转炉双渣法炼钢少渣冶炼
转炉双渣法炼钢少渣冶炼

3、少渣冶炼的关键技术
▪ 图7和图8分别为氧枪枪位和炉渣FeO含量 对脱磷阶段结束[P]含量的影响,可以看到, 采用较低枪位和高强度供氧,由于熔池搅拌 显著加强,尽管炉渣FeO含量降低至9.5%附 近,脱磷效率非但没有降低,反而有较大幅 度的提高。
第十七页,课件共有50页
2、双渣法少渣冶炼原理
▪ ②终渣碱度高、自由CaO含量高而不外排;排出的前期 渣中自由CaO含量低(前期造的低碱度渣 ),而节省了 CaO用量 ;
▪ ③传统工艺出钢后会有钢水留在炉内,一部分会随炉 渣倒出,而采用少渣冶炼工艺,吹炼终点不倒渣,因 而可以提高钢水收得率。
第十八页,课件共有50页
1、转炉双渣法少渣冶炼现状
▪ 马钢在120t转炉上进行少渣冶炼,用生白云石代替 部分石灰和镁球。
▪ 钢研总院研究对300t转炉的前期渣打水后返回使用, 每炉次加入3~6t返回渣,每炉可节约0.7~1t石灰。
▪ 鞍钢鲅鱼圈研究含磷钢冶炼,不加石灰而只加轻烧白 云石。
第十三页,课件共有50页
2、双渣法少渣冶炼原理
第四页,课件共有50页
1、转炉双渣法少渣冶炼现状
▪ 上个世纪的50--70年代,中国一些转炉钢厂在铁水硅、 磷含量高时,为了降低石灰消耗,减少吹炼过程喷溅, 改善脱磷效果,曾采用过出钢后留渣或“留渣--双渣” 炼钢工艺。后来,随着高炉生产水平提高(铁水硅含量 降低),高磷铁矿石用量减少(铁水磷含量降低),以 及顾忌留渣造成铁水喷溅的安全隐患,留渣或“留渣-双渣”炼钢工艺就不推荐采用了。
第七页,课件共有50页
1、转炉双渣法少渣冶炼现状
▪ 已经发表文章的单位(不完全统计)及生产转炉的 容量:
▪ 首钢京唐300t转炉 ;鞍钢260吨转炉 ;首钢迁安210t转炉; 沙钢180t转炉;酒钢120t转炉;日照120t转炉;马钢120t 转炉 ;莱钢120t转炉;首钢首秦100t转炉;湘钢80t转炉; 首钢长治80t转炉
转炉双渣法炼钢少渣冶炼.

基本反映了该炼钢方法的技术操作特点。从已发 表的报道来看,值得注意的有以下2点。
(1)转炉容量:80t~300t,表明少渣冶炼生产
的规模大
(2)讨论内容:操作技术;经济效益;前期渣
特点,形成了完整的工艺方法
1、转炉双渣法少渣冶炼现状
已经发表文章的单位(不完全统计)及生产转炉 的容量:
双渣法之所以能够在吹炼前期造渣倒掉,吹炼中
期再造渣,减少了总渣量也能够达到单渣法吹炼 大渣量的那种脱磷效果,原因就在于利用了脱磷 与温度的关系和基本原理。
2、双渣法少渣冶炼原理
由(2)式可知,温度对脱磷反应的影响非常显著, 当温度由1680℃降低至1350℃时,脱磷反应平衡
常数可大幅度增加6个数量级。少渣冶炼的基本
③传统工艺出钢后会有钢水留在炉内,一部分会
替部分石灰和镁球。 钢研总院研究对300t转炉的前期渣打水后返回使 用,每炉次加入3~6t返回渣,每炉可节约0.7~1t 石灰。
鞍钢鲅鱼圈研究含磷钢冶炼,不加石灰而只加轻
