阳钢铁公司第二炼轧厂1780mm 热连轧生产线的产品结构和主要工艺设备及其特点。
关键词:1780mm 热连轧; 安钢;粗轧机;精轧机;卷取区;精整区中图分类号:TG333 文献标识码:A 文章编号:1009-2374(2011)34-0080-02一、概述安阳钢铁股份有限公司(以下简称安钢)2005年对原有无缝钢管厂、薄板厂进行搬迁改造,目前正在建设一条集炼钢、炉外精炼、连铸和轧钢四位于一体的具有当今世界先进水平的1780热连轧生产线,是安钢“三步走”发展规划的关键项目,并于2007年6月轧出第一卷钢。
该生产线分两期建设,一期已建成投入使用2座步进式加热炉、1架带立辊的四辊可逆式粗轧机、1台转鼓式飞剪、7架四辊精轧机、2台卷取机,年产量为200万t/a;二期现已增建1座步进式加热炉、1台带立辊的二辊可逆式粗轧机、1台卷取机,年产量为400万t/a,并在钢卷库增设一条平整分卷机组,其年产量为80万t/a。
产品规格:带钢厚度1.2~19mm,带钢宽度800~1630mm,钢卷内径φ762mm,钢卷外径φ2150mm,最大卷重32t,钢卷单重 19.8kg/mm。
生产钢种有普通碳素结构钢、优质碳素结构钢、管线钢、低合金结构钢、低碳钢和超低碳钢。
二、主要工艺及设备(一)工艺流程其主要生产工艺流程为:炼钢→炉外精炼(LF、VD )→连铸→热装(冷装)→加热→粗除鳞→E1/R1粗轧机→E2/R2粗轧机→中间坯保护罩→切头剪→精除鳞→F1-F7精轧机→层流冷却→卷取机→打捆机→打号机→步进梁式运输机→入库。
(二)加热炉主要工艺设备热连轧加热炉上料辊道与连铸坯辊道直接连接,采用了板坯热送热装工艺、汽化冷却工艺和最佳燃烧控制模型。
长钢连铸设备及生产工艺

长钢连铸设备及生产工艺流程1长钢H型钢生产工艺流程图转炉出钢LF精炼钢包回转中间包修砌中间包烘烤中间包结晶器组装结晶器试压结晶器二次冷却拉矫机火焰切割机推钢机辊道输送铸坯提升输送机冷床及拉钢机热送至轧钢车间铸坯堆放2长钢H型钢连铸机主要工艺参数1机型:4机4流链式引锭杆全弧形连铸机2弧形半径:R10/15/30m(连铸矫直)3流间距:1800m4浇注断面 BB1:430*300*85mmBB2: 292*205*85mm5尺定:5.25~12m6结晶器:采用板式组合结晶器,铜板长700mm7结晶器振动方式:短臂四连杆震动装置,振幅:3~8m ;震频60~80次/分;9剪切机形式:自动火焰切割10浇注钢种:碳素结构钢Q235;桥梁结构钢Q3453连铸对钢水的要求1钢水P,S成分应达到以下要求2温度控制精炼后温度(未进入LF炉)3其他要求●每炉喂入120m硅钙线,底吹氩时间大于5分钟●钢水吊至平台前,向钢包中加入覆盖剂,保证钢水液面不裸露●钢水吹氩,喂丝后至开浇前时间不大于15分钟4长钢连铸主要设备及功能1钢包回转台功能:在浇注过程中起快速更换钢包的作用;测量钢包钢水重量;升降钢包方便引流;在事故中,可及时把钢包旋转到事故钢包的上方达到安全生产。
(事故回转180°所需时间30s)2中间包车功能:用于运送中间包,并支持中间包浇注。
特点:全悬式,单轮驱动3结晶器功能:结晶器安装在结晶器振动台架上,由交流电动机驱动齿轮减速机、偏心振动装置和四连杆机构,使结晶器得到上下方向均匀的振动;振幅则是通过更换偏心套而改变的。
频率由变频器控制。
