合成氨原料气的制备
合成氨生产原料气的制取
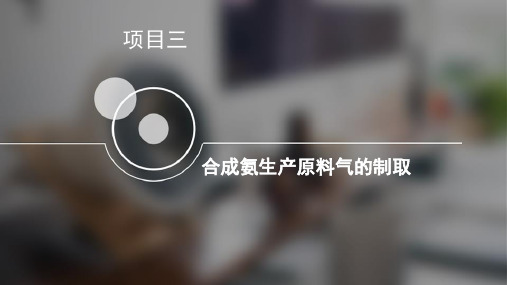
3. 蒸汽氧比 蒸汽与氧的比例,影响气化温度及煤气 的组成。蒸汽氧比增大,煤气中氢和一氧化 碳增加。但炉温下降,使甲烷含量提高。 一般控制在5~8kg/m3。
五、固定层连续气化岗位安全操作及环保措施
(1).岗位特点 见任务一“五” (2). 岗位物料的性质
主要物料性质见任务一第五点,还有氧气,氮气。氧气为助燃剂, 和氧化剂。
(3)、本岗位主要安全事故及处理方法
事故 炉内结渣,
炉顶出口煤气与灰 锁温度同时升高
现象
处理方法
(1)灰中渣块大
(1)提高汽氧比,与灰熔点相适应。
(2)炉箅电机电流超高或液压驱 (2)降低炉箅转速,加大负荷。
动的液压压力高
(3)CO2偏低
(1)出现沟流;出口煤气温度高, (1)降低负荷,增加汽氧比,短时增加炉箅转速来破坏风洞,检查气化炉
③炉箅。其作用是维持燃料层的 向下移动,均匀分布气化剂, 排灰入灰锁,破碎灰渣。
(2)煤锁和灰锁 气化炉顶设有煤锁,进行间歇 加煤 。 炉底设有灰锁,将灰渣 定期排入灰斗
图3-4 鲁奇炉 1、煤箱 2、分布器 3、水 夹槽4、灰箱 5、洗涤器
(3)灰锁膨胀冷凝器 灰锁膨胀 冷凝器的作用是灰锁泄压时将含有 的灰尘和水蒸气冷凝、洗涤下来, 使泄压气量大幅减少,同时保护 泄压阀门不被含有灰尘的水蒸气 冲刷磨损,延长阀门的使用寿命。
润滑油供油不足
煤锁温度正常而炉内缺煤,温度 高
灰锁下阀打不开,下灰少
降炉负荷,短时增加炉箅转速,若无效停车处理。
(1)降炉负荷,降汽氧比 (2)减小供气量,维持好煤气炉的压力。 (3)减少气化剂,转动炉箅。 (4)气化炉停车处理。
检查润滑油泵,注油点压力、管线是否通畅,调整油泵出口压力。
如何制备氨气

如何制备氨气制备氨气是一种常见的化学实验操作,可以用于许多化学反应和工业生产过程。
以下是制备氨气的一种方法:1.准备原料:氢气和氮气。
这两种气体在空气中含有较高的比例,可以通过分离空气来获得。
氢气可以通过水电解或酸碱中和反应制备,氮气则可以从空气中分离得到。
2.收集氢气和氮气:将氢气和氮气分别收集在两个储气罐中。
氢气罐应采用防爆设计,以防止氢气泄漏引发事故。
氮气罐则需要有良好的密封性能,以确保氮气不受污染。
3.准备合成氨的反应器:选用一个合适的反应器,如铁催化剂的固定床反应器或浆态床反应器。
反应器应具有良好的热传导性能和耐腐蚀性能。
4.加热反应器:将反应器加热至适当的温度,通常在400-600℃之间。
加热源可以是电热元件、蒸汽加热或导热油加热。
5.控制压力和流量:将氢气和氮气分别引入反应器,并控制压力和流量。
氢气和氮气的摩尔比应为1:3,以实现较高的氨合成收率。
6.添加催化剂:在反应器中加入适量的铁催化剂,如Fe-K催化剂。
催化剂可以提高反应速率,促进氨的合成。
7.监测反应过程:通过在线分析仪器监测反应器中的气体组成和温度。
当达到合适的氨合成收率时,可以调整氢气和氮气的流量,以维持反应器的稳定运行。
8.收集氨气:将合成氨气从反应器中引出,通过冷却装置将氨气液化。
