橡胶轮挡阻挡功效和失效模式分析与计算
设计失效模式及后果分析(DFMEA)

(设计FMEA)X 系统FEMA编号:A11-3510010AC001 子系统页码:第 1 页共37 页零部件A11-3510010AC 设计责任:技质部编制者:王勇——技质部车型年/车辆类型:A11奇瑞关键日期:2002.02.14FMEA日期:2002.02.14(设计FMEA)X 系统FEMA编号:A11-3510010AC002 子系统页码:第 2 页共37 页零部件:A11-3510010AC 设计责任:技质部编制者:王勇——技质部车型年/车辆类型:A11奇瑞关键日期:2002.02.14FMEA日期:2002.02.14潜在失效模式及后果分析(设计FMEA)X 系统FEMA编号:A11-3510010AC003 子系统页码:第 3 页共37 页零部件:A11-3510010AC 设计责任:技质部编制者:王勇——技质部车型年/车辆类型:A11奇瑞关键日期:2002.02.14FEMA日期:2002.02.14在失效模式及后果分析(设计FMEA)X 系统FEMA编号:A11-3510010AC003 子系统页码:第 4 页共37 页零部件:A11-3510010AC 设计责任:技质部编制者:王勇——技质部车型年/车辆类型:A11奇瑞关键日期:2002.02.14FEMA日期:2002.02.14潜在失效模式及后果分析(设计FMEA)X 系统FEMA编号:A11-3510010AC004 子系统页码:第 5 页共37 页零部件:A11-3510010AC 设计责任:技质部编制者:王勇——技质部车型年/车辆类型:A11奇瑞关键日期:2002.02.14FEMA日期:2002.02.14(设计FMEA)X 系统FEMA编号:A11-3510010AC004 子系统页码:第 5 页共37 页零部件:A11-3510010AC 设计责任:技质部编制者:王勇——技质部车型年/车辆类型:A11奇瑞关键日期:2002.02.14FEMA日期:2002.02.14核心小组:张平、王国强——厂务部/王勇、王小龙、夏根生、王玮、张延云——技质部(设计FMEA)X 系统FEMA编号:A11-3510010AC005 子系统页码:第7 页共37 页零部件:A11-3510010AC 设计责任:技质部编制者:王勇——技质部车型年/车辆类型:A11奇瑞关键日期:2002.02.14FEMA日期:2002.02.14(设计FMEA)X 系统FEMA编号:A11-3510010AC005 子系统页码:第8 页共37 页零部件:A11-3510010AC 设计责任:技质部编制者:王勇——技质部车型年/车辆类型:A11奇瑞关键日期:2002.02.14FEMA日期:2002.02.14(设计FMEA)X 系统FEMA编号:A11-3510010AC006 子系统页码:第9 页共37 页零部件:A11-3510010AC 设计责任:技质部编制者:王勇——技质部车型年/车辆类型:A11奇瑞关键日期:2002.02.14FEMA日期:2002.02.14(设计FMEA)X 系统FEMA编号:A11-3510010AC006 子系统页码:第10 页共37 页零部件:A11-3510010AC 设计责任:技质部编制者:王勇——技质部车型年/车辆类型:A11奇瑞关键日期:2002.02.14FEMA日期:2002.02.14潜在失效模式及后果分析(设计FMEA)X 系统FMEA编号:A11-3510010AC006 子系统第11 页共37 页零部件:A11-3510010AC 设计责任:技质部编制者:王勇—技质部车型年/车辆类型:A11-奇瑞关键日期:2002.02.14 FMEA日期:2002.02.14潜在失效模式及后果分析(设计FMEA)X 系统FMEA编号:A11-3510010AC006 子系统第12 页共37 页零部件:A11-3510010AC 设计责任:技质部编制者:王勇—技质部车型年/车辆类型:A11-奇瑞关键日期:2002年2月14日FMEA日期:2002年2月14日潜在失效模式及后果分析(设计FMEA)X 系统FMEA编号:A11-3510010AC 子系统第13 页共37 页零部件:A11-3510010AC 设计责任:技质部编制者:王勇—技质部车型年/车辆类型:A11-奇瑞关键日期:2002年2月14日FMEA日期:2002年2月14日潜在失效模式及后果分析(设计FMEA)X 系统FMEA编号:A11-3510010AC007 子系统第14 页共37 页零部件:A11-3510010AC 设计责任:技质部编制者:王勇—技质部车型年/车辆类型:A11-奇瑞关键日期:2002年2月14日FMEA日期:2002年2月14日潜在失效模式及后果分析(设计FMEA)X 