南通模具设计达人浅析模具分型面及设计注意事项
分型面和分模面的异同点
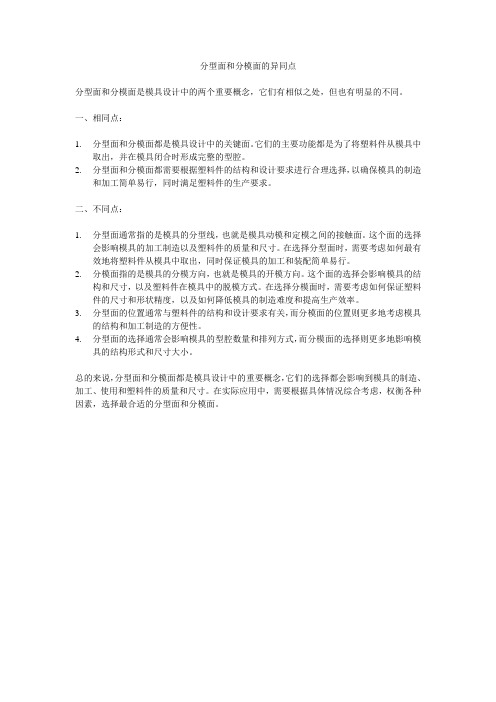
分型面和分模面的异同点
分型面和分模面是模具设计中的两个重要概念,它们有相似之处,但也有明显的不同。
一、相同点:
1.分型面和分模面都是模具设计中的关键面。
它们的主要功能都是为了将塑料件从模具中
取出,并在模具闭合时形成完整的型腔。
2.分型面和分模面都需要根据塑料件的结构和设计要求进行合理选择,以确保模具的制造
和加工简单易行,同时满足塑料件的生产要求。
二、不同点:
1.分型面通常指的是模具的分型线,也就是模具动模和定模之间的接触面。
这个面的选择
会影响模具的加工制造以及塑料件的质量和尺寸。
在选择分型面时,需要考虑如何最有效地将塑料件从模具中取出,同时保证模具的加工和装配简单易行。
2.分模面指的是模具的分模方向,也就是模具的开模方向。
这个面的选择会影响模具的结
构和尺寸,以及塑料件在模具中的脱模方式。
在选择分模面时,需要考虑如何保证塑料件的尺寸和形状精度,以及如何降低模具的制造难度和提高生产效率。
3.分型面的位置通常与塑料件的结构和设计要求有关,而分模面的位置则更多地考虑模具
的结构和加工制造的方便性。
4.分型面的选择通常会影响模具的型腔数量和排列方式,而分模面的选择则更多地影响模
具的结构形式和尺寸大小。
总的来说,分型面和分模面都是模具设计中的重要概念,它们的选择都会影响到模具的制造、加工、使用和塑料件的质量和尺寸。
在实际应用中,需要根据具体情况综合考虑,权衡各种因素,选择最合适的分型面和分模面。
模具分型面的设计和模仁大小的确定

一,分型面的设计分型面的设计和模仁的大小确定。
为了将产品从模具中取出,模具必须分成两个或数个部分,这些分离部分的接触表面通称为分型面分型面在模具中占有非常重要的位子,在设计模具时,首先考虑的就是这套模具分型面怎么做,如果连模具的分型都不知道,哪后须的工作也没法做了.到企业应聘模具设计时,往往要现场动手的就是做分型面,这关过不了,哪被录取的希望基本为零,如分型面做的又快又好,那你的成功率就大了.二.外观件的分型面的选取:1.肉眼观看.2.客户2D图纸指定.3.要保证母模胶位少,公模胶位多.如何利用UG软件选取分型面:1.利用拔模分析选择(粉红色与深兰色交界处或粉红色与绿色交界处)2.利用注塑模向导,自动抽取分型线.三.内置件的分型面的选取:1.要保证母模胶位少,母模尽量不要有机构.2.利用拔模分析分型面通常分为1.水平分型.2.垂直分型.3.倾斜分型(如图)4.台阶型分型面三,模仁和模架的确认。
