橡胶的压出
橡胶生产工艺简介

橡胶生产工艺简介橡胶生产工艺简介1 综述橡胶制品的主要原料是生胶、各种配合剂、以及作为骨架材料的纤维和金属材料,橡胶制品的基本生产工艺过程包括塑炼、混炼、压延、压出、成型、硫化6个基本工序。
橡胶的加工工艺过程主要是解决塑性和弹性矛盾的过程,通过各种加工手段,使得弹性的橡胶变成具有塑性的塑炼胶,在加入各种配合剂制成半成品,然后通过硫化是具有塑性的半成品又变成弹性高、物理机械性能好的橡胶制品。
2 橡胶加工工艺2.1塑炼工艺生胶塑炼是通过机械应力、热、氧或加入某些化学试剂等方法,使生胶由强韧的弹性状态转变为柔软、便于加工的塑性状态的过程。
生胶塑炼的目的是降低它的弹性,增加可塑性,并获得适当的流动性,以满足混炼、亚衍、压出、成型、硫化以及胶浆制造、海绵胶制造等各种加工工艺过程的要求。
掌握好适当的塑炼可塑度,对橡胶制品的加工和成品质量是至关重要的。
在满足加工工艺要求的前提下应尽可能降低可塑度。
随着恒粘度橡胶、低粘度橡胶的出现,有的橡胶已经不需要塑炼而直接进行混炼。
在橡胶工业中,最常用的塑炼方法有机械塑炼法和化学塑炼法。
机械塑炼法所用的主要设备是开放式炼胶机、密闭式炼胶机和螺杆塑炼机。
化学塑炼法是在机械塑炼过程中加入化学药品来提高塑炼效果的方法。
开炼机塑炼时温度一般在80℃以下,属于低温机械混炼方法。
密炼机和螺杆混炼机的排胶温度在120℃以上,甚至高达160-180℃,属于高温机械混炼。
生胶在混炼之前需要预先经过烘胶、切胶、选胶和破胶等处理才能塑炼。
几种胶的塑炼特性:天然橡胶用开炼机塑炼时,辊筒温度为30-40℃,时间约为15-20min;采用密炼机塑炼当温度达到120℃以上时,时间约为3-5min。
丁苯橡胶的门尼粘度多在35-60之间,因此,丁苯橡胶也可不用塑炼,但是经过塑炼后可以提高配合机的分散性顺丁橡胶具有冷流性,缺乏塑炼效果。
顺丁胶的门尼粘度较低,可不用塑炼。
氯丁橡胶得塑性大,塑炼前可薄通3-5次,薄通温度在30-40℃。
橡胶生产工艺简介
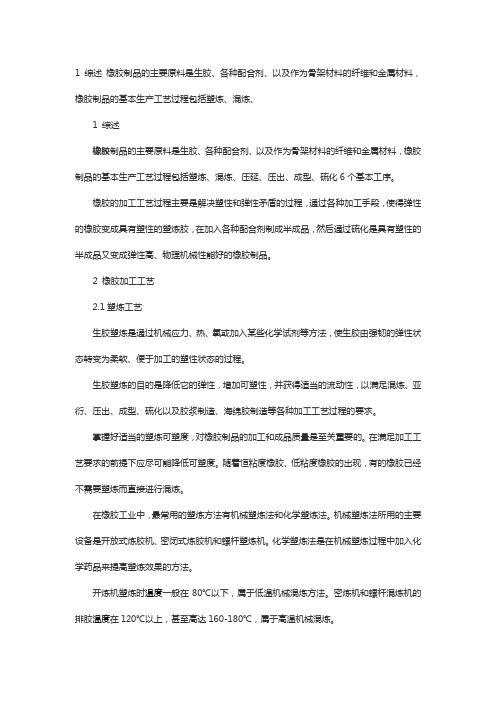
1 综述橡胶制品的主要原料是生胶、各种配合剂、以及作为骨架材料的纤维和金属材料,橡胶制品的基本生产工艺过程包括塑炼、混炼、1 综述橡胶制品的主要原料是生胶、各种配合剂、以及作为骨架材料的纤维和金属材料,橡胶制品的基本生产工艺过程包括塑炼、混炼、压延、压出、成型、硫化6个基本工序。