系统FMEA编号:A11-3510010AC007 子系统第15 页共37 页零部件:A11-3510010AC 设计责任:技质部编制者:王勇—技质部车型年/车辆类型:A11-奇瑞关键日期:2002年2月14日FMEA日期:2002年2月14日潜在失效模式及后果分析(设计FMEA)X 系统FMEA编号:A11-3510010AC008 子系统第16 页共37 页零部件:A11-3510010AC 设计责任:技质部编制者:王勇—技质部车型年/车辆类型:A11-奇瑞关键日期:2002年2月14日FMEA日期:2002年2月14日潜在失效模式及后果分析(设计FMEA)X 系统FMEA编号:A11-3510010AC008 子系统第17 页共37 页零部件:A11-3510010AC 设计责任:技质部编制者:王勇—技质部车型年/车辆类型:A11-奇瑞关键日期:2002年2月14日FMEA日期:2002年2月14日潜在失效模式及后果分析(设计FMEA)X 系统FMEA编号:A11-3510010AC008 子系统第18 页共37 页零部件:A11-3510010AC 设计责任:技质部编制者:王勇—技质部车型年/车辆类型:A11-奇瑞关键日期:2002年2月14日FMEA日期:2002年2月14日潜在失效模式及后果分析(设计FMEA)X 系统FMEA编号:A11-3510010AC008 子系统第19 页共37 页零部件:A11-3510010AC 设计责任:技质部编制者:王勇—技质部车型年/车辆类型:A11-奇瑞关键日期:2002年2月14日FMEA日期:2002年2月14日潜在失效模式及后果分析(设计FMEA)X 系统FMEA编号:A11-3510010AC008 子系统第20 页共37 页零部件:A11-3510010AC 设计责任:技质部编制者:王勇—技质部车型年/车辆类型:A11-奇瑞关键日期:2002年2月14日FMEA日期:2002年2月14日潜在失效模式及后果分析(设计FMEA)X 系统FMEA编号:A11-3510010AC009 子系统第21 页共37 页零部件:A11-3510010AC 设计责任:技质部编制者:王勇—技质部车型年/车辆类型:A11-奇瑞关键日期:2002年2月14日FMEA日期:2002年2月14日潜在失效模式及后果分析(设计FMEA)X 系统FMEA编号:A11-3510010AC009 子系统第22 页共37 页零部件:A11-3510010AC 设计责任:技质部编制者:王勇—技质部车型年/车辆类型:A11-奇瑞关键日期:2002年月14日FMEA日期:2002年2月14日潜在失效模式及后果分析(设计FMEA)X 系统FMEA编号:A11-3510010AC009 子系统第23 页共37 页零部件:A11-3510010AC 设计责任:技质部编制者:王勇—技质部车型年/车辆类型:A11-奇瑞关键日期:2002年2月14日FMEA日期:2002年2月14日潜在失效模式及后果分析(设计FMEA)X 系统FMEA编号:A11-3510010AC009 子系统第24 页共37 页零部件:A11-3510010AC 设计责任:技质部编制者:王勇—技质部车型年/车辆类型:A11-奇瑞关键日期:2002年2月14日FMEA日期:2002年2月14日潜在失效模式及后果分析(设计FMEA)X 系统FMEA编号:A11-3510010AC009 子系统第25 页共37 页零部件:A11-3510010AC 设计责任:技质部编制者:王勇—技质部车型年/车辆类型:A11-奇瑞关键日期:2002年2月14日FMEA日期:2002年2月14日潜在失效模式及后果分析(设计FMEA)X 系统FMEA编号:A11-3510010AC009 子系统第26 页共37 页零部件:A11-3510010AC 设计责任:技质部编制者:王勇—技质部车型年/车辆类型:A11-奇瑞关键日期:2002年2月14日FMEA日期:2002年2月14日潜在失效模式及后果分析(设计FMEA)X 系统FMEA编号:A11-3510010AC009 子系统第27 页共37 页零部件:A11-3510010AC 设计责任:技质部编制者:王勇—技质部车型年/车辆类型:A11-奇瑞关键日期:2002年2月14日FMEA日期:2002年2月14日潜在失效模式及后果分析(设计FMEA)X 系统FMEA编号:A11-3510010AC010 子系统第28 页共37 页零部件:A11-3510010AC 设计责任:技质部编制者:王勇—技质部车型年/车辆类型:A11-奇瑞关键日期:2002年2月14日FMEA日期:2002年2月14日潜在失效模式及后果分析(设计FMEA)X 