边界润滑状态下往复摩擦磨损的数值仿真研究
边界润滑条件下表面微细织构减摩特性的研究
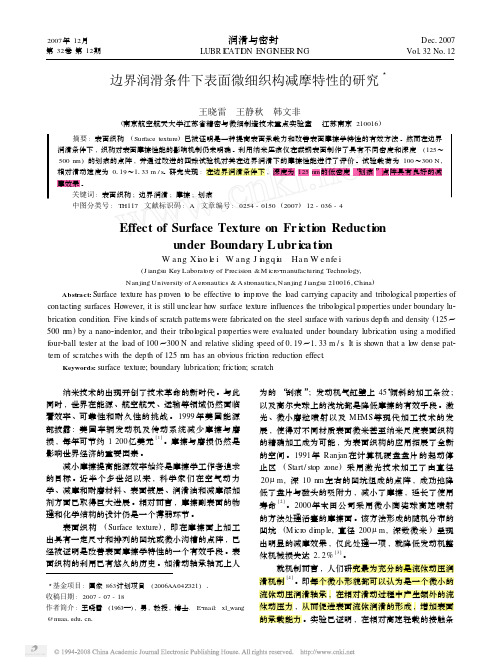
2007年12月第32卷第12期润滑与密封LUBR I CATI O N ENGI N EER I N GDec 12007Vol 132No 1123基金项目:国家863计划项目(2006AA04Z321)1收稿日期:2007-07-18作者简介:王晓雷(1963—),男,教授,博士.E 2mail:xl_wang @nuaa 1edu 1cn 1边界润滑条件下表面微细织构减摩特性的研究3王晓雷 王静秋 韩文非(南京航空航天大学江苏省精密与微细制造技术重点实验室 江苏南京210016)摘要:表面织构(Surface texture )已被证明是一种提高表面承载力和改善表面摩擦学特性的有效方法。
然而在边界润滑条件下,500n m )相对滑动速度为摩效果。
关键词:中图分类号:under Boundary Lubr i ca ti onW a ng Xi ao l e i W a ng J i ngq i u Ha n W e nfe i(J iangsu Key Laborat ory of Precisi on &M icr o 2manufacturing Technol ogy,Nanjing University of Aer onautics &A str onautics,Nanjing J iangsu 210016,China )Abstract:Surface texture has p r oven t o be effective t o i mp r ove the load carrying capacity and tribological p r operties ofcontacting surfaces .However,it is still unclear how surface texture influences the tribol ogical p r operties under boundary lu 2brication condition .Five kinds of scratch patterns were fabricated on the steel surface with vari ous dep th and density (125~500n m )by a nano 2indentor,and their tribological p r operties were evaluated under boundary lubricati on using a modified four 2ball tester at the load of 100~300N and relative sliding s peed of 0119~1133m /s .It is sho wn that a l ow dense pat 2tern of scratches with the dep th of 125nm has an obvious fricti on reducti on effect .Keywords:surface texture;boundary lubricati on;fricti on;scratch 纳米技术的出现开创了技术革命的新时代。
摩擦磨损过程的数值模拟与参数优化研究

摩擦磨损过程的数值模拟与参数优化研究摩擦磨损是指在两个物体之间接触和移动时,因摩擦力和接触力的作用,导致物体的表面互相磨擦而损耗的过程。
摩擦磨损现象在各个领域都存在,其产生的材料损失和能量消耗对机械设备的正常运行和寿命会产生影响,因此对摩擦磨损现象的研究显得至关重要。
目前,摩擦磨损过程的数值模拟是研究摩擦磨损过程的主要手段之一,它可以模拟摩擦磨损过程中的物理现象和变化规律,为摩擦磨损的机理研究提供了重要工具。
数值模拟的核心是建立物理模型和数值求解模型,因此,研究摩擦磨损过程的数值模拟需要从这两个方面进行探究。
一、物理模型的建立物理模型是指通过实验和理论分析,将待研究的物理过程描述为一个系统并建立它的数学模型。
对于摩擦磨损过程,建立物理模型的关键是确定模型的参数。
模型的参数包括材料性质、初始状态、摩擦系数、接触压力、接触面积等等。
对于材料性质的参数,要考虑材质的强度、硬度、韧性等因素,这些参数决定了材料的承载能力和抗摩擦磨损性能。
初始状态是指系统在开始模拟时的状态,如物体的初始位置、形状、速度等。
对于摩擦磨损过程,初始状态信息往往需要通过实验或者先前的仿真得到。
摩擦系数是描述物体表面间相互作用的参数,对模拟结果的精确度影响较大。
这个参数可以通过实验的方法或者利用现有的材料模型计算得到。
接触压力和接触面积是描述物体之间接触状态的两个重要参数,这些参数影响了摩擦力的大小和方向。
这些参数可以通过实验或者计算得到。
除了这些参数外,物理模型的建立还需要考虑各个过程的边界条件,以及各个过程之间的联系。
二、数值求解模型的建立在建立了物理模型之后,需要进行数值模拟计算。
应用数值模拟方法进行计算,需要建立出相应的数值求解模型。
这涉及到很多数学和计算机方面的知识。
对于摩擦磨损过程的数值模拟来说,数值求解模型需要包括以下几个方面的内容:第一,要考虑计算的时间和空间范围。
因为计算范围越大,计算量就会越大,因此需要考虑合适的时间和空间分辨率。
摩擦磨损行为的试验与数值模拟

摩擦磨损行为的试验与数值模拟摩擦磨损是日常生活中常见的现象,也是工程领域中一个重要的研究课题。
摩擦磨损现象的发生和演化对材料的性能和使用寿命具有直接影响。
因此,准确地理解和预测摩擦磨损行为对于材料的设计和优化至关重要。
为了更好地研究摩擦磨损行为,科研人员常常利用试验和数值模拟的方法进行深入研究。
试验是研究摩擦磨损行为最直接的方法之一。
研究人员可以通过设计并制造实验装置,在特定的加载和环境条件下,对不同材料进行摩擦磨损试验。
试验中常常使用摩擦系数、磨损量和磨损形貌来表征摩擦磨损行为。
通过试验,可以获得大量实验数据,用于分析和总结摩擦磨损行为的规律和机理。
然而,试验也存在一些局限性。
首先,试验过程受到试验装置的约束,很难模拟真实工况下的复杂摩擦磨损行为。
其次,试验数据量庞大,分析起来相对困难,并且很难得到全面覆盖各种参数和情况的数据。
这就需要借助数值模拟的手段来补充试验的不足。
数值模拟是通过计算机仿真方法来模拟和预测摩擦磨损行为的一种有效手段。
通过建立摩擦磨损的数学模型和物理模型,可以用数值方法对摩擦磨损过程进行模拟。
数值模拟可以灵活地设置参数和条件,用于研究试验中难以获得的细节和机理。
同时,数值模拟还可以节省大量的实验成本和时间,提高研究效率。
在摩擦磨损数值模拟中,常用的方法包括有限元法、分子动力学模拟和颗粒流模型等。
有限元法是一种基于连续介质力学原理的数值方法,适用于宏观尺度的研究。
分子动力学模拟则是基于原子分子层次上相互作用的数值模拟方法,适用于微观尺度的研究。
颗粒流模型则是一种基于颗粒物质运动的数值模拟方法,适用于中等尺度的研究。
这些方法分别适用于不同尺度的摩擦磨损研究,可以提供不同层面的信息和理解。
数值模拟在摩擦磨损研究中的应用非常广泛。
通过数值模拟,可以模拟和分析不同材料、表面形貌、加载条件下的摩擦磨损行为。
特别是在材料设计和优化中,数值模拟可以帮助研究人员快速预测材料的摩擦磨损性能,从而指导实验设计和材料选择。
基于润滑分析的活塞环二维磨损数值模拟研究

未 i 蕃 (鑫 萼 u L ( ) Li )6・ 』 蕊 J a + 未 = ’
d +6 d + d , … … … … ㈩ u £ 其中 . 面粗糙 效 应 是 由压 力 流 量 因子 吼 , 和剪 表
百 , … …… 。 J 。
进行 了讨 论 。
其 中, , 分别为燃气压力和活塞环弹力 , 和 分别为峰元承载和油膜承载 。
14 磨 损模 型 .
