石墨在精密铸造中的
铸造用石墨粉

铸造用石墨粉铸造用石墨粉是一种重要的铸造辅助材料,广泛应用于铸造工业中。
它具有很高的热导率和耐高温性能,能够有效地提高铸件的质量和铸造效率。
石墨粉的主要成分是石墨,经过特殊加工处理后形成细小的粉末状。
石墨具有良好的导热性能和润滑性能,能够提高铸件的热导率和润滑性,从而减少铸件变形和缺陷的产生。
石墨粉在铸造过程中能够提高铸件的密实度和表面质量,使得铸件具有更好的机械性能和耐磨性能。
石墨粉的粒径大小对铸造效果有着重要影响。
通常情况下,石墨粉的粒径越细,能够填充铸件间隙的能力越强,从而提高铸件的密实度和表面质量。
因此,在具体的铸造工艺中,需要根据铸件的形状和尺寸选择合适的石墨粉粒径,以达到最佳的铸造效果。
同时,石墨粉的粒径大小也会影响到铸件的机械性能和耐磨性能,因此在选择石墨粉时需要综合考虑各种因素。
石墨粉在铸造过程中还可以起到改善熔体流动性和减少铸件缺陷的作用。
石墨粉能够增加熔体的润湿性,使其更容易充填到铸件的每一个角落,从而提高铸件的完整性和减少铸件缺陷的产生。
同时,石墨粉还能够减少熔体与模具的接触面积,降低热应力和热裂纹的产生,提高铸件的抗热疲劳性能。
石墨粉还可以用于铸造模具的涂料。
在模具涂料中加入适量的石墨粉,能够提高模具表面的润湿性和抗粘性,使得铸件更容易脱模,减少模具磨损和修模的次数,提高模具的使用寿命和铸件的表面质量。
总结起来,铸造用石墨粉在铸造工业中发挥着重要的作用。
它能够提高铸件的热导率和润滑性能,提高铸件的密实度和表面质量,同时改善熔体流动性和减少铸件缺陷的产生。
因此,在铸造过程中选择合适的石墨粉,并合理使用,能够有效提高铸件的质量和铸造效率。
石墨在铝棒铸造中的作用
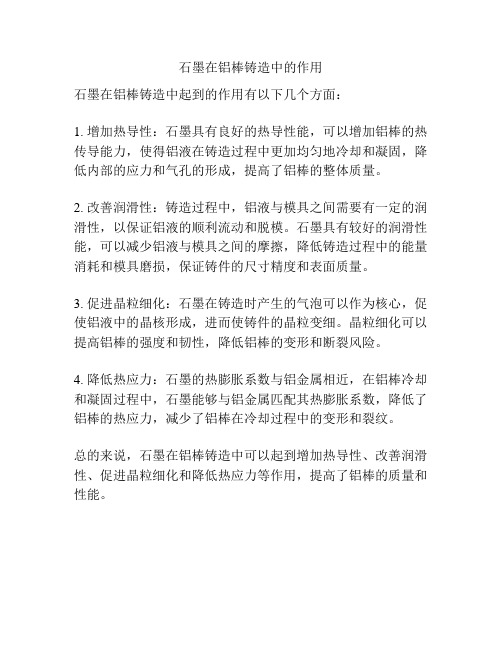
石墨在铝棒铸造中的作用
石墨在铝棒铸造中起到的作用有以下几个方面:
1. 增加热导性:石墨具有良好的热导性能,可以增加铝棒的热传导能力,使得铝液在铸造过程中更加均匀地冷却和凝固,降低内部的应力和气孔的形成,提高了铝棒的整体质量。
2. 改善润滑性:铸造过程中,铝液与模具之间需要有一定的润滑性,以保证铝液的顺利流动和脱模。
石墨具有较好的润滑性能,可以减少铝液与模具之间的摩擦,降低铸造过程中的能量消耗和模具磨损,保证铸件的尺寸精度和表面质量。
3. 促进晶粒细化:石墨在铸造时产生的气泡可以作为核心,促使铝液中的晶核形成,进而使铸件的晶粒变细。
晶粒细化可以提高铝棒的强度和韧性,降低铝棒的变形和断裂风险。
4. 降低热应力:石墨的热膨胀系数与铝金属相近,在铝棒冷却和凝固过程中,石墨能够与铝金属匹配其热膨胀系数,降低了铝棒的热应力,减少了铝棒在冷却过程中的变形和裂纹。
总的来说,石墨在铝棒铸造中可以起到增加热导性、改善润滑性、促进晶粒细化和降低热应力等作用,提高了铝棒的质量和性能。
石墨模具

石墨作为模具的原理
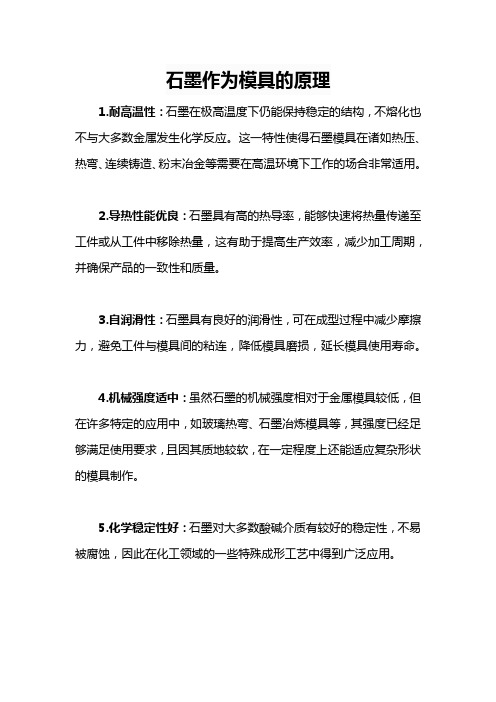
石墨作为模具的原理
1.耐高温性:石墨在极高温度下仍能保持稳定的结构,不熔化也不与大多数金属发生化学反应。
这一特性使得石墨模具在诸如热压、热弯、连续铸造、粉末冶金等需要在高温环境下工作的场合非常适用。
