锻件常用的热处理方法有哪几种
锻件热处理

锻件热处理锻件是一种金属成形加工方法,在完成锻造后需要经过热处理。
锻件热处理是指将锻件加热到一定的温度,使之发生一系列物理或化学变化,达到改变其组织结构和性能的目的。
本文将针对锻件热处理的流程、方法和机理进行阐述。
锻件热处理的流程锻件热处理流程通常包括三个步骤:加热、保温和冷却。
其中,加热和冷却的过程都非常关键,因为这两个步骤会直接影响到锻件的微观组织和力学性能。
1.加热加热是指将锻件加热到一定的温度,使之发生晶粒长大、变形、晶格缺陷消失、相变等变化,从而获得一定的机械性能。
加热温度和时间是通过锻件的成分、形状和尺寸等因素来决定的。
一般来说,锻件加热到一定温度后,其冷却速度直接影响到锻件的性能。
常见的加热方式包括电阻加热、燃气加热、电弧加热、激光加热等。
2.保温保温是指将已经加热到一定温度的锻件保持在一个固定的温度下一定时间,以使锻件内部保持均匀温度,从而达到热处理的效果。
保温时间和温度取决于锻件的材质和尺寸。
优化中间温度和时间会对晶粒尺寸和锻件性能有着直接的影响。
相较于加热和冷却,保温过程是一个相对简单的步骤。
3.冷却冷却是指将经过加热和保温过程的锻件缓慢冷却至室温,使之形成相应的组织结构和力学性能。
冷却方式和速度对锻件的性能有着直接的影响。
常用的冷却方式包括空气冷却、水冷却等。
锻件热处理的方法和机理1.灭火热处理灭火热处理是指将经过加热处理的锻件,迅速放入冷却介质中,使其迅速冷却达到强化锻件的目的。
灭火热处理可以分为水淬火、油淬火、高温淬火和空气冷却等多种方式,其中以水淬火的强度最大,油淬火次之,在高温淬火和空气冷却中最低。
灭火热处理的机理是利用快速冷却的方式,使锻件内部的物理性能和化学性能发生变化,形成更加细小的晶粒和组织结构。
从而达到提高锻件材质的强度和硬度的目的。
2.回火热处理回火热处理是指在灭火热处理完成后,对锻件进行再次加热并显著降低冷却速度,从而提高锻件的韧性和塑性。
对于某些硬度较高的锻件,为了兼顾强度与韧性的要求,通常需要进行回火处理。
热处理工艺在船舶工程中的应用

热处理工艺在船舶工程中的应用近年来,随着船舶工程的不断发展,热处理工艺在船舶制造和维修中的应用越来越广泛。
热处理工艺通过改变材料的组织结构和性能,提高船舶的强度、硬度和耐腐蚀性,从而改善船舶的整体性能和可靠性。
本文将详细介绍热处理工艺在船舶工程中的应用,并探讨其优势和挑战。
一、船舶锻件的热处理船舶锻件是船舶工程中重要的组成部分,其质量和性能对船舶的安全运行至关重要。
通过热处理工艺,可以改善锻件的组织结构和硬度,提高其耐久性和抗疲劳性能。
常用的船舶锻件热处理工艺包括正火、回火和淬火等。
正火是通过加热锻件至超过临界温度后保温一段时间,然后冷却至室温的方法。
这种热处理可以降低锻件的硬度,提高其可加工性和韧性。
回火是将正火后的锻件再次加热至适当温度,然后冷却至室温。
这种热处理可以消除锻件中的残余应力,提高其抗腐蚀性能和可靠性。
淬火是将正火后的锻件迅速冷却至低温,使其硬度大幅提高,从而提高其耐磨性和抗冲击性能。
二、船舶焊接件的热处理焊接是船舶制造和维修中常用的连接方法,焊接件的质量对船舶的结构强度和密封性有着重要影响。
通过热处理工艺,可以改善焊接件的组织结构和性能,提高焊接接头的可靠性和耐腐蚀性能。
焊接接头常常会出现硬化现象,这会导致焊接接头的脆性增加,从而降低其可靠性。
通过热处理工艺可以解除焊接接头中的硬化,提高其韧性和可靠性。
淬火和回火是常用的焊接件热处理方法。
淬火可以提高焊缝表面的硬度和耐磨性,而回火可以消除焊缝中的残余应力,提高其耐蚀性和韧性。
三、船舶管道的热处理船舶工程中的管道系统起着输送液体、气体和其他物质的重要作用。
通过热处理工艺,可以提高船舶管道的强度、耐腐蚀性和密封性,确保管道系统的安全运行。
船舶管道中常见的材料包括碳钢、不锈钢和铜合金等。
为了提高这些材料的硬度和强度,常常采用淬火热处理工艺。
对于不锈钢和铜合金等耐腐蚀材料,可以通过回火热处理工艺降低其硬度,提高其可塑性和焊接性。
总结:热处理工艺在船舶工程中的应用具有重要意义。
锻件常用的热处理方法退火

