CNC加工方法
cnc数控插铣加工使用方法大全这个太实用了

cnc数控插铣加工使用方法大全这个太实用了CNC插铣加工大幅提高切削效率和刀具寿命在提高金属切削效率上所取得的许多重大进展,都是刀具制造商、机床制造商和软件开发商共同努力的结果。
插铣(Z轴铣削)加工就是一个很好的例子。
插铣加工时,旋转的刀具沿着Z轴方向直接向下切入工件,并沿Z轴向上退刀,然后在X轴或Y轴方向横移一段距离,再进行与上一次切削部分重叠的垂直切削,切除更多的工件材料。
插铣加工有许多好处。
尤其是在长悬伸加工中(如铣削深模腔),传统的平面铣削方式(即从工件一侧铣到另一侧)为了尽量减小会引起颤振的侧向力,不得不降低切削速度。
而在插铣时,切削力直接传入机床主轴和工作台,因此可获得比传统铣削方式高得多的金属去除率。
据AMT软件公司介绍,该公司开发的Prospector CAM软件包中纳入了插铣功能,与使用纽扣型面铣刀的传统平面粗铣相比,插铣加工的金属去除率至少可以提高50%。
由于插铣能最大限度地减小作用于机床零部件的横向负荷,因此能用于刚性不足的老式机床或轻型机床,以提高生产率。
斗山机床公司营销经理John Ross对插铣可以减小作用于低性能机床上的切削力的说法表示赞同,但他补充说,在结构设计有利于插铣加工的新型机床上,能够最大限度地发挥该工艺的优势。
他指出,由于插铣切削力直接传入机床主轴和工作台,因此可以最大限度地减少因工件夹持不牢而产生的各种问题。
英格索尔(Ingersoll)刀具公司模具生产线产品经理Bill Fiorenza表示,插铣有助于减少传入刀具和工件中的切削热。
他说,“插铣加工时,传入工件的热量并不多,因为刀具旋转时切入和切出工件的速度很快。
只有移动步距的很小一部分工件与刀具接触。
”在切削难加工材料(如不锈钢、高温合金和钛合金)时,这一特点特别具有优势。
Fiorenza在进行插铣演示时解释说,“通常,金属切屑的温度很高,你甚至可以在切屑堆中烤热一块三明治。
然而,当插铣加工结束时,你可以马上把自己的手放在工件上,而且摸起来感觉比较凉。
cnc加工流程

cnc加工流程CNC加工流程。
CNC加工是一种高效精密的加工方法,广泛应用于各种工业领域。
它通过计算机控制机床进行加工,可以实现复杂零件的加工,提高生产效率,保证加工精度。
下面将详细介绍CNC加工的流程。
首先,CNC加工的第一步是设计图纸。
设计师根据产品的要求和工艺流程,利用CAD软件绘制出零件的三维模型和加工图纸。
这些图纸包括零件的尺寸、形状、加工工艺要求等信息,是CNC加工的基础。
接下来是编写加工程序。
程序员根据设计图纸,选择合适的刀具、工艺参数和加工顺序,编写加工程序。
这些程序包括刀具路径、进给速度、转速等信息,是CNC机床进行加工的指令。
然后是准备加工材料。
操作工根据加工图纸和程序,选择合适的材料,并进行切割、锯割或者铣削,将原材料加工成符合要求的工件。
这些工件将作为CNC加工的原料,进行后续加工。
接着是装夹工件。
操作工将加工好的工件安装在CNC机床上,并进行夹紧固定。
这一步需要保证工件的位置、角度和精度,以确保加工的准确性和稳定性。
随后是机床调试。
操作工将编写好的加工程序输入到CNC机床中,并进行调试。
这一步包括机床的各项参数设置、刀具的安装和校准、加工路径的检查等,以确保加工过程中的安全和稳定。
最后是CNC加工。
一切准备就绪后,CNC机床开始按照预先编写的加工程序进行加工。
在加工过程中,机床会根据程序自动进行刀具切削、进给运动、转速调节等操作,直到工件加工完成。
