首钢京唐公司1号高炉施工工艺探讨
唐钢中厚板1#高炉改造及施工技术研究
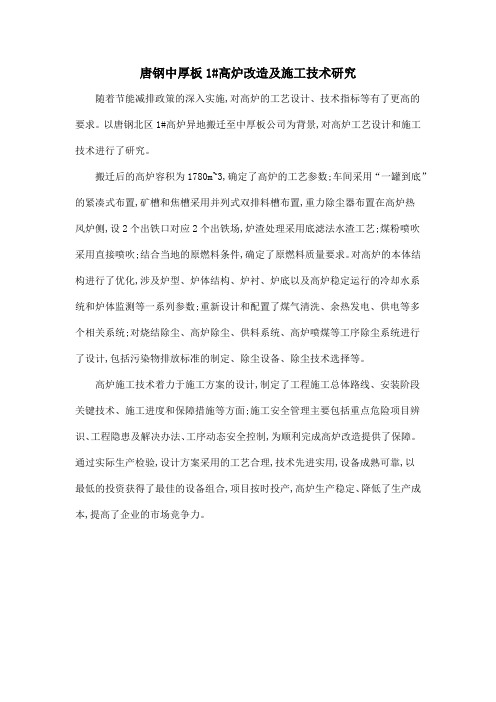
唐钢中厚板1#高炉改造及施工技术研究
随着节能减排政策的深入实施,对高炉的工艺设计、技术指标等有了更高的要求。
以唐钢北区1#高炉异地搬迁至中厚板公司为背景,对高炉工艺设计和施工技术进行了研究。
搬迁后的高炉容积为1780m~3,确定了高炉的工艺参数;车间采用“一罐到底”的紧凑式布置,矿槽和焦槽采用并列式双排料槽布置,重力除尘器布置在高炉热
风炉侧,设2个出铁口对应2个出铁场,炉渣处理采用底滤法水渣工艺;煤粉喷吹采用直接喷吹;结合当地的原燃料条件,确定了原燃料质量要求。
对高炉的本体结构进行了优化,涉及炉型、炉体结构、炉衬、炉底以及高炉稳定运行的冷却水系统和炉体监测等一系列参数;重新设计和配置了煤气清洗、余热发电、供电等多个相关系统;对烧结除尘、高炉除尘、供料系统、高炉喷煤等工序除尘系统进行了设计,包括污染物排放标准的制定、除尘设备、除尘技术选择等。
高炉施工技术着力于施工方案的设计,制定了工程施工总体路线、安装阶段关键技术、施工进度和保障措施等方面;施工安全管理主要包括重点危险项目辨识、工程隐患及解决办法、工序动态安全控制,为顺利完成高炉改造提供了保障。
通过实际生产检验,设计方案采用的工艺合理,技术先进实用,设备成熟可靠,以
最低的投资获得了最佳的设备组合,项目按时投产,高炉生产稳定、降低了生产成本,提高了企业的市场竞争力。
摘要通过对首钢京唐钢铁公司高炉项目钢结构工程

摘要:通过对首钢京唐钢铁公司高炉项目钢结构工程在唐山曹妃甸地区的高腐蚀环境下优选防腐配套工艺方案及涂装应用,解决了大型冶金建设项目钢结构工程在海洋性腐蚀环境下达到低投入、长效防腐蚀的问题。
关键词:金属钢结构;防腐蚀涂料;多层异类;系统供货.前言首钢搬迁曹妃甸地区整体建设,首先面对的就是金属钢结构的腐蚀问题。
在工业发达国家中,腐蚀造成的直接经济损失占国民经济总产值的~,每年腐蚀生锈的钢铁约占产量的,约的设备因腐蚀而报废。
在中国,由于金属腐蚀造成的经济损失每年高达亿元以上,占国民生产总值的。
长期以来,人们一直采用多种技术对金属加以保护,防止或延缓腐蚀的发生。
由于防腐涂料具有性能优异、使用方便、价格低廉等一些其他材料无法比拟的优点,因此在选择防腐措施时成为优先考虑的对象。
随着世界海洋工业的迅速发展和环境保护法对海洋涂料工业的影响,海洋防腐涂料也向高性能及环保型方向发展,出现了许多有发展前景的新技术。
我们依据曹妃甸地区特有的自然环境,从年初开始,经过大量的实验工作取得了充分的实验数据,设计了曹妃甸地区钢结构防腐工程涂料配套方案,于年月开始在首钢京唐钢铁公司高炉项目中广泛应用。
.腐蚀环境分析曹妃甸地区属暖温带季风大陆性气候,四季分明、气候干燥、雨少风多。
夏季高温、多阴雨,秋季冷暖适宜、晴天多,冬季寒冷、少雷多雾。
年平均气温℃,平均地面温度℃,年平均相对湿度。
年平均蒸发量1909.6mm,年平均气压,全年无霜期大约,港口冬季结冰约多天。