2.导热性能优良:石墨具有高的热导率,能够快速将热量传递至工件或从工件中移除热量,这有助于提高生产效率,减少加工周期,并确保产品的一致性和质量。
3.自润滑性:石墨具有良好的润滑性,可在成型过程中减少摩擦力,避免工件与模具间的粘连,降低模具磨损,延长模具使用寿命。
4.机械强度适中:虽然石墨的机械强度相对于金属模具较低,但在许多特定的应用中,如玻璃热弯、石墨冶炼模具等,其强度已经足够满足使用要求,且因其质地较软,在一定程度上还能适应复杂形状的模具制作。
5.化学稳定性好:石墨对大多数酸碱介质有较好的稳定性,不易被腐蚀,因此在化工领域的一些特殊成形工艺中得到广泛应用。
6.易于加工制造:石墨可以通过车削、铣削、电火花加工等多种方式进行精密加工,能够制作出精度高、表面光滑的模具型腔。
7.抗氧化涂层:现代技术还允许在石墨模具表面涂覆一层抗氧化维护涂层,以进一步增强其抗氧化能力和耐磨性,从而显著提高模具的工作寿命和耐用度。
ztl-10a型铸造石墨涂料成分
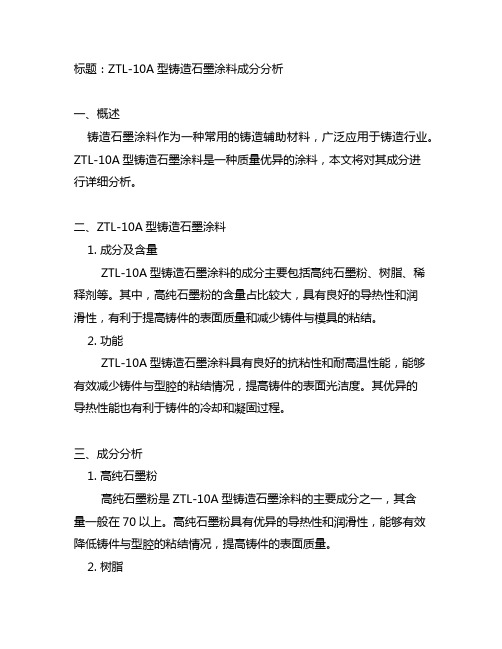
标题:ZTL-10A型铸造石墨涂料成分分析一、概述铸造石墨涂料作为一种常用的铸造辅助材料,广泛应用于铸造行业。
ZTL-10A型铸造石墨涂料是一种质量优异的涂料,本文将对其成分进行详细分析。
二、ZTL-10A型铸造石墨涂料1. 成分及含量ZTL-10A型铸造石墨涂料的成分主要包括高纯石墨粉、树脂、稀释剂等。
其中,高纯石墨粉的含量占比较大,具有良好的导热性和润滑性,有利于提高铸件的表面质量和减少铸件与模具的粘结。
2. 功能ZTL-10A型铸造石墨涂料具有良好的抗粘性和耐高温性能,能够有效减少铸件与型腔的粘结情况,提高铸件的表面光洁度。
其优异的导热性能也有利于铸件的冷却和凝固过程。
三、成分分析1. 高纯石墨粉高纯石墨粉是ZTL-10A型铸造石墨涂料的主要成分之一,其含量一般在70以上。
高纯石墨粉具有优异的导热性和润滑性,能够有效降低铸件与型腔的粘结情况,提高铸件的表面质量。
2. 树脂树脂是ZTL-10A型铸造石墨涂料的粘合剂,其主要作用是将高纯石墨粉固定在铸件表面,形成一层均匀的涂层。
树脂也能够提高涂料的附着力和耐高温性能。
3. 稀释剂稀释剂的添加能够调节涂料的流动性和粘度,使涂布更加均匀,提高涂层的光洁度和一致性。
四、应用与前景ZTL-10A型铸造石墨涂料的优异性能使其在汽车零部件、机械设备等领域得到了广泛应用。
随着高端制造业的发展和对产品质量要求的不断提高,ZTL-10A型铸造石墨涂料的市场前景十分广阔。
五、结论通过上述分析可知,ZTL-10A型铸造石墨涂料的成分主要包括高纯石墨粉、树脂、稀释剂等,具有良好的导热性和润滑性能。
其在铸造领域的应用前景广阔,有望成为铸造行业的重要材料之一。
六、参考文献[1] 王明. 铸造石墨涂料的研究与应用[J]. 机械科学与技术, 2017(12): 65-68.[2] 张强, 李艳. 高性能铸造石墨涂料的研究进展[J]. 材料工程, 2018(04): 154-157.七、ZTL-10A型铸造石墨涂料的性能优势ZTL-10A型铸造石墨涂料作为一种高性能的铸造辅助材料,具有几项明显的性能优势,使其在铸造行业得到了广泛的应用。