总的来说,CNC加工流程包括设计图纸、编写加工程序、准备加工材料、装夹工件、机床调试和加工等步骤。
每一步都需要严格按照要求进行操作,以确保最终加工出符合要求的零件。
随着技术的不断发展,CNC加工将会在更多领域得到应用,成为工业生产的重要环节。
CNC数控机床加工技术

CNC数控机床加工技术随着工业技术的不断进步,越来越多的工业领域开始采用数字化技术进行生产。
在机械加工领域,CNC数控机床加工技术已经逐渐成为主流。
本文将就CNC数控机床加工技术进行详细阐述。
什么是CNC数控机床?CNC数控机床是一种自动化机械设备,它主要通过计算机程序来实现高精度的加工。
相比于传统的机床设备,CNC数控机床具有高效率、高精度、高灵活性等多种优点。
通过CNC数控机床,我们可以轻松地实现复杂零件的加工,并且精度高、速度快、质量好。
CNC数控机床加工工艺CNC数控机床加工工艺主要分为以下几个步骤:1.设计加工程序在进行CNC数控机床加工前,首先需要编写相应的加工程序。
加工程序可以通过CAD/CAM辅助设计软件进行编写,并且可以根据不同的工件和加工要求进行调整。
2.选择机床和刀具在进行CNC数控机床加工时,需要选择合适的机床和刀具。
不同的工件需要不同的机床和刀具来完成加工任务。
同时,也需要根据加工要求选择合适的加工方式,如铣削、钻孔、车削等。
3.装夹工件装夹是CNC数控机床加工的一项重要环节。
工件装夹需要保证工件的稳定性和加工的准确性。
同时,也要注意工件与机床的协同性,保证加工顺利进行。
4.加工预处理加工预处理是指在加工前对机床和刀具进行正确的设置和校准。
通过校准,可以保证加工中的精度和质量。
5.加工控制加工控制是CNC数控机床加工的核心环节。
通过编程控制机床、刀具和工件的动态运动,实现高精度加工。
CNC数控机床加工的动态控制也是提高装备灵敏度和质量的重要手段。
6.加工后处理加工后处理是指在加工结束后,对加工件进行质量检查和表面处理。
通过质量检查和表面处理,可以保证加工件的质量和表面光洁度。
CNC数控机床加工技术优点CNC数控机床加工技术在工业生产中具有多项显著优点:1.高效率CNC数控机床加工技术采用自动化加工方式,可以显著提高生产效率和质量。
同时,CNC数控机床加工可以实现多工序自动化生产,提高生产效率和降低生产成本。
数控cnc加工操作流程

数控cnc加工操作流程
数控(CNC)加工是一种利用计算机控制机床进行加工的技术,它可以实现高精度、高效率的加工过程。
数控加工操作流程主要包括工件设计、编程、机床设置、加工操作和质量检验等环节。
首先,工件设计是数控加工的第一步。
在设计工件时,需要考虑到工件的形状、尺寸、材料等因素,以便确定加工的具体要求。
设计好工件后,就需要进行编程。
编程是数控加工的核心环节,它决定了机床的运动轨迹和加工路径。
编程可以通过手动编程、CAM软件编程或CAD/CAM集成编程等方式进行。
在编程过程中,需要考虑到刀具的选择、切削参数的设定等因素,以确保加工的精度和效率。
机床设置是数控加工的第三步。
在机床设置过程中,需要根据编程要求调整机床的各项参数,如工件夹持方式、刀具安装位置、加工速度等。
机床设置的准确性直接影响到加工质量和效率。
加工操作是数控加工的关键环节。
在加工过程中,操作人员需要监控机床的运行状态,及时调整加工参数,确保加工过程顺利进行。
同时,操作人员还需要注意安全问题,避免发生意外事故。
最后,质量检验是数控加工的最后一步。
在加工完成后,需要对工件进行质量检验,检查工件的尺寸精度、表面质量等指标是否