年平均降水量约~700mm,全年%左右的降水集中在、、三个月的夏季。
日照时间较长,太阳辐射强,日照百分率高达,全年平均日照约。
建设前期,曹妃甸地区的腐蚀环境基本属于海洋大气腐蚀,海洋性大气环境的相对湿度大,大气中含有海盐粒子。
沉积在金属表面上的海盐粒子,或者表面上原有的具有很强吸湿性的盐分与金属腐蚀物,会溶于水膜中形成强腐蚀性介质,而且海盐粒子为氯化物,渗透腐蚀性强,可以渗入钝化膜腐蚀底材,即便是不锈钢也会因其而产生点蚀。
1号高炉基本操作制度探讨

轻的煤气流分布。因此 ,找到不同炉型的合理堆
尖位 置对 于控 制煤 气流 分布 至关重 要 。
熔带以上间接还原 区变短影响 ,矮胖型高炉燃料
消耗有 可能 增加 、炉 温不 易控制 、炉况 稳定 性 稍 差 J l。另外 ,矮胖 型高 炉偏小 的炉 身和 炉腹 角使
2 焦炭质量 与高炉操作调节
虽 然炉 料 在 下 降过 程 中层 状 结 构保 持 不 变 ,
长期 以来 ,1号高 炉 围绕 原料 质 量进 行上 下
部调 剂相 结合 ,合理 分 配两 条煤气 通路 ,摸 索 出
一
套 高 炉调整 的规 律 ,使高 炉燃 耗指标 近年来 得
张思斌 :19 9 0年毕业于钢铁学院分院 ,现任炼铁厂 1 号高炉作业 区区域 长 高级工程师 。收稿/ 0 70 —2 2 0 —4 0
Be i e sd s, t e g sditi u i n i n e fe t e c n r lb r a i o i ai n o h h r i g s se h a srb to su d refci o to y og nc c mb n to ft e c a g n y tm v
矮胖 型高 炉 因料 柱 阻损相 对较 小 ,故在 一定
炉 腰 和炉 身 下 部 受 上 升 煤 气 流 冲 刷 而 使 侵 蚀 加
快。
风速动能条件下,相 同布料制度会出现与瘦高炉 型不同的煤气分布 ,1号高炉炉喉各点煤 气分布
唐钢一号高炉年修达产实践

a o n fbatn r sdq i l,h ir ui fw i o s o t ldtru hteajs n fodn m u t l ce e uc y tedsi t no oa f w wa n ol o g d t t ai o si a k tb o t r l c r e h h u me o l g
工艺装备
唐钢 一号高炉年修达产 实践
于海翔 何友 国 鲁新生
( 钢 股份 , 唐 河北 唐 山 0 3 0) 60 0
摘
要: 唐钢一号高炉年修后, 经过充分的前期准备, 送风后在快速加风过程 中及 时通过对装料制度的调整, 控制
两道气流的分布, 随煤气利用 的改善、 渣铁物理热 的增加, 逐步 降低焦 比、 提高焦炭 负荷 , 实现快速 降[i 为炉前 S] , 工作及后续加风创造了 良好的条件, 使高炉各项指标逐步优化 , 在短期 内顺利达产。
2 开炉 前 准 备
2 1 开炉原燃料 .