橡胶的加工工艺过程主要是解决塑性和弹性矛盾的过程,通过各种加工手段,使得弹性的橡胶变成具有塑性的塑炼胶,在加入各种配合剂制成半成品,然后通过硫化是具有塑性的半成品又变成弹性高、物理机械性能好的橡胶制品。
2 橡胶加工工艺2.1塑炼工艺生胶塑炼是通过机械应力、热、氧或加入某些化学试剂等方法,使生胶由强韧的弹性状态转变为柔软、便于加工的塑性状态的过程。
生胶塑炼的目的是降低它的弹性,增加可塑性,并获得适当的流动性,以满足混炼、亚衍、压出、成型、硫化以及胶浆制造、海绵胶制造等各种加工工艺过程的要求。
掌握好适当的塑炼可塑度,对橡胶制品的加工和成品质量是至关重要的。
在满足加工工艺要求的前提下应尽可能降低可塑度。
随着恒粘度橡胶、低粘度橡胶的出现,有的橡胶已经不需要塑炼而直接进行混炼。
在橡胶工业中,最常用的塑炼方法有机械塑炼法和化学塑炼法。
机械塑炼法所用的主要设备是开放式炼胶机、密闭式炼胶机和螺杆塑炼机。
化学塑炼法是在机械塑炼过程中加入化学药品来提高塑炼效果的方法。
开炼机塑炼时温度一般在80℃以下,属于低温机械混炼方法。
密炼机和螺杆混炼机的排胶温度在120℃以上,甚至高达160-180℃,属于高温机械混炼。
生胶在混炼之前需要预先经过烘胶、切胶、选胶和破胶等处理才能塑炼。
几种胶的塑炼特性:天然橡胶用开炼机塑炼时,辊筒温度为30-40℃,时间约为15-20min;采用密炼机塑炼当温度达到120℃以上时,时间约为3-5min。
丁苯橡胶的门尼粘度多在35-60之间,因此,丁苯橡胶也可不用塑炼,但是经过塑炼后可以提高配合机的分散性顺丁橡胶具有冷流性,缺乏塑炼效果。
橡胶软管胶料压出工艺和硫化技术进展
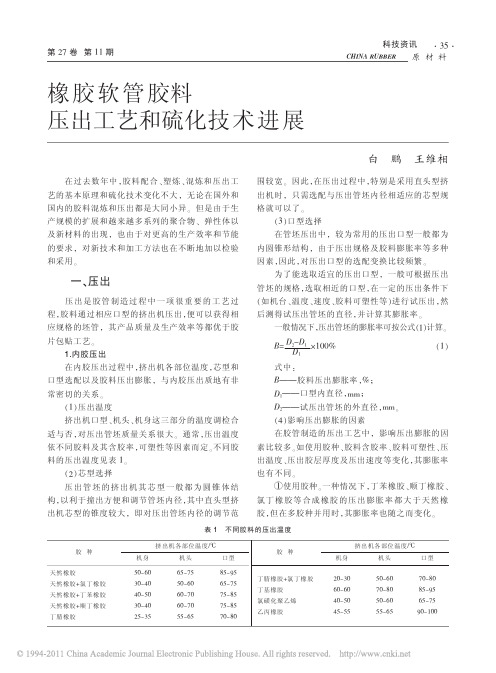
3.冷喂料压出和抽真空压出 采用冷喂料压出和抽真空压出,对改进胶管的 生产工艺和提高产品质量,将起着积极的作用。 冷喂料挤出机的主要结构特点是工作螺杆的长 径比 (L / D) 要比普通挤出机的螺杆大得多, 可达 12~17 (而一般为 4~6), 螺杆的螺纹结构可分为三 段,第一段为喂料段,由双螺纹向单螺纹过渡,中间 段为塑化段,由主副螺纹组成;第三段为压缩挤出 段,由单螺纹组成。 采用冷喂料压出的主要特点是压出前的胶料不 需经过热炼而直接将冷胶料喂入挤出机。 两段真空挤出机的螺杆分为前后两段,前段的 长径比 L / D 值一般为 12,螺纹较窄;后段的长径比 L / D 值为 8,螺纹较宽而深,前后两段之间的空隙为 真空室。 