瓦楞纸板常见质量问题的产生原因及解决办法
瓦楞纸板常见纸病的解决方案

瓦楞纸板常见纸病的解决方案一、开胶、假粘1、里纸开胶原因分析:1.1胶质量不符生产要求或腐败变质;1.2上胶量太小;1.3车速过快,瓦楞辊、压力辊热量不足;1.4压力辊压力不足;1.5瓦楞辊、压力辊的中高严重磨损。
解决方法:1.1更换合格胶液;1.2适量调大涂胶量;1.3提高瓦楞辊、压力辊温度,保证180℃以上开机,同时根据温度情况调整车速;1.4适当调整压力辊压力,以里、瓦纸粘合良好,里纸不露楞、瓦纸不碎为宜;1.5打磨或更换新压力辊、瓦楞辊。
1、面纸开胶、夹芯开胶原因分析:2.1胶量过小、烘干机速度过慢;2.2胶液稀薄,涂胶辊挂胶不足;2.3烘干机热板温度不足,胶液未充分糊化;2.4烘干机车速过快,纸板烘干不足;2.5烘干机传输带上面的压载辊没完全落下。
解决方法:2.1适当加大涂胶量,并酌情提高车速;2.2更换胶液或在原胶液中加入适量乳化剂;2.3升高烘干机热板温度至180℃以上开机;2.4减慢车速;2. 5落下压载浮辊。
原因分析:3.1瓦楞辊温度不足;3.2胶量过小,温度过高;3.3车速缓慢造成萃胶;3.4胶液黏度不够。
解决方法:3.1提高单面机工作温度;3.2调整涂胶量,关闭热源,待温度下降至180℃以下,160℃以上开机;3.3提高单面机速度;3.4适当增加胶液黏度。
2、面纸假粘原因分析:4.1烘干机热板温度不足;4.2胶液沉淀变质;4.3纸板在烘干机内停留时间过长。
解决方法:4.1待温度达到胶液能糊化时开机;4.2更换新胶;4.3尽量减少停机时间,换单换纸和断纸再续时动作要果断迅速。
二、倒楞1、单面纸板倒楞原因分析:1.1瓦楞辊磨损;1.2上下瓦楞辊间隙过大;1.3瓦楞纸定量太高且厚度太厚;1.4瓦楞纸水分过大;1.5瓦楞纸未经预热器,可塑性差。
解决方法:1.1磨削或更换瓦楞辊;1.2调整瓦楞辊间隙至0.5mm;1.3更换瓦楞纸;1.4调大预热包角,增大预热面积;1.5将瓦楞纸穿过预热器。
瓦楞纸板不良原因分析

瓦楞纸板不良原因分析瓦楞纸板是由瓦楞纸板芯和面纸组成的一种多层结构材料。
它主要用于包装和运输行业,承载能力强,便于加工和加工。
然而,在实际生产和使用过程中,我们经常会遇到各种瓦楞纸板的不良问题,这直接影响了其使用效果和质量。
以下是对瓦楞纸板不良原因进行分析的一些常见问题。
1.压痕和划痕:瓦楞纸板在生产过程中可能会出现压痕和划痕的问题。
这可能是由于设备不当调整或操作不规范导致的。
例如,如果压痕辊的间距不正确,或者生产速度过快,纸板受到了太大的力,就会出现压痕。
而划痕则可能是由于切割工具不锋利或切割速度过快而导致的。
2.破裂和撕裂:瓦楞纸板在运输和使用过程中容易出现破裂和撕裂的问题。
这可能是由于纸板的强度不足造成的,可能是由于纸板芯的纸张质量不好,或者纸张的厚度不足。
此外,如果瓦楞纸板在存储或运输过程中受到了湿气或温度变化的影响,也会导致纸板的强度减小,容易发生破裂和撕裂。