装入炉内 6c 3 h开炉 料 , 中净 焦 1 c 、 其 7h 空焦 3 c 、 0 h 正 常料 1 c , 6h 料线 1 m, . 具体 见表 3 7 。
i i c e so e r d cin t ss c s v r o u t . u p o
K w硎 8 batu n c  ̄n u l p i:e c epo u t nid x : lsfr ae a n ar arra ht r d ci e e h o n
( a g h nI n& s e C . d, e e T n sa 6 0 0 T n sa o r t l o t . b i a g h n0 3 0 ) e L H
Abl' | t n u k p i a d te a e u t rp r t n t e I BF o n s a r n & S e 1 n t e p o e s o e lI I ̄ Af ra n a e a n h d q ae p e a ai h # f Ta g h n Io I e r o te.i h r c s f t h
首钢京唐1号高炉降铁次实践的战略意义
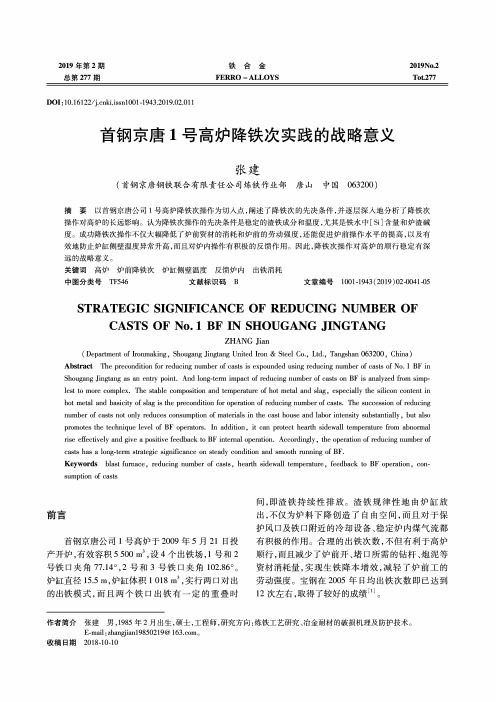
i 18 s 16
14
m 12 s
2012 2013 2014 2015 2016 2017 2018 时间
2019年第2 期 总第277期
D 0 1 :10.1 6 12 2 / k i.issn l0 01 -1943.2019.02.011
铁合金 FERRO-ALLOYS
2019NO.2 Tot277
首钢京唐1 号高炉降铁次实践的战略意义
张建
(首 钢 京 唐 钢 铁 联 合 有 限 责 任 公 司 炼 铁 作 业 部 唐 山 中 国 063200)
Keywords blast furnace, reducing number of casts, hearth sidewall temperature, feedback to BF operation, con
sumption of casts
刖S
首钢京唐公司1 号 高炉于2009年 5 月 2 1 日投 产开炉,有效 容 积 5 500 m3,设 4 个出铁场,1 号 和 2 号铁口夹角77.14°,2 号 和 3 号 铁 口 夹 角 102.86°。 炉 缸 直 径 15.5 m,炉 缸 体 积 1 018 m3,实行两口对出 的出铁模式,而 且 两 个 铁 口 出 铁 有 一 定 的 重 叠 时
间 ,即 渣 铁 持 续 性 排 放 。渣 铁 规 律 性 地 由 炉 缸 放 出 ,不 仅 为 炉 料 下 降 创 造 了 自 由 空 间 ,而且对于保 护 风 口 及 铁 口 附 近 的 冷 却 设 备 、稳 定 炉 内 煤 气 流 都 有积极的作用。合 理 的 出 铁 次 数 ,不但有利于高炉 顺 行 ,而且减少了炉前开、堵口所需的钻杆、炮泥等 资材消耗量,实 现 生 铁 降 本 增 效 ,减轻了炉前工的 劳动强度。宝 钢 在 2 0 0 5 年日均出铁次数即已达到 1 2 次左右,取得了较好的成绩[1]。
首钢京唐公司1号高炉工艺技术特点

( 简称首钢京唐公 司)一期建设 2 550 座 0 高 m