4拉矫机功能:拉矫机用于浇铸期间拉出热钢坯,同时将铸坯从弧曲面矫直送入中间辊道;在浇铸准备期间用于将引锭链经二次水冷导向插入结晶器中和结晶管道形成铸型。
特点:五辊杠上驱动,气缸压紧交流变频调速直传动,辊为冷;拉坯速度:2~4.1m/min 5引锭杆功能:把切断后和铸坯分离的引锭链移出辊道存放起来,准备下次浇铸时再用。
连铸连轧工艺及设备
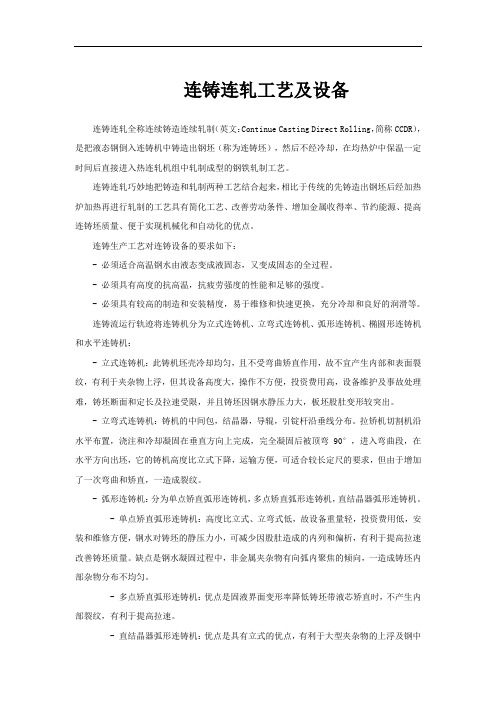
连铸连轧工艺及设备连铸连轧全称连续铸造连续轧制(英文:Continue Casting Direct Rolling,简称CCDR),是把液态钢倒入连铸机中铸造出钢坯(称为连铸坯),然后不经冷却,在均热炉中保温一定时间后直接进入热连轧机组中轧制成型的钢铁轧制工艺。
连铸连轧巧妙地把铸造和轧制两种工艺结合起来,相比于传统的先铸造出钢坯后经加热炉加热再进行轧制的工艺具有简化工艺、改善劳动条件、增加金属收得率、节约能源、提高连铸坯质量、便于实现机械化和自动化的优点。
连铸生产工艺对连铸设备的要求如下:- 必须适合高温钢水由液态变成液固态,又变成固态的全过程。
- 必须具有高度的抗高温,抗疲劳强度的性能和足够的强度。
- 必须具有较高的制造和安装精度,易于维修和快速更换,充分冷却和良好的润滑等。
连铸流运行轨迹将连铸机分为立式连铸机、立弯式连铸机、弧形连铸机、椭圆形连铸机和水平连铸机:- 立式连铸机:此铸机坯壳冷却均匀,且不受弯曲矫直作用,故不宜产生内部和表面裂纹,有利于夹杂物上浮,但其设备高度大,操作不方便,投资费用高,设备维护及事故处理难,铸坯断面和定长及拉速受限,并且铸坯因钢水静压力大,板坯股肚变形较突出。
- 立弯式连铸机:铸机的中间包,结晶器,导辊,引锭杆沿垂线分布。
拉矫机切割机沿水平布置,浇注和冷却凝固在垂直方向上完成,完全凝固后被顶弯90°,进入弯曲段,在水平方向出坯,它的铸机高度比立式下降,运输方便,可适合较长定尺的要求,但由于增加了一次弯曲和矫直,一造成裂纹。
- 弧形连铸机:分为单点矫直弧形连铸机,多点矫直弧形连铸机,直结晶器弧形连铸机。
- 单点矫直弧形连铸机:高度比立式、立弯式低,故设备重量轻,投资费用低,安装和维修方便,钢水对铸坯的静压力小,可减少因股肚造成的内列和偏析,有利于提高拉速改善铸坯质量。
缺点是钢水凝固过程中,非金属夹杂物有向弧内聚焦的倾向,一造成铸坯内部杂物分布不均匀。
- 多点矫直弧形连铸机:优点是固液界面变形率降低铸坯带液芯矫直时,不产生内部裂纹,有利于提高拉速。
- 1、下载文档前请自行甄别文档内容的完整性,平台不提供额外的编辑、内容补充、找答案等附加服务。
- 2、"仅部分预览"的文档,不可在线预览部分如存在完整性等问题,可反馈申请退款(可完整预览的文档不适用该条件!)。
- 3、如文档侵犯您的权益,请联系客服反馈,我们会尽快为您处理(人工客服工作时间:9:00-18:30)。
图片简介:本技术介绍了一种长材直接轧制铸坯保温装置、生产线及方法,属于钢铁冶金工业长材直接轧制技术领域,本铸坯保温装置包括设于箱体上的推钢机构、悬臂辊道、电加热装置和步进梁结构,步进梁结构包括活动梁和固定梁。
本铸坯保温生产线包括依次设置的炼钢炉、连铸机、拉矫机、定尺剪、并流辊道、铸坯保温装置、电磁感应补热装置和轧制线。
