六西格玛经典案例
六西格玛经典案例

六西格玛经典案例在六西格玛质量管理方法中,通过分析和改进业务流程,以减少缺陷和提高效率,从而实现优秀质量和高度效益。
以下是三个经典的六西格玛案例。
1. Motorola的六西格玛实践Motorola是六西格玛的奠基者之一、20世纪80年代,Motorola采用六西格玛方法,以改进生产过程并提高质量。
在一个以缺陷率而不是零缺陷为标准的产业中,Motorola在一年内将缺陷率从超过三十万个降低到每百万个产品中只有5个。
六西格玛的成功引起了其他公司的注意,并成为其他公司实施质量管理的典范。
2. General Electric(GE)的六西格玛实施GE是六西格玛的早期采用者,它将六西格玛引入公司的各个部门和业务领域。
公司的首席执行官杰克·韦尔奇在1995年将六西格玛作为公司的战略重点。
GE在实施过程中的一个成功案例是其航空发动机业务部门,该部门通过六西格玛方法降低了生产过程中的缺陷率,并提高了航空发动机的性能和可靠性。
GE的成功证明了六西格玛可以在各种行业中实现卓越的结果。
3.美国政府的六西格玛应用六西格玛方法不仅在企业界取得成功,而且在政府部门中也有很好的应用。
美国政府决定在1995年引入六西格玛方法,以提高效率并减少浪费。
例如,美国联邦航空管理局(FAA)使用六西格玛方法改进了飞行管制和管理过程,减少了航班延误和事故。
美国海军也采用了六西格玛方法来改善军舰维护和修理过程,提高了战斗力和减少了成本。
以上是六西格玛的三个经典案例,它们都展示了通过六西格玛方法来实现质量改进和效益提高的潜力。
这些案例证明了六西格玛是一个非常有力的质量管理方法,可以在各个领域带来显著的结果。
无论是在制造业、服务业还是政府部门,六西格玛都能够提供一个可靠的框架来解决质量和效率方面的挑战。
精益六西格玛的改善案例

精益六西格玛的改善案例案例:汽车制造流程改善背景:汽车制造公司在生产过程中遇到了一些问题。
产品质量不稳定,交付时间延长,成本高涨,因此需要通过改善流程来提高生产效率和降低成本。
目标:-提高产品质量稳定性,降低缺陷率-缩短交付时间,提高客户满意度-降低制造成本,提高利润率方法:1.项目选择:选择一个关键的制造流程进行改善。
在该公司中,组装过程是最关键且容易出现问题的环节,因此选择组装流程作为改善项目。
2.流程分析:通过流程图和价值流图,对组装流程进行详细分析。
识别出每个环节中的瓶颈和浪费,如等待时间、运输时间、不必要的重复工作等。
3.数据收集:收集关于缺陷率、交付时间和成本的数据。
这些数据将成为决策的基础。
4.根本原因分析:使用工具如鱼骨图、五力模型、因果图等,找出导致问题的根本原因。
可能的原因包括不合理的工作流程、不合适的设备、员工技能不足等。
5.解决方案设计:根据根本原因分析的结果,设计出改进方案。
例如,通过优化工作流程、提高设备质量、加强员工培训等。
6.实施改进:在一定范围内进行试点实施改进方案,收集数据并评估效果。
根据数据的结果,对方案进行调整和改进,直到达到预期的效果。
7.控制改进:建立一套监控体系,确保改进效果能够持续。
通过设立关键绩效指标(KPI)和改进计划,对改进方案进行监控和调整。
结果:经过精益六西格玛方法学的改进,该汽车制造公司取得了显著的效果:-产品质量稳定性得到明显提高,缺陷率显著降低。
-交付时间缩短,客户满意度有了显著提升。
-制造成本明显降低,利润率得以提高。
结论:。
6西格玛平安案例

6西格玛平安案例案例1一个半导体簿膜设备制造商在"6-Sigma"实施前的状况是:由于设计研发周期太长,该公司老是不能及时将产品推入市场,而且由于故障率太高,致使售后效劳和维修本钱太高。