炉 ,年产 炼 钢 生铁 88万 t 9 。其 中 ,1 高 炉 以 号 “ 高效 、低耗 、优质 、长 寿 、清 洁”为设 计理念 , 优化集 成 了国 内外先 进 的新 技术 、新工 艺 ,实现 了高炉 生产 的大型化 、高效化 、现代 化 、长 寿化 和清 洁化 。1号高炉 于 20 年 3月 1 07 2日开工 建 设 ,20 0 9年 5月 2 1日正式 点火 送风 ,实 现 了顺 利 开炉 、平稳 达产 。
关 键 词 超 大 型 高炉 工 艺技 术
TheTe hn c l o e sFe t e ft . as c i a Pr c s a ur so heNo 1 Bl tFur a e o n c f
S o g n i g a gUn t d I o n te . Lt . h u a gJ n t n ie r n a d S e l Co , d
富氧率为 35 .%,综合 冶炼强度 为 1 3 ( s ) . 5/ m . , 0 t d
净煤 气含尘量 为 5r / gm ,炉 顶煤气余 压发 电 a ( R )系统 吨铁发电量为 4 W ・,标煤工序 TT 5 k h 能耗 为 4 4k/,一代 炉役寿命 为 2 年 。 0 gt 5
A sr c T etc nc l rc s au e f h o1B f h u a gJn tn i dIo n te b ta t h h ia o e s e t rs eN . Fo o g n iga gUnt na d Se l e p f ot S e r
首钢京唐公司l号高炉

首钢京唐公司l号高炉首钢京唐公司I号高炉首钢京唐公司是中国首钢集团旗下的一家大型钢铁企业,位于河北省唐山市,是中国最大的钢铁炼焦企业之一。
本文将对首钢京唐公司I 号高炉进行详细介绍。
一、公司概况首钢京唐公司I号高炉建设于2007年,是首钢京唐公司的重要生产设施之一。
高炉采用煤气发生炉进行炼焦,主要生产高质量的生铁和炼钢炉料。
高炉炉顶直径为11.6米,有效容积为5500立方米,设计年产量达到320万吨。
二、生产工艺1.原料准备首钢京唐公司I号高炉主要使用铁矿石、焦炭和炉渣作为原料。
这些原料需经过严格的筛选、堆放和称重等工艺过程,确保原料的质量和配比的准确性。
2.煤气发生炉炼焦高炉采用煤气发生炉进行炼焦,炼焦过程中生成的煤气经过净化和处理后被送入高炉进行燃烧。
煤气发生炉具有炉温高、炉内压力稳定等特点,可使焦炭充分燃烧,提高高炉产量和炼铁质量。
3.高炉冶炼高炉冶炼过程中,原料在高炉内逐渐下降,同时与上升的煤气进行反应,产生流动状态下的固液、气三相反应。
经过冶炼,原料中的铁分子与碳分子结合,产生生铁。
同时,高炉中形成的炉渣通过铁口排出。
4.产品输送冶炼完成后,生铁和炼钢炉料通过铁口流出高炉,进入后续的钢铁生产流程。
炉渣则通过渣口排出,用于炼钢炉料和水泥生产等领域。
三、质量控制为确保产品质量,首钢京唐公司I号高炉采取了一系列的质量控制措施。
首先,在原料准备过程中,严格控制矿石、焦炭和炉渣的质量,并按照一定比例进行混合。
其次,煤气发生炉的稳定运行和净化处理,保证高炉内燃烧所需的高质量煤气。
最后,高炉冶炼过程中,控制温度、压力和流量等参数,确保生铁的质量符合要求。
四、环保措施首钢京唐公司I号高炉在生产过程中注重环境保护,采取了一系列的措施减少对环境的影响。