产品的分模面大致确定以后,接下来就是确定模仁和模架的尺寸了模架尽量采用标准模架和标准配件,这样有利于缩短模具的制造周期和降低成本设计界经常用的模架品牌有:龙记(LKM),富得吧(FUTABA),名利,天祥,重村等当模具比较特殊或客户特别要求时,须对模架得形状,尺寸,材料作更改时,就需重新设计模架,这种情况下,定购模架时就需要向供应商提供详细得图面,并标注上与标准模架得不同之处,当然,这样得模架单价也较贵,供应商一般可以给客户提供架初加工和精加工,一般我们都要求进行粗加工及粗掏模穴即可一.模架和模仁尺寸的确定模架的大小主要取决于产品的大小和结构,对模具而言,在保证足够的强度下,模具设计的越紧凑越好.根据产品的外形(投影面积和高度)和结构(侧向分型和抽芯)来确定模仁的尺寸,确定好模仁的尺寸以后,就可以确定模架的尺寸了以下是模仁和模架尺寸确定的参考图表以上数据,只是作为设计时的一个参考,在设计时还要注意一下几点;1.当产品高度过高时(X>=D时),应适当加大D,加大值=(X-D)/2.2.有时为了冷却水道和固定螺丝的需要,也要对尺寸加以调整.3.当产品结构复杂,须特殊分型或顶出机构,或须加滑块等机构时,也应对模仁和模架尺寸进行修改.应适当加大模架和厚度.2.方铁高度的确定:方铁的高度应保证有足够的顶出行程和5-10MM预留量,以保证产品完全顶出,并且上顶板不会碰到公模板顶部3.模架整体尺寸的确定:模具定好以后,因对模架整体结构进行校核,看模架是否适合,所选定的或客户指定的注塑机的型号,包括外形尺寸,厚度,最大开模行程,及顶出方式和顶出行程等.4.模仁材料的选定;制品为一般的塑胶,如ABS,PP,PC,等,模仁因选用P20,NAK80,718.等预硬钢,如用高光洁度或透明的塑料制品,如PMMA,PS,AS,等因选用420等耐腐蚀不锈钢,含玻纤增强的塑胶,因选用H13,SKD61等热处理钢,当制品材料为PVC或POM和加了阻燃剂时因选用420,2316等不锈钢.具体在"模具用钢材"一节再详细学习。
proe模具设计指南(11章)第五章分型面设计及检测

分型面是指将模具型腔分开以便取出制品的分离曲面,即上、 下模的接触面,应当根据实际情况定义分型面。分型面的位 置选择与形状设计是否合理,不仅直接关系模具的复杂程度, 也关系着模具制件的质量、模具的工作状态和操作的方便程 度,因此分型面的设计是模具设计中最重要的一步。分型面 的位置不同,使得成型制件型腔的相对位置也不相同,一般 有三种基本的形式。
5.1 分型面概述
5.1.2 分型曲面特征
➢ 创建曲面
5.1 分型面概述
5.1.2 分型曲面特征
➢ 裁剪曲面
5.1 分型面概述
5.1.2 分型曲面特征
➢ 合并曲面
5.1 分型面概述
5.1.2 分型曲面特征
➢ 曲面延拓
5.2 创建分型面
分型面是一种功能强大的曲面特征,因为合并的曲面会自动 与其相连,因此分型面是任何附属曲面片的父特征。完成的 分型面必须与要分割的工件、夹模器或体积块完全相交。定 义分型面的时候,还往往要伴随着填充破孔的步骤,具体的 操作在以后的章节中会有详细的说明。 在Pro/E中创建分型面应当按照如下规则:
5.5 检测分型面
5.5.1 分型面检查
5.5 检测分型面
5.5.2 投影面积计算
➢ 分型面必须与工件或模具体积块完全相交,多个曲面 可合并一起。
➢ 不同的分型面可能会相交。
5.2 创建分型面
5.2.1 拉伸分型曲面
5.2 创建分型面
5.2.2 阴影分型曲面
5.2 创建分型面
5.2.3 裙边分型曲面
5.2 创建分型面
5.2.4 复制分型曲面
5.3 修改分型面
5.3.1 合并分型曲面
5.1 分型面概述
5.1.1 分型面设计的原则
模具设计双分型面侧抽芯单分型面
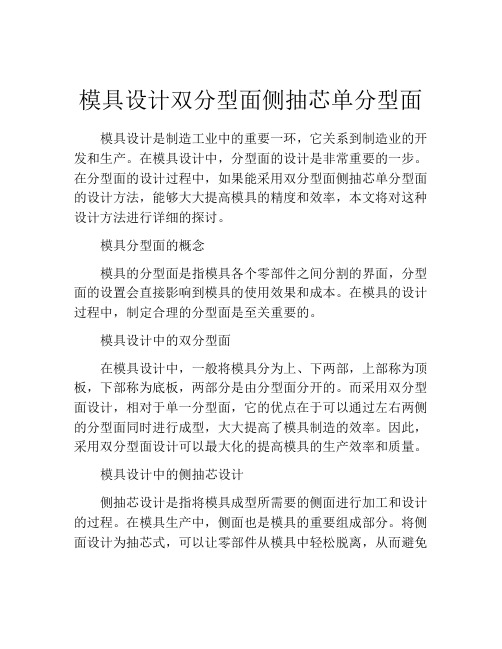
模具设计双分型面侧抽芯单分型面模具设计是制造工业中的重要一环,它关系到制造业的开发和生产。
在模具设计中,分型面的设计是非常重要的一步。
在分型面的设计过程中,如果能采用双分型面侧抽芯单分型面的设计方法,能够大大提高模具的精度和效率,本文将对这种设计方法进行详细的探讨。
模具分型面的概念模具的分型面是指模具各个零部件之间分割的界面,分型面的设置会直接影响到模具的使用效果和成本。
在模具的设计过程中,制定合理的分型面是至关重要的。
模具设计中的双分型面在模具设计中,一般将模具分为上、下两部,上部称为顶板,下部称为底板,两部分是由分型面分开的。
而采用双分型面设计,相对于单一分型面,它的优点在于可以通过左右两侧的分型面同时进行成型,大大提高了模具制造的效率。
因此,采用双分型面设计可以最大化的提高模具的生产效率和质量。
模具设计中的侧抽芯设计侧抽芯设计是指将模具成型所需要的侧面进行加工和设计的过程。
在模具生产中,侧面也是模具的重要组成部分。
将侧面设计为抽芯式,可以让零部件从模具中轻松脱离,从而避免了因为分离零部件不方便而产生的模具扭曲等问题,是一种相对于常规设计方式更加优越的方式。
双分型面侧抽芯单分型面设计在这种设计方式中,通过双分型面和侧抽芯,可以高效的完成模具的制作和使用。
该设计方式主要的思想就是将零部件置于模具中间部分(通常为核心),将其设计为单分型面,同时考虑到侧面的需要,再分别对两侧进行设计,设计两个分型面。
将型芯置于一个侧面中,借助侧面的抽芯器进行抽取,以实现模具的加工。
该设计方式主要的优点是可以降低模具的成本和加工难度,同时提升模具加工的效率。
通过双分型面,可以将加工时间和未成型部分的材料浪费减少到最低,同时,通过抽芯的方式,可以保证零部件轻松脱离,保证了模具加工过程中的稳定性和可靠性。
只要在设计过程中合理的采用双分型面侧抽芯单分型面的设计方法,可以明显提高模具制造的效率和质量,同时也能降低成本和减少因模具扭曲造成的浪费。
模具设计原则和核心以及注意事项
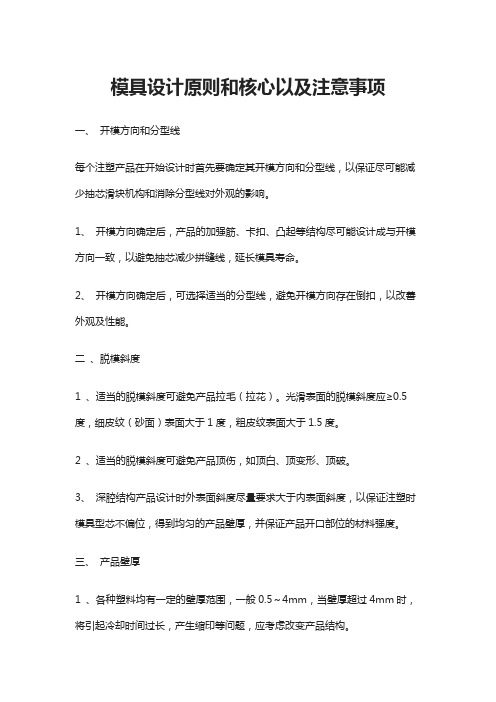
