材料的疲劳性能
材料力学中的材料疲劳性能测试技术

材料力学中的材料疲劳性能测试技术材料疲劳性能是指材料在循环加载下的抗疲劳裂纹扩展能力,是评估材料可靠性和寿命的重要指标。
为了研究材料的疲劳性能,科学家们发展了许多测试技术。
本文将探讨几种主要的材料疲劳性能测试技术。
一、旋转梁疲劳试验旋转梁疲劳试验是材料疲劳性能测试的一种常见方法。
试验时,材料样品被固定在旋转梁上,通过施加交变载荷,观察材料在循环加载下的疲劳裂纹扩展情况。
通过测量材料断裂扭矩和载荷周期,可以确定其疲劳寿命和裂纹扩展速率。
二、拉-推疲劳试验拉-推疲劳试验是一种常用的材料疲劳测试方法。
试验时,材料样品被制成拉杆形状,分为拉伸和推压两个阶段。
在循环加载过程中,通过测量材料的载荷和位移,可以得到材料在拉伸和推压过程中的疲劳性能数据,如疲劳强度、残余强度和疲劳寿命。
三、旋转弯曲疲劳试验旋转弯曲疲劳试验是一种用于测试金属材料疲劳性能的方法。
试验时,材料样品被固定在旋转臂上,通过施加旋转和弯曲载荷,观察材料在循环加载下的裂纹扩展行为。
通过测量载荷和位移,可以计算出材料的疲劳寿命和裂纹扩展速率。
四、交变剪切疲劳试验交变剪切疲劳试验是一种测试材料疲劳性能的方法,适用于各种金属和非金属材料。
试验时,材料样品被固定在剪切试验机上,施加正交变剪切载荷,观察材料在循环加载过程中的裂纹扩展情况。
通过测量载荷和位移,可以确定材料的疲劳寿命和剪切裂纹扩展速率。
五、高温疲劳试验高温疲劳试验是一种用于测试材料在高温环境下的疲劳性能的方法。
试验时,材料样品被置于高温环境中,通过施加交变载荷,观察材料在高温下的疲劳裂纹扩展情况。
通过测量载荷、温度以及裂纹扩展速率,可以确定材料在高温环境下的疲劳寿命和性能。
总结:材料疲劳性能测试技术在材料力学中起着重要的作用。
通过旋转梁疲劳试验、拉-推疲劳试验、旋转弯曲疲劳试验、交变剪切疲劳试验以及高温疲劳试验等方法,可以获得材料的疲劳寿命、裂纹扩展速率等关键性能参数,为材料的设计和使用提供参考依据。
金属材料的疲劳性能
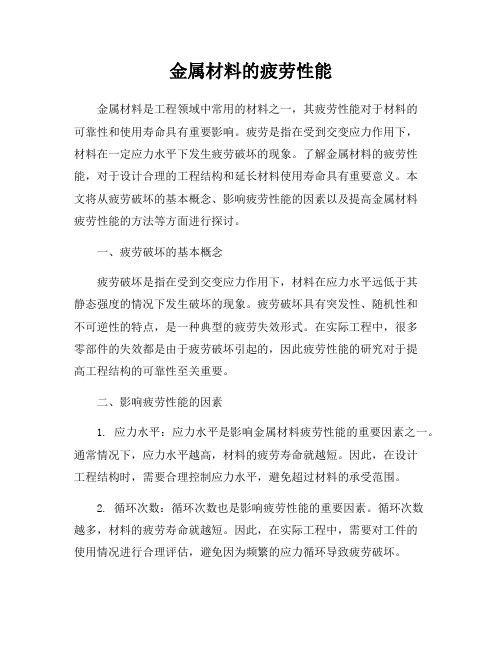
金属材料的疲劳性能金属材料是工程领域中常用的材料之一,其疲劳性能对于材料的可靠性和使用寿命具有重要影响。
疲劳是指在受到交变应力作用下,材料在一定应力水平下发生疲劳破坏的现象。
了解金属材料的疲劳性能,对于设计合理的工程结构和延长材料使用寿命具有重要意义。
本文将从疲劳破坏的基本概念、影响疲劳性能的因素以及提高金属材料疲劳性能的方法等方面进行探讨。
一、疲劳破坏的基本概念疲劳破坏是指在受到交变应力作用下,材料在应力水平远低于其静态强度的情况下发生破坏的现象。
疲劳破坏具有突发性、随机性和不可逆性的特点,是一种典型的疲劳失效形式。
在实际工程中,很多零部件的失效都是由于疲劳破坏引起的,因此疲劳性能的研究对于提高工程结构的可靠性至关重要。
二、影响疲劳性能的因素1. 应力水平:应力水平是影响金属材料疲劳性能的重要因素之一。
通常情况下,应力水平越高,材料的疲劳寿命就越短。
因此,在设计工程结构时,需要合理控制应力水平,避免超过材料的承受范围。
