金属的压缩实验
金属材料压缩实验报告

金属材料压缩实验报告金属材料压缩实验报告摘要:本实验旨在研究金属材料在不同压力下的变形行为。
通过对不同金属材料的压缩实验,测量其应力-应变曲线,分析材料的强度、塑性和变形机制。
实验结果表明,金属材料在受力时会发生塑性变形,而不同材料的变形行为受其晶体结构和成分的影响。
引言:金属材料是工程领域中常用的结构材料之一,其力学性能对于设计和制造具有重要意义。
了解金属材料在受力时的变形行为,可以帮助我们更好地选择和设计材料,提高结构的可靠性和安全性。
本实验通过金属材料的压缩实验,探究材料的变形行为和力学性能。
实验方法:1. 实验材料的选择:选择不同类型的金属材料,如铝、铜和钢等,以研究它们的变形行为。
2. 实验装置的搭建:搭建压力机实验装置,将金属试样放置在压力机上,并固定好。
3. 实验参数的设置:设置不同的压力值,如50MPa、100MPa和150MPa等,控制实验的变量。
4. 实验数据的采集:通过应变计和应力计等传感器,测量金属试样在不同压力下的应变和应力值。
5. 数据处理和分析:根据采集到的数据,绘制应力-应变曲线,并分析材料的强度和塑性等力学性能。
实验结果:将实验数据进行统计和分析后,得到了不同金属材料的应力-应变曲线。
曲线的斜率代表了材料的弹性模量,而曲线的形状则反映了材料的塑性变形行为。
铝材料的应力-应变曲线呈现出明显的线性关系,表明其具有较高的弹性模量。
当压力增加时,铝材料开始发生塑性变形,应变值逐渐增加。
这是由于铝材料的晶体结构具有较高的可滑移性,容易发生晶格滑移而导致塑性变形。
铜材料的应力-应变曲线也呈现出线性关系,但相比铝材料,其弹性模量略低。
随着压力的增加,铜材料的应变值也逐渐增加,但相对于铝材料,铜材料的塑性变形更加明显。
这是由于铜材料的晶体结构具有较大的晶体滑移平面密度,使得其塑性变形更容易发生。
钢材料的应力-应变曲线呈现出两个明显的阶段。
在较低的压力下,钢材料表现出线性弹性行为,应力和应变成正比。
金属压缩实验报告
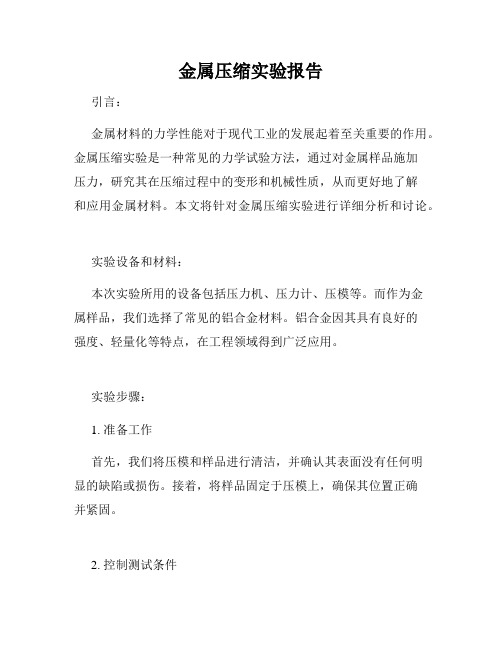
金属压缩实验报告引言:金属材料的力学性能对于现代工业的发展起着至关重要的作用。
金属压缩实验是一种常见的力学试验方法,通过对金属样品施加压力,研究其在压缩过程中的变形和机械性质,从而更好地了解和应用金属材料。
本文将针对金属压缩实验进行详细分析和讨论。
实验设备和材料:本次实验所用的设备包括压力机、压力计、压模等。
而作为金属样品,我们选择了常见的铝合金材料。
铝合金因其具有良好的强度、轻量化等特点,在工程领域得到广泛应用。
实验步骤:1. 准备工作首先,我们将压模和样品进行清洁,并确认其表面没有任何明显的缺陷或损伤。
接着,将样品固定于压模上,确保其位置正确并紧固。
2. 控制测试条件在开始实验之前,我们需要确定实验所需的测试条件,包括压力的范围、测试速率等。
这些条件将直接影响到实验结果的准确性。
在确定好条件后,将其输入到压力机中进行调节。
3. 进行实验根据所设定的测试条件,我们将开始进行金属压缩实验。
通过操纵压力机的操作杆,施加逐渐增加的压力于样品上,同时用压力计记录下实时的压力数值。