烧白云石。
2、双渣法少渣冶炼原理
双渣法过去主要用来冶炼高硅、高磷铁水,或者
在铁水硅、磷不高时要冶炼低磷钢或超低磷钢。
用的相关情况,在大分、八幡、室兰、君
津等钢厂采用,产钢量占新日铁总产钢量
55%左右,转炉炼钢石灰消 耗 减少了40%
以上。
1、转炉双渣法少渣冶炼现状
MUCR工艺将转炉冶炼分为2个阶段,在
第1阶段主要进行脱硅、脱磷,结束后倒 出部分炉渣,然后进行第2阶段吹炼,吹 炼结束后出钢但将炉渣保持在炉内,下一 炉在炉内留渣情况下装入废钢、铁水,然 后进行第1和第2阶段吹炼,并以此循环 往复。
某炼钢分厂转炉双渣工艺培训

05
转炉双渣工艺经济效益分 析
成本分析
原材料成本
转炉双渣工艺需要使用更多的原材料 ,如铁矿石、废钢等,增加了生产成 本。
能耗成本
人工成本
转炉双渣工艺需要更多的操作人员和 技术支持,增加了人工成本。
转炉双渣工艺需要消耗更多的能源, 如电力、燃气等,增加了能源成本。
效益分析
提高产量
转炉双渣工艺能够提高钢的产量 和质量,从而提高企业的生产效
泛应用,降低能耗和污染物排放。
新型炉衬材料
03
采用新型耐火材料和复合炉衬技术,提高炉龄和减少维护成本
。
市场发展前景
全球市场需求持续增长
随着全球经济的发展和钢铁行业的复苏,转炉双渣工艺市场将保 持稳定增长。
市场竞争格局变化
新兴市场和技术创新将改变转炉双渣工艺市场竞争格局,为优势企 业提供更多机会。
绿色环保标准推动市场发展
03
转炉双渣工艺安全注意事 项
安全防护措施
01
02
03
穿戴防护服
所有操作人员必须穿戴符 合要求的防护服,包括但 不限于安全帽、防护眼镜 、口罩等。
定期检查设备
对所有设备进行定期检查 ,确保设备处于良好状态 ,无安全隐患。
设置安全警示标识
在危险区域和设备上设置 明显的安全警示标识,提 醒操作人员注意安全。
长期效益
虽然转炉双渣工艺的投资回报周期较长,但长期来看,该工艺能够 为企业带来稳定的收益和竞争优势。
06
转炉双渣工艺未来发展展 望
技术发展趋势
自动化与智能化
01
随着工业4.0和智能制造的推进,转炉双渣工艺将实现自动化和
智能化,提高生产效率和产品质量。
氧气转炉“留渣+双渣”炼钢工艺技术分析

渣进 行 固化 处理 ,在 完成 固化 工作 之后 , 即 可将 铁水 与废 钢装 入其 中 ,开展 脱磷 吹 炼 ,这 一步 骤完 成后 即可 开展 倒渣 工作 , 并 步入 到脱 碳环 节 中 ,结 束 出钢与 留渣 工 作 ,循 环往 复 。该种 工艺 利用 了热 力学 原 理 ,在 炼终 点 ,温度 非 常高 ,此 时钢水 中 基 本上 没有 磷 ,不会 进行 脱磷 反应 ,在炉 中 留出一 定量 的终 渣 。在 进行 下一 吹炼 工 作 时 ,温度 也是 较低 的 ,但是 钢水 中 已经 有 大量 的磷 ,此 时炉 渣有 开始 能够 脱磷 , 在 吹炼 工作 的进 行下 ,在 温度 升高 之后 , 即 可在脱 磷 不利 的状 态下 将炉 渣倒 出 ,再 进行 脱碳 吹炼 ,这一 工艺 将上 炉 留渣原 理 充分 利 用起来 ,能够 减少 白云石和 石灰 的