模具设计原则和核心以及注意事项 一、 开模方向和分型线每个注塑产品在开始设计时首先要确定其开模方向和分型线,以保证尽可能减少抽芯滑块机构和消除分型线对外观的影响。
1、 开模方向确定后,产品的加强筋、卡扣、凸起等结构尽可能设计成与开模方向一致,以避免抽芯减少拼缝线,延长模具寿命。
2、 开模方向确定后,可选择适当的分型线,避免开模方向存在倒扣,以改善外观及性能。
二 、脱模斜度1 、适当的脱模斜度可避免产品拉毛(拉花)。
光滑表面的脱模斜度应≥0.5度,细皮纹(砂面)表面大于1度,粗皮纹表面大于1.5度。
2 、适当的脱模斜度可避免产品顶伤,如顶白、顶变形、顶破。
3、 深腔结构产品设计时外表面斜度尽量要求大于内表面斜度,以保证注塑时模具型芯不偏位,得到均匀的产品壁厚,并保证产品开口部位的材料强度。
三、 产品壁厚1 、各种塑料均有一定的壁厚范围,一般0.5~4mm,当壁厚超过4mm时,将引起冷却时间过长,产生缩印等问题,应考虑改变产品结构。
2、壁厚不均会引起表面缩水。
3 、壁厚不均会引起气孔和熔接痕。
四、加强筋1、 加强筋的合理应用,可增加产品刚性,减少变形。
2、 加强筋的厚度必须≤ (0.5~0.7)T产品壁厚,否则引起表面缩水。
3、 加强筋的单面斜度应大于1.5°,以避免顶伤。
五、圆角1、 圆角太小可能引起产品应力集中,导致产品开裂。
2、圆角太小可能引起模具型腔应力集中,导致型腔开裂。
3、 设置合理的圆角,还可以改善模具的加工工艺,如型腔可直接用R刀铣加工,而避免低效率的电加工。
4 、不同的圆角可能会引起分型线的移动,应结合实际情况选择不同的圆角或清角。
六、 孔1 、孔的形状应尽量简单,一般取圆形。
2 、孔的轴向和开模方向一致,可以避免抽芯。
3 、当孔的长径比大于2时,应设置脱模斜度。
此时孔的直径应按小径尺寸(最大实体尺寸)计算。
4 、盲孔的长径比一般不超过4。
防孔针冲弯5 、孔与产品边缘的距离一般大于孔径尺寸。
模具设计分型面的选择及设计原则

模具设计分型面的选择及设计原则
模具,是将塑料或金属按照产品设计图纸要求的形状和尺寸加工出来
的工具。
模具的设计和制造是任何塑料或金属制品的有效生产的必要环节,型面的选择和设计原则对模具的质量和成型效果有着重要的影响。
一、模具型面选择
1、了解加工工件材料特性,首先要了解加工工件的材料特性,以便
根据材料的性能、加工精度需求等,决定模具的塑料型面类型。
模具的材
料种类有:定型塑料、半定型塑料、硬质塑料、弹性体塑料、铝热模塑料等。
2、根据产品型号和尺寸,确定型面形状和尺寸;
3、根据成型材料的特性,确定模具型面料的厚度;
4、根据产品成型过程尺寸的变化,确定型面的设计模式;
5、根据成型方式及模具结构,确定腔体的形状;
6、根据负压上模原理,确定模具型口的设计;
7、确定附件的设计,包括定位件、导流件等;
8、根据设计要求,制定模具的总体尺寸和技术要求;
9、根据成型工艺需要,确定模具表面处理方式。
