轴承脂润滑计算公式
补充润滑脂加注量计算公式

补充润滑脂加注量计算公式润滑脂在机械设备中起着非常重要的作用,它能够减少摩擦、防止磨损、防止腐蚀,并且能够起到密封和防尘的作用。
然而,为了确保润滑脂能够发挥最佳的效果,我们需要正确地计算润滑脂的加注量。
本文将介绍补充润滑脂加注量计算公式及其相关知识。
首先,我们需要了解润滑脂的加注量计算公式。
润滑脂的加注量计算公式如下:润滑脂加注量 = (0.005 ×π× d × L) ÷ 1000。
其中,d为轴承内径(mm),L为轴承长度(mm),π为圆周率(3.14),0.005为润滑脂的加注量系数。
通过这个公式,我们可以根据轴承的内径和长度来计算出润滑脂的加注量。
这样可以确保润滑脂能够充分润滑轴承,并且不会造成过多的浪费。
接下来,我们来详细了解一下这个公式中的各个参数。
首先是润滑脂的加注量系数。
这个系数通常是由润滑脂的厂家提供的,它是根据润滑脂的性能和使用条件来确定的。
不同类型的润滑脂可能有不同的加注量系数,因此在计算润滑脂的加注量时,一定要使用正确的系数。
接下来是轴承的内径和长度。
这两个参数是确定润滑脂加注量的关键。
内径和长度越大,需要的润滑脂加注量也就越大。
因此,在使用润滑脂加注量计算公式时,一定要准确地测量轴承的内径和长度。
除了这个基本的计算公式外,还有一些其他因素也会影响润滑脂的加注量。
例如,轴承的转速、工作温度、工作环境等都会对润滑脂的加注量产生影响。
在实际使用中,我们还需要根据这些因素来对润滑脂的加注量进行修正。
此外,润滑脂的加注量还会受到润滑脂的老化和污染的影响。
当润滑脂老化或者受到污染时,它的润滑性能就会下降,这时就需要增加润滑脂的加注量,以确保轴承能够得到充分的润滑。
在实际使用中,我们通常会根据轴承的使用情况来确定润滑脂的加注量。
例如,对于高速运转的轴承,我们可能会增加润滑脂的加注量,以确保轴承在高速运转时能够得到充分的润滑。
而对于长时间停止运转的轴承,我们可能会减少润滑脂的加注量,以避免润滑脂的浪费。
轴承加油脂量计算公式
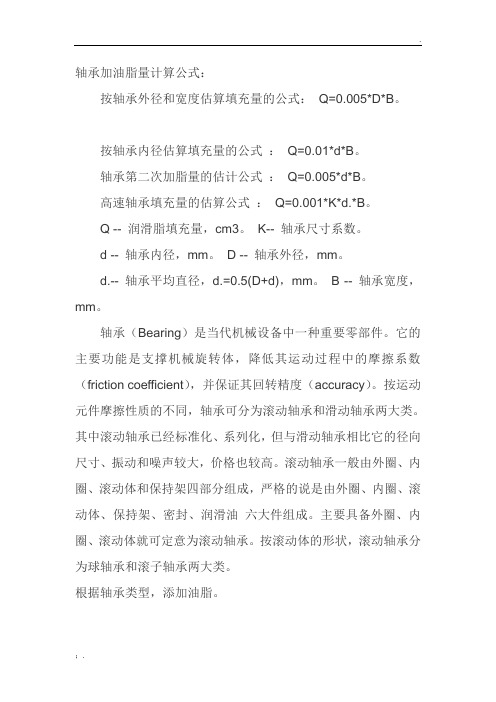
轴承加油脂量计算公式:
按轴承外径和宽度估算填充量的公式:Q=0.005*D*B。
按轴承内径估算填充量的公式:Q=0.01*d*B。
轴承第二次加脂量的估计公式:Q=0.005*d*B。
高速轴承填充量的估算公式:Q=0.001*K*d.*B。
Q -- 润滑脂填充量,cm3。
K-- 轴承尺寸系数。
d -- 轴承内径,mm。
D -- 轴承外径,mm。
d.-- 轴承平均直径,d.=0.5(D+d),mm。
B -- 轴承宽度,mm。
轴承(Bearing)是当代机械设备中一种重要零部件。
它的主要功能是支撑机械旋转体,降低其运动过程中的摩擦系数(friction coefficient),并保证其回转精度(accuracy)。
按运动元件摩擦性质的不同,轴承可分为滚动轴承和滑动轴承两大类。
其中滚动轴承已经标准化、系列化,但与滑动轴承相比它的径向尺寸、振动和噪声较大,价格也较高。