3.潞水和水印:潞水是指瓦楞纸板表面出现水印痕迹,给纸板的外观质量带来影响。
潞水可能是由于纸张表面平整度不好,或者纸张吸水性能不佳导致的。
此外,如果生产过程中的湿度控制不当,或者纸板表面存在杂质或污染物,也会导致潞水问题的出现。
4.尺寸不一致:瓦楞纸板的尺寸一致性是其质量的重要指标之一、如果纸板的尺寸不一致,可能会导致包装箱的组合困难,影响使用效果。
尺寸不一致的原因可能是由于生产过程中的设备调整不准确或操作不规范,或者纸板芯的厚度不一致,造成纸板的尺寸差异。
5.外观缺陷:瓦楞纸板的外观缺陷可能是指纸板芯表面的起泡、蜂窝状,或者面纸的褶皱、异常颜色等问题。
这些缺陷可能是由于纸张质量不佳、生产过程中的设备故障或不良操作导致的。
例如,如果纸张含水量不均匀,或者设备温度过高,就会导致瓦楞纸板表面起泡或蜂窝状。
综上所述,瓦楞纸板的不良问题可能是由于生产过程中的设备故障、操作不良、纸张质量不佳等因素导致的。
为了解决这些问题,生产厂家应该加强对设备的维护和调整,确保操作人员的培训和规范。
瓦楞纸板不良原因分析

瓦楞纸板不良原因分析瓦楞纸板是一种由多层纸板互相粘合而成的材料,具有良好的抗压性能和缓冲性能,广泛应用于各个行业的包装中。
然而,在生产和使用过程中,瓦楞纸板可能会出现一些不良现象,影响其使用效果和寿命。
下面将分析一些可能导致瓦楞纸板不良的原因。
1.原材料质量不良:瓦楞纸板的质量主要受原材料的影响,如果原材料质量不好,会直接影响到瓦楞纸板的质量。
比如,纸张的纤维长度不足、杂质过多、含湿率过高等都会导致瓦楞纸板的强度下降和易碎性增加。
2.生产过程不规范:瓦楞纸板的生产过程包括纸张的加工、糊合、干燥等环节,如果操作不规范或控制不当,会导致质量不良。
比如,糊合时糊胶的浓度不合适、温度控制不好、糊胶的均匀性不好等都会影响瓦楞纸板的强度和质量稳定性。
3.设备老化或损坏:生产瓦楞纸板需要使用一系列的设备,如纸张预处理机、糊合机、干燥机等。
如果这些设备老化或损坏,就会影响生产过程的正常进行,进而导致瓦楞纸板的质量下降。
4.储存条件不好:瓦楞纸板在生产出来后需要进行储存,如果储存条件不好,比如温度过高或者潮湿,会导致纸张变形、发霉,进而影响瓦楞纸板的强度和质量。
5.运输和包装不当:瓦楞纸板在运输和包装过程中也容易遭受挤压、湿泡等不良影响,特别是在长途运输或者储存时间较长的情况下,容易出现不均匀应力分布,导致瓦楞纸板强度下降或出现划痕、弯曲等问题。
6.设计不合理:瓦楞纸板在使用过程中有时受到外力的作用,特别是在堆叠、挤压等情况下,如果设计不合理,纸板可能容易变形、产生断裂、划痕等不良现象。
综上所述,瓦楞纸板不良的原因多种多样,涉及到原材料、生产过程、设备、储存和运输等多个方面。
为了提高瓦楞纸板的质量,减少不良现象的发生,需要从原材料的选择和质量控制、生产过程的改善和规范、设备的维护和更新、储存和运输条件的优化以及设计的合理性等方面进行改进和管理。
