搅齿造粒机应用在干法造粒的过程.
搅齿造粒机应用在干法造粒地过程

搅齿造粒机应用在干法造粒的过程炭黑是一种堆积密度很低的粉末状物质,易飞扬而污染环境,运输性极差。
一般说来,增加其密度,在某种程度上会克服或清除这些缺点,但也降低了它在介质中的分散性。
炭黑工业常以湿法或干法造粒的方式对粉状炭黑进行加工。
湿法造粒是上个世纪4o年代开发的一项技术。
在最近5O多年中,炭黑工业也在一直不断地改进湿法造粒过程,使之日臻完善。
这些改进主要包括如下几个方面:·开发各种粘合剂,提高造粒品的强度;·探索最适宜的搅齿排列方式,以产生理想的颗粒;·寻求合适的搅齿材质,明显降低其磨损速率;·摸索搅齿轴功率与水量的关系,建立炭黑/水自调系统;·改进设备结构,如筒壁夹套加热除去附着层、粉料人口加设螺旋叶片、局部更换搅齿尖以及保持搅齿尖与筒壁的最佳距离等。
尽管湿法造粒过程是一种能耗较高的单元操作,人们一直力图对它进行改造,但是,到目前为止该方法仍在世界上橡胶用炭黑的后加工工序中占主流地位。
对橡胶用炭黑而言,由于橡胶在混炼过程中粘度较高,高硬度的湿法造粒品在胶料中受到强烈的剪切作用,完全能均匀地分散在聚合物中。
另外,随着橡胶加工业混炼工序自动化程度的不断提高,炭黑的气力输送和自动称量,也要求使用强度较高的湿法造粒品。
至今,散装炭黑的规模亦愈来愈大,由集散纸箱、槽车,到容量lt 的太空包,以至lO一20t的大型集散箱运输。
从橡胶用户的需求来看,湿法造粒产品仍是人们所优选的。
炭黑在介质中的良好分散是制品达到最佳使用性能的基础。
在非橡胶应用领域,特别是塑料和油墨等制品中,由于聚合物性质和混配设备的制约,常采用干法造粒炭黑。
但是,这种造粒方式的粒子硬度较差,在贮运过程中粒子极易破碎,细粉量相对较多而且是变化的,导致喂料机很难均匀送料,致使混配过程不稳定。
另外,从炭黑生产的角度看,在普通的干法造粒机中,炭黑的造粒速率很慢,过程效率亦太低。
毫无疑问,对非橡胶用炭黑而言,提高现有干法过程的效率或寻求其他方式增加炭黑密度,仍是当前技术开发的热点。
造粒机工艺流程
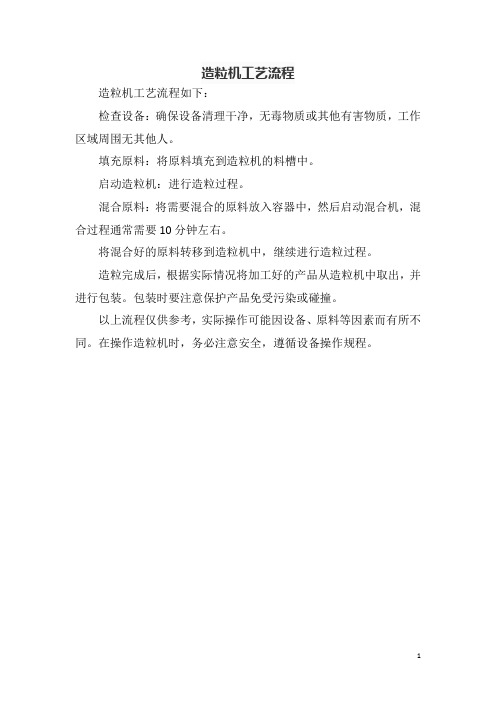
造粒机工艺流程
造粒机工艺流程如下:
检查设备:确保设备清理干净,无毒物质或其他有害物质,工作区域周围无其他人。
填充原料:将原料填充到造粒机的料槽中。
启动造粒机:进行造粒过程。
混合原料:将需要混合的原料放入容器中,然后启动混合机,混合过程通常需要10分钟左右。
将混合好的原料转移到造粒机中,继续进行造粒过程。
造粒完成后,根据实际情况将加工好的产品从造粒机中取出,并进行包装。
包装时要注意保护产品免受污染或碰撞。
以上流程仅供参考,实际操作可能因设备、原料等因素而有所不同。
在操作造粒机时,务必注意安全,遵循设备操作规程。
1。
高速搅拌切割制粒过程及影响因素简介

高速搅拌切割制粒过程及影响因素简介文章标题:高速搅拌切割制粒过程及影响因素简介概述:高速搅拌切割制粒是一种常见的固体制粒方法,它可以将粉末、颗粒或浆料转化为均匀的颗粒状物料。
在这个过程中,搅拌切割设备通过高速旋转刀片将原料分散并切割成均匀的颗粒。
