铸件缺陷分类
铸件外观缺陷图

铸件常见缺陷常见缺陷缺陷的分类:铸件常见缺陷分为孔眼、裂纹、表面缺陷、残缺类缺陷、形状及尺寸和重量不合格、成份及组织和性能不合格六大类。
1孔眼类缺陷孔眼类缺陷包括气孔、缩孔、缩松、渣眼、砂眼、等。
1.1.1气孔:别名气眼,气泡、由气体原因造成的孔洞。
铸件气孔的特征是:其表面一般比较光滑,主要呈梨形\圆形和椭圆形.一般在铸件表面露出,大孔常孤立存在,小孔则成群出现。
(如图)产生的原因是:来源于气体,炉料潮湿或绣蚀、表面不干净、炉气中水蒸气等气体、炉体及浇包等修后未烘干、型腔内的气体、浇注系统不当,浇铸时卷入气体、铸型等。
1.1.2缩孔缩孔别名缩眼,由收缩造成的孔洞。
缩孔的特征是:形状不规则,孔壁粗糙并带有技状晶,常出现在铸件最后凝固的部位,广义的缩孔包括缩松。
(如图)产生的原因是:金属在液体及凝固期间由于补缩不良而产生的孔洞,主要有以下几点:铸件结构设计不合理,浇铸系统不适当,冷铁的大小、数量、位置不符实际、铁水化学成份不符合要求,如含磷过高等。
浇注温度过高浇注速度过快等。
1.1.3缩松缩松别名疏松、针孔蜂窝、由收缩耐造成的小而多的孔洞。
缩松的特征是:铸件断面上出现的分散而细小的缩孔.助高倍放大镜才能发现的缩松称为显微缩松,铸件有缩松的部位,在气密性实验时易渗漏。
(如图)产生的原因同以上缩孔。
1.1.4渣眼渣眼别名夹渣、包渣、脏眼、铁水温度不高、浇注挡渣不当造成。
渣眼的特征是:铸件浇注位置上表面的非金属夹杂物。
通常在加工后发现与气孔并存,孔径大小不一,成群集结。
(如图)产生的原因是:铁水纯净度差、除渣不净、浇注时挡渣不好,浇注系统挡渣作用差、浇注时浇口未充满或断流。
1.1.5砂眼砂眼是夹着砂子的砂眼。
砂眼的特征是:铸件内部或表面带有砂粒的孔洞(如图)。
产生的原因是:型砂损坏脱落,型腔内的散砂或砂块未清除干净、型砂紧实度差、浇注时冲坏型芯、浇注系统设计不当、型芯表面涂料不好等。
1.1.6铁豆铁豆是夹着铁珠的孔眼、别名铁珠、豆眼、铁豆砂眼等。
铸造缺陷及其对策.pptx

4、防止方法:
1、优化铸件结构设计,壁厚均匀,过渡平滑,肋板 厚度和分布的合理化; 2、优化浇注系统,控制浇温、浇速使铸件各部位冷 却速度趋于一致; 3、降低有害元素,合理控制合金元素添加量; 4、合理设定开箱时间。
5、补救措施:
1、开止裂孔后焊补; 2、采用工业修补剂; 3、如在重要面,报废重铸。
第16页/共28页
4、防止方法: 1、优化工艺设计,合理设置浇注系统; 2、考虑使用保温冒口、发热冒口; 3、优化铸件结构设计; 4、模拟分析(CAE); 5、调整成份; 6、控制炉料.
第17页/共28页
5、补救措施: 1、轻者焊补或采用工业修补剂; 2、重者报废重铸.
