煤粉高效洁净燃烧技术
煤炭洁净加工技术的分类

煤炭洁净加工技术的分类
煤炭洁净加工技术可以分为以下几类:
1. 煤炭粉煤化技术:将煤炭磨碎成细小的煤粉,提高燃烧效率,减少烟气排放。
常见的煤炭粉煤化技术包括煤粉炉渣分离、煤粉气固分离等。
2. 煤炭燃烧优化技术:通过优化煤炭的燃烧过程,减少燃烧废气中的污染物排放。
常见的燃烧优化技术包括燃烧氧化剂预热、燃烧控制系统优化等。
3. 煤炭气化技术:将煤炭在高温和缺氧条件下转化为合成气体(包括CO和H2等成分),再经过清洁处理得到清洁燃料或
化工原料。
常见的煤炭气化技术包括煤气化、生物质气化等。
4. 煤炭液化技术:将煤炭经过加热和一定的催化剂处理后,转化为液体燃料,如煤油、柴油等。
常见的煤炭液化技术包括煤直接液化、煤间接液化等。
5. 煤炭燃气化技术:将煤炭通过煤燃气化装置,转化为燃气,再通过一系列净化处理得到清洁燃气。
常见的煤炭燃气化技术包括煤焦气气化、煤气补给炉燃气化等。
6. 煤炭金属提取技术:将煤炭中的有价值的金属元素进行提取,减少对环境的污染。
常见的煤炭金属提取技术包括煤炭中金属提取、煤矸石中金属提取等。
以上仅为煤炭洁净加工技术的一些常见分类,具体的分类方式还会根据技术的不断发展和创新而有所变化。
低负荷稳燃及低NOx煤粉燃烧技术.

(1)两级燃烧• 空气量分两段送入炉膛,第一级的空气量大约为80%左右,从主燃烧区送入;第二级的空气量占20%左右,从燃烧区的上方送入,两级喷口之间的距离为1.5~2m。
• 可以降低燃料型和温度型NOx 的生成。
• 应保证第二级空气与燃尽区火焰的混合良好,避免造成不完全燃烧。
• 一次燃烧区内由于缺氧,形成还原性气氛,这样使灰熔点降低,不仅容易引起结渣,还会产生腐蚀。
• 由于燃烧分段进行,火焰拉长,如果组织不好,焦炭难以燃尽,还会引起炉膛出口处的受热面结渣。
(2)MACT与A-MACT炉内脱氮技术 MACT炉内脱氮技术:• 控制主燃烧区的燃料与空气比为0.8~0.9。
• 在主燃烧器上方设置OFA(Over Fuel Air)供风,使主燃烧区生成的NOx 到达OFA区时,由于缺氧而被还原成N2。
• 在上二次风OFA喷口上部再设置一层附加空气AA (Additional Air),还原区的未燃物进入燃尽区后与 AA供风混合,被充分燃烧。
A-MACT燃烧技术:• 将AA供风进一步细分为上下两层,以促进未燃物与空气的均匀混合,提高燃烧效率• 可将NOx 控制在60~150ppm内。
(3)扩大还原燃烧技术• 在主燃烧区与燃尽区之间留有较大的空间,并注入IAP供风(分级风),形成HCN、NH3、HC等还原性气氛,促使NOx还原。