中 ,一般 不会 由于倒 渣损 失钢 铁料 量 ,该 之 后 ,必 须要及 时将 炉 渣倒 出 ,而采 用快
种工 艺 的优势是 非常 显著 的。 速 足量倒 渣工 艺 即可完成 这一 目的。 2 “ 留渣 + 双渣 ”炼 钢 工艺 开 发 与 使 2 - 3 S G R S 3 2 艺磷 控制 方式 。与一 般 的
氧气转炉“留渣+ 双渣” 炼钢工艺技术研究
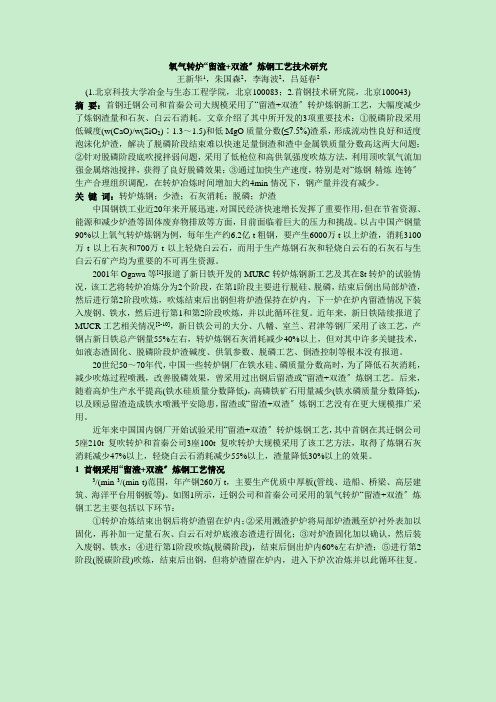
氧气转炉“留渣+双渣〞炼钢工艺技术研究王新华1,朱国森2,李海波2,吕延春2(1.北京科技大学冶金与生态工程学院,北京100083;2.首钢技术研究院,北京100043)摘要:首钢迁钢公司和首秦公司大规模采用了“留渣+双渣〞转炉炼钢新工艺,大幅度减少了炼钢渣量和石灰、白云石消耗。
文章介绍了其中所开发的3项重要技术:①脱磷阶段采用低碱度(w(CaO)/w(SiO2)∶1.3~1.5)和低MgO质量分数(≤7.5%)渣系,形成流动性良好和适度泡沫化炉渣,解决了脱磷阶段结束难以快速足量倒渣和渣中金属铁质量分数高这两大问题;②针对脱磷阶段底吹搅拌弱问题,采用了低枪位和高供氧强度吹炼方法,利用顶吹氧气流加强金属熔池搅拌,获得了良好脱磷效果;③通过加快生产速度,特别是对“炼钢-精炼-连铸〞生产合理组织调配,在转炉冶炼时间增加大约4min情况下,钢产量并没有减少。
关键词:转炉炼钢;少渣;石灰消耗;脱磷;炉渣中国钢铁工业近20年来开展迅速,对国民经济快速增长发挥了重要作用,但在节省资源、能源和减少炉渣等固体废弃物排放等方面,目前面临着巨大的压力和挑战。
以占中国产钢量90%以上氧气转炉炼钢为例,每年生产约6.2亿t粗钢,要产生6000万t以上炉渣,消耗3100万t以上石灰和700万t以上轻烧白云石,而用于生产炼钢石灰和轻烧白云石的石灰石与生白云石矿产均为重要的不可再生资源。
2001年Ogawa等[1]报道了新日铁开发的MURC转炉炼钢新工艺及其在8t转炉的试验情况,该工艺将转炉冶炼分为2个阶段,在第1阶段主要进行脱硅、脱磷,结束后倒出局部炉渣,然后进行第2阶段吹炼,吹炼结束后出钢但将炉渣保持在炉内,下一炉在炉内留渣情况下装入废钢、铁水,然后进行第1和第2阶段吹炼,并以此循环往复。
近年来,新日铁陆续报道了MUCR工艺相关情况[2-10],新日铁公司的大分、八幡、室兰、君津等钢厂采用了该工艺,产钢占新日铁总产钢量55%左右,转炉炼钢石灰消耗减少40%以上,但对其中许多关键技术,如液态渣固化、脱磷阶段炉渣碱度、供氧参数、脱磷工艺、倒渣控制等根本没有报道。
转炉少渣高效生产(江苏沙钢集团)(1)

沙钢集团
2 . 江苏沙钢集团宏发炼钢生产工艺流程
铁水车
KR脱硫
转炉
LF
RH
外发
销售
精整 室内堆放 轧制
连铸
火焰切割
沙钢集团
3. 江苏沙钢集团宏发炼钢厂转炉少渣工艺
