煅烧分解钾长石提取碳酸钾的实验研究
钾长石提钾实验方案

钾长石提钾实验方案方案一:NaCl熔盐浸取法本实验方案先参考钾长石提钾中的氯化物法,因为钾长石中主要组成为:K2O约7~11%,SiO2约65~75%,Al2O3约18~20%,还有部分微量杂质,与本实验的原料矿组成类似,而且实验所需药品及仪器易得,方法简单,先采用此方法做探索性实验,此方法中,破坏钾长石中的晶体结构是是制取钾肥的关键,而热分解时添加的助剂是必不可少的,本实验方案的是助剂NaCl(也可以采用CaCl2等其它助剂),实验开展的步骤为:先将矿与助剂按一定比例混合放在马弗炉中焙烧,取出冷却一段时间,浸取,过滤,定容,再用四苯硼钠重量分析法分析滤液中的钾含量,计算钾的溶出率,最后将钾钠分离,分步结晶。
实验的具体步骤如下:1.焙烧实验药品:原料矿;NaCl粉末实验仪器:分析天平;马弗炉;坩锅;烧杯;玻棒实验步骤:称取20g原料矿和20gNaCl粉末放入同一烧杯中,用玻棒将它们均匀混合后放入坩锅中,将坩锅放入马弗炉中加热,温度设定为800℃,加热为2h;其它条件不变,改变加热温度分别为850℃,900℃,950℃做三组单因素实验。
这个过程中,反应温度对熔出率有较大的影响,只有当温度高于氯化钠的熔点时,才能有较好的熔出率,NaCl的熔点是801℃,氯化钠与钾长石的配比和反应时间也有一定影响,最后根据钾的溶出率优化反应条件。
2.浸取分离实验步骤:取一定量水于烧杯中,将焙烧物放入水中,使可溶性组分转为液相,成为浸出液,然后抽滤,使浸出液与不溶性固体残渣分离。
3.钾离子的分析实验方法:分析方法为四苯硼酸钠重量法,四苯硼酸钠重量法是测钾的国标方法,也是目前土壤、肥料中钾含量测试应用最为广泛的一种分析方法。
其分析原理为:在碱性较弱的介质中,四苯硼酸钠溶液作为沉淀剂与待测溶液中的K+反应,形成白色的沉淀四苯硼钾,然后将所得沉淀进行过滤、洗漆、干燥并称重,根据沉淀的质量测得溶液中所含的钾含量。
其反应式为:Na[B(C6H5 )4]+ K+=KB (C6H5) 4+ Na+实验步骤:用移液管吸取25mL的溶液,置于烧杯中,然后移取已配制好的EDTA 溶液50rnL于入烧杯中并滴加酚酞2滴,用氢氧化钠溶液调至红色,放在通风橱内加热煮沸约15min,等其自然冷却或用流水使其冷却,如果红色消失,再滴加氢氧化钠调至红色。
钾长石活化焙烧_酸浸新工艺的研究(碳酸钾烧结,硫酸浸取)

时熔融的碳酸钾不能完全浸润钾长石,反应不完全, 导致分解效率偏低。当质量比由 0. 5 提高到 0. 6 时,钾长石 的 分 解 率 随 着 添 量 的 增 加 而 急 剧 提 高。 而 0. 8 以上的添加量并不会使分解率有进一步明显 的提高。因此将碳酸钾与钾长石的质量比控制在 0. 7 时较为适宜。通过对比文献[12]可得,本文在焙 烧温度稍有提高的条件下使质量比由 1. 2 减少为 0. 7,为实现工业化生产打下了良好的基础。 2. 1. 2 焙烧温度
表 4 浸出温度对分解率的影响
浸出温度 /℃
25
50
75
90
分解率 /%
84
43
35
22
由表 4 可知,室温更利于钾长石的分解,较高的 温度会给离子的水解创造有利环境,从而导致不溶 物的增多。 2. 2. 4 液固比
液固比对钾长石分解率的影响结果见图 4。
图 3 硫酸浓度对钾长石分解率的影响