石墨材料在铸锭多晶硅制造中的应用

太阳能单硅晶片的制取:二氧化硅-工业硅-多晶硅-单晶硅。
单晶硅是用多晶硅经过单晶炉拉制而成。
也就是多晶硅是生产单晶硅的直接原料。
其中石墨是用来还原二氧化硅的,也就是来提炼工业硅的添加剂。
完成后再用盐酸提纯获得高纯度的多晶硅,最后拉制成单晶硅。
4.1石墨材料在铸锭多晶硅制造中的应用4.1.1铸锭多晶硅2007年在全球半导体产业低速增长的情况下,中国的半导体产业持续发展,比2006年增长了20.8%,随着各国对可再生能源的重视,以及太阳能电池转换效率不断提高,产品成本不断下降,太阳能电池产量快速增长。
自2000年以来光伏市场的发展超过了工业历史上的任何一次飞跃。
2007年全球太阳能电池产量达到4000MW,较2006年增长了56%,中国2007年太阳能电池产量达到1088MW,同比增长148%,市场占有率由2006年的17%提升到27%。
光伏发电的前景已经被越来越多的国家和金融界认识,多晶硅材料不仅用于半导体集成电路单晶硅的生产,同时还大量用于光伏太阳能电池产业,特别是用多晶硅生产的单晶硅制造的太阳能电池片其转化效率高﹙13%-18%﹚。
硅太阳能电池所用的单晶硅片,主要来自两种工艺渠道生产、供应的。
一类是通过直拉单晶硅,生产出单晶硅棒,经切割等制成晶圆。
另外一类是以多晶硅为原料,通过铸锭方法制成铸锭多晶硅块,再利用线切割机加工制成晶圆。
在太阳能电池制造的工艺流程中,可以看出,多晶硅铸锭是整个光伏产业链中的一个非常重要的基础工序。
利用铸造技术制备硅多晶体,称为铸造多晶硅或铸锭多晶硅﹙multicrystalline silicon,mc-Si﹚。
铸造多晶硅虽然含有大量的晶粒、晶界、位错和杂质,但由于省去了高费用的晶体拉制过程,所以相对成本较低,而且能耗也较低,在国际上得到了广泛应用。
与直拉单晶硅相比,铸造多晶硅的主要优势是①材料利用率高、能耗小、制备成本低,而且其晶体生长简便,易于大尺寸生长;②可直接得到方锭,与拉制单晶圆棒相比,在切割制备硅片的过程中比较省料,提高了硅料的利用率,且方形较圆形易于提高电池模块的包装密度。
钢厂用石墨粉的用途

钢厂用石墨粉的用途
石墨粉是一种细粉末状的无机物质,由于具有优良的导电性、导热性、机械性能和化学稳定性,在钢铁冶炼过程中具有广泛的应用。
1. 作为石墨电极的原料:钢厂制造电解铜、铝、锰等金属时需要用到石墨电极,石墨粉是制造石墨电极的主要原料之一。
2. 作为炉衬材料:钢厂的高炉、转炉等设备需要有耐高温、抗腐蚀的炉衬材料。
石墨粉可以作为炉衬材料的原料,可以制成石墨砖、石墨块等产品,具有优良的耐火性能和抗腐蚀性能。
3. 作为铸造材料:钢厂需要生产各种规格的铸铁件、钢铁件等,石墨粉可以作为铸造材料的添加剂,可以改善铸件的铸造性能、提高材料的强度和韧性。
4. 作为涂料:钢厂生产的钢材需要进行防腐处理,石墨粉可以用于制作防腐涂料,具有较好的防腐、防水、耐磨性能。
综上所述,石墨粉在钢厂中有着广泛的应用,是钢铁冶炼过程中不可缺少的重要原料。
- 1 -。
石墨加工方法

石墨加工方法前言石墨是一种重要的非金属材料,具有良好的导电性、导热性和润滑性。
在工业生产中,常常需要对石墨进行加工,以满足不同领域的需求。