锻件常用的热处理方法退火
锻件常用的热处理方法之一是退火。
退火是指将金属加热到一定温度,保温一段时间后,以适当速度冷却至室温。
退火可以改善锻件的组织性能,减轻内应力,提高机械性能和加工性能。
常见的退火方法有以下几种:
1. 全退火:将锻件加热到高于临界温度,保温一定时间后冷却。
适用于各种锻件。
2. 球化退火:将锻件加热至高于临界温度,保温一段时间后通过较慢的冷却使组织转变为球状。
适用于合金钢、工具钢等。
3. 精细退火:将锻件加热至高于临界温度,保温后通过较快的冷却获得细小的晶粒尺寸。
适用于提高锻件的强度和韧性。
4. 均匀退火:将锻件加热至高于临界温度,保温后通过较慢的冷却使晶粒尺寸得到均匀分布。
适用于大型锻件或晶粒不均匀的锻件。
5. 线加热退火:采用电阻加热或电子束加热,将锻件加热至退火温度,通过较慢的冷却进行退火。
适用于特殊形状或大型锻件。
这些退火方法的选择要根据锻件的具体材料和要求来决定,以达到锻件组织和性
能的优化。
大型锻件的热处理

冷却工艺
回火冷却
大型锻件
一般在400℃以上的冷却速度应控制在50℃/h~ 高温回火 (≥450℃)后必须采用水冷或油冷等冷却较5℃/h,对于40Cr、3Cr13 等钢具有明显可逆回火脆性的材料,该种方法将使该材料的冲击韧性 显著降低。回火冷却时应考虑以下两点:①对无高温回火脆性材料, 如45、35CrMo、42CrMo、45CrMo钢等,采用随炉冷却或空冷的缓 慢冷却方式。②对具有高温回火脆性的材料,如40Cr、3Cr13、Crl2 钢等,在低温回火快的方式进行冷却,以避免出现回火脆性,为了进 一步消除由于回火冷却带来的应力,然后补充进行一次400C左右的 去除内应力退火。
BJTU
大型锻件热处理工艺
10224006 郭睿
北京交通大学
北京交通大学
目录大Βιβλιοθήκη 锻件研究原因大型锻件热处理缺陷
热处理工艺
研究原因
大型锻件
大型锻件是指用1000t或更大吨位水压机或其他 千吨以上压力机生产的锻件。随着大型锻件的尺寸 和重量的增加,热处理时有效厚度也随之发生变化。 由于截面的增大,不可避免地存在成分偏析、非金 属夹杂、显微空隙等冶金缺陷,再加上相变潜热的 影响,在加热和冷却过程中产生的应力较大,极易 引工件的畸变和开裂。
图示_02
大型锻件
大型锻件热处理 常见缺陷
大晶粒
晶粒不均匀
冷硬现象
裂纹 飞边裂纹 局部充填不足
龟裂 碳化物偏析级别不符要求
飞边裂纹 带状组织
热处理工艺
大型锻件
正火和淬火的加热
正火和淬火的加热
回火加热
正火和淬火冷却 回火冷却
加热工艺
正火和淬火的加热
大型锻件
大型锻件特别是合金钢锻件,在加热方式上应采用阶梯升温方式加热。有关 资料表明l2 J大型锻件在350℃~500℃以及600℃~800℃时工件表面与心部存在 最大温差,差值在300℃~400℃左右。因此采用在450℃与650℃保温一段时间, 然后再升温的加热方法是比较合适的。大型锻件正火和淬火加热温度的选择,理 论上与小型锻件是一致的,应取理论加热温度的上限,以保证偏析区也能达到相 应的正火或淬火温度,使工件充分奥氏体化。装炉温度≤400℃,并在450℃保持一 定时间,以进一步减小锻件在蓝脆温度范围 (250℃ ~ 350℃)内的温差。在 450℃ 保温之前由于锻件温度低,仍处于线弹性状态,如果表面与心部温差引起的热应 力过大,可致锻件在加热过程中早期开裂。因此,保温前加热速度一般控制在 30℃ / h-70℃ / h ; 450℃ 保温后可适当加快升温速度但不能超过 100℃ / h ~ 15012/ h。锻件经过 650℃ 保温后,心部与表面还可能存在温差,但由于锻件处 于塑性状态,尤其是当锻件加热到临界点温度以上时,相变超塑性伴随产生,因 而导致开裂的可能性极小,此时可按设备功率升温。均温时间凭经验目测决定, 锻件表面温度均匀一致并和炉墙颜色相同时为止,工艺不做要求,均温结束即开 始保温。
不锈钢锻件锻后热处理