液化后的氨气可以储存或直接用于工业生产。
9.废弃物处理:对反应产生的废弃物进行处理,如废水处理、废气处理等。
废水处理可以采用生物降解、化学氧化等方法;废气处理可以采用吸附、燃烧等方法。
10.安全防护:在整个制备氨气的过程中,要严格遵守安全规程,确保实验人员和设备的安全。
穿戴防护设备、定期检查设备运行状况、设置安全防护措施等都是必不可少的。
通过以上步骤,可以实现氨气的制备。
需要注意的是,在实际操作过程中,要根据实验条件和设备情况进行适当调整。
同时,了解氨气的性质和危险性,严格遵守安全规程,以确保实验的顺利进行。
合成氨原料气制取 第一节
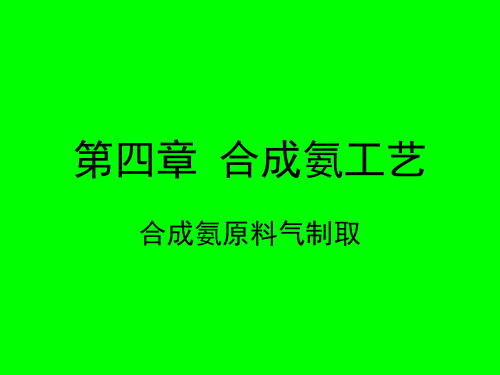
• CH4 + H2O=3H2 + CO ΔH0=206.4KJ
• CH4 + 2H2O=4H2 + CO2 ΔH0=165.3KJ
• 把转化后的气体送入用耐火材料衬里的二段转化 炉,同时向二段转化炉送入3.5MPa、450℃的空气 (空气加入量根据合成氨所需氮量配加)与一段转 化气汇合,这时空气中的全部氧和转化气中的部 分氢发生燃烧放热反应:
4.1.2 烃类蒸汽转化法
• 以轻质烃(天然气、油田气、炼厂气、轻油等)为 原料生产合成氨原料气。
• 各种低碳烃类与水蒸气反应都需经过甲烷蒸汽转 化阶段。故可用甲烷蒸汽转化代表气态烃类蒸汽 转化。
• 烃类蒸汽转化法应用最多的是加压两段催化转化法:
天然气(含氢0.25至0.5%),在 3.6MPa下被烟道气 预热到380℃左右,在脱硫器中经脱硫 (总硫含量小 于0.5μg/g)。然后在3.8MPa下配入3.5倍体积的中压水 蒸气,进一步加热到500℃左右,进入α-Al2O3为载体 的镍催化剂反应管(由耐热合金制成)。管外炉膛内用 天然气或其它气体加热, 90%的CH4气体在反应管 内于650至800℃下发生转化反应。
间歇式制半水煤气的主要步骤:
a. 空气吹风 b. 上吹制气 c. 下吹制气 d. 二次上吹 e. 空气吹净
• a. 空气吹风
空气从造气炉底部吹入,主要目的是送风发 热,提高炉温,吹风后的气体去废热锅炉回收热 量后放空。
• b. 上吹制气
水蒸气从炉底吹入生产水煤气,主要目的是 制气,制得的水煤气通过废热锅炉回收热量,除 尘、洗涤后送入气柜。
重质烃部分氧化法涉及的析碳反应:
CH4 = C + 2H2 2CO = CO2 + C CO + H2 = H2O + C
合成氨原料气的生产

合成氨原料气的生产一.煤气化(1)气化原理煤在煤气发生炉中由于受热分解放出低分子量的碳氢化合物,而煤本身逐渐焦化,此时可将煤近似看作碳。
①反应速率以空气为气化剂C+O2→CO2 △H=-393.770kJ/molC+1/2O2→CO △H=-110.595kJ/molC+CO2→2CO △H=172.284kJ/molCO+1/2O2→CO2 △H=-283.183kJ/mol在同时存在多个反应的平衡系统,系统的独立反应数应等于系统中的物质数减去构成这些物质的元素数。