二、模具设计原则
1、重点考虑模具的结构及制作的简单方便性,便于模具的调整和维护;。
最全注塑模具设计步骤以及注意事项的讲解
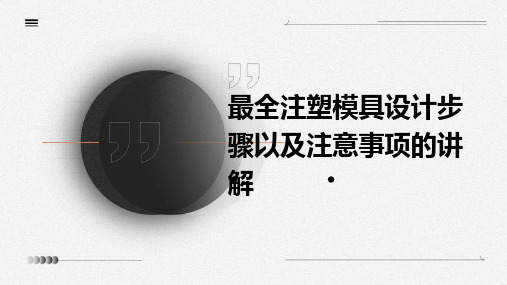
控铣削等加工方法,确保型芯、型腔的加工精度和表面质量。
02
浇口套、定位圈等关键零件加工工艺
采用高精度磨削、研磨等加工方法,保证零件的尺寸精度和形位公差。
03
导柱、导套等导向零件加工工艺
采用无心磨床、外圆磨床等高精度磨削设备,确保导向零件的精度和耐
磨性。
装配顺序和调试方法论述
装配顺序
遵循先下后上、先内后外的原则,先进行模架等支撑零件的装配,再进行型芯、型腔等成型零件的装配,最后进 行浇口套、定位圈等关键零件的装配。
根据模具结构确定加热装置的安装位置, 确保加热均匀且不影响模具其他功能。
油温机/水温机:适用于大型模具,加热 均匀,稳定性好。
03
06
考虑加热装置与冷却系统的协调,避免相 互干扰。
温度控制精度要求及实现途径
01
温度控制精度要求
02
根据制品要求确定温度控制精度,一般要求在±2℃ 以内。
03
对于高精度制品,温度控制精度要求更高,可达 ±1℃以内。
03
04
加强与客户和同行的沟 通和合作,不断提升服 务水平和市场竞争力。
培养高素质的人才队伍 ,为公司的可持续发展 提供有力保障。
感谢观看
THANKS
常见故障排查技巧和经验分享
常见故障排查技巧
介绍常见的注塑模具故障排查技巧,如检查模具磨损、清洗模具等。
经验分享
分享行业专家在注塑模具故障排除方面的经验和案例,提高读者解决问题的能力。
预防性维护策略推广
预防性维护策略
阐述预防性维护在注塑模具管理中的重要性 ,提出定期维护、保养和检查等策略。
推广实施
调试方法
在装配过程中,采用试装、试模等方法进行调试,确保模具各部件的配合精度和动作顺畅。对于复杂模具,还需 进行多次试模和调整,以达到最佳状态。
模具分型面的设计原则

模具分型面的设计原则1.参考工艺要求:模具的分型面必须符合产品的工艺要求。
分析产品的形状特点、结构特点、尺寸精度要求等,确定各个分型面的位置和形状。
2.尽量少的分型面:分型面越少,模具的制造成本越低,生产效率越高。
因此,在设计时应尽量减少分型面的数量,采用合理的设计来实现尽量少的分型面。
3.分型面的尺寸精度要求:分型面的尺寸精度要求直接影响模具的生产成本和加工难度。
因此,应根据实际需要合理确定分型面的尺寸精度要求。
4.考虑模具的制造工艺:在设计分型面时,需要考虑到模具的制造工艺,特别是模具的加工、组装和调试工艺。
尽量避免出现难于加工和调试的分型面,以减少模具的制造周期。
5.尽量采用直线分型面:直线分型面易于加工,可减少模具制造周期和成本。
因此,在设计分型面时,应尽量采用直线分型面,避免采用曲线或复杂的形状。
6.尽量采用平面分型面:平面分型面易于加工和调试,且模具的使用寿命较长。