转炉冶炼主要可分为单渣法、双渣法、双联法3种工艺。 单渣法的石灰消耗与铁水初始硅含量关系密切 ,一般在 30kg/t~50kg/t;双渣法冶炼通常在铁水硅含量较高的情况下 采用,转炉辅料消耗较高;双联法虽然能够降低原辅料的消 耗,但是需要额外增加专门用于脱磷的转炉。 沙钢集团宏发炼钢厂转炉的常规冶炼工艺为单渣留渣 法,冶炼超低磷钢种时采用双渣法。常规吹炼工艺的转炉平 均石灰消耗为 26kg/t,吹炼终点总渣量平均为95kg/t,简单 的工艺优化很难进一步降低其石灰消耗。为此,我厂与沙钢 研究院一道共同开发了转炉少渣冶炼工艺。
40 30 20 10 0 0
20
Dolomite,kg/t
Lime,kg/t
15 10 5 0
常规工艺 少渣工艺 试生产
平均22kg/t 平均17kg/t
0.25 0.5 %Si
常规工艺 少渣工艺 试生产
0.75
1
0
0.25
0.5 %Si
0.75
1
沙钢集团
6. 推广应用
0.005 50 50 0.01 100
枪位控制
230 220 210 200
Si<0.25% Si=0.25%--0.4% Si>0.4%
根据铁水成分,我 厂设计了三种枪位 控 制 模 式 :
Si<0.25%低硅模式 Si=0.25%--0.40%中硅 模式 Si>0.40%高硅模式 前期 高枪位吹炼主要 为了快速成渣,利用 前期低温优势最大效 率的去磷。
8-转炉“留渣-双渣”少渣炼钢工艺实践
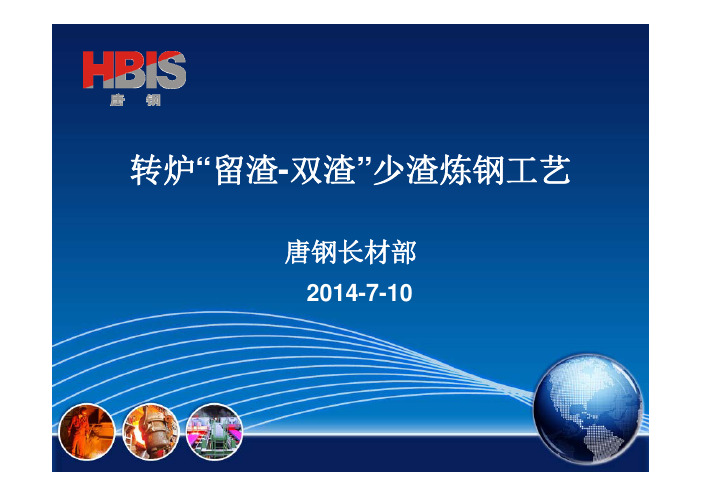
“留渣-双渣”工艺示意图
3.转炉脱磷影响因素
3.脱磷的基本原理
2[P]+5(FeO)+4(CaO)=4CaO·P2O5+5[Fe]
a 4CaO P2 O 5 a a
2 p 5 F eO
Kp
a
4 C aO
% 4CaO P2 O 5 4CaO P O 4 5 4 % P 2 f P2 % F e O 5 F e O % CaO C aO
演变:首钢公司从2011年开始,在首钢首秦和迁钢分别连续试验单
转炉“留渣-双渣”操作,取得较好的效果,目前首钢集团首钢长治, 首钢水钢均推广应用“留渣-双渣”少渣炼钢操作工艺,工艺相对成熟 。
1. 大幅度减少炼钢石灰、白云石等渣料消耗和炼钢渣量; 2. 可以利用出钢后炉渣的物理热,预热废钢; 3. 炼钢终渣含Tfe:15~25%,渣量减少可以降低钢铁料消耗; 4. 双渣倒渣的炉渣主要为脱磷阶段低碱度渣,自由CaO含量低, 可以简化炉渣处理; 5. 常规转炉出钢后留在炉内钢水随炉渣倒出,采用“留渣-少渣”工 艺终点少倒渣、出钢后不倒渣,可以提高钢水收得率。
FeO%
H11Mn2SiA
3A14306-1 3A14306-2 3B14615-1 3B14615-2 3C14935-1 3C14935-2 3A14301-1 3A14301-2 3B14603-1 3B14603-2 3B14612-1 3B14612-1
1 冶炼周期影响
