塑胶产品结构设计准则--出模角篇
塑胶产品结构设计准则--加强筋篇
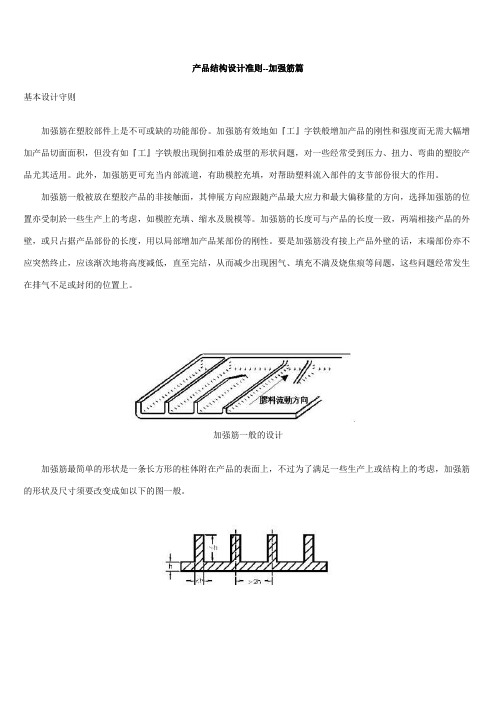
产品结构设计准则--加强筋篇基本设计守则加强筋在塑胶部件上是不可或缺的功能部份。
加强筋有效地如『工』字铁般增加产品的刚性和强度而无需大幅增加产品切面面积,但没有如『工』字铁般出现倒扣难於成型的形状问题,对一些经常受到压力、扭力、弯曲的塑胶产品尤其适用。
此外,加强筋更可充当内部流道,有助模腔充填,对帮助塑料流入部件的支节部份很大的作用。
加强筋一般被放在塑胶产品的非接触面,其伸展方向应跟随产品最大应力和最大偏移量的方向,选择加强筋的位置亦受制於一些生产上的考虑,如模腔充填、缩水及脱模等。
加强筋的长度可与产品的长度一致,两端相接产品的外壁,或只占据产品部份的长度,用以局部增加产品某部份的刚性。
要是加强筋没有接上产品外壁的话,末端部份亦不应突然终止,应该渐次地将高度减低,直至完结,从而减少出现困气、填充不满及烧焦痕等问题,这些问题经常发生在排气不足或封闭的位置上。
加强筋一般的设计加强筋最简单的形状是一条长方形的柱体附在产品的表面上,不过为了满足一些生产上或结构上的考虑,加强筋的形状及尺寸须要改变成如以下的图一般。
长方形的加强筋必须改变形状使生产更容易加强筋的两边必须加上出模角以减低脱模顶出时的摩擦力,底部相接产品的位置必须加上圆角以消除应力集过份中的现象,圆角的设计亦给与流道渐变的形状使模腔充填更为流畅。
此外,底部的宽度须较相连外壁的厚度为小,产品厚度与加强筋尺寸的关系图a说明这个要求。
图中加强筋尺寸的设计虽然已按合理的比例,但当从加强筋底部与外壁相连的位置作一圆圈R1时,图中可见此部份相对外壁的厚度增加大约50%,因此,此部份出现缩水纹的机会相当大。
如果将加强筋底部的宽度相对产品厚度减少一半(产品厚度与加强筋尺寸的关系图b),相对位置厚度的增幅即减至大约20%,缩水纹出现的机会亦大为减少。
由此引伸出使用两条或多条矮的加强筋比使用单一条高的加强筋较为优胜,但当使用多条加强筋时,加强筋之间的距离必须较相接外壁的厚度大。
塑胶产品模具的拔模角度确定
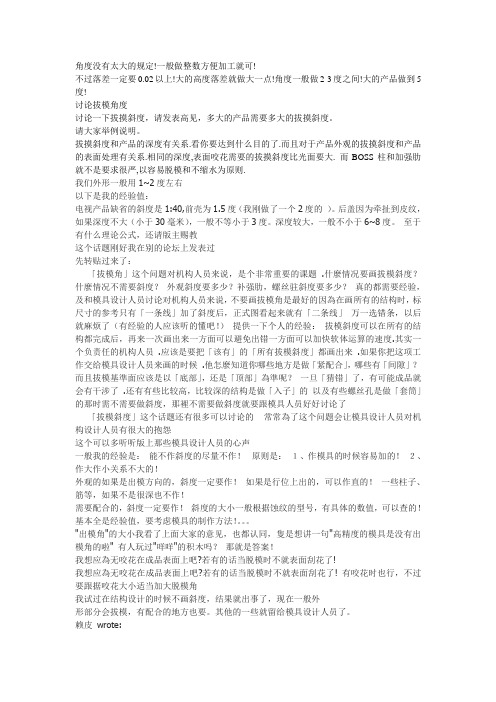
角度没有太大的规定!一般做整数方便加工就可!不过落差一定要0.02以上!大的高度落差就做大一点!角度一般做2-3度之间!大的产品做到5度!讨论拔模角度讨论一下拔摸斜度,请发表高见,多大的产品需要多大的拔摸斜度。
请大家举例说明。
拔摸斜度和产品的深度有关系.看你要达到什么目的了.而且对于产品外观的拔摸斜度和产品的表面处理有关系.相同的深度,表面咬花需要的拔摸斜度比光面要大. 而BOSS柱和加强肋就不是要求很严,以容易脱模和不缩水为原则.我们外形一般用1~2度左右以下是我的经验值:电视产品缺省的斜度是1:40,前壳为1.5度(我刚做了一个2度的)。
后盖因为牵扯到皮纹,如果深度不大(小于30毫米),一般不等小于3度。
深度较大,一般不小于6~8度。