售后效劳和维修本钱包括:(1)顾客埋怨、投诉和保修本钱;(2)客户维修本钱;(3)延迟发货和停产损失。
该公司一台设备的平均单价是US$7500K。
该公司希望通过"6-Sigma"的改进运作,能使公司赶上其竞争对手,如Toshiba,Actel,Applied,Material等公司。
该公司的"6-Sigma"运作是从建立"6-Sigma"团队开始的。
核心团队由研发工程、应用工程及可靠性工程组成,其它部门(如市场、制造、财务、质量等)负责支持与协助。
公司的总裁直接领导一个"6-Sigma"负责人,该"6-Sigma"负责人是由公司的副总裁担任。
在"6-Sigma"负责人之下,是"6-Sigma"黑带委员会(包括MBB黑带师、研发总监、技术总监)、"6-Sigma"财务委员会、研发系统1#、研发系统2#、研发系统3#和两个黑带项目团队。
该公司"6-Sigma"的推进步骤如下:由管理高层确定"6-Sigma"的开展计划和管理结构,选定KPI,然后进行管理高层的培训和"6-Sigma"BB培训。
在培训过程中,BB黑带项目也要同时选定和实施,最后是项目的审核。
选定的KPI是:(1)研发周期缩短2个月;(2)生产过渡期合格率由65%提高到80%;(3)减少客户报怨和维修率80%;(4)预计财务回报:通过降低研发周期可创造亿美元(US$350KK);通过提高合格率可创造2亿美元(US$200KK);通过降低维修成本可节约4亿美元(US$400KK)。
六西格玛案例分析
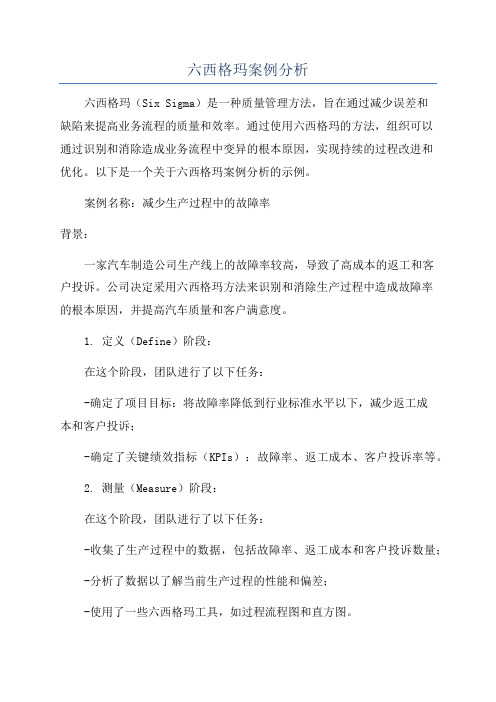
六西格玛案例分析六西格玛(Six Sigma)是一种质量管理方法,旨在通过减少误差和缺陷来提高业务流程的质量和效率。
通过使用六西格玛的方法,组织可以通过识别和消除造成业务流程中变异的根本原因,实现持续的过程改进和优化。
以下是一个关于六西格玛案例分析的示例。
案例名称:减少生产过程中的故障率背景:一家汽车制造公司生产线上的故障率较高,导致了高成本的返工和客户投诉。
公司决定采用六西格玛方法来识别和消除生产过程中造成故障率的根本原因,并提高汽车质量和客户满意度。
1. 定义(Define)阶段:在这个阶段,团队进行了以下任务:-确定了项目目标:将故障率降低到行业标准水平以下,减少返工成本和客户投诉;-确定了关键绩效指标(KPIs):故障率、返工成本、客户投诉率等。
2. 测量(Measure)阶段:在这个阶段,团队进行了以下任务:-收集了生产过程中的数据,包括故障率、返工成本和客户投诉数量;-分析了数据以了解当前生产过程的性能和偏差;-使用了一些六西格玛工具,如过程流程图和直方图。
3. 分析(Analyze)阶段:在这个阶段,团队进行了以下任务:-确定了导致故障率升高的根本原因;-使用了五力分析和鱼骨图等工具,以识别可能的原因;-根据数据和分析结果,确定了一个或多个关键影响故障率的因素。
4. 改进(Improve)阶段:在这个阶段,团队进行了以下任务:-开发了改进计划,包括减少故障率的具体措施和时间表;-实施了改进措施,并记录了结果。
5. 控制(Control)阶段:在这个阶段,团队进行了以下任务:-实施了独立检查和监控措施,以确保改善措施的可持续性;-追踪关键绩效指标,如故障率、返工成本和客户投诉;-确立了持续改进的机制,以确保过程持续优化。
通过使用六西格玛方法,该汽车制造公司成功降低了生产过程中的故障率。
在实施改进措施后,故障率从10%降低到行业标准的3%以下,成功降低了返工成本和客户投诉率。
此外,公司在生产线上建立了严格的质量控制措施和监控机制,以确保持续改进和优化。
精益六西格玛案例

精益六西格玛案例
