供应链管理优化
如何优化供应链管理

如何优化供应链管理随着全球化进程的加快以及市场竞争的日益激烈,供应链管理已经成为了企业管理中不可或缺的一个重要部分。
通过优化供应链管理,不仅可以提高企业生产和经营效率,还可以降低成本,提高盈利能力。
本文就从以下几个方面来谈谈如何优化供应链管理。
一、提高供应链透明度供应链透明度是指企业在供应链中所有环节实时掌握信息的能力,包括企业内部流程和流程外部环节。
提高供应链透明度是优化供应链管理的核心,因为只有掌握实时信息,企业才能快速响应市场变化、提高生产效率和优化成本。
企业可以通过以下方式来提高供应链透明度:1.建立供应商信誉评估机制建立供应商信誉评估机制,对供应商进行定期评估和监控,加强控制和管理供应商的行为。
评估供应商不仅可以实现供应商管理,还可以减少出现问题的概率。
2.建立供应链物流系统建立供应链物流系统,对产生物流成本和物流风险的点进行分析,实现供应链物流过程可视化管理。
此外,物流系统还可以通过跟踪和管理货物流动信息,使企业能够更好地掌握货物流动状态,提供追踪能力,为物流预警、客户服务和供应商管理提供数据依据。
3.实施供应链RFID电子化管理RFID标签的应用不仅可以帮助企业货物的跟踪和管理,还可以实时监控产品在供应链中的流动情况。
通过对RFID数据的分析,企业可以确定供应链中的瓶颈和问题,并实施改进措施。
二、优化供应链流程流程优化是提高供应链总体效益的重要手段,通过流程优化,可以提高供应链各阶段的效率,降低成本,提高顾客服务质量。
如何实施供应链优化流程?1.明确流程目标和时间节点明确流程的目标和时间节点,根据流程的目标,确定流程的时间和工作量,并制定流程实施计划。
2.识别流程瓶颈并进行改进瓶颈是流程优化的关键和重点,通过识别和解决瓶颈,可以提高流程效率。
比如,可以通过减少某一环节的工作量或调整工作顺序来提高效率,或者引入新的技术和设备来改进流程。
3.实施流程监控在流程实施过程中,需对流程进行监控,及时发现问题并解决问题。
供应链优化措施

供应链优化措施背景供应链是企业运营中至关重要的一环。
优化供应链管理可以提高企业的运营效率、降低成本,并帮助企业更好地满足顾客需求。
本文将介绍一些供应链优化措施。
1. 建立良好的合作关系建立良好的合作关系是优化供应链的基础。
与供应商、承运商和合作伙伴之间建立密切的合作关系,可以改善信息流通、提高反应速度,并降低沟通和协调成本。
2. 数据分析和预测数据分析和预测是供应链优化的重要工具。
通过对供应链数据进行分析和预测,企业可以更好地了解市场需求和供应链效率,并根据预测结果制定相应的优化策略。
3. 库存管理优化库存管理是提高供应链效率的关键。
通过准确预测需求、合理控制库存水平和采用先进的库存管理技术,企业可以降低库存成本、减少仓储空间占用,并提高交付速度和顾客满意度。
4. 使用技术和工具利用技术和工具可以帮助企业更好地管理供应链。
例如,使用物联网技术可以实时监控和追踪货物的位置和状态,提高物流效率;使用供应链管理软件可以简化供应链流程、提高数据准确性和实时性。
5. 进行供应链协同供应链协同是优化供应链的关键要素。
通过与供应链各环节的合作,优化协调和流程,可以减少因信息不对称和合作不畅而引起的问题,并提高整体供应链效率和灵活性。
6. 持续改进供应链优化是一个持续改进的过程。
企业应不断评估供应链的性能,并根据评估结果采取相应的措施进行改进。
同时,企业应积极关注市场和技术的变化,及时调整供应链策略,以适应新的需求和挑战。
结论通过实施上述供应链优化措施,企业可以提高供应链效率、降低成本,并更好地满足顾客需求。
然而,每个企业的供应链情况各不相同,因此,在实施优化措施时应结合实际情况进行评估和调整。
如何优化供应链管理?