本文将对高速搅拌切割制粒过程以及影响因素进行简要介绍,并分享一些个人观点和理解。
一、高速搅拌切割制粒过程:1. 设备介绍:高速搅拌切割制粒常用的设备包括高剪切搅拌机、高剪切混合机或高剪切切割机。
这些设备通常由旋转刀片、筒体和驱动装置组成。
在制粒过程中,原料通过进料口加入搅拌切割设备,旋转刀片高速旋转时,将原料分散并切割,形成均匀颗粒。
2. 切割原理:高速切割刀片的旋转速度和形状对制粒效果起着重要作用。
刀片旋转时,带动原料发生剪切和抛撒,进而将颗粒状物料切割成均匀颗粒。
切割过程中,刀片与原料之间的相对速度越大,切割作用就越明显。
刀片的形状也能够影响颗粒大小和形态。
3. 切割条件:高速搅拌切割制粒的切割条件包括刀片速度、刀片形状、搅拌速度、搅拌时间等。
不同的切割条件将导致不同的制粒效果。
刀片速度越高,制粒效果越好;刀片形状对颗粒形态有一定的影响;搅拌速度和时间决定了切割时间和强度,进而影响颗粒的大小和分布。
二、影响因素:1. 原料特性:原料的物理性质、颗粒大小和分布、含水量等都会影响高速搅拌切割制粒的效果。
物理性质包括粉末流动性、颗粒形状等,这些特性将影响切割和分散性能。
较大的颗粒可能需要更长的切割时间来获得均匀的颗粒。
含水量的变化也可能导致制粒效果的不稳定性。
2. 设备参数:高速搅拌切割设备的参数,如刀片速度、刀片形状、搅拌速度和时间等,决定了切割的强度和时间。
这些参数的选择与原料的特性有关,通过合理调控这些参数,可以获得所需的颗粒特性。
3. 外部环境:制粒过程中的外部环境也会对制粒效果产生一定影响。
湿度、温度、压力等因素都可能影响粉末的流动性、粘附性和切割效果。
干法制粒目的与制粒方法
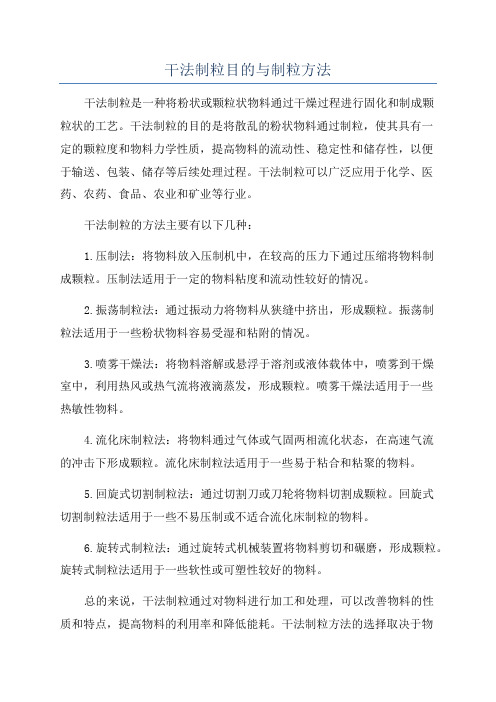
干法制粒目的与制粒方法干法制粒是一种将粉状或颗粒状物料通过干燥过程进行固化和制成颗粒状的工艺。
干法制粒的目的是将散乱的粉状物料通过制粒,使其具有一定的颗粒度和物料力学性质,提高物料的流动性、稳定性和储存性,以便于输送、包装、储存等后续处理过程。
干法制粒可以广泛应用于化学、医药、农药、食品、农业和矿业等行业。
干法制粒的方法主要有以下几种:1.压制法:将物料放入压制机中,在较高的压力下通过压缩将物料制成颗粒。
压制法适用于一定的物料粘度和流动性较好的情况。
2.振荡制粒法:通过振动力将物料从狭缝中挤出,形成颗粒。
振荡制粒法适用于一些粉状物料容易受湿和粘附的情况。
3.喷雾干燥法:将物料溶解或悬浮于溶剂或液体载体中,喷雾到干燥室中,利用热风或热气流将液滴蒸发,形成颗粒。
喷雾干燥法适用于一些热敏性物料。
4.流化床制粒法:将物料通过气体或气固两相流化状态,在高速气流的冲击下形成颗粒。
流化床制粒法适用于一些易于粘合和粘聚的物料。
5.回旋式切割制粒法:通过切割刀或刀轮将物料切割成颗粒。
回旋式切割制粒法适用于一些不易压制或不适合流化床制粒的物料。
6.旋转式制粒法:通过旋转式机械装置将物料剪切和碾磨,形成颗粒。
旋转式制粒法适用于一些软性或可塑性较好的物料。
总的来说,干法制粒通过对物料进行加工和处理,可以改善物料的性质和特点,提高物料的利用率和降低能耗。
