表面粗糙度的测量(精品 值得参考)
第五节零件的表面粗糙度(新标准)stu(精品-值得参考)

表面粗糙度的选用
Ra(μm) 50 25 12.5 6.3 3.2 1.6 0.8应用举例
明显可见刀痕 可见刀痕
粗车、粗铣、粗刨、钻、粗 粗糙度值最大的加工面,一般很少应
纹锉刀和粗砂轮加工
用
微见刀痕 可见加工痕迹 微见加工痕迹 看不见加工痕迹
粗车、刨、立铣、平铣、钻 不接触表面,不重要的接触面,如螺
基本符号加一小圆,表示表面是用不去除材料的方法获得。 例如:铸、锻、冲压变形、热轧、冷轧、粉末冶金等。 或是用于保持原供应状况的表面(包括保持上道工序的状况)
在上述三个符号的上边均可加一横线,用于标注有关参数和 说明
在上述三个符号的上边均可加一小圆,表示所有表面具有相同 的表面粗糙度要求要求
2、表面结构要求代号
8N9
Ra 6.3
10N9
Ra 6.3
Ra 6.3
( ) Ra 12.5
Ra 3.2
X Ra 12.5
Ra 6.3
Ra 12.5
Ra 12.5
X
Ra 3.2 Ra 3.2
X
Ra 12.5
X Ra 3.2
Ra 3.2
Ra 3.2
X Ra 12.5
Ra 6.3
改错
Ra 12.5
Ra 3.2
Ra 12.5 Ra 12.5
表面结构要求标注的主要规定
• 用细实线相连的表面只标注一次。
Ra 3.2
表面结构要求标注的主要规定
• 同一表面上有不同的表面结构要求要求 时,必须用细实线画出其分界线,并标 注出相应的表面结构要求代号和尺寸。
Ra 0.8
Ra 3.2
选择出标注正确的表面结构要求
Ra 6.3
实验二 表面粗糙度测量 表面粗糙度的测量方法常用

实验二 表面粗糙度测量表面粗糙度的测量方法常用的有光切法,光波干涉法及针触法等.工厂的车间中常用的还有粗糙度样板直接和被测工件对照的比较法,以及利用塑性和可铸性材料将被测工件表面的加工痕迹复印下来,然后再测量复印的印模,从而确定被测工件的表面粗糙度级别的印模法。
实验目的1. 建立对表面粗糙度评定的感性知识;2. 学习用双管显微镜(光切法)和干涉显微镜(干涉法)及电动式轮廓仪(针描法)测量表面粗糙度的方法。
实验2-1 用双管显微镜测量表面粗糙度Rz 值一、测量原理及计量器具说明参看图2-1,微观不平度十点高度Rz 是在取样长度l 内,从平行于轮廓中线m 的任意一条线算起,到被测轮廓的五个最高点(峰)和五个最低点(谷)之间的平均距离,即 135********Z (h +h +h +h +h )(h +h +h +h +h )R =5图2-1图2-2双管显微镜能检测1-80μm的表面粗糙度的Rz值。
双管显微镜的外形如图2-2所示。
它有1-光源;2-立柱;3-锁紧螺钉;4-微调手轮;5-横臂;6-升降螺母; 7-底座;8-纵向千分尺9-工作台固紧螺钉;10-横向千分尺;11-工作台;12-物镜组;13-手柄;14-壳体;15-测微鼓轮;16-目镜;17-照相机安装孔等部分组成。
双管显微镜是利用光切原理来测量表面粗糙度的,如图3所示,被测表面为P1、P2阶梯表面,当一平行光束从45°方向投射到阶梯表面上时,就被折成S1和S2两段。