由图 3 可知,当浸取剂全部为水时,分解率仅为 33% 。提高浸取液中硫酸浓度,有利于提高钾长石 的分解率。当硫酸浓度为 9mol / L 时,钾长石的分解 率达到了最大值。再增加硫酸浓度,钾长石的分解 率反而下降,可能是因为过高的硫酸浓度( > 9mol / L) 会导致类似 KAl( SO4 ) 2 的生成,起到絮凝作用而 导 致 不 溶 物 的 增 多。 另 外,酸 度 过 高,酸 的 消 耗 量 大,对设备的腐蚀严重,同时增加了生产成本。因此 综合考虑 3mol / L 的硫酸浓度比较适宜。 2. 2. 2 浸出时间
关键词:钾长石; 焙烧; 酸浸; 分解率 中图分类号:TF803. 2 文献标识码:A 文章编号:1000-6532(2012)01-0036-04
富钾页岩的焙烧提钾实验研究(氢氧化钠;硫酸浸取)

第16卷第10期 2007年10月中 国 矿 业CHINA MI NING MA GAZINEVol.16,No.10October 2007富钾页岩的焙烧提钾实验研究韩跃新,刘 杰,印万忠(东北大学资源与土木工程学院,辽宁沈阳110004)摘 要:针对朝阳地区的富钾页岩进行了焙烧提钾的实验研究。
通过对质量配比为m (NaOH )B m (页岩)=017B 1的混合物料进行XRD 分析和热分析,初步确定了在不同焙烧温度下以及在升温过程中,混合物料中存在的主要物相及其变化规律。
确定了适宜的焙烧提钾条件,并利用XRD 对提钾后的水不溶物进行了物相分析。
实验结果表明:钾长石和绢云母转变成可溶于热酸的钾霞石;在适宜的条件下,钾的浸出率可达88108%。
关键词:富钾页岩;焙烧提钾;钾长石;绢云母中图分类号:T F111112/T F111131 文献标识码:B 文章编号:1004-4051(2007)10-0098-05Study on roasting 2extracting potassium from the potassium 2rich shaleH AN Yue 2xin,LIU Jie,YIN Wan 2zhong(School of Resour ces &Civil Engineering,Nor theaster n Universit y,Shenyang 110004,China) Abstr act:The experiment of roasting 2extr acting potassium from the potassium 2rich shale in Caoyang is com plet ed 1XRD anaylsis and thermal analysis is ca rried out for mixed mat er ials of the mass r at io of sodium hydr oxide to shale being 0171And in differ ent roast ing temper atur e and in the course of heating 2up main phase in the shale sample and var iation of phase is confir med preparatorily 1At the same t ime,thr ough the exper iment of roasting 2extracting potassium,fitt ing condit ion of r oasting 2extr act ing potassium is found,and phase analysis for t he water 2insoluble after extr acting potassium is pr ogressed by XR D 1Abstr act:T he main factors that affect the leaching