只有全面有效地把控这些方面,才能保证瓦楞纸板的质量和可靠性,满足各个行业对包装的需求。
瓦楞纸板质量影响因素分析
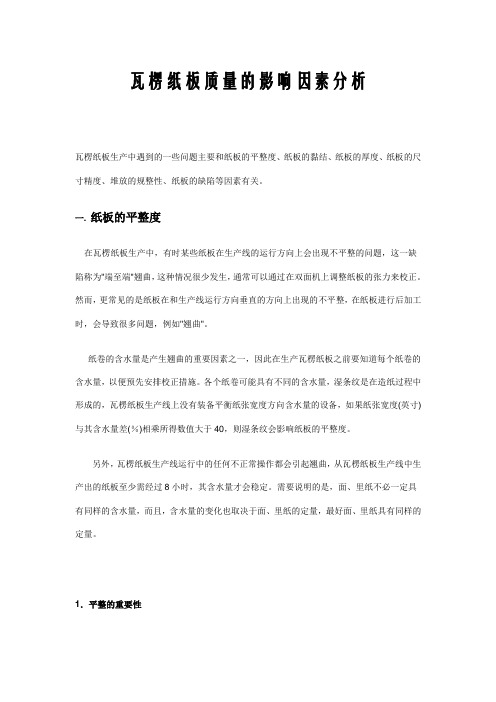
瓦楞纸板质量的影响因素分析瓦楞纸板生产中遇到的一些问题主要和纸板的平整度、纸板的黏结、纸板的厚度、纸板的尺寸精度、堆放的规整性、纸板的缺陷等因素有关。
一. 纸板的平整度在瓦楞纸板生产中,有时某些纸板在生产线的运行方向上会出现不平整的问题,这一缺陷称为"端至端"翘曲,这种情况很少发生,通常可以通过在双面机上调整纸板的张力来校正。
然而,更常见的是纸板在和生产线运行方向垂直的方向上出现的不平整,在纸板进行后加工时,会导致很多问题,例如"翘曲"。
纸卷的含水量是产生翘曲的重要因素之一,因此在生产瓦楞纸板之前要知道每个纸卷的含水量,以便预先安排校正措施。
各个纸卷可能具有不同的含水量,湿条纹是在造纸过程中形成的,瓦楞纸板生产线上没有装备平衡纸张宽度方向含水量的设备,如果纸张宽度(英寸)与其含水量差(%)相乘所得数值大于40,则湿条纹会影响纸板的平整度。
另外,瓦楞纸板生产线运行中的任何不正常操作都会引起翘曲,从瓦楞纸板生产线中生产出的纸板至少需经过8小时,其含水量才会稳定。
需要说明的是,面、里纸不必一定具有同样的含水量,而且,含水量的变化也取决于面、里纸的定量,最好面、里纸具有同样的定量。
1.平整的重要性当纸板直接作为成品出售时,翘曲往往被用户认为是质量问题而成为扯皮的根源。
更进一步说,瓦楞纸板的平整度对以后的加工操作有很大的影响。
在自动堆积机中,纸板平整才能堆积稳定,才能很方便地由滚轮传送器运出去,堆积的稳定性对于从瓦楞纸板生产线终端传送到库房,再从库房传送到后加工设备是很重要的。
后加工设备的自动进料器不能接受过于翘曲的纸板,翘曲的纸板会引起阻塞和机器停车,大大降低生产效率。
同时,如果后加工设备不能够连贯地传送纸板,就会导致不准确的印刷记数和模切操作.纸板翘曲也会导致粘盒、粘箱困难。
另外,纸板翘曲会降低纸箱的抗压强度,因为箱壁偏移使纸箱易垮塌。
2。
翘曲度的测量为了在瓦楞纸板生产线上进行各种调整以平整翘曲也为了纸板在厂内、外的质量控制,都需要测量翘曲度。
瓦楞纸板生产线常见问题及维护方法

瓦楞纸板生产线常见问题及维护方法1起楞过程中的常见故障及排除方法1.1瓦楞的高度不够,原因可能是压力或温度过低,或者纸张含水分过高。
解决办法是调整压力或辊温,或降低车速,使纸张得以干燥。
1.2瓦楞高度不均一,压出的瓦楞纸两边长短不同呈扇形。
这是由于瓦楞辊平行度不好或两端压力不均匀所致。
如左边瓦楞纸比右边短,应适当将上瓦楞辊左边升高,否则逆向调整。
1.3瓦楞纸卷曲成筒状,主要原因是上下辊筒温度差过大。
应检查上、下辊筒内加热源工作情况,或许其中之一出现故障,可予以修理或更换。
1.4瓦楞纸粘在瓦楞辊面上。
辊面温度过高或原纸水分含量过大都会出现这种现象。
此时应调整辊面温度,使纸张干燥后再压楞,若刮刀与辊槽不贴合,应调整或更换。