在正 常运 行情 况 下 , 内燃 机 零 部 件 特别 是 活 塞 环 的磨 损 形式 , 常见 和最 重 要 的 是 粘着 磨 损 外 加 最
1 计算模型
张 勇
50 4 ) 160 ( 南- - 华 - 大学,广 东 广州 ' XJ
摘要 : 进行 了活塞环 的二 雏磨损分析 , 解 了二 雄宙诺方程 、 联 膜犀 方程和 栽荷平衡 方程 , 分析 了活塞 环磨损量
及 磨 损 极 限 , 以试 验 结 果 对理 论 分 析散 了验 证 。 并
状态 , 然后对各结构和运行参数进行调整 , 对结果做 了对 比分 析 。磨 损 系 数 对 磨 损 量 的计 算 有 重 大 影 响 , 步 选 定 活 塞 环 取 17 ×1 , 缸 套 取 初 .8 0 气
7. 4× 1 8 0~ 。
2 数值求解过程及计算结果
以发动机活塞的第一道环为例计算分析活塞环 的磨损 量 。为此 需 要 了解 活塞 环 表 面 的载 荷 分 布 , 可先对活塞环—气缸套摩擦副进行润滑计算 , 以得
一
定 磨损 后 的活塞 环横剖 面 为抛 物线 型 :
h * x ……… …… …… () ( )= 3
一
。
大影响 , 并进一步影响到发动机的经济性 、 动力性和
摩擦学学报---磨损数值仿真技术的研究进展

第24卷 第2期摩擦学学报Vol24, No2 2004年3月TRIBOLOGY March,2004磨损数值仿真技术的研究进展汪选国,严新平,李涛生,吴 刚(武汉理工大学可靠性工程研究所,湖北武汉 430063)摘要:综述了近年来国内外磨损数值仿真技术研究进展和现状,重点评述了数值仿真方法在磨粒磨损、疲劳磨损、磨损表面形貌模拟和实际摩擦副磨损研究方面的应用.指出磨粒磨损仿真主要集中于二体磨损的磨损表面形貌分析和磨损预测;疲劳磨损仿真主要集中基于断裂力学方法的建模以及基于有限元方法的参数定量计算和疲劳裂纹行为数值模拟;实际摩擦副磨损仿真主要侧重于齿轮、凸轮和缸套 活塞环等典型摩擦副的磨损研究.就当前磨损数值仿真研究的主要问题和发展方向提出了建议.关键词:磨损仿真;磨粒磨损;疲劳磨损中图分类号:TH117.3文献标识码:A文章编号:1004 0595(2004)02 0188 05多年以来,摩擦学界在磨损机理、摩擦学系统分析理论与方法、磨损表面微观分析等方面进行了大量的研究[1~3].但磨损研究方法大多集中于实验研究,即要求针对某种标准试样,以某种选定的试验条件在专门的试验机上进行大量模拟试验,以进行经验性探索[4].这种实验研究方法耗费大量时间、人力、物力和财力,而由于实际摩擦学系统的复杂性和不同工况,某些模拟试验结果不能很好地用于摩擦学系统设计和实际工程应用,如磨损寿命预测、磨损动态监测和耐磨性设计等[4].而数值仿真技术可以弥补这些不足,为摩擦学研究提供了一种新的手段[4~7].将数值仿真技术用于摩擦学系统研究,在分析和研究摩擦学系统的基础上建立仿真模型,进而利用计算机对模型进行改进和完善,将显著提高摩擦学研究的效率和摩擦学系统特性预测的准确性[4].本文概述了当前磨损数值仿真技术研究的进展和现状,并提出今后的研究方向.1 磨粒磨损的数值仿真磨粒磨损指外界硬颗粒或对摩表面硬突起物在摩擦过程中引起表面材料脱落的现象[1].Rabinowicz 建立了关于磨粒磨损的经典模型[2],有关磨粒磨损的仿真研究大多立足于该经典模型.表面形貌对摩擦副性能的影响很大,由磨损和塑性变形引起的表面粗糙度变化是摩擦学系统性能具有时变特性的主要原因之一[8].因此,合理设计以及正确预测摩擦副的表面粗糙度很有必要.Zhang 等[9~11]基于随机过程理论提出了描述二体磨损过程中摩擦副表面形貌变化的磨损动态过程理论,在此理论基础上建立了软表面受硬表面微切削时表面粗糙度及磨损量的预测模型;该模型假设硬表面是绝对硬的刚体,不发生变形或磨损.刘峰壁等[8,12,13]在Zhang等的研究基础上建立了用于预测二体磨损过程中两磨损表面均发生磨损时的表面粗糙度及磨损量的模型;针对粗糙表面三体接触建立了数学模型,分析了三体接触中接触表面间距离和塑性变形量同第三体磨粒粒度分布、外载荷、接触表面微观几何参数及材料硬度之间的关系;并建立了三体磨粒磨损过程中摩擦副表面粗糙度的预测模型.在磨粒磨损过程中,有的磨粒参与磨损过程,有的则不参与,表现出统计学特征.Jacobson等[14]建立了考虑多个磨粒同时作用的纯切削过程的统计学模型,利用该模型研究了磨粒尺寸、载荷及工件表面硬度对磨损率的影响,预测了发生接触的磨粒数量和磨损表面形貌.Jiang等[15]对Jacobson等的模型进行了修正,从而使得修正模型能够反映磨损表面形貌变化及磨损模式对磨损过程的影响.Podra等[16]建立了锥形接触时考虑表面形貌影响的磨粒磨损模型,并利用有限元法和解析法计算了相应的磨损,发现由2种计算方法得到的结果相差较大,并指出其原因可能在于基金项目:湖北省自然科学基金资助项目(2002AB017).收稿日期:2003 05 29;修回日期:2003 09 02/联系人严新平,e mail:xpyan@mail.w .作者简介:严新平,男,1959年生,博士,教授,博士生导师,目前主要从事设备诊断工程、摩擦学技术应用和智能交通等方面的教学与科研工作.采用解析方法时未考虑弹性变形的影响.Peterseim 等[17]针对销 盘摩擦磨损试验数值仿真建立了模型,并开发了仿真计算的计算机程序;通过改变材料和试验的输入参数(销的结构、试验时间、载荷、试盘或砂纸特性参数等),可以计算磨损体积损失和磨损表面形貌参数.Li等[18]建立了微观动态磨损仿真模型,用以模拟磨损过程和预测磨损过程中材料性能的变化. Elalem等[19]利用该模型研究了几种金属材料的磨粒磨损性能,发现理论分析结果同试验结果相一致. N icholls等[20]用M onte Carlo方法模拟材料冲蚀磨损过程的随机特征,通过采用统计分布来描述每一种状态下的磨粒尺寸、材料性能和冲击速度,并计算每一次离散冲击磨损量以确定由所有离散冲击所造成的总磨损量.吴国清等[21,22]将M onte Carlo方法与数值模拟相结合,提出了二体磨料磨损的三维仿真模型,并利用该模型分析了磨粒粒度、尖锐度和圆锥度对磨损率的影响,发现粒度、尖锐度和圆锥度相互影响并共同决定磨粒的尺寸效应.综上所述,目前关于磨粒磨损的仿真研究主要集中于二体磨损的表面形貌和磨损预测,对三体磨损的仿真研究较为欠缺.同经典磨损计算方法相比,在磨粒磨损仿真研究中引入随机过程理论和统计学原理具有明显的优势.为了更精确地模拟二体磨损过程,需引入更多的影响因素以综合考虑整个磨损过程.2 疲劳磨损的数值仿真疲劳磨损指2个相互滚动、滑动或滚动兼滑动的磨损表面在循环接触应力作用下局部引发裂纹,裂纹逐步扩展,最后导致材料剥落的磨损过程[3].在各种磨损形式中都不同程度地存在疲劳过程,因此对疲劳磨损的研究一直受到广泛关注.Kapoor等[23]建立了韧性金属材料在循环滚动接触时的表面剥层磨损模型,并利用力学原理,将材料的磨损率同载荷、接触体的粗糙度、表面层材料的弹塑性联系起来,通过计算机仿真计算得到材料表面的磨损深度;但该模型没有考虑塑性变形导致的材料性能变化.