• 与两段燃烧法相比,NOx 减少了35%,由210ppm降低到130~140ppm。
洁净型煤工艺技术方案
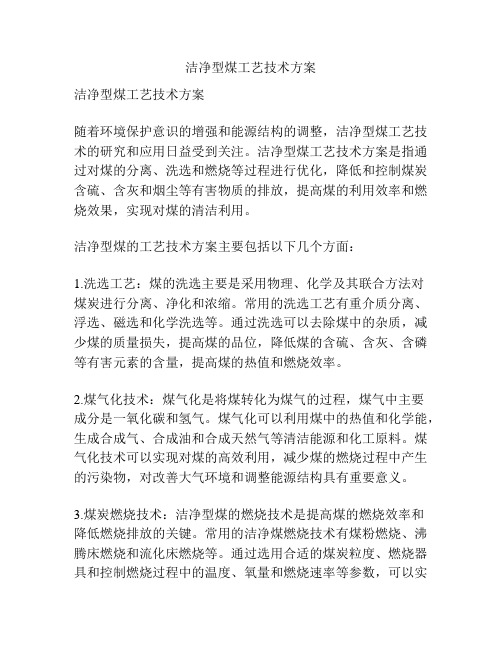
洁净型煤工艺技术方案洁净型煤工艺技术方案随着环境保护意识的增强和能源结构的调整,洁净型煤工艺技术的研究和应用日益受到关注。
洁净型煤工艺技术方案是指通过对煤的分离、洗选和燃烧等过程进行优化,降低和控制煤炭含硫、含灰和烟尘等有害物质的排放,提高煤的利用效率和燃烧效果,实现对煤的清洁利用。
洁净型煤的工艺技术方案主要包括以下几个方面:1.洗选工艺:煤的洗选主要是采用物理、化学及其联合方法对煤炭进行分离、净化和浓缩。
常用的洗选工艺有重介质分离、浮选、磁选和化学洗选等。
通过洗选可以去除煤中的杂质,减少煤的质量损失,提高煤的品位,降低煤的含硫、含灰、含磷等有害元素的含量,提高煤的热值和燃烧效率。
2.煤气化技术:煤气化是将煤转化为煤气的过程,煤气中主要成分是一氧化碳和氢气。
煤气化可以利用煤中的热值和化学能,生成合成气、合成油和合成天然气等清洁能源和化工原料。
煤气化技术可以实现对煤的高效利用,减少煤的燃烧过程中产生的污染物,对改善大气环境和调整能源结构具有重要意义。
3.煤炭燃烧技术:洁净型煤的燃烧技术是提高煤的燃烧效率和降低燃烧排放的关键。
常用的洁净煤燃烧技术有煤粉燃烧、沸腾床燃烧和流化床燃烧等。
通过选用合适的煤炭粒度、燃烧器具和控制燃烧过程中的温度、氧量和燃烧速率等参数,可以实现煤的充分燃烧,降低燃烧产物中的有害物质含量。
4.煤炭净化技术:煤炭净化技术主要是对煤炭中的尘埃、颗粒物和有机物进行去除和净化。
常用的煤净化技术有湿式电除尘、静电除尘和脱硫脱硝等。
通过煤炭净化技术可以提高煤炭的燃烧效率,减少烟气中的颗粒物和有害气体的排放,改善燃烧产物的环境适应性和资源利用效率。
综上所述,洁净型煤工艺技术方案是通过优化煤的洗选、气化、燃烧和净化等过程,降低和控制煤炭排放的有害物质,提高煤的利用效率和燃烧效果。
洁净型煤工艺技术方案的研究和推广应用,对于改善大气环境、实现能源可持续发展和推动绿色低碳经济具有重要意义。
低NOx煤粉燃烧技术

因此,不但延迟了燃烧过程,而且在还原性 气氛中降低了生成NOx的反应率,抑制了 NOx在这一燃烧中的生成量.为了完成全部 燃烧过程,完全燃烧所需的其余空气则通过 布置在主燃烧器上方的专门空气喷口OFA (over fire air)――称为"燃尽风(火上风) "喷口送入炉膛,与第一级燃烧区在"贫氧燃 烧"条件下所产生的烟气混合,在α>1的条 件下完成全部燃烧过程.由于整个燃烧过程 所需空气是分两级供入炉内,故称为空气分 级燃烧法.
