Q-ZZ 30021锻件热处理验收规范-2011(下发 版)
热处理工艺规范
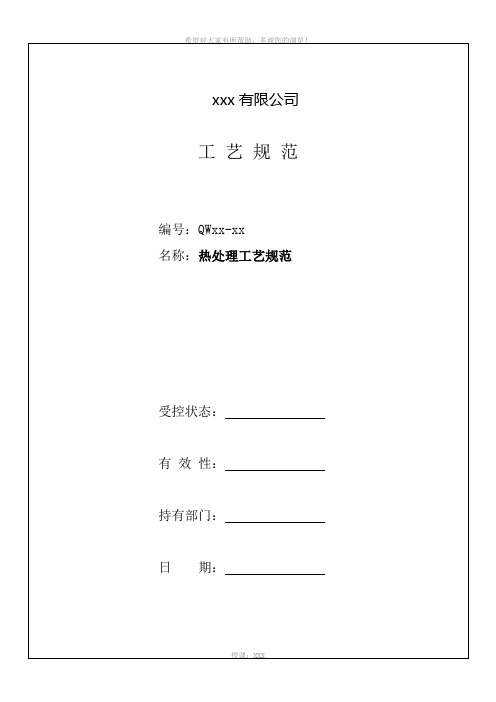
Ⅲ、Ⅳ、Ⅴ
允许温度偏差
±1℃
±3℃
5.1.5 高频淬火(感应热处理)加热电源及淬火机床:
5.1.5.1 感应加热电源输出功率及频率必须满足热处理要求,输出功率控制在±5%,或输出电压在±2.5%范围内。感应热处理机床和限时装置应满足工艺要求。
5.1.5.2 高频淬火机床精度要求如下表:
表5.1.5
5.3 仪表要求:
5.3.1 现场使用的控温和记录仪表等级应符合表5.1.1要求,检定周期按表5.1.3执行。
5.3.2 现场系统校验用的标准电位差计精度应不低于0.05级,分辨力不低于1μv,检定周期为6个月。
5.3.3 现场常用的热电偶技术要求,见下表:
表5.3.1
名 称
分度号
等级
使用温度
允许温度
(1)应向供货单位要求提供原材料质保书(包括生产厂家、牌号、规格、供货状态等)。
(2)若需要材料代用,必须向我司产品开发部办理材料代用手续。
(3)加强原材料管理,必须对原材料分类标识,防止混料,推荐使用前作火花鉴别等。
6.2 工艺参数控制:
严格按确定的《热处理作业检验指导书(或热处理工艺卡)》中具体工艺参数,包括热处理设备、装炉方式、装炉量、加热升温方式、加热温度、保温时间、冷却方式、冷却介质、冷却介质温度、渗剂种类、渗剂流量、感应加热温度、限时加热时间及电参数(阳极电压、阳极电流、槽路电压等);且按质量检验项目、标准与规范要求进行过程控制。
5.1.3 每台加热炉必须定期检测有效加热区,检测方法按GB/T9452和JB/T6049的规定,其保温精度应符合表5.1.2要求。应在明显位置悬挂带有有效加热区示意图的检验合格证。加热炉只能在有效加热区检验合格证规定的有效期内使用,检测周期见下表:
我国现行的热处理标准
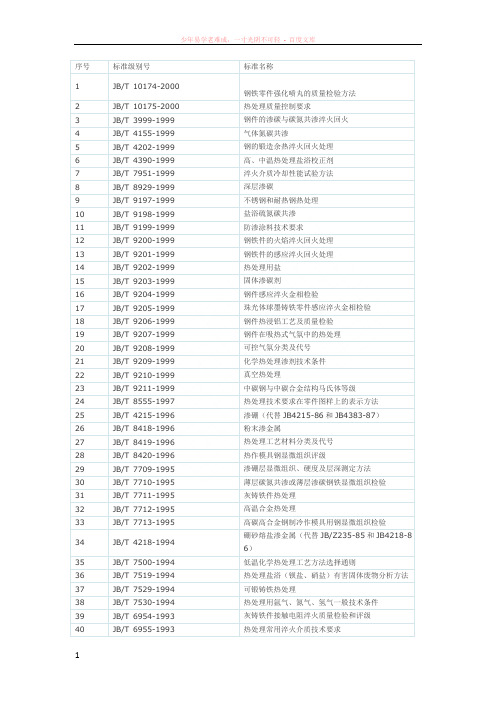
序号标准级别号标准名称1 JB/T 10174-2000钢铁零件强化喷丸的质量检验方法2 JB/T 10175-2000 热处理质量控制要求3 JB/T 3999-1999 钢件的渗碳与碳氮共渗淬火回火4 JB/T 4155-1999 气体氮碳共渗5 JB/T 4202-1999 钢的锻造余热淬火回火处理6 JB/T 4390-1999 高、中温热处理盐浴校正剂7 JB/T 7951-1999 淬火介质冷却性能试验方法8 JB/T 8929-1999 深层渗碳9 JB/T 9197-1999 不锈钢和耐热钢热处理10 JB/T 9198-1999 盐浴硫氮碳共渗11 JB/T 9199-1999 防渗涂料技术要求12 JB/T 9200-1999 钢铁件的火焰淬火回火处理13 JB/T 9201-1999 钢铁件的感应淬火回火处理14 JB/T 9202-1999 热处理用盐15 JB/T 9203-1999 固体渗碳剂16 JB/T 9204-1999 钢件感应淬火金相检验17 JB/T 9205-1999 珠光体球墨铸铁零件感应淬火金相检验18 JB/T 9206-1999 钢件热浸铝工艺及质量检验19 JB/T 9207-1999 钢件在吸热式气氛中的热处理20 JB/T 9208-1999 可控气氛分类及代号21 JB/T 9209-1999 化学热处理渗剂技术条件22 JB/T 9210-1999 真空热处理23 JB/T 9211-1999 中碳钢与中碳合金结构马氏体等级24 JB/T 8555-1997 热处理技术要求在零件图样上的表示方法25 JB/T 4215-1996 渗硼(代替JB4215-86和JB4383-87)26 JB/T 8418-1996 粉末渗金属27 JB/T 8419-1996 热处理工艺材料分类及代号28 JB/T 