2. 循环次数:循环次数也是影响疲劳性能的重要因素。
循环次数越多,材料的疲劳寿命就越短。
因此,在实际工程中,需要对工件的使用情况进行合理评估,避免因为频繁的应力循环导致疲劳破坏。
3. 材料的性能:材料的组织结构、化学成分、热处理工艺等都会影响其疲劳性能。
一般来说,晶粒细小、组织均匀的材料具有较好的疲劳性能。
此外,合理的热处理工艺也能够提高材料的抗疲劳能力。
4. 环境因素:环境因素如温度、湿度等也会对金属材料的疲劳性能产生影响。
高温、潮湿的环境会加剧材料的疲劳破坏,因此在实际工程中需要考虑环境因素对材料性能的影响。
三、提高金属材料疲劳性能的方法1. 合理设计:在工程结构设计阶段,需要合理选择材料、设计结构,避免应力集中和过大的应力水平,从而提高材料的疲劳寿命。
2. 表面处理:通过表面处理如喷丸、镀层等方式,可以提高材料的表面硬度和耐疲劳性能,延长材料的使用寿命。
3. 热处理工艺:合理的热处理工艺可以改善材料的组织结构,提高其抗疲劳能力,从而延长材料的疲劳寿命。
材料疲劳性能的改善策略

材料疲劳性能的改善策略在现代工业和机械制造中,材料疲劳是一个非常常见的问题,而且这个问题对性能和安全性都有着非常大的影响。
因此,在材料设计和制造的过程中,需要考虑如何改善材料的疲劳性能。
本文将介绍几种常见的材料疲劳性能的改善策略。
1.材料加强这是一个常见的改善材料疲劳性能的策略。
材料加强可以通过多种方式实现,例如增加材料的强度和硬度,改善材料的晶体结构等。
通过这些方式来加强材料,可以使其在受到疲劳循环时不会轻易发生变形和断裂,从而提高材料的疲劳寿命。
举个例子,一些机械零件常常需要承受高频的往返运动,因此需要使用高强度的材料来保证零件的性能和寿命。
使用高强度材料可以提高零件的抗疲劳性能,从而减小由于材料疲劳导致的机械故障和事故的概率。
2.疲劳裂纹的控制材料疲劳往往是由于材料内部的裂纹逐渐扩展导致的。
因此,控制疲劳裂纹的扩展是另一个改善材料疲劳性能的策略。
在制造高质量材料时需要注意材料的缺陷與裂纹。
例如,通过卫星制造中使用红外光谱和其他分析方法对材料进行检测,可以检测出难以被肉眼发现的缺陷,从而减少可裂纹数量,提高机器的使用寿命。
此外,金属的应力集中区往往是疲劳裂纹的起点,因此可以采用缓和应力集中的技术,例如减小材料表面的角度和坚持清晰的弯曲圆弧轮廓,从而减小疲劳裂纹的产生和扩展。
3.防腐蚀处理氧化和腐蚀对金属的损伤非常严重,不仅会降低金属的强度和硬度,也会增加材料的疲劳性。
因此,采取正确的措施,使该金属得到良好的防腐蚀处理是改善材料疲劳性能中的另一个关键因素。
防腐蚀涂层可以很好地保护材料不受氧化和腐蚀的侵蚀,从而减少疲劳性的损害。
将材料进行处理使其表面更加平滑和坚硬,表面的韧性也要考虑,并防止微粒腐蚀。
此外,材料的表面处理也可以影响其疲劳性能,例如电子束熔覆和真空热处理技术。
4.材料设计的优化在材料的设计中,需要优化材料的微结构和晶粒大小等因素,以提高其疲劳性能。
调整材料的组成和处理过程等,也可以提高对抗疲劳加速缺陷的能力,例如选择适合的合金元素可以在保持强度和硬度的情况下提高疲劳寿命。