符合要求。
只有通过质量检验,才能保证加工的质量和精度。
总的来说,数控加工操作流程包括工件设计、编程、机床设置、加工操作和质量检验等环节。
每个环节都至关重要,只有每个环节
都做好,才能保证数控加工的质量和效率。
希望以上内容对您有所
帮助。
cnc机械加工工艺流程

cnc机械加工工艺流程CNC机械加工是指利用计算机控制数控机床进行加工的一种加工方法。
通过预先编程的程序指令,控制机床进行精准的加工操作,从而实现各种各样的零件加工。
下面将对CNC机械加工的工艺流程进行详细介绍。
首先,CNC机械加工需要进行零件设计和绘图。
设计师根据零件的要求和规格,在CAD软件上进行设计并绘制出2D或3D图纸。
图纸要详细标明零件的尺寸、形状、加工要求等信息。
这是CNC机械加工的第一步。
接下来,将设计好的图纸导入CAM软件中进行程序编写。
CAM软件可以将设计好的图纸转化为机床能够理解的指令代码。
在CAM软件中,可以进行加工路径的规划、刀具路径的优化等操作,以保证加工过程的高效和准确。
之后,将编写好的程序代码导入CNC机床的控制系统中。
这一步需要通过USB、以太网等方式将程序代码传输到机床的控制器上。
控制器会根据程序代码的指令来控制机床的运动,包括刀具的运动轨迹、进给速度、转速等参数。
然后,进行刀具的安装和刀具准备工作。
根据加工过程的要求,选择合适的刀具,并进行刀具的安装和校准。
确保刀具的位置和角度正确。
接下来,进行机床的工艺准备工作。
这包括机床的开启,加工台的调整,工件的固定等。
通过调整机床和加工台的位置,使得刀具可以在正确的位置进行加工操作。
然后,开始机床的自动加工过程。
启动机床,根据程序代码的指令,机床开始进行自动化加工操作。
刀具按照预先设定的路径和加工参数,对工件进行切削、铣削、钻孔等操作。
整个加工过程中,刀具的位置和角度都受控于机床的控制系统。
最后,进行工件的检查和处理。
待加工完成后,取出工件进行检查。
检查工件是否符合设计要求,在尺寸、形状、表面光洁度等方面进行质量检验。
如果有需要,可以对工件进行二次加工或修整,以满足实际应用的需求。
综上所述,CNC机械加工的工艺流程是设计图纸、程序编写、程序传输、刀具安装、机床准备、自动加工、工件检查和处理。
这一流程充分利用了计算机和自动化技术,提高了加工效率和精度,为工业制造提供了重要的支持。
cnc数控加工常用的几种螺纹加工方法

螺纹加工是cnc数控加工非常重要的技术之一,螺纹的加工质量和效率将直接影响零件的加工质量及加工中心的生产效率。
随着cnc数控加工性能的提高及切削刀具的改进,螺纹加工的方法也在不断改进,螺纹加工的精度和效率也在逐渐提高。
为了使工艺人员能够在加工中合理选择螺纹加工方法,提高生产效率,避免质量事故,现将在实际中cnc数控加工常用的几种螺纹加工方法总结如下:首先来说:丝锥加工的分类及特点采用丝锥加工螺纹孔是最常用的加工方法,它主要适用于直径较小(D<30),孔位置精度要求不高的螺纹孔。
最早时期的技术师傅们,大多是用柔性攻丝方法来做的,不过柔性攻丝夹头结构复杂,成本较高,容易损坏,加工效率较低。
近年来,cnc数控加工的技术的逐步提高,刚性攻丝功能成为cnc数控加工的基本配置。
所以,之后刚性攻丝逐渐成为了螺纹加工的主要方法(刚性弹簧夹头夹持丝锥,主轴进给与主轴转速由机床控制保持一致)弹簧夹头相对于柔性攻丝夹头来说,结构简单,价格便宜,用途广泛,除夹持丝锥外,还可夹持立铣刀、钻头等刀具,可以降低刀具成本。