rate of pot assium in potash f eldspar were studied 1It is shown that potash feldspar and ser icite is tr ansmuted into ka liophilite that can dissolve in hot acid;in the suitable conditions,the extracting ratio of potassium reach 88108%1Key wor ds:potassium 2rich shale;roasting 2ext racting potassium;potash feldspar;ser icite收稿日期:2007-07-08基金项目:教育部新世纪优秀人才资助项目(NCET 205520291)作者简介:韩跃新(1961-),男,内蒙古赤峰人,教授,博士生导师。
钾长石提钾实验方案

钾长石提钾实验方案钾长石提钾实验方案方案一:NaCl熔盐浸取法本实验方案先参考钾长石提钾中的氯化物法,因为钾长石中主要组成为:K2O约7~11%,SiO2约65~75%,Al2O3约18~20%,还有部分微量杂质,与本实验的原料矿组成类似,而且实验所需药品及仪器易得,方法简单,先采用此方法做探索性实验,此方法中,破坏钾长石中的晶体结构是是制取钾肥的关键,而热分解时添加的助剂是必不可少的,本实验方案的是助剂NaCl(也可以采用CaCl2等其它助剂),实验开展的步骤为:先将矿与助剂按一定比例混合放在马弗炉中焙烧,取出冷却一段时间,浸取,过滤,定容,再用四苯硼钠重量分析法分析滤液中的钾含量,计算钾的溶出率,最后将钾钠分离,分步结晶。
实验的具体步骤如下:1.焙烧实验药品:原料矿;NaCl粉末实验仪器:分析天平;马弗炉;坩锅;烧杯;玻棒实验步骤:称取20g原料矿和20gNaCl粉末放入同一烧杯中,用玻棒将它们均匀混合后放入坩锅中,将坩锅放入马弗炉中加热,温度设定为800℃,加热为2h;其它条件不变,改变加热温度分别为850℃,900℃,950℃做三组单因素实验。
这个过程中,反应温度对熔出率有较大的影响,只有当温度高于氯化钠的熔点时,才能有较好的熔出率,NaCl的熔点是801℃,氯化钠与钾长石的配比和反应时间也有一定影响,最后根据钾的溶出率优化反应条件。
2.浸取分离实验步骤:取一定量水于烧杯中,将焙烧物放入水中,使可溶性组分转为液相,成为浸出液,然后抽滤,使浸出液与不溶性固体残渣分离。
3.钾离子的分析实验方法:分析方法为四苯硼酸钠重量法,四苯硼酸钠重量法是测钾的国标方法,也是目前土壤、肥料中钾含量测试应用最为广泛的一种分析方法。
其分析原理为:在碱性较弱的介质中,四苯硼酸钠溶液作为沉淀剂与待测溶液中的K+反应,形成白色的沉淀四苯硼钾,然后将所得沉淀进行过滤、洗漆、干燥并称重,根据沉淀的质量测得溶液中所含的钾含量。
贵州省钾长石提钾工艺初步研究
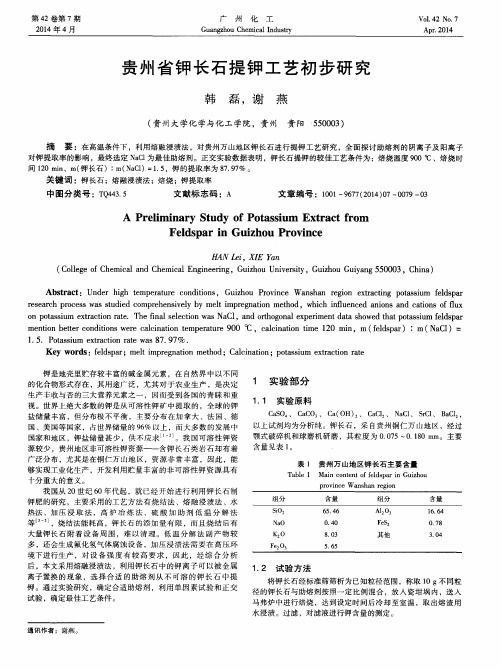
关 键 词 :钾长石 ; 熔融浸渍法 ; 焙烧;钾提取率
中图分类号 : T Q 4 4 3 . 5
文献标志码 :A
文章编号 : 1 0 0 1 — 9 6 7 7 ( 2 0 1 4 ) 0 7 — 0 0 7 9 — 0 3
( 贵 州大 学化 学与, f  ̄ X - 学 院 ,贵 州 I 贵阳 - 5 5 0 0 0 3 )
摘 要 :在高温条件下,利用熔融浸渍法 , 对贵州万山地区钾长石进行提钾工艺研究 ,全面探讨助熔剂的阴离子及阳离子