燃料分级燃烧
利用这一原理,将80-85%的燃料送入第一级燃烧 区,在α>1条件下,燃烧并生成NOx.送入一级燃烧 区的燃料称为一次燃料,其余15-20%的燃料则在 主燃烧器的上部送入二级燃烧区,在α<1的条件下, 形成很强的还原性氛围,使得在一级燃烧区生成 的NOx在二级燃烧区内被还原成氮原子,二级燃 烧区又称为再燃区,送入二级燃烧区的燃料又称 为二次燃料或者再燃燃料。在再燃区中不仅使得 已生成的NOx得到还原,还抑制了新的NOx的生 成,可使NOx的排放浓度进一步降低。
目前,国内外控制NOx排放的技术措施主要 有两大类: 采用低NOx的燃烧技术,通过改变燃烧过 程来有效地控制NOx的生成。 尾部烟道脱硝处理。使用选择性催化还原 (SCR)和选择性非催化还原(SNCR) 两种方式对烟道气进行处理。
低NOx煤粉燃烧技术目前主要有以下几种 1)低过量空气燃烧 2)空气分级燃烧 3)燃料分级燃烧 4)烟气再循环 5)低NOx燃烧器
燃料分级燃烧
在燃烧中已生成的NO遇到烃根CHi和未完全燃 烧产物CO、H2、C和CnHm时,会发生NO的还 原反应,反应式为: 4NO+CH4 =2N2+CO2+2H2O 2NO+2CnHm+(2n+m/2-1)O2 =N2+2nCO2+mH2O 2NO+2CO =N2+2CO2 2NO+2C =N2+2CO 2NO+2H2 = N2+2H2O
洁净煤技术

洁净煤技术1. 引言洁净煤技术是一种通过使用先进的煤燃烧和碳捕集技术来减少燃煤产生的污染物排放,并提高煤燃烧效率的方法。
煤是目前世界上最主要的能源来源之一,但其燃烧会产生大量的二氧化硫、氮氧化物和颗粒物等污染物,对环境和人类健康造成严重影响。
洁净煤技术的发展旨在解决这些问题,使煤燃烧更加环保和高效。
2. 洁净煤技术的分类洁净煤技术可分为燃烧技术和碳捕集技术两大类。
2.1 燃烧技术燃烧技术是通过改进煤燃烧过程来降低污染物排放的方法。
常见的燃烧技术包括:•燃烧控制:通过优化燃烧温度、燃料供给以及燃烧过程中的空气分配,减少煤燃烧过程中产生的污染物;•燃料预处理:对煤进行洗煤、破碎和干燥等处理,去除其中的杂质和水分,提高煤燃烧效率;•燃烧辅助技术:如气体再循环、预混煤粉燃烧等,可以降低煤燃烧过程中的氮氧化物排放。
2.2 碳捕集技术碳捕集技术是一种将二氧化碳从煤燃烧废气中分离和捕集的方法。
常见的碳捕集技术包括:•吸收法:利用化学吸收剂(如氨水和胺溶液)与废气中的二氧化碳发生反应,使其被吸收,并进一步进行分离和回收;•膜分离法:利用特殊薄膜将废气中的二氧化碳分离出来,实现捕集和回收;•吸附法:利用固体吸附剂,如活性炭和分子筛,吸附并分离废气中的二氧化碳。
3. 洁净煤技术的应用洁净煤技术已在全球范围内得到广泛应用。
以下是洁净煤技术在不同领域的应用示例:3.1 发电工业洁净煤技术在发电工业中的应用主要集中在大型燃煤发电厂。
通过采用燃烧控制、燃料预处理和燃烧辅助技术,可以降低发电过程中的污染物排放,并提高煤燃烧效率。
碳捕集技术的应用则可以实现二氧化碳的捕集和回收,减少碳排放。
3.2 工业锅炉工业锅炉是工业生产中常见的燃煤设备,也是污染物排放的重要来源之一。
洁净煤技术在工业锅炉中的应用可以有效减少煤燃烧产生的污染物,并提高能源利用效率。
3.3 煤气化工艺煤气化是一种将煤转化为合成气的过程,合成气可以用于制备液体燃料和化学品。
洁净煤技术