本文将从石墨的特性、加工方法和应用领域等方面进行探讨。
石墨的特性石墨是一种由碳元素形成的晶体,具有以下特性: 1. 导电性:石墨的导电性能良好,是金属的导电性的一半,可用于制造导电材料和电极。
2. 导热性:石墨的导热性较好,热传导系数高,可用于制造散热材料和制冷材料。
3. 润滑性:石墨具有良好的润滑性,可用于制造摩擦材料和润滑材料。
4. 耐腐蚀性:石墨具有较好的耐腐蚀性,可在酸碱等恶劣环境下使用。
5. 高温稳定性:石墨的熔点高达3850℃,在高温下仍能保持稳定。
石墨的加工方法石墨的加工方法主要有以下几种:1. 切削加工切削加工是一种常用的石墨加工方法,可以通过车削、铣削、钻削等工艺将石墨材料切削成所需形状。
在切削过程中,需要使用合适的刀具,并控制切削参数,如切削速度、进给量和切削深度等。
切削加工适用于加工复杂形状和高精度要求的石墨零件。
2. 磨削加工磨削加工是一种通过磨削石墨材料表面来达到精加工的方法。
磨削可以使用砂轮、金刚石磨头等磨料进行,可以提高石墨材料的表面精度和光洁度。
磨削过程中,需要控制磨削速度、进给量和磨削压力等参数。
磨削加工适用于加工精密度高、表面要求光洁的石墨零件。
3. 铸造加工铸造加工是一种通过将熔化的石墨注入到模具中,待石墨冷却凝固后得到所需形状的方法。
铸造加工适用于加工大型、复杂形状的石墨零件,可实现批量生产。
4. 电火花加工电火花加工是一种利用电火花放电加工石墨材料的方法。
通过电极和工件之间的电火花放电,在工件上形成微小的放电坑,从而实现对石墨材料的加工。
电火花加工适用于加工细小、精密的石墨零件。
石墨的应用领域石墨的应用领域非常广泛,主要包括以下几个方面:1. 铸造行业石墨在铸造行业中被广泛应用,可用于制造铸模、铸造模具和冷却器等。
- 1、下载文档前请自行甄别文档内容的完整性,平台不提供额外的编辑、内容补充、找答案等附加服务。
- 2、"仅部分预览"的文档,不可在线预览部分如存在完整性等问题,可反馈申请退款(可完整预览的文档不适用该条件!)。
- 3、如文档侵犯您的权益,请联系客服反馈,我们会尽快为您处理(人工客服工作时间:9:00-18:30)。
精铸件的缺陷如氧化夹杂、表面麻坑、缩孔缩松、裂纹等等都是在金属液浇注到型壳中后的瞬间产生的,要避免和减少铸件的缺陷最理想的途径就是,一是要保证金属液的纯净和最合适的温度;二是要尽量使型壳的特性能适应和顺从不同金属液在注入不同型壳时,金属液冷凝过程中的不同变化。
对于后者,业内同仁已成功的采取了许多外部的措施,如采用加碳盖箱法,使金属在还原气氛下冷却,以防止易氧化钢种的铸件表面产生麻坑;又如将型壳浇注前局部沾水或浇注后局部吹风喷水,改变铸件凝固顺序,以防止铸件局部产生缩孔。
诸如以上类似的方法很多,但大多是从型壳以外去采取的措施,本文作者受国外经验的启示,从型壳本身的材料进行改变,将石墨材料引用到制壳材料中,从寻找合适的石墨材料以及在不同结构铸件和不同金属上进行了反复试验,获得了一些实际的体会,为今后石墨砂和粉在制壳中的推广应用将起一定的推动作用。
1.对石墨的基本认识1.1. 石墨是碳元素的同素异形体。
自然界中由碳元素组成的固态物质可分为两大类,即一类为无定形结构的非晶质物质,如木炭、焦炭、煤、活性炭等,另一类为晶体结构的物质,有金刚石和石墨两种。