为此,Franklin等[24]对上述模型进行了改进和完善,从而可以较为真实地反映微观结构变化而引起的材料性能的统计变化.Flasker等[25,26]针对机械零件滚动和滑动接触时表面疲劳点蚀建立了仿真计算模型,并研究了不同接触表面和接触载荷下点蚀的形状以及应力强度因子同裂纹长度的关系,并将该模型用于2个啮合齿轮齿的表面点蚀仿真.O Neil等[27]用有限元方法研究了涂层材料在不同接触载荷下疲劳裂纹的形成和扩展过程.Chue 等[28]用断裂力学方法分析了滚动接触过程中应变硬化层对点蚀形成的作用,用二维有限元方法计算了 型和 型应力强度因子和应变能强度因子,计算分析预测结果与试验结果吻合.林刚等[29]利用弹性接触理论对接触面的切应力和法向应力进行叠加,然后经数值积分求出接触表面附近区域的应力曲线,进而研究了疲劳磨损、剥层磨损和压碎磨损机理.Fleming 等[30]利用线弹性断裂力学方法研究了亚表层裂纹沿滑动反方向扩展的模型,指出在接触区前方塑性变形区受压缩应力作用导致裂纹闭合,在接触区后方塑性变形区受拉伸应力作用导致裂纹扩展.Kimura等[31]基于磨损的剥层理论提出用纵向点接触模型评价裂纹尖端的应力强度因子(K 、K 、K ),并利用有限元法计算了钢和Si3N4的I形和L形裂纹扩展应力强度因子K 、K 、K 分布及其最大值.Ghorbanpoor 等[32]用有限元法模拟了磨粒磨损中以 型断裂为主导的裂纹萌生和扩展行为,发现应力强度因子K 随摩擦力的增大而增大,在与滑动方向大致成135 处达到最大值,裂纹扩展进入亚表层.在复合载荷作用下裂纹在某一临界深度沿滑动平行方向移动,最终遇到另一裂纹而发生片状剥层.Glodez等[33]用有限元法计算分析了基于圆柱体接触等效模型的应力强度因子同裂纹长度的定量关系,并对齿轮齿侧面的点蚀磨损进行了数值模拟研究.Komvopoulos等[34]用线弹性断裂力学和有限元法研究了均匀半平面在移动磨粒作用下的亚表层裂纹扩展行为,并阐述了裂纹长度与深度的比、接触区和裂纹界面的摩擦以及加载历程对 型和 型裂纹扩展方向的影响.Zhang等[35]用有限元法和最大拉应力准则分析了往复滑动半平面的表面裂纹扩展,发现裂纹屏蔽效应随裂纹间距减小而增强.此外,很多研究者将线弹性断裂力学和弹塑性断裂力学与有限元方法相结合来建立仿真模型,并利用仿真模型研究了磨损过程中疲劳裂纹的扩展行为.总体而言,疲劳磨损的数值仿真研究主要集中于用力学和断裂力学方法建立疲劳磨损模型,用有限元法进行参数定量计算和疲劳裂纹行为的数值模拟.由于疲劳磨损过程相当复杂,影响因素众多,必须建立切合实际的疲劳磨损力学模型.3 磨损表面形貌的数值仿真在磨损仿真研究中,首先应确定接触表面的形貌.目前,主要应用随机过程理论和统计学原理对表189第2期 汪选国等: 磨损数值仿真技术的研究进展面形貌进行数值模拟,以保证模拟表面与真实表面具有类似的统计学特征.黄逸云等[36,37]提出了关于随机表面形貌分析的计算机模拟方法.吴国清等[21,22]用Monte Carlo法模拟随机砂纸表面.Gu等[38]研究了真实表面的仿真方法,该仿真表面与真实表面的统计特征类似,只要将真实表面不同方向的轮廓参数输入计算机即可获得模拟表面,仿真结果与实际表面具有统计学上的一致性.M ajum dar等[39]指出粗糙表面具有分形特征,并用Weierstrass Mandelbrot(W M)分形函数来模拟粗糙表面,提出确定分形维数的方法.4 数值仿真在磨损研究中的应用除了前述有关磨损仿真的理论研究外,磨损仿真在实际摩擦副的磨损研究中也得到了应用.Lundvall 等[40]研究了2个弹性体接触时的磨损计算,并将相关结果应用于齿轮的仿真计算,发现齿轮的主要磨损形式为轻微磨损;这种轻微磨损可导致齿轮表面形貌和尺寸变化,引起齿轮的不均匀啮合甚至断裂失效. Flodin等[41]针对齿轮轻微磨损预测建立了数值仿真模型,指出可以将整个仿真过程视作初始值问题,而由于每一个啮合周期都会产生一定的磨损而使表面尺寸发生改变,故总的磨损是所有啮合周期所产生的磨损的总和.Olofsson等[42]研究了圆柱推力轴承在边界润滑状态下的磨损仿真,并用试验数据验证了仿真结果.江亲瑜等[4,5]利用离散数学理论,将数值方法和计算机相结合,提出了摩擦副磨损全过程的动态数值仿真模型,并用该模型研究了凸轮和齿轮的光面磨损,开发了相应的仿真计算软件.严立等[6]提出了利用智能仿真技术求解磨损问题的方法.他们在磨损试验、机理研究和系统分析的基础上,采用模糊推理和智能仿真方法对磨损状况进行演绎,利用有关基础理论、试验资料和经验知识,建立了包含灰匣、黑匣以及推理机构的框形综合仿真模型,进而评价系统的耐磨性能,预测其发生故障的可能性及使用寿命.他们还以船用柴油机缸套活塞环系统为例,通过摩擦学系统分析建立了仿真模型,并实现了计算机求解.潘尔顺等[43]从边界元的基本思想出发,将渐开线直齿圆柱齿轮简化为端面进行分析,从而将空间啮合问题简化为平面啮合问题,将边界曲线离散成许多的单元和结点,以计算任意啮合点的磨损量.左玉梅等[44]以凸轮挺柱为研究对象,在Archard模型基础上,考察了表面形貌对凸轮摩擦磨损性能的影响,并建立了内燃机凸轮挺柱在边界润滑状态下的摩擦磨损数学模型,提出了计算方法.孔凌嘉等[45,46]结合润滑状态建立了同时考虑边界润滑状态下二体磨损和三体磨损的内燃机缸套 活塞环系统的综合磨损模型,该模型可反映磨粒大小、分布及浓度对磨损的影响.刘[47]将系统分析方法和摩擦学行为相结合,以Archard磨损模型和系统论为基础,研究了磨粒浓度对缸套 活塞环磨损的影响,并基于台架试验结果建立了描述磨粒浓度动态变化对磨损影响的传递函数模型.在工程应用领域,关于摩擦副磨损仿真的研究主要着眼于齿轮、凸轮和缸套 活塞环系统.相关研究以Archard磨损模型为基础,并在仿真计算过程中适当考虑磨损过程中表面形貌和接触应力的变化.5 结束语数值仿真方法作为新的磨损研究手段和方法已引起摩擦学界的重视,并将发挥越来越重要的作用.目前关于磨损仿真研究的主要不足在于:磨损仿真模型预测结果同实际情况相差较大;建立仿真模型时的简化处理导致模型精确度不够高;利用Archard等经典磨损模型进行仿真计算时缺乏关于材料磨损率规律的准确数据.磨损仿真结果的可靠性和实用性在很大程度上取决于磨损模型的正确性和精确性.为了更好地发挥数值仿真方法在摩擦磨损研究中的作用,应在深化磨损机理研究、摩擦学系统分析方法及磨损表面微观分析的基础上建立更加完善和切合实际的磨损模型,并通过大量实验研究确定关于磨损率规律的准确数据.目前摩擦学仿真应用大多集中于特定的单个零件或摩擦副磨损的研究.今后应大力加强以下几方面的研究.首先,应加强磨损机理的仿真研究,并通过建立仿真模型以及进行理论和实验研究结果对比验证已有理论的正确性.其次,应在利用成熟的理论和模型的基础上实现磨损研究的定量化,以指导产品设计、零件优化设计、材料选择、寿命设计以及耐久性设计等.第三,应在仿真计算过程中考虑多因素的影响,以提高仿真结果的准确性和可靠性.第四,应该加强典型磨损试验的仿真研究,以减少磨损试验工作量,提高摩擦磨损测试效率.第五,应该加强机械系统的仿真及建模研究,从而实现系统运行过程的动态仿真以及系统状态的实时监控和预测.参考文献:[1] 温诗铸.摩擦学原理[M].