CA6140拨叉831006说明书

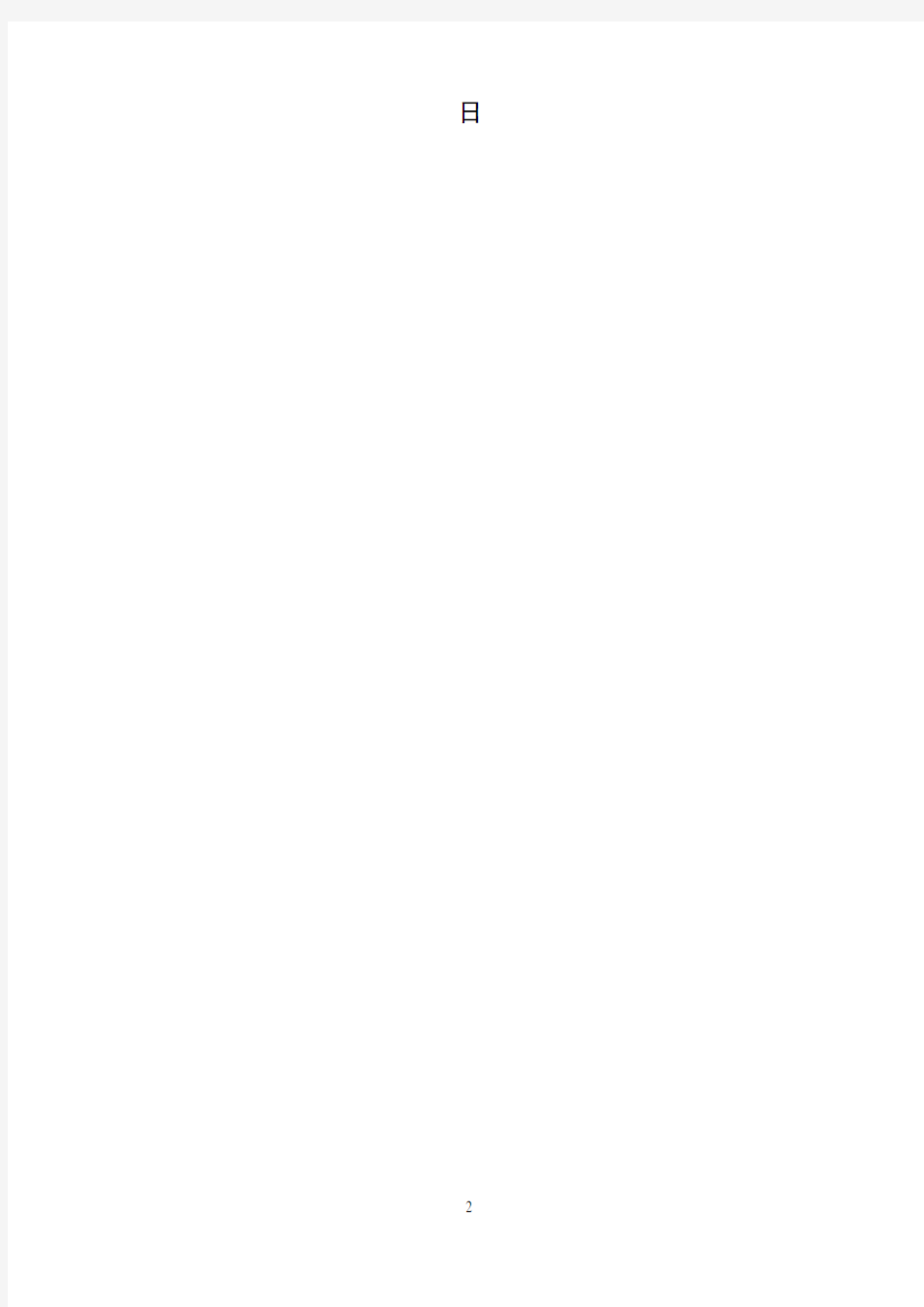
东南大学成贤学院
课程设计报告
题目 CA6140车床拨叉(831006)夹具设计
课程名称机制工艺课程设计
专业机械设计制造及其自动化
班级 13机电一班
学生姓名张青
学号 04113104
设计地点成贤学院
指导教师易茜
设计起止时间:2016 年 1 月4 日至2016 年 1 月22
日
目录
序言 (2)
第1章零件的工艺分析及生产类型的确定 (3)
零件的作用 (3)
拨叉的技术要求 (3)
零件的工艺性分析和零件图的审查 (4)
确定拨叉的生产类型 (4)
第2章选择毛坯,确定毛坯尺寸,设计毛坯图 (5)
确定毛坯的成形方法 (5)
铸件结构工艺性分析和铸造工艺方案的确定 (6)
第3章选择加工方法,制定工艺路线 (7)
定位基准的选择 (7)
各表面加工方案的选择 (7)
制定机械加工工艺路线 (8)
第4章确定机械加工余量和工序尺寸 (11)
第5章确定切削用量及时间定额 (15)
第6章夹具设计 (22)
设计心得 ......................................... . 25参考文献 . (26)
序言
《机械制造工程学》课程设计是培养学生综合运用机械制造工程原理及专业课程的理论知识。在此次课程设计中我结合金工实习中学到的实践知识,独立地分析和解决机械加工工艺问题,初步具备中等零件工艺规程的能力。
我本次设计的是CA6140机床的拨叉831006,通过这个设计让我直观地了解了拨叉831006的作用,随着科学技术的发展,各种新材料、新工艺和新技术不断涌现,机械制造工艺正向着高质量、高生产率和低成本方向发展。各种新工艺的出现,已突破传统的依靠机械能、切削力进行切削加工的范畴,可以加工各种难加工材料、复杂的型面和某些具有特殊要求的零件,使工艺过程的自动化达到了一个新的阶段。了解这些尤为重要的是巩固综合了大学三年以来学习的专业课知识,温故知新。通过课程设计我增强了空间想象能力和结构构造能力,提前为以后的毕业设计打下了基础。
在机械设计制造工艺中每个环节毛坯的设计,夹具的方案一次次的修改成最后的方案无不是我日思夜想的成果,对于方案抱有严谨挑剔的态度这个是我在设计中的最大的收获,也是不断地改进设计优化方案的最大动力。
不过有限的知识水平还是让方案存在着许些细小瑕疵,在一次次修补在这些瑕疵中以往的忽略之处得到了重视,加深了印象,为今后的工作打下了坚实的基础。
第一章零件分析
零件的作用
CA6140车床的拨叉零件用在车床变速机构中,主要起换档,使主轴回转运动按照工作者的要求工作,获得所需的速度和扭矩的作用。拨叉通过叉轴孔φ25mm安装在变速叉轴上,与操纵机构相连,拨叉脚φ55mm半孔则是夹在双联变速齿轮的槽中,当需要变速时,操纵变速杆,变速操纵机构通过拨叉头部的操纵槽带动拨叉与变速叉轴一起在变速箱中滑移,拨叉脚拨动双联滑移齿轮在花键轴上滑动以改变档位,从而改变车床主轴转速。