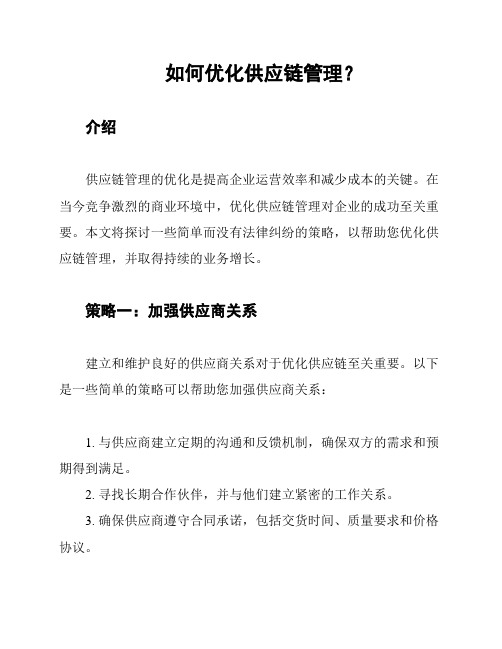
如何优化供应链管理?介绍供应链管理的优化是提高企业运营效率和减少成本的关键。
在当今竞争激烈的商业环境中,优化供应链管理对企业的成功至关重要。
本文将探讨一些简单而没有法律纠纷的策略,以帮助您优化供应链管理,并取得持续的业务增长。
策略一:加强供应商关系建立和维护良好的供应商关系对于优化供应链至关重要。
以下是一些简单的策略可以帮助您加强供应商关系:1. 与供应商建立定期的沟通和反馈机制,确保双方的需求和预期得到满足。
2. 寻找长期合作伙伴,并与他们建立紧密的工作关系。
3. 确保供应商遵守合同承诺,包括交货时间、质量要求和价格协议。
策略二:提高库存管理优化库存管理可以帮助您降低库存成本并减少过剩库存的风险。
以下是一些建议:1. 使用先进的库存管理系统,提高库存可见性和准确性。
2. 分析需求模式和销售趋势,以合理预测和规划库存水平。
3. 与供应商共享销售和库存数据,实现更有效的库存管理。
策略三:优化运输和物流有效的运输和物流管理可以减少运输成本和时间,并提高交付的可靠性。
以下是一些建议:1. 寻求合适的运输合作伙伴,以确保交付准时并降低运输成本。
2. 运用技术和实时数据分析,优化运输路线和交付计划。
3. 实施可持续运输和物流策略,减少对环境的负面影响。
策略四:采用信息技术解决方案信息技术的应用可以极大地改进供应链管理的效率和可靠性。
以下是一些建议:1. 使用供应链管理软件,以提高可见性和协作能力。
2. 实施自动化和智能化的流程,以减少人工错误和提高效率。
3. 整合供应链各个环节的数据,进行分析并做出预测,以支持决策制定。
结论优化供应链管理不仅可以提高企业的竞争力,还可以降低成本并改善客户满意度。
通过加强供应商关系,提高库存管理,优化运输和物流,以及采用信息技术解决方案,您可以实现持续的供应链管理优化,并为企业的成功打下坚实的基础。
以上是优化供应链管理的一些简单策略,可根据您的实际情况进行调整和应用。
祝您在优化供应链管理的道路上取得成功!。
优化供应链管理的五大策略

优化供应链管理的五大策略随着全球化的发展和市场竞争的加剧,企业对供应链管理的重视程度日益增加。
优化供应链管理可以帮助企业降低成本、提高效率、增强竞争力。
在当今复杂多变的市场环境下,如何有效地优化供应链管理成为企业亟需解决的问题。
本文将介绍优化供应链管理的五大策略,帮助企业更好地应对挑战,实现持续发展。
一、建立战略合作关系建立战略合作关系是优化供应链管理的重要策略之一。
企业应该与供应商、合作伙伴建立长期稳定的合作关系,共同制定发展战略,分享信息和资源,共同应对市场变化。
通过建立战略合作关系,企业可以实现供应链的协同管理,提高供应链的灵活性和响应速度,降低库存水平,减少物流成本,提高客户满意度。
二、采用信息技术支持信息技术在优化供应链管理中发挥着重要作用。
企业可以借助信息技术实现供应链的可视化管理,及时获取市场信息和需求信息,优化生产计划和库存管理,提高供应链的透明度和效率。
同时,信息技术还可以帮助企业建立供应链协同平台,实现供应链各环节的信息共享和协同决策,提高供应链的整体运作效率。
三、优化供应链网络设计优化供应链网络设计是提高供应链管理效率的关键。
