合成氨原料气的脱硫
化工工艺 合成氨除杂质

3.1二氧化碳的吸收方法概叙
主要方法有: (1) 物理吸收法 低温甲醇洗(Rectisol)法 常温甲醇洗(Amisol)法 MDEA法(物理—化学吸收) Selexol法(国外常用 NHD法(国内新开发)
(2) 化学吸收法 (3) 物理—化学吸收法
1) 物理吸收法 最早采用加压水脱除二氧化碳,经过减压将水再生。 此法设备简单,但脱除二氧化碳净化度差,出口二氧化碳一般在2% (体积)以下,动力消耗也高。近20年来开发有甲醇洗涤法、碳酸丙烯 酯法、聚乙二醇二甲醚法等,与加压水脱碳法相比,它们具有净化度 高、能耗低、回收二氧化碳纯度高等优点,而且还可选择性地脱除硫 化氢,是工业上广泛采用的脱碳方法。 (2) 化学吸收法 具有吸收效果好、再生容易,同时还能脱硫化氢等优 点。主要方法有乙醇胺法和催化热钾碱法。后者脱碳反应式为: K 2 CO3 CO 2 H 2 O 2 KHCO 3
工艺原理
一氧化碳变换反应式为: CO+H2O=CO2+H2 +Q (1-1) CO+H2 = C+H2O (1-2) 其中反应(1)是主反应,反应(2)是副反应, 为了控制反应向生成目的产物的方向进行,工业 上采用对式反应(1-1)具有良好选择性催化剂, 进而抑制其它副反应的发生。
合成氨工艺及反应原理简介

合成氨工艺及反应原理简介合成氨工艺采用烃类蒸汽转化法。
天然气经加压至4.05MPa,经预热升温在脱硫工序脱硫后,与水蒸汽混合,进入一段转化炉进行转化制H2,随后进入二段转化炉,在此引入空气,转化气在炉内燃烧放出热量,供进一步转化,同时获得N2。
工艺气经余热回收后,进入变换系统,将CO变为CO2,随后经脱碳、甲烷化反应除去CO和CO2,分离出的CO2送往尿素工艺。
工艺气进入分子筛系统除去少量水份,为合成氨提供纯净的氢氮混合气。
氢氮混合气经压缩至14MPa,送入合成塔进行合成氨的循环反应,少量惰性气体经过普里森系统分离进行回收利用。
产品氨送往尿素工艺和氨罐保存。
合成氨工艺的5个过程:1、天然气脱硫:R-SH+H2=RH+H2S H2S+ZnO=H2O(汽)+ZnS2、转化CH4+H20(汽)=CO+3H2 CH4+2H2O(汽)=CO2+4H2 (H2+ 1/2 O2=H2O)3、变换:CO+H2O(汽)=CO2+H24、脱碳:1)K2CO3+CO2+H2O⇔2KHCO32KHCO3⇔K2CO3+CO2+H2O2)甲烷化:CO+3H2=CH4+H2O CO2+4H2=CH4+2H2O5、N2+3H2=2NH31 脱硫系统工艺流程及原理1.1流程天然气进入界区后分为两路:一路作原料气,另一路作燃料气。
原料天然气进入原料气压缩机吸入罐116-F,除去携带的液体,经过原料气压缩机102-J被压缩到4.05MPa(G),经过原料气预热盘管预热到399℃,接着原料气与来自合成气压缩机103-J一段的富氢气混合。
经过Co-Mo加氢器101-D把有机硫转换成H2S,将3 ml/m3的有机硫转化为无机硫,原料气中总硫为30~90ml/m3左右,经氧化锌脱硫槽脱硫至总硫小于0.5mg/m3。
随后进入氧化锌脱硫槽,天然气中的硫化物被ZnO所吸附,制得合格原料气。