系统FMEA编号:A11-3510010AC011 子系统第29 页共37 页零部件:A11-3510010AC 设计责任:技质部编制者:王勇—技质部车型年/车辆类型:A11-奇瑞关键日期:2002年2月14日FMEA日期:2002年2月14日潜在失效模式及后果分析(设计FMEA)X 系统FMEA编号:A11-3510010AC012 子系统第30 页共37 页零部件:A11-3510010AC 设计责任:技质部编制者:王勇—技质部车型年/车辆类型:A11-奇瑞关键日期:2002年2月14日FMEA日期:2002年2月14日潜在失效模式及后果分析(设计FMEA)X 系统FMEA编号:A11-3510010AC013 子系统第31 页共37 页零部件:A11-3510010AC 设计责任:技质部编制者:王勇—技质部车型年/车辆类型:A11-奇瑞关键日期:2002年2月14日FMEA日期:2002年2月14日潜在失效模式及后果分析(设计FMEA)X 系统FMEA编号:A11-3510010AC013 子系统第32 页共37 页零部件:A11-3510010AC 设计责任:技质部编制者:王勇—技质部车型年/车辆类型:A11-奇瑞关键日期:2002年2月14日FMEA日期:2002年2月14日潜在失效模式及后果分析(设计FMEA)X 系统FMEA编号:A11-3510010AC013 子系统第33 页共37 页零部件:A11-3510010AC 设计责任:技质部编制者:王勇—技质部车型年/车辆类型:A11-奇瑞关键日期:2002年2月14日FMEA日期:2002年2月14日潜在失效模式及后果分析(设计FMEA)X 系统FMEA编号:A11-3510010AC013 子系统第34 页共37 页零部件:A11-3510010AC 设计责任:技质部编制者:王勇—技质部车型年/车辆类型:A11-奇瑞关键日期:2002年2月14日FMEA日期:2002年2月14日潜在失效模式及后果分析(设计FMEA)X 系统FMEA编号:A11-3510010AC013 子系统第35 页共37 页零部件:A11-3510010AC 设计责任:技质部编制者:王勇—技质部车型年/车辆类型:A11-奇瑞关键日期:2002年2月14日FMEA日期:2002年2月14日潜在失效模式及后果分析(设计FMEA)X 系统FMEA编号:A11-3510010AC014 子系统第36 页共37 页零部件:A11-3510010AC 设计责任:技质部编制者:王勇—技质部车型年/车辆类型:A11-奇瑞关键日期:2002年2月14日FMEA日期:2002年2月14日潜在失效模式及后果分析(设计FMEA)X 系统FMEA编号:A11-3510010AC015 子系统第37 页共37 页零部件:A11-3510010AC 设计责任:技质部编制者:王勇—技质部车型年/车辆类型:A11-奇瑞关键日期:2002年2月14日FMEA日期:2002年2月14日芜湖华亨汽车部件有限公司A11-3510010AC真空助力器带主缸总成DFMEA顾客名称:上汽奇瑞公司产品名称:真空助力器带主缸总成件号:A11-3510010AC编制部门:技术部门编制人/日期:夏根生/2002.02.14 审核人/日期:王小龙/2002.02.14。
失效模式及后果分析程序 - 新版2019(DFMEA)
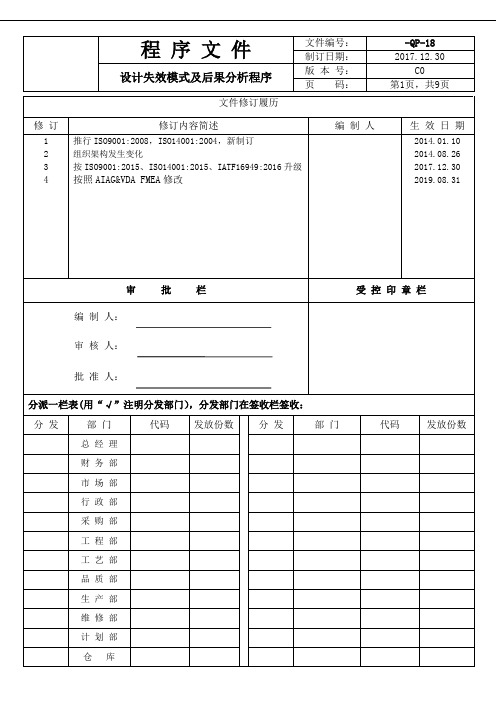
1.0目的在产品设计阶段,预先发现、评价产品可能潜在的失效与后果,及早找出能够避免或减少这些潜在失效发生的措施,并将此过程文件化,为以后的设计提供经验与参考。
2.0范围适用于产品设计中的设计失效模式及后果分析。
3.0职责3.1多方论证小组:负责制订DFMEA的各项内容及相关改进措施,建立纠正措施优先体系;当有新的失效模式出现时及时更改DFMEA。
3.2工艺部:主导多方论证小组分析并制订所有潜在失效模式及后果。
3.3各部门:参与DFMEA的制订和评估,相关纠正和预防措施的执行。
4.0定义4.1DFMEA:(Design Failure Mode& Effects Analysis)设计失效模式及后果分析.4.2顾客:顾客对DFMEA而言通常指“终端顾客”或“使用者”,但顾客也可能是法律法规要求4.3MSA:Measurement System Analysis(测量系统分析)包括准确性、线性、重复性、再现性、稳定性。
5.0流程无6.0内容6.1DFMEA制订说明:6.1.1工程部主导成立多方论证小组(即APQP策划小组);并确定DFMEA的实施项目。
多方论证小组根据客户的要求和生产加工情况,在APQP总进度中明确DFMEA项目的实施进度要求。