同时,采用刚性攻丝,可以进行高速切削,提高加工的效率,而且降低制造成本。
攻丝前螺纹底孔的确定螺纹底孔的加工对于丝锥的寿命、螺纹加工的质量等方面有较大影响。
通常,螺纹底孔钻头直径选择接近螺纹底孔直径公差的上限,例如,M8螺纹孔的底孔直径为Ф6.7+0.27mm,选择钻头直径为Ф6.9mm。
这样,可减少丝锥的加工余量,降低丝锥的负荷,提高丝锥的使用寿命。
关于丝锥的选择选择丝锥时,首先,必须按照所加工的材料选择相应的丝锥,刀具公司根据加工材料的不同生产不同型号的丝锥,选择时要特别注意。
因为丝锥相对于铣刀、镗刀来说,对被加工材料非常敏感。
例如,用加工铸铁的丝锥来加工铝件,容易造成螺纹掉牙、乱扣甚至丝锥折断,导致工件报废。
其次,应注意通孔丝锥与盲孔丝锥的区别,通孔丝锥前端引导较长,排屑为前排屑。
盲孔前端引导较短,排屑为后排屑。
CNC车床加工工作流程

CNC车床加工工作流程CNC车床是一种先进的数控加工设备,在现代制造业中起着至关重要的作用。
它通过计算机控制刀具和工件的相对运动,实现高精度的加工效果。
本文将详细介绍CNC车床加工的整个工作流程。
第一步:工件准备在进行CNC车床加工之前,我们首先需要准备工件。
工件可以是金属、塑料或其他材料。
根据加工要求和设计图纸,我们选择合适的材料,并进行必要的切割和修整,使得工件符合规格和尺寸要求。
第二步:制定加工方案在开始CNC车床加工之前,我们需要制定一个详细的加工方案。
这个方案包括加工序列、切削工艺参数、刀具选择以及刀具路径等细节。
通过充分的计划和准备,可以提高加工效率和加工质量。
第三步:编写加工程序CNC车床的加工过程是由编写的加工程序控制的。
加工程序是一套经过编写和调试的指令集,用于告诉CNC车床刀具如何相对于工件运动。
编写加工程序通常使用专门的编程软件,并遵循G代码和M代码的标准。
第四步:装夹工件在加工开始之前,我们需要将工件安装在CNC车床的工作台上。
这个过程称为装夹。
装夹的目的是保证工件的稳定性和准确位置,以便于加工刀具的定位和切削。
第五步:刀具设置与调试在加工过程中,我们需要选择合适的切削工具并进行设置和调试。
这包括安装切削刀具、设置切削参数(如速度、进给量等)以及校准CNC车床的坐标系和参考点。
第六步:加工操作一切准备就绪后,我们可以开始进行CNC车床的操作。
操作过程中,CNC车床根据加工程序的指令,自动控制刀具和工件的相对运动,完成各种切削、铣削、钻孔等加工工序。
操作人员需要密切关注加工过程,及时调整和修正参数,确保工件达到预期的加工质量。
第七步:加工检验与修正当工件加工完成后,我们需要对加工结果进行检验。
通过使用测量工具和设备,检查工件的尺寸、形状和表面粗糙度等参数是否符合设计要求。
如果有偏差或不合格的地方,我们需要进行相应的修正和调整,以达到所需的加工质量标准。
第八步:清洁与保养在完成CNC车床加工后,需要对设备进行清洁与保养。
CNC加工工艺及加工时计算
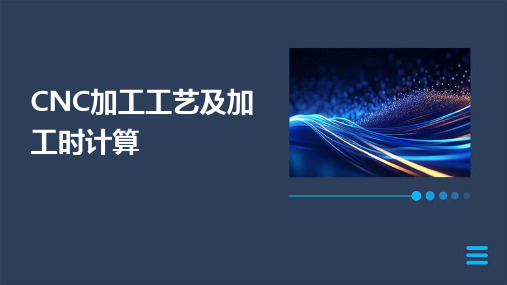
采用高效冷却方式,降低切削温度。
优化方法
优化刀具路径,减少空行程和刀具磨损 。
合理选择切削参数,提高切削效率。
精加工策略及优化方法
精加工策略:采用小刀 具、小切削深度和小进 给量,保证加工精度和
表面质量。
01
选择高精度切削参数和 刀具,确保加工精度。
03
加强机床刚性和稳定性 ,减少振动对加工精度
的影响。
寿命预测
根据刀具磨损规律,通过试验或经验公式预测刀具的使用寿命。寿命预测有助 于合理安排生产计划和降低生产成本。