北京:清华大学出版社,1990.190摩 擦 学 学 报 第24卷[2] 肖祥麟.摩擦学导论[J].上海:同济大学出版社,1990.[3] 张嗣伟.基础摩擦学[M].东营:石油大学出版社,2001.[4] Jang Q Y(江亲瑜),Li B L(李宝良).A softw are for w ear numerical simulati on of cam follow er systems(凸轮机构磨损数值仿真软件研究)[J].Lubricati on Engineering(润滑与密封),2000,(4):2 4.[5] Jiang Q Y(江亲瑜),Li M L(李曼林),Dong M Y(董美云),etal.Numerical simulati on of spur gears(渐开线齿轮磨损的数值仿真)[J].Journal of Dalian Railw ay Institute(大连铁道学院学报),1999,20(1):13 18.[6] Yan L(严立),Xu J J(徐久军).Research on th e si mulationmethod of w ear process(磨损问题的仿真求解研究)[J].Tribology(摩擦学学报),1999,19(1):50 55.[7] Yuan C Q(袁成清),Yan X P(严新平),Peng Z X(彭中笑).Review of Proceedi ngs of14th International Con feren ce on W ear ofM ateri als(关于第14届材料磨损国际会议的简要评述)[J].T ribol ogy(摩擦学学报),2003,23(4):356 360.[8] Liu F B(刘峰璧),Xie Y B(谢友柏).A prediction model for tw obody w ear proces s(二体磨损过程预测模型)[J].Journal of Xian Jiaotong University(西安交通大学学报),1998,32(2):20 23.[9] Zhang B,Xie Y B.Tw o body micro cutting wear model,Part I:Tw o dimensional roughness model[J].Wear,1989,129:37 48.[10] Zhang B,Xie Y B.Tw o body micro cutti ng w ear model,Part II:T hree dimensional roughness model[J].Wear,1989,129:49 58.[11] Zhang B,Xie Y B.Tw o body micro cutting wear model,Part III:Stable profile height distribution of a worn surface[J].Wear,1989,129:59 66.[12] Liu F B(刘峰璧),Li X E(李续峨),Xie Y B(谢友柏).Theoretical investigation on three body contact of rough s urface(粗糙表面三体接触理论研究)[J].C hi n ese Journal of M echanical Engineering(机械工程学报),1997,33(3):27 31.[13] Liu F B(刘峰璧),Li X E(李续峨),Xie Y B(谢友柏).A newmodel for predicting roughness of rubbing surface i n three bodyabrasive wear(三体磨损过程理论研究)[J].Chinese Journal ofM echanical Engineering(机械工程学报),2000,19(1):9 12. [14] Jacobson S,Wallen P,Hogmark S.Fundamental aspects of abrasive w ear studied by a n ew numerical simulation model[J].Wear,1988,123:207 223.[15] Jiang J R,S heng F H,Ren F S.M odeling of tw o body abrasivew ear under multiple contact conditions[J].W ear,1998,217:3545.[16]Podra P,Andersson S.Fi nite element analysis of w ear si mulationof a conical spinning contact considering surface topography[J].Wear,1999,224:13 21.[17] Peterseim J,Elsing R,Deuerler F.S imulation of sliding w ear ofhard phase containing metallic compound material s[J].M etall(Germany),1998,52:643 651.[18]Li D Y,Elalem K,Anderson M J,et al.A microscale dynamicalmodel for w ear simulation[J].Wear,1999,225 229:380 386. [19] Elalem K,Li D Y.Dynamical simul ation of an abrasi ve w ear process[J].Journal of Computer Aided M aterials Design(Netherlands),1999,6:185 193.[20] Nicholl s J R,Stephenson D J.M onte carlo modeling of erosi onprocesses[J].Wear,1995,186 187:64 77.[21] W u G Q(吴国清),Zhang X F(张晓峰),Fang L(方亮),et al.3D dynamic simulation of tw o body abrasion(两体磨料磨损的三维动态模拟)[J].Tribology(摩擦学学报),2000,20(5):360 364.[22] Wu G Q(吴国清),Fang L(方亮),Xing J D(邢建东),et al.Stochasti c simulation to the effect of abras i ve parameter on abrasive w ear(磨料尺寸对磨料磨损过程影响的的随机模拟)[J].Journal of Xi an Jiaotong University(西安交通大学学报),2001,35(5):527 531.[23] Kapoor A,Fran kli n F J.Tribological layers and the w ear of ductilematerials[J].Wear,2000,245:204 215.