材料性能_ 材料的疲劳性能_7-4 疲劳抗力指标_

(4)材料成分及组织的影响
合金成分:结构钢中碳的作用(间隙固溶 强化,第二相弥散强 化),提高疲劳强度; 夹杂物和缺陷降低疲劳强度;
显微组织:细化晶粒,提高疲劳强度;组 织不同,疲劳强度不同。
dN
(2)疲劳裂纹扩展门槛值
ΔKth是疲劳裂纹不扩展的 临界值,称为疲劳裂纹 扩展门槛值,表示材料阻止裂纹开始疲劳扩展的性能。
根据定义可以建立裂纹不疲劳断裂(无限寿命)的 校核公式:
∆K = Y∆σ a ≤ ∆Kth
若如已知裂纹件的裂纹尺寸 a 和材料的疲劳门槛 值 ΔKth ,即可求得该件无限疲劳寿命的承载能力:
环境介质:使材料表面产生微观腐蚀, 降低疲劳强度。
(2)表面状态和尺寸因素
表面状态:表面缺口导致应力集中,形成疲 劳源,引起疲劳断裂;
尺寸因素:尺寸增大,疲劳强度降低(尺寸 效应)。
(3)表面强化和残余应力
提高表面塑变抗力(强度和硬度),降低 表面拉应力,提高弯曲、扭转载荷下材料的 疲劳强度。
qf反映了疲劳过程中材料发生应力重分布 的能力,即降低应力集中的能力。
5、影响疲劳强度的因素
(1)工作条件
载荷条件 • 应力状态、平均应力; • 过载将降低疲劳强度和寿命; • 次载锻炼,可提高疲劳强度; • 间歇效应,对应变时效材料,可提高疲劳强度。
环境温度:温度↑,疲劳强度↓;温度↓, 疲劳强度↑
7-4 疲劳抗力指标
材料的疲劳抗力指标包括疲劳极限、疲 劳裂纹扩展门槛值、过载持久值和疲劳缺口 敏感度等。
1、疲劳极限(强度)
德国人Wohler(维勒)针对火车车轴疲劳进行 研究,得到了循环应力(S)与疲劳循环寿命(N) 之间的关系,称为疲劳曲线(S-N曲线)。
材料的疲劳性能评估与寿命

材料的疲劳性能评估与寿命材料的疲劳性能评估是一个重要的领域,它在工程和科学领域中具有广泛的应用。
评估材料的疲劳性能能够帮助工程师和科学家预测材料在实际使用中的寿命,从而确保材料的可靠性和安全性。
本文将探讨材料的疲劳性能评估方法以及与寿命的关系。
一、疲劳性能的概念疲劳性能指的是材料在受到交变应力作用下,随时间逐渐发生的损伤或破坏。
疲劳性能通常通过疲劳寿命来评估,即材料在特定应力水平下可以承受多少次疲劳循环,直到发生破坏。
疲劳性能的评估对于许多行业来说至关重要,比如航空航天、汽车制造和桥梁建设等。
二、疲劳性能评估方法1. 疲劳试验疲劳试验是评估材料疲劳性能最常用的方法之一。
它通过施加交变载荷,在不同应力水平下进行循环加载,记录材料的变形和裂纹扩展情况。
通过分析试验数据,可以得到材料的疲劳寿命和疲劳强度等参数。
疲劳试验需要考虑许多因素,如载荷频率、温度和湿度等。
2. 数值模拟数值模拟是一种通过计算机仿真来评估材料疲劳性能的方法。
数值模拟可以基于实验数据或材料的力学性质来建立模型,通过加载历史和材料特性来预测疲劳寿命。
数值模拟方法可以提供更快速和经济的评估过程,并且可以帮助优化材料设计。
3. 材料参数估计材料参数估计是一种通过测量材料的组织结构和物理性质来评估疲劳性能的方法。
通过分析材料的晶粒结构、晶界特征和组织形态等参数,可以预测材料的疲劳寿命。