洁净煤技术A12化工一班120702107 吕荣青摘要我国是一个多煤、少油、少气的国家,未来能源发展的政策仍是“煤为基础,多元发展”。
提高煤炭利用率、降低污染率,是我国能源工业发展的紧迫而现实的任务。
而完成这一任务,就需要大力发展洁净煤技术。
关键词:煤炭能源洁净煤技术1. 洁净煤技术的特点洁净煤技术是洁净、高效利用煤炭的先导性技术,最早由美国学者提出,主要是为了解决美国和加拿大边境的酸雨问题。
洁净煤技术是指从煤炭开发到利用全过程中,旨在减少污染物排放和提高利用效率的煤炭加工、转化、燃烧及污染控制等一系列新技术的总称,是使煤作为一种能源应达到最大限度的潜能利用,而将释放的污染控制在最低水平,实现煤的高效、洁净利用的技术体系。
洁净煤技术具有以下几个显著特点:首先,洁净煤技术以高硫煤为原料,以一碳化学为基础,采用多样化工艺,实现煤炭资源的优化配置、高效和清洁利用;其次,洁净煤技术涉及物理学、化学、生物学、地质学等多学科,化工、热工、环境等多技术,是一项多层次、多学科、综合性很强的系统工程;第三,洁净煤技术注重综合效益,实现了环境友好和经济发展的双重效益,即经济和环境的双赢。
传统意义上的洁净煤技术主要是指煤炭的净化技术及一些加工转换技术,即煤炭的洗选、配煤、型煤以及粉煤灰的综合利用技术,国外煤炭的洗选及配煤技术相当成熟,已被广泛采用;意义上洁净煤技术是指高技术含量的洁净煤技术,发展的主要方向是煤炭的气化、液化、煤炭高效燃烧与发电技术等等。
2.技术工艺洁净煤技术包括两个方面,一是直接烧煤洁净技术,二是煤转化为洁净燃料技术。
2.1直接烧煤洁净技术这是在直接烧煤的情况下,需要采用的技术措施:①燃烧前的净化加工技术,主要是洗选、型煤加工和水煤浆技术。
②燃烧中的净化燃烧技术,主要是流化床燃烧技术和先进燃烧器技术。
③燃烧后的净化处理技术,主要是消烟除尘和脱硫脱氮技术。
2.2煤转化为洁净燃料技术主要有四种:①煤的气化技术②煤的液化技术③煤气化联合循环发电技术④燃煤磁流体发电技术。
煤炭清洁利用技术发展方向及作用范本(2篇)

煤炭清洁利用技术发展方向及作用范本煤炭是世界上最重要的能源之一,然而,长期以来煤炭的高污染和高排放问题一直困扰着我们。
为了保护环境、提高能源利用效率,各国纷纷开始研发煤炭清洁利用技术。
本文将从技术发展方向和作用两个方面进行阐述。
一、煤炭清洁利用技术发展方向1. 煤炭洁净化技术煤炭洁净化技术主要是指将煤炭中的杂质和有害物质去除,从而提高燃烧效率和降低污染物的排放。
洁净化技术主要包括煤炭分选、煤炭洗选、煤炭脱硫等。
煤炭分选可以将煤炭中的杂质分离出来,提高煤炭的纯度和热值;煤炭洗选可以将煤炭中的灰分和硫分去除,降低燃烧时的污染物排放;煤炭脱硫可以将煤炭中的硫化物去除,减少二氧化硫排放。
煤炭洁净化技术的发展能够提高煤炭的利用效率,降低煤炭燃烧对环境的影响。
2. 煤炭高效燃烧技术煤炭高效燃烧技术主要是指提高煤炭的燃烧效率,减少污染物和温室气体的排放。
目前常见的煤炭燃烧技术包括煤粉燃烧、煤炭气化和煤炭流化床燃烧等。
煤粉燃烧是将煤炭研磨成细小的粉末,加上适量的空气进行燃烧,可以提高燃烧效率,减少污染物排放;煤炭气化是将煤炭在高温下分解为气体,可以得到高能煤气,用于发电和制造化工品;煤炭流化床燃烧是将煤炭放入流化床中燃烧,可以提高燃烧效率,并且燃烧产生的矿渣可以用于建筑材料。
煤炭高效燃烧技术的发展可以提高能源利用效率,减少污染物和温室气体的排放。