第18页/共28页
2.夹砂
的不同大小、形状的 孔洞缺陷的总称
缩孔 缩松
形状不规则,孔壁粗糙,常伴有粗大 树枝晶.夹杂物.裂纹等缺陷;
是细小的分散缩孔,断口呈海绵状;
疏松(显微缩松) 不作严格区分;
第3页/共28页
气 孔
第4页/共28页
针孔
2、裂纹、冷隔类缺陷
定义
缺陷名 称
特征
宏观(肉眼、PT、R T、MT、UT)或微 观(显微镜)判断发现 有开裂状纹络
1、铸件内部裂纹可采用超声波探伤(UT)、 磁粉探伤(MT)或射线探伤法(RT)进行检验; 2、铸件表面的裂纹可采用染色探伤法(PT)来 帮助确定,大部份是肉眼可直接发现的。
第24页/共28页
3、形成原因:
1、铸件结构或浇注系统设计不合理壁厚相差悬殊, 过渡圆角小; 2、铸造合金中有害元素(P、S等)超标,珠光体 元素过量; 3、铸件开箱过早,冷却过快; 4、合金收缩率大; 5、肋板设计不合理。
铸件常见缺陷修补及检验

铸件常见缺陷的鉴别、起因、修补及检验----------------------------------------------福联造型,呋喃树脂、酚醛树脂、覆膜砂专家1.缺陷的分类铸件常见缺陷分为孔眼、裂纹、表面缺陷、形状及尺寸和重量不合格、成份及组织和性能不合格五大类。
(注:主要介绍铸钢件容易造成裂纹的缺陷)1.1孔眼类缺陷孔眼类缺陷包括气孔、缩孔、缩松、渣眼、砂眼、铁豆。
1.1.1气孔:别名气眼,气泡、由气体原因造成的孔洞。
铸件气孔的特征是:一般是园形或不规则的孔眼,孔眼内表面光滑,颜色为白色或带一层旧暗色。
(如照片)气孔照片1产生的原因是:来源于气体,炉料潮湿或绣蚀、表面不干净、炉气中水蒸气等气体、炉体及浇包等修后未烘干、型腔内的气体、浇注系统不当,浇铸时卷入气体、铸型或泥芯透气性差等。
1.1.2缩孔缩孔别名缩眼,由收缩造成的孔洞。
缩孔的特征是:形状不规则,孔内粗糙不平、晶粒粗大。
产生的原因是:金属在液体及凝固期间产生收缩引起的,主要有以下几点:铸件结构设计不合理,浇铸系统不适当,冷铁的大小、数量、位置不符实际、铁水化学成份不符合要求,如含磷过高等。
浇注温度过高浇注速度过快等。
1.1.3缩松缩松别名疏松、针孔蜂窝、由收缩耐造成的小而多的孔洞。
缩松的特征是:微小而不连贯的孔,晶粒粗大、各晶粒间存在明显的网状孔眼,水压试验时渗水。
(如照片2)缩松照片2产生的原因同以上缩孔。
1.1.4渣眼渣眼别名夹渣、包渣、脏眼、铁水温度不高、浇注挡渣不当造成。
渣眼的特征是:孔眼形状不规则,不光滑、里面全部或局部充塞着渣。
(如照片3)渣眼照片3产生的原因是:铁水纯净度差、除渣不净、浇注时挡渣不好,浇注系统挡渣作用差、浇注时浇口未充满或断流。
1.1.5砂眼砂眼是夹着砂子的砂眼。
砂眼的特征是:孔眼不规则,孔眼内充塞着型砂或芯砂。
产生的原因是:合箱时型砂损坏脱落,型腔内的散砂或砂块未清除干净、型砂紧实度差、浇注时冲坏型芯、浇注系统设计不当、型芯表面涂料不好等。
(推荐)铸件外观缺陷图

铸件常见缺陷常见缺陷缺陷的分类:铸件常见缺陷分为孔眼、裂纹、表面缺陷、残缺类缺陷、形状及尺寸和重量不合格、成份及组织和性能不合格六大类。