不锈钢锻件锻后热处理
不锈钢锻件在锻造过程中会产生大量的应力和变形,因此需要进行锻后热处理来消除这些应力和变形,同时提高其力学性能和抗腐蚀能力。
常见的锻后热处理方法包括退火、固溶处理和时效处理。
1. 退火处理:通过加热至一定温度,保持一定时间后再缓慢冷却,使锻件内部组织得到均匀细小的晶粒,消除锻造过程中的应力和变形。
常用的退火处理方法有全退火、球化退火和退火软化处理。
2. 固溶处理:特定不锈钢合金中存在固溶相,通过加热至一定温度使其达到固溶态,然后迅速冷却到室温,可提高不锈钢合金的强度和硬度,并改善其耐腐蚀性能。
常用的固溶处理方法有单相固溶处理和双相固溶处理。
3. 时效处理:在固溶处理之后,将锻件加热至一定温度,保持一定时间后再通过快速冷却来稳定其组织和性能。
时效处理可进一步提高不锈钢锻件的强度和硬度,同时保持其良好的耐腐蚀性能。
需要注意的是,不同种类的不锈钢合金可能需要不同的热处理方法和工艺参数,因此在实际操作中需根据具体情况进行选择。
另外,合理控制热处理过程中的温度和时间,以确保达到预期的热处理效果。
42CrMo钢锻件热处理工艺

42CrMo钢锻件热处理工艺42CrMo钢锻件,锻后要求进行调质处理。
因其截面尺寸相差悬殊,水淬开裂倾向较大,油淬后大截面部位的淬火硬度又偏低,金相组织与力学性能不合格的情况时有发生,直接影响了曲轴疲劳强度及整机使用寿命。
1、淬火工艺2、淬火880℃,水冷、油冷3、调质硬度调质以后的硬度大概在HRC32-36之间,150C回火--55HRC 200C回火--53HRC [5][6] 300C回火--51HRC400C回火--43HRC 500C回火--34HRC 550C回火--32HRC 600C回火--28HRC 650C回火--24HRC4、具有高强度和高屈服点,综合力学性能比40Cr要好。
冷变形塑性和切削性均属中等,过热敏感性小,但有回火脆性倾向及白点敏感性。
一般在调质状态下使用5、采用水溶性淬火介质淬火工艺。
为保证淬火液的正常使用,须对淬火液温度进行严格的控制。
淬火介质的逆溶点为70℃,最佳使用温度为(30~60)℃。
将淬火液温度必须始终控制在工艺要求的范围内(见图4)。
6、工艺的确定及生产应用根据有关资料,我们用正交试验方法对连杆热处理工艺参数进行了优选,确定出比较适宜的介质浓度为8—20浓度为12%(可根据工件的大小、厚薄调整浓度在8~12),并在此基础上,经过补充试验确结果表明,连杆与曲轴的淬火硬度均达到或超过了45HRC,与原来用油淬工艺相比,淬火硬度提高(5~10)HRC。
金相检查表明,回火后的组织状态较油淬有明显的改善,故在强度相同的情况下,冲击韧度比油淬有了大幅度提高,由原来用油淬的80~100J/cm2提高到平均120J/cm2以上,力学性能与硬度的一次交检合格率分别达到100%和95%。
不仅淬火效果好,产品合格率高,而且淬火时无烟气,改善了生产环境。
对解决42CrMo等合金钢锻件“水淬开裂,油淬不硬”问题效果显著,并且,使用浓度低,粘度小,淬火时带出量少,消耗费用仅为油淬的50%一60%,可大大减少生产费用及不良品的损失费用。
模锻的后续工序介绍
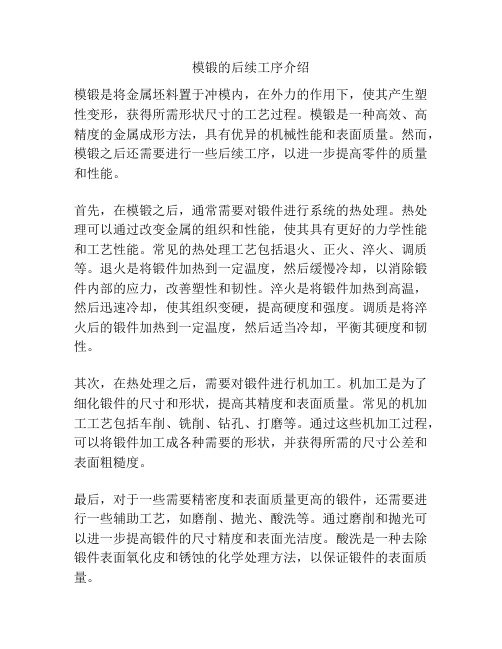
模锻的后续工序介绍模锻是将金属坯料置于冲模内,在外力的作用下,使其产生塑性变形,获得所需形状尺寸的工艺过程。
模锻是一种高效、高精度的金属成形方法,具有优异的机械性能和表面质量。
然而,模锻之后还需要进行一些后续工序,以进一步提高零件的质量和性能。
首先,在模锻之后,通常需要对锻件进行系统的热处理。
热处理可以通过改变金属的组织和性能,使其具有更好的力学性能和工艺性能。
常见的热处理工艺包括退火、正火、淬火、调质等。
退火是将锻件加热到一定温度,然后缓慢冷却,以消除锻件内部的应力,改善塑性和韧性。
淬火是将锻件加热到高温,然后迅速冷却,使其组织变硬,提高硬度和强度。
调质是将淬火后的锻件加热到一定温度,然后适当冷却,平衡其硬度和韧性。
其次,在热处理之后,需要对锻件进行机加工。
机加工是为了细化锻件的尺寸和形状,提高其精度和表面质量。
常见的机加工工艺包括车削、铣削、钻孔、打磨等。
通过这些机加工过程,可以将锻件加工成各种需要的形状,并获得所需的尺寸公差和表面粗糙度。
最后,对于一些需要精密度和表面质量更高的锻件,还需要进行一些辅助工艺,如磨削、抛光、酸洗等。
通过磨削和抛光可以进一步提高锻件的尺寸精度和表面光洁度。
酸洗是一种去除锻件表面氧化皮和锈蚀的化学处理方法,以保证锻件的表面质量。
总之,模锻是金属成形的重要方法,但仅仅完成模锻过程还不能得到最终的零件,还需要进行一系列的后续工序,如热处理、机加工和辅助工艺等。
这些工序的进行可以进一步提高锻件的质量和性能,满足不同工程需求。
继续进行后续工序的介绍。
热处理是模锻后一项非常重要的工序,它可以改变金属的组织和性能,提高锻件的力学性能和工艺性能。
常见的热处理工艺中,退火是一种广泛使用的方法。
退火过程中,锻件被加热到一定温度下,保温一段时间,然后缓慢冷却。
这个过程主要是为了消除锻件内部的应力,改善锻件的塑性和韧性。
退火后的锻件具有更好的成形性能和可加工性。
除了退火外,还有一些特殊的热处理工艺。
非标工程机械锻件加工方案