至于有什么理论公式,还请版主赐教这个话题刚好我在别的论坛上发表过先转贴过来了:「拔模角」这个问题对机构人员来说,是个非常重要的课题 .什麼情况要画拔模斜度?什麼情况不需要斜度?外观斜度要多少?补强肋,螺丝驻斜度要多少?真的都需要经验,及和模具设计人员讨论对机构人员来说,不要画拔模角是最好的因為在画所有的结构时,标尺寸的参考只有「一条线」加了斜度后,正式图看起来就有「二条线」万一选错条,以后就麻烦了(有经验的人应该听的懂吧!)提供一下个人的经验:拔模斜度可以在所有的结构都完成后,再来一次画出来一方面可以避免出错一方面可以加快软体运算的速度.其实一个负责任的机构人员 .应该是要把「该有」的「所有拔模斜度」都画出来 .如果你把这项工作交给模具设计人员来画的时候 .他怎麼知道你哪些地方是做「紧配合」,哪些有「间隙」?而且拔模基準面应该是以「底部」,还是「顶部」為準呢?一旦「猜错」了,有可能成品就会有干涉了 .还有有些比较高,比较深的结构是做「入子」的以及有些螺丝孔是做「套筒」的那时需不需要做斜度,那裡不需要做斜度就要跟模具人员好好讨论了「拔模斜度」这个话题还有很多可以讨论的常常為了这个问题会让模具设计人员对机构设计人员有很大的抱怨这个可以多听听版上那些模具设计人员的心声一般我的经验是:能不作斜度的尽量不作!原则是:1、作模具的时候容易加的!2、作大作小关系不大的!外观的如果是出模方向的,斜度一定要作!如果是行位上出的,可以作直的!一些柱子、筋等,如果不是很深也不作!需要配合的,斜度一定要作!斜度的大小一般根据蚀纹的型号,有具体的数值,可以查的!基本全是经验值,要考虑模具的制作方法!。
塑胶产品结构设计基本规则

塑胶产品结构设计基本规则设计基本规则壁厚的大小取决于产品需要承受的外力、是否作为其它零件的支撑、承接柱位的数量、伸出部份的多少以及选用的塑胶材料而定。
一般的热塑性塑料壁厚设计应以4mm为限。
从经济角度来看,过厚的产品不但增加物料成本,延长生产周期”冷却时间〔,增加生产成本。
从产品设计角度来看,过厚的产品增加引致产生空穴”气孔〔的可能性,大大削弱产品的刚性及强度。
最理想的壁厚分布无疑是切面在任何一个地方都是均一的厚度,但为满足功能上的需求以致壁厚有所改变总是无可避免的。
在此情形,由厚胶料的地方过渡到薄胶料的地方应尽可能顺滑。
太突然的壁厚过渡转变会导致因冷却速度不同和产生乱流而造成尺寸不稳定和表面问题。
对一般热塑性塑料来说,当收缩率”Shrinkage Factor〔低于0.01mm/mm时,产品可容许厚度的改变达;但当收缩率高于0.01mm/mm时,产品壁厚的改变则不应超过。
对一般热固性塑料来说,太薄的产品厚度往往引致操作时产品过热,形成废件。
此外,纤维填充的热固性塑料于过薄的位置往往形成不够填充物的情况发生。
不过,一些容易流动的热固性塑料如环氧树脂”Epoxies〔等,如厚薄均匀,最低的厚度可达0.25mm。
此外,采用固化成型的生产方法时,流道、浇口和部件的设计应使塑料由厚胶料的地方流向薄胶料的地方。
这样使模腔内有适当的压力以减少在厚胶料的地方出现缩水及避免模腔不能完全充填的现象。
若塑料的流动方向是从薄胶料的地方流向厚胶料的地方,则应采用结构性发泡的生产方法来减低模腔压力。
平面准则在大部份热融过程操作,包括挤压和固化成型,均一的壁厚是非常的重要的。