6.1.2多方论证小组组织品质部、工程部、生产部等相关部门的人员对整个生产流程进行评定。
6.1.3工程部针对过程失效模式和后果分析,确定相关过程的“严重度(S)”、“频度(O)”、“探测度(D)”,并通过S、O、D值的排列组合“措施优先级(AP)”,进行改进,编制DFMEA。
6.2在针对措施优先级(AP)行动时,需考虑以下因素:6.2.1严重度数高的(≥ 9)必须实施;6.2.2措施优先级(AP)为高(H)的优先实施;6.2.3措施优先级(AP)为中(M),但是易于实施,成本投入少的,优先实施。
6.2.4客户,项目小组,或者公司高层,在文件化的时候,提出采取改进措施的,给予实施;6.3工程部针对新产品、新材料、新技术应提交相关DFMEA资料。
dfmea潜在失效模式及后果分析案例

7
两侧导向筋强度不 足
CAE分析,导向筋 强度合理化 增加加强筋,提 高强度 连接处配合方式 选择合理
8
撞击导致结构破坏
8
连接处密封性差
密封性
手柄密封性 软管与软管连 不满足客户要 接管的密封性 求,影响手柄吸 差 尘效率 9 连接处密封性不足 增加密封件
裸机通过 重要部位断 需通过球 球击测试, 产品无法再使 裂(尤其是机 击测试 功能正常, 用 壳) 无断裂 电池包2000 电池包松脱或 次插拔寿命 电池使用效率 测试后挂靠 低 不牢 通过整机配 电池包撞墙 测试 机壳配合处断 裂
3
105
排除电池包倒扣位, 各暂定一个插拔力范 围。例3-5 kgf 1.参照样机考虑加弹 簧或弹片式减振结构
尺寸链分析计算保证尺 寸精度 尺寸链分析计算保证尺 寸精度 尺寸链分析计算保证尺 寸精度
检测插拔力 1.单边间隙 0.4mm以上 2.参照园林产 品
保证下盖与进 气口橡胶套翻 边配合无间隙 尘桶和下盖橡 胶密封圈尺寸 保证无间隙 分离管密封圈 翻边与尘桶之 间单边0.2mm过 盈 导流锥与橡胶 圈压装0.3mm过 盈 进气口与风机 橡胶套之间配 合单边过盈 过渡配合,IQC 尺寸全检 气阀密封圈喇 叭口做大,有 段直边配合 进气端两颗螺 丝柱保证高度 方向精度 密封圈与通风 盘内孔有单边 0.2mm过盈,检 测旋转力度 面接触部位开 槽加O型圈
8
A
1.塑件壳体加强筋 1.合理布设筋板 布设不合理 2.连接处强度薄 2.零件连接处强度 弱处加固 过于薄弱 1.机壳未做圆滑过 渡,磨损过大 2.电池包倒扣弹簧 疲劳 1.机壳参照园林 产品做圆滑过渡 2.选用成熟的电 池包 1.参照园林产品 机壳限位筋位强度 设计 2. 不够 配合尺寸计算累 积公差 1.参照园林产品 机壳与电池包卡扣 设计 2. 配合不当有干涉 配合尺寸计算累 积公差 机壳与电池包配合 配合尺寸计算累 间隙不当或无弹性 积公差 减震结构
橡胶摩擦及磨损分析

橡胶摩擦及磨损分析橡胶是非常重要且用量很大的工业材料之一,据不完全统计,2000年我国橡胶总消耗量将达220万吨,摩擦学性能是橡胶制品的一项非常重要的指标,例如橡胶轮胎的耐磨性能、刹车性能和行车效率、密封件的耐磨性等。
提高橡胶制品的耐磨性和使用寿命,可以在节约能源、材料、润滑剂等方面带来相当可观的经济效益和社会效益。
橡胶是一种弹性模量很低、粘弹性很高的材料,因此橡胶的摩擦具有不同于金属和一般聚合物的特征。
橡胶与刚性表面在滑动接触界面上的相互作用力包括粘着和滞后两项,而其摩擦力也正是由这两部分组成:F = F a+ F h式中F a——粘着摩擦力,F h——滞后摩擦力。
粘着摩擦起因于橡胶与对偶面之间粘着的不断形成和破坏,滞后摩擦则是由表面微凸体使滑动橡胶块产生周期性变形过程中能量的耗散引起的。
当橡胶在坚硬光滑的表面上滑动时,摩擦力主要表现为粘着摩擦,根据弹性体摩擦的粘着理论,可以得出粘着摩擦力F a为[6]:F a= K1S( E r/p r) tanδ (r<1)式中,K1——常数;S——滑动界面的有效剪切强度;p——正压力;E——储能模量;tanδ——损耗角正切(粘弹性参数)。
显然,橡胶的粘着摩擦与材料的损耗角正切tanδ成正比。
润滑剂的存在可以阻止橡胶与对偶间的直接接触,使粘着摩擦成分大大降低,滞后摩擦起主要作用。
根据弹性体滞后摩擦的松弛理论,可得出滞后摩擦力为[6]:F h= K2( p/E′) n tanδ (n≥1)式中,K2为与几何形状因子有关的常数。
滞后摩擦力也与tanδ成正比,所不同的是,滞后摩擦力与变形程度因子( p/E′) n成正比。
由此,橡胶的摩擦力可表示为F=[K1S(E′/p r)+K2(p/E′)n]tanδ金属和塑料磨损表面的特征是磨痕与摩擦方向平行,而橡胶磨损表面的磨痕却垂直于摩擦方向,并且磨痕在橡胶表面形成山脊状突起,突起之间间距相等,高度相同,形成所谓的磨损斑纹。