干法制粒方法的选择取决于物料的性质、用途和工艺要求,不同的方法有不同的适用范围和优缺点。
在实际应用中,需要根据具体情况进行选择和调整。
干法制粒设备原理

干法制粒设备原理干法制粒设备是一种常用的固体颗粒物处理装置,其原理为通过将粉状物料经过干燥、研磨和分类处理后,再通过压制或喷雾等方式将其转化为固体颗粒物。
下面将详细介绍干法制粒设备的原理。
首先,干法制粒设备主要包括干燥机、研磨机和分类器。
其中,干燥机主要用于去除物料中的水分,使其达到所需的湿度。
研磨机负责将固体物料进行研磨处理,使其达到所需的细度和均匀度。
分类器则是将物料按照粒径分级,以保证粒径在一定范围内的固体颗粒物。
除此之外,还有再结晶设备、喷雾制粒设备等用于特殊需求的制粒设备。
干法制粒设备的主要工作过程如下:首先,经过预处理的物料首先进入干燥机,在其中被热空气吹干,去除水分。
干燥后的物料进入研磨机,通过切割、碾磨和撞击等力量,将其研磨成细小的颗粒。
然后,经过研磨的物料再进入分类器,通过离心力将粒径较大的物料分离出来,而较小的物料则通过筛孔进行分级,以获得所需的颗粒物。
最后,固体颗粒物可通过收集器进行收集和包装。
干法制粒设备的原理主要包括以下几个方面:1. 研磨原理:物料在研磨机中经过旋转的刀片、球体或者滚轮等破碎装置的作用下,产生剪切、挤压、撞击等力量,使物料被破碎成细小的颗粒。
研磨机的选择和操作方式能够控制物料的细度和均匀度。
2. 干燥原理:干燥机通过热风产生的高温和流体化的气流,将物料中的水分蒸发出去。
干燥机常用的加热方式有燃烧炉加热、蒸汽加热等。
物料在干燥过程中需要注意温度和时间的控制,以避免过热或过烘干物料。
3. 分级原理:分类器通过离心力和筛孔的作用将不同粒径的物料进行筛分和分离。
离心力使大颗粒物沉降分离,而较小的颗粒则能够通过较细的筛孔顺利流出。
分类器的选择和参数的调整能够控制颗粒物的粒径分布。
总之,干法制粒设备通过干燥、研磨和分类等工序,将粉状物料转化为固体颗粒物。
研磨原理通过力学作用将原料研磨成所需粒度和均匀度的颗粒;干燥原理通过热风蒸发物料中的水分;分级原理通过筛孔和离心力将颗粒物按粒径分离。
造粒车间工艺流程图
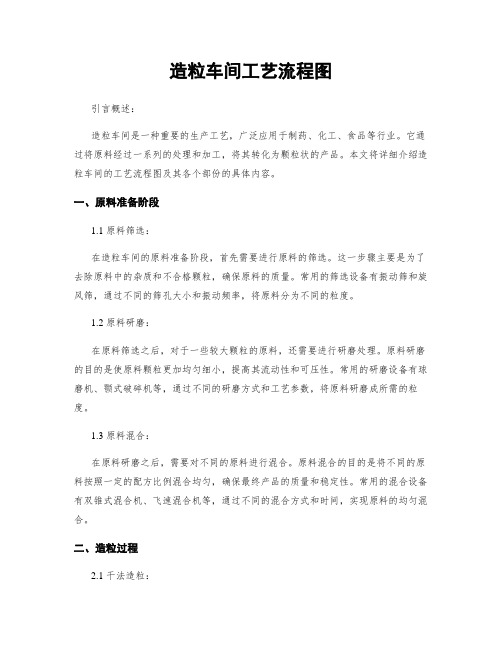
造粒车间工艺流程图引言概述:造粒车间是一种重要的生产工艺,广泛应用于制药、化工、食品等行业。
它通过将原料经过一系列的处理和加工,将其转化为颗粒状的产品。
本文将详细介绍造粒车间的工艺流程图及其各个部份的具体内容。
一、原料准备阶段1.1 原料筛选:在造粒车间的原料准备阶段,首先需要进行原料的筛选。
这一步骤主要是为了去除原料中的杂质和不合格颗粒,确保原料的质量。
常用的筛选设备有振动筛和旋风筛,通过不同的筛孔大小和振动频率,将原料分为不同的粒度。
1.2 原料研磨:在原料筛选之后,对于一些较大颗粒的原料,还需要进行研磨处理。
原料研磨的目的是使原料颗粒更加均匀细小,提高其流动性和可压性。
常用的研磨设备有球磨机、颚式破碎机等,通过不同的研磨方式和工艺参数,将原料研磨成所需的粒度。
1.3 原料混合:在原料研磨之后,需要对不同的原料进行混合。
原料混合的目的是将不同的原料按照一定的配方比例混合均匀,确保最终产品的质量和稳定性。