ZnO脱硫槽共二个,可以串联或并联操作,一般串联操作。
阀门及管线的配置可以使任何一个脱硫槽停止使用而另一个继续运转。
最新合成氨净化车间全厂流程、原理、设备及操作
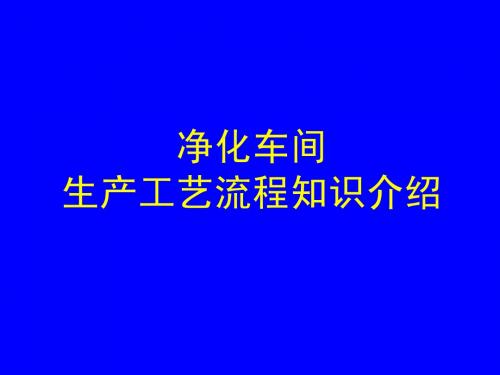
4、888脱硫贫液中悬浮硫含量低。溶液清亮有利于 降低脱硫系统的阻力。 5、888脱硫液对H2S的选择性好,当气体中的CO2/H2S 较高时,也能很好的把H2S脱除到规定的控制指标。 6、脱硫过程的副产物生成率低,吸收剂消耗低;硫 回收率高,副产硫磺纯度也高。 7、在888脱硫催化剂的作用下存在多硫化反应,并 在催化氧化时析出硫,再生时分离出去,具有抑 制和消除积硫堵塞管道与设备、填料的作用。 8、888脱硫催化剂的活性高、用量少、运行经济, 使用方便。不用添加其它助催化剂,预活化工艺 简单,时间短,无论以氨水或纯碱为吸收剂,均 能保持稳定的脱硫效率。
富液槽 贫液槽 再生槽 硫泡沫混合槽 溶液制备槽 液位调节器
H=7237 DN9000/DN8600/DN8000 高:(1700/2700)/2600/5000 DN3000 H=4578 V=29.5m3 DN2000 H=2200 V=6.9m3 DN1012×2000/DN728×1500/DN762×1612
副反应的影响和危害
1、因吸收H2S是靠Na2CO3来完成的,如果碳化 反应严重,溶液中Na2CO3含量过低,将影响 脱硫效率,并因溶液pH降低而使氧在再生 溶液中溶解度降低造成吸氧差,对析硫不 利。 2、若副反应严重,则碱耗剧增,有时虽大量 补碱也难以维持碱度在指标之内,直接影 响吸收与再生,造成生产被动和生产成本 增加。
工艺流程简述
1、气体流程 来自气柜的半水煤气(温度30℃左右、压力 0.0035MPa左右)经湿式电除尘进口水封进入湿式 电除尘进行除尘、除焦后,经湿式电除尘出口水 封、罗茨机进口水封进入罗茨风机加压到 0.049MPa后进入冷却清洗塔下部冷却段与来自冷 却清洗塔上部的循环水逆流接触。煤气冷却后进 入脱硫塔下部与来自贫液槽的脱硫液逆向接触进 行反应,脱去半水煤气中的硫化氢和部分有机硫, 经过脱硫后的半水煤气进入冷却清洗塔的清洗段 与清水逆向接触,清洗后的半水煤气进入静电除 焦器,然后去压缩一段入口。
合成氨 冷冻流程
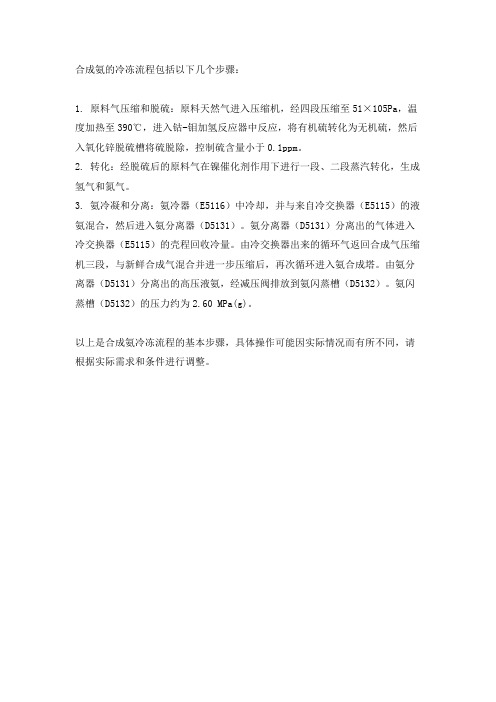
合成氨的冷冻流程包括以下几个步骤:
1. 原料气压缩和脱硫:原料天然气进入压缩机,经四段压缩至51×105Pa,温度加热至390℃,进入钴-钼加氢反应器中反应,将有机硫转化为无机硫,然后入氧化锌脱硫槽将硫脱除,控制硫含量小于0.1ppm。
2. 转化:经脱硫后的原料气在镍催化剂作用下进行一段、二段蒸汽转化,生成氢气和氮气。
3. 氨冷凝和分离:氨冷器(E5116)中冷却,并与来自冷交换器(E5115)的液氨混合,然后进入氨分离器(D5131)。
氨分离器(D5131)分离出的气体进入冷交换器(E5115)的壳程回收冷量。
由冷交换器出来的循环气返回合成气压缩机三段,与新鲜合成气混合并进一步压缩后,再次循环进入氨合成塔。