橡胶在铁路应用中的失效模式及预防措施
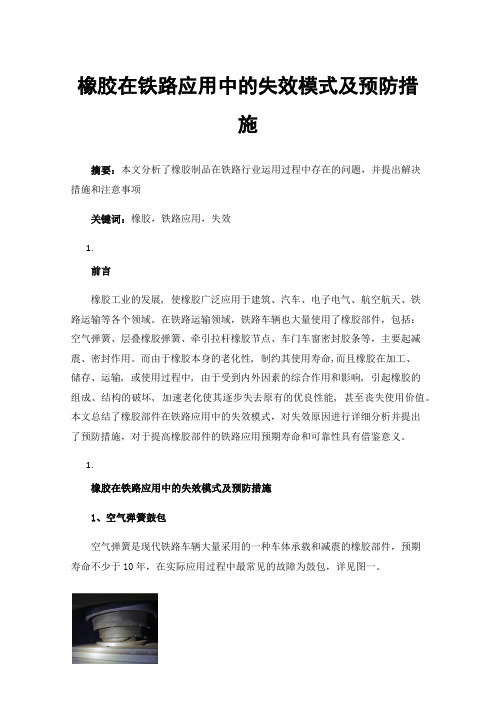
橡胶在铁路应用中的失效模式及预防措施摘要:本文分析了橡胶制品在铁路行业运用过程中存在的问题,并提出解决措施和注意事项关键词:橡胶,铁路应用,失效1.前言橡胶工业的发展, 使橡胶广泛应用于建筑、汽车、电子电气、航空航天、铁路运输等各个领域。
在铁路运输领域,铁路车辆也大量使用了橡胶部件,包括:空气弹簧、层叠橡胶弹簧、牵引拉杆橡胶节点、车门车窗密封胶条等,主要起减震、密封作用。
而由于橡胶本身的老化性, 制约其使用寿命,而且橡胶在加工、储存、运输, 或使用过程中, 由于受到内外因素的综合作用和影响, 引起橡胶的组成、结构的破坏, 加速老化使其逐步失去原有的优良性能, 甚至丧失使用价值。
本文总结了橡胶部件在铁路应用中的失效模式,对失效原因进行详细分析并提出了预防措施,对于提高橡胶部件的铁路应用预期寿命和可靠性具有借鉴意义。
1.橡胶在铁路应用中的失效模式及预防措施1、空气弹簧鼓包空气弹簧是现代铁路车辆大量采用的一种车体承载和减震的橡胶部件,预期寿命不少于10年,在实际应用过程中最常见的故障为鼓包,详见图一。
图一鼓包区域原因分析:(一)机理/结构及差异分析橡胶堆是一种较普遍的锥形橡胶堆结构。
根据既往经验,导致橡胶堆鼓包问题的一般原因为:产品局部位置橡胶内部出现裂口或橡胶-金属粘接不良,在运用过程中缺陷逐渐扩大,问题区域橡胶脱离本体后,在长期受力下被挤压形成鼓包状态。
(二)产品拆解分析芯轴上可见一小块明显的金属裸露区域(面积约0.15cm²),见图二,以裸露区域为起点向下成明显的扇形区域内均为薄层附胶,其他区域包胶良好,扇形最终区域与鼓包区域一致,即剥离起点为小块金属裸露区域,该区域面积小,排除金属骨架表面处理工艺不良,骨架整体污染的可能,判断是芯轴在硫化前的操作中(周转、预烘、装模等)偶然发生了局部磕碰、划伤,造成此处胶黏剂受到损伤,导致产品在使用中粘接失效。
图二空簧橡胶堆芯轴顶出破坏照片分析结论:鼓包问题原因为空簧橡胶堆芯轴在硫化前的操作中发生磕碰,造成芯轴上端局部位置胶黏剂受损,在使用中发生粘接破坏(属金属-胶黏剂破坏);芯轴包胶在使用过程中由缺陷区域开始逐渐向下剥离而形成鼓包。
胶带失效模式
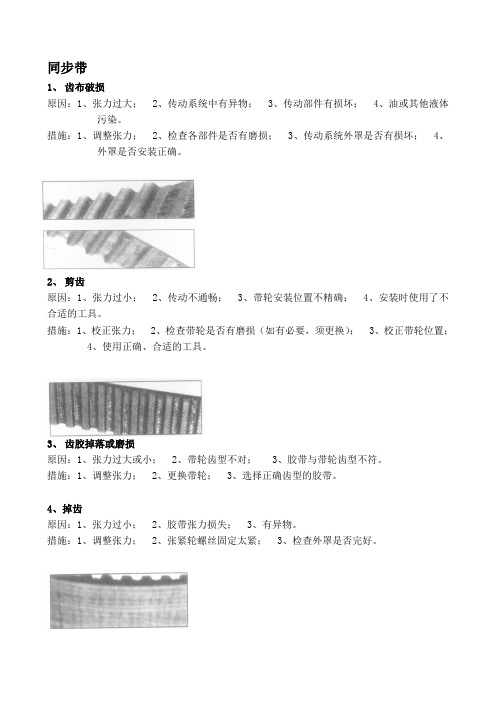
同步带1、齿布破损原因:1、张力过大; 2、传动系统中有异物; 3、传动部件有损坏; 4、油或其他液体污染。
措施:1、调整张力; 2、检查各部件是否有磨损; 3、传动系统外罩是否有损坏; 4、外罩是否安装正确。
2、剪齿原因:1、张力过小; 2、传动不通畅; 3、带轮安装位置不精确; 4、安装时使用了不合适的工具。
措施:1、校正张力; 2、检查带轮是否有磨损(如有必要,须更换); 3、校正带轮位置;4、使用正确、合适的工具。
3、齿胶掉落或磨损原因:1、张力过大或小; 2、带轮齿型不对; 3、胶带与带轮齿型不符。
措施:1、调整张力; 2、更换带轮; 3、选择正确齿型的胶带。
4、掉齿原因:1、张力过小; 2、胶带张力损失; 3、有异物。
措施:1、调整张力; 2、张紧轮螺丝固定太紧; 3、检查外罩是否完好。
5、背胶有裂痕原因:1、温度不正常。
措施:1、使用耐热橡胶加工的胶带。
6、胶带部分脱落或膨胀原因:1、油污。
措施::1、排除漏油故障。
7、带边磨损原因:1、带轮/张紧轮位置安装不精确; 2、轮缘磨损。
措施:1、校正带轮位置。
如果张紧轮固定太死则须调整;2、更换所有磨损的带轮。
8、噪音原因:1、张力不合适; 2、带轮位置不精确; 3、轮缘磨损。
措施:1、校正张力; 2、校正带轮位置; 3、更换已磨损的带轮。
9、线绳断裂原因:1、胶带过度弯折; 2、安装时使用不适用工具。
措施:1、不得使胶带过度弯折;2、不得使用不适用的工具或撬装胶带;别的扭曲或压迫胶带边缘。
安装时应使张紧轮完全松弛以便达到最小的传动长度。
多楔带1、顶布磨损原因:在胶带路径上可能有安装不合适的部件措施:1、更换胶带并检查所有部件; 2、校正张力。
2、掉楔原因:1、温度过高; 2、胶带老化。
措施:1、立即更换胶带。
3、起球原因:1、张力过小; 2、带轮位置安装不精确; 3、带轮有磨损。
措施:1、更换胶带; 2、更换磨损的带轮。
4、楔齿出现裂痕原因:1、温度持续过高; 2、张力过大; 3、自然老化。
东风车轮故障失效模式

车轮公司产品故障失效模式分析(十五)
1 故障模式:车轮总成轮胎裂纹、破 损、划伤
2 产品名称:
车轮总成 3 失效分析: 车轮总成轮胎裂纹、破损、划伤,引起车轮总成轮胎早期失效,车轮总成 异常损坏。 4 失效原因分析:
4.1 顾客因整车行驶不当,造成车轮总成轮胎碰撞破损与划伤。