厚胶的地方比旁边薄胶的地方冷却得比较慢,并且在相接的地方表面在浇口凝固后出现收缩痕。
更甚者引致产生缩水印、热内应力、挠曲部份歪曲、颜色不同或不同透明度。
若厚胶的地方渐变成薄胶的是无可避免的话,应尽量设计成渐次的改变,并且在不超过壁厚3:1的比例下。
下图可供叁考。
塑胶产品结构设计准则

从产品设计角度来看:过厚的产品會产生空穴气孔的可能性, 大大削弱产品的刚性及强度。
ห้องสมุดไป่ตู้
4
壁厚篇 (Wall)
最理想的壁厚分布是切面在任何一个地方都是平均的厚度,
但为了满足功能上的需求以致壁厚有所改变总是无可避免的。在
此情形,由厚胶料的地方过渡到薄胶料的地方应尽可能顺滑。太
突然的壁厚过渡转变会导致因冷却速度的不同和产生乱流而造成
支柱…………………………….No.16 支柱…………………………….No.17 支柱…………………………….No.18 支柱-ABS…...…………….……No.19 支柱-PBT………………………No.20 支柱-PC………………………..No.21 支柱-PS…..…………………...No.22 支柱-PSU……………………...No.23 洞孔……………………………No.24 洞孔-穿孔………...……………No.25 洞孔-盲孔………...……………No.26 洞孔-鑽孔………...……………No.27 洞孔-側孔…...…………………No.28 洞孔設計注意事項…………....No.29 洞孔設計注意事項…………....No.30 洞孔設計注意事項…………....No.31
转角位的设计准则亦适用于悬梁式扣位。理想数值是在0.5左右。
7
壁厚篇 (Wall)
熱塑性塑料的膠厚設計參考表
8
壁厚篇 (Wall)
熱固性塑料的膠厚設計參考表
9
壁厚篇 (Wall)
實例
大部份厚胶的设计可从使用加强筋及改变横切面形状取缔之。除了可减省物 料以致减省生产成本外,取缔后的设计更可保留和原来设计相同的刚性、强度及 功用。
塑胶产品结构设计准则
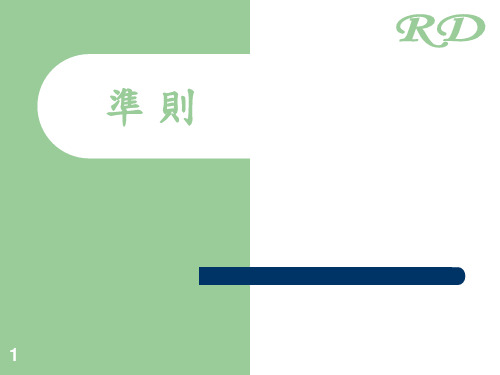
5
壁厚篇 (Wall)
平面准则
在挤压和固化成型过程中,均一的壁厚是非常的重要的。厚胶的地 方比旁边薄胶的地方冷却得比较慢,并且在相接的地方表面 在浇口凝 固后出现收缩痕。更甚者引致产生缩水印、热内应力、挠曲部份歪曲、 颜色不同或不同透明度。若厚胶的地方渐变成薄胶的是无可避免的话, 应尽量设计成渐次的改变,并且在不超过壁厚3:1的比例下。
11
壁厚篇 (Wall)
不同材質的設計要點………………PC;LCP PC 壁厚 壁厚大部份是由负载要求﹑内应力﹑几何形状﹑外型﹑塑料 流量﹑可注塑性和经济性来决定。PC建议最大壁厚:9.5mm 。 若要效果好,则壁厚应不过3.1mm 。在一些需要将壁厚增加使 强度加强时,肋骨和一些补强结构可提供相同结果。PC大部份 应用的最小壁厚在0.75 mm左右,再薄一些的地方是要取决于部 件的几何和大小。短的塑料流程是可以达到0.3 mm 壁厚。 壁厚由厚的过渡到薄的地方是要尽量使其畅顺。所有情况塑 料是从最厚的地方进入模腔内,以避免缩水和内应力。 均一的壁厚是要很重要的。可减少成型后的变型问题。 LCP 壁厚 由于液晶共聚物在高剪切情况下有高流动性,所以壁厚会比 其它的塑料薄。最薄可达0.4mm,一般厚度在1.5mm左右。
