转炉留渣双渣操作生产实践
转炉双渣法炼钢少渣冶炼.

基本反映了该炼钢方法的技术操作特点。从已发 表的报道来看,值得注意的有以下2点。
(1)转炉容量:80t~300t,表明少渣冶炼生产
的规模大
(2)讨论内容:操作技术;经济效益;前期渣
特点,形成了完整的工艺方法
1、转炉双渣法少渣冶炼现状
已经发表文章的单位(不完全统计)及生产转炉 的容量:
双渣法之所以能够在吹炼前期造渣倒掉,吹炼中
期再造渣,减少了总渣量也能够达到单渣法吹炼 大渣量的那种脱磷效果,原因就在于利用了脱磷 与温度的关系和基本原理。
2、双渣法少渣冶炼原理
由(2)式可知,温度对脱磷反应的影响非常显著, 当温度由1680℃降低至1350℃时,脱磷反应平衡
常数可大幅度增加6个数量级。少渣冶炼的基本
③传统工艺出钢后会有钢水留在炉内,一部分会
替部分石灰和镁球。 钢研总院研究对300t转炉的前期渣打水后返回使 用,每炉次加入3~6t返回渣,每炉可节约0.7~1t 石灰。
鞍钢鲅鱼圈研究含磷钢冶炼,不加石灰而只加轻
烧白云石。
2、双渣法少渣冶炼原理
双渣法过去主要用来冶炼高硅、高磷铁水,或者
在铁水硅、磷不高时要冶炼低磷钢或超低磷钢。
用的相关情况,在大分、八幡、室兰、君
津等钢厂采用,产钢量占新日铁总产钢量
55%左右,转炉炼钢石灰消 耗 减少了40%
以上。
1、转炉双渣法少渣冶炼现状
MUCR工艺将转炉冶炼分为2个阶段,在
第1阶段主要进行脱硅、脱磷,结束后倒 出部分炉渣,然后进行第2阶段吹炼,吹 炼结束后出钢但将炉渣保持在炉内,下一 炉在炉内留渣情况下装入废钢、铁水,然 后进行第1和第2阶段吹炼,并以此循环 往复。
某炼钢分厂转炉双渣工艺培训

05
转炉双渣工艺经济效益分 析
成本分析
原材料成本
转炉双渣工艺需要使用更多的原材料 ,如铁矿石、废钢等,增加了生产成 本。
能耗成本
人工成本
转炉双渣工艺需要更多的操作人员和 技术支持,增加了人工成本。
转炉双渣工艺需要消耗更多的能源, 如电力、燃气等,增加了能源成本。
效益分析
提高产量
转炉双渣工艺能够提高钢的产量 和质量,从而提高企业的生产效
泛应用,降低能耗和污染物排放。
新型炉衬材料
03
采用新型耐火材料和复合炉衬技术,提高炉龄和减少维护成本
。
市场发展前景
全球市场需求持续增长
随着全球经济的发展和钢铁行业的复苏,转炉双渣工艺市场将保 持稳定增长。
市场竞争格局变化
新兴市场和技术创新将改变转炉双渣工艺市场竞争格局,为优势企 业提供更多机会。
绿色环保标准推动市场发展
03
转炉双渣工艺安全注意事 项
安全防护措施
01
02
03
穿戴防护服
所有操作人员必须穿戴符 合要求的防护服,包括但 不限于安全帽、防护眼镜 、口罩等。
定期检查设备
对所有设备进行定期检查 ,确保设备处于良好状态 ,无安全隐患。
设置安全警示标识
在危险区域和设备上设置 明显的安全警示标识,提 醒操作人员注意安全。
长期效益
虽然转炉双渣工艺的投资回报周期较长,但长期来看,该工艺能够 为企业带来稳定的收益和竞争优势。
06
转炉双渣工艺未来发展展 望
技术发展趋势
自动化与智能化
01
随着工业4.0和智能制造的推进,转炉双渣工艺将实现自动化和
智能化,提高生产效率和产品质量。
转炉炼钢双渣法操作探究
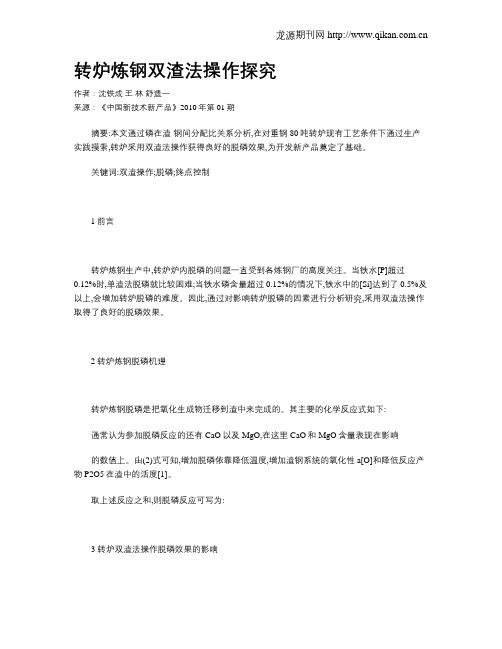
转炉炼钢双渣法操作探究作者:沈铁成王林舒遗一来源:《中国新技术新产品》2010年第01期摘要:本文通过磷在渣-钢间分配比关系分析,在对重钢80吨转炉现有工艺条件下通过生产实践摸索,转炉采用双渣法操作获得良好的脱磷效果,为开发新产品奠定了基础。