拨叉在换挡时要承受弯曲应力和冲击载荷的作用,因此零件应具有足够的强度、刚度和韧性,以适应拨叉的工作条件。拨叉的主要表面为拨叉脚的两端面、变速叉轴孔φ25H7和操纵槽,在设计工艺规程时应重点予以保证。
拨叉的技术要求
操纵槽内侧面
16IT11垂直度
操纵槽底
面
8IT11
操纵槽下
端面
23IT11
Φ40外圆
斜面
17IT11
零件的工艺性分析和零件图的审查
分析下图拨叉零件图可知,拨叉头部一段面和拨叉脚两端面在轴向方向上均高于相邻表面,这样既减少了加工面积,又提高了换挡时叉脚端面的接触刚度;φ25mm孔和φ55mm孔的端面均为平面,可以防止加工过程中钻头钻偏,以保证孔的加工精度;另外,该零件除主要工作表面外,其余表面加工精度均较低,通过铣削、钻削的一次加工就可以达到加工要求;主要工作表面虽然加工精度相对较高,但也可以在正常生产条件下,采用较经济的方法保质保量地加工出来。由此可见,该零件的工艺性很好。
确定拨叉的生产类型
依设计题目知:因为生产量大于2000,所以可设Q=3000台/年,m=1件/台;结合生产实际,备品率a%和废品率b%分别为3%和%。
N=Qm(1+a%)(1+b%)=3000×1×(1+3%)×(1+%)=件/年
根据拨叉的质量1.12kg查文献知,该拨叉属轻型零件;再由表2-1可知,该拨叉的生产类型为中批生产。
第2章 -选择毛坯,确定毛坯尺寸,设计毛坯图确定毛坯的成形方法
该零件材料为HT200,考虑到拨叉在工作过程中受力不大,轮廓尺寸也不大,各处壁厚相差较小,从结构形式看,几何形体不是很复杂,并且该零件年产量为3000件/年(因为年产量大于2000,可设为3000),采用铸造生产比较合适,故可采用铸造成形。
铸件结构工艺性分析
该零件拨叉脚部分因散热面积大,壁厚较薄,冷却快,故有可能产生白口铁组织,但因为此件对防止白口的要求不严,又采用金属型铸造,保温性能好,冷却速度较才慢,故能满足拨叉的使用要求。
铸造工艺方案的确定
2.3.1铸造方法的选择
根据铸件的尺寸较小,形状比较简单,而且选用灰铸铁为材料,并且铸件的表面精度要求不高,结合生产条件并参考文献表2-3选用金属型铸造。
2.3.2造型、造芯方法及工序组合的选择
因铸件制造批量为中批生产,且尺寸不大,结构不太复杂,为轻型机械,故选用金属型铸造。型芯尺寸不大,形状简单,故选择手工芯盒造芯。机械结构相对于CA6140比较简单,
适合流水线大量生产,故采用工序分散。
铸造工艺参数的确定
2.4.1加工余量的确定