(b) 圆角
15
支柱 ( Boss )
支柱突出胶料壁厚是用以装配产品、隔开对象及支撑承托其 它零件之用。空心的支柱可以用来嵌入件、收紧螺丝等。这些应 用均要有足够强度 支持压力 而不致于破裂。 支柱尽量不要单独使用,应尽量连接至外壁或与加强筋一同 使用, 目的: a.是加强支柱的强度 ; b.是使胶料流动更顺畅。 此外,因过高的支柱会导致產品成型时困气,所以支柱高度一般 是不会超过支柱外徑的2.5倍。加强支柱强度的方法,尤其是远离 外壁的支柱,除了可使用加强筋外,三角加强块Gusset plate的 使用亦十分常见。
出模角篇
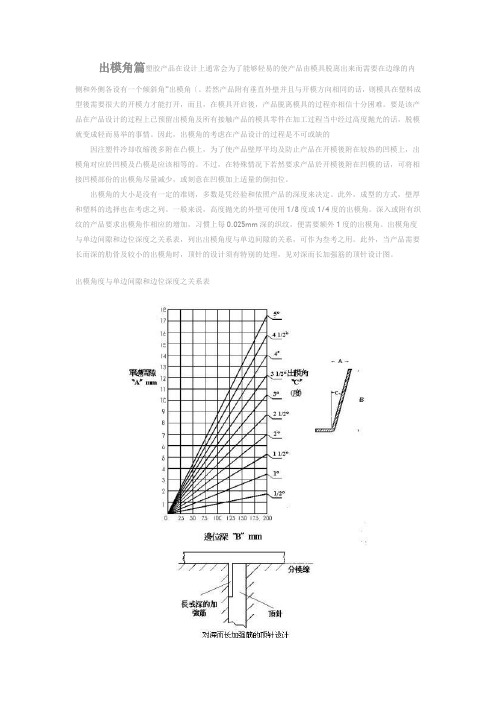
出模角篇塑胶产品在设计上通常会为了能够轻易的使产品由模具脱离出来而需要在边缘的内侧和外侧各设有一个倾斜角”出模角〔。
若然产品附有垂直外壁并且与开模方向相同的话,则模具在塑料成型後需要很大的开模力才能打开,而且,在模具开启後,产品脱离模具的过程亦相信十分困难。
要是该产品在产品设计的过程上已预留出模角及所有接触产品的模具零件在加工过程当中经过高度抛光的话,脱模就变成轻而易举的事情。
因此,出模角的考虑在产品设计的过程是不可或缺的因注塑件冷却收缩後多附在凸模上,为了使产品壁厚平均及防止产品在开模後附在较热的凹模上,出模角对应於凹模及凸模是应该相等的。
不过,在特殊情况下若然要求产品於开模後附在凹模的话,可将相接凹模部份的出模角尽量减少,或刻意在凹模加上适量的倒扣位。
出模角的大小是没有一定的准则,多数是凭经验和依照产品的深度来决定。
此外,成型的方式,壁厚和塑料的选择也在考虑之列。
一般来说,高度抛光的外壁可使用1/8度或1/4度的出模角。
深入或附有织纹的产品要求出模角作相应的增加,习惯上每0.025mm深的织纹,便需要额外1度的出模角。
出模角度与单边间隙和边位深度之关系表,列出出模角度与单边间隙的关系,可作为叁考之用。
此外,当产品需要长而深的肋骨及较小的出模角时,顶针的设计须有特别的处理,见对深而长加强筋的顶针设计图。
出模角度与单边间隙和边位深度之关系表不同材料的设计要点ABS一般应用边0.5°至1°就足够。
有时因为抛光纹路与出模方向相同,出模角可接近至零。
有纹路的侧面需每深0.025mm(0.001 in)增加1°出模角。
正确的出模角可向蚀纹供应商取得。
LCP因为液晶共聚物有高的模数和低的延展性,倒扣的设计应要避免。
在所有的肋骨、壁边、支柱等凸出膠位以上的地方均要有最小0.2-0.5°的出模角。
若壁边比较深或没有磨光表面和有蚀纹等则有需要加额外的0.5-1.5°以上。
产品结构设计准则--tolerance公差篇
产品结构设计准则--公差( Tolerance )
基本设计守则
大部份的塑胶产品可以达到高精密配合的尺寸公差,而一些收缩率高及一些软性材料则比较难于控制。
因此在产品设计过程时是要考虑到产品的使用环境,塑胶材料,产品形状等来设定公差的严紧度。