[24] Frankli n F J,Widiyarta I,Kapoor puter simulati on ofwear and rolling contact fati gue[J].Wear,2001,250 251:949955.[25] Flasker J,Fajdi ga G,Glodez S,et al.Numerical simulation ofsurface pitting due to contact loadi ng[J].International Journal ofFatigue(UK),2001,23(7):599 605.[26] Ren Z,Glodez S,Fl asker J.S i m ulation of surface pitting due tocontact loading[J].International Journal for Numerical M ethods in Engineering(UK),1998,43(1):33 50.[27] O Neil D A,Wayne S F.Numerical simulation of fracture in coated brittle materials subjected to tribo contact[J].J Eng M aterTechnol(Trans ASM E),1994,116(4):471 478.[28] Chue C H,Chung H H,Lin J F,et al.The effects of strai n hardened layer on pitting formation during rolling contact[J].W ear,2001,249;109 116.[29] Lin G(林刚),Xie J P(谢敬佩),Yang P R(杨茹萍),et al.Stresscomputati on of fatigue w ear and crush w ear(疲劳磨损和压碎磨损的应力计算)[J].Journal of Louyang Institute of T echnology(洛阳工学院学报),1994,15(3):13 18.[30] Fleming J R,Suh N P.M echanics of crack propagation in delamination w ear[J].W ear,1977,44:39 56.[31] Kimura Y,S hima M.Longitudinal contact point model for calculating stress instensity at s urface cracks in sliding wear[J].W ear,1991,141:335 347.[32] Ghorbanpoor A L,Ziiang J.Crack behavior for sliding contactproblems[J].Eng Fract M ech,1992,41(1):41 48.[33] Glodez S,W i nter H,Stuw e H P.A fracture mechanics model forthe w ear of gear flanks by pitting[J].Wear,1997,208:177 183.[34]Komvopoulos K,Cho S S.Finite element analysis of subsurfacecrack propagation in a halfspace due to a moving asperity contact[J].W ear,1997,209:57 68.[35]Zhang H Q,Sadeghipour K,Baran G.Numerical study of polymers urface w ear caused by sliding contact[J].W ear,1999,224:141 152.[36] Huang Y Y(黄逸云),Gu J X(顾新建).Computer si mulation ofrandom surface topography(随机表面形貌的计算机模拟)[J].Lubrication Engineering(润滑与密封),1990,(5):4 7.[37]Gu J X(顾新建),Huang Y Y(黄逸云).T he amplitude distribution fun ction of random rough surface and its simulation method(随191第2期 汪选国等: 磨损数值仿真技术的研究进展机粗糙表面的幅值分布函数及其模拟方法的探讨)[J].Journal of M echanical Science and Technology(机械科学与技术),1991,38(2):78 82.[38] Gu X J,Huang Y Y.T he modeling and simulation of a rough surface[J].Wear,1990,137(2):275 285.[39] M aj umdar A,Tien C L.Fractal characterization and simulation ofrough surfaces[J].Wear,1990,136(2):313 327.[40] Lundvall O,Klarbring A.Simulation of w ear by use of a nonsmooth Newton i an m ethod a spur gear appli cati on[J].M echanics of Structures and M achines,2001,29(2):223 238. [41] Flodin A,Andersson S.Simulation of mild w ear in spur gears[J].W ear,1997,207(1 2):16 23.[42] Olofsson U,Andersson S,Bj orklund S.S i mulation of mild w ear inboundary lubricated spherical roller thrust bearings[J].Wear,2000,241(2):180 185.[43] Pan E S(潘尔顺).Computer simulati on of gearing about load,stress and w ear in meshing process(齿轮啮合过程中载荷、应力及磨损的计算机模拟)[J].Journal of M echanical Science and Technology(机械科学与技术),2000,19(1):40 41.