环坝式真空挤出机的螺杆长径比 L / D 值在 15 以上,螺杆上设有 2~3 个环坝,螺杆输送的胶料 在此处便挤成薄片,然后落入真空室。 采用抽真空挤出机压出胶管, 能使管坯在压出 或包胶过程中, 排除胶料中的空气和水分, 提高管体 的密实性。 尤其在采用连续化生产时, 可避免或减少 制品在硫化过程中产生气泡、 脱层等质量问题。 此外,也有以普通挤出机进行抽真空压出的,其 方法主要是在机头配备抽空装置,当送入管坯压出 外胶时,可抽出管坯与胶层之间的空气及少量挥发 物,以提高压出胶层与管坯的密实性,可获得较好的 效果。 但由于这种抽空作用使送入的管坯产生一定 的阻力,因此,使压出的速度略有减慢。 4.复合压出法 这种压出方法是采用具有复合机头装置的挤出 机,在压出过程中,使胶管的不同胶层同时进行压 出,尤其适用于同时包覆在管状织物(骨架层)内外 的不同胶层,其主要优点是生产效率高,特别适用于 连续化生产。 这种挤出机的结构特点,主要包含一 延长的挤出机头,它具有一些管状装置,排列成两个 主要的环状通道,伸入上述机头的纵向出料口,其中 一个环状通道供压出内层胶,另一个通道口压出外 层胶,它可供不同的胶料进行压出。
橡胶压延与压出—压出(橡胶加工课件)

3. 挤出机的规格和型号如何表示?
❖ 规格表示
▪ 挤出机的规格是以螺杆外直径来表示,其单位是mm。
▪ 国产挤出机的规格有Φ30、Φ45(实验用);Φ60、Φ65、Φ85、Φ90 (挤出胶管);Φ115、Φ120、Φ150、Φ200(挤出胎面);Φ250、 Φ300(滤胶用)等。
❖ 型号表示
▪ 螺杆挤出机型号是以螺杆外直径前冠以符号来表示。
2. 挤出机有哪些分类方法?
❖ 按物料分橡胶挤出机和塑料挤出机; ❖ 按螺杆数目的多少可分为单螺杆、双螺杆和多螺杆挤出机; ❖ 按可否排气可分为排气和非排气挤出机; ❖ 按螺杆在空间的位置可分为卧式和立式挤出机; ❖ 按工艺条件(喂料方式)可分为热喂料和冷喂料挤出机; ❖ 按用途可分为塑炼、混炼、滤胶和压型挤出机等多种类型。
⑥ ③ 胶螺度料纹相可槽匹的塑配压性,缩否大比则,会流大造动,成性半半好成成,品品挤致断出密面速性尺度提寸快高不,,准挤但确出胶,变料甚形生
小热至,高表半,面易成出焦品现表烧裂面;纹光等滑弊,病挤。出一生般热接小,取但速可度塑要性比太大挤,
则挤出半成品缺乏挺性,易产生变形。
出速度稍快为宜。
8、什么是冷喂料挤出?有何特点?
挤出
挤出
• 预热机筒,机头,口型和芯型,一般采用蒸汽介质
加热至规定温度范围(需10~15min)。
6、热喂料挤出工艺操作流程方法?