关键词:双渣操作;脱磷;终点控制1前言转炉炼钢生产中,转炉炉内脱磷的问题一直受到各炼钢厂的高度关注。
当铁水[P]超过0.12%时,单渣法脱磷就比较困难;当铁水磷含量超过0.12%的情况下,铁水中的[Si]达到了0.5%及以上,会增加转炉脱磷的难度。
因此,通过对影响转炉脱磷的因素进行分析研究,采用双渣法操作取得了良好的脱磷效果。
2转炉炼钢脱磷机理转炉炼钢脱磷是把氧化生成物迁移到渣中来完成的。
其主要的化学反应式如下:通常认为参加脱磷反应的还有CaO以及MgO,在这里CaO和MgO含量表现在影响的数值上。
由(2)式可知,增加脱磷依靠降低温度,增加渣钢系统的氧化性a[O]和降低反应产物P2O5在渣中的活度[1]。
取上述反应之和,则脱磷反应可写为:3 转炉双渣法操作脱磷效果的影响3.1 重钢双渣法操作的过程控制情况在保证前期炉渣尽快化好的前提下,一次倒渣前采用高碱度、高氧化性和低温度的方式。
但是由于铁水硅含量较高达到0.5%,造成一次倒渣时碱度较低、温度较高,见表1。
从实际倒渣情况来看,一次倒渣后仍有少部分未倒尽的炉渣,这就要求我们必须加强终点控制。
为此,终点按照脱磷热力学条件进行控制(终点炉渣成分及温度控制见表2),以此降低转炉回磷。
3.2 温度对磷在渣-钢间的分配比影响从脱磷反应的热力学条件可知,脱磷反应的平衡常数K越大,磷在渣-钢间的分配比Lp越大。
温度对Lp的影响是通过对K的作用实现的。
K随反应温度的降低而增大,即低温有利于脱磷,同时,低温还会导致降低,也有利于脱磷。
由表1、2所列数据作出的转炉终点温度对磷在渣-钢间的分配比LP的影响的理论和实际关系图如图1所示。
首钢转炉“留渣-双渣”炼钢工艺技术开发与应用
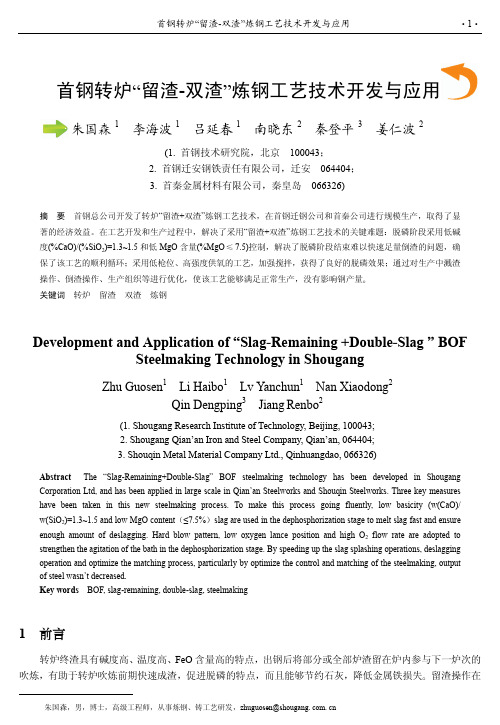
首钢转炉“留渣-双渣”炼钢工艺技术开发与应用朱国森1李海波1吕延春1南晓东2秦登平3姜仁波2(1. 首钢技术研究院,北京 100043;2. 首钢迁安钢铁责任有限公司,迁安 064404;3. 首秦金属材料有限公司,秦皇岛 066326)摘要首钢总公司开发了转炉“留渣+双渣”炼钢工艺技术,在首钢迁钢公司和首秦公司进行规模生产,取得了显著的经济效益。
在工艺开发和生产过程中,解决了采用“留渣+双渣”炼钢工艺技术的关键难题:脱磷阶段采用低碱度(%CaO)/(%SiO2)=1.3~1.5和低MgO含量(%MgO≤7.5)控制,解决了脱磷阶段结束难以快速足量倒渣的问题,确保了该工艺的顺利循环;采用低枪位、高强度供氧的工艺,加强搅拌,获得了良好的脱磷效果;通过对生产中溅渣操作、倒渣操作、生产组织等进行优化,使该工艺能够满足正常生产,没有影响钢产量。
关键词转炉留渣双渣炼钢Development and Application of “Slag-Remaining +Double-Slag ” BOFSteelmaking Technology in ShougangZhu Guosen1Li Haibo1 Lv Yanchun1 Nan Xiaodong2Qin Dengping3Jiang Renbo2(1. Shougang Research Institute of Technology, Beijing, 100043;2. Shougang Qian’an Iron and Steel Company, Qian’an, 064404;3. Shouqin Metal