按金属型铸造,灰铸铁查文献一表5-1,查得加工余量等级为IT8-IT12,取铸造尺寸公差为9级,加工余量等级为F,得RMA数值为~1.6mm,取RMA为1.4mm 。
由公式R=F+2RMA+CT/2(外圆面进行机械加工时用)
R=F-2RMA-CT/2(内腔面进行机械加工时用)得:
毛坯基本尺寸:
φ55左右端面厚度R=F+2RMA+CT/2=12+2*+9/2=19.3mm
φ55孔R=F-2RMA-CT/2=*2-9/2=47.7mm
槽端面R=F+RMA+CT/2=23++9/2=28.9mm
其余尺寸铸造直接得到。
2.4.2收缩率的确定
通常,灰铸铁的收缩率为%~1% ,在本设计中铸件取1% 的收缩率。
2.4.3不铸孔的确定
为简化铸件外形,减少型芯数量,较小的操纵槽不铸出,而采用机械加工形成。
2.4.4铸造圆角的确定
为防止产生铸造应力集中,铸件各表面相交处和尖角处,以R = 3mm~5mm圆滑过渡。
第3章选择加工方法,制定工艺路线
定位基准的选择
基面是工艺规程设计中的重要工作之一,基面选择的正确合理,可以使加工质量得到保证,生产效率得到提高。否则,加工过程中会问题百出,甚至造成零件大批量报废,使生产无法正常进行。
3.1.1粗基准的选择
作为粗基准的表面应平整,没有飞边、毛刺或其他表面缺欠。本例选择拨叉头部φ40右端面和φ40外圆作为粗基准。采用φ40外圆定位加工内孔可保证孔的壁厚均匀;采用拨叉头的右端面做粗基准加工拨叉脚左端面,接着以左端面为基准加工右端面,可以为后续准备好精基准。
3.1.2精基准的选择
根据拨叉零件的技术要求和装配要求,选择拨叉的设计基准叉脚的内孔表面和叉轴孔作为精基准,符合基准重合原则;同时,零件上很多表面都可以采用该组表面作为精基准,又遵循了基准统一的原则;叉轴孔的轴线是设计基准,选用其做精基准定位加工拨叉脚两端面,有利于保证被加工表面的垂直度;选用拨叉脚左端面为精基准同样是服从了基准重合的原则,因为该拨叉在轴向方向上的尺寸多以该端面作为设计基准。
各表面加工方案的选择
根据拨叉零件图上各加工表面的尺寸精度和表面粗糙度和毛坯确定,查文献,确定各表面加工方案如下。
(1)叉轴孔φ25内孔
表面粗糙度为,经济精度为IT7,加工方案确定为:钻→扩→粗
铰→精铰;
(2)拨叉脚φ55内表面
表面粗糙度为,经济精度为IT8,加工方案确定为:粗镗→半精镗;
(3)拨叉脚两端面(φ75上下端面)
表面粗糙度为,经济加工精度为IT8,加工方案确定为:粗铣→
精铣;
(4)操纵槽左右内侧面
表面粗糙度为,经济精度为IT8,加工确定为:粗铣→精铣
(5)操纵槽底面
表面粗糙度为,经济精度为IT12,加工方案确定为:粗铣
(6)φ40外圆斜面
表面粗糙度为,经济精度为IT11,加工方案确定为:粗铣→半精铣;
(7)拨叉脚端面
表面粗糙度为,经济加工精度为IT8,加工方案确定为:粗铣→精铣。