从垂直于光束的方向上就可在显微镜内看到S1和S2两段光带的放大象S1ˊ和S2ˊ。
同样,S1和S2之间的距离h也被放大为S1ˊ和S2ˊ之间的距离h1ˊ。
通过测量和计算,可求得被测表面的不平度高度h。
图4为双管显微镜的光学系统图。
由光源1发出的光,经聚光镜2、狭缝3、物镜4,以45°方向投射到被测工件表面上。
调整仪器使反射光束进入与投射光管垂直的观察光管内,经物镜5成象在目镜分划板上,通过目镜可观察到不平的光带(图5b)。
§3.2_表面粗糙度(精品 值得参考)
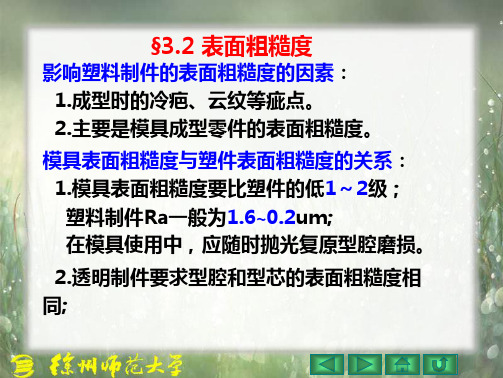
影响塑料制件的表面粗糙度的因素: 1.成型时的冷疤、云纹等疵点。 2.主要是模具成型零件的表面粗糙度。
模具表面粗糙度与塑件表面粗糙度的关系: 1.模具表面粗糙度要比塑件的低1~2级; 塑料制件Ra一般为1.6~0.2um; 在模具使用中,应随时抛光复原型腔磨损。
2.透明制件要求型腔和型芯的表面粗糙度相 同;
§3.2 表面粗糙度
3.而不透明制件则根据使用情况而定; 非配合表面和隐蔽面可取较大的表面粗糙
度值; 一般型腔的表面粗糙度要低于型芯的。
4.塑件的表面粗糙度与塑料的品有关
表面粗糙度的测量
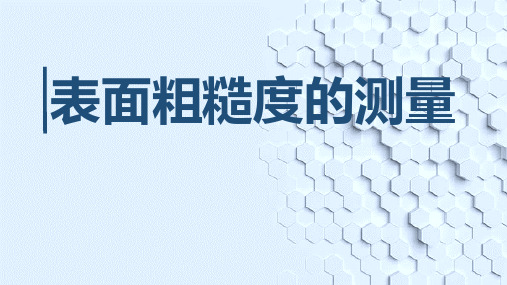
测量方法:
➢ 比较法
将表面粗糙度比较样块(简称样块)根据视觉和触觉与被测表面比较,判断被测表面粗糙度相当于 那一数值,或测量其反射光强变化来评定表面粗糙度(见激光测长技术)。样块是一套具有平面或圆柱表 面的金属 块,表面经磨、车、镗、铣、刨等切削加工,电铸或其他铸造工艺等加工而具有不同的表面 粗表糙 面度粗。糙有度时的可方直法接虽从然工简件便中,选但出会样受1品到)经主一过观般测因折量素弯并影:(评响R=定,0,合常θ格不=9后能0°作得) 为出样正块确。的利表用面样粗块糙根度据数视值觉。和触觉评定 ➢ 印摸法
测量方法:
➢ 干涉法
利用光波干涉原理 (见平晶、激光测长技术)将被测表面的形状误差以干涉条纹图形显示出来,并 利用放大倍数高(可达500倍)的显微镜将这些干涉条纹的微观部分放大后进行测量,以得出被测表面 粗糙度。应用此法的表面粗糙度测量工具称为干涉显微镜。这种方法适用于测量Rz和Ry为 0.025~0.8 微米的表面粗糙度。
1)一般折弯:(R=0, θ=90°)
➢ 光切法
光线通过狭缝后形成的光带投射到被测表面上,以它与被测表面的交线所形成的轮廓曲线来测量 表面粗糙度。由光源射出的光经聚光镜、狭缝、物镜1后,以45°的倾斜角将狭缝投影到被测表面,形 成被测表面的截面轮廓图形,然后通过物镜 2将此图形放大后投射到分划板上。利用测微目镜和读数 鼓轮(图中未示)先读出h值,计算后得到H 值。应用此法的表面粗糙度测量工具称为光切显微镜。它 适用于测量RZ和Ry为0.8~100微米的表面粗糙度,需要人工取点,测量效率低。
表面粗糙度的粗糙度的含义
02 表面粗糙度的测量方法
01 表面粗糙度的含义
含义:
02 表面粗糙度的测量方法
表面粗糙度的测量方法