[44] Zuo Y M(左玉梅),M a L(马力),Tang S X(唐少雄),e t al.Research on a calculation method of w ear value of a cam follow er i n ani nternal combustion engine(内燃机凸轮挺柱磨损数值计算方法的研究)[J].Journal of Wuhan University of Technology(Informa tion&M anagement Engineeri ng)[武汉理工大学学报(信息与管理工程版)],2001,23(3):40 43.[45] Kong L J(孔凌嘉).A tribological system study of the cylinder liner piston ring in i nternal combustion engines(内燃机缸套 活塞环摩擦学系统研究)[D].Xi an(西安):Xi an Jiaotong University(西安交通大学),1991.[46] Kong L J(孔凌嘉),Xie Y B(谢友柏).Calculati on of blow bygas,lubrication,fri ction and w ear in cylinder li n er piston ri ngs tribo systems(缸套 活塞环摩擦学系统漏气与润滑和磨损的计算)[J].Transactions of CSICE(内燃机学报),1992,10(3):267264.[47] Liu K(刘).Study on frictional and lubricating characteri stics ofa cylinder liner piston rings systems and establishment of w earmodel(缸套 活塞环系统摩擦、润滑特性的研究及磨损模型的建立)[D].Xi an(西安):Xi an J i aotong Universi ty(西安交通大学),1995.Research Status of Wear Numerical Simulation TechnologyWANG Xuan guo,YAN Xin ping,LI T ao sheng,WU Gang(Reliability Engineer ing I nstitute,Wuhan U niver sity of T echnology,W uhan430063,China)Abstract:The current state and prog ress of the study on w ear numerical sim ulation technolog y w ere summarized. T he application of numerical simulation methods to the study of abrasive w ear mechanism,fatig ue w ear mecha nism,w orn surface topography,and w ear prediction and calculation of components w as reviewed.It w as pointed out that the abrasive w ear simulation study was mainly concentrated on the prediction of tw o body wear,w hile the fatigue w ear simulation w as focused on the establishment of the model making use of fracture mechanics and finite element methods,by accounting for the parameters quantitative calculation and numerical simulation of the fatigue crack behavior.Besides,the wear simulation of practical frictional parts w as concentrated on the w ear analysis of g ear cam and cylinder liner piston ring systems.The problems to be solved and the future directions to be furthered w ere sug gested as w ell.Key words:w ear sim ulation;abrasive wear;fatigue w earAuthor:YAN Xin ping,male,born in1959,Ph.D.,Professor,e m ail:x pyan@m 192摩 擦 学 学 报 第24卷。
基于Archard修正模型的角接触球轴承磨损有限元分析

基于 Archard 修正模型的角接触球轴承磨损有限元分析
高恒强1, 蔡红娟2, 蔡苗2
(1������ 中国地质大学 ( 武汉) 机电学院, 湖北武汉 430074; 2������ 武昌首义学院信息科学与工程学院, 湖北武汉 430064)
摘要: 在分一定条件下接触区滑动速 度的分布, 指出了球在滚道上运动时纯滚动点的存在。 开展了球盘摩擦磨损试验, 得到了轴承钢在边界润滑条件下的摩擦 因数和磨损系数。 利用有限元方法和 Archard 磨损计算模型, 建立了球与内圈磨损的仿真计算模型, 并分析了运行时间、 径向载荷、 接触角等因素对轴承磨损的影响。
并 分 析 了 计 算 结 果 的 可 靠 性。 FENG 等[ 6 ] 利 用 Archard磨损理论建立了球轴承的磨损寿命模型, 并 通过球板磨损试验研究了载荷和润滑条件等因素对磨 损系数的影响。 以上研究采用磨损模型对滚动轴承的 接触面磨损进行了仿真计算。 但是, 计算精度或预测 效果却有 较 大 误 差, 主 要 原 因 是 磨 损 模 型 还 不 够 理想。
关键词: 角接触球轴承; Archard 模型; 有限元仿真; 磨损 中图分类号: TH12 文献标志码: A 文章编号: 1001-3881 (2018) 15-159-6
Finite Element Analysis on Wear of Angular Contact Ball Bearing Based on Archard Revision Model
Keywords: Angular contact ball bearing; Archard model; Finite element simulation; Wear
0 前言 角接触球轴承因其高速、 高精度、 高刚度及可同
边界润滑条件下的磨损实验
边界润滑条件下的磨损实验1王慰祖,黄平1华南理工大学机械工程学院(510640)Email: marsworm_@摘要:使用45#钢作为材料的球盘进行实验,其中盘的粗糙度分别为0.4μm,0.8μm和1.2μm,润滑剂分别使用150SN基础油和添加了油酸的150SN基础油。
利用Talysurf CLI 1000测量钢盘的磨损量。
实验表明添加剂可以有效减小磨损量。