常用的混合设备有双锥式混合机、飞速混合机等,通过不同的混合方式和时间,实现原料的均匀混合。
二、造粒过程2.1 干法造粒:干法造粒是一种常用的造粒方式,它通过将原料在干燥状态下进行造粒。
在干法造粒过程中,首先将混合好的原料送入造粒机,然后通过机械力或者压力将原料压制成颗粒状。
常用的干法造粒设备有压片机、制粒机等,通过不同的工艺参数和模具形状,制备出不同形状和大小的颗粒。
2.2 湿法造粒:湿法造粒是另一种常用的造粒方式,它通过将原料在湿润状态下进行造粒。
在湿法造粒过程中,首先将混合好的原料与适量的溶剂或者粘合剂混合,形成湿团。
然后将湿团送入造粒机,通过机械力或者压力将湿团压制成颗粒状。
常用的湿法造粒设备有制粒机、喷雾干燥机等,通过不同的工艺参数和喷嘴形状,制备出不同形状和大小的颗粒。
2.3 热熔造粒:热熔造粒是一种特殊的造粒方式,适合于一些高熔点或者易熔化的原料。
在热熔造粒过程中,首先将原料加热至熔点或者软化点,形成熔液。
干粉造粒工艺流程(一)

干粉造粒工艺流程(一)干粉造粒工艺干粉造粒是一种将粉末物料加工成颗粒状的技术。
该工艺广泛应用于制药、化工、农药、食品等行业。
其优点包括易于运输、存储和加工,因此备受青睐。
下面将详细介绍干粉造粒的各个流程。
原料预处理干粉造粒前,需要对粉末原料进行预处理。
这包括筛选、质检、混合等。
原料选用质量优良的,环保的,符合药典标准或符合其他工艺要求的物料。
原料进料应有完整的质量检测,检测结果应符合要求。
输送原料预处理后,将原料输送到造粒机。
输送方式可以是手动、机械等。
破碎将粉末原料送到各种碎料机进行粉碎,使其颗粒大小符合造粒机要求。
成型原料破碎后,进入造粒机成型。
造粒机主要分为压片机,滚筒机和喷雾干燥机。
不同模型的造粒机具有不同的原理和操作流程,但其基本步骤类似:粉末原料进入机器,经过一定的加工处理,最终成为固体颗粒。
干燥颗粒还未完全成型,含有水分。
造粒机通过喷淋干燥来获得所需的颗粒形态和含水量。
干燥温度和时间应控制得当,以保持颗粒品质和粒径分布。
颗粒成型后,通过筛分来控制颗粒大小,筛选得到所需的颗粒粒径范围。
包装完成粉末造粒后,需要进行包装,以便于贮存和销售。
包装应符合相关标准,如瓶装、袋装等。
总结干粉造粒工艺包含多个步骤,每个步骤都非常重要。
只有严格按照工艺要求,要求原料优质,进行混合,控制好干燥和筛分等环节,才能制成高质量的颗粒。
优缺点优点1.更高的稳定性:通过造粒可以改善原料中不规则颗粒的分布,提高粉末的稳定性和流动性,从而更容易地进行加工、输送和储存。
2.适应性强: 造粒可以适应不同的颗粒要求,例如不同的大小、形状、密度、比表面积和材料组成等方面。
3.高效性:由于颗粒比粉末更易于流动、混合和筛选,因此可显著提高生产效率和生产能力。
缺点1.复杂的制造过程:由于干粉造粒制造过程复杂,要求严格,需要更加谨慎、环保和卫生,从而会增加生产成本。
2.控制不易:干粉造粒的过程需要进行多次加工和控制,如果未能选用合适的生产设备和进行充分控制,可能会产生颗粒松散、粉尘和不均匀等问题。
干法制粒的方法