精益六西格玛是一种管理方法,它结合了精益生产和六西格玛的优点,旨在提
高效率和质量。
下面我们来看一个实际的案例,了解精益六西格玛是如何在实践中发挥作用的。
某汽车零部件制造公司在生产过程中遇到了一些问题,导致了生产效率低下和
产品质量不稳定。
经过分析,他们决定引入精益六西格玛方法来改善生产流程。
首先,他们进行价值流分析,找出了生产过程中的浪费和瓶颈。
然后,他们采
用精益工具,如5S和Kanban,对生产车间进行了重新布局和标准化。
同时,他们
还对员工进行了培训,让他们更好地理解和运用精益工具。
在改善生产流程的同时,公司还引入了六西格玛的方法,通过数据分析和流程
控制,找出了造成产品质量不稳定的根本原因,并采取了相应的改进措施。
经过一段时间的努力,公司取得了显著的成效。
生产效率得到了提高,产品质
量稳定性也得到了保障。
公司的客户满意度得到了提升,市场竞争力也得到了增强。
通过这个案例,我们可以看到精益六西格玛在实际中的应用效果。
它不仅可以
帮助企业提高效率和质量,还可以带来客户满意度和市场竞争力的提升。
综上所述,精益六西格玛是一种非常有效的管理方法,它可以帮助企业解决生
产过程中的问题,提高效率和质量,实现持续改进和持续增长。
希望更多的企业能够引入精益六西格玛,实现可持续发展。
六西格玛改进案例

六西格玛改进案例以六西格玛改进案例为题,列举如下10个案例:1. 生产流程改进案例:在一个制造业公司,生产流程中存在着许多瑕疵品。
为了提高产品质量,该公司采用了六西格玛方法进行改进。
通过分析生产过程中的关键环节,确定了引起瑕疵品的主要原因,并通过改进工艺和设备,减少了瑕疵品的产生率。
2. 供应链管理改进案例:一家零售公司的供应链管理存在着库存过剩和缺货的问题,导致了销售额下降。
为了解决这个问题,该公司运用了六西格玛方法,对供应链中的各个环节进行了优化。
通过提高库存预测的准确性,优化订货策略,以及改进供应商管理,该公司成功解决了库存过剩和缺货问题。
3. 客户投诉处理改进案例:一家电信运营商的客户投诉率较高,影响了公司的声誉。
为了改善客户满意度,该公司运用了六西格玛方法,对客户投诉处理流程进行了改进。
通过提高投诉处理的效率和质量,该公司成功降低了客户投诉率,并提升了客户满意度。
4. 销售流程改进案例:一家保险公司的销售流程存在着繁琐和低效的问题,导致了销售人员的工作效率低下。
为了提高销售业绩,该公司采用了六西格玛方法,对销售流程进行了改进。
通过简化流程、优化销售工具和培训销售人员,该公司成功提升了销售人员的工作效率和销售业绩。
5. 质量管理改进案例:一家制药公司的质量管理体系存在着缺陷,导致了产品质量不稳定。
为了提高产品质量,该公司采用了六西格玛方法,对质量管理体系进行了改进。
通过加强质量控制、改进检验方法和加强员工培训,该公司成功提升了产品质量的稳定性。
6. 项目管理改进案例:一个IT项目存在着进度延误和成本超支的问题,导致了项目无法按时交付。
为了解决这个问题,该公司采用了六西格玛方法,对项目管理进行了改进。
通过优化项目计划、加强资源管理和改进沟通机制,该公司成功提高了项目的进度控制和成本控制能力。
7. 售后服务改进案例:一家家电企业的售后服务存在着响应速度慢和问题解决率低的问题,导致了客户的不满意。
6西格玛课题优秀案例
6西格玛课题优秀案例
6西格玛是一种管理方法论,旨在通过精益和高效的方式提高组织的质量和效率。
下面是一些6西格玛优秀案例:
1. GE(通用电气):GE是最早采用6西格玛的公司之一,它成功地将其应用于所有业务领域,从而提高了效率、降低了成本,增强了客户满意度。
2. 联想:联想采用6西格玛改进了生产流程,消除了浪费,并大幅提高了产品质量和客户满意度。