由氨分离器(D5131)分离出的高压液氨,经减压阀排放到氨闪蒸槽(D5132)。
氨闪蒸槽(D5132)的压力约为2.60 MPa(g)。
以上是合成氨冷冻流程的基本步骤,具体操作可能因实际情况而有所不同,请根据实际需求和条件进行调整。
合成氨气体脱硫技术进展

合成氨气体脱硫技术的进展摘要全面回顾了国内、外湿式氧化法和干法脱硫技术的发展及技术进展,分析了各种技术的优势及存在的问题。
关键词气体净化脱硫进展在合成氨生产过程中,无论采用何种原料路线(煤、油、天然气)、何种工艺技术,其粗合成气中都含有大量的CO2,以煤为原料的合成气中还含有多种硫化物。
CO2和硫化物对氨合成催化剂有很强的毒性,因此在合成气进入氨合成塔之前,需将CO2和硫化物脱除,称为脱硫、脱碳工艺。
几十年来,脱硫、脱碳工艺不断发展、进步,新工艺的开发和老工艺的改进大量涌现,本文不可能一一论述,只将典型的、常用的工艺及其进展加以汇总,供选择工艺时参考。
1 脱硫技术的发展现状原料气脱除硫化物技术分为干法和湿法两大类,湿法脱硫又分为湿式氧化法和胺法。
湿式氧化法是溶液吸收H2S后直接转化为单质硫,单质硫分离后溶液循环使用;胺法是将吸收的H2S在再生系统释放,然后将H2S送至克劳斯装置再转化为单质硫,溶液则循环使用。
湿法脱硫多用于合成氨原料气中大量硫化物的脱除,干法脱硫则多用作精脱且对无机硫和有机硫都有较高的净化度。
1. 1 湿式氧化法脱硫技术的进展湿式氧化法脱硫是将硫化氢在液相中氧化成元素硫并予以分离,其特点为[1]:可将H2S直接转化为单质硫;脱硫效率高,净化后的气体残硫量低;既可在常压下操作,又可在加压下操作;脱硫剂可以再生循环使用,运行成本低。
(1)蒽醌二磺酸钠法(ADA法)蒽醌二磺酸钠法称为Stretford法或ADA法,近年来的技术进步主要体现在脱硫气体的预处理、硫回收、废液处理等方面。
该法以钒作为脱硫的基本催化剂,并采用蒽醌2, 7 -二磺酸钠(ADA)作为还原态钒的再生载氧体,吸收液由碳酸盐作介质。
ADA法的不足之处主要有:①悬浮的硫颗粒回收困难,易造成过滤器堵塞;②副产物使化学药品耗量增大;③脱有机硫和HCN的效率较低;④有害废液处理困难,可能造成二次污染;⑤细菌易积累;⑥腐蚀严重。
为克服该工艺存在的问题,又相继开发了Sulfolyn法和Unisulf法。
年产20万吨合成氨脱硫工段工艺设计

吉林化工学院课程设计题目年产20万吨合成氨脱硫工段工艺设计教学院化工与材料工程学院专业班级化工0904学生姓名鞠洪清学生学号 09110437指导教师刘艳杰2012年12月27日前言本设计是年产20万吨合成氨脱硫工段的工艺设计。
对合成氨和脱硫工艺的发展概况进行了概述。
着重详细介绍了脱硫工段的工艺流程、工艺条件、生产流程、技术指标等内容。
就脱硫车间的工艺生产流程,各脱硫方法对比, 栲胶脱硫, 三废治理及利用, 反应条件对反应的影响, 物料流程, 影响的因素, 着重介绍化工设计的基本原理、标准、规范、技巧和经验。
设计总的指导思想是, 理论联系实际、简明易懂、经济实用。