以水蒸气为气化剂C+H2O→CO+H2 △H=131.39kJ/molC+2H2O→CO2+2H2△H=90.20kJ/molCO+H2O→CO2+H2△H=-41.19kJ/molC+2H2→CH4△H=-74.90kJ/mol②反应速率气化剂和碳在煤气发生炉中的反应属于气固相非催化剂反应。
随着反应的进行,碳的粒度逐渐减小,不断生成气体产物。
反过程一般由气化剂的外扩散、吸附、与碳的化学反应及产物的吸附,外扩散等组成。
反应步骤分为:A. C+O2→CO2 的反应速率研究表明,当温度在775O C以下时,其反应速率大致表示为:R=ky o2式中 r-碳与氧生成二氧化碳的反应速率k-反应速率常数y o2- 氧气的速率B.C+CO2→2CO的反应速率此反应的反应速率比碳的燃烧反应慢得多,的一级反应。
在2000O C以下属于化学反应控制,反应速率大致是CO2C.CO+H2O→CO2+H2的反应速率碳与水蒸气之间的反应,在400-1000O C的温度范围内,速度仍较慢,因此为动力学控制,在此范围内,提高温度是提高反应速率的有效措施。
二.制取半水煤气的工业方法由以上可知,空气与水蒸气同时进行气化反应时,如不提供外部热源,则气+CO)的含量大大低于合成氨原料气的要求。
为解决气体成分与热量化产物中(H2平衡这一矛循,可采用下列方法:(1)外热法如利用原子能反应堆余热或其他廉价高温热源,用熔融盐、熔融铁等介质为热载体直接加热反应系统,或预热气化剂,以提供气化过程所需的热能。
合成氨的工艺流程

工艺流程 1.合成氨的工艺流程(1)原料气制备将煤和天然气等原料制成含氢和氮的粗原料气。
对于固体原料煤和焦炭,通常采用气化的方法制取合成气;渣油可采用非催化部分氧化的方法获得合成气;对气态烃类和石脑油,工业中利用二段蒸汽转化法制取合成气。
(2)净化对粗原料气进行净化处理,除去氢气和氮气以外的杂质,主要包括变换过程、脱硫脱碳过程以及气体精制过程。
①一氧化碳变换过程在合成氨生产中,各种方法制取的原料气都含有CO,其体积分数一般为12%~40%。
合成氨需要的两种组分是H2和N2,因此需要除去合成气中的CO。
变换反应如下:CO+H2OH→2+CO2 =-41.2kJ/mol 0298HΔ由于CO变换过程是强放热过程,必须分段进行以利于回收反应热,并控制变换段出口残余CO含量。
第一步是高温变换,使大部分CO转变为CO2和H2;第二步是低温变换,将CO 含量降至0.3%左右。
因此,CO变换反应既是原料气制造的继续,又是净化的过程,为后续脱碳过程创造条件。
②脱硫脱碳过程各种原料制取的粗原料气,都含有一些硫和碳的氧化物,为了防止合成氨生产过程催化剂的中毒,必须在氨合成工序前加以脱除,以天然气为原料的蒸汽转化法,第一道工序是脱硫,用以保护转化催化剂,以重油和煤为原料的部分氧化法,根据一氧化碳变换是否采用耐硫的催化剂而确定脱硫的位置。
工业脱硫方法种类很多,通常是采用物理或化学吸收的方法,常用的有低温甲醇洗法(Rectisol)、聚乙二醇二甲醚法(Selexol)等。
粗原料气经CO变换以后,变换气中除H2外,还有CO2、CO和CH4等组分,其中以CO2含量最多。
CO2既是氨合成催化剂的毒物,又是制造尿素、碳酸氢铵等氮肥的重要原料。