类别 加料 脱磷期 双渣 脱碳期 终点 加废钢 兑铁时间 前期吹炼时间 氮气刹渣 倒渣时间 中后期吹炼 拉碳、补吹时间 等待终点成分 出钢时间 溅渣时间 总冶炼周期 留渣-双渣 1.7 2.4 4.5 2.1 3 8.8 2 1 2.5 2 30 单渣法 1.7 2.2 4.5 / / 8.7 2 1 2.5 2.5 25.1
转炉炼钢少渣冶炼技术的探索实践

转炉炼钢少渣冶炼技术的探索实践陈志平;王多刚;虞大俊;左康林【摘要】介绍转炉少渣冶炼、炉渣热循环利用实践.可分两个阶段,脱碳出钢留渣、冶炼中期脱磷倒渣留渣与脱碳出钢留渣同时进行(留渣+双渣).脱碳留渣冶炼,通过出钢后倒渣、调渣过程控制,抑制留渣造成吹炼前期的喷溅.留渣冶炼使吨钢石灰消耗降低28.6%.“留渣+双渣”试验,控制转炉前期炉渣碱度及全铁,选择合适脱磷渣倒炉点及温度,保证前期渣脱磷率和泡沫化,最终前期脱磷率大于60%,排渣率大于50%.“留渣+双渣”技术,吨钢石灰消耗降低46.9%.【期刊名称】《宝钢技术》【年(卷),期】2014(000)006【总页数】4页(P17-20)【关键词】转炉冶炼;少渣炼钢;炉渣热循环技术;脱磷【作者】陈志平;王多刚;虞大俊;左康林【作者单位】上海梅山钢铁股份有限公司技术中心,江苏南京210039;上海梅山钢铁股份有限公司技术中心,江苏南京210039;上海梅山钢铁股份有限公司炼钢厂,江苏南京210039;上海梅山钢铁股份有限公司炼钢厂,江苏南京210039【正文语种】中文【中图分类】TF723.3高效、低成本、低排放生产是炼钢技术发展主要方向之一[1]。
20世纪90年代,新日铁提出单转炉实现少渣冶炼MURC[2](MUlti-Refining Converter)技术。
近年来,北京科技大学与首钢开发SGRS(Slag Generation Reduced Steel making)少渣炼钢工艺技术。
以往少渣冶炼技术概念,主要通过铁水预处理“三脱”技术,使有害元素去除负荷前移,减少转炉渣量[3]。
现指的少渣冶炼技术与上述不同,从热力学条件看,脱磷与脱碳存在矛盾。
首钢曹妃甸炼钢流程采取了新的技术,脱磷炉与脱碳炉分离,抓住转炉冶炼的关键任务的特点,原来1座转炉冶炼功能由2座转炉采取串联作业实现[4],脱磷炉半钢再用于脱碳炉,脱碳炉炉渣用于脱磷炉,实际上是钢水与炉渣在传质转移,体现高效与精细分工。
- 1、下载文档前请自行甄别文档内容的完整性,平台不提供额外的编辑、内容补充、找答案等附加服务。
- 2、"仅部分预览"的文档,不可在线预览部分如存在完整性等问题,可反馈申请退款(可完整预览的文档不适用该条件!)。
- 3、如文档侵犯您的权益,请联系客服反馈,我们会尽快为您处理(人工客服工作时间:9:00-18:30)。
1、转炉双渣法少渣冶炼现状
对于转炉吹炼前期渣的操作控制也进行了研究,
北京科技大学的王新华等在首钢迁安210t转炉上 试验,脱磷阶段采用低碱度(R=1.3~1.5)和低
MgO质量分数(≤7.5%)的渣系,能够形成流动