加工精度和表面质量评价
加工精度
指工件加工后的实际尺寸、形状和位置与图纸要求的符合程度。加工精度受机床精度、刀具精度、夹具精度 和工艺方法等多种因素影响。
表面质量
指工件加工表面的粗糙度、波纹度、残余应力和金相组织等特性。表面质量直接影响工件的耐磨性、耐腐蚀 性和使用寿命。
如手术器械、植入物等医疗器 械的加工。
艺术品制造
如雕塑、珠宝等艺术品的加工 。
02
加工时计算原理与方 法
切削力、切削热和切削温度
切削力
切削过程中刀具与工件之间的相互作用力,直接影响切削效率和刀具磨损。切削力的大小 与切削参数(切削速度、进给量、切削深度)、刀具几何参数(前角、后角、主偏角等) 和工件材料性质有关。
根据工件材料和加工要 求选择合适的铣刀,包 括铣刀类型、直径、齿 数、螺旋角等。
根据铣削方式和铣刀参 数,利用切削用量计算 公式或经验数据确定切 削速度、每齿进给量和 切削深度等切削用量。
根据工件形状和加工要 求,编写合适的加工程 序,包括加工路径、切 削用量和刀具补偿等。
根据切削用量、铣刀和 加工程序,利用加工时 间计算公式或仿真软件 计算加工时间。
- 1、下载文档前请自行甄别文档内容的完整性,平台不提供额外的编辑、内容补充、找答案等附加服务。
- 2、"仅部分预览"的文档,不可在线预览部分如存在完整性等问题,可反馈申请退款(可完整预览的文档不适用该条件!)。
- 3、如文档侵犯您的权益,请联系客服反馈,我们会尽快为您处理(人工客服工作时间:9:00-18:30)。
4、冷却方式:高压冷气。
十、刀尖圆角
常用的刀粒主要有以下几种刀尖圆角。
R0.4 R0.8 R5 R6 R8
第四章成型粗加工
一、粗成型余量:除特别说明外,一般余量为3MM,并且保证各大平面余量均匀。程式中下刀方式为沿边界斜线下刀,每层完成后要上升到安全高度。
3.冷却方式:加冷却液。
四、麻花钻
1、适用范围:用于加工直径的粗孔。
2、特性:加工前需定位,采用G83格式,抽屑距离(Q值)根据刀具大小、工件材料而定,加工退孔时做通值为L=3XDX0。3(D为刀具直径)
3、冷却方式:加冷却液。
五、粗波刀
1.适用范围:用于加工粗孔及精孔加工。
2.装有刀粒,采用G81格式,用此刀前需先加工好底孔。加工通孔一般做通5MM。
3、冷却方式:加冷却液。
八、拔头刀
1、适用范围:用于加工顶针托位,胚头孔托位等。
2、特性:用G83格式,切宽小于或等于3MM,大于3MM,可分几次加工到位,在加工顶针托位时,因其深度要求相当高(带有公差)。因此,须用拔头刀打粗孔,底部留数0。05-0。1MM,然后用直柄链槽铣刀,用G81格式一次加工到位,若没有此类规格的刀具,可用光刀锣出,另小于11的托位孔可用小光刀G83Q0。5一次性加工出。
3、走刀方式:要求刀具顺铣加工,即沿逆时针方向走刀加工内框,沿顺时针方向走刀加工外形框。
4、冷却方式:高压冷气。
三、精铣刀
1.适用范围:用于加工直身精框,但小直径光刀(3-6)可用于粗加工。
2.特性:用G42D计算器补正(COMPENSATION IN COMPUTER)。另有12MJ光刀,其加工效率很高,加工尽量多使用,在遇到转角时进给量控制在F220左右。
4.定位深度,2MM。
二、喷水钻
1.适用范围:用于加工大直径的粗孔(ф13以上)。
2.特性:装有刀粒,因此在加工前不用定位(大直径喷小钻自身有中心钻)G81格式,加上通孔时一般做通5MM
3.冷却方式:加冷却液。
三、高速钻
1.适用范围:用于加工小直径的粗孔。