挤出
挤出
• 供胶调节口型,检查挤出半成品尺寸、表面状态,直
至符合要求后才能开始挤出半成品;
• 半成品公差范围:一般小规格的为±0.75mm,大规格的为 ± 1.0~1.5mm。
• 通常,胶料的热塑性越高, 流动性越好,挤出越容易, 但热塑性太高,胶料挺性差,
橡胶加工工艺—橡胶压出工艺(高分子成型课件)
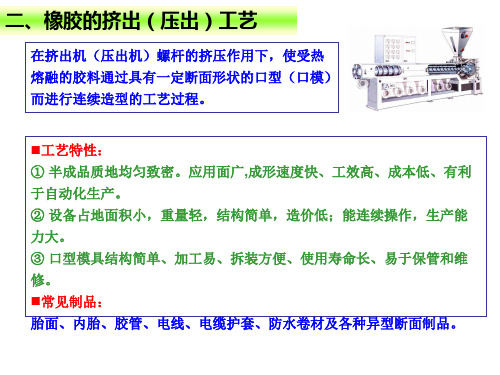
二、橡胶的挤出(压出)工艺
(一)压出机工作原理及胶料的运动状态 3 物料在口型中的流动状体和挤出变形 胶料经机头进入口型后,由于口型形状不同及内表 面对物料流动的阻碍,物料流动速度也存在有与机 头类似的速度分布。中间流速大,越接近口型壁流 速越小 。 一般粘弹性的物料,从口型挤出后就不可避免地存 在松弛现象,即:胶条的长度会沿挤出方向缩短, 厚度沿垂直挤出方向增加(离模膨胀现象或称作挤 出变形现象)。挤出后的变形(收缩和膨胀)可以控制 在一定范围,但不可能完全消除。要求收缩率为 2~5%。 物料可塑性小、含胶率大,填充剂用量小,物料挤 出快,机头和口型温度低,膨胀和收缩率就大。
二、橡胶的挤出(压出)工艺
在挤出机(压出机)螺杆的挤压作用下,使受热 熔融的胶料通过具有一定断面形状的口型(口模) 而进行连续造型的工艺过程。
工艺特性: ① 半成品质地均匀致密。应用面广,成形速度快、工效高、成本低、有利 于自动化生产。 ② 设备占地面积小,重量轻,结构简单,造价低;能连续操作,生产能 力大。 ③ 口型模具结构简单、加工易、拆装方便、使用寿命长、易于保管和维 修。 常见制品: 胎面、内胎、胶管、电线、电缆护套、防水卷材及各种异型断面制品。
二、橡胶的挤出(压出)工艺
(一)压出机工作原理及胶料的运动状态
1 胶料在挤出机中的运动状态
加料段:加入的条状胶料,受到旋转螺杆的推挤作用形成连续的胶 团,并沿着螺槽的空间一边旋转,一边不断前进。 压缩段:加料段输送过来的松散胶团在压缩段被逐渐压实、软化, 并把夹带的空气向加料段排出。同时胶团间间隙缩小,密度增高, 进而粘在一起,再加上受到剪切和搅拌作用,因而胶团逐渐被加热 塑化形成连续的粘流体。 挤出段:在挤出段,压缩段输送过来的物料进一步塑化均匀,并输 送到机头和口模处挤出成型。
橡胶的工艺流程
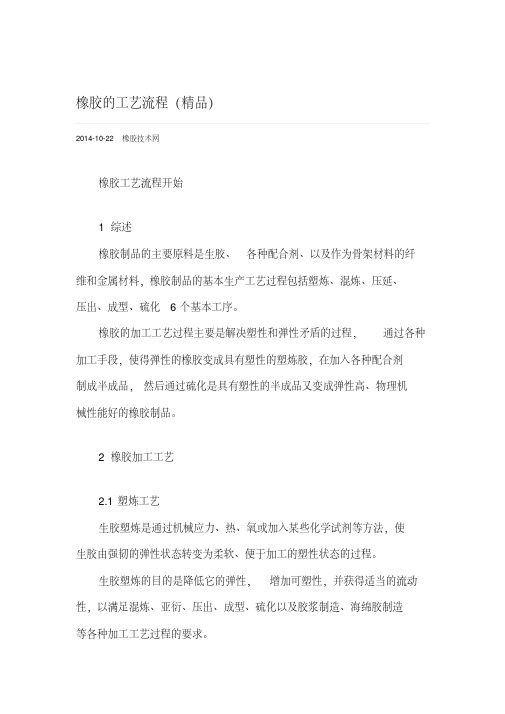
橡胶的工艺流程(精品)2014-10-22橡胶技术网橡胶工艺流程开始1 综述橡胶制品的主要原料是生胶、各种配合剂、以及作为骨架材料的纤维和金属材料,橡胶制品的基本生产工艺过程包括塑炼、混炼、压延、压出、成型、硫化6个基本工序。
橡胶的加工工艺过程主要是解决塑性和弹性矛盾的过程,通过各种加工手段,使得弹性的橡胶变成具有塑性的塑炼胶,在加入各种配合剂制成半成品,然后通过硫化是具有塑性的半成品又变成弹性高、物理机械性能好的橡胶制品。