Material Company Ltd., Qinhuangdao, 066326)Abstract The “Slag-Remaining+Double-Slag” BOF steelmaking technology has been developed in Shougang Corporation Ltd, and has been applied in large scale in Qian’an Steelworks and Shouqin Steelworks. Three key measures have been taken in this new steelmaking process. To make this process going fluently, low basicity (w(CaO)/ w(SiO2)=1.3~1.5 and low MgO content(≤7.5%)slag are used in the dephosphorization stage to melt slag fast and ensure enough amount of deslagging. Hard blow pattern, low oxygen lance position and high O2 flow rate are adopted to strengthen the agitation of the bath in the dephosphorization stage. By speeding up the slag splashing operations, deslagging operation and optimize the matching process, particularly by optimize the control and matching of the steelmaking, output of steel wasn’t decreased.Key words BOF, slag-remaining, double-slag, steelmaking1前言转炉终渣具有碱度高、温度高、FeO含量高的特点,出钢后将部分或全部炉渣留在炉内参与下一炉次的吹炼,有助于转炉吹炼前期快速成渣,促进脱磷的特点,而且能够节约石灰,降低金属铁损失。
氧气转炉“留渣+ 双渣” 炼钢工艺技术研究
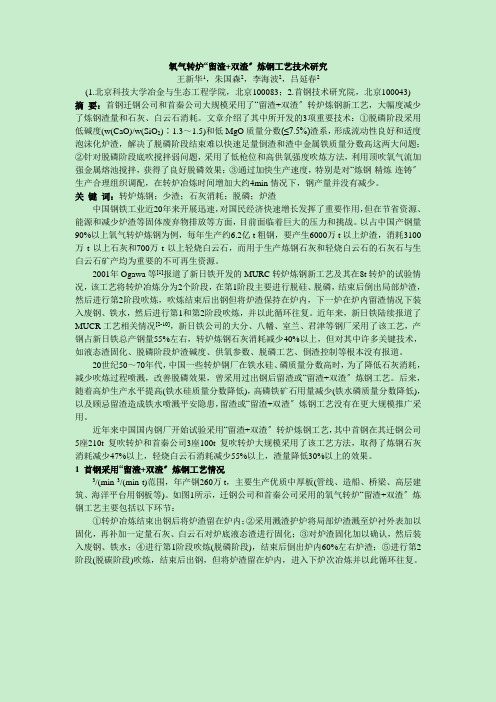
氧气转炉“留渣+双渣〞炼钢工艺技术研究王新华1,朱国森2,李海波2,吕延春2(1.北京科技大学冶金与生态工程学院,北京100083;2.首钢技术研究院,北京100043)摘要:首钢迁钢公司和首秦公司大规模采用了“留渣+双渣〞转炉炼钢新工艺,大幅度减少了炼钢渣量和石灰、白云石消耗。
文章介绍了其中所开发的3项重要技术:①脱磷阶段采用低碱度(w(CaO)/w(SiO2)∶1.3~1.5)和低MgO质量分数(≤7.5%)渣系,形成流动性良好和适度泡沫化炉渣,解决了脱磷阶段结束难以快速足量倒渣和渣中金属铁质量分数高这两大问题;②针对脱磷阶段底吹搅拌弱问题,采用了低枪位和高供氧强度吹炼方法,利用顶吹氧气流加强金属熔池搅拌,获得了良好脱磷效果;③通过加快生产速度,特别是对“炼钢-精炼-连铸〞生产合理组织调配,在转炉冶炼时间增加大约4min情况下,钢产量并没有减少。
关键词:转炉炼钢;少渣;石灰消耗;脱磷;炉渣中国钢铁工业近20年来开展迅速,对国民经济快速增长发挥了重要作用,但在节省资源、能源和减少炉渣等固体废弃物排放等方面,目前面临着巨大的压力和挑战。