非标工程机械锻件加工方案一、引言随着工程机械行业的不断发展,各种工程机械的需求不断增加。
工程机械锻件作为工程机械的关键零部件之一,其质量和精度要求极高。
为了满足市场需求,提高产品质量,本文将针对工程机械锻件加工方案进行详细阐述。
二、工程机械锻件加工工艺流程1. 锻造工程机械锻件首先需要进行锻造。
锻造是通过应用外力将金属进行塑性变形,从而得到所需形状的工艺方法。
对于工程机械锻件,常用的锻造设备有液压机、冲击锻机等。
在锻造过程中,要注意控制温度,保证金属成形的均匀性。
2. 热处理在锻造后,工程机械锻件需要进行热处理。
热处理是通过加热和冷却过程改变金属的结构和性能的工艺方法。
常用的热处理工艺包括退火、正火、淬火等。
热处理的目的是提高工程机械锻件的硬度、强度和耐磨性。
3. 机械加工在锻造和热处理之后,工程机械锻件需要进行机械加工。
机械加工是通过对金属进行切削、钻孔、铣削、打磨等工艺,将锻件加工成最终的形状和尺寸。
常用的机械加工设备有车床、铣床、钻床、磨床等。
机械加工过程中要注意控制加工精度和表面质量。
4. 装配最后,工程机械锻件需要进行装配。
装配是将各个零部件按照设计要求组装成完整的工程机械产品的过程。
在装配过程中要注意零部件之间的配合精度和间隙,保证整机的运行稳定和可靠。
以上是工程机械锻件的加工工艺流程,下面将详细介绍每个环节的加工方案。
三、工程机械锻件加工方案1. 锻造加工方案(1)选材工程机械锻件的选材应根据产品的使用环境和要求进行选择,常见的材料有碳素钢、合金钢、不锈钢等。
在选材时要考虑材料的强度、韧性、耐磨性等性能指标。
(2)设备选择对于不同材质和形状的工程机械锻件,需要选择不同类型的锻造设备。
通常情况下,大型扁锻件适宜采用液压机,而小型复杂形状的锻件适宜采用冲击锻机。
(3)控制参数在锻造过程中,要根据锻件的形状、尺寸和材质等因素,控制好温度和锻造速度,以保证锻件成形的均匀性和尺寸精度。
2. 热处理加工方案(1)退火对于一些碳素钢和合金钢的工程机械锻件,需要进行退火处理。