企业应该根据产品特性、市场需求和供应商地理位置等因素,合理设计供应链网络结构,优化供应链各环节的布局和连接方式。
通过优化供应链网络设计,企业可以降低运输成本、缩短交货周期、提高产品质量和服务水平,实现供应链管理的整体优化。
四、实施供应链风险管理供应链管理面临着各种内外部风险,如自然灾害、政治动荡、市场波动等,这些风险可能对供应链的正常运作造成影响。
因此,企业需要实施供应链风险管理,建立健全的风险评估和预警机制,及时应对各类风险事件,保障供应链的稳定运行。
同时,企业还可以通过多元化供应商、备份库存等方式降低风险,提高供应链的抗风险能力。
五、持续优化供应链绩效持续优化供应链绩效是优化供应链管理的长期任务。
企业应该建立科学的绩效评估体系,定期对供应链各环节进行评估和改进,发现问题、解决问题,不断提升供应链管理水平。
供应链管理实施方案的优化和改进措施
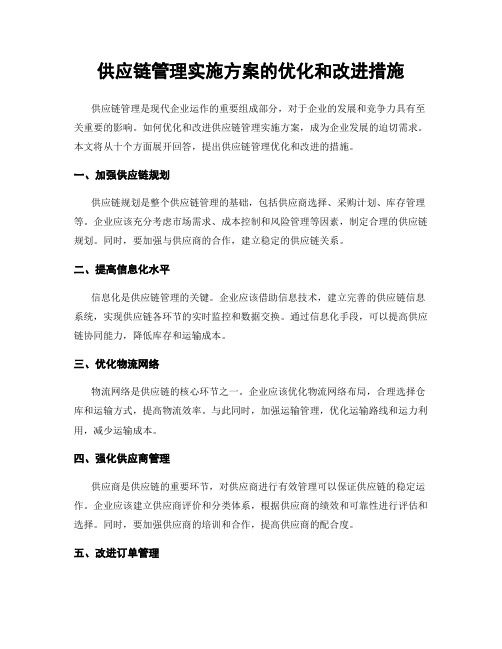
供应链管理实施方案的优化和改进措施供应链管理是现代企业运作的重要组成部分,对于企业的发展和竞争力具有至关重要的影响。
如何优化和改进供应链管理实施方案,成为企业发展的迫切需求。
本文将从十个方面展开回答,提出供应链管理优化和改进的措施。
一、加强供应链规划供应链规划是整个供应链管理的基础,包括供应商选择、采购计划、库存管理等。
企业应该充分考虑市场需求、成本控制和风险管理等因素,制定合理的供应链规划。
同时,要加强与供应商的合作,建立稳定的供应链关系。
二、提高信息化水平信息化是供应链管理的关键。
企业应该借助信息技术,建立完善的供应链信息系统,实现供应链各环节的实时监控和数据交换。
通过信息化手段,可以提高供应链协同能力,降低库存和运输成本。
三、优化物流网络物流网络是供应链的核心环节之一。
企业应该优化物流网络布局,合理选择仓库和运输方式,提高物流效率。
与此同时,加强运输管理,优化运输路线和运力利用,减少运输成本。
四、强化供应商管理供应商是供应链的重要环节,对供应商进行有效管理可以保证供应链的稳定运作。
企业应该建立供应商评价和分类体系,根据供应商的绩效和可靠性进行评估和选择。
同时,要加强供应商的培训和合作,提高供应商的配合度。
五、改进订单管理订单管理是供应链管理中的重要环节,对于准确满足客户需求和改进交付能力至关重要。
企业应该优化订单管理流程,提高订单处理效率,减少订单错误率。
并且,要和客户保持良好的沟通,加强对订单的跟踪和控制。
六、强化库存管理库存管理是供应链管理中的重要环节之一。
企业应该建立科学的库存管理模型,通过合理的预测和计划,控制库存水平,减少库存积压和滞销。
同时,要加强对库存的监控和定期盘点,确保库存的准确性。
七、加强质量管理质量是供应链管理的核心价值之一。
企业应该建立完善的质量管理体系,严格控制供应链各环节的品质要求。
要对供应商进行质量审核和考核,确保原材料和产品的质量达到标准。
同时,要建立快速反应机制,及时解决质量问题。
优化供应链管理的建议

优化供应链管理的建议随着全球化程度的提高和市场竞争的加剧,供应链管理对于企业的重要性不断凸显。
优化供应链管理可以提高企业的运营效率、降低成本、提升客户满意度等方面带来积极的影响。