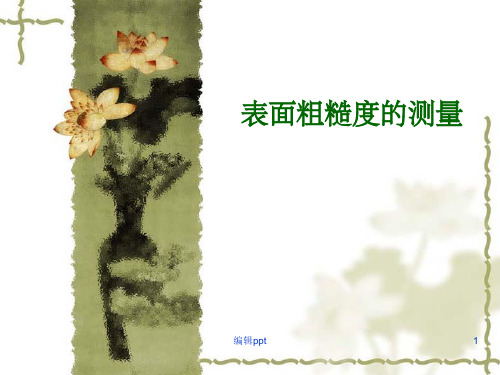
编辑ppt
1
第一节表面粗糙度的评定参数
主要内容:
1、主要术语及定义
取样长度L
评定长度L
n
轮廓中线m
2、6个评定参数
3个基本、3个附加
3、一般规定
重点: 3个基本评定参数
编辑ppt
2
一.主要术语及定义
1.实际轮廓:平面与实际表面相交所得的轮廓线。
按照相截方向的不同,它又可分为横向实际轮廓和纵向实 际轮廓。在评定或测量表面粗糙度时,除非特别指明,通 常均指横向实际轮廓,即与加工纹理方向垂直的截面上的 轮廓。
编辑ppt
17
取得表面测量信号以后,亦可用人工进行计算处理给出结果。
编辑ppt
18
❖ 15.2 表面粗糙度测量的基本原则
❖
(1)测量方向
❖
按现行标准所定义的各种粗糙度评定参数,是基于轮廓法确定数值,
是在被测表面的法向截面上的实际轮廓上进行测量的结果。由于垂直于
被测表面的法向截面存在各种不同的测量方向.试验表明,大多数的切
削加工表面,在横向轮廓上测得的粗糙度数值比较大,只是有的该铣加
工和个别端铣加工表面,在纵向轮廓上会有较大的数值。 如果在被测表
面上难以确定加工纹理方向,以及某些加工纹理紊乱或不存在固定方向
的表面,应分别在多个方向上测量,以获取最大参故值为结果.或取其
峰谷高度的最大值,计算一个区域的测量结果。
❖
编辑ppt
❖ 15.1 测量方法综述
❖ 对加工表面质量的评定,除了用视觉和触觉进行定性地比较检验的方 法以外,并逐步实现了用数值确定表面粗糙度参数值的定量测量。从本 世纪30年代陆续提出了测量粗糙度的方法原理和仪器以来,已发展了一 系列利用光学、机械、电气原理的表面粗糙度专用测量仪器,其基本结 构模式如图9—7所示。
第五章_表面粗糙度(精品 值得参考)

50, 25,12.5;6.3,3.2,1.6;0.8,0.4, 0.2; 0.1….μm等。
粗加工.一般 用于不重要 的接触面和 非配合面
半精加工.用于较 重要接触面和一 般配合面
精加工.用于要 求较高的接触 面和配合面
光加工.用于高速 运动的配合面和精 密量具的工作面
第二节 表面粗糙度的选择
第五章
表面粗糙度(主要参考书:课本、孙玉芹编)
参考标准:GB/T3505-2000 GB/T1031-1995 等
• 基本内容:掌握表面粗糙度的基本概念, 表面粗糙度的评定、选用、标注及测量。 • 重点内容:表面粗糙度的评定、选用及 标注。 • 难点内容:表面粗糙度的评定、选用。 • 操作技能:表面粗糙度的测量。
在取样长度范围内,被测轮廓线上各 点至基准线的距离的算术平均值。
Ra
yi
yn
l
x
1 l Ra y dx l 0
近似为
1 n Ra y i n i 1
2)轮廓最大高度RZ
在取样长度范围内,最大轮廓峰高Rp与最大轮廓谷深Rv之 和称之为轮廓最大高度,用符号Rz表示,即Rz = Rp + Rv
三、表面粗糙度参数值的选择
一般来说,表面粗糙度参数值愈小,表面就愈 光滑,其性能愈好,使用寿命也愈长。但绝不能认 为表面粗糙度值越小越好。因为其值越小,加工成 本就会越高。