8420-1996 热作模具钢显微组织评级29 JB/T 7709-1995 渗硼层显微组织、硬度及层深测定方法30 JB/T 7710-1995 薄层碳氮共渗或薄层渗碳钢铁显微组织检验31 JB/T 7711-1995 灰铸铁件热处理32 JB/T 7712-1995 高温合金热处理33 JB/T 7713-1995 高碳高合金钢制冷作模具用钢显微组织检验34 JB/T 4218-1994 硼砂熔盐渗金属(代替JB/Z235-85和JB4218-8 6)35 JB/T 7500-1994 低温化学热处理工艺方法选择通则36 JB/T 7519-1994 热处理盐浴(钡盐、硝盐)有害固体废物分析方法37 JB/T 7529-1994 可锻铸铁热处理38 JB/T 7530-1994 热处理用氩气、氮气、氢气一般技术条件39 JB/T 6954-1993 灰铸铁件接触电阻淬火质量检验和评级40 JB/T 6955-1993 热处理常用淬火介质技术要求41 JB/T 6956-1993 离子渗氮(代替JB/Z214-84)42 JB/T 6047-1992 热处理盐浴有害固体废物无害化处理方法43 JB/T 6048-1992 盐浴热处理44 JB/T 6049-1992 热处理炉有效加热区的测定45 JB/T 6050-1992 钢铁热处理零件硬度检验通则46 JB/T 6051-1992 球墨铸铁热处理工艺及质量检验47 JB/T 5069-1991 钢铁零件渗金属层金相检验方法48 JB/T 5072-1991 热处理保护涂料一般技术要求49 JB/T 5074-1991 低、中碳钢球化体评级50 GB/T 18177-2000 钢的气体渗氮51 GB/T 7232-1999 金属热处理工艺术语52 GB/T 17358-1998 热处理生产电能消耗定额及其计算和测定方法53 GB/T 16923-1997 钢的正火与退火处理54 GB/T 16924-1997 钢的淬火与回火处理55 GB15735-1995 金属热处理生产过程安全卫生要求56 GB/T 15749-1995 定量金相手工测定方法57 GB/T 13321-1991 钢铁硬度锉刀检验方法58 GB/T 13324-1991 热处理设备术语59 GB/T 12603-1990 金属热处理工艺分类及代号60 GB/T 11354-1989 钢铁零件渗氮层深度测定和金相组织检验61 GB/T 9450-1988 钢铁渗碳淬火有效硬化层深度的测定和校核62 GB/T 9451-1988 钢件薄表面总硬化层深度或有效硬化层深度的测定63 GB/T 9452-1988 热处理炉有效加热区测定方法64 GB/T 8121-1987 热处理工艺材料名词术语65 GB/T 5617-1985 钢的感应淬火或火焰淬火后有效硬化层深度。
外协外购件验收细则

外协外购件验收细则温州市雄正电器股份有限公司Q/XZJ-2017外购外协件验收细则1.范围本标准规定了外协外购件的检验和验收方法本标准适合于本公司生产的各种系列产品的外协外购件的检验和验收。
1.规范性引用文件下列文件中的条款通过本标准的引用而成为本企业标准的条款GB/T18418-2009家用卫生杀虫用品电热蚊香器GB/T1741-2004电热片蚊香用恒温电加热器GB/T2828.1逐批计数抽样检验标准GB/TGB/T1239.2冷卷园柱螺旋压缩弹簧技术条件GB/T1173铸造铝合金件的技术条件GB/T708冷扎钢板的技术条件GB/T12603热处理工艺及技术要求GB/T16938紧固件、螺栓、螺钉、螺柱和螺母通用技术条件GB/T276滚动轴承技术条件GB/T2705涂料、品种及其技术要求JB/T4378.1冷冲压件的技术条件2.检验和验收规则3.1外购外协件应按工艺图纸、标准及有关技术要求进行采购控制,检验和验收。