对钾 提取 率的影响 , 最终选定 N a C 1 为最佳助熔剂 。正交 实验数据表 明 , 钾 长石 提钾 的较佳工艺条件 为 : 焙烧温 度 9 0 0℃ 、焙烧 时
me n t i o n b e t t e r c o n d i t i o n s w e r e c a l c i n a t i o n t e mp e r a t u r e 9 0 0 ℃ ,c a l c i n a t i o n t i m e 1 2 0 mi n ,m( f e l d s p a r ): m( N a C 1 )=
Ab s t r a c t :U n d e r h i g h t e mp e r a t u r e c o n d i t i o n s ,G u i z h o u P r o v i n c e W a n s h a n r e g i o n e x t r a c t i n g p o t a s s i u m f e l d s p a r r e s e a r c h p r o c e s s wa s s t u d i e d c o mp r e h e n s i v e l y b y me l t i mp r e g n a t i o n me t h o d ,w h i c h i n l f u e n c e d a n i o n s a n d c a t i o n s o f l f u x o n p o t a s s i u m e x t r a c t i o n r a t e .T h e i f n a l s e l e c t i o n wa s N a C 1 。a n d o r t h o g o n a l e x p e r i me n t d a t a s h o we d t h a t p o t a s s i u m f e l d s p a r
钾长石在CaSO4及其分解产物下的焙烧反应研究

- 14 -第37卷第5期 非金属矿 Vol.37 No.5 2014年9月 Non-Metallic Mines September, 2014我国可溶性钾资源匮乏,不溶性钾矿石储量大且分布广。
钾肥是农业中不可或缺的三大肥料之一,以含钾矿石为原料,制备可溶钾将是我国解决钾肥依赖进口问题的途径之一[1]。
在钾长石制备可溶钾的方法中,焙烧法适合我国的国情[2]。
很多学者在利用钾长石制备可溶性钾肥方面做了广泛而深入的研究,为不溶性钾矿石制备钾肥提供了丰富的理论基础[3-5],但也存在以下不足:均需要大量天然石灰石作为置换反应的钙源;硫酸钙仅用于提供钾长石分解产物结合的硫源,用量少,同时在焙烧过程中会有部分分解为SO 2进入尾气中造成对环境的污染。
钾长石焙烧制备可溶性钾的过程中,CaO 用于与钾长石反应置换出K 2O ,K 2O 在高温下不稳定易升华,因此,用CaSO 4提供硫酸根与K 2O 结合成高温稳定的K 2SO 4,通过水淬而获得可溶性钾肥。
根据这一原理,夏举佩等[6-9]提出用硫酸钙替换石灰石,通过硫酸钙的分解产物提供钾长石置换反应的钙源,同时制备酸原料气SO 2,但对钾长石与硫酸钙及其分解产物钾长石在CaSO 4及其分解产物下的焙烧反应研究夏举佩* 彭 健 李国斌 苏 毅 阳超琴(昆明理工大学 化学工程学院,云南 昆明 650500)摘 要 根据硫酸钙还原分解产物成分,通过钾长石自身高温特性和添加硫酸钙及分解产物焙烧反应研究,探明实际体系下焙烧反应历程。