滚动轴承一般由外圈、内圈、滚动体和保持架四部分组成,严格的说是由外圈、内圈、滚动体、保持架、密封、润滑油六大件组成。
主要具备外圈、内圈、滚动体就可定意为滚动轴承。
按滚动体的形状,滚动轴承分为球轴承和滚子轴承两大类。
根据轴承类型,添加油脂。
加脂量过大,会使摩擦力矩增大,温度升高,漏油污染环境,耗脂量增大;而加脂量过少,则不能获得可靠润滑而发生干摩擦。
一般来讲,适宜的加脂量为轴承内总空隙体积的:
零类轴承25%——40%;
精密轴承15%——25%
是指空间的百分比。
轴承润滑油量计算及供油方式设计

轴承润滑油量计算滚动轴承润滑所需的油量在很大程度上取决于轴承类型、供油系统设计、润滑油类型等因素。
很难给出一个适合任何情况,具有广泛适用性的简单明了的公式。
具有油液自动传输功能的轴承(如角接触球轴承)所需油量大于不具有油液自动传输功能的轴承(如双列圆柱滚子轴承)所需油量。
尤其当速度性系数(n.dm)值较大时,其差异更明显。
通过大量实验,供油量Q的粗略计算公式如下:Q=WdB 式中Q——供油量,mm3/h W——系数,0.01mm/h d——轴承内径,mm B——轴承宽度,mm 然而,实际供油量还要在此数值基础上扩大4~20倍。
为了获得最佳润滑效果,还需通过实验来修正供油量多少。
4.2 供油方式设计对于高速旋转的轴承,为了可靠地将润滑油送入轴承内部,应十分重视供油方式(如喷嘴形式、安装位置等)的设计。
轴承润滑方式完全取决于轴承类型和配置方式(图4a)。
对单列轴承而言,最佳润滑方式为从一边进入轴承内部。
喷嘴孔应与内环齐平,不能指向保持架。
尤其当轴承自身吸排油方向不易确定时(如角接触球轴承),润滑油必须按上述方向进入轴承内部。
若条件许可,润滑油最好经过一个特制喷管后再进入轴承内部。
喷管长度取决于轴承大小,直径为0.5~1.0mm。
也允许把润滑油送到轴承外圈处(图4b)。
在这种情况下,要注意察看润滑油是否进入了钢球与外圈之间形成的压力区域。
对双列轴承而言,润滑油必须从与外圈滚道边齐平的地方喷入轴承内部,以对轴承充分润滑。
当轴承外径介于150~280mm时,需要再增加一个喷嘴。
此外,为了防止在轴承底部形成油渣沉淀,需要安装一个泄油管,其长度大于5mm。
为了满足现代机床高速主轴对润滑系统的要求,对油-气集中润滑系统的各个参数还要作进一步详细而精确的研究。
这是因为:润滑油类型、润滑方法、润滑量以及轴承类型、轴承配置等因素均对轴承转速提高有着决定作用。
润滑油计算公式

润滑油计算公式润滑油在机械设备中起着非常重要的作用,它能够减少摩擦、防止磨损、冷却和密封等。
因此,正确选择润滑油的类型和用量对于机械设备的正常运行和寿命具有至关重要的意义。
在实际应用中,我们需要根据设备的工作条件和润滑要求来计算润滑油的用量。
下面我们将介绍润滑油计算的基本公式和方法。
润滑油计算的基本公式为:润滑油用量 = (轴承容积 + 润滑油容积) ×润滑油更换倍率。
其中,轴承容积是指轴承内的润滑油容积,通常由设备制造商提供;润滑油容积是指设备中需要加注的润滑油总容积;润滑油更换倍率是指润滑油在使用过程中的消耗倍率,通常由设备的工作条件和使用频率来确定。