也就是说碳有三种同素异形体,它们是金刚石、石墨和无定形碳。
石墨的来源有两种,一种是天然石墨,大自然中蕴藏着丰富的石墨矿,中国是世界石墨矿储藏量笫-位的国家,主要分布在黑龙江、山东、河南、湖南等诸多省份,我国天然石墨来源丰富:另-种是人造石墨,是以人为的方法将高纯的无定形碳进行石墨化,人造石墨的纯度更高,有更广泛的应用领域。
1.2.天然石墨。
根据碳原子的晶形结构和大小的不同,可分为三类:①致密结晶状石墨,又称块状石墨。
石墨晶体直径大于0.1毫米,晶体肉眼可见,但排列杂乱无章,呈致密的块状构造,其特点是矿中碳的品位较高,一般为60%-65%,有时达到80%-98%,可塑性和滑腻性不如磷片石墨。
②鳞片石墨,石墨晶体呈鱼鳞状,为片层状的晶体结构,层内的碳原子排列成平面六边形,每个碳原子以三个共价键与其他碳原子结合,而层与层间的碳原子是靠分子间作用力相结合的,其特点是矿中碳的品位一般不高,通过多磨多选可获得鳞片石墨精矿,它与水基溶液不易混合,它的可浮性、润滑性和可塑性优于其他石墨,工业价值大。
③隐晶质石墨,又称土状石墨。
石墨晶体直径小于1微米,在电子显微镜下才能见到晶形,它是微晶石墨的集合体,其特点是矿中碳的品位较高,一般碳含量为60%-80%,少数高达90%以上,矿石可选性差,表面呈土状,缺乏光泽,润滑性差,但易与水基溶液混合。
天然石墨是在高温下形成的变质矿床,含有SiO2、Al2O3、FeO2、CaO、P2O5、CuO等杂质,常与石英、黄铁矿、碳素盐等矿物形式出现,还含有水、沥青、CO2、H2、CH4、N2等气体,虽经过选矿处理,但使用天然石墨时至少要检测其固定碳、硫、灰分、挥发分、等主要指标。
详见表一。
1.3.人造石墨。
它是用优质的粉状的经过煅烧的石油焦为原料,加入沥青作粘结剂,通过挤压、模压或等静压的方法压制成形,再在2500℃-3000℃非氧化性气氛中进行石墨化处理而获得的石墨质产品,如电极及各种形状的石墨制品,由于经过煅烧后的石油焦的碳含量高,杂质少,又经过高压成形,因而这种人造石墨具有高纯度、高密度、高强度的特点见表二,按纯度和致密度可分为普通人造石墨和高纯致密石墨,在制造业和科研上有广泛的用途,即使用废了,仍可将其破碎成砂和粉亦称为石墨碎,可作为优质的石墨材料使用。
石墨呈灰黑色,质软,人为加压成形的人造石墨质地较硬,比重为1.9~2.3,熔点高达3850±50℃。
它的主要特性是:耐高温,即使在超高温的电弧灼烧下,重量损失也很小;线膨胀系数很小为2×10-6,是电熔刚玉的1/4,锆英石的2/5,因此抗热震性高,温度突变时体积变化也小,故不会因此的加入而使模壳产生裂纹;导电性极好,导热性超过钢铁等金属材料,特别的是导热系数随温度升高而降低,在高温下石墨几乎是绝热体;化学稳定性好,不与酸碱及有机溶剂起反应;此外还有很好的可塑性、润滑性和高温强度。
在铸造生产中,对石墨并不陌生,如在金属熔炼中用石墨作为增碳剂,电弧炉炼钢用的电极及熔化有色金属的坩埚都是石墨制品,在铸铁及有色金属的砂型和金属型铸造中用石墨作铸型表面的涂料也非常普遍。
根据石墨的许多优良特性,在精密铸造制壳材料中有选择的使用石墨材料,以达到以下几个目的应是可行的。