4.2 车轮总成在生产、存贮、运输过程造成轮胎破损与划伤。 4.3 车轮总成轮胎在生产过程、存贮、运输过程造成的质量缺陷。车轮公司将 向车轮轮胎供应商追究制造质量责任。 5 责任单位:须分析具体实物判定。 5.1 属于条款4.1原因造成失效模式,责任单位是顾客。 5.2 属于条款4.2和4.3原因造成失效模式,责任单位是制造单位。本条款仅适用 车轮公司提供的车轮总成。
5 责任单位:制造单位 备注:
车轮公司产品故障失效模式分析(十二)
1 故障模式:车轮合成轮辋与轮辐焊 缝处裂纹或脱焊
2 产品名称: 各类型钢车轮合成
3 失效分析:
型钢车轮合成轮辋轮辐焊缝处裂纹或脱焊,引起车轮合成强度失效,车轮 总成可靠性丧失。
4 失效原因分析: 4.1 车轮合成轮辋与轮辐焊接工序焊接参数波动,车轮合成使用时轮辋与轮辐 焊缝处产生疲劳裂纹或脱焊。 4.2 车轮合成轮辋与轮辐焊接工序操作不当,车轮合成焊偏,使用时轮辋与轮 辐焊缝处产生疲劳裂纹或脱焊.。 4.3 顾客整车运营时严重超载,引起车轮合成轮辋与轮辐焊缝处产生疲劳裂纹 或脱焊。 5 责任单位:须分析具体实物和证据判定。 5.1 属于条款4.1和4.2原因造成失效模式, (顾客需出示产品使用中,车辆无严 重超载的证据,如运营单、车装货物等。)责任单位是制造单位。 5.2 属于条款4.3原因造成失效模式,责任单位是顾客。 备注:
车轮公司产品故障失效模式分析(九)
帘线橡胶复合材料多层结构的力学特性及失效形式研究

第2期
吴 健等.帘线/橡胶复合材料多层结构的力学特性及失效形式研究
68
轮 胎 工 业
2021年第41卷
研究搭接段间距对复合材料多层结构的力学性能 影响尤为重要。
为此,本工作针对典型帘线/橡胶复合材料结 构,开 展 不 同 帘 线 层 接 头 搭 接 形 式 和 不 同 搭 接 段 间 距 下 橡 胶 复 合 材 料 结 构 的 力 学 行 为 研 究,以 揭 示其对帘线/橡胶复合材料的失效形式以及强度 等 力 学 性 能 的 影 响 规 律,为 工 程 中 橡 胶 复 合 材 料 制品的设计与制备提供依据。
69
ःҦMPa
ःҦMPa
70
60
50
2 40
1
30
3
20
10
0
15
30
45Βιβλιοθήκη ःԪ%(a)顺型顺式70
60
50
40
1
3
30
2 20
10
0
15
30
45
ःԪ%
(b)顺型逆式
80
60
2 40
1 3
20
ःҦMPa
0
20
40
60
ःԪ%
(c)凹型凸型
搭接段间距/mm:1—5;2—15;3—25。
图5 不同搭接形式下帘线/橡胶复合材料的 应力-应变曲线
ୃଋ᫁ऎ
ୃଋ᫁ऎ
图3 拉伸试验机
- 1、下载文档前请自行甄别文档内容的完整性,平台不提供额外的编辑、内容补充、找答案等附加服务。
- 2、"仅部分预览"的文档,不可在线预览部分如存在完整性等问题,可反馈申请退款(可完整预览的文档不适用该条件!)。
- 3、如文档侵犯您的权益,请联系客服反馈,我们会尽快为您处理(人工客服工作时间:9:00-18:30)。
橡胶轮挡阻挡功效和失效模式分析与计算李福海 姚红宇中国民用航空总局航空安全技术中心北京朝阳区西坝河北里甲24号,100028摘 要:飞机轮挡是常用的地面安全设备,当飞机长期停放、过站或航后时,通常是利用轮挡阻挡飞机发生移动,从而避免引发航空地面事故。
目前国内常用的轮挡有橡胶轮挡、金属轮挡、塑料轮挡和木质轮挡。
本文以B737-300/800飞机为例,详细介绍了飞机停放时地面风载估算方法;以B737-300/800飞机轮胎外形轮廓实测数据和W92橡胶轮挡为例,讨论了轮挡阻挡功效及其可能失效形式,并在飞机依靠轮挡所能克服的最大风速条件下对W92橡胶轮挡的阻挡功效和可能失效形式进行了分析计算。
关键词:地面安全;地面风载;轮挡;阻挡功效;失效模式The Analysis and Calculation aboutthe Restraint Efficacy and Failure Forms of Rubber ChocksLi Fuhai, Yao HongyuCenter of Aviation Safety and Technology, CAACNo.24A, Xibahe Beili, Chaoyang District, Beijing 100028 Abstract:Wheel chocks are the most common ground devices used to restrain an airplane from movement due to normal wind, when the airplane is parked, transiting