3. 煤炭碳捕集和储存技术煤炭碳捕集和储存技术主要是指通过各种方法将燃烧产生的二氧化碳捕集并储存起来,从而减少温室气体的排放。
目前常见的煤炭碳捕集和储存技术包括化学吸收法、物理吸附法和生物固定化法等。
化学吸收法是指利用化学方法将二氧化碳吸附在吸附剂上,从而实现二氧化碳的分离和储存;物理吸附法是指利用物理方法将二氧化碳吸附在多孔材料上;生物固定化法是指利用微生物将二氧化碳转化为有机物质进行存储。
煤炭碳捕集和储存技术的发展可以有效地减少温室气体的排放,缓解全球气候变暖的问题。
洁净煤技术

1、洁净煤技术的定义和内涵?在煤炭开发和加工利用全过程中旨在减少污染和提高效率的煤炭加工、燃烧、转化和污染控制等新技术的总称。
是使煤炭作为一种能源应达到最大潜能的利用而释放的污染物控制在最低量,以实现煤的高效、洁净、经济利用为目的技术。
中国洁净煤技术是以煤炭洗选为源头、以煤炭气化为先导、以煤炭高效、洁净燃烧与发电为核心、以煤炭转化和污染控制为重要内容的技术体系。
2、煤炭燃烧的方式根据煤在燃烧过程中的运动状态分为:层状燃烧、悬浮燃烧、流态化燃烧(沸腾燃烧)3、CO2的捕集方式二氧化碳的捕集方式主要有三种:燃烧前捕集(Pre-combustion)、富氧燃烧(Oxy-fuel combustion)和燃烧后捕集(Post-combustion)。
依据捕获系统的技术基础和适用性,通常将火电厂CO2的捕集系统分为以下4种:燃烧后脱碳(post-combustion)、燃烧前脱碳(pre-combustion)、富氧燃烧技术(oxyfule)以及化学链燃烧技术(CLC)。
4、IGCC发电系统组成、发电原理、过程、优点整体煤气化联合循环(IGCC-Integrated Gasification Combined Cycle)发电系统,是将煤气化技术和高效的联合循环相结合的先进动力系统。
它由两大部分组成,即煤的气化与净化部分和燃气-蒸汽联合循环发电部分。
第一部分的主要设备有气化炉、空分装置、煤气净化设备(包括硫的回收装置),第二部分的主要设备有燃气轮机发电系统、余热锅炉、蒸汽轮机发电系统。
IGCC的原理是:煤经过气化和净化后,除去煤气中99%以上的硫化氢和接近100%的粉尘,将固体燃料转化成燃气轮机能燃用的清洁气体燃料,供入燃气轮机的燃烧室,产生高温燃气以驱动燃气轮机发电,再利用燃气轮机高温排气经余热锅炉产生的蒸气推动蒸汽轮机做功发电,即使得燃气发电与蒸汽发电联合起来。
指煤经过气化产生中低热值煤气,经过净化除去煤气中的硫化物、氮化物、粉尘等污染物,变为清洁的气化燃料,燃烧后先驱动燃气轮机发电,然后利用高温烟气余热在废热锅炉内产生过热蒸汽驱动蒸汽轮机发电。
- 1、下载文档前请自行甄别文档内容的完整性,平台不提供额外的编辑、内容补充、找答案等附加服务。
- 2、"仅部分预览"的文档,不可在线预览部分如存在完整性等问题,可反馈申请退款(可完整预览的文档不适用该条件!)。
- 3、如文档侵犯您的权益,请联系客服反馈,我们会尽快为您处理(人工客服工作时间:9:00-18:30)。
煤粉高效洁净燃烧技术 Prepared on 22 November 2020煤粉高效洁净燃烧技术近年来,随着各国政府对环保工作的日益重视,全世界范围内都兴起了治理污染、保护环境的运动。
新的环保技术及产品不断涌现,同时也不断地产生新的难题。