性良好和适度泡沫化的炉渣,解决了脱磷阶段结
束难以快速足量倒渣和渣中金属铁含量高这两大
3、少渣冶炼的关键技术
图7和图8分别为氧枪枪位和炉渣FeO含量
对脱磷阶段结束[P]含量的影响,可以看到, 采用较低枪位和高强度供氧,由于熔池搅 拌显著加强,尽管炉渣FeO含量降低至 9.5%附近,脱磷效率非但没有降低,反而 有较大幅度的提高。
3、少渣冶炼的关键技术
采用上述高效脱磷工艺,在铁水磷含量为
溅,引发重大安全事故。迁钢公司曾采用加入多
量石灰、白云石或废钢直接冷却对液态炉渣进行 固化的方法,但发现存在以下问题: ①如石灰、白云石加入量多,造成脱磷阶段炉渣 碱度和MgO含量过高,导致倒渣困难;
3、少渣冶炼的关键技术
②如采用废钢对液态渣进行冷却固化,由于废钢
尺寸不均衡,常发生炉内废钢“搭棚”情况,炉 底液态渣不能被充分固化,存在安全隐患。通过
稳定运行。
3、少渣冶炼的关键技术
为了使炉渣具有良好的流动性,还须对MgO含量
进行严格控制。后面的图为210t转炉脱磷阶段结
束时倒渣量与渣中MgO含量的关系,当将MgO含
量控制在7.5%以下时,倒渣量可在8t以上,能够
满足少渣冶炼工艺稳定运行的要求,为此规定对 脱磷阶段炉渣MgO含量按低于7.5%控制。这一 MgO含量控制目标低于常规工艺初期渣的MgO含 量控制目标值,采用后并未发现对炉龄有不利影
③传统工艺出钢后会有钢水留在炉内,一部分会
随炉渣倒出,而采用少渣冶炼工艺,吹炼终点不
倒渣,因而可以提高钢水收得率。
2、双渣法少渣冶炼原理
根据我们最近对前期渣和终点渣中微区P分布的研 究结果可以确认,不同温度下炉渣中微区磷含量 的最高点与Ca含量的关系不同,前期低温渣中,
微区里磷含量的最高点在Ca=15%的附近,而终点
0.075%左右情况下,脱磷阶段结束可将[P] 含量降低至0.029%左右,脱碳阶段终点钢 水[P]含量最低可脱除至0.006%,平均为 0.0096%,能够满足除少数超低磷钢种外绝 大多数钢种对[P]含量的控制要求。
3、少渣冶炼的关键技术
液态终渣快速固化技术 采用少渣冶炼工艺,对上炉留在炉内的液态渣必 须加以固化,才能确保装入铁水时不发生激烈喷
渣中含磷量远低于前期低温时的平衡值,且含有
大量的氧化铁,从而在下一炉吹炼初期低温下有 较高的脱磷能力。在操作上,当下一炉温度上升 至对脱磷不利之前,将炉渣部分倒出,等于倒出 了一部分磷,再加入渣料造渣进行第2阶段吹炼
到终点,炉内的磷远远少于原有的量。
2、双渣法少渣冶炼原理
由于上一炉的炉渣可以被下一炉再利用,因而能
替部分石灰和镁球。 钢研总院研究对300t转炉的前期渣打水后返回使 用,每炉次加入3~6t返回渣,每炉可节约0.7~1t 石灰。
鞍钢鲅鱼圈研究含磷钢冶炼,不加石灰而只加轻
烧白云石。
2、双渣法少渣冶炼原理
双渣法过去主要用来冶炼高硅、高磷铁水,或者
在铁水硅、磷不高时要冶炼低磷钢或超低磷钢。
3、少渣冶炼的关键技术
2)针对低枪位、高供氧速率吹炼引起的渣中
