纺织品的数码印花
2024年纺织数码印花机市场环境分析
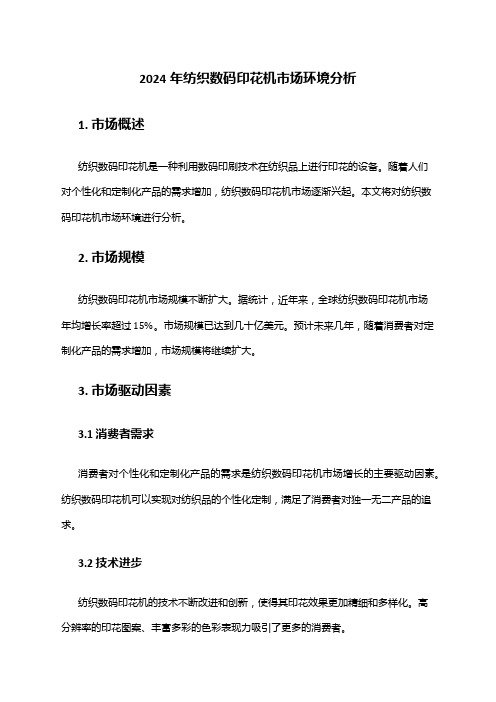
2024年纺织数码印花机市场环境分析1. 市场概述纺织数码印花机是一种利用数码印刷技术在纺织品上进行印花的设备。
随着人们对个性化和定制化产品的需求增加,纺织数码印花机市场逐渐兴起。
本文将对纺织数码印花机市场环境进行分析。
2. 市场规模纺织数码印花机市场规模不断扩大。
据统计,近年来,全球纺织数码印花机市场年均增长率超过15%。
市场规模已达到几十亿美元。
预计未来几年,随着消费者对定制化产品的需求增加,市场规模将继续扩大。
3. 市场驱动因素3.1 消费者需求消费者对个性化和定制化产品的需求是纺织数码印花机市场增长的主要驱动因素。
纺织数码印花机可以实现对纺织品的个性化定制,满足了消费者对独一无二产品的追求。
3.2 技术进步纺织数码印花机的技术不断改进和创新,使得其印花效果更加精细和多样化。
高分辨率的印花图案、丰富多彩的色彩表现力吸引了更多的消费者。
3.3 环保要求纺织数码印花机相比传统印花机具有环保优势。
其采用水性染料和无污染的打印过程,减少了对环境的污染。
随着环保要求的提高,纺织数码印花机市场受到了更多的关注。
4. 市场竞争纺织数码印花机市场竞争激烈,主要有以下几个竞争因素:4.1 产品质量和印花效果纺织数码印花机的产品质量和印花效果是竞争的关键。
消费者对于印花的色彩、精细度和持久性有着高要求,只有具备优秀的印花效果的产品才能在竞争中脱颖而出。
4.2 价格价格是竞争的重要因素之一。
市场上存在着高端、中端和低端纺织数码印花机产品,价格差异较大。
消费者在选择时会对价格进行比较,选择性价比高的产品。
4.3 售后服务售后服务是消费者选择纺织数码印花机的重要考虑因素。
优质的售后服务能够提供技术支持、设备维护等保障,满足消费者的需求。
5. 市场前景纺织数码印花机市场前景广阔。
随着消费者对个性化和定制化产品需求的增加,纺织数码印花机将得到更广泛的应用。
同时,随着技术进步和环保要求的提高,纺织数码印花机市场将迎来更多的机遇。
浅析数码喷墨印花在纺织领域的应用
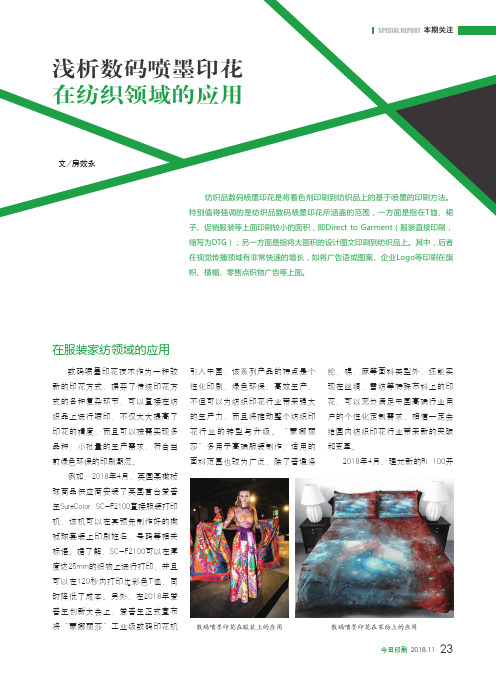
今日印刷 2018.1123本期关注SPECIAL REPORT 浅析数码喷墨印花在纺织领域的应用在服装家纺领域的应用数码喷墨印花技术作为一种较新的印花方式,摒弃了传统印花方式的各种复杂环节,可以直接在纺织品上进行喷印,不仅大大提高了印花的精度,而且可以按需实现多品种、小批量的生产需求,符合当前绿色环保的印刷潮流。
例如,2018年4月,英国某橄榄球商品供应商安装了英国首台爱普生SureColor SC-F2100直接服装打印机,该机可以在其预先制作好的橄榄球套装上印刷姓名、号码等相关标语。
据了解,SC-F2100可以在厚度达25mm的织物上进行打印,并且可以在120秒内打印出彩色T恤,同时降低了成本。
另外,在2018年爱普生创新大会上,爱普生正式宣布将“蒙娜丽莎”工业级数码印花机数码喷墨印花在服装上的应用数码喷墨印花在家纺上的应用纺织品数码喷墨印花是将着色剂印刷到纺织品上的基于喷墨的印刷方法。
特别值得强调的是纺织品数码喷墨印花所涵盖的范围,一方面是指在T恤、裙子、促销服装等上面印刷较小的面积,即Direct to Garment(服装直接印刷,缩写为DTG);另一方面是指将大面积的设计图文印刷到纺织品上。
其中,后者在视觉传播领域有非常快速的增长,如将广告语或图案、企业Logo等印刷在旗帜、横幅、零售点织物广告等上面。
引入中国,该系列产品的特点是个性化印刷、绿色环保、高效生产,不但可以为纺织印花行业带来强大的生产力,而且将推动整个纺织印花行业的转型与升级。
“蒙娜丽莎”多用于高端服装制作,适用的面料范围也较为广泛,除了普通涤纶、棉、麻等面料类型外,还能实现在丝绸、雪纺等特殊布料上的印花,可以充分满足中国高端行业用户的个性化定制需求,相信一定会给国内纺织印花行业带来新的突破和变革。
2018年4月,理光新的RI 100开文/房效永本期关注SPECIAL REPORT始商用,该机采用了理光的压电喷墨技术,能够实现清晰、高品质的打印效果。
数码印花材料
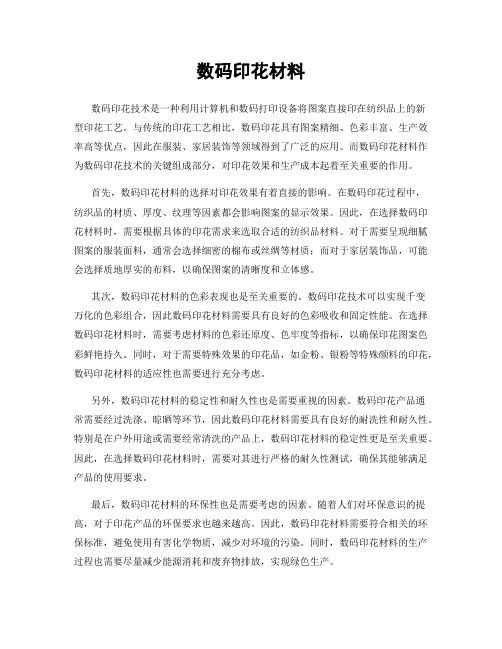
数码印花材料数码印花技术是一种利用计算机和数码打印设备将图案直接印在纺织品上的新型印花工艺。
与传统的印花工艺相比,数码印花具有图案精细、色彩丰富、生产效率高等优点,因此在服装、家居装饰等领域得到了广泛的应用。
而数码印花材料作为数码印花技术的关键组成部分,对印花效果和生产成本起着至关重要的作用。
首先,数码印花材料的选择对印花效果有着直接的影响。
在数码印花过程中,纺织品的材质、厚度、纹理等因素都会影响图案的显示效果。
因此,在选择数码印花材料时,需要根据具体的印花需求来选取合适的纺织品材料。
对于需要呈现细腻图案的服装面料,通常会选择细密的棉布或丝绸等材质;而对于家居装饰品,可能会选择质地厚实的布料,以确保图案的清晰度和立体感。
其次,数码印花材料的色彩表现也是至关重要的。
数码印花技术可以实现千变万化的色彩组合,因此数码印花材料需要具有良好的色彩吸收和固定性能。
在选择数码印花材料时,需要考虑材料的色彩还原度、色牢度等指标,以确保印花图案色彩鲜艳持久。
同时,对于需要特殊效果的印花品,如金粉、银粉等特殊颜料的印花,数码印花材料的适应性也需要进行充分考虑。
另外,数码印花材料的稳定性和耐久性也是需要重视的因素。
数码印花产品通常需要经过洗涤、晾晒等环节,因此数码印花材料需要具有良好的耐洗性和耐久性。
特别是在户外用途或需要经常清洗的产品上,数码印花材料的稳定性更是至关重要。
因此,在选择数码印花材料时,需要对其进行严格的耐久性测试,确保其能够满足产品的使用要求。
最后,数码印花材料的环保性也是需要考虑的因素。
随着人们对环保意识的提高,对于印花产品的环保要求也越来越高。
因此,数码印花材料需要符合相关的环保标准,避免使用有害化学物质,减少对环境的污染。
同时,数码印花材料的生产过程也需要尽量减少能源消耗和废弃物排放,实现绿色生产。
总之,数码印花材料作为数码印花技术的关键组成部分,对印花效果和产品质量有着重要的影响。
在选择数码印花材料时,需要综合考虑材料的选择、色彩表现、稳定性、耐久性和环保性等因素,以确保最终的印花产品能够满足市场和客户的需求。
纺织品数码印花技术综述

纺织品数码印花技术综述
随着人们对时尚的追求和需求的不断提高,纺织品出现了越来越多的个性化需求。
为满足这种需求,数码印花技术应运而生。
纺织品数码印花技术是指将印花图案通过计算机控制的数码喷墨设备直接喷印在纺织品上,以制作个性化或小批量的图案纺织品。
相比传统的印刷方式,数码印花技术具有印刷图案丰富多彩,颜色层次感强,印花成本低,生产周期短等优点。
数码印花技术的主要应用领域是服装、家居纺织品、鞋帽等行业。
其应用可以大大提高产品的附加值和市场竞争力,满足不同消费者的需求,并推动纺织业的发展。
目前,国内的数码印花技术已经具备了较高的水平,不仅能够印刷出高清晰度、高色彩还原度的图案,还能够印刷在各种不同材质的纺织品上。
未来,纺织品数码印花技术将不断发展,向智能化、自动化的方向发展,推动行业不断向前进步。
棉织物数码印花上浆工艺
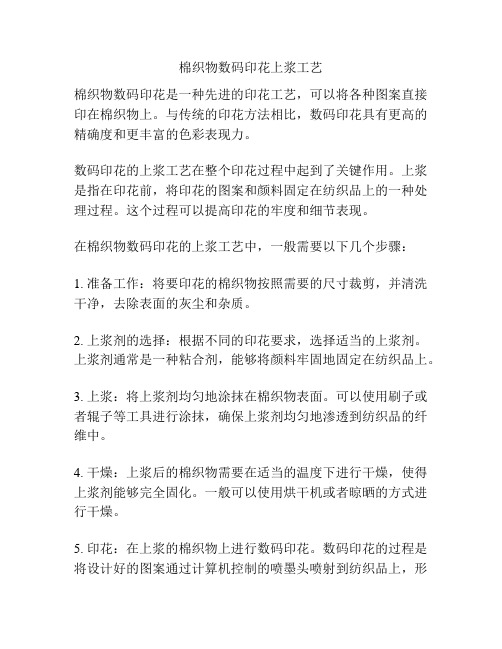
棉织物数码印花上浆工艺
棉织物数码印花是一种先进的印花工艺,可以将各种图案直接印在棉织物上。
与传统的印花方法相比,数码印花具有更高的精确度和更丰富的色彩表现力。
数码印花的上浆工艺在整个印花过程中起到了关键作用。
上浆是指在印花前,将印花的图案和颜料固定在纺织品上的一种处理过程。
这个过程可以提高印花的牢度和细节表现。
在棉织物数码印花的上浆工艺中,一般需要以下几个步骤:
1. 准备工作:将要印花的棉织物按照需要的尺寸裁剪,并清洗干净,去除表面的灰尘和杂质。
2. 上浆剂的选择:根据不同的印花要求,选择适当的上浆剂。
上浆剂通常是一种粘合剂,能够将颜料牢固地固定在纺织品上。
3. 上浆:将上浆剂均匀地涂抹在棉织物表面。
可以使用刷子或者辊子等工具进行涂抹,确保上浆剂均匀地渗透到纺织品的纤维中。
4. 干燥:上浆后的棉织物需要在适当的温度下进行干燥,使得上浆剂能够完全固化。
一般可以使用烘干机或者晾晒的方式进行干燥。
5. 印花:在上浆的棉织物上进行数码印花。
数码印花的过程是将设计好的图案通过计算机控制的喷墨头喷射到纺织品上,形
成所需的图案。
6. 固化:印花后的棉织物需要进行固化处理,使得颜料能够牢固地固定在纺织品上。
一般可以采用高温烘烤或者使用固化剂进行固化。
通过上述步骤,棉织物数码印花的上浆工艺可以保证印花效果的质量和持久性。
同时,上浆也可以提升纺织品的手感和光泽度,使得印花的效果更加优秀。
数码印花的优缺点
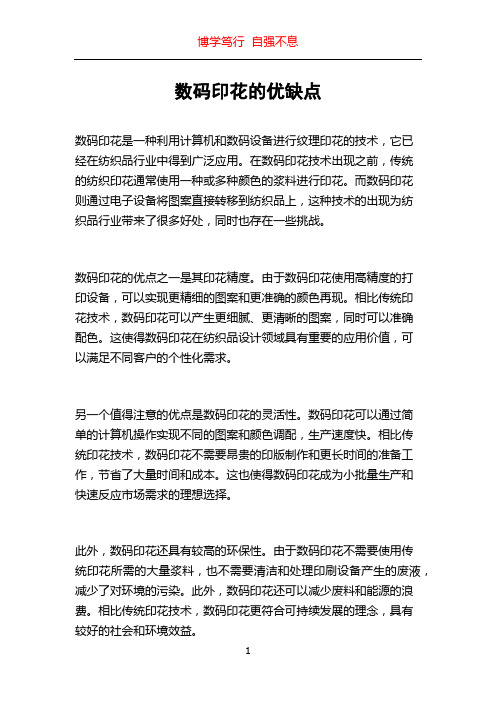
数码印花的优缺点数码印花是一种利用计算机和数码设备进行纹理印花的技术,它已经在纺织品行业中得到广泛应用。