关键词:边界润滑 磨损 吸附膜中图分类号:TH117.21.引言边界润滑一直是摩擦学研究的重要方向,边界润滑问题在卫星轴承、微机器人以及仪器设备的启动和停车过程中都普遍存在,而超负荷、制造误差等因素也能使设备处于边界润滑状态。
边界润滑条件下,膜厚很薄,通常只有几个分子层的厚度,摩擦副之间存在摩擦副的直接接触,润滑性能会受到摩擦副表面特性和润滑剂分子特性的影响[1,2]。
本文主要介绍边界润滑条件下的磨损实验。
润滑试验在处于油池中的球盘机构上进行,使用Talysurf CLI 1000表面轮廓仪测量钢盘的表面磨损情况,测量采用CLA聚焦测法,量程选用3 mm。
2.实验介绍2.1 润滑实验实验采用球-盘机构,具体尺寸如图1所示。
上方的球保持静止,下方的盘可以恒速转动,盘由变速电机带动。
实验数据由通过电路由计算机实时采集。
实验中的球盘都采用45#钢,实验中使用的钢盘的粗糙度分别为0.4μm,0.8μm和1.2μm,润滑剂分别采用150SN的基础油和添加油酸的150SN润滑油,其必要特性和实验数据见表1。
正式实验之前,系统有5分钟的跑合时间,以除去试样表面的毛刺。
实验中采用了电阻11本课题得到高等学校博士学科点专项科研基金(项目编号:20020004020)资助- 1 -法来辅助判断边界润滑状态。
实验采用0.068 m/s 和0.3 m/s 两种速度,载荷为18.5 N ,每个试样的摩擦时间为一小时在测量之前,盘和球都用乙醚清洗过。
表5-1 150SN 基础油特性参数数值 40℃时的运动粘度 (cSt ) 30 100℃时的运动粘度 (cSt )5 粘度指数100 25℃时的密度 (g/ml)0.8432.2 表面轮廓测量磨损的测量使用英国Talyor Hobson 公司出品的Talysurf CLI 1000型表面轮廓仪,仪器照片如图2所示。
边界润滑过程中摩擦化学反应机理的研究进展
摩 擦 化 学是 摩 擦 学 的 一 个 重 要 分 支 , 化 学 是 与摩 擦 学 的 一个 交 叉 学 科 , 主要 研 究 相 对 运 动 中
自身 的工 作需 要 , 择 其 中具 有 代 表 性 的 文献 进 行 选 了整理 , 希望 可 以 为今 后 添 加剂 的研 发 工 作 提供 方
润
滑
油
21年第2卷 01 6
轮、 凸轮 、 蜗杆 和活 塞环等 部件 的工作 环境 。 边 界润 滑 状 态 下 摩 擦 表 面 之 间 的 凹 凸处 发 生
碰撞 , 根据 负 荷 和 材 料 性 质 的 不 同 , 面 会 发 生 局 表 部 弹性 形 变 和 塑 性 形 变 , 刻 条 件 下 还 会 发 生 断 苛 裂 。随之 发 生能 量 释放 如 机械 能 和 热 , 造成 接 触 点
() 3 摩擦化学反应 的产物对于摩擦过程 中润滑 效果起到了举足轻重的作用 ; () 4 基础油 的黏度对于摩擦磨损的影响很小 ; () 5 一般 发生在 低 速 高 负荷 的工 况 , 轴承 、 如 齿
具体来说 , 摩擦化学重点是对 添加剂在摩擦过 程中的作用机理进行研究 , 这对于提高添加剂开发
氧化时间/ n mi
图 3 2 5 下 不 同金 属 对 酯类 基 础 油 的 氧化 催 化 作 用 2℃
似 ; 2是 SC表 面 有 效 的 润 滑 膜 。 因 为 SC 比 图 i i
SN 的脆 度 要 大 , 要 形 成 更 厚 的润 滑 膜 才 能 起 i 需 到 降 低 摩 擦 的作 用 。
剂 的发 展 趋 势 对 今 后 摩 擦 化 学 的 热 点 问 题进 行 了 总结 和展 望 。
关键词 : 摩擦化 学 ; 边界润滑 ; 添加剂 ; 摩擦化 学反应
往复活塞杆密封圈磨损的仿真
往复活塞杆密封圈磨损的仿真李鑫;冯海生【摘要】对往复运动活塞杆上的橡胶密封圈进行了磨损仿真研究.建立了密封圈与活塞杆接触的有限元模型,考虑到活塞杆采用车削的方式加工,用正弦函数表征活塞杆接触表面形貌、密封圈橡胶材料的非线性特性和外部高温高压环境因素,利用有限元技术中的生死单元技术模拟密封圈材料的损失.结果表明,高压力将导致较大的磨损深度,高温度将导致较宽的磨损宽度.初始阶段,最大密封压力随着温度和压力的增加而变大;随着磨损的进行,温度和压力越高,最大密封压力下降越快.活塞杆表面粗糙度幅值越大,密封压力下降越快.【期刊名称】《河北科技师范学院学报》【年(卷),期】2017(031)001【总页数】5页(P64-68)【关键词】密封圈;磨损;仿真;有限元模型【作者】李鑫;冯海生【作者单位】中国电子科技集团公司第38研究所机电技术研究部,安徽合肥,230094;埃夫特智能装备股份有限公司研发中心【正文语种】中文【中图分类】TH136弹性密封圈是液压设备中的常用元件[1],关于直线运动活塞杆用的密封圈研究可以追溯到20世纪30~40年代[2,3]。
尽管单个密封圈的成本低廉,但是密封圈一旦失效,有时会引起整个系统工作失效,甚至发生危险事故。
然而,在对密封圈设计时往往依赖于工程经验、专家知识或者实验/理论研究[4,5]。
随着有限元理论的不断完善以及相关软件应用不断成熟,研究密封圈密封性能的手段也不断丰富。
弹性流体动力学(Elastohydrodynamic Lubrication, EHL)模型常常用于描述密封圈的密封性能[6]。
有时密封圈需要在高速下工作,密封间隙内的热影响则不能忽略。
因此,热弹性流体动力学模型便应运而生。
除此之外,基于逆润滑理论的数值模型也得到广泛应用[7]。
近年来,材料磨损对密封圈密封性能的影响逐渐被加以考虑。
Nandor Bekesi[8]模拟了往复直线运动活塞杆用唇型密封圈的磨损过程,Ye Zibo[9]利用有限元方法和实验相结合的手段研究了PTFE油封的密封性能和磨损机理。
摩擦磨损试验机的虚拟设计与仿真分析
东北大学硕士学位论文目录目录独创性声明…………………………………………………………………I摘要……………………………………………………………………..IIAbstract………………………………………………………………………………………………………………..III第1章绪论……………………………………………………………..11.1课题研究的背景和意义…………………………………………………………………..11.2国内外研究现状及发展动态……………………………………………………………..21.3虚拟设计技术简介…………………………………………………………………………41.4课题研究的思路及主要内容……………………………………………………………..5第2章摩擦磨损试验机的总体设计……………………………………72.1试验机的功能及技术参数………………………………………………………………..72.2试验机的设计依据………………………………………………………………………..72.3试验机的系统组成…………………………………………………………………………92.3.1动力传动系统…………………………………………………………………….102.3.2加载系统…………………………………………………………………………..112.3.3感应加热系统…………………………………………………………………….112.3.4润滑系统………………………………………………………………………….122.4试验机的机械系统建模…