1孔眼类缺陷孔眼类缺陷包括气孔、缩孔、缩松、渣眼、砂眼、等。
1.1.1气孔:别名气眼,气泡、由气体原因造成的孔洞。
铸件气孔的特征是:其表面一般比较光滑,主要呈梨形\圆形和椭圆形.一般在铸件表面露出,大孔常孤立存在,小孔则成群出现。
(如图)产生的原因是:来源于气体,炉料潮湿或绣蚀、表面不干净、炉气中水蒸气等气体、炉体及浇包等修后未烘干、型腔内的气体、浇注系统不当,浇铸时卷入气体、铸型等。
1.1.2缩孔缩孔别名缩眼,由收缩造成的孔洞。
缩孔的特征是:形状不规则,孔壁粗糙并带有技状晶,常出现在铸件最后凝固的部位,广义的缩孔包括缩松。
(如图)产生的原因是:金属在液体及凝固期间由于补缩不良而产生的孔洞,主要有以下几点:铸件结构设计不合理,浇铸系统不适当,冷铁的大小、数量、位置不符实际、铁水化学成份不符合要求,如含磷过高等。
浇注温度过高浇注速度过快等。
1.1.3缩松缩松别名疏松、针孔蜂窝、由收缩耐造成的小而多的孔洞。
缩松的特征是:铸件断面上出现的分散而细小的缩孔.助高倍放大镜才能发现的缩松称为显微缩松,铸件有缩松的部位,在气密性实验时易渗漏。
(如图)产生的原因同以上缩孔。
1.1.4渣眼渣眼别名夹渣、包渣、脏眼、铁水温度不高、浇注挡渣不当造成。
渣眼的特征是:铸件浇注位置上表面的非金属夹杂物。
通常在加工后发现与气孔并存,孔径大小不一,成群集结。
(如图)产生的原因是:铁水纯净度差、除渣不净、浇注时挡渣不好,浇注系统挡渣作用差、浇注时浇口未充满或断流。
1.1.5砂眼砂眼是夹着砂子的砂眼。
砂眼的特征是:铸件内部或表面带有砂粒的孔洞(如图)。
产生的原因是:型砂损坏脱落,型腔内的散砂或砂块未清除干净、型砂紧实度差、浇注时冲坏型芯、浇注系统设计不当、型芯表面涂料不好等。
1.1.6铁豆铁豆是夹着铁珠的孔眼、别名铁珠、豆眼、铁豆砂眼等。
常见压铸件缺陷及解决方法
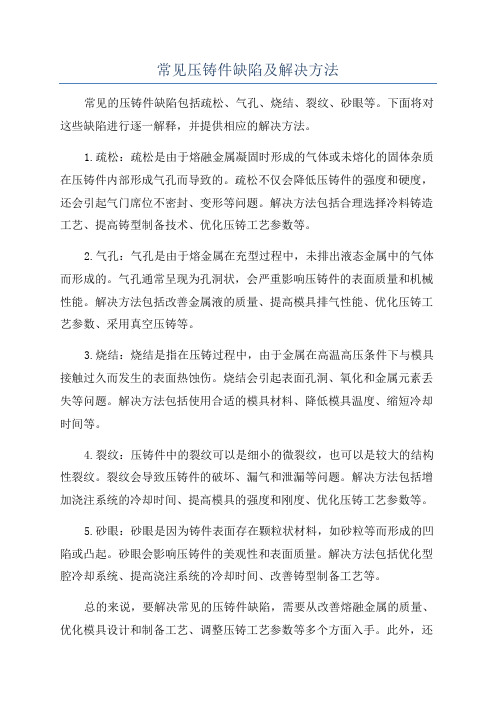
常见压铸件缺陷及解决方法常见的压铸件缺陷包括疏松、气孔、烧结、裂纹、砂眼等。
下面将对这些缺陷进行逐一解释,并提供相应的解决方法。
1.疏松:疏松是由于熔融金属凝固时形成的气体或未熔化的固体杂质在压铸件内部形成气孔而导致的。
疏松不仅会降低压铸件的强度和硬度,还会引起气门席位不密封、变形等问题。
解决方法包括合理选择冷料铸造工艺、提高铸型制备技术、优化压铸工艺参数等。
2.气孔:气孔是由于熔金属在充型过程中,未排出液态金属中的气体而形成的。
气孔通常呈现为孔洞状,会严重影响压铸件的表面质量和机械性能。
解决方法包括改善金属液的质量、提高模具排气性能、优化压铸工艺参数、采用真空压铸等。
3.烧结:烧结是指在压铸过程中,由于金属在高温高压条件下与模具接触过久而发生的表面热蚀伤。
烧结会引起表面孔洞、氧化和金属元素丢失等问题。
解决方法包括使用合适的模具材料、降低模具温度、缩短冷却时间等。
4.裂纹:压铸件中的裂纹可以是细小的微裂纹,也可以是较大的结构性裂纹。
裂纹会导致压铸件的破坏、漏气和泄漏等问题。
解决方法包括增加浇注系统的冷却时间、提高模具的强度和刚度、优化压铸工艺参数等。