煤粉燃烧在污染排放中占重要地位,也是历来治理污染的重点和难点。
许多国家在治理环境污染活动中一直把它作为中心任务,也取得了比较明显的效果。
据预测,2000~2010年我国煤炭在一次能源需求中的比重仍为70%左右,2050年可降至50%以下,但煤炭消费的绝对量还是大大增加了。
因此,对我国政府而言,控制环境保护总体指标,首先必须控制燃煤造成的污染,其出路无非在于大力发展以煤炭高效洁净利用为宗旨的洁净煤技术。
在洁净煤技术不断发展的十几年内,国内外均开发了许多产品和成套技术。
有先进的选煤技术、水煤浆技术、煤炭气化、煤炭液化技术,有循环流化床、增压循环流化床、整体煤气化联合循环等技术,有各种处理水平的烟气净化技术及粉煤灰综合利用技术等。
综合考虑我国现状,煤粉高效洁净燃烧及烟气净化技术在近期应有较广阔的应用空间。
●煤粉高效洁净燃烧技术及烟气净化技术现状煤粉高效洁净燃烧及烟气净化技术包括高效燃烧技术、低NOx燃烧技术、烟气脱硫技术、烟气脱硝技术、除尘技术等。
现简要介绍如下:一般而言,煤粉高效燃烧技术与低NOx燃烧技术是互为矛盾的两种技术。
降低NOx生成与排放根本在于控制燃烧区域的温度不能太高,但低温燃烧又影响煤粉的燃烧率,协调好这两项技术的应用使之达到综合最佳效果是目的,实际上就要求对煤粉燃烧的全过程加以控制。
既能够保证煤粉着火的稳定性,又有较低的燃烧温度,同时有足够长的并在一定温度下的燃烧时间保证燃烬。
目前世界上较先进的燃烧技术基本兼顾了这些因素,其中以直流燃烧器为主的有:ABB-CE公司利用一次风弯头的惯性分离作用,在弯头出口中间设置有孔隔板,将煤粉气流分成上浓下淡两段气流,形成上下浓淡煤粉燃烧器,并在喷口处装有轴向距离可调整的V型钝体,通过合理组织二次风,同时达到了稳定、高效、低NOx排放的燃烧效果;三菱重工(MHI)开发了PM型燃烧器,利用弯头的离心作用,把一次风分成上下浓淡两股气流,同时采用烟气再循环和炉内整体分级燃烧技术,也达到了较好的效果。
以旋流燃烧器为主的有:FW公司利用旋风子使进入主燃烧器的一次风浓度增加,并降低一次风速以保证煤粉气流着火稳定性,并控制NOx的生成量;有较多工业应用的还有B&W公司的PAX型旋流煤粉燃烧器、日本I HI公司的宽调解范围旋流煤粉燃烧器、德国斯坦米勒公司多级分级供风旋流燃烧器等。
上述这些工业产品均能够保证NOx排放在400mg/Nm3以下,并具有较高燃烧效率。
目前国外正在开发的低NOx燃烧技术可以控制NOx 生成量是在200mg/Nm3左右,已达到了比较高的水平。
但由于世界上很多先进国家对NOx排放规定了严格的标准,仅靠改进和提高燃烧技术难以达到NOx控制值,因而有些锅炉机组在尾部增设了烟气脱硝装置。
我国近年来也开发了很多型式的低NOx燃烧技术,具有代表性的是浓淡煤粉燃烧器,包括水平浓淡、上下浓淡直流燃烧器、旋流燃烧器和可控浓淡旋流煤粉燃烧器等。
但由于我国存在煤种多变等问题,致使这些技术在应用中遇到了一些问题,包括采用国外类似技术制造的燃煤机组也遇到了同样的问题。
通过努力,最近针对褐煤锅炉已开发并已工业应用了具有一定煤种自适应性的低负荷稳燃低NOx排放成套燃烧技术,可以控制NOx排放量在400mg/Nm3以下,燃烧效率在99%以上,比较先进。
烟气脱硫、脱硝与除尘是烟气净化的三个主要内容。
在烟气脱硫方面,湿法脱硫占绝对主导地位,在发达国家占有市场90%以上。