实验过程中,我们需要关注样品的变形情况并进行记录。
实验结果:根据实验所得的数据,我们可以得到金属压缩实验的结果。
通过分析实验数据,我们可以得到以下结论。
1. 压力-变形曲线根据实验数据绘制压力-变形曲线,我们可以观察到压力与金属样品的变形之间的关系。
在开始时,随着压力的增加,金属样品的变形量增加较为缓慢。
当压力超过一定阈值后,样品的变形速率开始急剧增加。
2. 压缩方式通过观察样品的实际形变,我们可以了解金属在压缩过程中所经历的变形方式,如拉伸、弯曲等。
这有助于我们理解金属材料的力学性质,并为进一步研发新材料提供参考。
3. 材料性能通过分析实验数据,我们可以得到样品的应力-应变曲线,进一步计算出材料的屈服强度、抗拉强度等力学性能指标。
这些性能指标可以反映出金属样品的力学特性,对于材料的选用和工程应用具有重要意义。
实验意义:金属压缩实验是研究金属材料力学性质的重要手段之一。
实验3-金属材料的压缩实验

实验三 金属材料的压缩实验一、实验目的1.测定低碳钢(Q235 钢)的压缩屈服点sc σ和铸铁的抗压强度bc σ。
2.观察、分析、比较两种材料在压缩过程中的各种现象。
二、设备和仪器1.WES-600S 型电液式万能试验机。
2.游标卡尺。
三、试样采用1525ϕ⨯(名义尺寸)的圆柱形试样。
四、实验原理低碳钢(Q235 钢)试样压缩图如图3-1b 所示。
试样开始变形时,服从胡克定律,呈直线上升,此后变形增长很快,材料屈服。
此时载荷暂时保持恒定或稍有减小,这暂时的恒定值或减小的最小值即为压缩屈服载荷F SC 。
有时屈服阶段出现多个波峰波谷,则取第一个波谷之后的最低载荷为压缩屈服载荷F SC 。
尔后图形呈曲线上升,随着塑性变形的增长,试样横截面相应增大,增大了的截面又能承受更大的载荷。
试样愈压愈扁,甚至可以压成薄饼形状(如图3-1a 所示)而不破裂,因此测不出抗压强度。
铸铁试样压缩图如图3-2a 所示。
载荷达最大值F bc 后稍有下降,然后破裂,能听到沉闷的破裂声。
铸铁试样破裂后呈鼓形,破裂面与轴线大约成45o,这主要是由切应力造成的。
图3-1 低碳钢试样压缩图 图3-2 铸铁试样压缩图五、实验步骤1.测量试样尺寸用游标卡尺在试样高度重点处两个相互垂直的方向上测量直径,取其平均值,记录数据。
2.开机打开试验机及计算机系统电源。
3.实验参数设置按实验要术,通过试验机操作软件设量试样尺寸等实验参数。
4.测试通过试验机操作软件控制横梁移动对试样进行加载,开始实验。
实验过程中注意曲线及数字显示窗口的变化。
实验结束后,应及时记求并保存实验数据。
5.实验数据分析及输出根据实验要求,对实验数据进行分析,通过打印机输出实验结果及曲线。
6.断后试样观察及测量取下试样,注意观察试样的断口。
根据实验要求测量试样的延伸率及断面收缩率 7.关机关闭试验机和计算机系统电源。
清理实验现场.将相关仪器还原。
六、实验结果处理1. 参考表3-1记录实验原始数据。
金属材料压缩实验报告

一、实验目的1. 了解金属材料在压缩载荷作用下的力学行为。
2. 测定金属材料的屈服极限、抗压强度和弹性模量。
3. 比较不同金属材料的压缩性能。