目录前言 (1)摘要 (4)1.总论 (5)1.1.1栲胶法脱硫的发展 (6)1.1.2栲胶脱硫剂介绍 (6)1.1.3栲胶脱硫的反应机理 (7)1.1.4栲胶溶液的预处理 (7)1.1.5生产中副产品硫磺的回收工艺 (8)1.1.5.1劳斯法硫磺回收工艺 (8)1.1.5.2劳斯法硫磺回收工艺原理 (9)1.1.6生产中副产品硫磺的应用 (11)1.1.6.1硫磺的基本应用 (11)1.1.6.2硫磺的几种专门应用 (11)1.2文献综述 (14)1.2.1前言 (14)1.2.2脱硫法介绍 (15)2. 流程方案的确定 (16)2.1各脱硫方法对比 (16)2.2栲胶脱硫法的理论依据 (18)2.3工艺流程方框图 (19)3. 生产流程的简述 (20)3.1简述物料流程 (20)3.1.1气体流程 (20)3.1.2溶液流程 (20)3.1.3硫磺回收流程 (20)3.2工艺的化学过程 (22)3.3反应条件对反应的影响 (23)3.3.1影响栲胶溶液吸收的因素 (23)3.3.2影响溶液再生的因素 (25)3.4工艺条件的确定 (26)3.4.1溶液的组成 (26)3.4.2喷淋密度和液气比的控制 (26)3.4.3温度 (27)3.4.4再生空气量 (27)4. 物料衡算和热量衡算 (27)4.1物料衡算 (27)4.2热量衡算 (30)5. 车间布置说明 (34)6. 三废治理 (35)6.1废水的处理............................................................................. 错误!未定义书签。
工业制氨气的方法
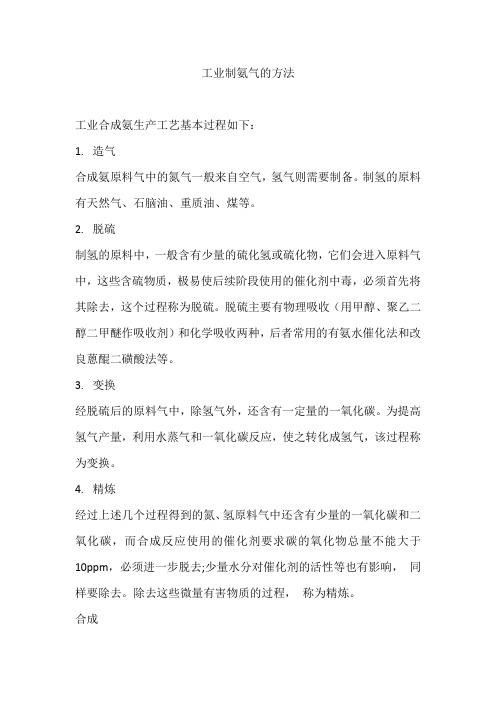
工业制氨气的方法
工业合成氨生产工艺基本过程如下:
1.造气
合成氨原料气中的氮气一般来自空气,氢气则需要制备。
制氢的原料有天然气、石脑油、重质油、煤等。
2.脱硫
制氢的原料中,一般含有少量的硫化氢或硫化物,它们会进入原料气中,这些含硫物质,极易使后续阶段使用的催化剂中毒,必须首先将其除去,这个过程称为脱硫。
脱硫主要有物理吸收(用甲醇、聚乙二醇二甲醚作吸收剂)和化学吸收两种,后者常用的有氨水催化法和改良蒽醌二磺酸法等。
3.变换
经脱硫后的原料气中,除氢气外,还含有一定量的一氧化碳。
为提高氢气产量,利用水蒸气和一氧化碳反应,使之转化成氢气,该过程称为变换。
4.精炼
经过上述几个过程得到的氮、氢原料气中还含有少量的一氧化碳和二氧化碳,而合成反应使用的催化剂要求碳的氧化物总量不能大于10ppm,必须进一步脱去;少量水分对催化剂的活性等也有影响,同样要除去。
除去这些微量有害物质的过程,称为精炼。
合成
经过上述处理并经过多级压缩后达到指定高压(一般为32MPa)的氮、氢混合气,送到合成塔中在一定温度(~500℃)范围内,经催化剂(Fe2O3为主体)作用,进行合成反应。
粗原料气的净化—硫化物的脱除(合成氨生产)

由脱随塔流出的富液,送至脱硫闪蒸槽而后进人H2S提浓塔,塔顶进液 为脱硫贫液,中部进液为脱硫富液。在H2S提浓塔后还有一个闪蒸槽。 闪 蒸气压缩后作为H2S提浓塔的气提气。由H2S提浓塔出来的气体含H2S25% 左右,可直接送至克劳斯法制硫装置。由脱碳闪蒸槽出来的闪蒸气含CO2 99%左右,可作尿素生产原料之用。