2.1.利用石墨在高温下与氧反应,形成还原性气氛,保护注入铸型的高温金属不被氧化。
石墨在低温下几乎不氧化,400℃以上才开始轻微氧化,随着温度升高氧化速度加快,并生成CO2或CO, 当在1000℃以下时C + O2 = CO2 ,在1000℃以上时2C + O2 = 2CO ,因此为达到这一目的,可在过渡层中选用高纯致密的人造石墨砂作撒砂材料,-当高温金属进入型壳的型腔中,产生的还原气氛更靠近型壳面层接触的金属,对金属防氧化的较果更好,但同时也不必担心过渡层的石墨砂会在型壳焙烧中烧蚀而溃退,一方面是高纯致密的人造石墨砂氧化失重速度很慢,见表三,另一方面石墨砂是被包复在硅溶胶的浆料中有一定的保护作用,而且在箱式焙烧炉中焙烧型壳时,都是在缺氧状态下且焙烧时间短,石墨砂粒失重有限,不足以影响型壳强度。
表三石墨在空气中加热时的氧化速度2.2.利用石墨在高温下的绝热性,可增加金属液对型壳薄壁型腔的充型能力,还可改变型壳局部散热能力,达到改变铸件的冷却凝固顺序。
为了达到这一目的可在型壳的笫三层及以后层次用人造石墨砂代替煅烧高岭土砂,表四是我们使用的石墨砂的主要成分,由于石墨在高温型壳中的隔热作用,金属液注入型壳后散热慢,延长了金属流动时间,其好处是一方面铸件特簿部位不易欠铸,另一方面是由于金属凝固时间延缓,厚壁铸件的补缩通道不致很快堵塞,从而增加浇冒口对铸件的补缩能力,而且还可在型壳需要缓冷部位,单独的撒石墨砂,使型壳各部有不同的冷却速度,弥补工艺设计的不足,克服铸件的缩孔缩松倾向。
表四人造石墨和块状石墨的主要成分表2.3.利用石墨在型壳焙烧过程的氧化逸散,在型壳中形成均匀弥散的微孔,从而增加了型壳的透气性和溃散性。
为实现这一目的,可在背层浆料的最后两层和封浆层中加入一定比例的天然石墨粉,可以选用块状或土状天然石墨粉,我们使用的天然石墨粉的成分见表四,由于石墨颗粒细小,天然石墨中固定碳稍低且有挥发物,故在型壳焙烧中就会部分烧失,既使型腔成还原气氛又增加型壳透气性,若单纯为了增加型壳的退让性,使簿壁长形的铸件不致因收缩受阻而裂纹,并不计较其准确的尺寸时,即可在背层的前几层浆料中就加入石墨粉,加入量也可适当增加。
3.应用举例3.1 应用于形成还原性气氛有些材质的金属液在凝固过程中对还原性气氛有特别要求,但有的铸件往往受结构和工艺条件的限制,制造的还原性气氛难以满足铸件的要求克服“麻点”。
如图四铸件的材质ZG20Cr13,质量34.3Kg。
在图示“A”区59mm处有个肥厚块,即有个相对独立的热节区,设置的冒口受23mm两槽的影响,极易在两槽的转角处形成缩裂,浇注完后采用两至三次的补浇冒口解决了缩裂,但却延误了最佳的“盖箱”时间,铸件的表面已在氧化性条件下凝固结壳而出现大面积的“麻点”。
我们采用在制壳的第四层撒石墨砂替代莫来砂,当金属液浇入型壳后,石墨在壳型内形成一道“CO”的还原性气膜绝热层,同时铸件的表面凝固时间被推迟,一方面金属表面“麻点”的形成条件受到了限制,同时也使金属液的“补缩”通道向着顺序凝固的有利方向走,等补浇完毕再“盖箱”,虽然中间有4~5分钟的时间,铸件清理后的“麻点”问题却很少见或不可见。
图五为紫铜铸件重5.1Kg,一串两个和浇注系统共重21Kg。