二、实验原理金属材料在压缩过程中,其应力与应变之间存在一定的关系。
根据胡克定律,在弹性阶段,应力与应变呈线性关系。
当超过弹性极限后,应力与应变的关系变为非线性,此时材料将发生塑性变形或断裂。
屈服极限是材料开始出现塑性变形时的应力值,抗压强度是材料在压缩过程中能承受的最大应力值。
三、实验仪器与材料1. 万能试验机2. 游标卡尺3. 金属材料试样(低碳钢、铸铁等)四、实验步骤1. 准备试样:将金属材料试样加工成圆柱形,确保试样表面平整,无划痕、锈蚀等缺陷。
2. 测量试样尺寸:使用游标卡尺测量试样的高度和直径,精确到0.01mm。
3. 安装试样:将试样放置在万能试验机的上下压盘之间,确保试样中心线与试验机中心线重合。
4. 设置试验参数:根据试样材料和试验要求,设置试验机的加载速度、加载范围等参数。
5. 进行试验:启动试验机,使试样受到压缩载荷,观察试样变形和破坏情况。
6. 记录数据:记录试样在压缩过程中的应力、应变、变形等数据。
五、实验结果与分析1. 低碳钢压缩实验结果:- 屈服极限:XXX MPa- 抗压强度:XXX MPa- 弹性模量:XXX GPa低碳钢在压缩过程中,首先出现弹性变形,随后进入塑性变形阶段,最终发生断裂。
屈服极限和抗压强度反映了低碳钢的压缩性能。
2. 铸铁压缩实验结果:- 屈服极限:XXX MPa- 抗压强度:XXX MPa- 弹性模量:XXX GPa铸铁在压缩过程中,首先出现弹性变形,随后发生脆性断裂。
屈服极限和抗压强度反映了铸铁的压缩性能。
六、实验结论1. 低碳钢和铸铁在压缩过程中均表现出弹性变形和塑性变形阶段,但铸铁的塑性变形较小,更容易发生脆性断裂。
2. 低碳钢的屈服极限和抗压强度高于铸铁,说明低碳钢的压缩性能优于铸铁。
3. 通过压缩实验,可以了解金属材料的力学性能,为工程设计提供参考。
金属材料压缩试验实验报告

金属材料压缩试验实验报告
一、实验目的
本实验旨在用压缩机测试金属材料的压缩性能,掌握其压缩变形特征及相关物理性能,为材料的正确使用提供重要参数依据。
二、实验原理
压缩实验研究材料在压缩荷载作用下的变形特性和失稳破坏特性,在此过程中还可以测量压缩变形过程中的应力应变特性,从而推断材料的压缩强度和塑性性能。
实验装置为压缩机,其主要功能是在特定的负载作用下,实现特定的压缩变形量,观察变形的变化规律及破坏过程,从而推断试样的界面特性和压缩性能。
三、实验方法
1.准备试样:将标准试样安装在压缩机上,确保其垂直放置;
2.测试设置:设定负载范围,设定变形速率,控制变形过程;
3.测量变形:连续测量试样的变形量,记录数据;
4.结果分析:根据测量的变形量,推断材料的压缩强度和塑性性能,结合实验结果,得出确定的实验报告。
四、实验结果
根据本次实验测量的压缩变形结果,金属材料经受压缩时,在荷载折算为0.15MPa时,变形量为0.2mm;在荷载折算为0.50MPa时,变形量为0.4mm;在荷载折算为1.00MPa时,变形量为0.6mm; 在荷载折算为2.00MPa时,变形量为0.8mm。
同时,在压缩变形过程中,没有发现明显的破坏现象。
五、结论
本次实验,金属材料在压缩变形过程中,没有发现明显的破坏现象,可以推算出该材料的压缩强度以及塑性性能,可以满足压缩变形要求。