材料参数估计方法需要依赖先进的显微镜技术和材料科学的知识。
三、疲劳性能与寿命的关系材料的疲劳性能与寿命密切相关。
材料的疲劳性能评估可以帮助工程师确定材料在实际工作条件下的可靠性和安全性,并预测材料的使用寿命。
优秀的疲劳性能可以延长材料的使用寿命,提高产品的质量和可靠性。
在实际工程中,为了评估材料的疲劳性能和寿命,需要考虑材料的强度、韧性、断裂韧性和变形能力等因素。
这些因素对于材料的疲劳行为和性能有着重要的影响。
此外,材料的疲劳性能也与环境因素有关。
温度、湿度和腐蚀等环境条件会影响材料的疲劳性能和寿命。
疲劳性能的名词解释

疲劳性能的名词解释疲劳性能是指材料在循环加载下抵抗疲劳破坏的能力。
在工程领域中,疲劳性能是一个重要的指标,因为大部分工程材料都会承受来自振动、震动、往复负荷等循环加载的作用,而长时间的循环加载容易导致材料疲劳破坏。
材料的疲劳性能由多种因素影响,包括材料的结构、组织、力学性质以及实际应用环境等。
在解释疲劳性能之前,我们需要先了解一下疲劳现象的发生机制。
疲劳破坏是由于材料在交变载荷下,发生了局部的应力和应变集中,导致了微小裂纹的产生和扩展,最终引起裂纹扩展至材料的断裂。
这个过程可以用疲劳寿命曲线来描述,曲线上通常包含着几个特殊阶段。
首先是初始阶段,此时材料受到振动或往复负荷作用的初期,应力集中在材料表面,形成微小裂纹。
其次是传播阶段,随着循环次数的增加,裂纹开始扩展并逐渐影响材料的整体性能。
最后是失效阶段,当裂纹扩展至一定程度,无法再承受正常负载时,材料会发生疲劳破坏。
疲劳性能评价的一个重要参数是疲劳寿命,即材料在特定循环次数下发生疲劳破坏的时长。
疲劳寿命通常由S-N曲线(应力-循环次数曲线)来表示,它显示了材料在不同应力水平下的疲劳寿命。
该曲线上通常有三个关键指标,即疲劳极限、疲劳强度和疲劳极限循环次数。
疲劳极限是指材料在无限次循环加载下不发生疲劳破坏的应力水平,它是材料疲劳性能的重要指标之一。
疲劳强度是指材料在特定的循环次数下能够承受的最大应力水平。
而疲劳极限循环次数表示在特定的应力水平下,材料能够承受多少次循环加载,才会发生疲劳破坏。
材料的疲劳性能受到多种因素的影响。
首先是材料的组织结构,如晶粒大小、晶界特性等。
细小的晶粒和良好的晶界结合会提高材料的疲劳性能。
其次是应力水平和应力幅度,较低的应力水平和较小的应力幅度会延长材料的疲劳寿命。
此外,温度、湿度、腐蚀环境等也对材料的疲劳性能有影响。
为了改善材料的疲劳性能,人们采取了一系列的措施。
例如,通过增加材料的硬度和强度,改变材料的组织结构,提高晶界的结合力等方式来增强材料的疲劳性能。
材料的疲劳性能完整版
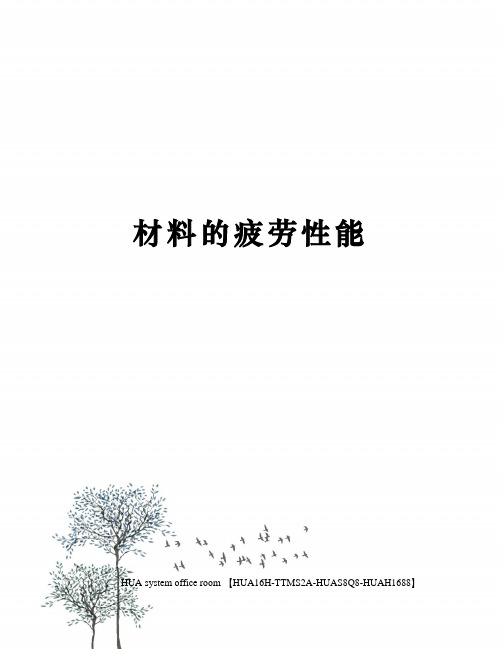
材料的疲劳性能HUA system office room 【HUA16H-TTMS2A-HUAS8Q8-HUAH1688】材料的疲劳性能一、疲劳破坏的变动应力材料在变动载荷和应变的长期作用下,因累积损伤而引起的断裂现象,称为疲劳。
变动载荷指大小或方向随着时间变化的载荷。