3. 诺基亚:诺基亚采用6西格玛来提高其生产效率,降低了缺陷率,并提高了客户满意度。
4. 波音:波音公司采用6西格玛来提高飞机生产过程中的效率和质量,减少了缺陷率和生产时间,并提高了客户满意度。
5. 福特汽车:福特引入6西格玛来提高其生产流程,从而减少了制造缺陷、降低了成本,并提升了客户满意度。
这些公司的成功案例证明了6西格玛管理方法论的实用性和有效性,可以帮助组织提高质量、降低成本、增强客户满意度和竞争力。
六西格玛案例分析
六西格玛案例分析六西格玛是一种用于改进流程和提高质量的管理方法,起源于20世纪80年代的美国,并迅速传播到全球各个行业。
以下是一个六西格玛案例分析。
某汽车制造公司的生产线在生产过程中遇到了一些问题,导致产品质量不稳定并出现了一些缺陷。
公司决定使用六西格玛方法来改进生产流程和提高产品质量。
首先,公司成立了一个专门的团队来负责这个项目。
团队由各个部门的专业人员组成,包括生产、质量控制、设计和工程等。
团队首先进行了问题的分析和数据收集。
他们通过观察生产线,收集了各个环节的数据,包括生产时间、产品缺陷情况和操作员的培训记录等。
接下来,团队使用六西格玛的DMAIC方法来改进生产流程。
他们首先进行了一个流程映射,将整个生产流程以图表的形式展示出来,以便更好地理解和分析。
通过分析数据,团队发现在某个特定的环节,产品缺陷率特别高。
他们进一步调查发现,由于操作员没有得到足够的培训和支持,他们在这个环节上的操作不够规范和标准化,导致了缺陷的产生。
为了解决这个问题,团队进行了一些改变。
他们重新设计了工作流程,并制定了更加详细和清晰的操作规范。
同时,他们也加强了对操作员的培训和技能提升。
在新的工作流程和操作规范的指导下,生产线的产品缺陷率明显下降。
并且,在实施改进后的几个月内,产品缺陷率一直稳定在一个较低的水平上。
通过这个案例的分析,我们可以看到六西格玛方法在这个汽车制造公司的生产线改进中发挥了重要的作用。
通过数据收集和分析,团队能够准确地找到问题的根源,并制定相应的改进方案。
通过重新设计工作流程和加强对操作员的培训,生产线的产品质量得到了明显的提高。
这个案例也展示了六西格玛方法在提高流程稳定性和质量方面的潜力。
6西格玛课题优秀案例
6西格玛课题优秀案例
六西格玛是一种质量管理方法,旨在通过统计学的方法和工具来降低产品和服务的缺陷率,提高生产效率和降低成本。
下面是一些六西格玛课题的优秀案例:
1. LG 电子的微波炉门泄漏问题:LG 电子在制造微波炉时遇到
了门泄漏问题,这严重影响了产品质量和品牌形象。
通过使用六西格玛方法,LG 电子的团队确定了问题的根本原因,并制定了改进计划,最终成功解决了这个问题。
2. 波音公司的飞机维修成本降低:波音公司使用六西格玛方法来降低飞机的维修成本,通过分析和测量,确定了问题的的根本原因,并采取了一系列措施来减少维修成本。
这项改进不仅降低了公司的运营成本,还提高了飞机的可靠性和安全性。
3. 沃尔玛的库存管理优化:沃尔玛使用六西格玛方法来优化库存管理,通过测量和分析问题,制定了一套优化方案,成功地降低了库存成本和提高了供应链的效率。
4. 通用电气的生产效率提高:通用电气使用六西格玛方法来提高生产效率,通过分析和测量,确定了问题的根本原因,并采取了一系列措施来提高效率,最终提高了公司的盈利能力。
这些案例展示了六西格玛方法在各个领域的应用和成功的结果,不仅提高了产品或服务的质量,还降低了成本和提高了生产效率。
六西格玛管理经典案例
六西格玛管理经典案例
一、六西格玛管理经典案例之一:GE精益实施之路
GE公司,历经几个体系转变期,从企业体系和精益思想的推行,到