2 橡胶加工工艺2.1塑炼工艺生胶塑炼是通过机械应力、热、氧或加入某些化学试剂等方法,使生胶由强韧的弹性状态转变为柔软、便于加工的塑性状态的过程。
生胶塑炼的目的是降低它的弹性,增加可塑性,并获得适当的流动性,以满足混炼、亚衍、压出、成型、硫化以及胶浆制造、海绵胶制造等各种加工工艺过程的要求。
掌握好适当的塑炼可塑度,对橡胶制品的加工和成品质量是至关重要的。
在满足加工工艺要求的前提下应尽可能降低可塑度。
随着恒粘度橡胶、低粘度橡胶的出现,有的橡胶已经不需要塑炼而直接进行混炼。
在橡胶工业中,最常用的塑炼方法有机械塑炼法和化学塑炼法。
机械塑炼法所用的主要设备是开放式炼胶机、密闭式炼胶机和螺杆塑炼机。
化学塑炼法是在机械塑炼过程中加入化学药品来提高塑炼效果的方法。
开炼机塑炼时温度一般在80℃以下,属于低温机械混炼方法。
密炼机和螺杆混炼机的排胶温度在120℃以上,甚至高达160-180℃,属于高温机械混炼。
生胶在混炼之前需要预先经过烘胶、切胶、选胶和破胶等处理才能塑炼。
几种胶的塑炼特性:天然橡胶用开炼机塑炼时,辊筒温度为30-40℃,时间约为15-20min;采用密炼机塑炼当温度达到120℃以上时,时间约为3-5min。
丁苯橡胶的门尼粘度多在35-60之间,因此,丁苯橡胶也可不用塑炼,但是经过塑炼后可以提高配合机的分散性顺丁橡胶具有冷流性,缺乏塑炼效果。
顺丁胶的门尼粘度较低,可不用塑炼。
氯丁橡胶得塑性大,塑炼前可薄通3-5次,薄通温度在30-40℃。
压出的三种橡胶的比较
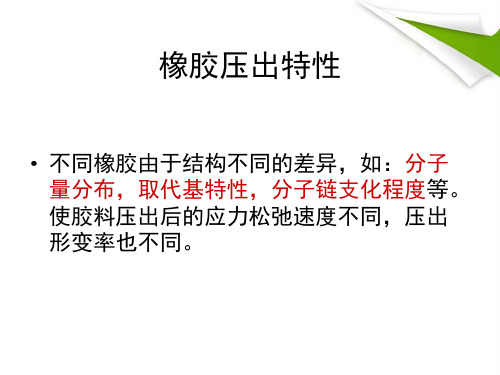
反式
CH3 C
( CH2
CH2 ) n C
H
反式-1,4-聚异戊二烯也称杜仲胶, 分子链有序,易结晶,通常温度下 为硬质固体。
天然橡胶的压出特性
压出速度快,压出变形较小,半成品 表面光滑,尺寸稳定性好,且致密度 高。
原因:➢NR分子主链上与双键相邻的 σ 键容易旋转,
分子柔性好,在常温处于无定形状态;
橡胶压出特性
• 不同橡胶由于结构不同的差异,如:分子 量分布,取代基特性,分子链支化程度等。 使胶料压出后的应力松弛速度不同,压出 形变率也不同。
天然橡胶 NR
天然橡胶的结构
主要成分橡胶烃是顺式-1,4-聚异戊二烯的线性高聚物
CH3 C
CH2
H C
CH2 n
n为5000~10000,相对分子量在3 万~3000万之间,常温下是无定形 高弹性物质。
顺丁橡胶 BR
结构CH2 CH CH C源自2 x顺丁橡胶的压出特性压出形变稍大,压出速度较慢,抗热 撕裂性能差,对温度敏感,压出适应 温度范围较窄。
原因:➢顺丁橡胶分子链柔顺好,分子结构比较规整,
主链上无取代基,分子间作用力小
➢碳链不饱和度较高 ➢克服周围分子链的阻力和作用力小,内摩擦小
结论: 胶料的弹性最好,生热低
➢分子链上侧甲基体积小,数目少,位阻效应小; ➢非极性分子,分子间相互作用小,对分子链内
旋转约束和阻碍小。
结论: 胶料的流动性好,弹性高,可塑度高。
丁苯橡胶 SBR