在实际应用中,我们可以根据设备的工作条件和润滑要求来确定轴承容积和润滑油容积,然后结合润滑油更换倍率来计算润滑油的用量。
下面我们将通过一个实例来详细介绍润滑油计算的具体步骤。
假设某设备的轴承容积为100ml,润滑油容积为200ml,润滑油更换倍率为0.2,现在我们需要计算该设备每次加注润滑油的用量。
首先,我们需要计算出润滑油的用量,根据上述公式,润滑油用量 = (轴承容积 + 润滑油容积) ×润滑油更换倍率 = (100ml + 200ml) × 0.2 = 60ml。
因此,该设备每次加注润滑油的用量为60ml。
除了以上的基本公式外,润滑油的用量还受到设备的工作条件、使用频率、润滑油的品牌和类型等因素的影响。
在实际应用中,我们需要根据具体的情况来确定润滑油的用量,并且在使用过程中进行适当的调整。
另外,润滑油的使用和管理也是非常重要的,正确的使用和管理能够延长设备的使用寿命、提高工作效率、降低维护成本。
因此,在使用润滑油时,我们需要注意以下几点:1. 根据设备的工作条件和润滑要求来选择合适的润滑油品牌和类型;2. 确保润滑油的质量符合相关标准,并且定期进行检测和更换;3. 根据设备的使用频率和工作条件来确定润滑油的更换周期;4. 对于不同类型的设备,需要采用不同的润滑方法和管理措施。
滚动轴承摩擦力矩发热量及油量计算

滚动轴承摩擦力矩发热量及油量计算
油润滑所需油量的运算
1、摩擦力矩的估算公式
Pd M μ5.0=
式中
M : 摩擦力矩,Nmm
μ : 轴承的摩擦系数
P : 当量动负荷,N
d : 轴承公称内径,mm
2、摩擦力矩的精确运算公式:
Mdrag Mseal Msl Mrr M +++=
式中
M : 总摩擦力矩, Nmm
Mrr : 滚动摩擦力矩,Nmm
Msl : 滑动摩擦力矩,Nmm
Mseal : 密封件的摩擦力矩,Nmm
Mdrag: 由于拖曳缺失、涡流和飞溅等导致的摩擦力矩,Nmm
3、轴承的摩擦缺失在轴承内部几乎全部变为热量,因而致使轴承温度升高,轴承的发热量能够用以下公式进行运算:
Mn Q 41005.1-⨯=
式中
Q : 发热量,kW
M : 摩擦力矩,Nmm
n : 轴承转速,r/min
4、循环油润滑及喷油润滑所需油量运算公式
T
r c dnP G ∆⋅⋅⋅⨯=-601088.14μ 式中
G : 所需油量,L/min
μ : 摩擦系数,
d : 轴承公称内径,mm
n : 轴承转速,r/min
P : 轴承当量动负荷,N
c : 油的比热,kJ/kg ℃
r : 油的密度,g/cm 3
△T : 油的温升,℃
上式运算得到的是发热量全部通过油带走时所需的油量,未考虑其余散热因素。
一样来说,实际油量约为以上运算油量的1/2-2/3。
但散热量随着使用机械及使用条件而有所不同,因此宜先以运算油量的2/3进行运转,通过测量轴承温度和进、排油温度逐步减小油量,直至确定最佳油量。
附表:各类轴承的摩擦系数(参考)。
轴承干油润滑时耗油量的计算
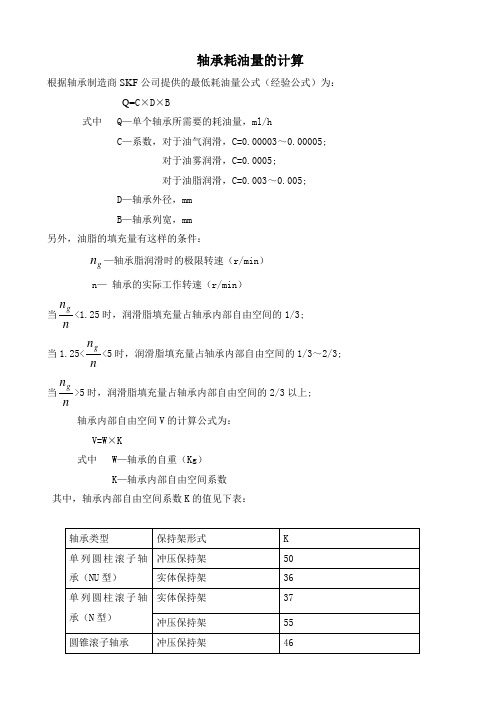