以下是我对优化供应链管理的建议:1.加强供应链协调能力供应链管理涉及到多个环节和部门之间的协调合作,因此,加强供应链的协调能力是提高整体效率的关键。
通过建立供应商、制造商和销售商之间的紧密合作关系,提高信息流畅度和物流效率,能够减少库存堆积、降低成本,并且能够更快地响应市场需求,提供更好的客户服务。
2.优化采购管理采购管理是供应链管理的核心环节之一,它直接影响到生产能力和产品质量。
为了优化采购管理,企业可以采取以下措施:(1)建立供应商评估制度,评估供应商的质量、可靠性、交货期等指标,并与优秀供应商建立长期稳定的合作关系。
(2)建立合理的采购计划,根据市场需求和库存情况做出准确的采购决策,避免过多或过少的材料采购,减少库存的浪费和滞销风险。
(3)引入信息化技术,优化采购流程,实现采购订单的自动化处理和供应商信息的实时更新,提高采购效率和准确性。
3.强化物流管理物流管理是供应链管理的重要组成部分,通过优化物流管理可以实现准时交货、降低库存成本和缩短供应链周期。
以下是一些建议:(1)建立独立的物流管理团队,负责物流规划、运输安排和货物跟踪等工作。
(2)与物流合作伙伴密切合作,共同制定物流方案,优化运输路线,减少运输成本和时间。
(3)引入物流信息系统,实现物流信息的实时监控和追踪,提高货物的可视性和物流效率。
4.优化库存管理库存管理直接关系到企业的资金周转和成本控制。
有效的库存管理可以降低库存成本、减少库存风险、提高供应链的反应速度。
以下是几点优化库存管理的建议:(1)建立合理的库存管理模型,确定最优的库存水平和订货批量。
(2)通过预测市场需求,优化库存规划,减少过剩和缺货情况的发生。
(3)优化供应链中的库存点布局,减少运输距离和运输时间,降低库存持有成本。
优化供应链管理的建议

优化供应链管理的建议随着全球市场的不断扩大和竞争的加剧,优化供应链管理成为企业发展的关键。
一个高效的供应链管理能够帮助企业降低成本、提高效率,同时也能够增加客户满意度和市场竞争力。
以下是我对如何优化供应链管理的建议。
1. 加强供应商合作供应链管理的关键在于与供应商之间的紧密合作。
为了提高供应链的效率和灵活性,企业应与供应商建立稳定的合作关系,并且互相分享信息和资源。
同时,建立供应商评估体系,定期对供应商进行评估,并与之保持良好的沟通和协调,以确保供应链的稳定性和可靠性。
2. 引入信息技术支持信息技术在供应链管理中起到了至关重要的作用。
企业应该优先考虑引进适当的供应链管理软件,以实现对供应链的全面管理和控制。
通过信息技术的支持,企业能够实时监控供应链的各个环节,并快速做出相应的调整和决策,提高供应链的反应速度和灵活性。
3. 实施供应链可视化供应链可视化是指通过数据分析和可视化工具,将供应链的各个环节和关键指标直观地展示出来,以便管理层和相关人员能够更好地了解供应链的运作情况,并及时发现和解决问题。
通过实施供应链可视化,企业能够更好地进行供应链规划、资源配置和决策制定,从而提高供应链的效率和管理水平。
4. 加强库存管理库存管理是供应链管理中非常重要的一环。
企业应该根据市场需求和供应能力,科学合理地制定库存策略,并实施有效的库存管理措施。
通过准确的需求预测和库存优化,企业能够降低库存成本、减少滞销和过剩库存,并提高供应链的灵活性和响应速度。