其他为半干法脱硫、炉内喷钙尾部增湿、排烟循环硫化床法、电子束氨法等脱硫技术。
从发展看,湿法脱硫仍由于其指标高而占主导地位,排烟循环硫化床脱硫方法也由于其技术经济的综合优势而逐步占据了一些市场并将在发展中国家逐步得到大量应用。
对我国而言,对新建机组最好采用湿法脱硫技术设备一步到位;对改造机组视煤种含硫量而定,如高硫煤可采用排烟循环硫化床方法,对低硫煤可采用炉内喷钙配以尾部增湿,尤其是现已存在的大量水膜除尘器可以综合利用其价值。
在烟气脱硝方面,国外一般采用选择性还原反应装置,去除烟气中大部分的氮氧化物,其他方法尚在开发和研究阶段。
国内由于资金、场地等限制,尚无工业应用先例,而且暂时也无能力完成示范机组建设。
在烟气除尘方面,由于发达国家对烟尘排放率和超细颗粒脱尘率的要求持续升高,许多国家已逐步将电除尘器改为脉冲反吹滤袋式除尘器,这可以澳大利亚、美国等国家为代表。
我国近期计划把大批中型机组的旋风除尘器或水膜除尘器替换成电除尘器,指标为出口烟尘不超过200mg/Nm3,飘尘则无要求。
在拟建的大连台山增压循环硫化床锅炉上,中方准备采用脉冲反吹式滤袋除尘器,以达到较高性能。
●国家电站燃烧工程技术中心“八五”、“九五”期间科研工作情况和成果应用情况一、研究设施情况介绍无论机理研究还是中试规模试验均可分为三部分:空气动力特性试验、气固两相流特性试验和煤燃烧特性试验,因此,中心分别建设了三个试验大厅以满足三种试验的不同要求。
空气动力特性试验大厅共800m²,供风母管制,总风量为50000 Nm³/h,分四个区域:单只燃烧器流动特性研究区、炉内流动特性区、优化结构节能降阻区、测量装置与风门检测和其他产品技术开发区。
测试仪器有丹迪三维热线系统,PIV系统和其他常规仪器仪表。
目前已完成了30多台架试验室研究工作并多在现场应用中取得了比较好的效果。
此外,还有其他的配套机理研究试验台架和流场计算软件等。
气固两相流试验大厅500m²,也是供风母管制,总风量为35000 Nm³/h,压头10000Pa,供粉量可达200kg/h,粉为碳化硅或煤粉及电厂飞灰三种。
可进行浓淡燃烧器开发、旋风分离及除尘器改进和电除尘、滤袋除尘器研究以及脱硫塔流动特性研究,也可进行磨损试验研究等。
此外还有独立的煤粉均分器试验台、自动可调叶栅百叶窗煤粉分配器试验台及其它机理试验台。
测试仪器有激光全息照相系统、片光源拍摄系统、库尔特粒度仪、光纤浓度分析系统、流场图形再现分析系统及及其它浓度和流场的常规测试系统。
●煤燃烧特性试验大厅700m²,可分为三大部分。
第一大部分为引进加拿大安大略省电力公司燃煤燃烧中试试验系统装置(CRF)。
每小时燃煤量为20kg,热功率为。
该装置分原煤干燥系统、原煤粉碎系统、制粉系统、燃烧系统、一二次风系统、烟气处理系统、炉内喷钙系统、烟气除尘系统、烟气成分测试系统和控制系统等。
测试系统与控制系统采用罗斯蒙特烟气在线分析系统和其它流量、温度、压力传感器,全部输入计算机并由计算机对所有变量进行在线动态调整,以满足试验条件和要求。
该装置可全面准确地模拟原煤干燥、粉碎、制粉、输粉、燃烧、烟气处理的全过程,可重点进行运行参数、燃料品质对燃烧的稳定性、燃烬程度、沉积物的形成、污染物的形成、粒子的排放和收集的影响程度的评估与研究,并可在此过程中开发新的低NOx燃烧技术、炉内喷钙技术和其它烟气处理技术。
这套装置自动化程度高,控制、测试仪器水平高,试验重复率好,可进行较为广泛的技术开发与研究,是国际上较为先进的煤燃烧试验装置之一。