2瓦楞辊的维护与保养方法2.1使用前要检查瓦楞辊的平行度和紧固情况,调整好辊间配合压力。
2.2使用时要注意对瓦楞辊进行充分的润滑。
生产中在瓦楞辊表面喷洒少量油雾或减摩剂,会使瓦楞辊间磨损减少,也可防止瓦楞纸断裂和起泡现象的发生。
2.3使用后要清除配合压力,清扫辊面。
切忌用水冲洗高温辊面,否则将会使辊变形,加速磨损。
2.4定期保养。
瓦楞辊正常情况下可生产2000万米左右的瓦楞纸板,如果每天生产5万米瓦楞纸板,大约一年后就要进行磨削加工修理,磨削后的瓦楞辊直径约减少1.0mm,瓦楞的系数增大,原纸与胶粘剂用量也增多。
3瓦楞纸箱在印刷中应注意的问题3.1避免满版印刷瓦楞纸箱满版或四周印刷图文时,除压印辊对瓦楞纸板有压皖的作用外,油墨对纸面还有浸润作用,这些将使瓦楞纸箱的抗压强度降低。
因此,瓦楞纸箱印刷图文越简单越好,并尽可能避免在整个箱面上到处印刷图文,更不要满版印色。
3.2避免带状(与瓦楞纸板机械方向相同)印刷有的装潢设计人员由于缺少印刷工艺知识,设计的纸箱印刷图案有一些横向的渐变线条。
当印刷时,印刷压力将瓦楞压溃。
纸箱的这一区域将发生应力集中,因而最易折断。
3.3油墨颜色要醒目由于瓦楞纸板本身的颜色相当暗,所以在选择印刷的颜色时必须考虑到尽量选用颜色饱和度大的,着色力强的油墨(如大红色),否则印出来的颜色与希望的颜色会有很大差距。
瓦楞纸板各种常见纸病的解决方案
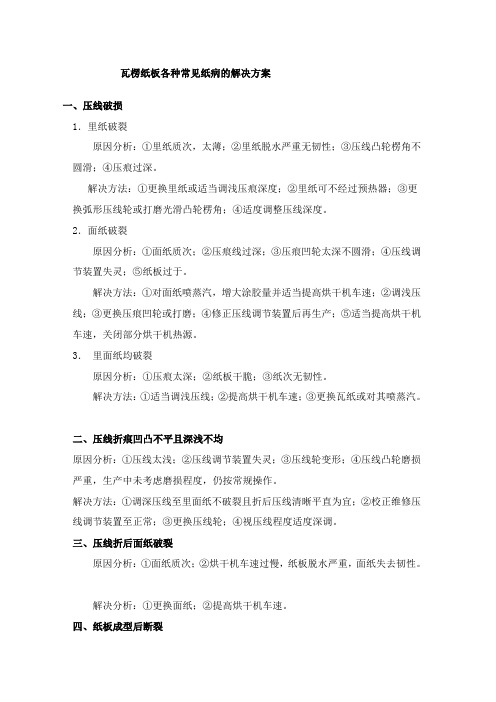
瓦楞纸板各种常见纸病的解决方案一、压线破损1.里纸破裂原因分析:①里纸质次,太薄;②里纸脱水严重无韧性;③压线凸轮楞角不圆滑;④压痕过深。
解决方法:①更换里纸或适当调浅压痕深度;②里纸可不经过预热器;③更换弧形压线轮或打磨光滑凸轮楞角;④适度调整压线深度。
2.面纸破裂原因分析:①面纸质次;②压痕线过深;③压痕凹轮太深不圆滑;④压线调节装置失灵;⑤纸板过于。
解决方法:①对面纸喷蒸汽,增大涂胶量并适当提高烘干机车速;②调浅压线;③更换压痕凹轮或打磨;④修正压线调节装置后再生产;⑤适当提高烘干机车速,关闭部分烘干机热源。
3.里面纸均破裂原因分析:①压痕太深;②纸板干脆;③纸次无韧性。
解决方法:①适当调浅压线;②提高烘干机车速;③更换瓦纸或对其喷蒸汽。
二、压线折痕凹凸不平且深浅不均原因分析:①压线太浅;②压线调节装置失灵;③压线轮变形;④压线凸轮磨损严重,生产中未考虑磨损程度,仍按常规操作。
解决方法:①调深压线至里面纸不破裂且折后压线清晰平直为宜;②校正维修压线调节装置至正常;③更换压线轮;④视压线程度适度深调。
三、压线折后面纸破裂原因分析:①面纸质次;②烘干机车速过慢,纸板脱水严重,面纸失去韧性。
解决分析:①更换面纸;②提高烘干机车速。
四、纸板成型后断裂原因分析:①瓦纸质次;②纸板过分干燥;③成型工序设备调节不当;④压线太浅,瓦楞未压扁或成型后折叠摇盖时高强瓦楞将面纸撑破,瓦楞随之断裂。