在数码印花技术出现之前,传统的纺织印花通常使用一种或多种颜色的浆料进行印花。
而数码印花则通过电子设备将图案直接转移到纺织品上,这种技术的出现为纺织品行业带来了很多好处,同时也存在一些挑战。
数码印花的优点之一是其印花精度。
由于数码印花使用高精度的打印设备,可以实现更精细的图案和更准确的颜色再现。
相比传统印花技术,数码印花可以产生更细腻、更清晰的图案,同时可以准确配色。
这使得数码印花在纺织品设计领域具有重要的应用价值,可以满足不同客户的个性化需求。
另一个值得注意的优点是数码印花的灵活性。
数码印花可以通过简单的计算机操作实现不同的图案和颜色调配,生产速度快。
相比传统印花技术,数码印花不需要昂贵的印版制作和更长时间的准备工作,节省了大量时间和成本。
这也使得数码印花成为小批量生产和快速反应市场需求的理想选择。
此外,数码印花还具有较高的环保性。
由于数码印花不需要使用传统印花所需的大量浆料,也不需要清洁和处理印刷设备产生的废液,减少了对环境的污染。
此外,数码印花还可以减少废料和能源的浪费。
相比传统印花技术,数码印花更符合可持续发展的理念,具有较好的社会和环境效益。
然而,数码印花也存在一些缺点。
首先是设备投资成本较高。
数码印花所需的高精度打印设备、计算机和相关软件需要较大的投资,尤其对于小型纺织厂来说是一笔较大的负担。
此外,数码印花耗材成本也较高,如打印墨水的价格较传统浆料贵。
因此,数码印花需要投资者权衡其成本效益来衡量其可行性。
其次,数码印花的生产速度相对较慢。
虽然数码印花在小批量生产和个性化定制方面具有优势,但相比传统印花生产线,其生产速度较慢。
这对于需要大量批量生产的纺织品厂商来说可能是一个问题。
因此,数码印花的应用范围在一定程度上受到限制。
最后,数码印花的耐久性也是一个需要注意的问题。
虽然数码印花在图案和颜色再现方面有着显著的优势,但与传统印花相比,其耐洗耐磨性能较差。
数码印花机的工作原理

数码印花机的工作原理
数码印花机是一种通过数码技术将图案或文字直接印在纺织品上的设备。
它的工作原理主要包括以下几个步骤:
1. 图像处理:首先,将设计好的图案或文字输入到电脑软件中,并进行图像处理。
可以通过调整颜色、大小、旋转等参数来得到满意的效果。
2. 喷墨打印:接下来,将处理好的图像传输到数码印花机上。
数码印花机采用了喷墨打印技术,利用喷头将油墨喷射到纺织品上。
喷头通过电脑控制,根据图像的要求在纺织品上进行精确的喷印。
3. 固化处理:印花完成后,需要对纺织品上的油墨进行固化处理,以确保印花图案的持久性。
通常使用热风或紫外线固化设备。
热风固化需要利用高温烘干,使油墨在纺织品上迅速干燥和固化;紫外线固化则是利用紫外线灯照射,使油墨中的化学物质快速反应,实现固化效果。
4. 后处理:固化后,还需要进行后处理工序,如洗涤、烫平等。
洗涤是为了去除固化后的油墨表面残留物,保持印花的清晰度和亮丽度;烫平则是将纺织品展平,使其表面光滑整齐。
总之,数码印花机借助于数码技术和喷墨打印技术,能够在纺织品上快速实现高质量的印花效果。
它的工作原理包括图像处理、喷墨打印、固化处理和后处理等环节,为纺织品印花提供了高效、精确和耐久的解决方案。
数码印花流程
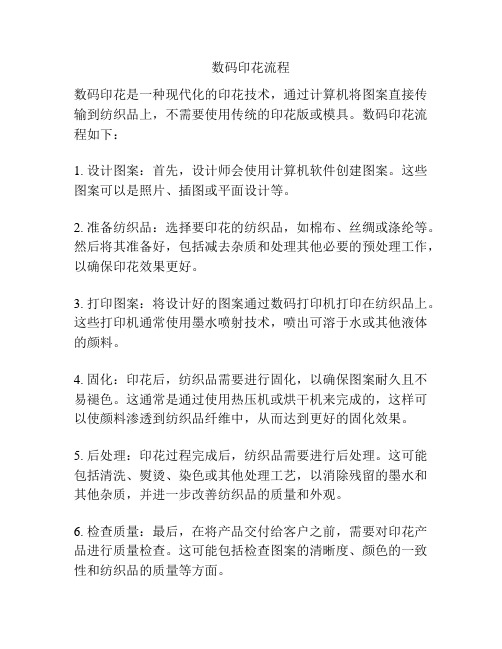
数码印花流程
数码印花是一种现代化的印花技术,通过计算机将图案直接传输到纺织品上,不需要使用传统的印花版或模具。
数码印花流程如下:
1. 设计图案:首先,设计师会使用计算机软件创建图案。
这些图案可以是照片、插图或平面设计等。
2. 准备纺织品:选择要印花的纺织品,如棉布、丝绸或涤纶等。
然后将其准备好,包括减去杂质和处理其他必要的预处理工作,以确保印花效果更好。
3. 打印图案:将设计好的图案通过数码打印机打印在纺织品上。
这些打印机通常使用墨水喷射技术,喷出可溶于水或其他液体的颜料。
4. 固化:印花后,纺织品需要进行固化,以确保图案耐久且不易褪色。
这通常是通过使用热压机或烘干机来完成的,这样可以使颜料渗透到纺织品纤维中,从而达到更好的固化效果。
5. 后处理:印花过程完成后,纺织品需要进行后处理。
这可能包括清洗、熨烫、染色或其他处理工艺,以消除残留的墨水和其他杂质,并进一步改善纺织品的质量和外观。
6. 检查质量:最后,在将产品交付给客户之前,需要对印花产品进行质量检查。
这可能包括检查图案的清晰度、颜色的一致性和纺织品的质量等方面。
总体而言,数码印花流程简化了印花过程,减少了制作模具和印刷版的时间和成本。
它还可以实现更高的图案细节和色彩鲜艳,为纺织品行业带来更多创意和机会。
然而,数码印花仍然需要专业的设备和技术人员来进行操作和维护,以确保印花质量和效率的提高。
- 1、下载文档前请自行甄别文档内容的完整性,平台不提供额外的编辑、内容补充、找答案等附加服务。
- 2、"仅部分预览"的文档,不可在线预览部分如存在完整性等问题,可反馈申请退款(可完整预览的文档不适用该条件!)。
- 3、如文档侵犯您的权益,请联系客服反馈,我们会尽快为您处理(人工客服工作时间:9:00-18:30)。
INK JET PRINTING ON TEXTILESDr John ProvostAbstractWith the increased pressure from developing textile markets in the Far East the textile printer in Europe, Japan and the USA must respond with both increased quality and shorter time of response.This means supplying new design concepts, sample and production printed fabrics in a wide range of colour ways in a time frame unheard of a few years ago.One area that has seen development is in the pre-printing area with increasing use of CAD/CAM systems and digital printing systems ,with ink jet printing systems being targeted .Since the 1991 ITMA digital textile printing systems have been available that can be used for proofing and small sample production . A considerable number of major research projects ( in Europe , Japan and the USA ) aimed at taking digital textile printing to the full production scale are underway .The present paper will review the latest development in the digital ink jet printing of textiles and highlight the future direction this technology will take in textile printing.IntroductionThe textile printing business is a large and complex business with production of prints required on all textile substrates from cotton to the wide range of synthetic fibres. Each of these fibres has to be printed with a dyestuff class to enable fixation (by various chemical or physical methods) to the textile to impart the 'wash and wear' characteristics demanded by the consumer.Total production of textile prints approaches 19 linear billion metres of fabric per year and shows an average growth rate of the order of ~2% per year.However, hidden behind these small growth figures are a relative decline in the developed Western