除着顾客的要求愈来愈高,以往的可以配合起来的观念慢慢的要修正过来。
配合、精密和美观是要同时的能在产品上发挥出来。
公差的精密度高,产品质素相对提高,但随之而来的是增加了成本和因达到要求而花更多的时间。
故此公差的设定可以跟随不同塑料来作一标准,以下是几种由塑料供应商提供的塑料公差设计要点。
而设计的容许公差范围是可在美国SPI规格内找得到。
不同材料的设计要点
LCP
液晶共聚物成品容许公差随着设计的复杂程度和壁厚而定。
薄壁的部份经常可以在液晶共聚物的产品上可找得到。
而且液晶共聚物容许公差可是极小容许公差的50%。
LCP液晶高分子设计容许公差的指南
PET
宝特龙(PET) 的设计公差准则
POM
精密公差的标准叁考表。
产品结构设计——塑胶件结构设计基本原则
——塑胶件结构设计基本原则塑胶件结构设计基本原则1.避免翘曲准则2.细长筋受拉准则3.避免内切准则4.避免尖锐棱角准则1.避免翘曲准则翘曲现象经常出现于塑料构件中,所以塑料件的结构设计应特别注意避免翘曲。
翘曲的主要原因是由于模塑成型过程中,构件冷却不均匀,产生内应力,引起翘曲变形。
造成冷却不均匀的原因主要有三种:(1)材料分布不均匀;(2)散热边界条件不均匀;(3)结构不对称。
1.避免翘曲准则壁厚不均匀的构件易出现却不均匀现象,从而导致构件翘曲变形。
在因构件本身功能要求的限制无法做到的情况下,应在两不同壁厚之间留有缓慢的过渡段。
不合理结构合理结构1.避免翘曲准则壁厚过大的塑件内部易产生空洞等缺陷,所以常设置加强筋提高构件的刚度。
过薄或过厚的加强筋也会导致构件的翘曲变形。
加强筋的壁厚要与底板壁厚相当,不要超过底板的壁厚。
不合理结构合理结构s 0.6s3s1.避免翘曲准则壁厚均匀的塑件也会产生翘曲变形,下图左侧的大平板从几何形状上来说完全均匀,但冷却不均匀;外部冷却快,内部冷却慢;板越大,不均匀越严重。
解决这个问题的方法是将平板改成拱板,下图右图所示,这样提高了板的抗弯刚度,从而有利于减少或消除构件的翘曲变形。
不合理结构合理结构1.避免翘曲准则另一种因冷却不均匀而产生翘曲变形的结构是带拐角的塑件。
拐角内外散热速度不一样,内慢外快。
解决的措施是加大内拐角的散热面积,改直角为倒角或设置一槽。
不合理结构合理结构2.细长筋受拉准则加强筋是塑胶件中的常见结构,一般比较细长。
塑料的弹性模量很低,所以易出现失稳问题,特别是细长结构。
应使细长筋尽量处于受拉状态。
不合理结构合理结构3.避免内切准则有内切结构无法直接脱模,必须用模芯或侧向抽芯机构,增大了模具制造的复杂性,从而增加了模具成本。
塑料件的结构设计应考虑到脱模的可能与方便,应避免有内切的结构。
下图左侧结构内外都有内切问题,即不可能用单一模具制作,从而增大模具的制造成本,其改进结构如右图所示。
塑胶产品结构设计准则
在塑胶件上开孔使其和其它部件相接合或增加产品功能上的组合是常用的手法,洞 孔的大小及位置应尽量不会对产品的强度构成影响或增加生产的复杂性, 常见孔的 类型如下:
孔离边位或内壁边之要点 :
confidential
16
四、塑胶产品结构设计准则-洞孔 (Hole)