5.砂眼:砂眼是因为铸件表面存在颗粒状材料,如砂粒等而形成的凹陷或凸起。
砂眼会影响压铸件的美观性和表面质量。
解决方法包括优化型腔冷却系统、提高浇注系统的冷却时间、改善铸型制备工艺等。
总的来说,要解决常见的压铸件缺陷,需要从改善熔融金属的质量、优化模具设计和制备工艺、调整压铸工艺参数等多个方面入手。
此外,还需要采用适当的检测手段,如金相分析、X射线检测、超声波检测等,对压铸件进行质量检验,及时排除可能存在的缺陷。
铸造缺陷鉴别
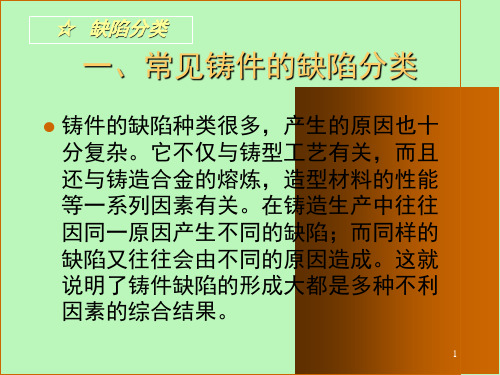
二、孔洞类铸造缺陷的鉴别
①、缩孔常见部位示意 图
17
二、孔洞类铸造缺陷的鉴别
②、缩松:铸件断面上 出现的分散而细小的 缩孔。有时借放大镜 才能发现。缩松部位 在水压试验时会渗漏 疏松:形状和缩松 相似,但孔洞更细小, 组织粗大,石墨粗大 等缺陷也可能导致铸 件组织疏松。
18
二、孔洞类铸造缺陷的鉴别
网状或脉状分布的毛 刺称脉纹。
24
三、多肉类缺陷的鉴别
2、抬 箱(抬 型): 铸件在 分型面 部位高 度和宽 度增大
25
三、多肉类缺陷的鉴别
3、涨砂: 铸件内、 外表面局 部胀大, 形成不规 则的瘤状 金属凸起 物。
26
三、多肉类缺陷的鉴别
4、冲砂: 铸件表面 上有粗糙 不规则的 金属瘤状 物,常位 于浇口附 近。在铸 件其它部 位则往往 出现砂眼。
36
六、残缺类缺陷
浇不到: 由于金 属液未 完全充 满型腔 而产生 的铸件 缺肉。
37
六、残缺类缺陷
2、缺 损:在 铸件清 理或搬 运时, 损坏了 铸件的 完整性。
38
七、尺寸、形状和重量差错类缺陷
1、变型: 由于收 缩应力 或型壁 变形、 开裂引 起的铸 件外形 和尺寸 与图纸 不符。
12
二、孔洞类铸造缺陷的鉴别
③、反应气孔:液态金 属的某些成分之间或 液态金属与铸型在界 面上发生化学反应产 生的气孔。 气孔位于铸件表皮 下,有的呈分散的针 状,有的隐藏在铸件 上部并伴有夹渣。
13
铸件气孔实例(1)
14
铸件气孔实例(2)
15
二、孔洞类铸造缺陷的鉴别
2、缩孔:形状为不规 则的封闭或敞露的孔 洞,孔壁粗糙并带有 枝状晶,且晶粒粗大。 常出现在铸件最后凝 固的部位(热节处)
铸造缺陷分类标准
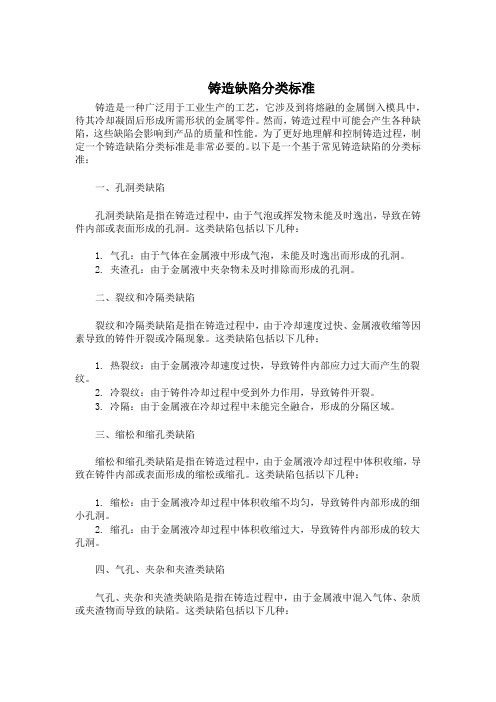
铸造缺陷分类标准铸造是一种广泛用于工业生产的工艺,它涉及到将熔融的金属倒入模具中,待其冷却凝固后形成所需形状的金属零件。
然而,铸造过程中可能会产生各种缺陷,这些缺陷会影响到产品的质量和性能。
为了更好地理解和控制铸造过程,制定一个铸造缺陷分类标准是非常必要的。
以下是一个基于常见铸造缺陷的分类标准:一、孔洞类缺陷孔洞类缺陷是指在铸造过程中,由于气泡或挥发物未能及时逸出,导致在铸件内部或表面形成的孔洞。
这类缺陷包括以下几种:1. 气孔:由于气体在金属液中形成气泡,未能及时逸出而形成的孔洞。
2. 夹渣孔:由于金属液中夹杂物未及时排除而形成的孔洞。