textile printing markets and a much larger growth in the developing markets in the Far East.For the Developed print markets to survive into the 21st century a strategy has to be developed based on (i) speed of response, (ii) short lot production, (iii) short delivery times, (iv) increased innovation and new fashion ideas, and (v) the formation of 'partnerships' with the major retail groups (the printers' customer).To achieve this strategy the printer must take an integrated approach to the whole textile printing process ( design /proofing and production ) (1).The printer has to examine:* the pre-printing stage (CAD/CAM)* the quicker production of sample prints (using digital printing technologies whether direct ( ink Jet ) or indirect ( transfer technologies )* selection of a compatible dye range to ensure minimum transfer from sample to bulk production and consequent less down time when designs are proofed /sampled on digital systems before being printed on analogue systems .The first two steps, the use of CAD systems and the quick production of sample prints are the'key' starting elements of this strategy. It is in this area that we have seen rapid developments in the use of ink jet printing techniques using the digital output from CAD systems.The major reason for the concentration of research programmes on ink jet printing is the realisation that dyes used in digital technologies could be modified and adapted from the same dyes used in current conventional screen textile printing. It should therefore be possible to develop new systems, initially for 'proofing /sample' printing ,that would eliminate the need for preparing full separations and engraving. The technology is advancing at a rapid rate with machines available up to the 100 square metre /hour level with further advances expected at the 1999 ITMA in Paris and over the subsequent next 5 years .Full scale production machines which will replace conventional analogue systems are still many years away .The development of full size ink jet print systems is the target of a number of ambitious plans with projects both in Europe ,USA and Japan.Pre Print Stage in Textile PrintingIf we examine the production time scale of a textile print from design conception to bulk print we can see the considerable advantages to be gained from design selection and sampling using ink jet print technology. To obtain a "feel" for the production time scale of a textile print let us examine the situation for a totally manual approach to the production of a textile print. Figure 1 gives an overview of the stages carried out in the production of a textile print.CONVENTIONAL TEXTILE PRINTING PRODUCTIONSAMPLE PRODUCTION: TIME SCALE 2-8 WEEKSBULK PRODUCTION: TIME SCALE 3-12 WEEKSFigure 1 Textile Printing by Conventional Manual MethodsIn conventional textile printing ,an original design was manually traced, films produced and individual screens or rollers engraved for each colour (i.e. if a textile design has 24 colours then 24 screens have to be produced unlike the CMYK process colour system used in the graphic arts industry). A 'proof' (or sample ) print was produced in a number of colour ways on the textile substrate supplied by the customer prior to submitting to the customer for approval..The time scales indicated in Figure 1 are still typical of those currently achievable by the textile printer who has not adopted digital technologies . However over the last few years there has been considerable investment by the printer and the majority of textile printers now have CAD systems.With the right investment the printer can scan designs into a CAD system where he can reduce the number of colours, manipulate designs, put into repeat, colour and produce separations. The digital information produced can then subsequently be used to produce screens directly, via the latest laser