………………………………………………………………122.4.1零部件三维实体模型的建立…………………………………………………….122.4.2机械系统虚拟装配模型的建立………………………………………………….1312.4.3机械系统装配模型干涉检验…………………………………………………….15.2.5本章小结…………………………………………………………………………………16第3章试验机关键零部件的有限元分析………………………………173.1轴承座和传动轴的结构静力分析………………………………………………………173.1.1轴承座的静力分析……………………………………………………………….173.1.2传动轴的静力分析……………………………………………………………….20f东北大学硕士学位论文目录5.3有限元分析模型的建立…………………………………………………………………625.3.1感应加热一维模型的建立……………………………………………………….625.3.2边晃条件、分析单元与网格划分……………………………………………….635.3.3电磁场与温度场相互耦合的实现……………………………………………….655.4感应加热实际工况模拟与分析…………………………………………………………665.4.1工况模拟工艺参数与材料特性参数…………………………………………….665。
- 1、下载文档前请自行甄别文档内容的完整性,平台不提供额外的编辑、内容补充、找答案等附加服务。
- 2、"仅部分预览"的文档,不可在线预览部分如存在完整性等问题,可反馈申请退款(可完整预览的文档不适用该条件!)。
- 3、如文档侵犯您的权益,请联系客服反馈,我们会尽快为您处理(人工客服工作时间:9:00-18:30)。
武汉理工大学
硕士学位论文
边界润滑状态下往复摩擦磨损的数值仿真研究
姓名:陈怀松
申请学位级别:硕士
专业:载运工具运用工程
指导教师:严新平
20051101
武汉理工大学硕士学位论文
式中,w代表微凸体所承受的载荷,oS代表较软材料的受压屈服极限,考虑到实际磨损率小几个数量级,故引进了磨损系数k,用来解释形成两微凸体相遇形成磨粒所需要的次数(n=l/k)。
由于软材料的布氏硬度H与屈服极限o。
之间的关系,一般也用式(2-2)表示:
矿:☆丝(2—2)
日
2.2.2.2修正的粘着磨损模型
现实中组成摩擦副表面的并不是纯金属,而是覆盖了一层润滑油膜或其它表面膜(如氧化膜或污染膜),C.N.Rowe等人对简单的粘着理论加以修正,并从Archard的磨损方程出发研究,引入了考虑与金属间接触面积有关的滑动金属特性参数‰,以及与润滑剂有关的特性数13,得到Archard磨损的修正模型:
矿=km∥(1+掣2)等(2—3)
门
其中盯、‰为常数,p为摩擦系数,p为与润滑油有关的特性。
虽然该公式中并没有说明p具体与什么有关,但是根据大量的分析结果表明,润滑油的粘度系数对磨损程度有一定影响。
在边界润滑状态下,润滑油中其他元素的成分也在很大程度上决定了∥的值的变化,如含s、cl的浓度或者是否含极压添加剂等。
2.3缸套一活塞环往复磨损的仿真模型
2.3.1磨损模型的基本假设
根据缸套一活塞环摩擦副运动特性及边界磨损的特点,提出以下四种假设
1)摩擦副表面的接触是
粗糙表面弹性接触过程,微凸
体高度呈高斯分布,应力满足
赫兹接触理论;
2)边界润滑中的绝大部
分载荷都由峰元承担,润滑油
武汉理工大学硕士学位论文
第3章缸套一活塞环往复磨损试验及结果
由于柴油机活塞一活塞环,缸套系统是往复摩擦磨损运动中最复杂也极具有代表性的摩擦系统,以其作为研究对象,不仅对于研究边界润滑与磨损具有重要的理论意义,而且为摩擦学仿真提供数据支持,确定和修正仿真模型参数起到决定性作用。
本次研究正是以该系统中的缸套.活塞环摩擦副为研究对象,在MW-2型往复磨损试验机上进行了一系列的摩擦磨损试验。
3.1试验目的
通过对比试验探索缸套一活塞环摩擦副在试验条件下随载荷、往复速度等外摩擦因素的磨损规律,为磨损仿真模型提供数据支持,确定和修改模型的参数。
采集伴随着磨损过程的摩擦学信息,包括摩擦系数、磨损量、表面形貌、温度的变化规律,探索它们之间的内在联系。
3.2试验系统简介
本次试验在MW-2型高速往复磨损试验机上进行,试验机是在本校自制的WMJ一1500试验机的基础上改装而成,集可变压力、可变速度、可变供油量、可测温度、可测摩擦力于一体的多功能摩擦磨损试验设备,其外观照片如图3-1所不。
图3-1MW-2型高速往复磨损试验机外观图
武汉理工大学硕士学位论文
表4.5缸套.活塞环表面形貌特征
磨损试验外摩擦条件试件描述
类型载荷往复速度缸套活塞环缸套活塞环(N)(r/min)
100300有少量黑色氧表面布满细小
干摩擦化物的条纹,夹杂少
量黑色氧化物500300黑色和红色氧表面有较深鞍
化物增多宽的划痕
300200网格数变少。
布满小的麻点,
表面有少许黑表面有撕脱的
色的小孔洞痕迹
100300网格较为密布满均匀细密
集,深度变化的划痕
不大
300300网格变浅,表表面有大量黑
面均匀分布有色麻点,还有少
凹坑和撕脱的量较深的划痕
痕迹
边界润滑
500300网格较浅处被瞎痕十分密集,
磨平,表面有尺寸较宽较深
微裂纹出现
300100
网格变得较为出现细密的划
密集,深度变痕
浅
300500表面有蓝色回表面有细密的
火色,网格变划痕,附着有少
稀最氧化物
武汉理工大学硕士学位论文
表4-6磨损试验的润滑油油样铁谱分析所获得的典型磨粒特征
磨损试验编外摩擦条件铁谱图像磨粒特征类型号
载荷往复速度
(N)(r/rain)
1100300大量为小尺寸颗粒,有少量表面有
凹坑的大磨粒。
干摩擦
2500300大的滑动磨粒,表面有平行的划
痕,大部分磨粒里暗黑色
3300200磨粒以细长的切削磨粒为主
4lOO300均匀的小尺寸磨粒
5300300磨粒呈薄片状,表面较光滑
6500300大尺寸的切削磨粒,表面有划痕,边界润滑且有直的棱边。
7300100表面粗糙,有擦痕,形状不规则
8300500小片状磨粒,局部出现黑色氧化
物
通过对比分析可知,不同试验条件下摩擦副表面的形貌变化和磨粒形貌存在藿一定程度的相关性。
对于干摩擦磨损,在高载、高速和低速条件下都发生
武汉理工大学硕士学位论文
5.3.3.2载荷条件下的应力分析
根据试件在实验条件下的工况,限制模型的自由度,同时施加300N和600N两组载荷,求解。
进入ANSYS后处理器,即可获得接触区域的压力、接触应力及应变。
由于活塞环和缸套配合情况较好,故接触面所受压力比较均匀,在300N外加载荷作用下试件1/2截面的应力分布如图5-2所示。
图5-2机械负荷下接触应力分布云图
通用后处理功能中一个强大的功能就是能够把任何计算结果数据映射到模型的任意路径上。
在指定的路径上可以进行各种数学运算和微积分运算,从而可以得到有用的计算结果。
5.3.3.3APDL语言
由于施加一次载荷和边界条件只能获得一组仿真数据,这样对于计算相同模型不同摩擦状态下的接触应力场非常繁琐,ANSYS参数化设计语言(APDL,ANSYSParametricDesignLanguage)为计算提供了方便。
改变材料参数和试验载荷、速度就能获得不同的应力应变结果,部分代码如下:。