FeO含量降低的问题,增加了铁矿石加入量和加 入批次,以在加强熔池搅拌同时,使渣中能够保
持足够的FeO含量。
3)采用添加小粒石灰,合理控制炉渣碱度和
MgO含量(防止碱度、 MgO含量过高)等方法,
加快脱磷阶段渣料熔化,促进脱磷反应。
国内已经发表的工业试验和生产的报告有20余篇,
基本反映了该炼钢方法的技术操作特点。从已发 表的报道来看,值得注意的有以下2点。
(1)转炉容量:80t~300t,表明少渣冶炼生产
的规模大
(2)讨论内容:操作技术;经济效益;前期渣
特点,形成了完整的工艺方法
1、转炉双渣法少渣冶炼现状
已经发表文章的单位(不完全统计)及生产转炉 的容量:
量的炉渣具有重要意义。如倒渣量不足,会出现:①
炉内渣量逐炉蓄积,碱度不断增加,倒渣愈加困难的 情况,最后导致少渣冶炼无法接续,循环被迫停止; ②炉渣流动性会逐炉变差,渣中裹入金属铁珠量大, 钢铁料消耗增加;③倒渣困难会增加冶炼时间,炉内 渣量波动也会对吹炼过程控制稳定性造成很大影响。
3、少渣冶炼的关键技术
原理便是利用了转炉冶炼前期温度低这一有利于 脱磷反应的热力学条件,将上炉终渣用于下炉吹 炼初期脱磷,并在温度上升至对脱磷不利之前, 将炉渣部分倒出,然后再加入少量渣料造渣进行 第2阶段吹炼进一步脱磷。
2、双渣法少渣冶炼原理
上一炉的终渣之所以能够用于下一炉的前期脱磷,
是由于上一炉终渣在高温下的脱磷能力低,以致
造成终点钢水[P]不合格而必须进行后吹、补吹。
3、少渣冶炼的关键技术
采用少渣冶炼工艺在吹炼前期脱磷阶段高效脱磷 的关键是:①加强金属熔池搅拌,促进熔池内部 [P]向渣/铁界面传输;②通过调整供氧或加入铁矿
石、氧化铁皮等提高渣中氧化铁活度。
为此开发了脱磷阶段高效脱磷技术,主要特点是: 1)氧枪枪位较常规工艺吹炼前期枪位降低 100~200mm,供氧强度控制在3.0m3/(min· t) 以上。
渣中,微区里磷含量的最高点在Ca=35%的附近。 可见前期渣必须要把渣碱度减低到1.5左右才可能 最大程度地吸收铁水中的磷。
前期渣和终点渣中各微区的P含量 与其微区中Ca含量的关系
转炉钢渣背散射图像中的微区形象
3、少渣冶炼的关键技术
一 炉
的
操 作 过 程
3、少渣冶炼的关键技术
脱磷阶段炉渣流动性控制与足量倒渣 采用少渣冶炼工艺,脱磷阶段结束后能否快速倒出足
鞍钢在260吨转炉上进行少渣冶炼,前期放
渣时熔渣碱度控制在1.5~2.0,终渣碱度控 制在2.8~3.2,效果是石灰单耗小于25kg/t 钢,轻烧白云石单耗小于15 kg/t钢。 本钢研究得出,少渣冶炼的前期脱磷率可 高达50~60%。
1、转炉双渣法少渣冶炼现状
马钢在120t转炉上进行少渣冶炼,用生白云石代
响。
3、少渣冶炼的关键技术
采用了以上所述较低碱度和MgO含量渣系 后,基本上解决了倒渣这一影响少渣冶炼 工艺稳定运行的关键难题。迁钢210t转炉脱 磷阶段倒渣量在6.0~12.5t(铁水[Si]含量变 化影响),倒渣时间在4.0~5.0min;首秦