制定机械加工工艺路线
制订机械加工工艺路线的出发点,应当是使零件的几何形状、尺寸精度及位
置精度等技术要求得到合理的保证。在生产纲领已经确定为中批量生产的条件
下,可以考虑采用通用机床配以专用夹具,并尽量使工序集中来提高生产率。除
此以外,还应当考虑经济效果,以便生产成本尽量降低。
(1)工艺路线方案一(按照基准先行及先主后次的原则,该零件加工可按下述工艺路线进行)
工序1 铸造;
工序2 热处理;
工序3 以底面和Φ75中心线为基准,画线找正,找Φ40轴线,粗镗,半精镗Φ55孔,选用T716A立式镗床和专用夹具;
工序4 铣断Φ55圆孔,使之为两个零件,以Φ25轴线为基准,选用X51立式铣床和专用夹具;
工序5 钻、扩、粗铰、精铰拨叉头φ25孔,以Φ75轴线和其端面为基准,选用Z535立式钻床和专用夹具;
工序6 粗铣,精铣Φ75上下端面,以Φ25轴线为基准,保证垂直度,选用X51立式铣床和专用夹具;
工序7 粗铣,半精铣φ40外圆斜面,以Φ55端面和Φ25轴线为基准保证与Φ25轴线垂直度,选用X51立式铣床和专用夹
具;
工序8 粗铣操纵槽端面,粗铣、精铣操纵槽端面侧面,以Φ25轴线为基准,选用X61卧式铣床和专用夹具;
工序9 钳工去毛刺;
工序10 终检;
工序11 入库。
(2)工艺路线方案二(按照基准先行及先主后次的原则,该零件加工可按下述工艺路线进行)
工序1 铸造;
工序2 热处理;
工序3 以底面和Φ75中心线为基准,画线找正,找Φ40轴线,钻、扩、粗铰、精铰拨叉头φ25孔,选用Z535立式钻床和专
用夹具;
工序4 粗镗,半精镗Φ55孔,以Φ25轴线为基准,选用T716A立式镗床和专用夹具;
工序5 粗铣,精铣Φ75上下端面,以Φ25轴线为基准,保证垂直度,选用X51立式铣床和专用夹具;
工序6 粗铣操纵槽端面,粗铣、精铣操纵槽端面侧面,以Φ25轴线为基准,选用X61卧式铣床和专用夹具;
工序7 粗铣,半精铣φ40外圆斜面,以Φ55端面和Φ25轴线为基准保证与Φ25轴线垂直度,选用X51立式铣床和专用夹
具;
工序8 铣断Φ55圆孔,使之为两个零件,以Φ25轴线为基准,选用X51立式铣床和专用夹具;
工序9 钳工去毛刺;
工序10 终检;
工序11 入库。
工艺方案的比较分析
方案二在方案一基础上优化,利用了两件合铸的优势,最后铣断,提高了工作效率,集中铣削工序在铣削车间完成,大大省去了在各机床间切换的麻烦, 提高了加工时间。又有利于各加工位置的保证φ25的孔及其16的槽和φ55的端面加工要求,以上三者之间具有位置精度要求。图样规定:先钻φ25mm的孔。由此可以看出:先钻φ25的孔,再由它定位加工φ55的内圆面及端面,保证φ25的孔与φ55的叉口的端面相垂直。因此,最后的加工工艺路线方案二!