盲孔设计要点: 盲孔是靠模具上的镶针形成,而镶针的设计只能单边支撑在模具上,因此很容易 被溶融的塑料使其弯曲变形,造成盲孔出现椭圆的形状,所以镶针的长度不能过长。 盲孔深度最大是直径的3倍,考虑模具镶针强度要求直径最小0.8mm。 外观件上的各种凹槽,如雕刻文字等,要求棱线分明,导致过渡太急,易产生气
confidential
12
三、塑胶产品结构设计准则-支柱 ( Boss )
对于外观件,当有螺丝柱子,需要进行缩水验证,依照上页图示意,塑胶壁厚 1.5 ,螺丝柱子外径3.4,验证结果 NG:(1.8-1.5)/1.5*100%=20% >8%。 外观面有可能会有缩水痕迹。
改善方案如下图:
当缩水验证NG时,可在增加火山口及加深螺丝孔深度来改善。 外观部品综合考虑缩水与螺丝柱子强度,塑胶壁厚要求大于1.3。 适当的辅以三角或十字加强筋方式,可大幅度提高强度和改善料流填充。
confidential
4
一、塑胶产品结构设计准则-壁厚
B. 转角位的设计准则亦适用於悬梁式扣位。因这种扣紧方式是需要将悬梁臂弯 曲嵌入,转角位置的设计图说明如果转角弧位R太小时会引致其应力集中系数 (Stress Concentration Factor)过大,因此,产品弯曲时容易折断,弧位R太大 的话则容易出现收缩纹和空洞。因此,圆弧位和壁厚是有一定的比例。一般 介乎0.2至0.6T之间,理想数值是在0.5T左右。
塑胶产品结构设计准则
confidential
13
三、塑胶产品结构设计准则-支柱 ( Boss )
对于外观件,当有螺丝柱子,需要进行缩水验证,依照上页图示意,塑胶壁厚 1.5 ,螺丝柱子外径3.4,验证结果 NG:(1.8-1.5)/1.5*100%=20% >8%。 外观面有可能会有缩水痕迹。
改善方案如下图:
当缩水验证NG时,可在增加火山口及加深螺丝孔深度来改善。 外观部品综合考虑缩水与螺丝柱子强度,塑胶壁厚要求大于1.3。 适当的辅以三角或十字加强筋方式,可大幅度提高强度和改善料流填充。
confidential
18
四、塑胶产品结构设计准则-洞孔 (Hole)
对于塑胶部品,结合线处强度较弱,受力容易破裂。当通孔处于产品边部,同 时有配合力量要求时,要求孔壁距离外侧壁1.5mm(如因结构原因无法保证 1.5mm, 采用模具设置冷料槽成型后再剪除,但最小要1.0mm),对于卡勾槽尽 量采用盲孔。
10
三、塑胶产品结构设计准则-支柱 ( Boss )
支柱 ( Boss )基本设计守则:
A. 支柱尽量不要单独使用,应尽量连接至外壁或与加强筋一同使用,目的是加 强支柱的强度及使胶料流动更顺畅。
B. 实心支柱的直径大小取壁厚的0.5~0.7倍,当有缩水管理要求时,需使用使用 缩水公式验证。
C. 过高的支柱会导致塑胶部件成型时困气,所以支柱高度一般是不会超过支柱 直径的3倍。过高的支柱要考虑其强度及逃气问题。
塑胶产品结构设计准则
Paul ren
confidential
1
塑胶产品结构设计准则
一. 壁厚 (Thickness) 二. 加强筋(Rib) 三. 支柱 (Boss) 四. 洞孔 (Hole) 五. 扣位(Snap Joint) 六. 出模角(Draft Angle) 七. 螺紋(Screw) 八. 文字(Text) 九. 咬花(Texture)