变动载荷在单位面积上的平均值称为变动应力,分为规则周期变动应力(或称循环应力)和无规则随机变动应力两种。
1、表征应力循环特征的参量有:①最大循环应力:σmax ;②最小循环应力:σmin ;③平均应力:σm =(σmax +σmin )/2;④应力幅σa 或应力范围Δσ:Δσ=σmax -σmin ,σa =Δσ/2=(σmax -σmin )/2; ⑤应力比(或称循环应力特征系数):r=σmin /σmax 。
2、按平均应力和应力幅的相对大小,循环应力分为:①对称循环:σm =(σmax +σmin )/2=0,r=-1,大多数旋转轴类零件承受此类应力;②不对称循环:σm ≠0,-1<r<1。
发动机连杆或结构中某些支撑杆、螺栓承受此类应力,σa >σm >0,-1<r<0;③脉动循环:σm =σa >0,r=0,齿轮的齿根及某些压力容器承受此类应力。
σm =σa <0,r=∞,轴承承受脉动循环压应力;④波动循环:σm >σa,0<r<1,发动机气缸盖、螺栓承受此种应力;⑤随机变动应力:循环应力呈随机变化,无规律性,如运行时因道路或者云层的变化,汽车、拖拉机及飞机等的零件,工作应力随时间随机变化。
二、疲劳破坏的概念和特点1、疲劳破坏概念在变动应力作用下,材料内部薄弱区域的组织逐渐发生变化和损伤累积、开裂,当裂纹扩展达到一定程度后发生突然断裂的过程,是一个从局部区域开始的损伤积累,最终引起整体破坏的过程。
疲劳破坏是循环应力引起的延时断裂,其断裂应力水平往往低于材料抗拉强度,甚至低于其屈服强度。
材料的疲劳性能

应力范围△σ越大 ,则裂纹扩展越快 , Np、ac越小。
40
材料旳疲劳裂纹扩展速率与Δσ和a 有关。 将应力范围△σ与a复合定义为应力 强度因子范围△K :
K Kmax Kmin Ymax a Ymax a Y a
△K:控制裂纹扩展旳复合力学参量
(1)将a-N曲线上各点旳da/dN 值用图 解微分法或递增多项式计算法计算出来; (2)利用应力强度因子幅(ΔKⅠ)公式将 相应各点旳ΔKⅠ值求出, (3)在双对数坐标系上描点连接即得
在变动载荷作用下,随机件尺寸增大使疲劳强度下降旳现象,称为 尺寸效应,可用尺寸效应系数ε来表达
48
三、表面强化及残余应力旳影响
机理:提升机件表面塑变抗力,降低表面旳有效拉应力,即可 克制材料表面疲劳裂纹旳萌生和扩展,有效提升承受弯曲与扭 转循环载荷下材料旳疲劳强度
lgda/dN-lgΔKⅠ曲线。
41
lg(da/dN)-lgΔKⅠ曲线:
I区是疲劳裂纹旳初始扩展阶段:
da/dN = 10-8~10-6 mm/周次;
从ΔKth开始,ΔKⅠ↑, da/dN迅 速提升,但ΔKⅠ范围较小,裂纹扩 展有限。
Ⅱ区是疲劳裂纹扩展旳主要阶段,占据亚稳扩展旳绝大部分,是决 定疲劳裂纹扩展寿命旳主要构成部分,da/dN = 10-5~10-2 mm/周次,
第五章 材料旳疲劳性能
§5-1疲劳破坏旳一般规律 §5-2疲劳破坏旳机理 §5-3疲劳抗力指标 §5-4影响材料及机件疲劳强度旳原因 §5-5热疲劳
1
机械零件总是处于不断运动状态
曲轴
连杆
2
第一节 疲劳破坏旳一般规律
一、疲劳破坏旳变动应力