以占中国产钢量90%以上氧气转炉炼钢为例,每年生产约6.2亿t粗钢,要产生6000万t以上炉渣,消耗3100万t以上石灰和700万t以上轻烧白云石,而用于生产炼钢石灰和轻烧白云石的石灰石与生白云石矿产均为重要的不可再生资源。
2001年Ogawa等[1]报道了新日铁开发的MURC转炉炼钢新工艺及其在8t转炉的试验情况,该工艺将转炉冶炼分为2个阶段,在第1阶段主要进行脱硅、脱磷,结束后倒出局部炉渣,然后进行第2阶段吹炼,吹炼结束后出钢但将炉渣保持在炉内,下一炉在炉内留渣情况下装入废钢、铁水,然后进行第1和第2阶段吹炼,并以此循环往复。
近年来,新日铁陆续报道了MUCR工艺相关情况[2-10],新日铁公司的大分、八幡、室兰、君津等钢厂采用了该工艺,产钢占新日铁总产钢量55%左右,转炉炼钢石灰消耗减少40%以上,但对其中许多关键技术,如液态渣固化、脱磷阶段炉渣碱度、供氧参数、脱磷工艺、倒渣控制等根本没有报道。
转炉双渣法炼钢少渣冶炼

1、转炉双渣法少渣冶炼现状
对于转炉吹炼前期渣的操作控制也进行了研究,
北京科技大学的王新华等在首钢迁安210t转炉上 试验,脱磷阶段采用低碱度(R=1.3~1.5)和低
MgO质量分数(≤7.5%)的渣系,能够形成流动
性良好和适度泡沫化的炉渣,解决了脱磷阶段结
束难以快速足量倒渣和渣中金属铁含量高这两大
3、少渣冶炼的关键技术
图7和图8分别为氧枪枪位和炉渣FeO含量
对脱磷阶段结束[P]含量的影响,可以看到, 采用较低枪位和高强度供氧,由于熔池搅 拌显著加强,尽管炉渣FeO含量降低至 9.5%附近,脱磷效率非但没有降低,反而 有较大幅度的提高。
3、少渣冶炼的关键技术
采用上述高效脱磷工艺,在铁水磷含量为
溅,引发重大安全事故。迁钢公司曾采用加入多
量石灰、白云石或废钢直接冷却对液态炉渣进行 固化的方法,但发现存在以下问题: ①如石灰、白云石加入量多,造成脱磷阶段炉渣 碱度和MgO含量过高,导致倒渣困难;
3、少渣冶炼的关键技术
②如采用废钢对液态渣进行冷却固化,由于废钢
尺寸不均衡,常发生炉内废钢“搭棚”情况,炉 底液态渣不能被充分固化,存在安全隐患。通过
稳定运行。
3、少渣冶炼的关键技术
为了使炉渣具有良好的流动性,还须对MgO含量
进行严格控制。后面的图为210t转炉脱磷阶段结
束时倒渣量与渣中MgO含量的关系,当将MgO含
量控制在7.5%以下时,倒渣量可在8t以上,能够
满足少渣冶炼工艺稳定运行的要求,为此规定对 脱磷阶段炉渣MgO含量按低于7.5%控制。这一 MgO含量控制目标低于常规工艺初期渣的MgO含 量控制目标值,采用后并未发现对炉龄有不利影
③传统工艺出钢后会有钢水留在炉内,一部分会
转炉留渣操作技术
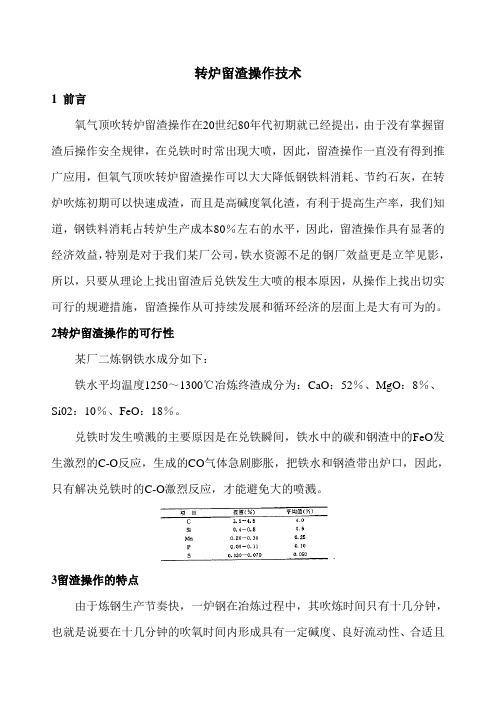
转炉留渣操作技术1 前言氧气顶吹转炉留渣操作在20世纪80年代初期就已经提出,由于没有掌握留渣后操作安全规律,在兑铁时时常出现大喷,因此,留渣操作一直没有得到推广应用,但氧气顶吹转炉留渣操作可以大大降低钢铁料消耗、节约石灰,在转炉吹炼初期可以快速成渣,而且是高碱度氧化渣,有利于提高生产率,我们知道,钢铁料消耗占转炉生产成本80%左右的水平,因此,留渣操作具有显著的经济效益,特别是对于我们某厂公司,铁水资源不足的钢厂效益更是立竿见影,所以,只要从理论上找出留渣后兑铁发生大喷的根本原因,从操作上找出切实可行的规避措施,留渣操作从可持续发展和循环经济的层面上是大有可为的。