研究结果表明:在1200 ℃下,硫酸钙能与钾长石进行反应,形成低共熔物K 2Ca 2(SO 4)3,此物质结构稳定,无水溶特性;CaS 不与钾长石反应,二者独立存在于体系中;CaO 有较好反应活性,能置换出钾长石中的氧化钾;在有硫酸钙存在时,当氧化钙量不足时生成K 2S 2O 8,当氧化钙充足时则生成K 2SO 4。
硅、铝酸的钙盐则与体系物料配比及操作条件有关。
钾长石混盐焙烧-浸出提钾过程研究
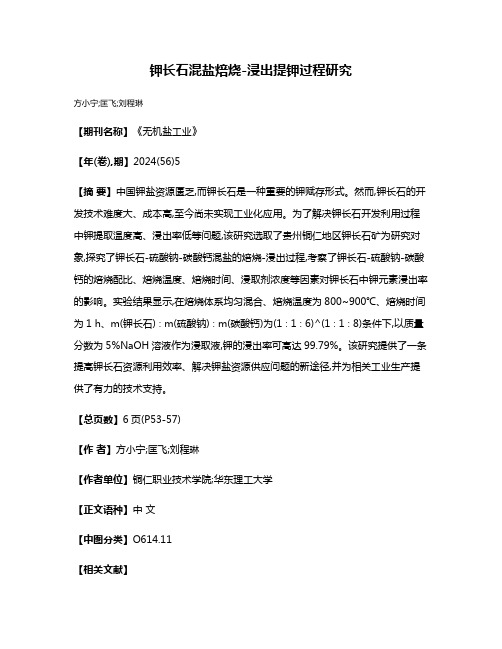
钾长石混盐焙烧-浸出提钾过程研究
方小宁;匡飞;刘程琳
【期刊名称】《无机盐工业》
【年(卷),期】2024(56)5
【摘要】中国钾盐资源匮乏,而钾长石是一种重要的钾赋存形式。
然而,钾长石的开发技术难度大、成本高,至今尚未实现工业化应用。
为了解决钾长石开发利用过程中钾提取温度高、浸出率低等问题,该研究选取了贵州铜仁地区钾长石矿为研究对象,探究了钾长石-硫酸钠-碳酸钙混盐的焙烧-浸出过程,考察了钾长石-硫酸钠-碳酸钙的焙烧配比、焙烧温度、焙烧时间、浸取剂浓度等因素对钾长石中钾元素浸出率的影响。
实验结果显示,在焙烧体系均匀混合、焙烧温度为800~900℃、焙烧时间为1 h、m(钾长石)∶m(硫酸钠)∶m(碳酸钙)为(1∶1∶6)^(1∶1∶8)条件下,以质量分数为5%NaOH溶液作为浸取液,钾的浸出率可高达99.79%。
该研究提供了一条提高钾长石资源利用效率、解决钾盐资源供应问题的新途径,并为相关工业生产提供了有力的技术支持。
【总页数】6页(P53-57)
【作者】方小宁;匡飞;刘程琳
【作者单位】铜仁职业技术学院;华东理工大学
【正文语种】中文
【中图分类】O614.11
【相关文献】
1.表面活性剂与钾长石提钾过程的相容性研究
2.温度制度对钾长石-硫酸钙-碳体系焙烧提钾、还原脱硫以及CO_2矿化的影响
3.钾长石-氯化钙焙烧提钾过程研究(英文)
4.无盐焙烧-稀酸浸出提钒工艺研究
5.钾钠混盐提钾工艺研究
因版权原因,仅展示原文概要,查看原文内容请购买。
一种酸法提取钾长石中可溶性钾的方法[发明专利]
![一种酸法提取钾长石中可溶性钾的方法[发明专利]](https://img.taocdn.com/s3/m/95539de081eb6294dd88d0d233d4b14e85243e24.png)
(10)申请公布号 (43)申请公布日 2013.12.04C N 103420399 A (21)申请号 201310317664.6(22)申请日 2013.07.26C01D 3/00(2006.01)C01D 5/00(2006.01)C01D 7/00(2006.01)C01D 9/00(2006.01)C01D 13/00(2006.01)(71)申请人成都化工股份有限公司地址611400 四川省成都市新津县新津工业园区B 区(72)发明人钟林 陈鹏 钟国林 吴佳伟常守平(54)发明名称一种酸法提取钾长石中可溶性钾的方法(57)摘要本发明公开了一种酸法从钾长石中提取可溶性钾的方法,包括以下步骤:将钾长石粉末与低浓度酸、助剂氢氟酸(HF)或者萤石(CaF 2)直接投料,装于密闭的衬蒙乃尔400合金或衬四氟高压反应釜中反应,生成物降温至室温,过滤,滤液进行减压蒸馏,蒸干、冷却后的固体即为可溶性钾盐。
本发明酸法提取可溶性钾采用低浓度酸和低含量的氢氟酸(HF)或萤石(CaF 2)作为助剂,在不超过150℃的低温条件下,有效地破坏了钾长石的内部结构,提升了可溶性钾的提取率,产率达90%以上,整个提取工艺具有流程简单、低温、酸及助剂用量小、环境污染少、提取率高、成本低廉等优点,实际应用和工业化前景好。