因此变换气中CO2的脱除必须兼顾这两方面的要求。
一般采用溶液吸收法脱除CO2。
根据吸收剂性能的不同,可分为两大类。
一类是物理吸收法,如低温甲醇洗法(Rectisol),聚乙二醇二甲醚法(Selexol),碳酸丙烯酯法。
合成氨原料气的制备方法

合成氨原料气的制备方法合成氨是一种重要的化工原料,广泛应用于合成尿素、硫酸铵、硝酸铵等农业肥料的生产中,同时也是用于生产合成纤维、合成塑料、合成染料等化工产品的重要原料。
合成氨的制备方法主要有两种,分别是哈伯-玻苏曼法和氮氢氧化物还原法。
1.哈伯-玻苏曼法哈伯-玻苏曼法是最常用的工业合成氨的方法,其主要反应是氮气和氢气在高温高压条件下通过催化剂合成氨。
具体步骤如下:(1)空气的预处理:将气源空气经过压缩、过滤、去除水分和二氧化碳等处理后,进入空气分离机,将氮气与氧气分离。
(2)硝氧化:对分离出来的氮气进行硝化反应,将氮气转化为二氧化氮。
通过将氮气与氧气在高温高压条件下经过氧化催化剂的催化作用,生成二氧化氮。
(3)合成氨反应:将已经生成的二氧化氮与氢气混合,并通过冷凝和压缩等操作,将混合气体送入空气反应器中。
在高温高压条件下,通过铁-铁-铁铬催化剂的作用,二氧化氮与氢气发生反应,生成氨气。
2.氮氢氧化物还原法氮氢氧化物还原法是一种相对新的合成氨方法,其原理是将氮气和氢气通过一系列反应和催化作用转化为合成氨。
(1)氮气的预处理:与哈伯-玻苏曼法相似,将气源空气经过处理,将氮气与氧气分离。
(2)硝化反应:将分离出来的氮气与氧气在高温高压条件下经过氧化催化剂的催化作用,生成二氧化氮。
(3)氮氧化物的催化还原:将二氧化氮经过一系列反应步骤,包括氧化、还原和催化等多个阶段的循环反应。
氧化阶段是将二氧化氮与空气中的氧气经过催化剂的作用,部分转化为三氧化二氮。
还原阶段是将三氧化二氮与氢气在高温高压条件下反应,生成亚氮化合物。
催化阶段则是将亚氮化合物经过合适的催化剂作用,转化为氨气。
这两种方法中,哈伯-玻苏曼法是目前工业上最常用的方法,其具有规模大、成本低的优势。
氮氢氧化物还原法则相对较新,其具有可持续发展的潜力,在节能减排、降低工艺复杂度等方面具有一定优势。
随着科技的不断进步,相信合成氨制备方法将会得到更多的改进和创新。
合成氨工艺

合成氨工艺————————————————————————————————作者:————————————————————————————————日期:合成氨工艺流程(1)原料气制备将煤和天然气等原料制成含氢和氮的粗原料气。
对于固体原料煤和焦炭,通常采用气化的方法制取合成气;渣油可采用非催化部分氧化的方法获得合成气;对气态烃类和石脑油,工业中利用二段蒸汽转化法制取合成气。
(2)净化对粗原料气进行净化处理,除去氢气和氮气以外的杂质,主要包括变换过程、脱硫脱碳过程以及气体精制过程。
①一氧化碳变换过程在合成氨生产中,各种方法制取的原料气都含有CO,其体积分数一般为12%~40%。
合成氨需要的两种组分是H2和N2,因此需要除去合成气中的CO。