二、裂纹和冷隔类缺陷裂纹和冷隔类缺陷是指在铸造过程中,由于冷却速度过快、金属液收缩等因素导致的铸件开裂或冷隔现象。
这类缺陷包括以下几种:1. 热裂纹:由于金属液冷却速度过快,导致铸件内部应力过大而产生的裂纹。
2. 冷裂纹:由于铸件冷却过程中受到外力作用,导致铸件开裂。
3. 冷隔:由于金属液在冷却过程中未能完全融合,形成的分隔区域。
三、缩松和缩孔类缺陷缩松和缩孔类缺陷是指在铸造过程中,由于金属液冷却过程中体积收缩,导致在铸件内部或表面形成的缩松或缩孔。
这类缺陷包括以下几种:1. 缩松:由于金属液冷却过程中体积收缩不均匀,导致铸件内部形成的细小孔洞。
2. 缩孔:由于金属液冷却过程中体积收缩过大,导致铸件内部形成的较大孔洞。
四、气孔、夹杂和夹渣类缺陷气孔、夹杂和夹渣类缺陷是指在铸造过程中,由于金属液中混入气体、杂质或夹渣物而导致的缺陷。
这类缺陷包括以下几种:1. 气孔:由于金属液中混入气体而形成的气泡。
2. 夹渣:由于金属液中夹杂的固体颗粒物而形成的夹渣。
五、形状和表面类缺陷形状和表面类缺陷是指在铸造过程中,由于模具设计、制造或操作不当导致的铸件形状或表面质量的缺陷。
这类缺陷包括以下几种:1. 模具痕迹:由于模具设计或制造不当,导致铸件表面留下的痕迹。
2. 表面粗糙:由于金属液冷却过程中表面收缩不均匀,导致铸件表面粗糙。
铸件缺陷
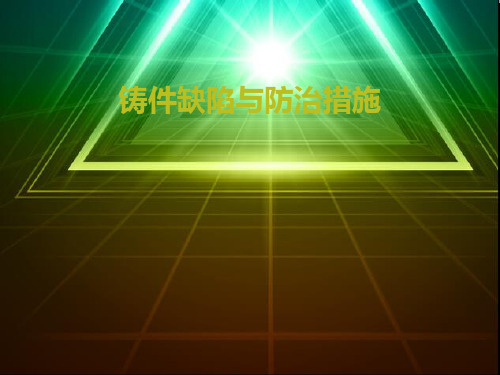
砂眼
造型工作
1、 造型时,不要一下把砂子放满砂箱内,先放一部分,每个位置都要充满 砂子后,用工具砸实,再放砂子充满,最后震实。防止砂型薄弱处在浇铸过程 中被铁水冲到型腔内部,导致砂眼。 2、造型开启砂箱时,要注意模型与砂型之间不能碰撞,防止砂型裂纹和掉 肉。 3、流涂时,砂型表面清理干净,防止浮砂与涂料粘在砂型表面,浇注时铁 水冲刷掉砂。
砂眼
砂眼
砂眼
砂眼
特征 : 在铸件内部或表面有充塞着型砂的孔眼。
砂眼
造成铸件砂眼的原因有哪些? 砂眼是指大型铸件内部或表面带有砂粒的孔洞。砂眼缺陷多产生在铸件浇注位置 的上表面。 砂眼主要是由于砂型等工序不够细致所造成的。具体表现在: 1、砂型和砂芯的强度太低,承受不住金属液的冲刷。 2、型腔内有薄尽弱部分,容易被金属液冲坏形成砂眼。 3、内浇道开设不当,使进入型腔的金属液产生很大的冲刷力,将型砂冲落而带 入型腔。 4、砂型和砂芯的烘干不良,不能保证足够的强度。 5、铸型搁置时间太长,降低了砂型砂芯的强度,增加铸件产生砂眼的可能性。 6、合型工作不够仔细,未将型腔中散落的型砂清除干净。
铸件缺陷与防治措施
铸造缺陷分类
一孔、眼类:气孔、缩孔、缩松、渣眼、砂眼等
二裂纹类:热裂、冷裂等
三表面缺陷类:粘砂、结疤、夹砂、冷隔等
四铸件形状、尺寸、重量不合格:多肉、浇不足、 抬箱、错箱、错芯、变形、损伤、尺寸超差、重 量超差等
五铸件成分、组织、性能不合格:化学成分不合 格、金相不合格、偏析、过硬、白口、物理机械 性能不合格等
砂眼
合箱工作