engraving technology, or by conventional means using computer produced films. However, the 'rate determining step' and major bottleneck is the production of the many colour ways at the sample print stage. Digital printing technologies can reduce these bottlenecks considerably. These new technologies can reduce the time taken for colour way/sample selection and have greatly increased the efficiency of the printer in bringing design concepts to the market place.This has consequently led to much more increased research activity in the field of textile ink jet printing . Integration of an ink jet printing system into the already available digital technologies( CAD, Laser Engraving etc ) would give the possibility of shortening the time to market dramatically .A future scenario is shown in Figure 2 ,where the acceptance of the sample by the customer is made on the basis of an ink jet print . This is not a full reality at present , however with possible developments it could well become a possibility.TEXTILE SAMPLE (PROOFING) BY INK JETSAMPLE ACCEPTANCE BULK PRODUCTION 1-3 DAYS 2 WEEKSFigure 2 Possible Future Scenario for Sample to Bulk ProductionThe first systems were developed as long ago as the 1970’s ( the ICI /CCL continuous ink jet developments) (2) . Although there were a number of ambitious programmes over the subsequent years, it was not until the early 1990’s that programmes in Europe and Japan produced commercially available systems .Although the current paper is concerned with ink jet printing for textiles with consequent requirement for fine jet technology there were major developments in the carpet industry during those early years of digital printing .Two commercial systems were developed , the Millitron system (3) which uses an array of jets with continuous streams of dye liquor which can be deflected by a controlled air jet and the 'ChromoJet' system ( from the Zimmer Comapany of Austria (4).Both these systems offer only coarse resolution which has not proved acceptable to the textile printer. However , they did indicate the many benefits of adopting ink jet printing technologies .For sample and proofing purposes Stork of Holland introduced the 'Trucolor' TCP system at the 1991 ITMA exhibition in Hanover (5).The Stork system is system is based on the Hertz binary continuous jet system (6). A full description of the principles can be found in the paper by Hertz and Samuelson (7).Over the last 25 years there have been many projects in the textile ink jet field . These projects have used in many cases differing print head technologies . It is significant in the textile printing field that no one single print head technology has become established . The complete range of print head technologies are currently being researched by the many published projects .An excellent review of textile ink printing has been published by Dawson (2).Textile projects in jet printing have been considerable over the last 25 years , some of the major projects are listed below .•Continuous Multi-Level Deflected Technology• C.S.I.R.O (Australia )• TOXOT (Image)Zimmer ( Jemtex Print heads )• Continuous Binary Systems• Burlington Project (10)• Amethyst (STORK) (5)• Thermal Ink Jet Technology ("Drop on Demand" System)• Canon "Wonderprint" Systems (11) (12) (13)• Encad (USA )• Shima Seiki ( Japan )• ColorSpan (USA)• Piezo Drop on Demand Technology• Seiren “ViscoTex “ System• Mimaki SJ1300/JV Series TX 1600/TX2 Series• Konica Nassenger KS System• DPS 65 ( Magic Print Heads from Aprion )• Dupont( Vutek ) Spectra Print Heads• Leggett and Platt ( Spectra Print Heads )There is on going trend in the last 2 years at adapting wide format graphic printers to textile printing systems and producing individual printed articles for sale to the retailer / consumer .The majority of these systems are developing ink formulations based on dye