选用表面粗糙度参数值的总原则:首先满 足功能要求,其次是考虑经济性及工艺性。 在满足功能要求的前提下,参数值应尽可能 大些。
三、表面粗糙度参数值的选择(续)
第一节 表面粗糙度的基本概念
一、表面粗糙度概念
1、定义 在零件被加工表面上,具有微小间距和峰谷所 组成的微观几何形状的特征,称为表面粗糙度。
表面粗糙度怎么测量 测量表面粗糙度的方法 详解
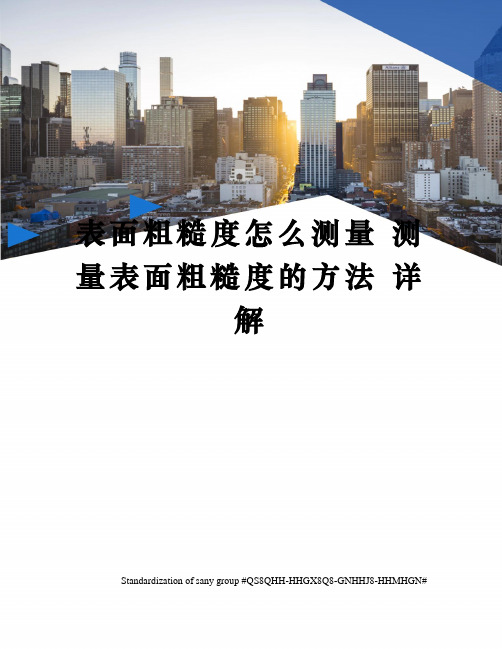
表面粗糙度怎么测量测量表面粗糙度的方法详解Standardization of sany group #QS8QHH-HHGX8Q8-GNHHJ8-HHMHGN#表面粗糙度怎么测量_ 测量表面粗糙度的方法内容来源网络,由深圳机械展收集整理!表面粗糙度的检测,我们常用的有以下几中方法1.显微镜比较法,;将被测表面与表面粗糙度比较样块靠近在一起,用比较显微镜观察两者被放大的表面,以样块工作面上的粗糙度为标准,观察比较被测表面是否达到相应样块的表面粗糙度;从而判定被测表面粗糙度是否符合规定。
此方法不能测出粗糙度参数值2.光切显微镜测量法,Rz:~100;光切显微镜(双管显微镜)是利用光切原理测量表面粗糙度的方法。
从目镜观察表面粗糙度轮廓图像,用测微装置测量Rz值和Ry值。
也可通过测量描绘出轮廓图像,再计算Ra值,因其方法较繁而不常用。
必要时可将粗糙度轮廓图像拍照下来评定。
光切显微镜适用于计量室3.样块比较法,直接目测:;用放大镜:~;以表面粗糙度比较样块工作面上的粗糙度为标准,用视觉法或触觉法与被测表面进行比较,以判定被测表面是否符合规定用样块进行比较检验时,样块和被测表面的材质、加工方法应尽可能一致;样块比较法简单易行,适合在生产现场使用4.电动轮廓仪比较法,Ra:~;Rz:~25;电动轮廓仪系触针式仪器。
测量时仪器触针尖端在被测表面上垂直于加工纹理方向的截面上,做水平移动测量,从指示仪表直接得出一个测量行程Ra值。
这是Ra值测量常用的方法。
或者用仪器的记录装置,描绘粗糙度轮廓曲线的放大图,再计算Ra或Rz 值。
此类仪器适用在计量室。
但便携式电动轮廓仪可在生产现场使用5干涉显微镜测量法,Rz:.032~;涉显微镜是利用光波干涉原理,以光波波长为基准来测量表面粗糙度的。
被测表面有一定的粗糙度就呈现出凸凹不平的峰谷状干涉条纹,通过目镜观察、利用测微装置测量这些干涉条纹的数目和峰谷的弯曲程度,即可计算出表面粗糙度的Ra值。
表面粗糙度的测量(精品 值得参考)
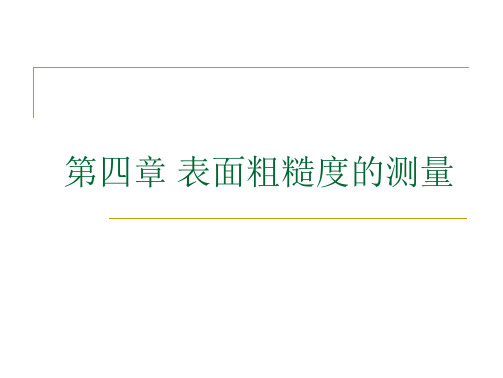
3、测量方法 测量前,选择相应的物镜并已知定度值C。然后调节 显微镜使视场呈现清晰的狭缝及表面像,且至狭缝像的一 个边缘最清晰为止。 (1)测量Rz值: 其测量方法应符合定义。Rz值可按下式计算:
(2)测量Ry值:
(3)测量单峰平均间距S值
(4)测量平均间距Sm
(5)用光切法测量Ra值 因测量与计算都很麻烦,故很少应用
第四章 表面粗糙度的测量
§4.1 概述
一、表面形貌误差的概念与形成
1. 表面形貌误差分类: 实际加工表面通常包括如下三种表面形貌 误差:
表面粗糙度:波距小于1mm,大体呈周期性变化, 属于微观几何形状误差; 表面波度:波距在1-10mm,呈周期性变化,属 于中间几何形状误差; 形状误差: 波距大于10mm,无明显周期性变化, 属于宏观几何形状误差。 纹理方向、伤痕
由于物镜分辨率及景深的限制,光切法测量范围 一般为: Rz=(80~0.8) m(旧国际▽3~▽9)。
双管显微镜
1-底座;2-立柱;3-横梁;4-手轮;5-固定螺丝;6-微调手轮;7-壳体 8-锁紧手柄;9-工作台;10-物镜组;11-测微目镜;12-燕尾导轨;13-千分尺
双管显微镜视场图
二、光切法测量表面粗糙度
1、光切法原理 用一狭窄的扁平光以一定倾斜角照射到被 测面,发生反射,将表面微观不平度用显微镜 放大成像进行观测。
2、测量仪器原理及定度 (1)原理
(a)测量装置结构简图;(b)目镜视场的影像;(c)测量原理简图 1—光源; 2—聚光镜;3—狭缝; 4、5—物镜; 6—分划板;7—目镜; 8—被测表面
(1)最小二乘中线: 使轮廓上各点的轮廓偏转距y(在测量方向 上轮廓上的点至基准线的距离)的平方和为最 小的基准线。
- 1、下载文档前请自行甄别文档内容的完整性,平台不提供额外的编辑、内容补充、找答案等附加服务。
- 2、"仅部分预览"的文档,不可在线预览部分如存在完整性等问题,可反馈申请退款(可完整预览的文档不适用该条件!)。
- 3、如文档侵犯您的权益,请联系客服反馈,我们会尽快为您处理(人工客服工作时间:9:00-18:30)。
§4.3 表面粗糙度的测量方法
一、表面粗糙度的测量方法分类
定性评定:待测表面和已知表面光洁度级别的 标准样板相比较,通过目估或借助显微镜以判 别其级别。
定量评定:通过一定的测量方法和相应的仪器, 测出待测表面的不平度数值。
1、与表面粗糙度标准样板比较 表面粗糙度样板:按各种加工方法做成的 不同几何形状的一套标准表面样板,用来与被 测的表面相比较。
三、表面形貌测量的特点与范围
特点:通常为量程小、测量分辨率高(nm)、无目标 靶。 表面粗糙度测量的范围 现在表面分析技术已远走出机械零件,如: 1. 微电子工业:硅片、磁盘表面、光盘、光学元件 2. 材料科学:表面形貌分析、材料微裂纹 3. 生物科学:细胞生物、芯片、遗传学 4. 科学研究:纳米技术、物理、化学、生物等基础科 学等
(2)定度:
在光切显微镜上,把确定测微目镜的鼓轮上每小格所对 应的被测峰谷高度值的过程叫作“定度”。 定度首先是求物镜的放大倍率。求物镜的放大倍率的方 法是用一个标准刻线尺(通常为专用附件,刻度间隔为 0.01mm,共101条刻线)来测定各个物镜的实际放大倍 率。物镜放大率为:
令C=5/V,则:h=Cn 式中,n为测量峰谷高度时两次读数的差值(格数)。 显然,上式使用简便。 C值的物理意义就是测微鼓轮一小格所对应的峰谷方向的高度值。
第四章 表面粗糙度的测量
§4.1 概述
一、表面形貌误差的概念与形成
1. 表面形貌误差分类: 实际加工表面通常包括如下三种表面形貌 误差:
表面粗糙度:波距小于1mm,大体呈周期性变化, 属于微观几何形状误差; 表面波度:波距在1-10mm,呈周期性变化,属 于中间几何形状误差; 形状误差: 波距大于10mm,无明显周期性变化, 属于宏观几何形状误差。 纹理方向、伤痕