轴承耗油量的计算根据轴承制造商SKF 公司提供的最低耗油量公式(经验公式)为:Q=C ×D ×B式中 Q —单个轴承所需要的耗油量,ml/hC —系数,对于油气润滑,C=0.00003~0.00005;对于油雾润滑,C=0.0005;对于油脂润滑,C=0.003~0.005;D —轴承外径,mmB —轴承列宽,mm另外,油脂的填充量有这样的条件:g n —轴承脂润滑时的极限转速(r/min )n — 轴承的实际工作转速(r/min ) 当n n g<1.25时,润滑脂填充量占轴承内部自由空间的1/3;当1.25<n n g<5时,润滑脂填充量占轴承内部自由空间的1/3~2/3; 当n n g>5时,润滑脂填充量占轴承内部自由空间的2/3以上;轴承内部自由空间V 的计算公式为:V=W ×K式中 W —轴承的自重(Kg )K —轴承内部自由空间系数其中,轴承内部自由空间系数K 的值见下表:举例说明:参数为95/145×24的深沟球轴承,实际工作转速为800~2000 r/min轴承内径为95mm ,则内径代号为19,查手册得到型号为6019系列,油脂润滑时的极限转速为4000 r/min ,重量为1.15Kg,查上表得,K=61,所以,轴承内部自由空间V=WK=1.15×61=70.15mlnn g=4000/(800~2000)=2~5, 故1.25<n n g <5 所以润滑脂填充量Q=V ×(1/3~2/3)=23.4~46.8ml而由轴承制造商SKF 公司提供的最低耗油量得:m i n Q =C ×D ×B=0.005×145×24=17.4ml/h。
轴承的计算公式.
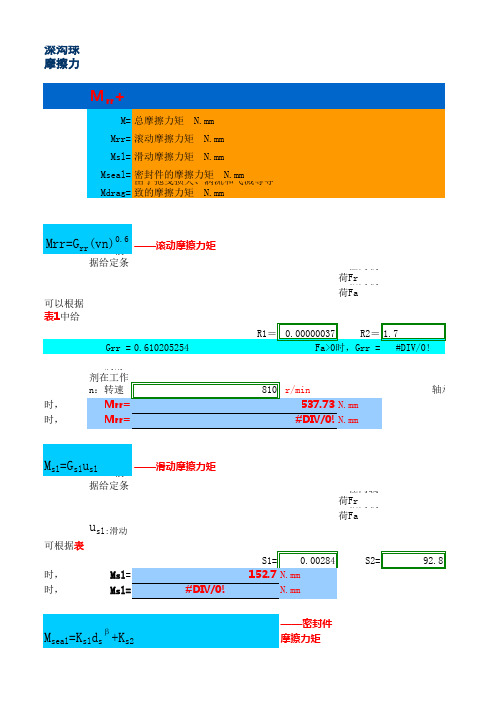
NR=
242.19713 W
Fa=0时
NR=
如果冷却系数(指轴承与环境温度之间每一度温差所带走的热量)是已知数,则可用以下公式粗略估算轴
∆T=N_R/W_s
∆T:温升 ℃
N_R:功率损耗 W
W_S:冷却系数
20
Δ T=
12.10986 ℃ Fa=0时
Δ T=
管方向,只取正值
10000 N 0N
117.5 mm
深沟球摩擦力矩的准确计算,要考虑四个不同导致摩擦的因素:
M=Mrr+Msl+Mseal+Mdrag
M= 总摩擦力矩 N.mm Mrr= 滚动摩擦力矩 N.mm Msl= 滑动摩擦力矩 N.mm Mseal= 密封件的摩擦力矩 N.mm Mdrag= 由于拖曳损失、涡流和飞溅等导致的摩擦力矩 N.mm
轴承额定动载荷C0=
100 mm2/s 76500 N
10000 N 0N
油);0.1(以传动液润滑)
摩擦系数Usl:
0.04
2.25 2
0.00017
1
列球轴承常数:
3.1
75
160
滚动摩擦的切入发热和贫油回填效应的
.28 v^0.64 )
油回填常数,脂润滑为: 0.00000006
2847.70 N.mm #DIV/0! N.mm
轴向载荷Fa
usl:滑动摩擦系数,当润滑条件良好,可取以下值:0.05(矿物油);0.04(合成油);0.1(以传动液润滑)
Gsl的值可根据表1中给出的公式计算,几何常数S则可从表2中找到
当Fa=0时, Msl=
S1= 0.00284