3.2外购外协件按其对产品质量的影响程度分为A、B、C三类,实施A、B、C管理法:A类:关键件全检外购件必须提供理化性能检验单。
B类:重要件抽检外购件按需要提供理化性能检验单。
C类:一般件对外购件的型号规格、合格品标志等进行目测验证。
3.3质检部对采购部提供的《外协外购件报检单》,按图纸、标准及有关技术要求验收入库。
对B类抽检的外协外购件,根据GB/T2828-2008一般检验水平为Ⅱ,规定了正常检查一次抽检方案见表1:批量范围抽样数(个)合格质量水平(AQL)2.5 4.0 6.5(个)/Ac Re Ac Re Ac Re 1-82010101 9-153010101 16-255010112 26-50801121251-901312122391-150********151-28032233456281-50050345678501-12008056781011根据抽样检验结果,若抽样数中发现不合格品数小于或等于合格判定数(Ac),则判该批是合格批,可以接收;若抽样数中发现不合格数大于或等于不合格判定数(Re),则判该批是不合格批应拒收。
铸造材料技术要求和验收规范
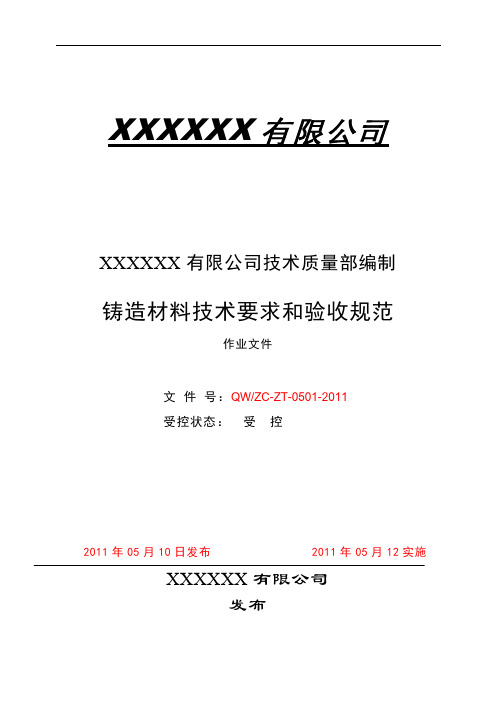
XXXXXX有限公司XXXXXX有限公司技术质量部编制铸造材料技术要求和验收规范作业文件文件号:QW/ZC-ZT-0501-2011受控状态:受控2011年05月10日发布 2011年05月12实施XXXXXX有限公司发布1.目的规范众鑫机械公司主要铸造原材料的各项技术要求及原材料进厂检验标准2.范围适用于铸造、熔化等材料的验收。
3. 技术要求和验收规范3.1生铁3.1.1铸造用生铁技术条件a)各种牌号的生铁应符合表1的规定。
b)各牌号生铁应铸成5±2kg小块,而大于7kg和小于2kg的铁块其重量之和不超过总重量的10%,最大长度不超过220 mm,质量不大于10 kg。
表1 铸造用生铁(GB/T 718—2005)c)铸铁块表面应洁净,不得有炉渣和砂粒,但允许有石灰和石墨。
d)铸铁生铁应做含碳量的分析,但其结果不作考核依据。
e)生铁中钛、砷、铅、铋、锑等微量元素含量的总和不得超过0.12%。
3.1.2生铁验收规范3.1.2.1生铁的验收应凭供方质量合格证明和本公司理化部门的成分化验单进行验收,硅、锰、硫、磷均作为验收指标,含碳量也应化验,但不作为验收指标。
如化学成分不符合要求,要做退货处理或请示主管领导批准让步接收处理。
3.1.2.2化验取样方法a)验证试样的代表批量以供方来货生铁重量为批。
b)从生铁堆上取样时,按批量大小在铁堆上均匀分布若干个取样部位,每个部位采取完整的一块生铁作为一个试样。
具体取样份数,按下列原则确定:小于30t取三块,30~100t每增加10t多取一块。
c)无论取几个样块进行化验,化验结果应符合同一个铁号及相同的化学成分,有一个样块不合格,应视为整批不合格,要做退货处理或请示主管领导批准让步接收处理。
3.1.2.3化验方法1.硅的测定:草酸-硫酸亚铁硅钼蓝光度法2.锰的测定:过硫酸铵氧化光度法3.磷的测定:铋磷钼蓝光度法4.碳的测定:气体容量法5.硫的测定:碘酸钾容量法3.2废钢3.2.1范围:适用于电炉熔炼铸铁调整成分用碳素废钢3.2.2废钢技术条件a)废钢应是45号钢以下的普通碳素钢,其化学成分(%)应符合下列要求:C:≤0.45; Si:0.01~0.6; Mn:≤1.60; p:≤0.045; S:≤0.04 Cr: ≤0.06; Ti:≤0.06;铝<0.8% Mo、Ni不作为验收合格条件,但必须化验用于指导生产;球铁用:Mn:≤0.60,灰铁用:Mn:≤1.60b)废钢中不允许混有高锰钢、轴承钢、不锈钢、硅钢片,灰口、白口铸铁和球铁。
铸铁件通用检验标准
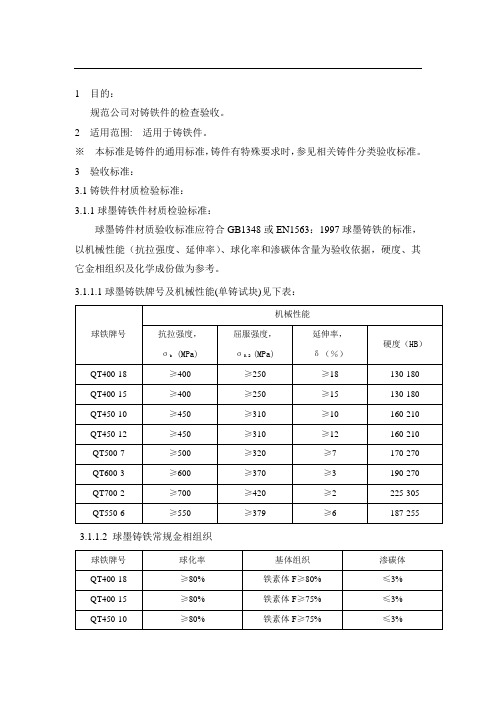