结构
顺式、反式- 1,4、1,2-结构的比例以及 St 和丁 二烯单元的分布等
CH2 CH CH CH2 x CH2 CH y CH2 CH z CH CH
丁苯橡胶的压出特性
压出
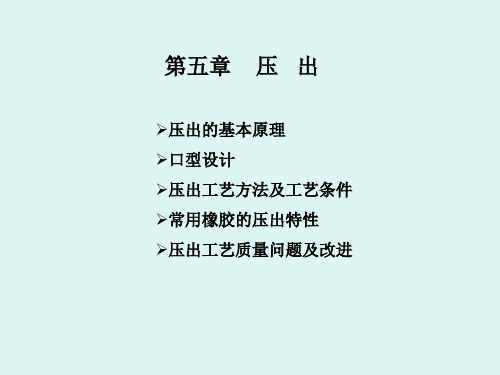
• • • • • •
二、口型设计的方法 1、胶料压出膨胀率的计算 B=D/D0×100% 两种方法: ⑴ 相同或相似半成品的膨胀率来计算 ⑵ 相同工艺方法和条件,相同胶料和近似口型的 条件下,通过公式计算
• 2、设计方法步骤 • ① 在确定的工艺条件(温度、压出速度等)下, 任选一个口型,用同一配方胶料压出一段坯料, 计算压出膨胀率。 • ② 依据计算出的压出膨胀率确定口型样板尺寸 • 口型样板尺寸=半成品尺寸/压出膨胀率 • 口型直径=(设计内径+内胶壁厚×2)/压出膨胀 率 (中空制品) • 其它因素:半成品断面变形,中间大边缘小
• 三、压出后的工艺 冷却 裁断 称量 停放 • (1) 冷却 • 目的:一是降低半成品的温度,防止存放中发生焦烧 • 二是降低半成品热塑性和变形性,使断面尺寸尽快 的稳定下来,并具备一定的挺性而防止变形 • 方法:自然冷却(效果差,薄型)和强制冷却(厚制品) • 强制冷却:冷水冷却(水槽冷却、喷淋冷却、混合冷却) 和强风冷却 • 大型半成品→预缩处理→冷却
• • • • •
② 压出机规格 压出机规格太大 压出机规格太小 压出机的长径比大 螺纹槽压缩比大
• • • • •
③ 工艺条件 压出温度过低 压出温度过高 压出速度过快 压出速度过慢
其它:压出半成品的接取装置速度和压出速度要相匹配
• 2、冷喂料压出法
• 胶料喂入压出机之前无需加热软化,室温加入
• • • •
(3)横流(环流) 螺纹槽内垂直于螺纹线方向的旋转流动 使胶料混合、热交换及胶料均匀塑化,对压出速度无影响 (4)漏流
• 四种流动形式的综合
• 三、压出变形 • 1、胶料在口型中的流动
• 2、压出变形 • 胶料经口型压出后的半成品,长度和厚度方面发生形变
- 1、下载文档前请自行甄别文档内容的完整性,平台不提供额外的编辑、内容补充、找答案等附加服务。
- 2、"仅部分预览"的文档,不可在线预览部分如存在完整性等问题,可反馈申请退款(可完整预览的文档不适用该条件!)。
- 3、如文档侵犯您的权益,请联系客服反馈,我们会尽快为您处理(人工客服工作时间:9:00-18:30)。
自动连续供胶。
• 3.2螺杆
• 螺纹有单头、双头和复合螺纹。
– 单头螺纹多用于滤胶;
– 双头螺纹的螺杆两沟槽同时出胶,出胶快而均匀,适 于压出造型;
• 热炼后便可用传送带连续向压出机供胶,也可以 用人工喂料的方式。供料应连续均匀,以免造成 压出机喂料口脱节或过剩。
• 4.2压出成型
• 在压出成型之前,压出机的机筒、机头、口型和 芯型要预先加热到规定温度,使胶料在挤出机的 工作范围内处于热塑性流动状态。