S2=
152.7 N.mm
轴承的计算公式
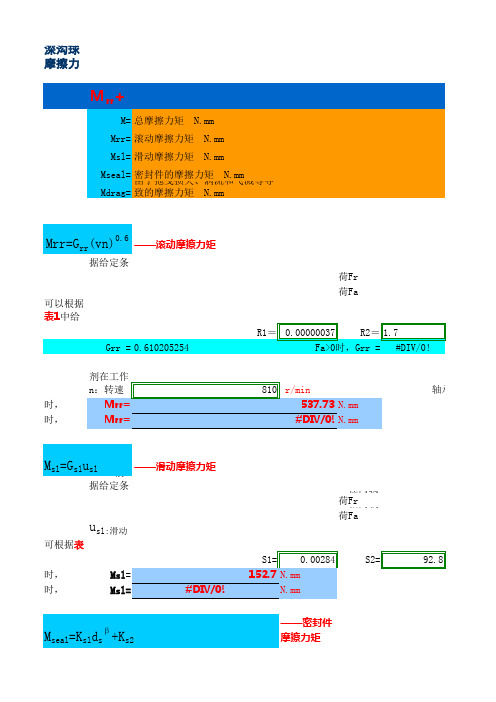
M= Mrr+
M= 总摩擦力矩 N.mm
Mrr= 滚动摩擦力矩 N.mm
Msl= 滑动摩擦力矩 N.mm
Mseal= 密由封于件拖的曳摩损擦失力、矩 涡流和N.飞mm溅等导 Mdrag= 致的摩擦力矩 N.mm
Mrr=Grr(Grvrn:)根0.6 ——滚动摩擦力矩
据给定条
Grr的值 可以根据 表1中给
10000 N 0N
摩擦系数Usl:
0.04
2.25 2
0.00017
1 3.1
75 160
滚动摩擦的切入发热和贫油回填效应的
.28 v^0.64 )
0.00000006
2847.70 N.mm #DIV/0! N.mm
Fa=0时 Fa>0时
W Fa〉0
#DIV/0! 时
111
#DIV/0!
℃ Fa〉0 时
21.41 N.mm
iKzr=w=单球列
和d=双轴列承球 内D=径轴尺承 外径尺
在新的摩擦模型中引入了减少系数 和 ,分别用来考虑滚动摩擦的切入发
切影入响发:热
∅_ish ∅_rs
减少系
数:——
∅_ish=1/(1+1.84×〖10〗^(-9) 〖(n d_m )〗^1.28 v^0.64 )
0.923646
贫油回填 减少系 数:——
∅_rs=1/(e^(K_rs vn(d+D)) √(K_z/(2(D-d))))
3.663692474
贫油回填常
Krs= 数,脂润滑
将以上的 其它效应
=
功率 损M耗=∅_ish ∅_rs
因轴承的 摩擦而造
如果冷却 系数(指
- 1、下载文档前请自行甄别文档内容的完整性,平台不提供额外的编辑、内容补充、找答案等附加服务。
- 2、"仅部分预览"的文档,不可在线预览部分如存在完整性等问题,可反馈申请退款(可完整预览的文档不适用该条件!)。
- 3、如文档侵犯您的权益,请联系客服反馈,我们会尽快为您处理(人工客服工作时间:9:00-18:30)。
轴承脂润滑计算公式
SKF计算公式:(适用性广)
SKF轴承补充油脂量:
1、从轴承侧面补充油脂的适量可从公式Gp = 0,005 D B得到,(手动润滑)
2、从轴承外圈或内圈的环形槽和注油孔补充油脂的适量可从Gp = 0,002 D B得到。
(自动润滑)
式中
Gp = 补充时加入的油脂量,单位为克
D = 轴承外径,mm
B = 轴承总宽度(推力轴承使用总高度H),mm
SKF轴承补充时间:
纵向单位:tf 运行小时
横向单位:Abf
其中:A=ndm n=转速r/min dm=轴承平均直径0.5(d+D)mm
bf=轴承系数,取决于轴承种类和载荷条件载荷比C/P,见表2;
再润滑间隔时间t f是一个估计值,对于运行温度为摄氏70度、使用高质量锂增稠剂/矿物油油脂的轴承比较有效。
福伊特计算公式(适用于高速或较高速的轴承润滑)
quantity of grease:
M = (D x B x 0,002)[g] (自动润滑)
D= outside diameter of bearing B= width of bearing 周期为168小时。