1目的:规范公司对铸铁件的检查验收。
2适用范围: 适用于铸铁件。
※本标准是铸件的通用标准,铸件有特殊要求时,参见相关铸件分类验收标准。
3 验收标准:3.1铸铁件材质检验标准:3.1.1球墨铸铁件材质检验标准:球墨铸件材质验收标准应符合GB1348或EN1563:1997球墨铸铁的标准,以机械性能(抗拉强度、延伸率)、球化率和渗碳体含量为验收依据,硬度、其它金相组织及化学成份做为参考。
3.1.1.1球墨铸铁牌号及机械性能(单铸试块)见下表:3.1.1.2 球墨铸铁常规金相组织3.1.1.3球墨铸铁化学成份3.1.2灰铸铁件材质检验标准:灰铸件材质验收标准应符合GB9439或EN 1561:1997灰铸铁件的标准,以机械性能(抗拉强度)和硬度为验收依据,金相组织及化学成份做为参考。
3.1.2.1灰铸铁牌号及机械性能(单铸试块)见下表:HT250 250-350 190-2403. 1.2.2 灰铸铁常规金相组织3.1.2.3灰铸铁化学成份3.1.3 材质检验取样规范3.1.3.1机械性能检查:机械性能测试的试棒,每班次每种牌号至少浇一组,有新产品时增加一组,每组浇三根,若铸件进行退火处理,必须连同试棒(试块)一同进行热处理(若是渗碳体超标需热处理的件,按热处理后铸件本体的金相组织来验收)。
机械性能试验:二根用于生产厂测试性能(第一根合格则该批次合格,余下试棒留存(留有生产日期、包次标识),在工厂存放,存放期三年;若第一根试棒不合格,测试剩余二根,若第二根不合格则该批次产品全部报废;若第二根合格,应加试第三根,合格则判定该炉产品合格,若第三根不合格则该批次产品全部报废)。
材质检测报告存根(原始记录)保留11年。
常规灰铸铁试棒见下图:常规球墨铸铁试棒见下图:其余其余ASTM536标准(美标)试棒见下图3.1.3.2金相组织检查:球铁铸件从每包铁水的最后一型附铸金相试块或铸件本体进行检验,依次往前直到合格(或本包铁水所浇铸件检验完)为止。
铸件表面质量验收规范
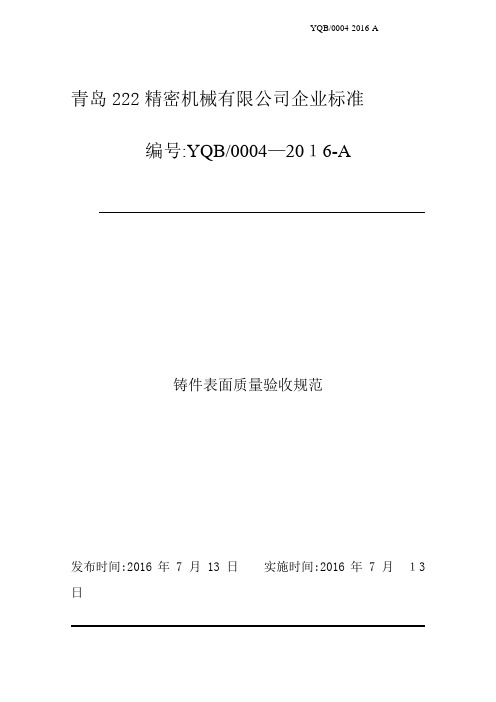
青岛222精密机械有限公司企业标准编号:YQB/0004—2016-A铸件表面质量验收规范发布时间:2016年 7 月 13 日实施时间:2016年 7 月13 日青岛222精密机械有限公司发布1、目的为加强本公司对铸件的质量控制,保证本公司产品的外观质量及加工性能,特制订铸件表面质量验收规范;2、适用范围本规范适用于公司所有外来铸铁(钢)件的外观质量验收,包括表面缺陷、尺寸精度、表面粗糙度的验收;3、引用标准(1)JB/T 5000。
4-2007重型机械通用技术条件第4部分铸铁件;(2)JB/T 5000.6-2007 重型机械通用技术条件第6部分铸钢件;(3)GB6414-1999 铸件尺寸公差与机械加工余量;(4)GB/T6060.1-1997 表面粗糙度比较样块;(5)GB/T15056—1994 铸造表面粗糙度评定方法;(6)Q/XC5101—2001铸铁件通用技术条件;(7GB/T11351—1989铸件重量公差4、名词解释(1)全数选别:检验项目100%检测;5、验收项目及标准铸件的表面质量主要包括铸件的表面缺陷、尺寸精度、形状偏差、表面粗糙度、表面清理质量等;5.1铸件表面缺陷的检验5.1。
1表面缺陷检验的一般要求(1)铸件非加工表面上的浇冒口必须清理得与铸件表面同样平整,加工面上的浇冒口残留量应符合技术要求,若无要求,则按表8执行;(2)在铸件上不允许有裂纹、通孔、穿透性的冷隔和穿透性的缩松、夹渣等机械加工不能去除的缺陷;(3)铸件非加工表面的毛刺、披缝、型砂、砂芯等应清理干净;(4)铸件一般待加工表面,允许有不超过加工余量范围内的任何缺陷存在;重要加工面允许有不超过加工余量2/3的缺陷存在,但裂纹缺陷应予清除;加工后的表面允许存在直径*长度*深度小于等于2*2*2的非连片孔洞的铸造缺陷;(5)作为加工基准面(孔)和测量基准的铸件表面,平整度小于等于2.0毫米、粗糙度Ra50以内;(6)铸件表面气孔、砂眼、夹渣面积不大,但比较分散或者有连片麻点的表面不予接收;(7)除技术要求特别注明的铸件外,对于表面有气孔、缩孔、砂眼等缺陷的铸钢件允许补焊,但铸铁件未经允许不得焊补(铸铁件实行一案一判的原则)但补焊面积不允许超过铸件面积的10%,焊接质量应符合JB/T 5000。