2转炉留渣操作的可行性某厂二炼钢铁水成分如下:铁水平均温度1250~1300℃冶炼终渣成分为:CaO:52%、MgO:8%、Si02:10%、FeO:18%。
兑铁时发生喷溅的主要原因是在兑铁瞬间,铁水中的碳和钢渣中的FeO发生激烈的C-O反应,生成的CO气体急剧膨胀,把铁水和钢渣带出炉口,因此,只有解决兑铁时的C-O激烈反应,才能避免大的喷溅。
3留渣操作的特点由于炼钢生产节奏快,一炉钢在冶炼过程中,其吹炼时间只有十几分钟,也就是说要在十几分钟的吹氧时间内形成具有一定碱度、良好流动性、合适且TFe和MgO含量正常泡沫化的炉渣,以保证冶炼成分和温度同时双命中的钢水,并减少对炉衬的侵蚀,留渣操作贯穿于炼钢整个冶炼周期,主要是靠所留炉渣的物理热和炉渣化学性能,使其具有迅速参与反应、并促进前期炉渣的快速形成、提高去除P、S的效率、节省石灰用量。
3.1有利于去磷在氧气顶吹转炉中,磷的氧化是在炉渣-金属界面中进行的,其反应式为:生成的磷酸铁在高温下极其不稳定,它可以重新分解生成P2O5,而P2O5是不稳定的化合物,因此,仅靠生成P2O5。
不能去除磷,但P2O5是酸性化合物,若用碱性化合物与其结合生成稳定的化合物可以去除。
研究认为,在碱性渣中P2O5与CaO形成稳定的(CaO)x P2O5型的化合物,其中x为3或4,因此,操作中需加入石灰,使其生成稳定的化合物3CaO· P2O5。
复吹转炉双渣法生产低磷钢工艺实践

第30卷 第4期2008年8月四川冶金Sichuan M eta llurgy Vol .30 No .4Aug .,2008作者简介王海宝,6年月毕业于东北大学,现在首钢技术研究院从事炼钢工艺研究,助理工程师。
复吹转炉双渣法生产低磷钢工艺实践王海宝 徐莉 刘春明 宁林新(首钢技术研究院)【摘 要】 首钢第二炼钢厂通过优化复吹转炉双渣工艺制度,提高转炉前期脱磷效果,在无预处理脱磷设备条件下,可以生产钢材磷含量在0.010%以下的低磷钢,满足钢种对钢质洁净度的特殊要求。
【关键词】 低磷钢 双渣操作 钢质洁净度 复吹转炉PRAC T I C E O F PR ODUC ING LOW PHO SPHO RUSSTEEL B Y DO UB LE S LAG PROC ESS IN B O FW ang Haibao Xu L i L iu Chun m ing N ing L inxin(Shougang R es earch I n s ti t u t e of Techno l ogy)[Abstra ct] This artic le describes the practice of dephosphorization pr ocess by double slag m ethod inBO F .The result shows that even w ithout hot m eta l p retr eat m ent equipm ent we can reduce the phos phor us c ontent below 0.010%in ShougangNO.2stee l m aking plant and it m eets the require m ent of pur e steel .[Key words] low phos phorus steel,double slag p r oce ss,steel purity,BOF1 前言为了适应全球能源需要的扩大,今年来石油、天然气等海下资源开采量越来越大,而与之对应的海下环境却越来越恶劣,腐蚀性加强。