金属材料的压缩实验
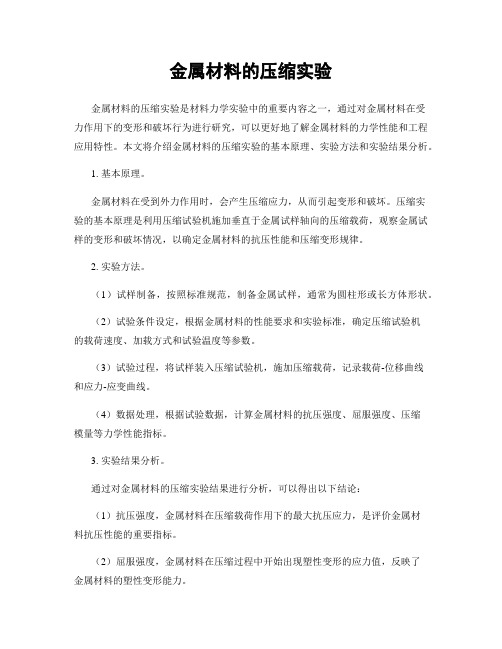
金属材料的压缩实验金属材料的压缩实验是材料力学实验中的重要内容之一,通过对金属材料在受力作用下的变形和破坏行为进行研究,可以更好地了解金属材料的力学性能和工程应用特性。
本文将介绍金属材料的压缩实验的基本原理、实验方法和实验结果分析。
1. 基本原理。
金属材料在受到外力作用时,会产生压缩应力,从而引起变形和破坏。
压缩实验的基本原理是利用压缩试验机施加垂直于金属试样轴向的压缩载荷,观察金属试样的变形和破坏情况,以确定金属材料的抗压性能和压缩变形规律。
2. 实验方法。
(1)试样制备,按照标准规范,制备金属试样,通常为圆柱形或长方体形状。
(2)试验条件设定,根据金属材料的性能要求和实验标准,确定压缩试验机的载荷速度、加载方式和试验温度等参数。
(3)试验过程,将试样装入压缩试验机,施加压缩载荷,记录载荷-位移曲线和应力-应变曲线。
(4)数据处理,根据试验数据,计算金属材料的抗压强度、屈服强度、压缩模量等力学性能指标。
3. 实验结果分析。
通过对金属材料的压缩实验结果进行分析,可以得出以下结论:(1)抗压强度,金属材料在压缩载荷作用下的最大抗压应力,是评价金属材料抗压性能的重要指标。
(2)屈服强度,金属材料在压缩过程中开始出现塑性变形的应力值,反映了金属材料的塑性变形能力。
(3)压缩模量,金属材料在弹性阶段的应力-应变比值,描述了金属材料在受力作用下的刚度和变形能力。
4. 实验应用。
金属材料的压缩实验结果对材料的工程应用具有重要意义,可以指导材料的选用和设计,提高工程结构的安全可靠性和使用性能。
此外,还可以为金属材料的加工工艺和成形工艺提供科学依据,优化工艺参数,提高生产效率和产品质量。
5. 结语。
通过对金属材料的压缩实验的介绍,我们可以更好地了解金属材料的力学性能和工程应用特性,为材料科学研究和工程实践提供参考和指导。
希望本文能对相关领域的研究和实践工作有所帮助,促进金属材料领域的发展和进步。
金属压缩实验报告

金属压缩实验报告金属压缩实验报告引言:金属是一种常见的材料,广泛应用于工业生产和日常生活中。
了解金属的物理性质对于优化金属材料的使用具有重要意义。
本次实验旨在通过金属压缩实验,探究金属在不同条件下的变形行为及其影响因素。
实验目的:1. 了解金属在压缩过程中的变形行为;2. 探究金属的变形特性与压缩力、温度等因素的关系;3. 分析金属的力学性质,如屈服强度、抗拉强度等。
实验材料和仪器:1. 实验材料:铝合金、钢材等;2. 实验仪器:万能试验机、温度计、测量尺等。
实验步骤:1. 准备工作:a. 清洁实验材料,确保表面无杂质;b. 标定万能试验机,确保准确测量压缩力;c. 温度计校准,确保测量温度的准确性。
2. 实验设计:a. 选择不同金属材料进行压缩实验;b. 设定不同压缩力和温度条件,进行多组实验。
3. 实验操作:a. 将待测金属样品放置在万能试验机上;b. 设定初始压缩力和温度,开始实验;c. 记录每次实验的压缩力、温度和变形情况;d. 重复实验,获取更多数据。