systems rather than pigments with the aim of obtaining fixation and consequently wider shade gamut , improved “handle” and excellent colour fastness properties. The development of reliable ink systems for textiles is only a recent introduction . Also the challenges of obtaining reliable print systems for Disperse dye inks ( both for transfer and direct printing ) is only just being realised .As cellulose printing (cotton, viscose rayon) and blends with cellulose accounts for nearly 70% of all textile printing consequently considerable research has been aimed at developing stable ink formulations based on reactive dyes. A further reason for developing ink formulations based on reactive dyes is the inherent higher price of the finished print with consequent higher margins for the printer.Reactive Dyes in Textile Ink JetReactive dyes were first introduced in 1956 (13) These dyes have suitable groups capable of forming a covalent link between the dye and the hydroxyl in the cellulose . In textile printing two essential types have developed; (i) monohalogenotriazine types which react by a nucleophilic substitution mechanism , and (ii) groups which react by the addition of the nucleophilic group of the substrate to a C=C double bond on the reactive group (the most common of this class are sulphuric acid esters of ß-hydroxyethylsulphones which form vinyl sulphone groups under alkaline conditions).Due to the differing reactivities of the two types and the need for long term stability in conventional printing the first type - the monohalogenetriazine types are the most popular in textile printing, accounting for approximately 85% of conventional textile printing on cellulosic fabrics.The reactive scheme for a typical monochloro-s-triazinyl dye is shown in Figure 3. The reaction takes place under alkaline conditions and heat (normally steam fixation at 102°C for 10 minutes) together with other additives such as urea.REACTION SCHEME FOR REACTIVE DYE(MONOCHLORO-S-TRIAZINE) WITH CELLULOSEFigure 3 Reactive Scheme for Reactive Dye Monochloro-s-triazinyl type) with CelluloseThere are many factors which must be taken into effect when developing dyes , dye formulations and the ink systems for the wide range of head technologies being researched today .Figure 4 highlights some of the factors which must be taken into consideration when designing ink systems for specific print head and substrate combinations . The development of specific ink systems is very complex undertaking and is very much a comprise situation , balancing the properties of the ink vehicle with performance criteria set by the print head technology and at the same time taking in the requirements of the media/substrate (17 ).In conventional textile printing the reactive dye is applied to the textile with alkali and all the necessary additional chemicals in the form of a print paste. The print is then normally steamed to fix the dye to the hydroxyl groups within the cellulose and subsequently washed to remove any unreacted colour, chemicals and the thickener. A much more complex process than conventional ink jet printing on paper. This requirement for extra chemicals to fix the reactive dye, the reactivity of the dye itself under alkaline conditions and the relative small amount of ink formulation applied has led to the modification of conventional print technology and the introduction of chemical pre-treatments (2) (5).Textile Substrate Pre Treatment TechnologyWith ink jet textile print systems that use dyes, the chemicals required for fixation of the dyes have to be applied by a padding or coating application prior to ink jet printing. However, even with the application of the conventional print chemicals colour yield is still not comparable to that achieved by conventional printing processes. This in the main is due to the very much smaller amount of ink