5. 建立跨部门协作机制供应链管理需要各个部门之间的密切协作和合作。
企业应该建立横向沟通的机制,促进不同部门之间的信息共享和协同工作。
同时,建立跨部门的绩效考核和激励机制,以激发员工的积极性和创造力,促进供应链管理的协调和提升。
总结:优化供应链管理是企业发展的重要任务。
通过加强与供应商的合作、引入信息技术支持、实施供应链可视化、加强库存管理和建立跨部门协作机制,企业能够提高供应链的效率和灵活性,降低成本,提高客户满意度,增强市场竞争力。
优化供应链管理措施
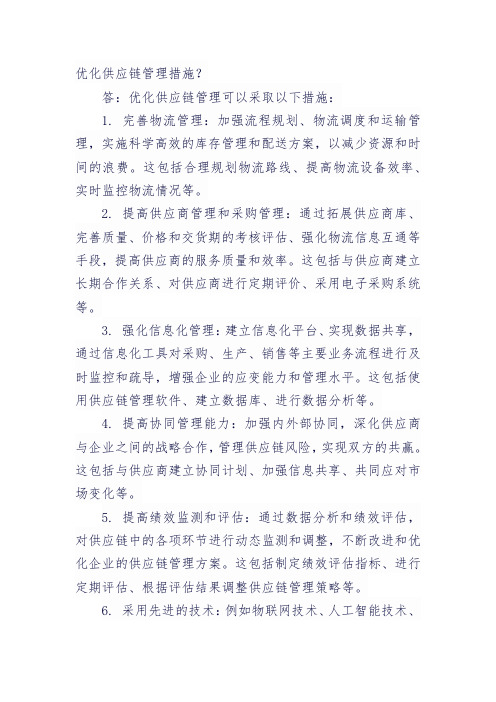
优化供应链管理措施?答:优化供应链管理可以采取以下措施:1. 完善物流管理:加强流程规划、物流调度和运输管理,实施科学高效的库存管理和配送方案,以减少资源和时间的浪费。
这包括合理规划物流路线、提高物流设备效率、实时监控物流情况等。
2. 提高供应商管理和采购管理:通过拓展供应商库、完善质量、价格和交货期的考核评估、强化物流信息互通等手段,提高供应商的服务质量和效率。
这包括与供应商建立长期合作关系、对供应商进行定期评价、采用电子采购系统等。
3. 强化信息化管理:建立信息化平台、实现数据共享,通过信息化工具对采购、生产、销售等主要业务流程进行及时监控和疏导,增强企业的应变能力和管理水平。
这包括使用供应链管理软件、建立数据库、进行数据分析等。
4. 提高协同管理能力:加强内外部协同,深化供应商与企业之间的战略合作,管理供应链风险,实现双方的共赢。
这包括与供应商建立协同计划、加强信息共享、共同应对市场变化等。
5. 提高绩效监测和评估:通过数据分析和绩效评估,对供应链中的各项环节进行动态监测和调整,不断改进和优化企业的供应链管理方案。
这包括制定绩效评估指标、进行定期评估、根据评估结果调整供应链管理策略等。
6. 采用先进的技术:例如物联网技术、人工智能技术、区块链技术等,可以提高供应链的自动化和智能化水平,减少人为错误和延误,提高供应链管理的效率和准确性。
7. 建立应急计划:为应对供应链中可能出现的突发事件,如自然灾害、供应商破产等,企业应建立应急计划,以确保供应链的稳定性和连续性。
8. 关注可持续发展:在选择供应商和产品时,企业应考虑环境和社会影响,确保供应链的可持续性。
这包括选择环保的供应商、使用可再生资源等。
9. 加强员工培训:定期对员工进行供应链管理相关的培训,提高他们的专业知识和技能水平,使他们能够更好地执行供应链管理策略。
10. 建立良好的企业文化:通过建立良好的企业文化,可以促进企业内部的沟通和协作,提高员工的归属感和责任感,从而提高供应链管理的效果。
- 1、下载文档前请自行甄别文档内容的完整性,平台不提供额外的编辑、内容补充、找答案等附加服务。
- 2、"仅部分预览"的文档,不可在线预览部分如存在完整性等问题,可反馈申请退款(可完整预览的文档不适用该条件!)。
- 3、如文档侵犯您的权益,请联系客服反馈,我们会尽快为您处理(人工客服工作时间:9:00-18:30)。
工序调度
1 2 3 4 5 6 7
指定要调度的工序 指定调度日期
工序(序列))排序
设置最佳化时间 有限排产 核查工序日期 中间点法排产
1.