实验结果与讨论:1. 压缩力与变形行为的关系:实验结果表明,随着压缩力的增加,金属材料的变形程度逐渐增加。
当压缩力达到一定值时,金属开始出现塑性变形,即不可逆变形。
这表明压缩力是影响金属变形的重要因素。
2. 温度对金属变形的影响:实验结果显示,温度对金属的变形行为有显著影响。
在较低温度下,金属的变形主要表现为弹性变形,而在较高温度下,金属更容易发生塑性变形。
这是因为高温下金属的晶格结构更容易发生位错滑移,从而导致塑性变形的发生。
3. 力学性质的分析:通过实验数据的分析,可以计算出金属的屈服强度、抗拉强度等力学性质。
这些性质可以用来评估金属材料的可靠性和适用性,并为工程设计提供参考。
结论:通过金属压缩实验,我们了解了金属在不同条件下的变形行为及其影响因素。
压缩力和温度是影响金属变形的重要因素,而力学性质的分析则可以评估金属材料的性能。
这些实验结果对于优化金属材料的使用和设计具有重要意义,为工业生产和日常生活中金属材料的应用提供了科学依据。
金属材料的压缩实验
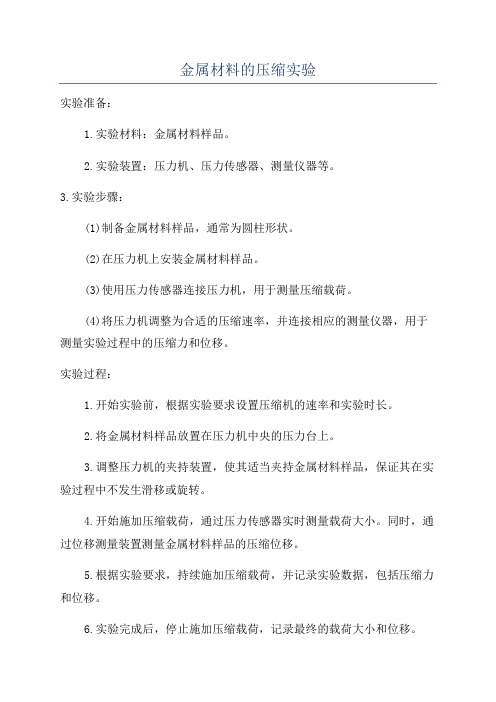
金属材料的压缩实验
实验准备:
1.实验材料:金属材料样品。
2.实验装置:压力机、压力传感器、测量仪器等。
3.实验步骤:
(1)制备金属材料样品,通常为圆柱形状。
(2)在压力机上安装金属材料样品。
(3)使用压力传感器连接压力机,用于测量压缩载荷。
(4)将压力机调整为合适的压缩速率,并连接相应的测量仪器,用于测量实验过程中的压缩力和位移。
实验过程:
1.开始实验前,根据实验要求设置压缩机的速率和实验时长。
2.将金属材料样品放置在压力机中央的压力台上。
3.调整压力机的夹持装置,使其适当夹持金属材料样品,保证其在实验过程中不发生滑移或旋转。
4.开始施加压缩载荷,通过压力传感器实时测量载荷大小。
同时,通过位移测量装置测量金属材料样品的压缩位移。
5.根据实验要求,持续施加压缩载荷,并记录实验数据,包括压缩力和位移。
6.实验完成后,停止施加压缩载荷,记录最终的载荷大小和位移。
实验结果分析:
1.根据实验数据,计算金属材料样品在压缩载荷下的应变。
2.绘制应力-应变曲线,分析金属材料的压缩性能,包括抗压强度、屈服强度、断裂强度等。
3.根据实验结果,研究金属材料的塑性变形行为和变形机制。
4.进一步分析实验结果,评估金属材料在实际应用中的可靠性和适用性。
金属材料的压缩实验是材料力学研究中重要的实验方法之一,通过该实验可以对金属材料的力学性能进行深入研究,为金属材料的设计和应用提供重要的依据。
因此,对金属材料的压缩实验进行深入的研究和分析,对于工程领域的材料选择和优化具有重要意义。
- 1、下载文档前请自行甄别文档内容的完整性,平台不提供额外的编辑、内容补充、找答案等附加服务。
- 2、"仅部分预览"的文档,不可在线预览部分如存在完整性等问题,可反馈申请退款(可完整预览的文档不适用该条件!)。
- 3、如文档侵犯您的权益,请联系客服反馈,我们会尽快为您处理(人工客服工作时间:9:00-18:30)。
金属的压缩实验一、概述实验表明,工程中常用的塑性材料,其受压与受拉时所表现出的强度、刚度和塑性等力学性能是大致相同的。