干法制粒的方法嘿,咱今儿个就来聊聊干法制粒的那些事儿!你可别小瞧这干法制粒,它就像是一门神奇的手艺,能把各种材料变成有用的颗粒呢!干法制粒啊,简单来说,就是不用加水或其他液体,直接把粉末变成颗粒。
这就好比是把一堆散沙变成坚固的城堡,厉害吧!那它到底是怎么个干法呢?首先呢,得有合适的原料粉末。
这粉末就像是盖房子的砖头,得质量好才行呀。
要是粉末本身就不行,那后面可就难搞咯!然后呢,把这些粉末放进一个特殊的机器里,这个机器就像是一个魔法盒子,能让粉末发生奇妙的变化。
在这个过程中呀,压力可是个关键的因素。
就好像你要把面团揉得紧紧的,让它成型一样。
通过施加合适的压力,粉末就能紧紧地黏在一起,变成颗粒啦。
这可不是随随便便就能做到的,得掌握好那个度,不然要么压不紧,颗粒松松垮垮的;要么压得太狠了,把粉末都给压坏啦!还有啊,机器的设计也很重要呢。
就跟咱家里的电器一样,不同的牌子性能可不一样。
好的干法制粒机器,就像是一个得力的助手,能让整个过程更加顺利、高效。
你想想看,要是没有干法制粒,那我们生活中的好多东西可就不一样啦!那些药品呀、食品呀,说不定就没那么方便好用了呢。
干法制粒让这些东西的生产变得更简单、更高效,也让我们能更快地享受到它们带来的好处。
咱再来说说干法制粒的优点吧。
它不用加液体,这就避免了一些麻烦呀。
比如说,有些粉末遇水可能会变质,或者产生一些不好的反应。
用干法制粒就不用担心这些问题啦!而且呀,它还能节省能源呢,不用加热什么的,多环保呀!那干法制粒就没有缺点吗?当然也有啦!比如说,它对粉末的要求比较高,如果粉末太潮湿或者太细,可能就不太好制粒。
还有呀,有时候颗粒的质量可能不太稳定,这可得好好注意呢!总之呢,干法制粒这门技术既有它的神奇之处,也有需要注意的地方。
我们要好好了解它,才能更好地利用它呀!你说是不是?这干法制粒的方法,可真是值得我们好好研究研究呢!。
- 1、下载文档前请自行甄别文档内容的完整性,平台不提供额外的编辑、内容补充、找答案等附加服务。
- 2、"仅部分预览"的文档,不可在线预览部分如存在完整性等问题,可反馈申请退款(可完整预览的文档不适用该条件!)。
- 3、如文档侵犯您的权益,请联系客服反馈,我们会尽快为您处理(人工客服工作时间:9:00-18:30)。
搅齿造粒机应用在干法造粒的过程炭黑是一种堆积密度很低的粉末状物质,易飞扬而污染环境,运输性极差。
一般说来,增加其密度,在某种程度上会克服或清除这些缺点,但也降低了它在介质中的分散性。
炭黑工业常以湿法或干法造粒的方式对粉状炭黑进行加工。
湿法造粒是上个世纪4o年代开发的一项技术。
在最近5O多年中,炭黑工业也在一直不断地改进湿法造粒过程,使之日臻完善。
这些改进主要包括如下几个方面:·开发各种粘合剂,提高造粒品的强度;·探索最适宜的搅齿排列方式,以产生理想的颗粒;·寻求合适的搅齿材质,明显降低其磨损速率;·摸索搅齿轴功率与水量的关系,建立炭黑/水自调系统;·改进设备结构,如筒壁夹套加热除去附着层、粉料人口加设螺旋叶片、局部更换搅齿尖以及保持搅齿尖与筒壁的最佳距离等。
尽管湿法造粒过程是一种能耗较高的单元操作,人们一直力图对它进行改造,但是,到目前为止该方法仍在世界上橡胶用炭黑的后加工工序中占主流地位。