- 1、下载文档前请自行甄别文档内容的完整性,平台不提供额外的编辑、内容补充、找答案等附加服务。
- 2、"仅部分预览"的文档,不可在线预览部分如存在完整性等问题,可反馈申请退款(可完整预览的文档不适用该条件!)。
- 3、如文档侵犯您的权益,请联系客服反馈,我们会尽快为您处理(人工客服工作时间:9:00-18:30)。
转炉留渣双渣操作生产实践 吕凯辉 (福建三安钢铁有限公司炼钢厂,福建 泉州 362411) 摘 要:介绍了福建三安炼钢厂的转炉留渣双渣操作,以及留渣操作中安全问题的解决措施,分析了应用留渣双渣操作工艺的石灰消耗、钢铁料耗、转炉炉龄、氧耗、冶炼周期、脱磷等效果。通过优化顶底复吹转炉留渣双渣工艺制度,提高转炉前期脱磷效果,在无铁水预处理的设备条件下可以冶炼高铬铁水,满足了对钢的洁净度要求。 关 键 词:转炉;留渣;双渣;操作;实践 0 引言 留渣双渣操作是将转炉上炉部分或全部的高碱度、高氧化亚铁的渣留在炉中,然后在吹炼第一期结束时倒出来,重新造渣的操作模式[1]。该工艺具有高的碱度和比较高的∑(FeO)含量,对铁水具有一定的去磷和去硫能力,且本身还含有大量的物理热,将该种炉渣部分地甚至全部留在炉内可以显著加速下一炉初期渣的成渣过程,提高吹炼前期去磷率、节省石灰用量和提高炉子的热效率。但在留渣双渣操作中,必须特别注意防止兑铁水时产生严重喷溅[2]。福建三安炼钢厂研究了留渣操作喷溅和预防的机理,摸索出了1套留渣操作方法,取得了显著的经济效益。 1 福建三钢的留渣双渣操作 三安炼钢厂结合本厂的实际情况(高炉使用“印尼高铬矿”时,铁水铬含量高,由于铬能显著降低磷的活度,铁水中的铬氧化生成大量Cr2O3,使脱磷渣“硬化”,不利于脱磷反应的进行,转炉渣脱磷能力下降),实行的生产工艺为:“留渣双渣法”加“高拉后吹”的生产冶炼工艺,留渣双渣法工艺对于高磷高硅高铬等铁水的冶炼比较具有实用性,其工艺流程为:溅渣留渣→进废钢铁水→下枪冶炼→起泡沫渣时提枪倒渣下枪→脱碳升温出钢。该工艺和一般工艺的差异在于倒渣操作在吹炼中途进行,其原理是:在温度为1320~1420℃时,转炉冶炼脱磷脱硅效果较明显;而温度>1550℃时,转炉渣对于脱磷是反效果的,也即会回磷。所以在脱硅、脱磷操作基本完成后进行倒渣操作,能有效脱磷,不影响冶炼周期,可以降低转炉石灰消耗和钢铁料消耗。 脱磷的有利条件是低温、高碱度、高(FeO),所以脱磷主要在吹炼前期完成,中后期控制好化渣情况,避免炉渣返干,炉内要均匀升温。 2 几种造渣方法的对比 氧气转炉常用的造渣方法有4种:单渣法、双渣法、留渣法和留渣双渣法。 2.1 单渣法 在吹炼过程中只造1次渣,中途不倒渣、不扒渣,直到吹炼终点出钢。单渣操作工艺比较简单,吹炼时间短,劳动条件好,易于实现自动控制。正常情况下脱磷效率在80%左右,脱硫效率为30%~40%;第一批渣料是在开吹的同时加入,第二批渣料的加入时间是在硅锰氧化基本结束,第一批渣料基本化好,碳焰初起时加入。 2.2 双渣法 在吹炼中期倒出或扒除1/2~2/3炉渣,然后加入渣料重新造渣的方法为双渣操作。根据铁水成分和所炼钢种的要求,也可以多次倒炉倒渣造新渣。在铁水含硅较高,或含磷大于0.5%,或含硫并不高而吹炼优质钢,或吹炼中、高碳钢种时,都可以采用双渣操作。采用双渣操作可以在转炉内保持最小的渣量,同时又能达到最高的去除磷硫效率。双渣操作脱磷效率在90%以上,脱硫效率约45%。双渣操作会延长吹炼时间,增加热量损失,降低金属收得率,不利于自动控制,恶化劳动条件。 