formulation applied by the print head .It must also be noted that different print head technologies apply also differing amounts of ink ( ink jet volumes are measured using “picolitre “units ). This is in contrast to conventional printing where the amount of print formulation applied can be up to 200 gm/sq. metre or more (dependent on the actual weight/sq. metre of the textile) with ink jet the amount of ink formulation applied can be as small as20mls/square metre .Actual amounts applied by the various print technologies differ depending on the actual print head principle ,nozzle size( drop volume ), frequency rate ( which determines the number of drops /second ). Also with ink jet printing on textiles the amount of ink applied is constant for a specific head technology. With these considerable extra constraints an integral part of any successful ink jet textile system is the pre-treatment technology .For an textile ink jet application to be successful ,the dye chemists(or textile chemists) and the media must work in a close relationship with the systems integrator ( and the print head developer).These pre treatment chemical and process methods must be developed for specific dye types and substrate combinations.Application Areas of Current Ink Jet PrintersThe major application areas of jet printing have been in the pre-printing (proofing and sample print areas) , small run ”on demand” printing ( sometimes referred to as “Agile Manufacturing “Model ) .Ink Jet Printing has also been used to produce colour catalogues and the easier communication of colour information (16 ).Other uses of textile ink jet include,• At the colouring and design stage. Samples on fabric can be obtained quickly in a choice of colour ways without having to make films, screens or print paste so customers can make the "Go/NoGo" decision for a particular design in a particular colour combination. Correlation of the print produced for the sample print by ink jet must subsequently be reproduced in the production using screen technology .Methods have been developed to achieve this “Match to Print “ (MTP ) capability (16 ) .• Ink Jet printers can be used as a method of producing small-scale production prints of exclusive designs (for example for ties, scarves and pocket handkerchiefs) within a very short time compared to any procedure involving an engraving stage.This “on demand “ printing to the 100metre length produced by ink jet will become of increasing importantThe introduction of the Canon “WonderPrint “ bubble jet printing system , which was announced at the Vienna 17th IFVTCC Congress in June 1996 , which is capable of printing 100square metres /hour will lead to further developments for ink jet print machines in this production scale area .Similarly one-off sample prints for use in garments for selection purposes by a retailer, photographing for mail-order catalogues or publicity material in advance of bulk production can be produced.Since the introduction of this approach customers can submit a new design (or could submit digital information produced from his own CAD system) to the textile printer. The textile printer could then scan the design into a CAD system, subsequently working through the necessary cleaning-up, repeat setting, separation and colouring stages that many of the new systems are capable of carrying out. The 'key' element of the procedure is that the textile printer can use the CAD generate digital information to drive the jet printer and produce a sample print. The subsequent jet printed sample follows the normal post printing operations of steaming and washing-off. This enables the production of realistic small samples in a short time without the requirement of engraving screens or producing conventional sample prints.Only when firm decisions have been made would screens be engraved and a conventional sample printed