1、清除砂型、砂芯表面浮砂和尖角砂,清除浇铸系统内、排气孔内多余浮砂,砂型和 砂芯强度不够的,坚决不能使用,防止浇铸后造成砂眼。 2、刷涂料时,不能遗漏,均匀涂在砂型和砂芯表面,防止铁水冲击掉砂子。 3、烘烤砂型和砂芯时,火的强度适合,不能将砂芯和砂型烤酥,降低砂子强度。 4、合箱摆箱运输时,两个砂箱不能摞放,防止砂型之间撞击,产生裂纹,影响砂型强度。 5、流涂浇口杯时,清理表面浮砂,防止砂子粘在表面,。 6、放置浇口杯时,一定将浇口边上的尖角砂清理掉,防止高温铁水将造型时,不要一下把砂子放满砂箱内,先放一部分,每个位置都要充满 砂子后,用工具砸实,再放砂子充满,最后砸实。防止砂芯强度差,浇铸过程 中砂芯被铁水冲刷掉砂子。 2、造芯开芯盒时,要稳和对称,防止砂型与模型之间摩擦,产生裂纹和砂 型松动。 3、砂芯存放时,砂芯之间留有缝隙,防止砂芯与砂芯摩擦掉砂。 4、砂芯存放时,注意防水防潮,防止砂芯强度减弱。
- 1、下载文档前请自行甄别文档内容的完整性,平台不提供额外的编辑、内容补充、找答案等附加服务。
- 2、"仅部分预览"的文档,不可在线预览部分如存在完整性等问题,可反馈申请退款(可完整预览的文档不适用该条件!)。
- 3、如文档侵犯您的权益,请联系客服反馈,我们会尽快为您处理(人工客服工作时间:9:00-18:30)。
铸件缺陷分类
一、GB5611—1998《铸造名词术语》对铸件缺陷分类的规定:
1、多肉类缺陷;
2、孔洞类缺陷;
3、裂纹、冷隔类缺陷;
4、表面缺陷;
5、残缺类缺陷;
6、形状及重量误差类缺陷;
7、夹杂类缺陷;
8、性能、成分、组织不合格。
二、铸造缺陷术语(72项)
1、多肉类缺陷(8项)
1.1飞翅(飞边)
1.2毛刺
1.3抬型(抬箱)
1.4胀砂
1.5冲砂
1.6掉砂
1.7粘模多肉
1.8外渗物(外渗豆)
2、孔洞类缺陷(9项)
2.1气孔
2.2针孔
2.3表面针孔
2.4皮下气孔
2.5 缩孔
2.6 缩松
2.7 疏松
2.8渗漏
2.9呛火
3、裂纹、冷隔类缺陷(9项)3.1 冷裂
3.2 热裂
3.3 缩裂[收缩裂纹]
3.4 热处理裂纹
3.5网状裂纹[龟裂]
3.6 白点(发裂)
3.7 冷隔
3.8 浇注断流
3.9重皮
4、表面缺陷(14项)
4.1 鼠尾
4.2 沟槽
4.3 夹砂结疤(夹砂)
4.4涂料结疤
4.5 机械粘砂(渗透粘砂)
4.6 化学粘砂(烧结粘砂)
4.7 表面粗糙
4.8粘形
4.9龟裂[网状裂纹]、
4.10流痕[水纹]
4.11印痕
4.12皱皮
4.13 缩陷
4.14拉伤
5、残缺类缺陷(6项)
5.1 浇不到(浇不足)
5.2 未浇满
5.3 炮火
5.4损伤(机械损伤)
5.5型漏(漏箱)
5.6漏空
6、形状及重量误差类缺陷(6项)6.1 拉长
6.2 超重
6.3 变形
6.4 错型(错箱)
6.5 错芯
6.6 偏芯(漂芯)
7、夹杂类缺陷(9项)
7.1 夹杂物
7.2 冷豆
7.3 内渗物(内渗豆)
7.4 渣气孔
7.5 砂眼
8、性能、成分、组织不合格(11项)8.1 亮皮
8.2 菜花头
8.3 石墨漂浮
8.4 石墨集结
8.5 组织粗大
8.6 偏析
8.7 硬点
8.8 反白口
8.9 球化不良
8.10 球化衰退
8.11 脱碳。