(51)Int.Cl.权利要求书1页 说明书4页 附图1页(19)中华人民共和国国家知识产权局(12)发明专利申请权利要求书1页 说明书4页 附图1页(10)申请公布号CN 103420399 A*CN103420399A*1/1页1.一种酸法从钾长石中提取可溶性钾的方法包括以下步骤:(1)将钾长石粉料,低浓度无机酸,助剂氢氟酸(HF)或者萤石(CaF 2)直接投料,装于密闭的衬蒙乃尔400合金或衬四氟高压反应釜中反应;(2)取出步骤(1)反应生成物,降温至室温,过滤;(3)对步骤(2)中滤液进行减压蒸馏,蒸干、冷却后的固体即为可溶性钾盐。
- 1、下载文档前请自行甄别文档内容的完整性,平台不提供额外的编辑、内容补充、找答案等附加服务。
- 2、"仅部分预览"的文档,不可在线预览部分如存在完整性等问题,可反馈申请退款(可完整预览的文档不适用该条件!)。
- 3、如文档侵犯您的权益,请联系客服反馈,我们会尽快为您处理(人工客服工作时间:9:00-18:30)。
K+体系 。将母液用 CO2 酸化 , 偏硅酸根等离子以原
硅酸或聚硅酸的形式沉淀下来 。选择 CO2 的最主要
原因是 : 本项工艺前部焙烧反应过程中放出大量的
CO2 ,若该工艺工业化后 ,不对此回收 ,势必对大气构
( 3) 3 K[ AlSi 3O8] + 9 K2CO3 = K3Al 3O6 + 9 K2SiO3 + 9CO2 ↑
( 4)
3Ca[ Al 2Si 2O8] + 7. 5 K2CO3 = 2 K3Al 3O6 + 1. 5Ca 2SiO4
+ 4. 5 K2SiO3 + 7. 5CO2 ↑
( 5)
1. 1 1. 0 1. 2 1. 0 1. 2 1. 1 1. 2 1. 1 1. 0
98. 94 99. 20 99. 40 0. 46
99. 85 99. 63 99. 82 98. 94 99. 25 99. 51 99. 12 98. 87 98. 25
Na[ AlSi 3O8] + 3 K2CO3 = NaAlO2 + 3 K2SiO3 + 3CO2 ↑
表 2 焙烧温度对分解率的影响
焙烧温 度/ ℃ 740 760 780 800 820 840 860 880 900 分解率
75. 3 74. 6 78. 11 77. 21 92. 51 96. 08 97. 56 92. 80 89. 20 %
有了温度单因素实验的基础 , 设计了 4 因素 3 水平的正交实验 , 影响分解率的主要因素有生料粒 度 、焙烧温度 、焙烧时间和碳酸钾用量 。经过数轮正 交实验 , 得出最佳反应条件 : 焙烧温度 860 ℃; 焙烧 时间为 40min ; 生料粒度对分解率影响不大 , 碳酸钾 适宜加入量为钾长石 ∶K2CO3 = 1 ∶1. 2 ; 考虑到成 本 ,碳酸钾用量不宜过大 。
2FeOOH = Fe 2O3 + H2O ↑
( 6)
K 1 - x {Al 2[ ( Si 3 + xAl 1 - x) 4O10] (OH) 2} + K2CO3 =
K3Al 3O6 + K2SiO3 + CO2 ↑+ H2O ↑
( 7)
2. 2 CO2 酸化实验 浸取液呈强碱性 , 化学分析
结果 (表 4 中 J S - 1 样品) 表明其主要成分是 SiO32 - 、
0. 28 0. 03
0. 08 0. 00
0. 73 0. 64
0. 67 0. 50
0. 38 0. 40
14. 01 14. 97
0. 30 0. 20
1. 78 0. 82
0. 20 0. 11