for final approval prior to bulk production.In addition production of colour atlases that can be ink jet printed onto cloth opens up new possibilities in the specification and communication of colours. Easy translation of ink jet sample prints into bulk production recipes could also be made easier by the use of colour atlases. These recipes can be transmitted electronically to automatic dispensing colour systems for production of colours for production printing. This then gives the capability of 'integrating' the total textile print production process.The potential of integrating sample and production using digital systems and ink jet print technology has been recently described (16).Recent DevelopmentsAs discussed in the introduction ,conventional textile printing uses a separate screen for each of the colours required. The conventional textile printer has therefore the complete range of colours to choose from when producing a design. For example, if a customer requires a bright orange colour he can choose a bright orange dye to satisfy the customer.With ink jet printing technology ('continuous' and 'drop-on-demand' ink jet print heads ) colours are normally produced using 4 colours only (Cyan, Magenta, Yellow and Black), therefore to produce a bright orange the yellow and magenta are used. Therefore, using the CMYK process colour approach it was soon realised that only 70 percent of the colour gamut of the total available gamut to the textile printer could be achieved .Canon also with their “WonderPrint “ bubble jet printer have added extra colours , besides the CMYK set , they have added two extra colours ( orange and a blue ) , together with two dilute inks .This trend to extra colours ,in addition to the standard CMYK set , to satisfy the textile printer will see increasing developments over the next few years .Machines are now available with both 6 and 8 colour systemsThe use of spot colours ( pre mixed colours ) ,using the ink jet printer to apply the design only is also an area of interesting debate . It is known that some projects have taken this approach .Also the combination of ink jet digital printing with conventional analogue printing to produce “hybrid” prints is also another concept under investigation.The development of new colorants with increased colour value and solubility will also be an increasing trend as the concentration of colour in an textile ink jet formulation is far higher than conventional paper ink jet . This requirement for extra dye in an ink formulation for textiles obviously can effect the life time of the print head which can be a significant extra cost .An obvious challenge would be to develop a radical new approach with a coloration system which gives 100 percent fixation with no wash off , giving the possibilities of taking digital printing further down stream to the retailer or even the consumer.The whole area of textile ink jet is under considerable research activity at the moment . Just taking patents related to dyes/applications (not machinery developments) in the textile ink jet area we have seen over 150 in the last 4 years alone ( 92 percent originating from Japan )Finally , the overall cost equation has to be taken into consideration ( including all stages i.e. cost of engraving, sampling, etc ) .Currently the use of textile ink jet is only economic for sample prints or when the production is under 50 metres when detailed comparison are taken with the conventional methods ( including the cost of engraving )With the increased research activity this figure will increase but it will be some years before actual production figures that some analysts predict will be realised in practise .ConclusionsThe availability of textile ink jet systems for the sample and proofing market is now established, which has led to significant benefits to the textile printer. In