or after flight. There are rubber chocks, metal chocks, urethane chocks and wooden chocks used in China.This paper introduces the method of calculating the thrust and lift forces on airplanes on the ground. It also studies the restraint efficacy and the failure forms of W92 chock during extreme high wind conditions.Key words: ground safety; the wind load upon the airplane; wheel chock; restraint efficacy; failure form一、引 言我国民航飞机多数是从国外引进而来,目前从欧美进口使用的飞机,其有关各种地面保障设备多需单独购买,为了节约资金、降低费用,因此一些机场和维修单位参照国外的轮挡进行仿制,从而使得国内在用轮挡五花八门、难以管理。
近年来,由于这些仿制轮挡本身阻挡功能失效,或者由于轮挡使用不规范等原因,导致飞机移动或受损,造成的地面事故或不安全事件有所增多。
据了解,目前国内有关轮挡的设计和生产资料基本没有,而有关轮挡的使用也只是在民用航空器维修手册等资料中有一些简单说明和要求;国内虽有厂商生产轮挡,但由于生产的轮挡未经试验和鉴定,生产的轮挡是否满足实际使用要求,是否对轮胎有腐蚀作用或其它影响都有待证明。
因此,研究轮挡的使用条件、使用中反映出来的问题和失效模式,研究轮挡的阻挡功效,对于确保飞机的地面安全是非常重要和有意义的。
二、飞机停放时地面风载分析与计算本文规定坐标系如图1所示,坐标原点位于机头顶点在地面的投影处,X轴通过原点沿纵轴指向机尾,Y轴通过原点指向机身右侧,Z轴由右手法则确定,其中Y-Z平面为基准面。
图1 飞机坐标系由于飞机几何外形的气动属性,飞机停放时逆风摆放虽稳定性好,但最容易被风吹动而后退;垂直风向摆放时,即在900侧风作用下最容易在风中打转。
因此,本文仅讨论逆风和垂风摆放两种极限情况。
2.1 飞机前视图投影面积及形心计算1)面积估算方法介绍从B737-800飞机AMM手册中截取飞机侧视图,利用图形软件测量飞机长度,可知飞机长度显示尺寸与标注尺寸比为4.70,如图2所示。
同理可测得飞机高度显示尺寸与标注尺寸比为4.55。
因此,侧视图上任一封闭图形面积被放大21.39倍。
图2 飞机长度测量再次利用图形软件,用多条折线圈描垂尾边界,并形成封闭图形,可测得垂尾面积放大后数值为569.97㎡,如图3所示。
因此,可以计算求得垂尾面积为26.65㎡。
垂尾标注面积是26.44m2,面积计算误差精度为0.79%,因此本方法用于工程计算是可靠的。
图3 垂尾投影面积测量2)飞机前、侧视图投影面积计算由上述面积计算方法,在飞机前视图上计算求得长度平均放大比例为5.32,高度平均放大比例为6.30,前视图投影面积放大后为1287.20m2,所以前视图实际投影面积为38.37 m2;在飞机侧视图上计算求得长度平均放大比例为4.62,高度平均放大比例为4.62,侧视图投影面积放大后为3569.37m2,所以侧视图实际投影面积为166.59 m2。
3)飞机侧视图投影轮廓形心计算利用图形软件可以计算求得侧视图形心距基准距离为21.34m,形心距地面高度为4.09m,如图4所示。
图4 飞机侧视图投影轮廓形心2.2飞机地面停放时风载计算1)前风升力计算方法图5是B737-800在襟翼为50位置时的“滑跑时间-速度-地面承重”试验数据图。
由于实际飞机在停放时襟翼应为00,所以依据图5计算的前风升力会偏大,即地面对飞机的摩擦力会偏小。
因此,如果在襟翼为50位置时飞机不能被前风吹动,襟翼在00位置时飞机也不会被吹动。
图5飞机滑跑时地面对飞机支撑力由图5可建立飞机升力公式:G L=0.0321VG和地面对飞机的支撑力近似公式:G v=(9.8-0.0321V)G其中:G L—飞机升力(N);G v—地面对飞机的支撑力(N);V—飞机滑跑速度(m/s);G—飞机重量(N)。
2)前风、900侧风下推力计算方法依据《飞机机体系留设计要求》中有关风载计算方法,可知风对飞机的推力公式:D=6331A(V/100)2其中:D—平行于风向的合力(N);A—飞机垂直于风向的平面内的投影面积(㎡);V—风速(m/s)。
假设飞机依靠轮挡所能克服的最大风速为飞机需要系留时的最小风速,可以计算求得前风升力、地面支撑力、前风推力和侧风推力,如表1所示。