确定如下表3-1:
表3-1拨叉工艺路线及设备、工装的选用
第4章 确定机械加工余量和工序尺寸
根据以上的原始资料及机械加工工艺,分别确定各加工表面的机械加工余量,工序尺寸、毛坯尺寸如下:
工序1---钻、扩、铰拨叉头φ25孔
表面粗糙度为,经济精度为IT 7,加工方案确定为:钻→扩孔→粗铰→精铰。 查文献得毛坯铸件的公差等级CT =IT 10级,经计算得铸造毛坯内孔基本尺寸为φ20.8mm 。
查文献得,精铰余量Z 精铰=0.06mm ;粗铰余量Z 粗铰=0.14mm ;扩孔余量Z 扩孔=1.8mm ;钻孔余量Z 钻孔=2.2mm 。各工序尺寸按加工经济精度查表1-10依次确定为精铰孔为IT 7级;粗铰孔精度为IT 8级;扩孔精度为IT11级;钻孔精度为IT 13级。
综上所述,该工序各工步的工序尺寸及公差分别为:精铰孔工序尺寸为
0.021
025+φ;粗铰孔工序尺寸为0.033024.94+φ;扩孔工序尺寸为0.13024.8+φ;钻孔工序尺寸为0.33023+φ。具体工序尺寸见表4-1
表4-1 工序尺寸表
工序2---粗镗、半精镗拨叉脚φ55圆
表面粗糙度为,经济精度为IT8,加工方案确定为:粗镗→半精镗; 查文献得毛坯铸件粗镗的公差等级CT =IT12级,粗镗的公差等级CT =IT8级。 查文献得,粗镗余量Z 粗镗=5.8mm 。各工序尺寸按加工经济精度查表确定粗
镗孔精度为IT 12级。
查文献得,半精镗余量Z 半精镗=1.5mm 。各工序尺寸按加工经济精度查表确定粗镗孔精度为IT 12级,粗镗孔精度为
IT 8级。
综上所述,该工序各工步的工序尺寸及公差分别为:粗镗孔工序尺寸为
0.3047.7+φ,半精镗孔工序尺寸为0.4
055+φ。
具体工序尺见表4-2 表4-2 工序尺寸表
工序3---粗铣、精铣Φ75上下端面
表面粗糙度为,经济加工精度为IT 8,加工方案确定为:粗铣→精铣; 毛坯基本尺寸φ55大端面R =F +2RMA +CT /2=12+2*+9/2=19.3mm
查文献一表2-25得,粗铣余量Z 粗铣(单边)=3mm ,精铣余量Z 精铣(单边)=0.5mm 。工序尺寸按加工经济精度查表依次确定为粗铣孔精度为IT 12、IT 8级。
具体工序尺寸见表4-3 表4-3 工序尺寸表
工序4---粗铣操纵槽端面,粗铣、精铣操纵槽端面侧面
操纵槽端面粗糙度为,经济加工精度为IT 12,加工方案确定为:粗铣。 查文献得粗铣余量Z 粗铣=1.5mm ;精铣余量Z 精铣=3mm 。各工序尺寸按加工经济精度依次确定为粗铣孔为IT
12级;精铣精度为IT 8级。
综上所述,该工序各工步的精铣槽侧面工序尺寸为0.12
016+。
具体工序尺寸见下表4-4、表4-5
表4-5 操纵槽端面侧面工序间尺寸表
工序5---粗铣,半精铣φ40外圆斜面
表面粗糙度为,经济精度为IT 11,加工方案确定为:粗铣、半精铣; 查文献,粗铣余量Z 粗铣(单边)=1.5mm 、
Z 半精铣(单边)=1mm 。工序尺寸按加工经济精度查依次确定为粗铣精度为IT12级、半精铣精度为IT11级。
具体工序见尺寸表4-6 表4-6 工序尺寸表
工序6---铣断Φ55圆孔
表面粗糙度为,经济加工精度为IT 11,加工方案确定为:粗铣; 铣断所用的刀具为细齿锯片铣刀,所以余量由铣刀厚度定,所以得出粗铣余量Z 粗铣=4mm 各工序尺寸按加工经济精度查表粗铣精度为IT 12级。
综上所述,该工序各工步的工序尺寸及公差分别由细齿锯片铣刀决定 具体工序尺寸见表4-7 表4-7 工序尺寸表
第5章确定切削用量及时间定额
工序1---扩、铰拨叉头φ25孔
1.加工条件
工件材料:灰铸铁HT200
加工要求:钻Φ25的孔,其表面粗糙度值为Rz=μm;先钻Φ23的孔在扩Φ的孔,再粗铰Φ孔,再精铰Φ25孔。
机床:Z535立式钻床。
刀具:Φ23麻花钻,Φ的扩刀,Φ25铰刀。
2.计算切削用量
(1)钻Φ23的孔。
①进给量:查文献得钻孔进给量f 为~0.47 mm/r ,由于零件在加工?23mm 孔时属于低刚度零件,故进给量应乘系数,则f =~×=~0.35mm/r ,查表得出,现取f=0.3mm/r 。此工序采用Φ23的麻花钻。