3、测量方法 测量前,选择相应的物镜并已知定度值C。然后调节 显微镜使视场呈现清晰的狭缝及表面像,且至狭缝像的一 个边缘最清晰为止。 (1)测量Rz值: 其测量方法应符合定义。Rz值可按下式计算:
(2)测量Ry值:
(3)测量单峰平均间距S值
(4)测量平均间距Sm
(5)用光切法测量Ra值 因测量与计算都很麻烦,故很少应用
表面粗糙度对零件的使用性能有着重要的影响,主要 表现在:
对摩擦和磨损的影响:表面粗糙度大—磨损大—寿 命低 对配合性的影响:表面粗糙度影响配合性质的稳定性 对接触刚度的影响:表面越粗糙,接触刚度越低 对疲劳强度的影响:表面越粗糙,疲劳强度越低 对抗腐蚀性的影响:粗糙的表面易造成表面锈蚀 对结合密封性的影响 对检验零件时的测量不确定度、零件的外形美观等的影响
轮廓支承长度与取样长度之比,就是轮廓 支承长度率。
三、一般规定
1.为保证零件的表面质量,可按功能需要规定表面粗 糙度。
2.在规定表面粗糙度要求时,必须给出粗糙度参数值 和测定时的取样长度值两项基本要求,也可规定表 面纹理、不同区域的粗糙度等附加要求。
3.评定过程中,不应把表面缺陷(如沟槽、气孔、划 伤等)包含进去,必要时,应单独规定表面缺陷要 求。
此外,当被测表面段很短(不足一个取样长度), 不适宜采用Ra评定时,也常采用Rz参数。
4、轮廓微观不平度的平均间距Sm 含有一个轮廓峰和相邻轮廓谷的一段中线 长度Sm,称为轮廓微观不平度间距。
5、轮廓单峰平均间距S 两相邻轮廓单峰的最高点在中线上的投影 长度S,称为轮廓单峰的间距。
6.轮廓支承长度率tp (反映耐磨性) 一根平行于中线且与轮廓峰顶线相距为C的 线与轮廓峰相截所得到的各段截线bi之和,称 为轮廓支承长度p
(1)最小二乘中线: 使轮廓上各点的轮廓偏转距y(在测量方向 上轮廓上的点至基准线的距离)的平方和为最 小的基准线。
(2)算术平均中线: 在取样长度范围内,划分实际轮廓为上、 下两部分,且使上下两部分的面积相等的线。
(a)轮廓最小二乘中;(b)轮廓算术平均中线
二、评定参数及数值
对评定参数的基本要求: (1)正确、充分反映表面微观几何形状特征; (2)具有定量的结果; (3)测量方便。 国标从水平和高度两方向各规定了三个评 定参数,三个基本参数,三个附加的评定参数
便携式表面粗糙度仪
影响因素: 触针形状 & 测量力
非接触测量方法
①光学探针法 ②临界角法 ③外差干涉法
测量时,压电驱动器线性移动参考表面,从而 导致两个光束相位发生移动。系统记录不同相位下 条纹强度,并综合光强数据,作出随相位变化的光 强变化波形。表面高度由以下公式得出: H(x,y) = λ*Ф(x,y)/(4*Π) λ为光源波长,Ф(x,y)是相位。 当条纹图案足够时,这项技术是可靠的。但如 果相邻测点高度超过λ/4,半波长的倍数会被忽略。
3、轮廓最大高度Ry (新的国家标准中用Rz ) 在取样长度内,轮廓峰顶线和轮廓谷底线之间 的距离。
lr
c Xs1 Xsj Xsn Ry
Ra、Rz 哪个能充分反映粗糙度的特性?