表1 飞机停放时地面风载刹车状态 有停留刹车 无停留刹车地面状况 冰雪 湿滑 干燥 冰雪 湿滑 干燥kts 20 40 55 10 20 30 速 度m/s 10.29 20.58 28.29 5.14 10.29 15.43 前风升力(N) 0.3303G0.6605G0.9080G0.1650G0.3303G 0.4952G 前风推力(N)HB7082-94 2572.1410288.5719441.51641.792572.14 5783.57侧风推力(N)HB7082-94 11167.3744669.5084408.502786.4211167.37 25110.32三、橡胶轮挡阻挡功效及其失效模式分析橡胶轮挡的工作原理:当机轮压在轮挡上时,由轮挡反作用力的水平分量阻挡飞机移动,由“轮胎/轮挡”界面和“轮挡/地面”界面的摩擦力防止轮挡移动,由轮挡的刚度保持轮挡的形状,由轮挡的强度保持轮挡完好不破损。
根据该工作原理,其失效模式大致可以分为: 1)阻挡功能失效:是指轮挡在各外力作用下无法保持平衡状态而发生运动,或者由于各种因素造成无法正常使用,失效形式包括推开、爬越、翻滚、崩开、压住等等。
本文将对上述各种失效形式进行分析、讨论。
2)理化性能失效:是指轮挡使用的材料无法承受外力作用而破损,或者轮挡受压变形过大,不能正常工作,或者橡胶材料固有属性发生变化,失效形式包括强度、刚度失效、热老化、耐酸碱性能降低等等。
3.1 轮挡、轮胎尺寸实测数据处理1)轮挡尺寸参数B737-800飞机使用W92轮挡,实际工作中多用两个W88轮挡代替。
W92轮挡实物如图6所示,其剖面实测尺寸如图7所示。
图中尺寸单位为㎜,其中上部倒角半径为10㎜。
图6 W92轮挡实物图 图7 W92轮挡侧面剖视图 2)轮挡使用假设轮挡摆放时,每个轮挡距轮胎的摆放空隙可能不同。
因此,在大风作用下,轮胎与轮挡接触并有爬上趋势时,会造成飞机有前后俯仰或左右倾斜的趋势。
但实际上,由于规定的摆放距离很小,所以由于摆放距离的差值造成的飞机俯仰或倾斜程度也会很小,其影响可以忽略不计。
因此,本文中假设每个轮挡摆放时距机轮的距离相等。
3)轮胎轮廓参数轮胎在实际使用中由于外力作用会发生变形,表2是某公司B737-300飞机在停放时、加载后主轮轮胎外形轮廓实测数据。
表2 主轮轮胎外形轮廓测试数据横坐标(㎜)纵坐标(㎜)停放时出港前0 0 0203 218 13243 257 26270 283 39292 300 52315 319 64352 363 96382 391 128409 421 160430 435 192依据表2数据,可绘制该飞机主轮轮胎外形变形前后轮廓,其与轮挡接触情况如图8、图9所示。
图8 飞机停放时轮胎与轮挡接触示意图 图9 飞机加商载后轮胎与轮挡接触示意图 其中蓝色虚线为飞机停放时轮胎外形拟合曲线,红色点划线为加载后轮胎外形拟合曲线,分别相当于将处于水平位置的基础圆向下平移45㎜和60㎜,如图10所示。
图10 轮胎变形前后拟合曲线B737-800飞机主轮轮胎较B737-300飞机的略大,尺寸为H1130.3×419.1-533.4(单位:㎜)。
因为B737-800飞机主轮轮胎与B737-300飞机的主轮轮胎材料相同、尺寸相近,所以可以近似认为B737-800飞机主轮轮胎在停放时和加载后的轮廓拟合曲线与B737-300飞机的有相同的向下平移量,如图11和图12所示。
两种情况下,轮胎都是与轮挡上部相接触,与实际情况相符,如图13所示。
图11 飞机停放时轮胎与轮挡接触示意图 图12 飞机加载后轮胎与轮挡接触示意图图13 W88轮挡与轮胎接触位置5)飞机称重记录飞机在过夜停放时,其重量由飞机基本空重、剩余燃油等几部分组成,其中基本空重占主要比例。
此外,在地面状态一定的情况下,飞机重量越大,地面所能提供的最大滑动或滚动摩擦力就越大。
因此,本文以某架B737-800飞机喷漆后的称重数据进行各种情况下的可能失效形式计算和验证,如表3所示。
如果此种重量下轮挡不失效,则在其它更大的飞机重量下也不会失效。
表3飞机称重记录第一次测量(㎏)第二次测量(㎏)测量点平均值(㎏)总重(㎏)指示值 修正值指示值修正值41005.36 前起落架 3336.68 0.45 3336.680.91 3336.00左起落架 左轮 8972.21 -2.278965.40-1.3618808.75右轮 9829.97 -5.909836.32-4.08左轮 9846.75 -0.919855.370.00右起落架右轮 8963.59 -0.918959.51-0.9118813.973.2失效形式分析如前文所述,本文只考虑前风和900侧风两个风向;同时刹车情况分为有、无刹车两种;地面情况分为干燥、湿滑和冰雪三种。