对橡胶用炭黑而言,由于橡胶在混炼过程中粘度较高,高硬度的湿法造粒品在胶料中受到强烈的剪切作用,完全能均匀地分散在聚合物中。
另外,随着橡胶加工业混炼工序自动化程度的不断提高,炭黑的气力输送和自动称量,也要求使用强度较高的湿法造粒品。
至今,散装炭黑的规模亦愈来愈大,由集散纸箱、槽车,到容量lt 的太空包,以至lO一20t的大型集散箱运输。
从橡胶用户的需求来看,湿法造粒产品仍是人们所优选的。
炭黑在介质中的良好分散是制品达到最佳使用性能的基础。
在非橡胶应用领域,特别是塑料和油墨等制品中,由于聚合物性质和混配设备的制约,常采用干法造粒炭黑。
但是,这种造粒方式的粒子硬度较差,在贮运过程中粒子极易破碎,细粉量相对较多而且是变化的,导致喂料机很难均匀送料,致使混配过程不稳定。
另外,从炭黑生产的角度看,在普通的干法造粒机中,炭黑的造粒速率很慢,过程效率亦太低。
毫无疑问,对非橡胶用炭黑而言,提高现有干法过程的效率或寻求其他方式增加炭黑密度,仍是当前技术开发的热点。
有关造粒过程的简单描述等人在研究炭黑的内聚性(Cohesiveness)时发现,加压成型的炭黑块,随着密度的微小增加,其抗张强度迅速增大。
Rwei等人则进一步发现,炭黑块的抗张强度与其密度的4次方成正比。
他们在测定粒子在剪切流中的破碎与磨损性时也证实,炭黑的分散性与粒子密度呈类似的函数关系。
显然,造粒炭黑的粒子强度和分散性,受其密度的影响十分强烈。
在干法造粒过程中,粉状炭黑沿转鼓的筒壁滚动,聚集体靠范德华力与静电力附聚在一起。
造粒转鼓的圆周速度只有1—2m/s。
因而,这种造粒过程进行得相当柔和与缓慢。
若转鼓的圆周速度太高,在离心力的作用下,粒子则不沿筒壁发生滚动,而且作用于粒子球上的作用力太大,反而会使粒子破碎。
在湿法造粒时,粉状炭黑必须被水润湿到一定程度,以取代聚集体表面上吸附的气体。
润湿后的粉末,通过液桥和毛细力附着在一起。
在机械力作用下,粒子附聚与长大。
湿法造粒的优点在于,以水作为介质,不仅造粒速度快,过程效率高,而造粒品的强度亦较高。
造粒质量,一般以影响炭黑贮运性能有关的参数来衡量。
最常用的指标是,细粉量、粒子磨损量、堆积强度、单个粒子强度、平均颗粒尺寸以及颗粒尺寸分布等。
搅齿造粒机用于干法造粒搅齿造粒机,历来是湿法造粒的关键设备。
它与干燥机串联一起,完成炭黑的湿法造粒过程。
现在,搅齿造粒机用于干法造粒,其目的主要有两个。
一是改进现有干法造粒的过程效率;再则是提供分散性好、细粉量低而粒子尺寸分布更均匀的造粒品。
众所周知,搅齿造粒机在用于湿法过程时,搅齿端的圆周线速度一般应在1O~20m/s范围;炭黑在造粒机中的停留时间也很短,只有几秒钟。
当这种搅齿造粒机用于干法过程时,业已证实,其搅齿端的圆周线速度应降至1~6m/s,而炭黑在造粒机中的停留时间应延长到20~180s。
在这样的工艺条件下,即使不向搅齿造粒机中加水,也能获得质量稳定的造粒炭黑。
以搅齿造粒机进行干法造粒的流程示于图1。
从图中可见,该流程的特点是,造粒机轴线不是水平放置,而是粉状炭黑入口稍低,粒状炭黑出口稍高。
造粒机轴线与水平线呈0~15。
的倾角。
与传统的千法造粒一样,粉状炭黑要与一定量的母粒一起送入造粒机。