用六西格玛管理体系建设精益文化,大力推进GE精益实施。
在实施精益时,GE着重了解和践行客户价值,做到把握核心任务,
以及提高效率、降低成本,这是GE精益思想的本质。
GE整合了一套全面的“六西格玛管理体系”,并在全球范围内实施。
精益实施经历了6个步骤:(1)确定客户要求;(2)确定核心任务;(3)创
建团队;(4)执行;(5)实施管理系统;(6)持续改进。
另外,GE还采取了一系列有效措施来强化精益文化,如GE Vitality Index,持续改进态度等,以不断激发员工的热情,并落实精益思想。
GE精益实施的成功标志着GE有能力将精益理念扎根并落实于企业管
理实践中,让每一个员工充分意识到精益的重要性和必要性。
二、六西格玛管理经典案例之二:印度JCB公司实施精益管理
印度JCB公司是印度最大的出口制造商之一,主要生产破碎机和压路机。
由于全球化竞争日益激烈,JCB公司意识到必须推进精益制造,以提
高生产效率,提升产品质量和减少破费。
因此,JCB公司用六西格玛管理体现实施精益管理。
- 1、下载文档前请自行甄别文档内容的完整性,平台不提供额外的编辑、内容补充、找答案等附加服务。
- 2、"仅部分预览"的文档,不可在线预览部分如存在完整性等问题,可反馈申请退款(可完整预览的文档不适用该条件!)。
- 3、如文档侵犯您的权益,请联系客服反馈,我们会尽快为您处理(人工客服工作时间:9:00-18:30)。
砂、组织疏松等缺陷可得到显著性的改善
,对发动机的质量、公司的产品声誉、售 后服务等都会带来巨大的无形收益。
407×0.268×(10900-4500)=698086.4元。
故每年可节约:
共节约有效金额
106万元RMB
14
361247.04+698086.4=1059333.44元。
D-8: 人力组织
6. 项目预计收益:
水套芯的磕碰伤率由破损率(12.5%)和缺陷率(87.5%)组成,破损直接导致水套芯的报废,有缺陷的水套芯必须在 造型前进行现场修补方可使用,但可能会引起铸造缺陷,降低铸件的铸造质量。
A、硬性收益:
通过铸造厂07、08年及09年1~5月份的气缸体造型总数223254只,每月平均25个工作日测算出,日均需生产水套芯 352个,气缸体水套芯的破损率由12.5%降低至2%,减少水套芯的生产数为:352×(12.5-2)%×25×12=11088(个/ 年)。每个水套芯的平均生产成本为32.58元。每年节约成本约:11088×32.58=361247.04元。根据07、08年统计, 由于水套芯铁夹砂造成的气缸体报废数为813个,平均每年有407个,气缸体铸件单重268Kg,气缸体商品价10900 元/吨,扣除可回收材料费4500元/吨,则:407×0.268×(10900-4500)=698086.4元。故每年可节约: 361247.04+698086.4=1059333.44元。
D
M A I C
项 目 已 完 成
17
M 阶段目录
M-1: Y的测量系统分析
M-2: Y的流程能力分析 M-3:鱼骨图
D
MA I Cຫໍສະໝຸດ M-4: C&E矩阵
M-5:失效模式分析(FMEA) M-6:快速改善措施 M-7:快速改善后的 2nd FMEA M-8: M 阶段小结
18
M-1: Y的测量系统分析(离散型)
改善达 成目标
降幅98.48%
13
D-7: 效果及成本预算
Hard Saving
通过铸造厂07、08年及09年1~5月份的气 缸体造型总数223254只,每月平均25个工作日测 算出,日均需生产水套芯 352 个,气缸体水套芯
D
M A I C
Soft Saving