纯(紫)铜是纯金属,液态纯金属的凝固与合金不同的是没有凝固区域,固体与液体由同一界面(称为凝固前沿)清楚地分开,由外至里逐层向内凝固,这样的凝固方式其凝固时间特长。
纯铜极易氧化和吸气,是因为逐层凝固和凝固时间特长所引起的。
故铸件表面易产生针孔、麻面、黑色的裂口等缺陷,铸件断面组织粗大。
若采用在还原性气氛条件下冷却能有效的控制质量。
这点不难理解,如果是采用砂型铸造一般都会采用干型并在其型腔表面刷石墨涂料,这就昭示了前述的还原性气氛条件下的冷却方法。
针对此件的结构和材质的凝固特性,补缩采用向浇冒口补浇4~5次铜液,时间间隔共有几分钟。
如果再采用常规的硅溶胶制壳工艺制壳,“盖箱”所制造的还原性气氛,远不能满足及时性的要求而没有什么作用。
为此我们制定的制壳工艺是在第三层撒16~30目的石墨砂,第四层撒10~16目的石墨砂,共七层加封浆,之前之后的硅溶胶的制壳工艺没有改变。
焙烧温度设定850℃,保温时间25分钟,铸件加工后没有发现问题。
图五右展示的是将浇注后的模壳敲破后的断面和与金属液接触的表面状况。
观察其浇口杯处(方框内)已不见黑色的石墨砂颜色,即可认为是被完全氧化了,但也没有出现明显可见的被“烧”掉的孔洞存在;在其下部石墨砂层仍“犬牙交错镶崁”在涂料层间依稀可认。
之前焙烧温度设定1050℃,保温40分钟,铸件浇注后清理型壳时,石墨层把加固层分离,面层和过渡层依附在铸件上,此两层的石墨颜色由黑变褐黄,清理后的铸件表面全部是“麻坑”,大的有4~5mm大,小的也大于1mm以上,棱角也不清晰,铸件全部报废。
我们将在此温度和保温设定下焙烧好后的模壳打开,断面的颜色同前述基本一致,那么可以肯定的是与金属液的浇注温度和速度无关,主要在焙烧上,由于“过烧”致使“碳”成分被氧化掉,当铜液浇入型壳后,还原性气氛的基本物质条件不存在了,因此出现上述问题的症结也就在情理之中了。
3.2.解决厚薄不均的模壳结构而引起的焙烧不透现象有些铸件的沟槽或结构性的局部位置凹陷,形成的模壳层间连在一起形成“搭桥”,本是四层的或五层的型壳,此处可能就是乘以2倍的关系,变成八层十层或更厚了,在一个模壳里壁厚相差悬殊太大,焙烧炉内是很难烧透和烧均匀的。
过厚的局部地方烧不透铸件上易形成侵入性气孔,反之另一种情况是将肥厚的地方焙烧透了,费时费能源的同时还易产生变形或伴随其它问题的发生。
同时过厚的模壳也使蓄热系数增大,散热慢铸件此处容易产生缩孔、缩松等问题。
图六示铸件的材质是“SCS13”,铸件的中部有一凹槽,模壳工艺要求7层加封浆,制完壳后此凹槽处刚好填平(在粘浆的过程中此槽也容易淤浆也是造成填平的原因之一),此处的模壳层实际厚度最少是12层的结构。
模壳的焙烧时此处很难烧透,易产生“麻点”。
我们曾采用过第五层后填砂,但由于封闭困难,焙烧后漏砂致使在浇注过程中出现“漏钢”,断芯或孔变形、或两孔间不同轴现象的缺陷。
现采用在第五层后撒石墨砂,在焙烧的过程中石墨即使完全被氧化(烧掉),但此层的涂料浆形成的网络仍是相互连接的,烧损的只是镶崁的石墨而已,事实也证明了它的基本强度仍可抵御金属液的冲击,这是其一;其二当焙烧烧到石墨层时,石墨的“高温绝热”性质便开始发挥“效益”了,如果我们把它理解为有一种“放热”作用,那么这个石墨层就是一个“热火层” 。