因此,在设计分型面时,应尽量采用平面分型面,避免采用曲面或复杂的形状。
7.考虑产品的浇注和冷却:在设计分型面时,应考虑产品的浇注和冷却。
合理设计分型面的位置和形状,可使产品的浇注平稳,避免产生气泡或缺陷;同时,也能保证产品的冷却效果良好,使产品达到预期的性能和质量。
8.考虑模具的维护和维修:在设计分型面时,应考虑模具的维护和维修。
合理设计分型面的位置和形状,可使模具的保养和修复更加方便,减少模具的损耗和维修成本。
9.考虑产品的脱模:在设计分型面时,应考虑产品的脱模。
合理设计分型面的位置和形状,可使产品的脱模更加容易,减少脱模力和脱模损伤,提高模具的使用寿命。
总之,模具分型面的设计需要考虑到产品的形态特征和结构特点,参考工艺要求和模具制造工艺,以及产品的浇注、冷却和脱模等因素。
合理设计分型面,可提高模具的生产效率和成形质量,降低模具的制造成本和维护成本。
- 1、下载文档前请自行甄别文档内容的完整性,平台不提供额外的编辑、内容补充、找答案等附加服务。
- 2、"仅部分预览"的文档,不可在线预览部分如存在完整性等问题,可反馈申请退款(可完整预览的文档不适用该条件!)。
- 3、如文档侵犯您的权益,请联系客服反馈,我们会尽快为您处理(人工客服工作时间:9:00-18:30)。
南通模具设计达人浅析模具分型面及设计注意事项
模具分型面是什么?一般来说,模具都有两大部分组成:动模和定模(或者公模和母模),分型面是指两者在闭和状态时能接触的部分,也是将工件或模具零件分割成模具体积块的分割面,具有更广泛的意义。
分型面的设计直接影响着产品质量、模具结构和操作的难易程度,是模具设计成败的关键因素之一。
那么设计模具分型面时候,需要注意哪些呢?南通科迅教育资深老师来为大家详细讲解,下面以一个简单的产品分型为例。
1.我们看到这样一个盒盖类的产品,如图1
图1 通过,摆正、分析斜率以后我们就会看到下图2
图2
可以比较直观的看到冷暖色调,这样我们基本就可以确定产品的分型线如下图3中的黄色线
图3
2.分型面的一个原则是:简单,便于加工。
这时,我们使用拉升功能,对黄色边框线进行水平方向的拉升如图4
图4 操作后,会得到如下图5的效果
图5
3.这时,我们发现四个圆角的分型面未做。
设计圆弧角的面时,我们要注意尽量的做到光顺、平滑,不要出现大角度的扭曲。
这个造型中,我们首先使用桥接的功能。
在外圈做出一条过度线。
如图6,
图6
4.我们再使用N变曲面的功能,画出一个曲面,如下图7
图7
在艺术曲面实际的操作过程中,我们一定要注意,什么时候应该使用相切,这是将一个面与相邻的那个面过度的平顺与否的关键,如图8
图8
此时,我们一个圆角的面已经ok,那么剩下的3个圆角面,大家自己动手试验下。
分型面的制作有非常多的方式方法。
上述所说的只是其中一种,大家如果感兴趣,欢迎多和南通科迅教育老师们交流。