解决方法:①更换瓦纸;②保证纸板含水量在10±3左右;③注意成形各工序的设备调节并调至最佳状态;④烘干机加速并加大涂胶量,压线调深。
五、纵切毛边原因分析:①分纸刀已钝或刀刃有缺口;②上下刀咬合过深;③上下刀之间有间隙。
解决方法:①打磨或更换新刀;②调节上下刀重合至最佳状态;③将上下两刀靠紧,用手转动刀轮,灵活不伤刀为宜。
六、横切纸板拖尾原因分析:①横刀已钝;②横切刀上下两片咬合不正,纸板切不断的部位在机械力作用下带起撕裂的面瓦纸;③横切机瞬时加速调节不当,引起阻纸。
瓦楞纸板常见质量问题和产生原因及解决办法

修正瓦楞辊的贴合间隙 清理瓦楞表面异物
瓦楞辊贴合间隙大
• 修正瓦楞辊的贴合间隙
瓦画辊贴合间隙不平衡 •
导纸板位置不正、磨损或带
脏
瓦楞原纸含水水均衡
•
瓦楞原纸的张力太小
•
检查并修正或更换导纸 板
加大予热包角 适当调整张力控制
瓦楞纸板常见质量问题和产生原因及 解决办法
质量问题
平行度
• 瓦楞辊表面带脏
• 清理瓦楞辊,保持干净
• 导纸板位置不正,、带脏或磨损 • 检查、修正、清理或更换导
纸板
• 涂胶辊、浮动辊间隙不当
• 调整二者的贴合间隙
• 粘合剂质量不好
• 检查并重新制作粘合剂
• 瓦楞原纸含水不均衡张力小 • 适当予热并加大张力控制
• 过纸天桥张力不均衡
瓦楞纸板常见质量问题和产生原因及 解决办法
1. 面纸予热包角太大 2. 里纸予热包角太小 3. 过纸天桥堆积过多 4. 单面机涂胶量过大
5.涂胶仙涂胶量偏少
6.车速太低
7.双面机热板温度高
8.重量辊施加压力过大
解决办法
• 减少包角、降低予热 • 增大包角、加强予热 • 减少过纸天桥的堆积 • 适当控制单面机的着胶
量 • 适当增大涂胶机的着胶
7.双面机热板温度高 8.重量辊施加压力过大
解决办法
• 减少包角、降低予热
• 增大包角、加强予热 • 减少过纸天桥的堆积 • 适当控制单面机的着胶
量 • 适当增大涂胶机的着胶
量 • 根据实际运行质量,适
当提高车速
• 提高车速或人为降低热 板
• 适当投放重量辊
PPT文档演模板
瓦楞纸板常见质量问题和产生原因及 解决办法
瓦楞纸板及印刷不良问题产生的原因及解决办法(PPT54页)

二
双面机加热板温度不够
部
车速太快
分
脱
原纸含水量太高
胶
胶黏剂质量不好
胶黏剂附着量小
解决办法
检查冷凝水排放装置和 供水气压是否符合要求 检查供气部分是否有故障
适当降低车速 加大预热或换纸
修正胶黏剂质量 加大胶黏剂附着量
产生原因
单面机涂胶量过小
涂胶机涂胶量过大
一
双面机加热温度不够
横
向
面纸预热包角太小 、里纸预热包角太大
原因
滚筒压力不足 墨层太厚
油墨黏度太高
解决办法
适量调高滚筒之间的压力 调薄墨层
适当稀释油墨
四 印面油 墨粉化 ,摩擦 后容易 脱落, 墨色浑 浊
原因
油墨过稀 油墨变质
解决办法
减少稀释溶剂,增加油墨浓度 给油墨增添树脂剂量,增强 油墨黏性和粘接附着性能
换掉变质的油墨
原因