碳素钢铸件标准

目次1.范围 (1)2.规范性引用文件 (1)3.牌号 (2)4.技术要求 (2)5试验方法 (8)6检验规则 (11)7检验文件 (12)8标志、包装、运输和贮存 (13)8.1每个铸件应在非加工面上(不影响配合的面)做下列标志或其中一部分。
(13)附录 (14)碳素钢铸件通用技术条件1.范围本标准规定了碳素钢铸件的牌号、要求、试验方法、检验规则、检验文件、标志、包装、运输和贮存。
本标准适用于产品的图样及技术文件中无特殊要求的低碳钢铸件,凡产品图样或技术文件中无特殊要求时,均应符合本标准的规定。
本标准适用于产品的设计、生产和验收,外协铸件签订技术协议时参照使用。
2.规范性引用文件下列文件对于本文件的应用是必不可少的。
凡注日期的引用文件,仅所注日期的版本适用于本文件。
凡不注日期的引用文件,其最新版本(包括所有修改单)适用于本文件。
GB/T223 钢铁及合金的化学分析方法GB/T228 金属材料室温拉伸试验方法GB/T229-2007 金属材料夏比摆锤冲击试验方法GB/T231.1 金属布氏硬度试验第一部分:试验方法GB/T4336 碳素钢和中低合金钢火花源原子发射光谱分析方法(常规法)GB/T5677 铸钢件射线照相及底片等级分类方法GB/T6060.1-1997 表面粗糙度比较样块铸造表面GB/T6397 金属拉伸试验试样GB/T6414-1999 铸件尺寸公差与机械加工余量GB/T7233 铸钢件超声探伤及质量评级方法GB/T8170 数值修约规则与极限数值的表示和判定GB/T8493-1987 一般工程用铸造碳钢金相GB/T9443-2007 铸钢件渗透检测GB/T9444-2007 铸钢件磁粉检测GB/T11352-1989 一般工程用铸造碳钢件GB/T15056 铸造表面粗糙度评定方法3.牌号碳素钢铸件的牌号为:ZG230-450;ZG270-500;ZG310-570。
4.技术要求4.1机械性能4.1.1碳素钢铸件的热处理,除在图样和有关技术文件中注明者外,均应进行正火或退火处理,经正火或退火后的机械性能功能应符合表4-1的规定。
中国热处理标准大全

中国热处理标准大全机械部热处理标准JB/T 10174-2000 钢铁零件强化喷丸的质量检验方法JB/T 10175-2000 热处理质量控制要求JB/T 3999-1999 钢件的渗碳与碳氮共渗淬火回火JB/T 4155-1999 气体氮碳共渗JB/T 4202-1999 钢的锻造余热淬火回火处理JB/T 4390-1999 高、中温热处理盐浴校正剂JB/T 7951-1999 淬火介质冷却性能试验方法JB/T 8929-1999 深层渗碳JB/T 9197-1999 不锈钢和耐热钢热处理JB/T 9198-1999 盐浴硫氮碳共渗JB/T 9199-1999 防渗涂料技术要求JB/T 9200-1999 钢铁件的火焰淬火回火处理JB/T 9201-1999 钢铁件的感应淬火回火处理JB/T 9202-1999 热处理用盐JB/T 9203-1999 固体渗碳剂JB/T 9204-1999 钢件感应淬火金相检验JB/T 9205-1999 珠光体球墨铸铁零件感应淬火金相检验JB/T 9206-1999 钢件热浸铝工艺及质量检验JB/T 9207-1999 钢件在吸热式气氛中的热处理JB/T 9208-1999 可控气氛分类及代号JB/T 