首先,煤气发生炉和高炉煤气净化系统有效去除了废气中的有害物质,保证废气排放符合国家标准。
其次,对高炉炉渣进行资源化利用,减少了废渣的排放量。
此外,首钢京唐公司还加强了废水处理和固体废物管理,确保废水和废物的处理符合环保要求。
首钢京唐公司1号高炉低碳生产实践
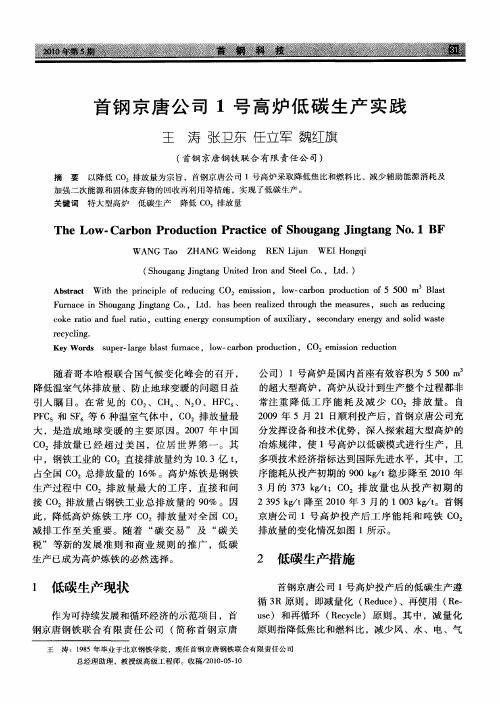
降 低温 室气 体排放 量 、防止地 球变 暖 的问题 日益
引人 瞩 目。在 常 见 的 C : C N O、HF O、 H、 2 C
PC F 和 s 等 6种 温 室 气体 中 ,C :排 放 量最 O
大 ,是造 成 地 球 变 暖 的 主 要 原 因பைடு நூலகம்2 0 0 7年 中 国
首 钢 京 唐 公 司 1号 高 炉 低 碳 生 产 实 践
王 涛 张 卫东 任 立军 魏红旗
( 首钢 京唐钢 铁联 合 有 限责任 公 司)
摘 要 以降低 c :排放量为宗 旨,首钢京唐公 司 1号高炉采取 降低焦 比和燃 料比 、减少辅 助能源消耗及 0 加强二次能源 和固体废 弃物的 回收再利用等措施 ,实现 了低 碳生产。 关键词 特大 型高 炉 低碳 生产 降低 C 排放量 O
Th w— r o o u to a t e o h u a g J n t n . e Lo Ca b n Pr d c i n Pr ci fS o g n i g a g No 1 BF c
WA G T o Z N iog R N L a WE o gi N a HA G We n E i n d j IH n q
( hu a gJ gagU i dI n adSel o,Ld ) S o gn i t nt r n te C . t. n n e o
Ab ta t W ih t e p i i l fr du i g sr c t h rncp e o e cn CO2 e iso m s i n, lw— a b n p o u t n f5 0 o c r o r d ci o 5 0 m Bl s o at
F r a e i h u a gJn tn . Ld u n c n S o g n iga gCo , t .h sb e e l e ru h teme s rs s c srd cn a e n rai d t o g h a ue , u h a e u ig z h
- 1、下载文档前请自行甄别文档内容的完整性,平台不提供额外的编辑、内容补充、找答案等附加服务。
- 2、"仅部分预览"的文档,不可在线预览部分如存在完整性等问题,可反馈申请退款(可完整预览的文档不适用该条件!)。
- 3、如文档侵犯您的权益,请联系客服反馈,我们会尽快为您处理(人工客服工作时间:9:00-18:30)。
在首钢京唐钢铁厂一期一步5500m3高炉施工中,北京首钢建设集团有限公司(首建集团公司)全面总结了日本、欧洲5000m3以上高炉及国内大型高炉的设计和生产经验,坚持“高效、低耗、优质、长寿、清洁”的设计理念,采用先进实用、成熟可靠、节能环保、优质长寿的工艺技术和设备材料,实现了高炉的大型化、高效化、现代化、长寿化、清洁化。
此高炉为国内首座5000m3以上特大型高炉,采用了当今国际炼铁技术领域的十大类、68项先进技术,具有21世纪国际先进水平和强大的竞争力。