但广泛使用的脆性材料,其抗压强度很高,抗拉强度却很低。
为便于合理选用工程材料,以及满足金属成型工艺的需要,测定材料受压时的力学性能是十分重要的。
因此,压缩实验同拉伸实验一样,也是测定材料在常温、静载、单向受力下的力学性能的最常用、最基本的实验之一。
二、实验目的1、观测低碳钢压缩时的屈服荷载F SC2、测定铸铁压缩时的抗压强度σbC3、观察并比较低碳钢和铸铁在压缩时的变形和破坏现象。
三、实验设备1、液压式万能材料试验机2、游标卡尺四、试样的制备按照国标GB7314-87《金属压缩试验方法》,金属材料的压缩试样多采用圆柱体,如图2-16所示。
试样长度L=(2.5~3.5)d0的试样适用于测定σpc、σtc、σsc、σbc;L=(5~8)d0的试样适用于测定σpc0.01、E e;L=(1~2)d0的试样适用于测定σbc、。
为了尽量使试样受轴向压力,加工试样时,必须有合理的加工工艺,以保证两端面平行,并与轴线垂直。
σpc-规定非比例压缩应力σtc-规定总压缩应力σsc-压缩屈服点σbc-抗压强度σpc0.01-规定非比例压缩应变为0.01%时的应力E e-压缩弹性模量五、实验原理以低碳钢为代表的塑性材料,轴向压缩时会产生很大的横向变形,但由于试样两端面与试验机支承垫板间存在摩擦力,约束了这种横向变形,故试样中间部分出现显著的鼓胀,如图2-17所示。
塑性材料在压缩过程中的弹性模量、屈服点与拉伸时相同,但在到达屈服阶段时不像拉伸试验时那样明显,因此要仔细观察才能确定屈服载荷F sC。
当继续加载时,试样越压越扁,由于横截面面积不断增大,试样抗压能力也随之提高,曲线持续上升,如图2-18所示。
除非试样过分鼓出变形,导致柱体表面开裂,否则塑性材料将不会发生压缩破坏。
因此,一般不测塑性材料的抗压强度,而通常认为抗压强度等于抗拉强度。
以铸铁为代表的脆性金属材料,由于塑性变形很小,所以尽管有端面摩擦,鼓胀效应却并不明显,而是当应力达到一定值后,试样在与轴线大约成450~550的方向上发生破裂,如图2-20所示。
这是由于脆性材料的抗剪强度低于抗压强度,从而使试样被剪断六、实验步骤1、用游标卡尺测量试样直径,方法是在试样原始标距中点处两个相互垂直的方向上测量直径,并取其算术平均值。
2、根据低碳钢屈服载荷和铸铁抗压强度的估计值, 选择试验机的示力盘,并调整其指针对零。
3、调整好自动绘图器。
4、准确地将试样置于试验机活动平台的支承垫板中心处。
5、调整试验机夹头间距,当试样接近上支承板时,开始缓慢、均匀加载。
6、对于低碳钢试样,将试样压成鼓形即可停止试验。
对于铸铁试样,加载到试样破坏时(主针回摆150左右)立即停止试验,以免试样进一步被压碎。
金属的拉伸实验指导书一、概述常温、静载下的轴向拉伸试验是材料力学试验中最基本、应用最广泛的试验。
通过拉伸试验,可以全面地测定材料的力学性能,如弹性、塑性、强度、断裂等力学性能指标。
这些性能指标对材料力学的分析计算、工程设计、选择材料和新材料开发都有及其重要的作用。