• 经热炼后的胶料以胶条形式通过运输带送至压出 机的加料口,并通过喂料辊送至螺杆,胶条受螺 杆的挤压通过机头口型而成型。
机头与口型
• 掌握胶料的膨胀率是口型设计的关键。 • 膨胀率影响因素:
– 胶料品种、配方、胶料可塑度,机头温度、压出速度 、半成品规格、压出方式等。
• 对于各种实心制品压出的板式口型来说需要掌握 压出胶料的断面变形通常是中间大边缘小
各种实心制品压出断面的变形图
• 对于中空圆形制品来说,一般厚度较口型增加, 少,而胶条长度的收缩较大。
• 口型尺寸选样的原则主要有两方面:一是口型断 面形状和压出胶条断面形状间的变化;另一是口 型断面和胶条断面各尺寸间可能收缩和膨胀的程 度。
• 4、橡胶压出工艺
• 4.1胶料热炼
• 除冷喂料挤出机外,经混炼和冷却停放的胶料在 进入压出机前必须进行充分的热炼,目的是进一 步提高胶料均匀性和可塑性,使胶料易于压出。
橡胶的压出
1、基本原理
橡胶挤出(习惯上叫橡胶压出)是在压出机(挤出机) 中对混炼胶加热与塑化,通过螺杆的旋转,使胶料在螺杆 和机筒筒壁之间受到强大的挤压作用,不断向前推进,并 借助于口型(口模)压出具有一定断面形状的橡胶半成品。
在橡胶制品工业中,压出的应用面很广,如轮胎的胎 面、内胎、胶管、胶带、电线电缆外套以及各种异形断面 的连续制品都可以用压出成型来加工。此外,它还可用于 胶料的过滤、造粒,生胶的塑炼以及上下工序的联动,如 在热炼与压延成型之间,压出起到前后工序衔接作用。
• 胶料可塑性大,则压出时内摩擦小,生热低,不易焦烧, 同时因为流动性好,压出速度快,压出物表面比较光滑, 但压出物易变形.尺寸稳定性差。
• 5.2压出机的结构特征
• 压出机大小的选择要根据压出物断面大小及厚度 决定
• 口型过大而螺杆推力小时会造成机头内压不足, 压出速度慢而不均匀,所得半成品形状不完整;
• 口型过小,机头内压过大,压出速度虽快,但螺 杆对胶料剪切作用增大,容易引起胶料生热,增 加了焦烧的危险性。
• 5.3压出温度
• 低温压出时,压出物断面较紧密,高温压出时则 易出现气泡或焦烧,但收缩率较小。
• 通常口型处温度最高,机头次之,机身则最低。
– 机身部分使胶料受到强大挤压作用,故温度宜低。而 且在压出时胶料受螺杆及机筒剧烈的摩擦作用,将产 生大量的热,所以螺杆中心要通冷却水,以防料温过 高面烧焦。
– 复合螺纹螺杆的加料段为单头螺纹,便于进料,出料 端为双头螺纹,出料均匀。
– 压出机的螺杆通常是双头螺纹或复合螺纹。
• 橡胶压出机与塑料挤出机的主要差别在于其长径比较小,
• 这是因为,橡胶的粘度很高,在挤出过程中会产生大量的 热,缩短压出机的长度,可保持温度升高在一定限度之内 ,防止胶料过热和焦烧。橡胶压出机的长径比大小,取决 于冷喂料(大)或热喂料(小)。
螺杆温度 /°C 20-25 20-25 20-25 20-25 20-25 20-25
各种常用橡胶的压出温度
• 5.4压出速度