2.特性:加工前需定位,采用G83格式,抽屑距离(Q值)根据刀具直径大小、工件材料而定,加工通孔时做通值为L=3+DX0。3。(D为刀具直径)
1.中心钻G81打宝位点,确定钻孔位置。
2.麻花钻G83打一般的粗孔,中粗孔。
3.高速钻G83加工一般的粗孔,中粗孔。
4.硬质合金钻G83加工种类同以上两类。
5.喷水钻G81加工一些回针孔,边司孔。
6.拨头刀G83加工一些顶针,回针托位。
7.粗波刀G81中粗加工一些喷水钻打过的孔。
8.精波刀G81精加工一些精度要求高的孔。
3.走刀方式:要求刀具逆铣加工,即顺时针方向走刀加工内框,沿逆时针方向走外形框。
4.却方式:加冷却液。
四、钻铣刀
1.适用范畴:用于开粗及中粗加工。
2.特性:可走动下刀,也可先钻落刀孔,再从孔的地方下刀,(G83Q0。5)铣刀只能铣,不能钻,钻铣刀中粗加工前要求先插角。
3.走刀方式:要求刀具铣加工,即沿逆时针方向走刀加工内框,沿顺时针方向走处形框。
2注意工字面板及底板有时是偏中取数
六、钻孔编写步骤
1、接收图纸,从网上调出相应图档:
电脑操作顺序:
FILE CONVERTER DXF8。1AUTODESK(9。1)RDADFILE DEF
2、整理图档:
将图纸取数中心平移至坐标原点(0,0,0)旋转或镜像,达到自己相要的加工位置,删除不需要的图素,其尺寸及坐标达到准角无误,最后存档MC8(*。MC9)
4.冷却方式:高压冷却。
五、插角刀
1.适用范围:专用于插角用。
2.特性:是根据一些旧一点刀自行改制而成,插直角采用G81格式,在插带底R的角时用PENCIL式作3D刀路插角。
3。冷却方式:高压冷气。
六、AX小无敌铣刀
1.适用范围:用于小型框粗加工。
2.特性:装有刀粒,只能铣不能钻,可走动下刀加工,其加工效率很高,可代替整体硬质合金小光开粗。
———M13;
G80;
M05;
M30;
%
注:程式中不能出现G00Z,钻不同深度只能采取一个G86。
五、三种基本取数方式
i.分中取数:板长、板宽分中(余量四边留)
ii.基准角取数:以一基准角取数找中心(余量在相对应的面留)
iii.单边取数:一边分中(余量两边留),一边单边取数(余量在相对应的面留)
附加:1零点取数(0,0)
3.特殊孔的加工:
(1)运水孔——这类孔一般放在枪钻机上做,例如侧运水孔。
(2)管钉孔、精孔——这类孔尺寸要求较高,一种孔我们可能分几次去加工完成。例如10。00精孔。加工方案如下:首先9。5钻咀钻,其次9。8三刃捻把,最后10精波刀(或10捻把)
4.有托位孔的加工:
分几次完成,例如Φ16顶针孔托位深8。
二、精成型开粗:余量单边留3MM,底面为1MM(此时我们可在参数中将刀半径加大2MM而在余量的参数设置填入1MM)其他同粗成型一样。
5.顶棍孔——位于下模底板,是模具施力顶出装置,所在位置。
6.弹弓孔——一般位于开模面,起到辅助分模作用。
7.管钉孔——在模具中位置比较精确,多用作定位及精密配合。
8.胚头孔——与螺钉配合锁紧模板,连接各部析达到牢固可靠。
9.牙孔——在模具中比较常见,一般收镶件和加固零件。
10.唧咀孔——在产中产品的进料中,与注塑机喷嘴相接。
3、草稿列出加工种类及选用加工刀具,确定加工参数准确合理。
4、编写程序:
电脑操作顺序:T LPATHS DRIN ATOMATIC自动选点。
ENTITIAS
WIMDO征选点
PUFTORNS
SUBPGMOPS
参数设置及修改:
TOOLPATHS——OPERATIONS——
4、冷却方式:高压冷气。
二、一点刀