五
印
印版上有旧墨堆积
上
翘
输送桥架纸板过多堆积
输送桥架输出瓦 楞纸板张力过大
解决办法
适当加大张力系 统的控制力度
适当预热 检查、修整传动装 置,保证运转正常
减少堆积量
适当减少纸板输出张力控制
产生原因
传送带运行压力不够
四
纵
输送桥架输出瓦 楞纸板张力不够
向
向
下
面纸含水量不均衡
翘
面纸张力太大
解决办法
适当加大张力系 统的控制力度
调整前色干燥速度、尽 量在后一色印刷前干燥
问题
供墨系统清洁不彻底
七 墨 杠
水墨本身含有未完 全溶解的颜料颗粒
解决办法
更换产品时将供墨系统彻底 清洁干净,注意避免前后两 种产品颜色相差很远且使用 同一印刷色组的大面积印刷
- 1、下载文档前请自行甄别文档内容的完整性,平台不提供额外的编辑、内容补充、找答案等附加服务。
- 2、"仅部分预览"的文档,不可在线预览部分如存在完整性等问题,可反馈申请退款(可完整预览的文档不适用该条件!)。
- 3、如文档侵犯您的权益,请联系客服反馈,我们会尽快为您处理(人工客服工作时间:9:00-18:30)。
适当予热并加大张力控制
过纸天桥张力不均衡
楞倾斜
1.涂胶辊和浮动辊不平行
检查和修正二者的调整装置
2.双面机重量辊位置不当或压力大
适当控制重量辊的投放并检查平衡度
3.过纸天桥张力太大
减低控制器的张力
4.瓦楞原纸含水过高
加大予热器包角和双面机热量
5.瓦楞辊不平行
调整和修正瓦楞辊的平行度
调整二者之间的合理间隙
8.涂胶辊和浮动辊不平行
检查没压装置和机械调整系统
9.帆布带升降机构工作不正常
检查并排除热量不足的因素
10.热量不够,淀粉过早凝合
适当减少予热
11.双面机重量辊放置不当
调整和重置重量辊
12.粘合剂形成团块,上胶不匀
解决粘合剂的质量
横向向下翘曲
1.涂胶机涂胶量过小
适当加大涂胶机着胶量
加大过纸天桥的张力控制系统,增大或减小张力
9.瓦楞原纸张力过大
减小张力系统的摩擦
10.面纸、芯纸、瓦原纸含水不均衡
适当予热或更换面纸、芯纸、瓦楞原纸
楞损伤
1.瓦楞原纸质量不好
更换瓦楞原纸
2.瓦楞辊磨损
简易修复或更换瓦楞辊
3.瓦楞辊贴合间隙太小
修正和调整瓦楞辊的贴合间隙
4.导纸板磨损、带脏、位置不当
清理脏物、调整位置或更换导纸板
切断长度不稳定
1.过纸天桥张力控制太大
适度降低过纸天桥物输出张力,减少堆积
2.面纸的张力太大
适度降低面纸的张力
3.双面机对单面瓦楞纸板的牵引力不足
检查和修正引纸部位的故障,帆布带的张力
4.车速忽快忽慢,不稳定
保持正常、稳定的车速
5.横切机输纸压力不够
增加输纸辊的配重
纵切刀口出现过重裂痕
1.上、下刀刃重合深度不适
6.瓦楞辊贴合间隙太小
修正瓦楞辊的贴合间隙
楞不均
1.瓦楞辊表面有脏物
清理瓦楞表面异物
2.瓦楞辊贴合间隙大
修正瓦楞辊的贴合间隙
3.瓦画辊贴合间隙不平衡
检查并修正或更换导纸板
4.导纸板位置不正、磨损或带脏
加大予热包角
5.瓦楞原纸含水水均衡
适当调整张力控制