二、实验目的1、测定低碳钢的屈服强度R el、抗拉强度R m、断后延伸率A11.3和断面收缩率Z2、测定铸铁的抗拉强度R m3、观察上述两种材料在拉伸过程中的各种现象,并绘制拉伸图(F─曲线)4、分析比较低碳钢和铸铁的力学性能特点与试样破坏特征三、实验设备及测量仪器1、万能材料试验机2、游标卡尺四、试样的制备试样的制备应按照相关的产品标准或GB/T 2975的要求切取样坯和制备试样。
试验表明,所用试样的形状和尺寸,对其性能测试结果有一定影响。
为了使金属材料拉伸试验的结果具有可比性与符合性,国家已制定统一标准。
依据此标准,拉伸试样分为比例试样和非比例试样两种,试样的横截面形状有圆形和矩形。
这两种试样便于机加工,也便于尺寸的测量和夹具的设计。
本试验所用的拉伸试样是经机加工制成的圆形横截面的长比例试样,即L=10 d。
如图2-10(a)所示。
金属的拉伸实验和§2-8 低碳钢材料弹性模量E的测定章节中所引用的如:R m、R el、A11.3、Z、F、S等符号来自于GB/T 228-2002 《金属室温拉伸实验方法》,代替GB/T 228-1987标准中所引用的σb、σs、δ、Ψ、P、A。
其它章节的符号仍引用原有的标准的符号。
图中L e为试样平行长度,L0为试样原始标距(即测量变形的长度)。
d为圆形试样平行长度部分原始直径。
图2-10 (b)为矩形截面试样,其中a为矩形试样的原始厚度,b为矩形试样平行部分原始宽度,S0为试样平行部分原始横截面面积,r为试样两端较粗部分到平行部分过渡圆弧半径。
拉伸试样由夹持段、过渡段和平行段构成。
试样两端较粗部分为夹持段,其形状和尺寸可根据试验机夹头情况而定。
过渡段常采用圆弧形状,使夹持段与平行段光滑连接。
五、实验原理依据国标GB/T 228-2002《金属室温拉伸实验方法》分别叙述如下:1、低碳钢试样。
在拉伸试验时,利用试验机的自动绘图器可绘出低碳钢的拉伸曲线,见图2-11所示的F—ΔL曲线。
图中最初阶段呈曲线,是由于试样头部在夹具内有滑动及试验机存在间隙等原因造成的。
分析时应将图中的直线段延长与横坐标相交于O点,作为其坐标原点。
拉伸曲线形象的描绘出材料的变形特征及各阶段受力和变形间的关系,可由该图形的状态来判断材料弹性与塑性好坏、断裂时的韧性与脆性程度以及不同变形下的承载能力。
但同一种材料的拉伸曲线会因试样尺寸不同而各异。
为了使同一种材料不同尺寸试样的拉伸过程及其特性点便于比较,以消除试样几何尺寸的影响,可将拉伸曲线图的纵坐标(力F)除以试样原始横截面面积S0,并将横坐标(伸长ΔL)除以试样的原始标距(2)、屈服阶段SK。
当应力超过弹性极限到达锯齿状曲线时,示力盘上的主针暂停转动或开始回转并往复运动,这时若试样表面经过磨光,可看到表征晶体滑移的迹线,大约与试样轴线成450方向。
这种现象表征试样在承受的拉力不继续增加或稍微减少的情况下变形却继续伸长,称为材料的屈服,其应力称为屈服点(屈服应力)。
示力盘的指针首次回转前的最大力(F su上屈服力)或不计初始瞬时效应(不计载荷首次下降的最低点)时的最小力(F sL下屈服力),分别所对应的应力为上、下屈服点。
示力盘的主针回转后所指示的最小载荷(第一次下降后的最小载荷)即为屈服载荷F s。
由于上屈服点受变形速度及试样形状等因素的影响,而下屈服点则比较稳定,故工程中一般只定下屈服点。