变换反应如下:CO+H2OH→2+CO2 =-41.2kJ/mol 0298HΔ由于CO变换过程是强放热过程,必须分段进行以利于回收反应热,并控制变换段出口残余CO含量。
第一步是高温变换,使大部分CO转变为CO2和H2;第二步是低温变换,将CO含量降至0.3%左右。
因此,CO变换反应既是原料气制造的继续,又是净化的过程,为后续脱碳过程创造条件。
②脱硫脱碳过程各种原料制取的粗原料气,都含有一些硫和碳的氧化物,为了防止合成氨生产过程催化剂的中毒,必须在氨合成工序前加以脱除,以天然气为原料的蒸汽转化法,第一道工序是脱硫,用以保护转化催化剂,以重油和煤为原料的部分氧化法,根据一氧化碳变换是否采用耐硫的催化剂而确定脱硫的位置。
工业脱硫方法种类很多,通常是采用物理或化学吸收的方法,常用的有低温甲醇洗法(Rectisol)、聚乙二醇二甲醚法(Selexol)等。
粗原料气经CO变换以后,变换气中除H2外,还有CO2、CO和CH4等组分,其中以CO2含量最多。
CO2既是氨合成催化剂的毒物,又是制造尿素、碳酸氢铵等氮肥的重要原料。
因此变换气中CO2的脱除必须兼顾这两方面的要求。
一般采用溶液吸收法脱除CO2。
工业制氨气的方法
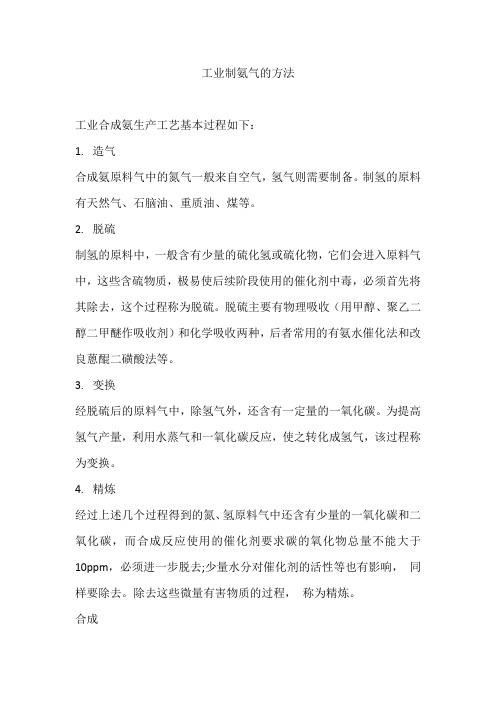
工业制氨气的方法
工业合成氨生产工艺基本过程如下:
1.造气
合成氨原料气中的氮气一般来自空气,氢气则需要制备。
制氢的原料有天然气、石脑油、重质油、煤等。
2.脱硫
制氢的原料中,一般含有少量的硫化氢或硫化物,它们会进入原料气中,这些含硫物质,极易使后续阶段使用的催化剂中毒,必须首先将其除去,这个过程称为脱硫。
脱硫主要有物理吸收(用甲醇、聚乙二醇二甲醚作吸收剂)和化学吸收两种,后者常用的有氨水催化法和改良蒽醌二磺酸法等。
3.变换
经脱硫后的原料气中,除氢气外,还含有一定量的一氧化碳。
为提高氢气产量,利用水蒸气和一氧化碳反应,使之转化成氢气,该过程称为变换。
4.精炼
经过上述几个过程得到的氮、氢原料气中还含有少量的一氧化碳和二氧化碳,而合成反应使用的催化剂要求碳的氧化物总量不能大于10ppm,必须进一步脱去;少量水分对催化剂的活性等也有影响,同样要除去。
除去这些微量有害物质的过程,称为精炼。
合成
经过上述处理并经过多级压缩后达到指定高压(一般为32MPa)的氮、氢混合气,送到合成塔中在一定温度(~500℃)范围内,经催化剂(Fe2O3为主体)作用,进行合成反应。
- 1、下载文档前请自行甄别文档内容的完整性,平台不提供额外的编辑、内容补充、找答案等附加服务。
- 2、"仅部分预览"的文档,不可在线预览部分如存在完整性等问题,可反馈申请退款(可完整预览的文档不适用该条件!)。
- 3、如文档侵犯您的权益,请联系客服反馈,我们会尽快为您处理(人工客服工作时间:9:00-18:30)。
3、合成氨原料气制备核心设备选型、结构、作用 及工作原理
煤气发生炉——固体原料煤从炉顶部加入,随煤气
炉的运 行向 下移动,在与从炉底进入的气 化剂逆流相遇的同时,受炉底燃料层高温气体加热, 发生物理、化学反应,产生粗煤气。此粗煤 气经粗 除尘后可直接供燃烧设备使用。
4、合成氨原料气制备工艺涉及的安全使用及急 救措施