6.瓦楞原纸的张力太小
塌楞
1.瓦楞辊表面不清洁
清除瓦楞辊表面脏物
2.里纸予热包角太小
增大包角、加强予热
3.过纸天桥堆积过多
减少过纸天桥的堆积
4.单面机涂胶量过大
适当控制单面机的着胶量
5.涂胶仙涂胶量偏少
适当增大涂胶机的着胶量
6.车速太低
根据实际运行质量,适当提高车速
7.双面机热板温度高
提高车速或人为降低热板
8.重量辊施加压力过大
适当投放重量辊
纵向向上翘曲
1.原纸张力不够
5.粘合剂附着量小
调整合理间隙,增大粘合剂附着量
6.车速太快
适当降低车速
面纸折皱
1.原纸本身质量问题
1.喷水增湿或加大张力以及更换原纸
2.原纸含水不均衡
2.加大予热包角或喷水增湿
3.原纸两端边过紧
3.适当加大张力和予热
高低楞
瓦楞辊表面温度不均衡
检查冷凝水排放情况
瓦楞辊磨损
更换瓦楞辊或简单的用油石修复
5.运行中的机械性破坏
检查并修处长机械性不当造成的损伤
楞折皱
1.瓦楞辊平行度不好
修正或调整瓦楞辊的平行度
2.瓦楞辊磨损
简易修处长或更换瓦楞辊
3.瓦楞原纸含水不均衡
适当予热,使其保持平均的含水
4.瓦楞原纸质量不好
更换瓦楞原纸
5.瓦楞原纸张力太小
适当调整张力控制系统,加大张力
厚度不够
1.涂胶辊和浮动辊间隙过小
适度控制张力系统
面纸压破裂
1.双面机热量过大
降低热量,提高车速
2.原纸质量不好
更换原纸
3.上、下压线轮相对位置不正
修正和调整上、下压线轮位置
4.原纸含水太小
喷淋、减小予热
5.压线轮间隙调整不合适,间隙过小,压线太深,使面纸承压过大;间隙过大,压线太轻,在弯折时,面纸受力过大而破裂
按照瓦楞纸板的结构和使用材质,适度调整咬合间隙
适当加大张力系统的控制力度
2.原纸含水不均衡
适当予热或喷水后予热
3.予热包角调控不平衡
检查并修整传动装置,保证运转平行
4.过纸天桥过多堆积
减少堆积
5.过纸天桥输出瓦楞纸板张力过大
适当减小输出张力控制
纵向向下翘曲
1.帆布带运行压力不够
检查并修正帆布带的张力
2.过纸天桥图形出瓦楞纸板疑义力不够
适当增大输出张力控制
瓦楞纸板常见质量问题的产生原因及解决办法
质量问题
产生原因
解决办法
粘合不好
1.面纸张力过大
调整刹车装置,减小磨擦力
2.面纸、芯纸水份大
加大予热力度或调纸
3.粘合剂附着量小
调整二者之间的合理间隙楞辊与涂胶辊不平行
修正粘合剂的质量
6.不好
修正导纸板位置,清理脏物
7.导纸板位置不正或有脏物
3.面纸含水不均衡
喷水并适当予热
4.面纸张力太大
减小对面纸的张力控制
S形翘曲
原纸水分分布不均衡
喷淋或予控制
瓦楞辊使用不同幅面的纸,表面磨损不均匀
简易修复或更换瓦楞辊
环境湿度太大
增大予热器包角、降低车速、提高粘合剂质量
涂胶辊和浮动辊不平行
适当修正和调整
双向翘曲
原纸水分分布不均衡
喷淋或予热控制
帆布带横向张力不均衡
2.瓦楞辊热量不均衡
检查冷凝水排放情况
3.粘合剂粘度不够
调整粘合剂的制作,检查各种原料质量
4.粘合剂附着量太大