2.3 留渣法 将上炉终渣的一部分或全部留在炉内给下炉使用。终点熔渣的碱度高、温度高,并且有一定(TFe)含量,留到下一炉有利于初期渣尽早形成,并且能提高前期去除磷硫的效率,有利于保护炉衬,节省石灰用量。采用留渣操作时,在兑铁水前要先加石灰或者加废钢稠化冷凝熔渣,当炉内无液体渣时方可兑入铁水,以避免引发喷溅。 2.4 留渣双渣法 将上炉终点渣的一部分或全部留在炉内,然后在吹炼第一期结束时倒出来,重新造渣。留渣双渣法的终渣一般有高的碱度和比较高的∑(FeO)含量,对铁水具有一定的去磷和去硫能力,且本身还含有大量的物理热。将这种炉渣部分,甚至全部留在炉内,可以显著加速下一炉初期渣的成渣过程,提高吹炼前期去磷和去硫率,节省石灰用量和提高转炉的热效率。在这种留渣法中,要特别注意防止兑铁水时产生严重喷溅。 按照以上4种造渣模式的对比,铁水成分平均值:Si68%,Mn35%,P120%,S58%;温度1329℃,一倒双命中范围1600~1660,C≥0.10%,P≤0.030%;冶炼正常、喷溅少。表1为统计30炉4种留渣法的主要参数。 3 留渣双渣法的兑铁水操作 福建三安炼钢厂在留渣双渣操作中,特别注意防止兑铁水时产生严重喷溅。留渣双渣操作终渣中含有FeO成分,这种终渣留待下一炉,在兑入铁水时必会发生(FeO)+[C〗=[Fe]+CO;2(FeO)+[C]=2[Fe]+CO2的化学还原反应。若终渣中FeO含量高于25%,还原反应会更激烈,瞬间产生大量的气体,造成爆发性喷溅事故。因此,必须降低渣中FeO含量,而其中影响含量的因素有: (1)钢中碳—氧平衡规律。碳含量高,氧含量就低;碳含量低时,氧含量相应就高。 (2)钢水中余锰和氧之间的关系。在ω[c]<0.1%时,锰对氧化性的影响比较明显,余锰高氧含量就会降低。 (3)钢水温度高,则氧含量高。 (4)操作工艺对钢水的氧含量也有影响。高枪位、低氧压操作会增加钢水的氧含量,补吹会增加钢水中的氧含量,提枪前加烧结矿等调温会增加钢水中的氧含量。 稳定吹炼操作可以降低氧含量,如:提倡“高拉后吹法”和一倒“双命中”操作。吹炼以不“返干”、不喷溅、均匀升温、全程化渣、快速脱碳与脱硫为原则。由于留渣冶炼初期要求稍低枪位操作,渣中TFe含量高可快速脱除磷硫,并及时倒渣;吹炼中期,适当降低枪位控制合适(TFe)含量以防喷溅;吹炼后期最好降低枪位以减少渣中TFe含量,提高钢水收得率。 4 留渣双渣法的冶炼操作 (1)保持有效炉容比,合理控制转炉装入量,控制终渣的R=2.8~3.2,MgO=8%~l4%;确保炉底稳定,防止炉底大起大落,保持炉型正常减少喷溅。 (2)先加生铁块、废钢,然后将转炉前后摇动,使生铁块、废钢表面含碳物质与渣中FeO反应,降低留渣氧化性,再缓慢兑铁水;兑铁前必须要把渣子溅干和加炉底料,防止产生爆发性喷溅。 (3)控制氧枪的枪位,使炼钢过程得以平稳进行,解决炉渣喷溅问题。 ①开吹时,在点着火后要及时降枪以控制渣中(TFe),基本采取硬吹状态,前期吹炼时间大于4min、温度在1320~1420℃。由于留渣操作模式,可以得到流动性良好的炉渣,在获得较好脱磷效果的同时也易发生喷溅;如果吹炼在5min以上不需压渣,提枪摇炉倒渣尽可能地多倒富磷渣,防止冶炼后期回磷。 ②倒掉足够的富磷渣再下枪吹炼,此时要立刻加入第二批料以防止下枪冶炼时渣中(TFe)过高,产生大喷溅现象。 ③在吹炼中期,由于碳的激烈氧化,(TFe)被大量消耗,熔渣的矿物组成发生了变化,由2FeO2SiO2→CaO2FeO2SiO2→2CaO2SiO2,熔点升高,石灰的渣化有些停滞,就会出现“返干”现象。