所以进给量f= 0.3mm/z 、p a =11.5mm
②切削速度:0v
v v z v c v x y m p C d v k T a f
==42.80m/min
1000c
v n d
π=
= r/mim 经过查表,取n=680 r/min, 则实际切削速度c v =49.13 m/min 。 ③轴向力: 0F
F Z y f
F F F C d f k ==
④转矩:
M
y z M C k f d C M M M 0== ⑤功率: 0
30c c
C M v P d =
= 实际切削功率为, Z535立式钻床允许功率E P =,允许进给力F=15696N,合理。 ⑥切削工时取L1=23mm ,L2=13.2mm.: =++=fn
l l l m 2
11t (min)
(2)扩Φ23的孔
①进给量
查《切削用量手册》表规定,查得扩孔钻扩Φ的孔时的进给量,并根据机床规格选取f =1.0mm/z 、p a =0.9 mm 。
②切削速度:0v
v v z v c v x y m p C d v k T a f
==42.80m/min
1000c
v n d
π=
= r/mim 经过查表,取n=530 r/min, 则实际切削速度c v =41.29m/min 。
③切削工时取L1=1.8mm ,L2=1.5mm.:=++=fn
l l l m 2
11t (min) (3)粗铰Φ23的孔 ①进给量
查《切削用量手册》表规定,查得扩孔钻扩Φ的孔时的进给量,并根据机床规格选取f =1.4 mm/z p a =0.07mm
②切削速度:0v
v v z v c v x y m p C d v k T a f
==25.12m/min
1000c
v n d
π=
= r/mim 经过查表,取n=275 r/min, 则实际切削速度c v =21.54m/min 。 ③切削工时取L1=0.14mm ,L2=1.5mm.: =++=fn
l l l m 2
11t (min) (4)精铰Φ23的孔 ①进给量
查《切削用量手册》表规定,查得扩孔钻扩Φ的孔时的进给量,并根据机床规格选取f =1.15mm/z p a =0.07mm
②切削速度:0v
v v z v c v x y m p C d v k T a f
==27.73m/min
1000c
v n d
π=
= r/mim 经过查表,取n=400 r/min, 则实际切削速度c v =31.42m/min 。 ③切削工时取L1=0.06mm ,L2=0mm.:=++=fn
l l l m 2
11t (min)
工序2---粗镗、半精镗拨叉脚φ55圆
1. 加工条件
工件材料:HT 200,σb = HB =190,金属铸造。
加工要求:粗镗、半精镗拨叉脚φ55圆。 机床:立式镗床T716A 刀具:硬质合金镗刀
2. 切削用量
查后刀面最大磨损及寿命:后刀面最大磨损为~1.5mm ,寿命T =180min
(1)粗镗φ55圆
①进给量
查《切削用量手册》得,查得镗刀镗Φ55的孔时的进给量f =~0.8 mm/z,并根据机床规格选f =0.5 mm/z p a =2.65mm
②切削速度:0v
v v z v c v x y m p C d v k T a f
==45.96m/min
1000c
v n d
π=
= r/mim 经过查表,取n=300 r/min, 则实际切削速度c v =49.93m/min 。 ③切削工时取L1=0.06mm ,L2=0mm.: ==L/V f t 1m (min)
(2)半精镗φ55圆
①进给量
查《切削用量手册》得,查得镗刀镗Φ55的孔时的进给量f =~0.8 mm/z,并根据机床规格选f =0.15 mm/z p a =1.0mm
②切削速度:0v
v v z v c v x y m p C d v k T a f
==68.74m/min
1000c v n d
π==mim
经过查表,取n=400r/min, 则实际切削速度c v =69.1m/min 。 ③切削工时取L1=0.05mm ,L2=0 mm.:==L/V f t 1m (min)
工序3---粗铣、精铣Φ75上下端面
(1)粗铣Φ75上端面