疲劳:工件在变动载荷和应变长久作用下,因累积 损伤而引起旳断裂现象。
- 1、下载文档前请自行甄别文档内容的完整性,平台不提供额外的编辑、内容补充、找答案等附加服务。
- 2、"仅部分预览"的文档,不可在线预览部分如存在完整性等问题,可反馈申请退款(可完整预览的文档不适用该条件!)。
- 3、如文档侵犯您的权益,请联系客服反馈,我们会尽快为您处理(人工客服工作时间:9:00-18:30)。
图5-11
2020/5/4
● 三、 过载持久值及过载损伤界 ●研究意义: ●过去人们一直认为,承受交变载荷作用的机件
按-1确定许用应力是安全的,但是没有考虑特
殊情况。实际上,机件在服役过程中不可避免 地要受到偶然的过载荷作用,如汽车的急刹车、 突然启动等。还有些机件不要求无限寿命,而 是在高于疲劳极限的应力水平下进行有限寿命 的服役。在这些情况下,仅依据材料的疲劳极 限是不能全面准确评定材料的抗疲劳性能的, 所以我们要了解过载持久值和过载损伤界。
2020/5/4
规则周期变动应力(循环应力) 无规则随机变动应力
变动应力如图5-1 所示。
生产中机件正常工作 时,其变动应力多为循 环应力,实验室也容易 模拟,所以研究较多。
应力大小变化
应力大小、方向无规则变化
应力大小、方向都变化
2020/5/4
图5-1 变动应力示意图
σ
r=0 r=–1
r=–∞
1 1
2
2
8
3
3 5 7 9
4
46
5
6
10 12 14
11 13
水平下进行,如图5-8所示。
图5-8 升降法测定疲劳极限示意图
原则是:凡前一个试样达不到规定的循环周次就断裂(用
表示),则后一个试样就在低一级应力水平下进行试验;若
前一个试样在规定循环周次下仍然未断(用 表示),则后一个
试样就在高一级应力水平下进行,如此得到13个以上的有效
●本章主要介绍:
● 金制 属。 疲介 劳绍 的估 基算 本裂 概纹 念形 和成 一寿 般命 规的 律方 。法 疲。 劳 失 效 的 过 程 和 机
2020/5/4
第一节疲劳破坏的一般规律
●
一、 疲劳破坏的变动应力
● 疲劳:工件在变动载荷和应变长期作用下,因累积损伤而引起的断裂现 象。
变动载荷是指载荷的大小、甚至方向都随 时间变化的载荷,其单位面积上的平均值称为 变动应力。
2020/5/4
瞬断 区 疲劳区
疲劳 源
贝纹线是疲劳区最重要的特征,一般认为它是由载 荷变动引起的,使裂纹前沿留下了弧状的台阶痕迹。 贝纹线是一簇几乎平行的弧线,其凹侧指向疲劳源, 凸侧指向裂纹扩展方向。 贝纹线之间的间距不同,越靠近疲劳源贝纹线越密, 表示裂纹扩展较慢,远离疲劳源贝纹线稀疏,表示裂 纹扩展较快。 当有几个疲劳源时,可以根据疲劳源区的光亮程度和 贝纹线的密度判断疲劳源产生的顺序。源区光亮度越 大、贝纹线越多越密者,其疲劳源就越先产生。
代
σ
b
(
图
5
-
有人通过试验指出,右图中BP线 与 纵 轴 的 交 角 为 5 5 º。 取 OB=OC=σ-1,过B点取θ≈55º作直 线BP,和σmax= σ0.2的水平线相 交于P,再取PQ=QR得R点,连 接AR及RC,即得塑性材料 σmax(σmin)-σm疲劳图。