9209-1999 化学热处理渗剂技术条件JB/T 9210-1999 真空热处理JB/T 9211-1999 中碳钢与中碳合金结构马氏体等级JB/T 8555-1997 热处理技术要求在零件图样上的表示方法JB/T 4215-1996 渗硼(代替JB4215-86和JB4383-87)JB/T 8418-1996 粉末渗金属JB/T 8419-1996 热处理工艺材料分类及代号JB/T 8420-1996 热作模具钢显微组织评级JB/T 7709-1995 渗硼层显微组织、硬度及层深测定方法JB/T 7710-1995 薄层碳氮共渗或薄层渗碳钢铁显微组织检验JB/T 7711-1995 灰铸铁件热处理JB/T 7712-1995 高温合金热处理JB/T 7713-1995 高碳高合金钢制冷作模具用钢显微组织检验JB/T 4218-1994 硼砂熔盐渗金属(代替JB/Z235-85和JB4218-86)低温化学热处理工艺方法选择通则JB/T 7519-1994 热处理盐浴(钡盐、硝盐)有害固体废物分析方法JB/T 7529-1994 可锻铸铁热处理JB/T 7530-1994 热处理用氩气、氮气、氢气一般技术条件JB/T 6954-1993 灰铸铁件接触电阻淬火质量检验和评级JB/T 6955-1993 热处理常用淬火介质技术要求JB/T 6956-1993 离子渗氮(代替JB/Z214-84)JB/T 6047-1992 热处理盐浴有害固体废物无害化处理方法JB/T 6048-1992 盐浴热处理JB/T 6049-1992 热处理炉有效加热区的测定JB/T 6050-1992 钢铁热处理零件硬度检验通则JB/T 6051-1992 球墨铸铁热处理工艺及质量检验JB/T 5069-1991 钢铁零件渗金属层金相检验方法JB/T 5072-1991 热处理保护涂料一般技术要求JB/T 5074-1991 低、中碳钢球化体评级中国国家热处理标准GB/T 18177-2000 钢的气体渗氮GB/T 7232-1999 金属热处理工艺术语GB/T 17358-1998 热处理生产电能消耗定额及其计算和测定方法GB/T 16923-1997 钢的正火与退火处理GB/T 16924-1997 钢的淬火与回火处理GB 15735-1995 金属热处理生产过程安全卫生要求GB/T 15749-1995 定量金相手工测定方法GB/T 13321-1991 钢铁硬度锉刀检验方法GB/T 13324-1991 热处理设备术语GB/T 12603-1990 金属热处理工艺分类及代号GB/T 11354-1989 钢铁零件渗氮层深度测定和金相组织检验GB/T 9450-1988 钢铁渗碳淬火有效硬化层深度的测定和校核GB/T 9451-1988 钢件薄表面总硬化层深度或有效硬化层深度的测定GB/T 9452-1988 热处理炉有效加热区测定方法GB/T 8121-1987 热处理工艺材料名词术语GB/T 5617-1985 钢的感应淬火或火焰淬火后有效硬化层深度的测定。
- 1、下载文档前请自行甄别文档内容的完整性,平台不提供额外的编辑、内容补充、找答案等附加服务。
- 2、"仅部分预览"的文档,不可在线预览部分如存在完整性等问题,可反馈申请退款(可完整预览的文档不适用该条件!)。
- 3、如文档侵犯您的权益,请联系客服反馈,我们会尽快为您处理(人工客服工作时间:9:00-18:30)。
Q/ZZ
锻件热处理验收规范
中国重型汽车集团有限公司发布
前 言
本标准代替QZZ 30021—1996《锻件热处理验收规范》。
本标准与QZZ 30021—1996相比,主要变化如下:
——标准的编排格式按GB/T 1.1—2009《标准化工作导则 第1 部分:标准的结构和编写》的规定 进行了调整;
——对原标准中3.2条、3.3条进行了修订,并取消了原标准中5.3.2条;