本书仅对近年来备受人们关注的Slexol怯(中国称为NHD法)脱硫作简介。此法 1965 年首先由美国Alied Chenical公司采用,至今已有 40多套装置在各国运 行。脱硫剂的主体成分为聚乙二醇二甲醒,商品名为Selexol。它是一种聚乙 二醇二甲醚同系物混合体。分子式为CH3O CH-O- CH2 nCH。 式中n为3-9。 平均相对分子质量为22-242。各种同系物的质量分数,%大致如下。
3、脱硫剂活性好,容易再生,定额消耗低
脱硫剂活性好,容易再生,可以降低生产的费用,符合工业生 产的经济性。
4、不易发生硫堵
硫堵:进脱硫塔气体的成分不好,杂志耗量较高;反应时析出的 硫不能及时排出;脱硫塔淋喷密度不够;再生空气量不足,吹风强度 低等原因造成硫堵。
5、脱硫剂价廉易得
采用最多的是廉价的石灰、石灰石和用石灰质药剂配制的碱性溶 液。以提高生产的经济性。
酞菁钴价格昂贵,但用量很少,脱硫液中PDS含量仅在数十个cm3/ m3左右。PDS的吨氨耗量一般在1.3-2.5g左右,因而运行的经济效益也较 显著。
此法也可脱除部分有机硫。若脱硫液中存在大量的氰化物,仍能导致 PDS中毒,但约经60h靠其自身的排毒作用,其脱硫活性可以逐渐恢复。 PDS对人体无毒,不会发生设备硫堵,无腐蚀性。
再
较高的温度有利于硫磺的分离,使析出的硫易于凝聚,
生
- 1、下载文档前请自行甄别文档内容的完整性,平台不提供额外的编辑、内容补充、找答案等附加服务。
- 2、"仅部分预览"的文档,不可在线预览部分如存在完整性等问题,可反馈申请退款(可完整预览的文档不适用该条件!)。
- 3、如文档侵犯您的权益,请联系客服反馈,我们会尽快为您处理(人工客服工作时间:9:00-18:30)。
—钴(Co)钼(Mo)加氢-氧化锌脱硫
12化工三班 1203023028 李俊旗
合成氨原料气的净化
氨合成反应需要高纯度的H2和N2。 无论以固体(煤或焦炭)还是用烃 类(天然气、石脑油等)为原料获 得的原料气中,都含有一氧化碳、 二氧化碳、硫化物等不利于合成反 应的成分,需要在进入合成塔之前 除去。
硫化物的危害
1.影响催化剂活性导致其中毒 转化催化剂 变换催化剂 氨合成催化剂 甲醇合成催化剂 2.腐蚀设备和管道
目的:延长催化剂使用寿命,减少设备腐蚀。还 可副产硫磺
二、硫化物的脱除方法 •硫化氢溶解在脱硫溶剂中再反应-化学法 • 硫化氢溶解在特定溶剂中-物理法 • 既有物理溶解又有化学反应-物理、化学法
外观 尺寸,mm 堆密度,kg/L 比表面,m2/g 孔容,ml/g 平均孔半径,Å
深灰色球 Φ3.5~4.5 0.8~1.0 40~60 0.43 215
备 注
用于脱除微 只用于在石 用于气、液 量H2S和“反应 脑油为原料的 态烃高温脱硫, 性”有机硫以保 大型氨厂加氢 对不含复杂有 护低温变换催 转化之后 机硫的天然气 化剂 亦可单独使用
• 钴钼加氢法还可将烯烃加氢转变成饱和烷 烃,从而减少蒸汽转化工序析碳的可能。
• 催化剂:以氧化铝(Al2O3)为载体,由氧化钴