目前,中心对这套试验装置又进行了一些改造,重建了燃烧系统、增加了燃烧功率至,增加了烟气尾部增湿活化装置、增加了悬浮法烟气脱硫装置,并正在开展新的研究。
第二大部分是与荷兰能源基金会(ECN)合建的常压夹带流气化和燃烧模拟装置(AEFGC)。
它装有一个整体、预混合和多级平火焰煤气燃烧器,每小时燃煤量为5g左右,通过在不同级段提供不同的混合气粉,模拟颗粒在实际过程中经历的初始加热率、预混合和气态环境,是近似单颗粒机理研究的基础设施。
同它配备的有气体分析系统、供粉系统、测试系统和其它先进的控制系统。
第三部分是基础研究设施,包括热重/差热同步分析实验室、燃料元素快速分析及燃料其它特性分析实验室。
可进行燃煤着火特性、燃烬率、燃烧反应动力学以及脱硫的机理性试验研究和分析。
除这些物理研究之外,中心还配置了一些专门人员进行流动、扩散和燃烧的数值模拟研究工作,并从德国引进了一套包括NOx生成预测的数值模拟软件,取得了一定的成果。
二、研究情况和应用情况:“八五”、“九五”期间,中心先后承担了百余项纵向、横向科研与生产改造和产业制造项目。
其中国家科委“九五”重点攻关项目专题子专题项目七项、国家计委示范生产线建设项目两项。
另外,国内外发表论文百余篇,并多次获得国家科委、国家电力公司、东北电力集团公司、辽宁省科委与沈阳市的奖励。
现简要介绍一下研究的重点课题和应用情况。
(一)整体分级低NOx燃烧技术开发该项目是国家“九五”重点攻关项目子专题。
研究内容是开发一种从整体上将煤粉着火区与燃烬区分开,获得低负荷稳燃、低NOx排放、提高煤粉燃烧效率、降低炉内结渣强度、提高机组出力效果的实用技术。
通过理论分析和数值模拟研究、试验室机理研究和中试等多种研究手段研究,中德专家共同提出了一种工程改造方案,并在元宝山发电厂2号炉上得以实施。
该锅炉由德国Steimueller公司制造,额定蒸发量h,于1986年投产。
作为当时国内最大的火力机组存在着炉内严重结渣,再热器超温严重,锅炉出力仅为额定出力75%,NOx排放为1000mg/Nm3以上等严重问题。
改造方案实施后,解决了上述全部问题。
并且,改造方案工程实施难度较小。
这一课题的完成,使中心在掌握褐煤燃烧特性、合理组织燃烧结构、降低污染物排放、减轻结渣等方面都取得了较好的成果。
(二)具有自适应性的低NOx煤粉燃烧技术研究:该项目是国家“九五”重点攻关项目子专题。
一般的低NOx燃烧技术,不随煤种变化而变化,也不因负荷变动而随之相应调整。
这样有时在煤种及负荷变动很大的情况下,就不可避免地发生喷口结渣或低NOx燃烧效果不佳等共伴矛盾。
在本项目研究中,采取了将煤粉分为二级浓缩的办法,一级是自动可调的增强效果浓缩器或强制均分器,一级为基础浓缩器。
二种方法结合可得到与负荷和煤种变化同步变化的连续可调浓缩比,实现可控燃烧过程。
从而实现沿炉膛高度方向热负荷可调、提高燃烧效率、低NOx燃烧、减少再热器减温水、避免炉内结渣、低负荷稳燃性能好等功能。
这项技术及产品适用于风扇磨煤机的燃烧制粉系统,实施时还应配套中心研制的FDD 智能型流量测量装置等以确保合理配置二次风等。
该技术产品已应用于二台300MW机组和三台200MW机组,均取得了相当显着的经济效益和社会效益。
(三)可调、可控、均分、均流、低阻的煤粉均分器开发:该项目也是国家“九五”重点攻关项目子专题。