——删除原标准3.4条对等温退火工艺晶粒度检测,增加调质工艺;
——对原标准3.5条增加了“如没有规定,一般锻件按取样部位处总脱碳层深度,每边应小于或等于有效厚度的1%”
——对原标准中3.6条进行了修订,增加了“但当锻件尺寸不够取拉伸试样时,则应按强度与硬度值进行换算后,对该锻件在取拉伸试样部位进行硬度检测。
”
——对原标准中5.3.3条进行了修订,取消金相组织半级的规定;
——在新标准中增加了3.8条和3.9条对过热和过烧的规定;
——原标准中规定了拉伸性能,在新标准中修订为力学性能,并增加了对冲击韧性的检验规定; ——新标准中增加了非调质钢的有关规定;
——取消了原标准5.3.2中所列出的各种具体钢号;
——因GB/T 13320-2007较91版作了很大的改动,故金相组织评级图参照GB/T 13320-2007; ——原标准中取样位置已经不适用,对力学性能的取样位置按DIN EN 10083-1:2006-10重新作了规定;
——增加了5.4.1和5.4.2条款,对热处理硬度的测定位置进行了明确规定;
——对金相试样的取样位置重新作了规定,取消原标准中对边部和心部金相组织的判定依据; ——取消了原标准5.5.3中对金相试样的硬度检测;
——因GB6397已取消,所以本标准中取消了GB6397标准;
——本次修订删除了原标准中的“斯达—斯太尔汽车”、“等温退火”等词语;
—— 增加了GB/T 229冲击试验标准和DIN EN 10083-1:2006-10 力学性能取样标准;
——对原标准的附录A进行了修订。
本标准的附录A为规范性附录。
本标准为第一次修订。
本标准由中国重型汽车集团有限公司提出。
本标准由中国重型汽车集团有限公司技术中心归口。
本标准主要起草人:鲁统轮、李玉新。
本标准所代替标准的历次版本发布情况为:——QZZ 30021-1996。
锻件热处理验收规范
1 范围
本标准规定了钢质锻件的金相组织、晶粒度、硬度、脱碳层、力学性能、过热及过烧等检验验收的技术条件。
本标准适用于经过正火处理、调质处理、锻后控冷处理的结构钢模锻件。
2 规范性引用文件
下列文件对于本文件的应用是必不可少的。
凡是注日期的引用文件,仅所注日期的版本适用于本文 件。
凡是不注日期的引用文件,其最新版本(包括所有的修改单)适用于本文件。
GB/T 224 钢的脱碳层深度测定法
GB/T 228 金属材料室温拉伸试验方法
GB/T 229 金属夏比缺口冲击试验方法
GB/T 230 金属洛氏硬度试验方法
GB/T 231 金属布氏硬度试验方法
GB/T 6394 金属平均晶粒度测定法
GB/T 13320-2007 钢质模锻件金相组织评级图及评定方法
GB/T 13299 钢的显微组织评定方法
DIN EN 10083-1:2006-10 淬火和回火钢 第1部分:一般交货技术条件
3 要求
3.1 锻件经热处理后应符合本标准的规定,并按产品图和锻件图的有关技术要求。
3.2 中碳结构钢正火处理的锻件,以及中碳低合金非调质钢锻后控冷处理的锻件,金相组织的合格级别应按GB/T 13320-2007第一组评级图取1~4级。
3.3 调质钢调质处理的锻件,金相组织的合格级别应按GB/T 13320-2007第三组评级图取1~4级。
3.4 正火或调质后锻件的奥氏体晶粒度合格级别,应按GB/T 6394取5∽8级,且其晶粒度不均匀程度应小于3个等级。
3.5 锻件的脱碳层深度按锻件图或相关的技术条件要求执行。
如没有规定,一般锻件按取样部位处总脱碳层深度,每边应小于或等于有效厚度的1%。
3.6 当产品图中对零件的热处理有明确的力学性能要求时,则应对该锻件按规定取样进行试验,并应达到其力学性能指标。
但当锻件尺寸不够取拉伸试样时,则应按强度与硬度值进行换算后,对该锻件在关键部位进行硬度检测。
3.7 当产品图中对零件的热处理硬度有明确的检测要求时,则应按要求检测。