一期一步高炉总高126.4m,有效容积5500m3,年工作日355天,年生产449万吨铁水,设计寿命25年(一代炉龄)。
共完成土方6.4万m3,浇筑混凝土5.315万m3,钢结构制作安装2.9万吨,设备安装9224吨,电缆敷设123.5公里,各种管道4.5公里,并成功实现了1号5500m3高炉基础混凝土连续浇筑84.5小时,共10454m3.基础混凝土施工的主要特点和技术难点高炉基础2007年3月12日正式开始施工, 4月2日上午9:00开始浇筑砼,经过连续84.5个小时的不间断浇注,顺利完成了浇注混凝土10454m3的施工任务。
整个高炉基础施工历时24天。
5500m3高炉基础浇注是国内最厚的大体积混凝土浇注工程,工程量最大,质量要求高,养护困难,必须一次不间断连续浇注完成。
首建集团公司高度重视,组织工程技术人员制定了详细周密的技术方案和施工组织实施方案,并聘请国内知名的混凝土裂缝专家进行评审和技术把关。
施工中采用了国内最先进的测温技术和应力应变技术,随时掌握内外温差,确保控制在25℃以内。
搅拌站至高炉工地往返6公里的运距,采用了26台9m3的水泥罐车,每台按规定时间跑12个往返,共1248车次。
整个施工过程没有发生任何安全质量问题,创造了中国冶金工程建设史上的新纪录。
为了获得大积体混凝土施工数据,首钢集团公司采用电脑监控技术,对砼内部温度及砼应力进行了监测,获得了第一手数据资料。
使砼内外温差、内部应力达到了非常理想的水平。
工程实体达到了内实外光的要求,受到了专家一致好评,开创了国内冶金行业大体积混凝土施工的新纪元。
钢结构制作安装特点、技术难点高炉炉壳炉壳安装精度要求很高,组对后要求严格将风口带、铁口带水平标高偏差控制在4mm以内、对口错边量6mm以内、炉壳钢板圈的最大直径与最小直径差(55.8mm),以及钢板圈相对炉底中心的最大偏差不大于30mm.在跨带冷却壁的围板安装中,易产生焊接收缩,要满足冷却壁的安装精度要求,围板安装难度就增加了。
作业场地属沿海气候,空气湿度大,雨雪天气多,极易产生气孔、延迟裂纹、未熔合、夹渣等焊接缺陷。
钢板材质属于微合金高强钢(HSLA)。
需要解决在焊接、冷却过程中的热裂、冷裂、氢致裂纹等问题。
该材质中含有氮元素,如果焊接不当很容易产生时效脆化,因此需要严格控制焊接工艺参数,防止因氮元素的偏聚而出现的裂纹、气孔等现象。
由于高炉容积较大,最大直径处达18.6m.受客观条件和吊装能力所限,大部分炉壳围板不能在地面组焊成型后整带吊装到位,有部分立缝只能在高空焊接完成。
热风围管热风围管内部砌筑和喷涂对管道椭圆度要求很高,允许偏差在5mm内,比普通大直径卷焊钢管制作椭圆度要求提高了5mm. 42个短节对应高炉42个风口直吹管,要确保42套风口设备的安装精度,对短节弦长以及相互间尺寸的加工和安装精度提出了很高要求。
热风围管安装精度,环管上表面高低差要求控制在10mm内。
围管内表面至高炉外壳的距离允许偏差要求控制在20mm以内。
上升管、五通球上升管在70m高空对接安装,垂直度控制在20mm以内。
五通球需开5个孔与四根上升管和一根下降管相联,然后在110m高空进行组对安装,开孔位置允许偏差3mm,开孔直径与支管直径之差2~5mm.五通球在113m高空安装组对,安装标高偏差要求控制在±30mm以内,纵横中心偏差不超过30mm.构件的安装顺序给吊车的设置和吊装带来很大难度。