particular the reduction of lead times, reducing stock levels, responding to fashion changes quickly will make the European, American and Japanese printer more competitive.The next stage in the development will be the availability of short run ink jet machines capable of printing up to the 100 square metre production area. This will lead to the development of a new type of printer closer to the retailer ( the so called “Agile Manufacturing” model) .Full production ink jet printing still has a number of major technical barriers to overcome, not least is the cost equation . However the race is on to develop production systems; currently there is no clear print head technology winner . There are a number of competing head technologies,each probably developing into their own market segments.The key parameter for a production textile ink jet printer is the cost and reliability of the ink head under production conditions and the availability of innovative chemical solutions to colour, ink formulations and pre treatment technologies.The success of any textile Ink jet project is the development of partnerships between machinery makers(print head manufacturers ), specialist chemical manufacturers to bring dye synthesis expertise and pre treatment chemistry ,together with the forward looking textile printer .For those players , head manufacturers, systems integrators , chemical manufacturers and importantly the textile printer (end users), who get the equation right the potential rewards will be significant.References(1) J R Provost, 'Dynamic Response in Textile Printing', Textile Chemist & Colorist, June1995, Vol 27, No. 6, p11.(2) T L Dawson, 'Jet Printing', Rev. Progress in Coloration, 22 (1992) 22.(3) K Dunkerley, 'Developments in Carpet Printing', Rev. Progress in Coloration, 11 (1981) 74.(4) T L Dawson, B Roberts, 'Dyeing and Printing Method for the Coloration of Carpet Yarn andCarpet Piece by Jet Impregnation', JSDC 93 (1977) 439.(5) S O Aston, J R Provost, H Masselink, 'Jet Printing with Reactive Dyes', JSDC 109 (1993)147.(6) C H Hertz, 'Ink Jet Printing', Advances in Electronics and Electron Physics vol 65 (1985)91 (Academic Press)(7) C H Hertz, B A Samuelson, 'Ink Jet Printing of High Quality Images', J Imaging Tech 15(1989) 141.(8) E ureka Project, EU796.(9) B rite-Euram Project, BRE2-CT93-0544.(10) Graham, L, 'Ink Jet Systems for Dyeing and Printing of Textiles, Textile Chemist &Colorist 21 (1989) No. 6, p27.(11) Anon., “Kanebo and Canon Jointly Develop Bubble Jet Printing System”, Japan TextileNews, March 1993, p90.(12) Kanebo/Toshin, U.S. Patent, 5 345 863 (17th September 1994).(13) A Johnson (Ed.), 'The Theory of Coloration of Textiles' (2nd Edition), Society of Dyersand Colourists 1989, p428-486.(14) J R Provost, 'Ink Jet Printing on Textiles', Surface Coating International (JOCCA) 77(1994) 36.(15) Zeneca, European Patent Application 534,660 A1 (14th September 1992).(16) J.R.Provost, R.J.M.Kool, J.V. Lammeren, “Integrated Digital Approach to ColorManagement In Textile Printing “, Textile Chemist and Colorist , 28( 1996 ) No 8 p71-75 (17) very ,J.R. . Provost “Color Media Interactions in Ink Jet Printing “ 13thInternational Conference on Digital Printing Technologies , I. S. and T. 1997 pages 437 -442.TEXTILECOLOUR/INK FORMULATIONSPRINT HEAD TECHNOLOGIESTEXTILE/INK INTERACTIONPROPERTY:PERFORMANCE:Colour value/yieldChroma (colour quality)Rub fastnessDrying timeSpreading/wicking Water fastness Light fastnessSurface tension ViscositySpecific gravity pHConductivity Dye purityDye purity/solubility Toxicological properties Particle size StabilityAccoustic properties Shelf lifeDrop performanceInk/Material compatibility Nozzle clogging Nozzle crusting Biological growth ContaminationLong-term operabilityCOLOR-TEXTILE INTERACTIONS IN INK JET PRINTINGFigure 4 Ink/Print Head/Media Interaction in Ink Jet Printing。