本技术通过在连铸并流辊道后设置铸坯保温装置,当因轧线短时故障导致连铸坯无法生产时,连铸坯进入铸坯保温装置进行保温,待故障处理完成后,铸坯保温装置中连铸坯通过其内的步进梁结构出钢并经电感应补热后进行轧制,整个生产过程中除少量头尾坯外,无连铸坯下线,提高了长材直接轧制生产线的直轧率及成材率。
技术要求1.一种长材直接轧制铸坯保温装置,其特征在于,所述铸坯保温装置(6)包括设于箱体(66)上的推钢机构(61)、悬臂辊道(62)、电加热装置(63)和步进梁结构,所述步进梁结构包括活动梁(64)和固定梁(65)。
2.根据权利要求1所述的长材直接轧制铸坯保温装置,其特征在于,所述电加热装置布置于箱体内侧的顶部、侧面及底部,采用电阻加热器。
3.根据权利要求1所述的长材直接轧制铸坯保温装置,其特征在于,所述箱体外侧的顶部及侧面设有纤维模块的保温盖,底部设有耐火隔热砖。
4.一种长材直接轧制铸坯保温生产线,包括依次设置的炼钢炉(1)、连铸机(2)、拉矫机(3)、定尺剪(4)、并流辊道(5)、电磁感应补热装置(7)和轧制线(8),其特征在于,在并流辊道与电磁感应补热装置之间设有如权利要求1-3任一项所述的铸坯保温装置(6),所述连铸机的水平段辊道和定尺剪后的输送辊道均采用保温辊道。
5.根据权利要求4所述的长材直接轧制铸坯保温生产线,其特征在于,还包括横移台架,设于铸坯保温装置与电磁感应补热装置之间,或设于铸坯保温装置上。
6.根据权利要求5所述的长材直接轧制铸坯保温生产线,其特征在于,所述横移台架的上方设置保温罩。
7.根据权利要求4所述的长材直接轧制铸坯保温生产线,其特征在于,所述定尺剪后的输送辊道的辊面速度为180m/min~300m/min。
8.根据权利要求4所述的长材直接轧制铸坯保温生产线,其特征在于,所述电磁感应补热装置具备温度闭环控制。
9.根据权利要求4所述的长材直接轧制铸坯保温生产线,其特征在于,所述铸坯保温装置里的连铸坯在一小时内温降≤100℃,两小时内温降≤200℃。
10.一种长材直接轧制铸坯保温生产方法,包括将铸坯依次经多流连铸、定尺切割、并流、电磁感应补热、轧制、冷却收集,其特征在于,采用如权利要求4-9任一项所述的生产线,所述生产方法还包括:在连铸的水平段辊道和定尺切割后的输送辊道采用保温输送,且在连铸及轧制故障时,连铸机至轧制前的连铸坯进入铸坯保温装置进行保温,并故障排除后,首先推出铸坯保温装置内的连铸坯。
技术说明书一种长材直接轧制铸坯保温装置、生产线及方法技术领域本技术属于钢铁冶金工业长材直接轧制技术领域,具体涉及一种长材直接轧制铸坯保温装置、生产线及方法。
背景技术线棒材作为钢铁行业的重要产品之一,应用广泛。
目前棒线材生产方法主要是采用多流连铸机生产出小方坯或小圆坯,将铸坯切割后通过热送辊道送到加热炉,加热炉将铸坯加热后送至轧机进行轧制。
具体工艺流程如下:连铸机→拉矫机→切割机→运输辊道→移钢机→分钢机→热送辊道→加热炉台架→加热炉→粗轧机组→中轧机组→精轧机组→收集装置。
其中,多流铸坯需通过移钢机分批移送至分钢机台架上,再由分钢机逐根放置到热送辊道上,通过热送辊道运输至加热炉进行加热,加热完毕后送至轧钢车间进行轧制。
该生产方法存在较多的问题和不足:1)生产流程长、温度损失高;2)若直接热送,到轧机入口时温度太低导致轧机功率大幅增加。
随着我国对能源、环保要求提高,各专家学者提出了多种方法,如免加热轧制技术,无头连铸连轧技术,如图1、2所示。