五通球重量达62吨,安装中心标高▽113m,DBQ4000吊车只能在五通球吊装到位后擎住,再利用630吨吊车进行第四根上升管弯管的安装。
下降管下降管上联五通球,下接旋风除尘器,是自立门架式结构的超长(66m)钢管斜横梁,中间无支撑,两端为固定口连接。
设计要求整体门架结构形成前,五通球及旋风除尘器伸出部分不能承受较大的悬臂弯矩。
下降管安装位置高(上口标高113.2m,下口标高63.103m),重量大(176t),其下是矩形出铁厂房;吊装重量大,考虑施工成本及场地狭窄的现场条件,无法使用两台超大型吊车抬吊就位。
同时沿海施工吊装构件高空横向风力大(常年3级风以上)。
由于五通球上伸出弯管及旋风除尘器上斜插管为空间结构,管壁厚20mm,空中组装误差及焊接变形较大,下降管与其为固定口相连,空中组对困难。
炉体框架炉体框架柱截面尺寸大,内部结构极为复杂,施工图深化设计和加工制作难度很大。
框架结构内部采用了横向横隔板、纵向T型加劲肋的结构形式。
框架柱在12m内就有9组横隔板和10根T型钢,箱型柱内部结构复杂,焊接量大,易变形。
框架柱单节柱最重达101吨。
各层平台采用八卦式结构布置,设计要求平台梁两端安装精度控制在1mm以内,以保证高强螺栓的安装。
防腐蚀要求高该地区属于沿海地区,空气湿度大,氯离子含量高,对钢结构腐蚀性强,因此除锈防腐是非常重要的环节。
因此采用喷砂除锈达到Sa2.5级后,刷富锌底漆,它是性能优异、具备阴极保护的电化学涂料。
底漆:环氧富锌漆一遍,干膜厚度60μm(室外);中间漆:环氧云铁漆一遍,干膜厚度80μm(室外);面漆:脂肪族聚氨酯面漆两遍,干膜厚度60μm(室外)。
在炉本体钢结构制作安装中采取的有效措施高炉炉壳安装和焊接控制工艺炉壳安装和焊接工艺流程:设备调试→炉壳吊装组对→装配交检→焊前预热→炉壳立缝焊接→炉壳环缝焊接→焊接检验→焊后热处理。
高炉第1带~12带炉壳按出厂单元进行吊装、组对焊接;第13带~16带先在安装现场组焊成单带,然后整带安装就位;第17带~22带在工厂每相邻两带组焊成一个单元,然后发运到安装现场直接吊装就位。
第23带、第24带+25带分别在工厂组焊成带,然后发运到安装现场直接吊装就位。
吊装组对后调整、测量,再调整、复测,合格后加固,进行焊接,采用二氧化碳气体保护焊的方法。
严格执行焊前预热、焊后缓冷、焊后热处理工艺,采用电加热方法,利用计算机控制技术+WDJK-360型控制柜对履带式电加热器进行适时控制,设定控制参数实现全程自动控制,保证了焊接和热处理的质量;同时这也是解决由于现场高湿度可能引起焊接缺陷问题的措施之一。
预热温度:120~150℃;后热温度:250~300℃;热处理温度:650℃。
严格控制焊接程序,先焊炉内侧焊缝,然后在外侧碳弧气刨清根、打磨合格后,再对外侧焊缝实施焊接,同时采取对称焊、多层多道焊、分段退焊等方法,最大限度降低因为厚板焊接存在的拘束度过大而产生裂纹的可能性。
针对BB503材料的特点:在焊接过程中为防止氮元素在焊缝处偏聚,严格控制熔合比,严格控制焊接线能量和层间温度。
针对沿海焊接施工的特点,严格执行了以下控制措施:在炉壳对接、组焊过程中,视天气情况,适当采取防风、防雨、防雪等措施,确保焊接质量要求。
严格清理焊接坡口表面及两侧距坡口边缘30㎜内的水渍、铁锈、油污、渣和其它杂质。