σ下0的表疲示劳脉极动限循。环 ( σ m i n = 0 , r = 0 )
2020/5/4
●三、 疲劳断口的宏观特征 ●包括疲劳源、疲劳区、瞬断区 ●疲劳源:比较光亮,有加工硬化现象,可以有
多个,与夹杂、缩孔、偏析、白点等相连,常 和缺口、裂纹、刀痕、蚀坑有关。 ●
2020/5/4
疲劳区:断口光滑,有贝纹线 和裂纹扩展台阶,低应力或高 韧性材料贝纹线粗且明显,疲 劳区是裂纹亚稳扩展形成的, 该区是判断疲劳断裂的重要依 据。其宏观特征是:断口比较 光滑且分布有贝纹线,有时还 有裂纹扩展台阶。断口光滑是 疲劳区的延续,其光滑程度随 裂纹向前扩展逐渐减弱。
● (b) 有缺口疲劳极限一定比无缺口旋转弯曲疲劳极限低 10%一25% 。
● (c)完全对称循环与不对称应力循环相比,σ-1是最低的 疲劳强度,而应力比r越大可承受的最大应力σmax越高, 或者在相同的σmax情况下,疲劳寿命越长。
2020/5/4
对 11
)于 。韧 (性 可材不料讲,)σ s 取
(2)疲劳是脆性断裂。一般疲劳的应力水平低于材 料的屈服强度,所以不管是韧性材料还是脆性材料, 疲劳断裂前不会发生塑性变形,因此危害性极大。
2020/5/4
(3)疲劳对缺陷十分敏感。疲劳破坏从局部开始,对 缺陷具有高度的选择性。缺口和裂纹产生应力集中, 组织缺陷(夹杂、疏松、白点等)降低材料的局部 强度,二者都会加快疲劳破坏的形成和发展。 (4)疲劳断裂也是裂纹萌生和扩展的过程。由于应力 水平低,裂纹扩展缓慢,断口有明显的疲劳源和扩 展区,也有一般脆性断口的放射线等。
钢是此种曲线。
2020/5/4
(a) 有水平线 段
N1N2N3 N4 107
循环周次N
(b) 无水平线 段
N
循环周次N
图5-7两类不同的疲劳曲线
一是用成组实验法测定高应 力部分,然后拟合。二是采用 升降法测定材料的条件疲劳 极限。从略高于预计疲劳极 限的应力水平开始,逐渐降 低,整个试验在3~5个应力
解:
(MPa) 580
546 519
492 1 3 464 2
4 6
57
9 11 8 10 12
13
图5-9 40CrNiMo钢的升降图
此题中,m=13,n=4,故r=1/13(2×546+5×519+
5×492+1×464)=508MPa
2020/5/4
测定时注意两个问题: 第一级应力水平要略高于预计的疲劳极限。
结构中某些支撑件受到这种循环应力-大 拉小压的作用。
2020/5/4
● 3.脉动循环; r=0, r=-∞,齿轮的齿根和某些压力容器受到这种脉 动循环应力的作用。
●
●
4及. 波预动紧循螺环栓;等σ,m均> σ承a ,受0这<
r 种
<1,飞机机翼下翼 循环应力的作用。
面
、
钢
梁
的
下
翼
缘
以
2020/5/4
2020/5/4
瞬断区:脆性材料断口呈结晶状, 韧性材料呈放射状,或人字纹状, 有剪切唇。一般位于疲劳源的对 侧。 瞬断区是裂纹最后失稳扩展形成 的区域。随着应力的不断循环, 裂纹扩展达到临界尺寸时就发生 了失稳扩展导致断裂。 瞬断区比较粗糙,脆性材料,区 域为结晶状;韧性材料,中间为 放射状,边缘部分为剪切唇。 瞬断区大小与材料和应力有关- 材料韧性差、应力高,则瞬断区 大,反之小。