氨、液氨和氨水均具有毒性。氨主要通过呼吸道呼吸和皮肤接 触对人体产生伤害。 合成氨的生产设备系统应严加紧闭、严防泄漏,生产车间应提 供充分的局部排风和全面通风,生产现场必修装有工业卫生设 施。当空气中氨浓度超标时,应按规定佩戴必要的防护用品, 如防毒面具,防毒口罩、防护眼镜、防护手套、防护服等。 氨泄漏时,应急处理人员可戴自给正压式呼吸器或防毒面具, 穿防静电工作服或一般消防防护服,不要直接接触泄漏物。
气柜——气体管道穿过水槽底板和水槽中的水进入钟罩,实现气体的输 入或排 出。第二塔节上挂圈立板插入钟罩下挂圈水封,第二塔节即 被提起,如此依次提起各塔节。在输出气体时,钟罩和塔节的动作过 程相反。钟罩及塔节依靠导轨和导 轮保证升降平稳。 除尘器——利用旋转的含尘气流所产生的离心力,将颗粒污染物从气体 中分离出来。
目前工业上的固体燃料为原料制取合成氨原料气的 方法,根据气化方式不同,主要有固定床间歇汽化 法、固定床连续汽化法、沸腾床连续汽化法和气流 床连续汽化法。
2、合成氨原料气制备工艺流程图阐述及工艺条件 的控制
2、合成氨原料气制备工艺流程图阐述及工艺条件
的控制
间歇式制半水煤气的工艺条件:
⑴温度——炉温应较熔点温度50摄氏度 ⑵吹风速度——提高吹风速度可使氧化层反应加速,吹风气中CO 含量的降低,从而减少了热损失 ⑶蒸汽用量——上吹时间不宜过长,下吹时间比上吹长 ⑷燃料层高度——较高的燃料层 ⑸循环时间及其分配——一般不超过3min ⑹气体成分——调节半水煤气中(CO+H2)与N2的比值 ⑺燃料品种的变化与工艺条件的调整——优质的固体燃料(焦炭 或无烟煤)对固定床煤气发生炉气化时允许燃料层较高,吹风 速度大,炉温高,因而蒸汽分解率高,煤气产量大;而对劣质 的固体燃料,则应根据具体情况调整工艺操作指标。
c H 2o co H 2
H 131kg / mol
c H 2o co2 H 2
H 90.3kg/mol
1、合成氨原料气的制备方法及原理
1 1 c o2 co2 2 2
H -393 .8kg / mol
c o2 co2
H -110 .6kg / mol
合成氨原料气的制备
汇报时间:2013年的制备方法及原理 2、合成氨原料气制备工艺流程图阐述及工艺条 件的控制 3、合成氨原料气制备核心设备选型、结构、作 用及工作原理 4、合成氨原料气制备工艺涉及的危化品性质、 安全使用及急救措施
1、合成氨原料气的制备方法及原理
合成氨原料气的制备方法有:⑴固体燃料汽化法 ⑵烃类蒸汽转化法 ⑶重油部分氧化法 我们选择合成氨的制备方法是固体燃料汽化法。 制备原理→原料气中有效成分与氮气比例为3.1~3.2 煤或焦炭的碳元素与水蒸气反应生成水煤气。
洗气塔——当其有一定进气速度的含尘气体经进气管进入后, 尾气塔中冲击水层并改变气体的运动方向,而尘粒由于惯性则 继续按原方向运动,其中尾气塔中大部分尘粒与水粘附 后便停留在水中,在冲击水浴后,有一部分尘粒随气体 运动,与冲击水雾并与循环喷淋水相结合,在尾气塔内 进一步充分混合作用,此时含尘气体中的尘粒便被水捕 集,尘水径离心或过滤脱离,因重力经塔壁流入循环池 ,净化气体外排。