如图所示,母粒乃是由贮缶14经螺旋输送器送人搅齿造粒机10的进料口15的。
造粒机的外壁,用夹套加热,由恒温器16调节到所需温度。
该方法的优点在于,通过调整搅齿的圆周线速度和平均停留时间,即可满足任一特定炭黑品种的造粒质量要求。
另外,与传统的转鼓式造粒机相比,过程效率显著提高。
适当选择搅齿造粒机尺寸,如内径700~800ram,在保持理想的造粒质量的条件下,设备生产能力可达2t/h或更高。
工艺参数对造粒质量的影响下面,以一台实验用搅齿造粒机为例,研究工艺参数对造粒质量的影响。
这台实验用造粒机,筒壁内径200mm,长度1200mm,夹套温度控制在100℃,粉状炭黑最大处理能力约60kg/h。
实验用粉状炭黑,近似于N231类产品,其BET表面积120m2/g,DBP吸油值106ml/100g,24M4DBP值81ml /100g,而堆积密度约为120g/L。
停留时间当搅齿轴的转速保持恒定的条件下,炭黑在造粒机中的停留时间,可通常以下式表达:/式中,t为平均停留时间;mf为造粒机中炭黑填充量;m为炭黑进料量。
平均停留时间,取决于造粒机中的炭黑填充量和炭黑进料量。
粉状炭黑,通常是由螺旋输送机送入搅齿造粒机的。
因此,在设备达到稳定运转的条件下,造粒炭黑产量、粉状炭黑处理和螺旋输送机的喂料量皆是相同的,并可在很宽的范围内调节。
显然,可以通过调节搅齿造粒机轴线与水平线的夹角,来改变造粒机中的炭黑填充量和延长停留时间。
当然,炭黑在造粒机中的填充量与停留时间也受搅齿轴转速的影响。
造粒炭黑产量保持恒定时,随着搅齿轴转速的加快,炭黑填充量与停留时间彼此成比例地减少。
实验表明,停留时间的调整,应在保持造粒机产量恒定的条件下,改变造粒机的倾斜度,即造粒机轴线与水平线的夹角在0—15。
之内,优选的停留时间宜在20~180s范围之内。
为此,要为每个倾斜角度计算出稳定运转条件下造粒机内的炭黑填充量。
不同倾斜度的造粒机所造出的粒状炭黑性能参见表1。
从表中数据可见,随着造粒机倾角的增大,造粒炭黑的细粉量和粒子磨损量下降,平均颗粒尺寸增大,尺寸分布明显变窄,堆积密度基本不变,而单个粒子强度有所下降。
母粒回流量原则上说来,任何类型的炭黑均可用搅齿造粒机实施干法造粒。
实验证实,比表面积和结构均较低的炭黑容易造粒。
比表面积和结构均较高的炭黑也容易造粒。
相反地,比表面积高而结构低的炭黑或比表面积低而结构高的品种,则难于造粒。
为了引发造粒过程,因此将一部分母粒送回造粒机。
母粒回流量最好是造粒炭黑产量的5%-15%。
对难于造粒的炭黑品种,母粒回流量可高达50%。
对易于造粒的品种,母粒可以不回流或在造粒设备开始运转正常之后停止回流。
表2中数据表明,对实验所用的炭黑而言,随着母粒回流量的增加,细粉量和磨损量均开始减少,在回流量达到30%时,二者呈最小值;然后,随着回流量的进一步加大,二者又回升至较大值。
当回流量比较高时,粒子尺寸分布明显变窄,堆积密度稍有增加。
然而,粒子硬度几乎不受母粒回流量的影响。
应当强调,母粒的最佳回流量,取决于炭黑类型。
它必须由各种炭黑分别通过实验确定。
表10中数据仅是该实验炭黑(近似于N231)的测定结果。