气缸体水套芯的缺陷率由 87.5%降低至 1%,可明显提高水套芯在造型时的完好率 ,减少砂芯的现场修补及后续的造型、浇 注、清理等工序的工时损失和动力、刀具 、机器设备耗损等的浪费;对后面各工序 的连续性生产提供了基本保障;同时,铸 件由于水套芯的磕碰伤所引起的夹砂、粘
更换的发 动机编号 及客户追 偿清单 给分厂领导 的短信
5
D-1: 项目选定
D
M A I C
铸造厂领导及时组织相关部门研究分析问题,决定成立项目改 善小组,尽最大努力减少铸件的粘砂等缺陷。
制定 对策
6
D-1: 项目选定
D
M A I C
存在磕 碰伤的 水套芯
经多方研究及论证,认为水套部位残留余砂极有可能是有磕碰伤的水套芯 流入型腔浇注后造成的粘砂,在机加工工部没有清洗干净而导致的(铸造没有 铸件内腔清洗手段)。由于受到传统工艺及生产条件的限制,水套芯在生产及 转运过程中一直存在较为普遍的磕碰伤状况。因此项目组决定突破传统工艺和 思维限制,运用六西格玛工具和方法论有效降低水套芯的磕碰伤难题。
的破损率由12.5%降低至2%,减少水套芯的生
产数为:352×(12.5-2)%×25×12=11088 (个/年)。每个水套芯的生产成本为32.58元。 每年节约成本约:11088×32.58=361247.04元。 根据07、08年统计,由于水套芯铁夹砂造成的气 缸体报废数为813个,平均每年有407个,气缸体 铸件单重268Kg,气缸体商品价10900元/吨,扣 除可回收材料费4500元/吨,则:
B、软性收益:
气缸体水套芯的缺陷率由87.5%降低至1%,可明显提高水套芯在造型时的一次完好率,减少砂芯的现场修补及后续的 造型、浇注、清理等工序的工时损失和动力、刀具、机器设备耗损等的浪费;对后面各工序的连续性生产提供了基 本保障;同时,铸件由于水套芯的磕碰伤所引起的铁夹砂、粘砂、组织疏松等缺陷可得到显著性的改善,对发动机 的质量、公司的产品声誉、售后服务等都会带来巨大的无形收益。 7.团队成员: 区分 绿带 黑带 绿带 绿带 核心成员 核心成员 团队成员 部 门 丁树良 铸一车间 王伟春 技术科 何帅伟 技术科 王慧勇 质保科 江晓明 铸一车间 彭国江 铸一车间
10
D-4: 项目范围
宏观流程图
原砂 树脂 制芯 浸涂 烘干
D
M A I C
造型
浇注
与项目密切相关的流程
铲车 转运
水套芯
钻孔
整芯
浸涂
烘房
铲车 转运
造型
流 程 均 在 项 目 组 可 控 范 围 内
11
D-5: Y及缺陷定义
Y 定义 小Y 定义
D
M A I C
Y. 水套芯的磕碰伤率:射制完成的水套芯,在后续的钻孔、整芯、浸 涂、烘干、搬运等多道加工工序过程中由于发生磕碰而达不到工艺要求 完好的损伤率。影响水套芯磕碰伤率的主要指标有:水套芯紧实率、常 温强度、砂芯转运的平稳度、涂料层的抗擦落强度。 Y1.水套芯紧实率:水套芯砂的紧实程度,一般通过水套芯的重量来反映。 Y2.常温强度:也称存放强度,是影响后道工序的主要性能指标。 Y3.砂芯转运的平稳度:砂芯在用转运小车、铲车等搬运时的摇晃程度。 Y4.涂料层的抗擦落强度:经烘干固化后的涂料层具有的表面强度。 缺陷1.水套芯紧实率低:当水套芯重量低于10.6kg时,浸涂后强度明显 降低,容易发生水套芯断裂、破碎等。 缺陷2. 常温强度低:当砂芯的常温强度指标值低于2.0MPa时,水套芯 容易在存放、转运、下芯等后道工序中产生破损。 缺陷3.砂芯转运的平稳度差:砂芯转运后每车的水套芯报废数>1或者发 生涂料等擦落的水套芯数≥50%。 缺陷4.涂料层的抗擦落强度差:烘干后的涂料层当用手指抚摸就掉粉末 时,水套芯容易在转运下芯时发生涂料擦落砂子擦落等缺陷。
Champion: 刘念煌
D