100t转炉脱磷阶段倒渣量在4.0~8.0t,倒渣
问题。
1、转炉双渣法少渣冶炼现状
北科大何肖飞等对少渣炼钢的前期渣进行
了研究,发现当前期渣碱度在1.2~1.8范围 内时,其半球点温度基本上在1380度以下, 渣中游离CaO含量在0.7%左右。 迁钢210t转炉的前期渣倒渣量可达8t,首秦 100t转炉的前期渣倒渣量可达可达5t。
1、转炉双渣法少渣冶炼现状
大量试验,开发了将溅渣护炉与炉渣固化相结合
的液态终渣快速固化工艺,其主要特点为:
转炉双渣法炼钢少渣冶炼
北京科技大学 李宏
目录
1、转炉双渣法少渣冶炼现状
2、双渣法少渣冶炼原理
3、少渣冶炼的关键技术
4、锰在渣-钢间的分配及钢水
残锰最大化
1、转炉双渣法少渣冶炼现状
2001年新日铁发表文章介绍了其开发的少 渣冶炼新工艺--- MUCR转炉炼钢工艺。
近年来,新日铁陆续报道了MUCR工艺应
双渣法之所以能够在吹炼前期造渣倒掉,吹炼中
期再造渣,减少了总渣量也能够达到单渣法吹炼 大渣量的那种脱磷效果,原因就在于利用了脱磷 与温度的关系和基本原理。
2、双渣法少渣冶炼原理
由(2)式可知,温度对脱磷反应的影响非常显著, 当温度由1680℃降低至1350℃时,脱磷反应平衡
常数可大幅度增加6个数量级。少渣冶炼的基本
15%,为使炉渣全部熔化(均匀液相),炉渣 二元碱度须控制在1.3以下。考虑到渣中还含有 MnO、MgO等能够适当扩大该三元系液相区范
围,因此为使炉渣充分熔化,炉渣碱度不应超
过1.5。
R=1.5左右
3、少渣冶炼的关键技术
后面的图为1400℃下CaO-SiO2-FeO系黏度
值(Pa· s),可以看到,在脱磷阶段炉渣 FeO含量在9%~15%范围内,当碱度在 0.82~1.5范围时,炉渣具有较低的黏度 (0.2~0.4 Pa· s ),而当碱度超过1.5时, 等黏度线变得密集,黏度值随碱度增加而 快速提高,炉渣流动性显著变差。
够大幅度减少炼钢石灰、白云石等原材料消耗和 炼钢渣的产出量。
由以上介绍可知少渣冶炼有如下3个优点:
①减少了转炉排出渣量,就减排了渣中的铁,因
此可以降低钢铁料消耗;但没有减少排磷量,前
期渣中排出。
2、双渣法少渣冶炼原理
②终渣碱度高、自由CaO含量高而不外排;排出
的前期渣中自由CaO含量低(前期造的低碱度 渣 ),而节省了CaO用量 ;
3、少渣冶炼的关键技术
后面的图为迁钢公司210t转炉和首秦公司 100t转炉采用少渣冶炼工艺,脱磷阶段结束 后倒渣量与炉渣碱度的关系。可以看到, 倒渣量随碱度降低而增加,当脱磷阶段炉 渣碱度控制在1.5左右时,迁钢210t转炉倒
渣量可大于8.0t,首秦100t转炉倒渣量可多
于5.0t,这个量能够保证少渣冶炼工艺顺利
能否快速倒出足量的脱磷炉渣,主要取
决于炉渣流动性控制,为此须做到:① 炉渣充分熔化,不含未溶石灰颗粒以及 MgO、2CaO· SiO2等高熔点析出相;② 炉渣具有较低的黏度;③适当提高脱磷 阶段温度。
3、少渣冶炼的关键技术