• 压出机在正常操作时应保持一定的压出速度。如果速度改 变而口型拍胶面积一定,将导致机头内压的改变,影响压 出物断面尺寸和长度收缩的差异。对于压出同一性质的胶 料,在温度不变的情况下,压出速度提高,压出物膨胀相 应减小。
常见的橡胶制品
• 2、特点
• 压出工艺操作简单、经济,半成品质地均 匀、致密,容易变换规格,设备占地面积 小,结构简单、操作连续、生产率高,是 橡胶工业生产中的重要工艺过程。
3、橡胶压出的设备
压出机与塑料挤出机的结构原理相近似,压出机的主要部 件是机身、螺杆、机头和口型等。
• 3.1机身
– 压出机的机身为一夹套圆筒,与螺杆装配在一起,对胶料起塑化 输送作用,在夹套内可通入蒸汽或冷却水调温。
– 机头部分,要使胶料塑性提高以便进入口型成型,故 温度宜高些。
– 口型处短暂的高温,一方向使大分子松弛加快,塑性 增大,弹性恢复小,压出后膨胀及收缩率降低;另一 方面也减少了焦烧的危险。
• 总之,控制压出机各段的温度是为了使半 成品获得光滑的表面,稳定尺寸和减少收
缩率。此外,在压出过程中温度不易调整 ,以免影响压出的质量;
• 为了减少橡胶的剪切和造成的粘性生热,橡胶压出机螺杆 的螺槽深度通常相当大。
• 橡胶压出机螺杆的压缩比A相对较小。
• 3.3机头与口型
• 机头与机身衔接,用作安装口型。 • 口型是决定压出半成品形状和大小的模具,一般
分为两种。
– 一种是压出实心和片状半成品用的,是一块带有几何 形状的铜板;
– 一种是压出中空半成品用的,是由外口型、芯型及支 架组成,芯型上有喷射隔离剂的孔。
• 4.3冷却、裁断、称量或卷取
• 压出的半成品要迅速冷却,防止半成品变形和存 放时产生自流,使半成品进行冷却收缩,稳定其 断面尺寸。生产上常用水喷淋或水槽冷却方法。
• 经过冷却后的半成品,有些需经定长裁断、称量 等步骤,然后接取停放。有些半成品冷却后可卷 在容器或绕盘上来停放。
喷淋冷却槽 卷取或存放
胶种
NR BR CR NBR SBR IIR
机筒温度 /°C 50-60 30-40 20-35 30-40 40-50 30-40
机筒温度 /°C 75-85 40-50 50-60 65-90 70-80 60-90
口型温度 /°C 90-95 90-100 <70 90-110 90-100 90-120
• 5、压出成型的影响因素
• 5.1胶料的组成和性质
• 胶料中含胶量大时,压出速度慢,半成品收缩率大,表面 不光滑。在一定的范围内,胶料随含填充剂数量的增加, 其压出性能改善。不但压出速度能提高,而且收缩性也减 少,但胶料的硬度增大,压出时生热明显。胶料中掺有松 香、沥青或油膏矿物油等软化剂可增大压出速度,改善压 出半成品的表面性能。掺用再生胶的胶料压出速度较快, 而且能降低压出物的收缩率及减少压出时的生热。
• 5.5压出物的冷却
• 冷却的目的是及时降低压出物的温度,增加半成品存放期 内的安全性,减少其焦烧的危险,同时使半成品的形状尽 快地稳定下来,以免变形。