屈服应力是衡量材料强度的一个重要指标。
(3)、强化阶段KE。
过了屈服阶段以后,试样材料因塑性变形其内部晶体组织结构重新得到了调整,其抵抗变形的能力有所增强,随着拉力的增加,伸长变形也随之增加,拉伸曲线继续上升。
KE曲线段称为强化阶段,随着塑性变形量的增大,材料的力学性能发生变化,即材料的变形抵抗力提高,塑性降低。
在强化阶段卸载,弹性变形会随之消失,塑性变形将会永久保留下来。
强化阶段的卸载路径与弹性阶段平行,卸载后重新加载时,加载线与弹性阶段平行,重新加载后,材料的比例极限明显提高,而塑性性能会相应下降。
这种现象叫做形变硬化或冷作硬化。
当拉力增加,拉伸曲线到达顶点E时,示力盘上的主针开始返回,而副针所指的最大拉力为F m,由此可求得材料的抗拉强度。
它也是材料强度性能的重要指标。
(4)、局部变形阶段EG(颈缩和断裂阶段)。
对于塑性材料来说,在承受拉力F m以前,试样发生的变形各处基本上是均匀的。
在达到F m以后,变形主要集中于试样的某一局部区域,该处横截面面积急剧减小,这种现象即是“颈缩”现象,此时拉力随着下降,直至试样被拉断,其断口形状呈碗状,如图2-13(a)所示。
试样拉断后,弹性变形立即消失,而塑性变形则保留在拉断的试样上。
利用试样标距内的塑性变形来计算材料的断后延伸率A11.3和断面收缩率Z。
六、实验步骤1、根据试样的形状、尺寸和预计材料的抗拉强度来估算最大拉力,并以此力作为示力盘量程的40%~80%,以选择合适的示力盘和相应的摆锤。
然后,选用与试样相适应的夹具。
2、在试样的原始标距长度L0范围内用划线机等分10个分格线,以便观察标距范围内沿轴向变形的情况和试样破坏后测定断后延伸率。
3、根据国标GB/T 228-2002《金属室温拉伸试验方法》中的规定,测定试样原始横截面积。
本次试验采用圆形试样,应在标距的两端及中间处的两个相互垂直的方向上各测一次横截面直径,取其算术平均值,选用三处测得的直径最小值,并以此值计算横截面面积。
4、安装试样,依据万能材料试验机的操作规程进行操作,将示力盘指针调零,并将自动绘图装置调好。
经指导教师检查后即可开始试验。
5、加载试验,在试验过程中,要求均匀缓慢地进行加载。
对于低碳钢试样的拉伸试验,要注意观察拉伸过程四个阶段中的各种现象。
并记下屈服载荷F el值,最大载荷F m值。
对于铸铁试样,只需测定其最大载荷F m值。
试样被拉断后立即停机,并取下试样。
6、对于拉断后的低碳钢试样,要分别测量断裂后的标距L U和颈缩处的最小直径d U。
测定L U的方法为:将试样断裂后的两段在断口处紧密地对接起来:1)、如果试样断口断在试样中部,直接测量原标距两端的距离作为断后的距。
2)、若断口处到最邻近标距端线的距离小于1/3L0时,则需要用“移位法”来计算L U。
其方法是:在长段上从拉断处O取基本等于短段格数得B点,接着取等于长段所余格数[偶数,图2-15(a)]的一半,得C点;或者取所余格数[奇数,图2-15(b)]分别减1与加1的一半,得C和C1点。
移位后的L1分别为:AB+2BC或者AB+BC+BC1。
测定断面收缩率时,在试样颈缩最小处两个相互垂直的方向上测量其直径d1,取其算术平均值作为d1计算其断面收缩率。