M A I C
指导: 成
伟
丁树良 GB: 何帅伟 王慧勇
评审: 陈建华
部门: 铸一车间 核心人员:丁树良
部门:技术科 核心人员:王伟春
部门:技术科 核心人员:何帅伟
部门:质保科 核心人员:王慧勇
部门:铸一车间 核心人员:江晓明
部门:铸一车间 核心人员:彭国江
贡献率: 80% 职责: 组织工艺 方案的设 计、实施
2009/06/20
绿 带 丁树良 何帅伟 王慧勇
2009/06/20
刘念煌
2009/06/20
杨际斌
2009/06/20
制作好 的水套 芯
水套芯浸 涂、烘干、 转运等
12.5 气缸体 破损率 水套芯 % 87.5 磕碰伤率 缺陷率
4. 开始日期: 2009年6月
结束日期: 2009年12月 2
项目授权书
每个检验员与标准 评估一致性 检验员 验数 符数 百分比 95 % 臵信区间 30 30 100.00 (90.50, 100.00) 江小明 30 30 100.00 (90.50, 100.00) 彭国江 30 30 100.00 (90.50, 100.00) 王慧勇 检验员之间 评估一致性 验数 符数 百分比 95 % 臵信区间 30 30 100.00 (90.50, 100.00 所有检验员与标准 评估一致性 验数 符数 百分比 95 % 臵信区间 30 30 100.00 (90.50, 100.00)
D
M
A I C
测量内容:水套芯的破损与有缺陷(离散数据) ★[样本数量]:共30个 ★[测量环境]:铸造厂 ★[测 量 者]:王慧勇、江晓明、彭国江 ★[记 录 者]:何帅伟 ★[测量方法]:目测:对于30个水套芯,其中有3件破损其余有缺陷的样本进行测量系统分析。
检验员自身 评估一致性 检验员 验数 符数 百分比 30 30 100.00 江小明 30 30 100.00 彭国江 30 30 100.00 王慧勇 95 % 臵信区间 (90.50, 100.00) (90.50, 100.00) (90.50, 100.00)
降低气缸体水套芯磕碰伤率
部 门 : 杭发公司铸造厂 项目负责人 : 丁树良 何帅伟 王慧勇 项 目 周 期 : 2009年6月--12月
1
项目授权书
• 项目编号: • 项目名称: 降低气缸体水套芯 磕碰伤率 •部 门: 杭发公司铸造厂 •绿 带:丁树良 何帅伟 王慧勇
1.项目陈述: 水套芯是影响发动机铸件性能的关键砂芯,由于其具有薄壁、形状复杂、易变形等特点,因此在 生产、运输过程中的磕碰伤就一直成为制约产能和质量的主要瓶颈,对后续的造型、浇注、铸件的清 理、机加工等工序以及铸件质量和由此引起的发动机售后服务等都造成了很大的影响。采取有效手段 迅速改进水套芯磕碰伤,对于提升发动机铸件质量具有重要意义。 2. 项目范围 : 供应商 水套芯 制芯工 部 输 入 流 程 输 出 满足工艺 要求的水 套芯 用 户 造型、浇 注等后续 工序 3.现状及目标 : 项目指标 单 潜在最佳 现状 目标值 位 值 2 1 1 0.5 公司倡导者 项目倡导者 财务专员 签字 日期 李克宽
5.内部、外部顾客需求 :
在气缸体造型时,经常发现水套芯有裂纹,涂料被部分擦落掉,严重者部分地方已擦落到砂子甚至导致砂芯的报废等 磕碰伤,必须经现场修补才能使用。是延误生产、引起铸件发生铁夹砂、粘砂、组织疏松、表面光洁度降低等缺陷的一个 原因,影响后道工序直通率的主要原因。 清理气缸体时,经常发现气缸体水套底部有铁夹砂缺陷存在,需多次返工才能清理干净,清理不掉的将导致报废, 加重了清理工人的劳动强度以及人力、动力、机器设备等的浪费。对公司的铸件质量、整体的发动机质量、产品的售后服 务和声誉等产生重要影响。