严格控制焊材的含水量:CO2气体保护焊用的CO2气体应保持干燥,气体纯度不小于99.8%(体积法),含水量不大于0.005%(重量法)。
严格执行焊前预热、焊后后热、缓冷的工艺措施。
为保证炉壳的尺寸和炉顶标高,采取了带与带之间预留间隙的方法进行调整,通过计算使间隙在2~4mm内,在焊后收缩的情况下,完全满足了冷却壁的安装和炉顶设备安装的要求。
热风围管制作、安装工艺采用数控切割,切割后的尺寸极限偏差控制在±1mm内。
围管短节组对过程中,依次检查组对后内侧和外侧弦长,以保证围管整体圆度。
制作完成后整体预拼装,对有超差部分进行地面调整。
在9.9m平台上组对,提前在平台上划出十字中心线、围管内外边缘线,围管整体组装完后进行焊接加固,防止变形。
在34m平台上设立4个吊点,利用滑轮组进行同步整体吊装,吊装过程中全程监测高度。
吊装到位后测量环管内表面至高炉外壳的距离,在确保合格后利用垂直吊杆固定。
上升管制作安装工艺采用数控切割下料,把切割偏差控制在了±1mm以内。
上升管地面组对,整体吊装,减少高空作业难度和满足上升管垂直度的要求。
五通球制作安装工艺措施球片用专用胎具压制,为保证各块边缘成形精度,在每块四周加放3倍板厚的压头量。
五通球支架和支撑按30°周圈布置,在基准圆外侧的球壳板处均匀点焊定位块,然后以定位块和胎具为基准,按顺序装配赤道带壳板。
待纵缝定位焊接完成后装上、下极带。
五通球与上升管四个接口设立活动短节,以便在高空组对时调整,提高了组装精度,加快了施工进度。
根据五通球焊接容易变形等特点,首建集团公司经过精确定位,对五通口相贯线进行精确切割,并加设16道放射型防变形拉筋,保证了其椭圆度达到图纸及规范要求。
下降管计算机模拟吊装技术。
根据现有施工场地及吊车起重能力,确定吊装构件大小(分2段吊装),施工前用计算机模拟整个吊装过程,精确制定下降管部件现场组对位置、吊车及起吊重物运行路线、就位过程,确保构件平稳无障碍吊装。
精确计算构件重心,确定主吊点及调整绳悬挂点,确保构件按安装位置角度起吊。
下降管上装有梯子、栏杆及均压放散管等附件,必须精确计算组装后构件的重心,选择正确的主吊点及调整绳悬挂点,在离开地面前调整好角度,才能精确安装就位,实现与固定口的组对。
采用可调式支架,空中调整及支撑上管段。
按照安装位置,用计算机模拟设计上管段“人”字形支撑架,支脚与炉顶平台梁铰接,在炉顶平台设链式起重机,用钢丝绳拉支架顶住横梁,在五通球上焊接吊耳挂固定定滑轮,通过链式起重机、钢丝绳调整支撑架位置,进而支撑或调整管段安装角度。
仪器精确测量五通球伸出管及旋风除尘器斜插管空间位置,确定下管段长度及角度。
用进口高精度TDA5005全站仪精确测量五通球伸出管口、旋风除尘器斜插管口相对高炉中心线的角度、位置座标点,计算确定下段管的长度,测量精度达到了0.3mm.三角形法测量下管段吊起角度,配重调整,使吊起角度与安装就位角度完全相同。
按安装就位角度精确计算下管段重心,用吊车试吊离地面,下管段上口挂重锤,由下管口下部拉钢线,用钢角尺测量使钢线与重锤线垂直后,测量两钢线长度与计算值对比,然后在两管端调整配重,直至两者相等后起吊。
选择晴朗风力小的天气,上午10点钟以后吊装,避免沿海早晚风大的影响。
通过实施以上6项措施,下降管上段2小时吊装就位组对完,下段4小时吊装就位组对完,管口长度偏差23mm,径向偏差5mm,高于规范径向偏差10mm的要求,而且快捷安全完成吊装任务。