(CoO)和氧化钼(MoO3)组成。Mo含量为 5~13%,Co含量为1~6%。钴钼催化剂 须经硫化后才具有相当的活性。经硫化后 的活性组分主要为MoS2,Co9S8。
• 脱硫剂的组成
•
附. 氧化锌脱硫剂 的化学组成和物理性质
型 化 学 组 成, % 号 ZnO MgO MnO2 SiO2 Al2O3 T302 80~85 6~8 3~5 T(T)303 ≥99 T304 ≥90 6~8 T305 >95 C7-2 75~80
10~12 8~10
白色条状 Φ4×4~6 1.30~1.45 6~9 ≥0.235 770 白色条状 Φ5×5~10 1.15~1.35 10~20 0.30~0.36 320 白色条状 Φ4×4~10 1.10~1.30 28 0.40 284 白色条状 Φ4×4~6 1.1~1.2 20~35 0.3 200
• 工艺条件:操作条件,温度一般在300~
400℃,压力0.7~7.0MPa,入口气态烃空 速为500~2000h-1,液态烃空速0.5~6h-1, 加氢量一般按照保持反应后气体中有5~ 10%氢为准。
• ②氧化锌脱硫
• 基本原理: • • • H2S+ZnO=ZnS+H2O C2H5SH+ZnO=ZnS+C2H4+H2O H2+ C2H5SH+ZnO= ZnS+C2H6+H2O ZnO(80-90%) Al2O3
钴(Co)钼(Mo)加氢转化串联氧化锌脱硫工艺流程图
• 在实际操作中,氧化锌常采用两套吸收设 备,一台操作,一台备用。当操作中的一 台吸硫能力下降时,更换到备用设备;为 减少吸硫剂的使用量,通常将设备出口的 氧化锌重新装入吸硫设备的入口处,即从 设备套数和流程设置解决问题。
•与固体物质进行反应(催化转化法)-化学法
湿 法 脱 硫
• 被吸附在固体吸附剂上再脱附(吸附法)-物理法
干法脱硫
干法脱硫
适用于含S量较少、净化度高的情况
氧化锌法、钴钼加氢法、氢氧化铁法、活性碳法等
湿法脱硫
适用于含S量较大、净化度要求低的场合
化学吸收法、物理吸收法和化学物理综合吸收法等
钴(Co)钼(Mo)加氢-氧化锌脱硫
可与加氢转 化催化剂串联 使用,也可用 作低温变换保 护剂
可使S含量 降到0.1ppm 以下,可单 独使用,也 可与加氢转 化催化剂串 联使用
影响硫容的因素:
硫容:单位体积 脱硫剂所能吸收 的硫,kg/m3
0
10000
20000
温度
汽气比
影响因素
空速
氧化锌脱硫示意图
*氧化锌脱硫只能脱除硫化氢和一些简单的有 机硫化物。不能除去噻吩等复杂的有机硫化 物。而所有的有机硫化物在钴(Co)钼(Mo)催 化剂作用下能全部加氢转化成容易脱除的硫 化氢。 *工业生产中一般采用钴(Co)钼(Mo)加氢转化 串联氧化锌脱硫工艺,先将有机硫化物转化 成无机硫化物硫化氢,再脱除硫化氢,可使 总的硫含量降到0.1cm3/m3以下。
①钴(Co)钼(Mo)加氢 原理:在300-400 ℃温度下,采用钴钼加氢脱硫催化剂, 使有机硫与氢反应生产容易脱除的硫化氢和烃。再用氧化
锌吸收硫化氢,即可达到较好的脱硫效果。
反应:RSH+H2=RH+H2S RSR’+2H2=RH+R’H+ H2S COS+H2=CO+H2S CS2+4H2=CH4+2H2S