供应链优化事项 优化产品开发与设计
加强机会管理和订单管理 多工厂计划模式 设定计划缓冲时间 运用能力计划进行生产排程 合理确定物料分类和采购策略 运用长期模拟计划确定长周期采购计划
2.
3.
4.
5.
6.
7.
8.
合理确定集中采购模式
合理设定安全库存 供应商评估 计划交货周期 计划时界
9.
10.
11.
12.
订单分布趋势
订单交货日期分布图 有效意向数量 管理有效数量 确定订单数量 管理订单数量
订单总量、确定订单、 意向订单都随时间推 移而减少;但近期 订单数量随 (10月)订单总量超 时间而减少 过产能和实际销售, 远期(11月)则不足
12.
生产排程
工序1生产准备时间 A B 料 A 0 10 B 30 0 C 30 25 C 20 15 0
排程的优化是降低生产成本提高产能利用的主要手 段
需求时间
A
C
切换时间
B B
切换时间
C
A 满足交货期, 生产周期长
A
切换时间
C
切换时间
A
A
切换时间
B
计划优化, 但有拖欠
A
A
切换时间
B
切换时间
C
供应链管理
[ 应用优化事项 ]
1.
供应链优化事项 优化产品开发与设计
加强机会管理和订单管理 多工厂计划模式 设定计划缓冲时间 运用能力计划进行生产排程 合理确定物料分类和采购策略 运用长期模拟计划确定长周期采购计划
2.
3.
4.
5.
6.
7.
8.
合理确定集中采购模式
合理设定安全库存 供应商评估 计划交货周期 计划时界
•所用部件发货工厂为其它工厂 •在部件发货工厂产生相关需求 •部件发货工厂可视为部件生产车间+仓库
多工厂计划模式3-生产工厂和计 划工厂 •在计划工厂进行需求计划和生产订单创建
•在生产工厂展开BOM,产生所用部件相关需求,安排生产 •生产完成后,在计划工厂收货 •生产工厂可视为部件生产车间
1.
供应链优化事项 优化产品开发与设计
订单 结束日期
可用日期
提前期排产
在旺季为备产能:当 如果计划日期落在当 前确定订单+未来确 前日期外,则系统会 定订单+部分畅销车 使用减少策略以减少 型 缓冲时间
生产前缓冲
生产后缓冲
10
20
30
订单开始日期
计划开始日期 计划开始日期
计划结束日期 计划结束日期
订单结束日期
工序(按工艺路线) 工序(按工艺路线)
200 180 160 140 120 100 80 60 40 20 0
淡季为旺季备产能: 在旺季为备产能:当 前确定订单+未来确 当前确定订单+未来 49台6128HG-4 定订单+部分畅销车 确定订单+部分畅销 车型管理订单 型
在旺季为备产能:当 通过销售与运作计划 前确定订单+未来确 来自动平衡意向订单, 定订单+部分畅销车 保证采购计划和生产 型 能力计划
9.
10.
11.
12.
产品开发与设计过程中存在着问题
CAD系统缺乏设计方法学的支持,仅仅被作为绘图工 具 在各种应用系统中重复输入相同数据
缺乏有效的分类系统和完善的编码系统,不能充分利 用已有的零部件资源 缺少可变型的产品模型 缺乏完善的数据管理和过程管理系统
上述问题造成了设计人员始终 处于超负荷被动的状态
系列产品和组合产品的开发 产品编码的系统化
产品技术文件的系统化
工程数据管理系统优化
采用先进的工程数据管理系统(PDM/EDM) 计算机集成工具(CAD/ERP集成工具)
建立智能化的产品模型
1.