Q/ZZ 30021—××××
3.8 当发现锻件组织有过热时,参照GB/T 13299 《钢的显微组织评定方法》规定,当魏氏组织不大于3级时可以使用,大于3级不能使用。
3.9 当发现锻件组织有过烧时,则该批锻件应按报废处理。
3.10 对重要锻件另有技术条件或标准,则应按其技术条件或标准执行。
4 抽样
4.1 硬度的测定按每个热处理批次取百分之一抽检,但每批次至少抽三件。
4.2 金相组织的评定,以及晶粒度、脱碳层的测定,按每个热处理批次取一个试样。
4.3 力学性能的测定按锻件毛坯的每个热处理批次,其中所规定硬度范围的上限附近和下限附近各取一个样件,或根据实际情况由供需双方协定。
5 试验方法
5.1 试样的制取
5.1.1 取样部位应选取零件的关键部位,或反映锻件热处理质量特征的部分,或按产品图纸的要求等。
5.1.2 金相试样的取样部位
有特殊约定的,按约定执行。
没有约定的,按锻件的有效厚度处作为取样部位。
5.1.2.1 当锻件取样部位有效厚度≤20mm时,以二分之一处作为检验部位制取。
5.1.2.2 当锻件取样部位有效厚度>20mm时,以距表面10 mm处作为检验部位制取。
5.1.3 力学性能试样的取样部位见产品图要求或附录A,试样形状分别见GB/T 228和GB/T 229。
5.1.4 试样应在冷态下用机械方法截取。
如用热切等方法截取时,必须将其影响区完全去除,不能出现因受热而导致组织改变的现象。
5.1.5 金相试样经抛光后用含有体积分数2%∽5%的硝酸酒精溶液浸蚀。
5.2 金相组织的评定
5.2.1 正火或锻后控冷锻件的金相组织在金相显微镜下放大100倍观察,取其最差组织予以评定,但必须结合高倍观察以确定相结构,参照GB/T 13320-2007评级图1或图2评定。
调质锻件试样的金相组织在金相显微镜下放大500倍观测,取其最差组织,参照GB/T 13320-2007评级图3予以评定。
5.2.2 当所评金相组织介于两个级别之间时,以下一级为判定级别,例如大于3级小于4级则判为4级。
5.3 正火或调质后锻件的奥氏体晶粒度评定的方法按GB/T 6394中的比较法进行。
5.4 硬度的测定
5.4.1 当产品图中对零件的热处理硬度有明确的测定部位时,则应按产品图的指定部位检测。
5.4.2 当产品图中对零件的热处理硬度没有明确的测定部位时,则指锻件毛坯的表面硬度,按 5.1.1选取测量硬度部位。
5.4.3 布氏硬度的测定按GB/T 231进行,洛氏硬度的测定按GB/T 230进行。
Q/ZZ 30021—2011 5.4.4 根据需要可对锻件的指定部位取样加工后,测定其截面的硬度分布情况,乃至绘出硬度分布曲线进行评议。
5.5 脱碳层深度的测定
5.5.1 在所检验的锻件金相试样上测量脱碳层深度。
5.5.2 脱碳层深度的测量按GB/T 224进行。
5.5.3 在金相显微镜下放大100倍观察和测量,以最严重处的深度作为脱碳层深度。
5.6 力学性能的测定
5.6.1 拉伸试验按GB/T 228进行。
5.6.2 冲击试验按GB/T 229进行。
5.7 复验和判定规则
5.7.1 在试验过程中,如果是由于试验方法或试样制备的缺陷,而造成试验结果不能达到规定的要求时,则该次试验结果无效,并应重新进行试验。
5.7.2 如果试验正确无误,但其结果不能达到规定的要求,则可以进行一次复验。
其方法是,对于每个经试验不合格的项目,应在同一批锻件中按抽样数量的两倍抽样进行试验。
5.7.3 如果复验中的试验结果均合格,则该批锻件判为合格。
如果复验中的试验结果有一项不合格,则该批锻件判为不合格。
Q/ZZ 30021—××××
附 录 A
(规范性附录)
力学性能试样的截取位置 A.1 力学性能试样的截取位置见表A.1
Q/ZZ 30021—2011 表A.1力学性能试样的截取位置(续)。