2 结果与讨论 2. 1 焙烧原矿 从热力学角度来说 , 温度是决定 反应能否发生的主要因素 。为了找出较佳的煅烧温 度 ,实验中设计了温度单因素实验 (表 2) ,分别将配 比 为 钾 长 石 ∶K2CO3 = 1 ∶1. 2 的 反 应 物 料 , 在 740 ℃、760 ℃、780 ℃、800 ℃、820 ℃、840 ℃、860 ℃、 880 ℃和 900 ℃温度下进行焙烧 , 固定反应时间为 1h ,生料粒度为 80 目 ,钾长石分解率见表 2。从结果 可知 , 平衡反应的温度亦即焙烧反应的较佳温度范 围为 820~880 ℃。由于 K2CO3 的熔点为 913 ℃,故无 再提高反应温度的必要 。
开发非水溶性钾矿资源生产钾盐 , 主要利用钾 长石热分解 - 水浸法提取钾盐 , 研究重点在于助熔 剂和工艺条件的选择 。赵恒勤 [1 ]等利用碱石灰助熔 烧结钾长石 , 解决了焙烧工艺问题 ; 湖南化工研究 院采用旋风冶炼 , 以煤 、磷矿石 、钾长石 、白云石和 氯化钙为原料 ,得到钾肥和钙镁磷肥 [2 ];四川地矿局 利用绿豆岩 (富钾凝灰岩) 生产钾镁硅肥获得成功 , 实现了由非水溶性钾矿资源直接生产钾肥 [3 ]。但目 前的工作 , 缺乏从热力学 、动力学及反应机理方面 深入研究 。文献[ 4]分析了在有石膏 、碳酸钙条件下 钾长石分解的动力学 , 但焙烧熟料体系的复杂性 , 对于制备纯度较高的钾盐 , 或者说对于浸取液的分 离 ,势必存在问题 。国外 ,只有印度学者 Saxena E 和 Dasgupta A 等在钾长石焙烧工艺方面有过报道 [5 。 ,6 ]
第 27 卷第 1 期 2004 年 1 月
非金属矿
Non - Metallic Mines
Vol. 27 No. 1 Jan. , 2004
煅烧分解钾长石提取碳酸钾的实验研究
苗世顶1 ,2 马鸿文 1 冯武威 1 张 盼 1 刘 贺 1
(1 中国地质大学材料科学与工程学院 ,北京 100083 ;2 阜阳师范学院化学系 ,阜阳 236300)
品达到彩电工业用碳酸钾 (电子级) 的质量要求 , 从 而使矿物聚合材料成为该工艺的净产出 。本项工艺 之所以用碳酸钾做焙烧助剂 , 是因为钾激发矿物聚 合材料的性质远优于其它激发剂 [8 ]。技术经济分析 表明 ,该工艺有着良好的产业化前景 。 1 实验部分 1. 1 原料 钾长石矿粉来自于江苏丰县 , 物相分 析表明 ,其主要成分为钾长石 、伊利石 、石英 ,另含少 量针铁矿等 ,样品 J S - 1 化学全分析结果见表 1。作 为焙烧原料 , 本实验对该矿粉进行了破碎至 120 目 、 摇床选矿 、酸法除铁的预加工 ,以提高原料中钾长石 的含量 。除铁后的钾长石粉样品 J S - 2 化学全分析 结果 ,见表 1。
度强
2500 2000 1500 1000 500
0
A A A :β- Ca3SiO5 B : K2CO30. 5H2O
C :Ca2Fe (SiO2) (Si2O7) (OH) xH2O
A C A
C
C
A A
BBBCCB
B B
A BB A
ABBB B B B
0 10 20 30 40 50 60 70 2θ/ (°)
根据热力学分析和计算 , 结合熟料中少量不溶 物的物相鉴定 , 可推测钾长石 + K2CO3 体系热分解 反应的可能反应步骤 。因为熟料几乎全溶于水 , 产 物中不会出现钾长石玻璃或高温透长石 , 熟料物相 只有铝酸盐 、偏硅酸盐等可溶性盐类 ; 另外 , 不溶物 残渣中有 Ca2SiO4 , 故可假定有下列反应发生 。结合 查阅的热力学数据 [9 ,10 ] , 初步计算了各个反应在 1133 K条件下的吉布斯函数变均小于 0 , 表明下列 各反应在该条件下能自发反应 :