搅齿轴转速当实验用造粒机的搅齿轴转速在150~500r/min内变化,搅齿尖的圆周线速度相当于在1~6m /s范围内。
搅齿轴转速与造粒性能之间的关系参见表3。
看来,随着搅齿轴转速的增加,细粉量和磨损量开始减少,粒子尺寸分布亦更窄。
当搅齿轴转速在400r/min时(搅齿尖线速度相当于4.2m/s),这3项指标均呈现一最小值。
尔后,随着转速的增加,它们又呈上升趋势。
当转速在500r/min(相当于搅齿尖线速度5.3m/s),粒子大量破碎,细粉量急剧增加。
粉状炭黑处理量为了考察造粒机的粉状炭黑处理量对造粒过程的影响,进料量从10kg/h至60kg/h变化,造粒产品质量数据参见表4。
从表中结果可知,细粉量与粉状炭黑处理量的多少无关,细粉量在1.4%~3.2%之间变化。
磨损量则随处理量的增加而减少。
应当指出,上述4项工艺条件对造粒质量的影响均是在特定的造粒机尺寸和一种实验炭黑条件下获得的数据。
为了在搅齿造粒机中造出合乎要求的炭黑粒,必须适当地调整操作参数,以与干法造粒的质量要求相匹配。
搅齿造粒机与转鼓造粒机串联尽管搅齿造粒机完全可单独用于干法造粒,制备出质量合乎要求的粒子,但另有一项技术方案是,把搅齿造粒机串联在传统的转鼓式造粒之前,使后者的生产能力提高1.5~2.5倍,大幅提高了设备效率。
实验炭黑,选用一种普通色素品种,其BET表面积为90m/g,DBP 吸油值52ml/100g,24M4DBP 值46ml/100g,粉状产品的堆积密度为194g/L。
实验用搅齿造粒机的设备尺寸与上述的相同。
其主要工艺参数为,搅齿轴转速350r/min,粉状炭黑进料量40kg/h,母粒回流量11kg/h。
在这种条件下干法制备的产品,再作为原料送入传统的转鼓造粒机中。
实验所用的转鼓造粒机,直径600mm,长度4000mm。
当造粒机以传统操作,送入粉状炭黑,处理量从10kg/h开始,以增量20kg/h逐步递增,到处理量为30kg/h时,造粒质量尚能满足要求;当处理量增至50kg/h时,已完全不能造粒。
当以搅齿造粒机的产品为原料时,该转鼓造粒机的炭黑处理量可达70kg/h。
搅齿造粒机中加入添加剂对干法造粒而言,Jordan曾开发了一种在粉状炭黑中添加2%-15%可溶于油墨的一种油料,然后再进行干法造粒"J。
这种造粒品要比普通的干法产品的粒子更牢固,而且很容易分散在油墨中。
这是由于粒子中炭黑的密度较低,而且又含有可溶于油墨的油料,所以分散效果颇佳。
后来,人们又尝试看向粉状炭黑中添加各种蜡,以不同方式进行造粒。
然而,在这些研究工作中,蜡的添加量普遍偏高,有的竞高达40%以上,影响到造粒品的应用。
最近,Vogler和Callahan 等人分别研究,将一种在环境温度下呈固态的可熔融材料,以低于10%的添加量,用于搅齿造粒机的干法造粒过程。
添加剂的添加位置及喷入方式研究,向粉状炭黑中加入熔融的蜡或蜡的混合物,以强化搅齿造粒机的干法造粒过程。
为了防止炭黑粘在造粒机筒壁及机内部件上,加蜡之后,整个造粒机的温度要比蜡的熔点高上10%~20%。
蜡的加入位置,要尽量靠近粉状炭黑入口,必须在造粒区的前三分之一段内将蜡喷洒到炭黑上。
这样,方能保证蜡尽可能早地与炭黑均匀混合。