针对免加热轧制技术,技术专利“一种线棒材连铸坯免加热直轧系统及方法”(CN106180191B)提出了线棒材连铸坯免加热直轧系统及方法,包括依次紧密设置的连铸机、快速定尺剪、切后辊道、铸坯流汇聚辊道、运输热送辊道和线棒材轧机;所述铸坯流汇聚辊道将每一流上的铸坯汇聚到运输热送辊道上,所述切后辊道与铸坯流汇聚辊道之间设置有用于阻挡铸坯进入和放行的闸门机构。
本技术连铸机高效连铸,铸坯拉出温度高,形状规整,温度损失小,铸坯剪断快速,铸坯起始温度高。
通过闸门机构,剪断的铸坯依次有序进入高速铸坯流汇聚辊道,操作简便,易组织生产。
铸坯到轧机入口温度高,可免加热直接轧制,对轧机损伤小。
但无法解决连铸工序及轧钢工序出现故障时,因等待产生的连铸坯废坯问题。
技术专利“一种无加热低温轧制小方坯生产钢筋的装置及其生产方法”(CN103480647A)虽然取消了加热炉,但该装置采用连铸坯多排并行、再由横向调配装置分钢后单根送入热送辊道的方式,会造成后进入热送辊道的连铸坯等待时间过长而温降过大,并且由于需要横移分钢,也增加了连铸坯的冷却时间,可见该装置与目前常用的热送热装技术并无本质区别,连铸坯温降过大,无法满足轧机的轧制要求,不具有可行性。
技术专利“用于生产棒线材和型材的连铸-直接轧制装置及方法”(CN104550237A)提出了型材棒线材的连铸连轧方法,但由于坯料由连铸机至粗轧机组,只是采用保温罩进行保温,至粗轧机组铸坯表层温度会降至900℃左右,芯部温度也只有950℃,无法实现优特钢轧制要求,且由于连铸与长材轧钢界面衔接问题,直轧率不高,导致产线产量不高。
针对无头连铸连轧技术,技术专利“利用钢水余热生产型材棒线材的连铸连轧方法”(CN102310078A)提出了利用钢水余热生产型材棒线材的连铸连轧方法,实现型材棒线材生产的低消耗和二氧化碳的低排放,但由于受目前连铸水平限制,单条产线产量不高,采用多流生产时轧机过多,投资过大。
达涅利基于其高速连铸技术,采用MIDA方案,实现连铸连轧,但目前均为投产,且单条产线产量较低,投资及运营性价比不高因此有必要设计一种长材直接轧制生产线,以克服上述问题。
技术内容针对目前线棒材生产中存在的问题,本技术提供一种长材直接轧制铸坯保温装置、生产线及方法,在连铸并流辊道出口设置铸坯保温装置,当因短时轧制及连铸故障时,可使连铸机、连铸辊道、轧前辊道的连铸坯进入铸坯保温装置进行保温,待产线故障恢复后,保温装置的连铸坯可继续生产,由于无温降,无连铸坯下线问题,其提高了直接轧制生产线直轧率,提高了成材率,降低能源消耗,无碳排放,同时可提高收益。
本技术是通过以下技术方案来实现的:本技术提供的一种长材直接轧制铸坯保温装置,所述铸坯保温装置包括设于箱体上的推钢机构、悬臂辊道、电加热装置和步进梁结构,所述步进梁结构包括活动梁和固定梁。
进一步,所述电加热装置布置于箱体内侧的顶部、侧面及底部,采用电阻加热器。
进一步,所述箱体外侧的顶部及侧面设有纤维模块的保温盖,底部设有耐火隔热砖。
本技术还提供一种长材直接轧制铸坯保温生产线,包括依次设置的炼钢炉、连铸机、拉矫机、定尺剪、并流辊道、电磁感应补热装置和轧制线,还在并流辊道与电磁感应补热装置之间设有上述的铸坯保温装置,所述连铸机的水平段辊道和定尺剪后的输送辊道均采用保温辊道。
优选的,还包括横移台架,设于铸坯保温装置与电磁感应补热装置之间,或设于铸坯保温装置上。
优选的,所述横移台架的上方设置保温罩。