修正和调整涂胶间隙、减小着胶量
5.帆布带污损、透气性不好
清洗和烘干帆布带
6.双面机热板表面有异物
清除异物,保持表面清净
7.导纸板带脏、磨损或位置不正
检查和修正导纸板、清理脏物或换导纸板
8.涂胶辊和单面瓦楞纸板在运行中的速度不适应
8.乞讨楞辊贴合间隙不合适
修正瓦楞辊的贴合间隙,检查相关部件
9.瓦楞辊表面温度不够
检查冷凝水放和供气系统
10.瓦楞辊表面有脏物
清除异物保持干净
11.导纸板位置不正、磨损或有脏物
修正位置或更换导纸板、清理脏物
12.过纸天桥堆积过多、张力太大
减少堆积、控制降低输出张力
13.瓦楞原纸质量不好
更换瓦楞原纸
14.瓦楞原纸张力过大
瓦楞辊运转不正常
检查两端轴承情况和传动部分
瓦楞辊贴合间隙不一致
调整和修正瓦楞辊的贴合间隙
瓦楞辊平行度不一致
检查和修正上、下瓦楞辊的平行度
瓦楞辊表面带脏
清理瓦楞辊,保持干净
导纸板位置不正,、带脏或磨损
检查、修正、清理或更换导纸板
涂胶辊、浮动辊间隙不当
调整二者的贴合间隙
粘合剂质量不好
检查并重新制作粘合剂
保持清洁和干燥,适当调整张力系统
里、面原纸张力过大或过小
加紧或放松刹车、控制张力
予热器浮动辊工作不正常
检查或修正运转部分零件、保证水平工作
过纸天桥、予热器、涂胶机中心线不正
如安装失误应重新修正、部分偏斜加以调整
部分脱胶
1.粘合剂质量不好
改善粘合剂质量
2.粘合剂附着量小
调整合理间隙,增大粘合剂着量
3.瓦楞辊表面温度不均衡或温度不够
适度调整,保证正常的工作间隙
2.涂胶机涂胶量大,使楞峰变形
减少涂胶量
3.双面机热板或帆布带有异物
清理杂物,保持洁净
4.帆布带污损,透气性不好,湿度大
清洁帆布带并保持干燥
5.重量辊数量使用不当
合理使用重量辊
6.横切机输纸辊不平行或重力大
适度减小输纸辊重力,调整平行度
7.瓦楞辊磨损,楞高度不够
更换瓦楞辊
按瓦楞纸板的结构和用料适度调整
2.上、下刀刃贴合间隙不适
保证正常的贴合间隙
3.瓦楞纸板含水过高或过低
根据实际情况加大予热或减少予热
4.原纸质量不好
更换原纸
5.刀具磨损
更换园刀
6.纵切机运转不平稳
检查和修正轴承、套框及有关的部件
2.双面机热板温度不够
增加热板温度
3.过纸天桥单面瓦楞纸板含水不够
适当啬过纸天桥单面瓦楞纸板的堆积,保持一定的水份
4.三重予热器加热过量
减小予热包角
5.单面机涂胶量过小
增大单面机的施胶量
6.车速太快
适当减你车速
7.单面瓦楞纸板运行张力不够
调整张力控制系统、增大阻力
横向向上翘曲
1.面纸予热包角太大
减少包角、降低予热
检查冷凝水排放装置和供气气压是否符合要求
4.双面机热板温度不够
检查供气部分是否有故障
5.原纸含水高
加大予热或换纸
6.车速太快
适当降低车速
双向翘曲
1.粘合剂粘度低
增加粘合剂浓度
2.双面机带脏,热量不够
清理双面机并检查供气系统
3.原纸含水高
加在予热或更换原纸
4.纵切机分切园刀调整不当
调整分切园刀的咬合和贴合间隙