1、适用范围:用于加带斜度的精框及三维刀,精铣刀无法加工的直身精框。
2、特性:在其它刀具无法进行加工时可选用一点刀开中粗(只限制12以上可使用),以及光底刀无法加工时,待为常用刀粒R为0。8,采用G41D?用控制器来补正(COMPEN SATION IN CONTROL)
2、特性:用此刀加工前,需先加工好牙底孔,及倒C角。
3、冷却方式:高压冷气。
十二、O-RING刀
1、适用范围:用于加工胶圈孔。
2、特性:有标准O-RING刀(HASCO和SK)和非标O-RING两种,采用G81格式,在加工中常有一些非标O-RING,因此需填写《特殊刀具订做申请表》知会IE部制作O-RING刀,并要求提供加工参数。
常见的孔类型及名称
1.钉孔——我们常叫导柱孔、直边孔,它在模具中可以导向,起定位的作用,贯穿上下。
2.回针孔——常位于下模中,连接于针板间,也可以说直起到复位作用。
3.顶针孔——位于下模B板和针板与顶针配合起推出产品(塑件)作用。
4.撑头孔——位于下模针板间与撑头配合支撑下模,穿撑头棒,通常孔往大于撑头直径1-2mm.
2、特性:有D50,D125两种,大框可用D125光底,再用D50清角。
3、走刀方式:精框双向走刀。
4、冷却方式:高压冷气。
九、插铣刀
1、适用范围:用于中小形框粗加工。
2、该刀具中只能铣不能钻,可走动下刀加工,尽量代替钻铣刀,小圆刀,加工小框及开槽等。加工效率高于现用钻铣刀,小圆刀,而且不容易损坏,在开粗框时,刀粒R角填入距离A值即可。
11.运水孔——上、下模常有或贯穿或一段,有侧面运水,直运水,可通水冷却。
12.拉令孔——一般模板四周或上下面打有大的螺丝孔,可以方便吊模。
13.斜孔——一般位于上模,斜抽芯,斜滑块配用。
14.O-Ring孔——模框内有些有运水孔上需加密封圈而制作的一类孔。
二、加工孔的刀具
针对我们公司加工孔所配备的一些刀具作以下介绍:
13.枪钻G86加工一些深度较大的孔,如运水孔、顶针孔之类。
14.锣牙刀CAMTOWR专用锣刀。
15.圆槽刀G81做ORING孔加工。
三、刀具选择及加工顺序
1.加工孔的一般程序:定位钻孔(扩孔或攻牙)
2.加工孔时刀具考虑一般遵循:先后顺序1喷水钻2硬质合金3高速钻4麻花钻。除了喷水钻打孔前不需定位外,其余几种钻咀都需要先打定位点。
----
-----
G80
程序尾G0Z100
二)例G83:G83是步进钻孔循环,麻花钻及一些钻咀用该指令较多.
%
程式头---
------
---
G0G90 X—Y—
程序部分G98 G83 Z—R—Q—F—
----
-----
G80
三)例G86是搪孔循环,在本公司用于枪钻指令,做一些孔.
G86 X Y Z R10 F M13;
3、冷却方式:加冷却液。
九、枪钻
1、适用范围:主要用于加工运水孔,顶针孔等深度较深的孔。
2、特性:用G86格式。
3、冷却方式:加冷却油。
十、捻把三刃钻
1、适用范围:主要用于加工管钉孔及一些精孔。
2、特性:采用G81格式。
3、冷却方式:加冷却液。
十一、锣牙刀
1、适用范围:用于一些标准公制牙刀无法加工的公制牙时,用此刀来锣出牙孔。
2、特性:装有刀粒:刀粒有R5 R6及R8,不同直径刀具装的刀粒不同,因此在输入刀粒R时,一定要对准,在加工深度大于刀具直径的情况下,要彩分段加工(开粗、开精)。做精时采用G41控制器补正COMOENSATIONIN CONTROL)
3、走刀方向:要求刀具顺铣加工,即沿逆时针方向走刀加工内框,沿顺时针方向加工外形框。
3)Φ10扩前一孔。