- 1、下载文档前请自行甄别文档内容的完整性,平台不提供额外的编辑、内容补充、找答案等附加服务。
- 2、"仅部分预览"的文档,不可在线预览部分如存在完整性等问题,可反馈申请退款(可完整预览的文档不适用该条件!)。
- 3、如文档侵犯您的权益,请联系客服反馈,我们会尽快为您处理(人工客服工作时间:9:00-18:30)。
塑胶产品结构设计准则--出模角篇
基本设计守则
塑胶产品在设计上通常会为了能够轻易的使产品由模具脱离出来而需要在边缘的内侧和外侧各设有一个倾斜角”出模角〔。
若然产品附有垂直外壁并且与开模方向相同的话,则模具在塑料成型後需要很大的开模力才能打开,而且,在模具开启後,产品脱离模具的过程亦相信十分困难。
要是该产品在产品设计的过程上已预留出模角及所有接触产品的模具零件在加工过程当中经过高度抛光的话,脱模就变成轻而易举的事情。
因此,出模角的考虑在产品设计的过程是不可或缺的
因注塑件冷却收缩後多附在凸模上,为了使产品壁厚平均及防止产品在开模後附在较热的凹模上,出模角对应於凹模及凸模是应该相等的。
不过,在特殊情况下若然要求产品於开模後附在凹模的话,可将相接凹模部份的出模角尽量减少,或刻意在凹模加上适量的倒扣位。
出模角的大小是没有一定的准则,多数是凭经验和依照产品的深度来决定。
此外,成型的方式,壁厚和塑料的选择也在考虑之列。
一般来说,高度抛光的外壁可使用1/8度或1/4度的出模角。
深入或附有织纹的产品要求出模角作相应的增加,习惯上每0.025mm深的织纹,便需要额外1度的出模角。
出模角度与单边间隙和边位深度之关系表,列出出模角度与单边间隙的关
系,可作为叁考之用。
此外,当产品需要长而深的肋骨及较小的出模角时,顶针的设计须有特别的处理,见对深而长加强筋的顶针设计图。
出模角度与单边间隙和边位深度之关系表
不同材料的设计要点
ABS
一般应用边0.5°至1°就足够。
有时因为抛光纹路与出模方向相同,出模角可接近至零。
有纹路的侧面需每深0.025mm(0.001 in)增加1°出模角。
正确的出模角可向蚀纹供应商取得。
LCP
因为液晶共聚物有高的模数和低的延展性,倒扣的设计应要避免。
在所有的肋骨、壁边、支柱等凸出膠位以上的地方均要有最小0.2-0.5°的出模角。
若壁边比较深或没有磨光表面和有蚀纹等则有需要加额外的
0.5-1.5°以上。
PBT
若部件表面光洁度好,需要1/2°最小的脱模角。
经蚀纹处理过的表面,每增加0.03mm(0.001 in)深度就需要加大1°脱模角。
PC
脱模角是在部件的任何一边或凸起的地方要有的,包括上模和下模的地方。
一般光华的表面1.5°至2°已很足够,然而有蚀纹的表面是要求额外的脱模角,以每深0.25mm(0.001 in)增加1°脱模角。
PET
塑胶成品的肋骨,支柱边壁、流道壁等,如其脱模角能够达到0.5°
就已经足够。
PS
0.5°的脱模角是极细的,1°的脱模角是标准方法,太小的脱模角会使部件难于脱离模腔。
无论如何,任何的脱模角总比无角度为佳。
若部件有蚀纹的话,如皮革纹的深度,每深0.025mm就多加1°脱模角。