供应链优化事项 优化产品开发与设计
加强机会管理和订单管理 多工厂计划模式 设定计划缓冲时间 运用能力计划进行生产排程 合理确定物料分类和采购策略 运用长期模拟计划确定长周期采购计划
00:00
星期一 06:00
星期二
12:00
18:00
00:00Байду номын сангаас
06:00
14200 装配
订单(共享)
订单 工序 数量
00:00
星期一 06:00
星期二
12:00
18:00
00:00
06:00
2010 0010 2020 0020 2030 0010
10 5 10
信息行 表格部分 图示部分
图表
图表
14100 装配
27.1999 7 13.0 185 %
28.1999 10
29.1999 12
需求 总需求 6.5 h 13.0 h 物料 T-F101 T-B102 数量 20 35 UM PC PC 订单 工序 描述 装配 装配
0001891 0010 0001953 0030
计划表:图形形式
工作中心
工作中心
销售机会管理和订单管理
机会管理
机会管理的目的在于:加强对市场需求信息的收集、分析和跟踪,强 调信息的准确和及时,对公司发现的所有机会(一般意向)进行有效 的管理。从整个公司的层面来考虑机会跟踪的可行性和必要性。对确 定跟踪并有一定把握的一般意向转为有效意向订单。
机会管理包括以下两个方面: ·关键客户(Key Account)的机会管理 ·非关键客户(Non-Key Account)的机会管理
%
竞争近况及分析
竞争对手: 竞争对手强项: 竞争对手弱项: 客户关键人物掌握:
已完成销售任务和计划动作
已完成: 客户反馈: 计划完成: 人员和费用投入计划:
1.
供应链优化事项 优化产品开发与设计
加强机会管理和订单管理 多工厂计划模式 设定计划缓冲时间 运用能力计划进行生产排程 合理确定物料分类和采购策略 运用长期模拟计划确定长周期采购计划
2.
3.
4.
5.
6.
7.
8.
合理确定集中采购模式
合理设定安全库存 供应商评估 计划交货周期 计划时界
9.
10.
11.
12.
多工厂计划模式1-工厂间库存 转储 •物料接收工厂向物料发出工厂下库存转储订单
•物料发出工厂根据库存转储订单安排生产、采购、物料转运等 •物料接收工厂根据库存转储订单安排收货
多工厂计划模式2-部件从发货工 厂库存消耗 •装配体在其工厂计划、生产
订单管理
订单管理的目的在于:对于机会管理中确定跟踪的订单,从全公司范 围,制订订单策略,协调资源(生产、采购、资金、技术等),以确 保订单的成功率和交付率。 订单管理包括: ·有效意向订单 ·确定订单
机会管理
销售机会描述
TBD
销售策略,人员和BD活动
产品策略: 价格策略: 人员和经验: SME: 合作伙伴策略: Up-to-date综合Win Odds:
生产技术准备
全新设计
市场预测 市场
新产品形成过程
生产管理
制造、检验
交货、用户服务
用户
客户订单产品制造过程 外协 外购 厂家 采购
变型设计
销售部门技术组
合同管理
签订合同
产品结构优化
通过产品的标准化降低零部件种类数;进而降低生产成本
- 产 品 设 计 的 ABC 分 析
% 成本所占比率
100 80 60
最优的计划
能力计划:处理流程
可用能力设定
计划制定
能力需求计算 能力评估与调度 能力减少
可用能力
工作中心计划
工作时间 休息时间
06:00
07:00
08:00
09:00
10:00
11:00
12:00
13:00
14:00
15:00
16:00
17:00
工作中心能力:表头屏幕信息
开始时间 结束时间 休息时间 工作时间 07:00:00 16:30:00 01:30:00 8.00 小时 能力利用率 能力的数量 能力 90% 4 28.8 小时
工作中心的分级结构
工厂 制造 部门 1
16 H
机器
装配 部门 2
4H
运输
测试
18 H
劳动力
工作中心 组1
工作中心 组 10
10 H
机器
8H
劳动力
2H
运输
6H
机器
10 H
劳动力
2H
运输
工作中心 组 20
10 H
机器
8H
劳动力
2H
运输
4H
劳动力
6H
机器
6H
劳动力
2H
运输
工作中心 101
工作中心 102
日 日 日 日 日 日 日 日 日 日 日 日 日 日 日 日 日 日 日 日 日 日 日 日 日 日 日 日 日 日 22 24 26 28 30 月2 月4 月6 月8 10 12 14 16 18 20 22 24 26 28 30 月1 月3 月5 月7 月9 11 13 15 17 19 9月 9月 9月 9月 9月 10 10 10 10 10月 10月 10月 10月 10月 10月 10月 10月 10月 10月 10月 11 11 11 11 11 11月 11月 11月 11月 11月
订单 开始日期 成品 订单 结束日期 计划订单