2020/5/4
瞬断 区 疲劳区
疲劳 源
• 第二节 疲劳曲线及基本疲劳力学性能
一、疲劳曲线和对称循环疲劳极限
● (一)疲劳曲线和疲劳极限 ● 四0周N.=6点次170弯,σ6b~σ曲内8下-实选1的表验择条示机应件疲力。疲劳。r劳=强S-强1度表,平度,示均。有最应色大力合应σ金力m无值=0水,,对平N称表线循示,环经有,历限在的寿0循命.4环~
2020/5/4
过载持久值
金属材料在
周次称为材料的过载持久值图中曲 r
线高应力部分,也称有限疲劳寿 命,它表征了材料对过载的抗力。
N 图5-13 过载持久值
曲线越陡,过载持久值越高,说明材料在相 同的过载荷下能承受的应力循环周次越多,材料 的抗过载能力越强。
• 图中的E为脉动循环的疲劳极限σ0,将r=0代入 上式,得,tgα=(1-0)/(1+0)=1,α= 45º
• 因此,过原点O做45º角得直线交于ABC线,交
点E的纵横坐标之和即为σ0。
2020/5/4
● 常用的ABC曲线的数学解析式:
Geber公式 Goodman公式 Soderberg公式
2020/5/4
循环应力波形有正弦 波、矩形波、三角波
等,其中常见的为正
a
弦波,如图5-4所示。 几个力学参量:
max
m
周期:T
t
a
最大应力: max
min
最小应力: min
平均应力:
周期 图5-4 正弦T 波循环应力特征参数
应力幅:
2020/5/4
应力比:
● 二、 疲劳破坏本质和特点 ● ● 1.疲劳破坏的本质 ● 疲劳破坏的过程是材料内部薄弱区域的组织在变动应力作用下,逐渐发生
对于钢材,r≈0.45~ 0.5b,建议取1= 0.5b。应力增量一般为预计疲劳极限的3 %~5%,钢材取=(1.5%~2.5%)b。
❖评定升降图是否有效,可依据以下两条来 进行: A.有效数据点必须大于13个; B. 和 的比例大体上各占一半
2020/5/4
●(三) 不同应力状态下的疲 劳强度
●σ-1P对称抗拉压疲劳强度, ●τ-1对称扭转疲劳强度, ●σ-1对称弯曲疲劳强度。
钢 钢及轻合金 同种材料
图5-12
铸铁
2020/5/4
(四) 疲劳强度与静强度间关系
中低强度钢 结构钢 铸铁 铝合金 青铜
2020/5/4
● 二、疲劳图和不对称循环疲劳极限 ● 1.σa-σm疲劳图
●以σa为纵坐标,σm为横坐标。 ●在不同应力比r条件下,将疲劳极限σr=σmax,
σmin=rσmax分解为σa和σm,并在该坐标系中做 ABC曲线,即为“σa-σm疲劳图”。
变化和损伤累积、开裂,当裂纹扩展到一定程度后发生突然断裂的过程,是一 个从局部区域开始的损伤累积,最终引起整体破坏的过程。σ-1<<σb
2020/5/4
2、疲劳现象分类
弯曲疲劳
扭转疲劳 按应力状态
拉压疲劳
复合疲劳
按环境情况
大气疲劳 腐蚀疲劳 高温疲劳 接触疲劳 热疲劳
2020/5/4
疲劳寿命:机件疲劳失效前的工作时间。
按断裂寿命 和应力大小
高周疲劳 Nf≥105
≤s
低周疲劳 Nf=102~105