优选的,所述定尺剪后的输送辊道的辊面速度为180m/min~300m/min。
优选的,所述电磁感应补热装置具备温度闭环控制。
优选的,所述铸坯保温装置里的连铸坯在一小时内温降≤100℃,两小时内温降≤200℃。
本技术还提供一种长材直接轧制铸坯保温生产方法,包括将铸坯依次经多流连铸、定尺切割、并流、电磁感应补热、轧制、冷却收集,还在连铸的水平段辊道和定尺切割后的输送辊道采用保温输送,且在连铸及轧制故障时,连铸机至轧制前的连铸坯进入铸坯保温装置进行保温,并故障排除后,首先推出铸坯保温装置内的连铸坯。
本技术的优点在于:1、本技术通过在连铸并流辊道后设置铸坯保温装置,当因轧线短时故障导致连铸坯无法生产时,连铸坯进入铸坯保温装置进行保温,该铸坯保温装置具备电加热功能,减少碳排放,待产线故障处理完成后,铸坯保温装置中连铸坯通过其内的步进梁结构出钢并经电感应补热后进行轧制,整个生产过程中除少量头尾坯外,无连铸坯下线,提高了长材直接轧制生产线的直轧率(高达99.5%)及成材率。
2、本技术工艺布置简单,解决长材直接轧制生产线连铸坯下线问题,大大提高直接轧制直轧率,投资及运行成本低,易于实现工业化生产,具有明显的经济效益。
3、本技术采用高速连铸技术进行多流连铸,保证连铸机小时产量,进而保证生产线产量;通过连铸流数与轧线产量及小时产量进行匹配。
4、本技术的多流连铸坯经定尺剪切割后,进行连铸坯定尺,考虑连铸速度及连铸坯头尾温差,对连铸坯进行定尺,连铸坯头尾温差较小,保证后续轧钢过程中连铸坯头尾及芯表温差小,降低轧件性能差异。
5、本技术的连铸坯浇铸时水平段辊道及定尺切割后的输送辊道采用保温辊道,同时定尺剪切割后连铸坯采用快速辊道,以保证连铸坯进快进入后续工序,减小连铸坯运行过程中的头尾温差。
6、本技术配有电磁感应补热装置,根据连铸坯温度进行补温,电磁感应补热具备闭环功能,加热后连铸坯温度稳定,头尾温差小。
7、本技术连铸坯经轧机轧制后,可实现控轧控冷工艺,实现长材(包含线棒材)生产,产品质量好,合金成本低。
本技术的其他优点、目标和特征在某种程度上将在随后的说明书中进行阐述,并且在某种程度上,基于对下文的考察研究对本领域技术人员而言将是显而易见的,或者可以从本技术的实践中得到教导。
本技术的目标和其他优点可以通过下面的说明书来实现和获得。
附图说明为了使本技术的目的、技术方案和优点更加清楚,下面将结合附图对本技术作进一步的详细描述,其中:图1为典型免加热线棒材生产线工艺布置简图;图2为典型无头连铸连轧线棒材生产线工艺布置简图;图3为本技术直接轧制线棒材生产线实施例布置简图;图4为本技术直接轧制铸坯保温装置;图5为本技术直接轧制铸坯保温装置的步进梁结构简图;图6为本技术直接轧制铸坯保温装置的电加热结构简图;图7为本技术直接轧制连铸坯温度模拟计算值;元件标号说明:炼钢炉1、连铸机2、拉矫机3、定尺剪4、并流辊道5、铸坯保温装置6、电磁感应补热装置7、轧制线8;推钢机构61、悬臂辊道62、电加热装置63、活动梁64、固定梁65、箱体66。
具体实施方式以下通过特定的具体实例说明本技术的实施方式,本领域技术人员可由本说明书所揭露的内容轻易地了解本技术的其他优点与功效。
本技术还可以通过另外不同的具体实施方式加以实施或应用,本说明书中的各项细节也可以基于不同观点与应用,在没有背离本技术的精神下进行各种修饰或改变。