本文从实验上得出钾长石在助熔剂 K2CO3( 工 业级合格品) 存在的情况下煅烧分解 , 熟料水浸取 , 再用 CO2 酸化浸取液 , 原钾长石中的 Si 、Al 等元素 沉淀 ,沉淀物用于制备矿物聚合材料 [8 ];滤液经浓缩 除杂 , 制备出电子级碳酸钾 。本项研究中原料焙烧 用掉的是纯度较低的碳酸钾 (工业级合格品)1 期
非金属矿
2004 年 1 月
表 1 原料的化学全分析结果/ %
样品
SiO2
TiO2
Al 2O3
Fe2O3
FeO
MnO
MgO
CaO
Na2O
K2O
P2O5
H2O +
H2O -
JS- 1 JS- 2
55. 01 62. 04
0. 72 0. 86
18. 15 18. 87
7. 52 0. 14
摘 要 探讨了碳酸钾助熔焙烧钾长石分解 , 熟料水浸取 , CO2 酸化浸取液 , 过滤除去沉淀 , 滤液经结晶除杂提取碳酸钾的过程 。实验表 明 : 分解钾长石最佳焙烧温度为 860 ℃, 焙烧时间 40min , 滤液酸化后的最佳 p H 值为 8. 0 , 滤液制备出的 K2CO3 , 达到 GB/ T1587 - 2000 Ⅱ型要 求 。并用差热/ 热失重和 X 粉晶衍射法对焙烧熟料进行分析 ,初步分析了分解反应的机理 。
图 2 不溶物残渣的 X - 粉晶衍射图
(测试单位 :石油化工研究院物质结构室)
表 3 碳酸钾助熔焙烧分解钾长石实验结果
正交序列
生料粒度 目
焙烧温度 ℃
焙烧时间 min
碳酸钾量
分解率 %
1132 2111 3123 1221 2233 3212 1313 2322 3331
K( 1 ,j) K( 2 ,j) K( 3 ,j) 级差
60 80 100 60 80 100 60 80 100
99. 30 99. 25 99. 19 0. 11
860 860 860 880 880 880 900 900 900
99. 77 99. 23 98. 75 1. 02
80 40 60 60 80 40 40 60 80
99. 42 99. 21 99. 17 0. 30
Abstract K- feldspar is decomposed by calcination with the flux of potassium carbonate , the resultant was resolved in water , acidified by CO2 , the residue was removed by filtration and the remaining solution was prepared potassium carbonate. The experiment shows the optimum reaction temperature is 860 ℃; The calcination time is 40min ; the p H of acided filtrated solution is 8. 6 ; and K2CO3 prepared by filtrated solution is up to GB/ T 1587 - 2000 Ⅱ specification. In addition , the resultant is analyzed by thermal analysis of TGand DTA , and the baked materials were analyzed by X - ray diffraction. With the above analysis , the dissociation mechanism is proposed.