当粗糙度值在0.025~6.3 m时,轮廓好测量,标 Ra (一般用电动轮廓仪进行测量);
Rz 用于控制不允许出现较深加工痕迹的表面,
一、主要术语及定义
1. 实际轮廓:平面与实际表面相交所得的 轮廓线。
按照相截方向的不同,可分为横向实际 轮廓和纵向实际轮廓。除非特别指明,通常 均指横向实际轮廓,即与加工纹理方向垂直 的截面上的轮廓。
2. 取样长度L:用于判别和测量表面粗糙度 时所规定的一段基准线长度。
量取方向:在轮廓总的走向上。 目的:限制和削弱表面波度对表面粗糙度测量 结果的影响。 选择原则:下一页
触针法又称针描法,它是一种接触式测量方法,是利用 仪器的测针与被测表面相接触,并使测针沿表面轻轻划 过以测量表面粗糙度的一种测量法。它是将一个很尖的 触针(半径可以做到微米量级的金刚石针尖)垂直安置 在被测表面上作横向移动,由于工作表面粗糙不平,因 而触针将随着被测表面轮廓形状作垂直起伏运动。将这 种微小位移通过电路转换成电信号并加以放大和运算处 理,即可得到工作表面粗糙度参数值;也可通过记录器 描绘出表面轮廓图形,再进行数据处理,进而得出表面 粗糙度参数值。这类仪器垂直方向的分辨率最高可达到 几纳米。 适宜测量值为5-0.02m范围内的表面粗糙度。
4、仪器的测量误差和示值相对误差的检定 (1)测量误差的主要因素有:瞄准误差、测微目镜 制造误差、估读误差、定度用标准尺误差、被测工件 定位误差、仪器使用调整误差等。 (2)仪器示值误差的检定:根据国家计量检定规程, 仅检定其示值相对误差是否在要求的范围内,测量范 围(即物镜)不同,要求不同。 (3)仪器示值相对误差的检定是用受检定的光切显 微镜去实测已知其刻线深度的单刻线样板(也可用阶 梯量块代替),则涉式轮廓仪
激光干涉式轮廓仪中,干涉系统的测量镜与触针分别位于杠 杆的两端,其位移量之间为确定的比例关系,因此由测得的 测量镜的位移量可算得触针的位移量。 与电感式轮廓仪相比,激光式轮廓仪具有宽量程和高分辨的 特点。
4、压电式轮廓仪
压电式轮廓仪具有压电特性的晶体作为传感器的换能元件。 硅脂是一种粘滞性很强的液体,当触针随工件表面快速上下 运动时,液体摩擦很大,可认为触针杆被夹紧在槽片中,压 电晶片因触针的位移而产生变形,并在晶片表面产生与变形 成比例的电荷。 压电式轮廓仪结构紧凑,便于携带。
二、光切法测量表面粗糙度
1、光切法原理 用一狭窄的扁平光以一定倾斜角照射到被 测面,发生反射,将表面微观不平度用显微镜 放大成像进行观测。
2、测量仪器原理及定度 (1)原理
(a)测量装置结构简图;(b)目镜视场的影像;(c)测量原理简图 1—光源; 2—聚光镜;3—狭缝; 4、5—物镜; 6—分划板;7—目镜; 8—被测表面
测量方法:目测法-▽6以下表面(即Ra值大于 2.5m);用5~10倍放大镜比较- ▽6 ~ ▽8的 表面;用比较显微镜- ▽8以上的表面;也可用 手摸靠感觉来判断被加工表面的粗糙度。 注意点:样板与被测件的加工方法、材料、形状 都相同。
适用范围:工厂比较常用,尤其是车间检验中常 用。一般只用于粗糙度评定参数值较大的情况下, 其判断的准确性很大程度上取决于检验人员的经 验,当有争议时可用仪器进行测量。
l
a
标准平面
解 若工件表面是平的,等厚条纹应 为平行于棱边的直线条纹。由于一条 条纹对应一个厚度,由图的纹路弯曲 情况可知,
工件表面的纹路是凹下去的。 由图:H = a sin 因 :lsin = /2, H 所以纹路深度
工件
a H l 2
四、触针法测量表面粗糙度
1、触针法的测量原理
3. 评定长度L:
评定轮廓所必须的一段长度,它包括一个或 数个取样长度。 目的:为充分合理地反映某一表面的粗糙度特 性(加工表面有不同程度的不均匀性)。 选择原则:一般按五个取样长度来确定。
4.轮廓中线m
是评定表面粗糙度数值的基准线。具有几 何轮廓形状与被测表面几何形状一致,并将被 测轮廓加以划分的线。类型有:
§4.2 表面粗糙度的评定参数
国家标准
我国参照国际标准(ISO),对原表面粗糙 度国家标准GB 1031-1983、GB 131-1983作了 修订和增订,新国标有: GB/T 3505-2000《 表面结构的术语、定义及参 数》 GB/T 1031-1995《表面粗糙度 参数及其数值》 GB/T 131-1993《机械制图 表面粗糙度符号、 代号及其注法》。
三、干涉显微镜测量表面粗糙度