在处理炉渣“返干”或加速终点渣形成时,不要加入过量的矿石,或用过高的枪位吹炼,避免(TFe)积聚。 ④终点适时降枪,降枪过早熔池碳含量还较高,碳的氧化速度迅速加快,也会产生大喷;炉役前期炉膛小,同时温度又低,要注意适时降枪,避免TFe含量过高,引起喷溅;补炉后炉衬温度偏低,前期温度随之降低,要注意及时降枪,控制渣中(TFe)含量,以免喷溅。 ⑤吹炼中发生喷溅就不能轻易降枪,因为降枪后碳氧反应更加激烈,会加剧喷溅;应适当提枪迅速压枪,这样可缓和碳氧反应和降低熔池升温速度,再借助于氧射流的冲击吹开熔渣,有利于气体的排出。 ⑥在炉温很高时,可以在提枪的同时适当加一些石灰稠化熔渣,有时对抑制喷溅也有些作用,也可加压渣剂减少喷溅。此外,适当降低氧流量也能减弱喷溅强度。 (4)改进化渣工艺,在保证前期可以点着火的同时减少首批料加入量。通过提前成渣,将泡沫渣的高峰期前移,与脱碳时刻错开以便提枪摇炉倒渣;后批料要在二次下枪时立刻加入,防止喷溅;在脱碳期到达之前,降低供氧强度,然后再将其平缓地恢复到正常值;变枪变压吹氧,保证全程化渣;加强底吹搅拌,提高脱磷脱碳效率;吹炼终期采用高压低枪位操作,加强搅拌,保证终点钢水成分、温度均匀,同时降低炉渣氧化性。 5 出钢操作 补吹时间较长,如有加石灰导致炉渣渣泡时,尽量要倒渣,倒渣完后可以向炉内加入少量压渣剂,避免因前期渣下到钢包或者渣泡导致摇炉角度不到夹渣出钢引起回磷。出钢过程中,第一次摇炉一定要到位,不能夹渣出钢。后面的摇炉要及时跟上,出钢快完成时,钢流要尽量靠近包壁,发现下渣马上抬炉,这样能有效减少下渣量。另外,挡渣车的挡渣操作要及时、准确,发现挡渣挡不住要采取应急措施,比如吹氩站气量稍微调小一些,或者加点脱硫剂稠化炉渣,尽量不要让表面炉渣全部卷进钢水中。渣子如果全部化透,回磷会增多,出钢P≥0.030%是比较危险的。出钢温度高、到站温度高,对钢水回磷也有很大影响,所以温度要控制好。按上述操作方法倒渣是在脱硅磷操作基本完成后进行,能有效脱磷,不影响冶炼周期。 6 经济效益 (1)氧耗。单渣操作法的氧耗为48.11m3/h,留渣双渣法的氧耗为45.36m3/h,同比节约2.75m3/h。 (2)石灰耗。单渣操作法的石灰耗为39.85kg/t,留渣双渣法的石灰耗为33.55kg/t,同比节约6.3kg/t。 (3)钢铁料耗。一般转炉炉渣中含有9%的铁珠和11%的FeO,留渣双渣操作将炉渣留待下炉使用,有利于初期渣尽早形成并且能提高前期去除磷硫的效率。在起泡沫渣时摇炉倒富磷渣,避免了喷溅时铁的损失,减少了炉渣带走的铁量,可以直接降低钢铁料消耗4kg/t。 (4)半钢渣和终渣的碱度与炉龄之间的关系,见表2、表3。
分析表2、表3的终渣样成分,留渣双渣法操作的炉渣碱度满足溅渣要求,MgO含量控制有波动;由于终渣MgO含量8.00%左右(偏低),镁球的加入方式应在倒渣后下枪吹炼再加入,保证终渣MgO含量满足溅渣要求。 留渣双渣法操作控制了终渣FeO含量,加上倒渣后再加入的镁球作用,提高了终炉渣MgO含量,为提高炉龄奠定了基础。 7 结语 福建三安炼钢厂采用留渣双渣法操作,满足了生产工艺和产品质量的要求。溅渣护炉技术改变了留渣氧化性能,复吹技术有效地解决了留渣操作的安全问题,并推动了留渣操作的应用。留渣双渣法操作有利于初期化渣和脱磷,并可以回收大量金属,吨钢石灰消耗降低6.3kg,钢铁料消耗降低5kg,经济效益非常可观。留渣双渣法初期渣碱度提高,可以减少对炉衬的侵蚀,从而提高炉衬寿命和炉龄。