电石渣中氯离子对水泥窑生产的影响的报告
电石渣氯离子高的原因
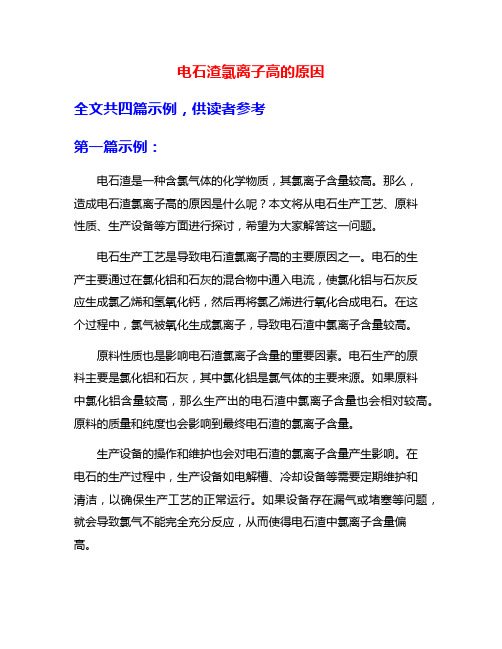
电石渣氯离子高的原因全文共四篇示例,供读者参考第一篇示例:电石渣是一种含氯气体的化学物质,其氯离子含量较高。
那么,造成电石渣氯离子高的原因是什么呢?本文将从电石生产工艺、原料性质、生产设备等方面进行探讨,希望为大家解答这一问题。
电石生产工艺是导致电石渣氯离子高的主要原因之一。
电石的生产主要通过在氯化铝和石灰的混合物中通入电流,使氯化铝与石灰反应生成氯乙烯和氢氧化钙,然后再将氯乙烯进行氧化合成电石。
在这个过程中,氯气被氧化生成氯离子,导致电石渣中氯离子含量较高。
原料性质也是影响电石渣氯离子含量的重要因素。
电石生产的原料主要是氯化铝和石灰,其中氯化铝是氯气体的主要来源。
如果原料中氯化铝含量较高,那么生产出的电石渣中氯离子含量也会相对较高。
原料的质量和纯度也会影响到最终电石渣的氯离子含量。
生产设备的操作和维护也会对电石渣的氯离子含量产生影响。
在电石的生产过程中,生产设备如电解槽、冷却设备等需要定期维护和清洁,以确保生产工艺的正常运行。
如果设备存在漏气或堵塞等问题,就会导致氯气不能完全充分反应,从而使得电石渣中氯离子含量偏高。
电石渣氯离子高的原因主要包括生产工艺、原料性质和生产设备等多个方面。
只有在控制好这些因素,合理调整生产工艺和提高设备操作技术水平的情况下,才能保证生产出质量稳定、氯离子含量适中的电石渣产品。
希望本文的介绍能为大家对电石渣氯离子高的原因有所帮助。
第二篇示例:电石渣中含有高浓度的氯离子,这是因为电石渣是电石生产过程中产生的副产物。
电石是一种由石灰石和焦炭经过高温炼制得到的化学物质,主要用于生产氯化钾和氯气等化工产品。
在电石的生产过程中,经过高温炼制后会产生大量的废弃物,其中包括电石渣。
电石渣含有高浓度的氯离子的原因主要有以下几点:电石生产过程中需要大量的氯离子参与化学反应。
在电石的炼制过程中,氯离子是一种必不可少的化学物质,它可以与其他物质发生化学反应,从而形成氯化钾和氯气等产品。
电石生产过程中会大量消耗氯离子,而产生电石渣则是因为部分氯离子未能完全反应而被残留在产物中。
水泥中氯离子造成危害分析及防治方法
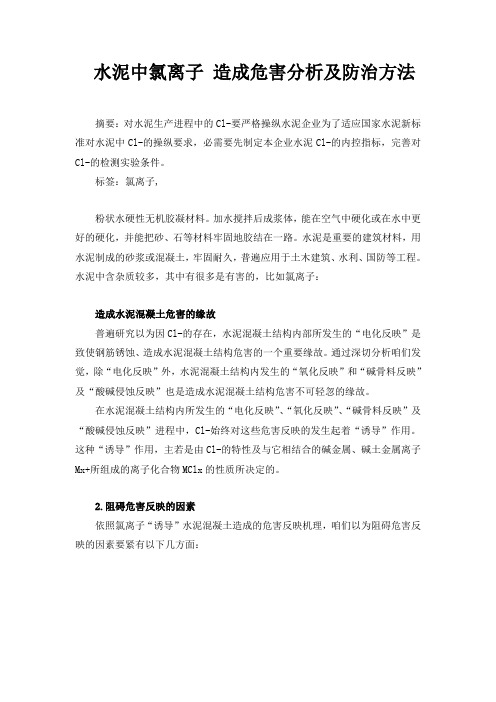
水泥中氯离子造成危害分析及防治方法
摘要:对水泥生产进程中的Cl-要严格操纵水泥企业为了适应国家水泥新标准对水泥中Cl-的操纵要求,必需要先制定本企业水泥Cl-的内控指标,完善对Cl-的检测实验条件。
标签:氯离子,
粉状水硬性无机胶凝材料。
加水搅拌后成浆体,能在空气中硬化或在水中更好的硬化,并能把砂、石等材料牢固地胶结在一路。
水泥是重要的建筑材料,用水泥制成的砂浆或混凝土,牢固耐久,普遍应用于土木建筑、水利、国防等工程。
水泥中含杂质较多,其中有很多是有害的,比如氯离子:
造成水泥混凝土危害的缘故
普遍研究以为因Cl-的存在,水泥混凝土结构内部所发生的“电化反映”是致使钢筋锈蚀、造成水泥混凝土结构危害的一个重要缘故。
通过深切分析咱们发觉,除“电化反映”外,水泥混凝土结构内发生的“氧化反映”和“碱骨料反映”及“酸碱侵蚀反映”也是造成水泥混凝土结构危害不可轻忽的缘故。
在水泥混凝土结构内所发生的“电化反映”、“氧化反映”、“碱骨料反映”及“酸碱侵蚀反映”进程中,Cl-始终对这些危害反映的发生起着“诱导”作用。
这种“诱导”作用,主若是由Cl-的特性及与它相结合的碱金属、碱土金属离子Mx+所组成的离子化合物MClx的性质所决定的。
2.阻碍危害反映的因素
依照氯离子“诱导”水泥混凝土造成的危害反映机理,咱们以为阻碍危害反映的因素要紧有以下几方面:。
氯离子对G级水泥水化影响的化学机理研究
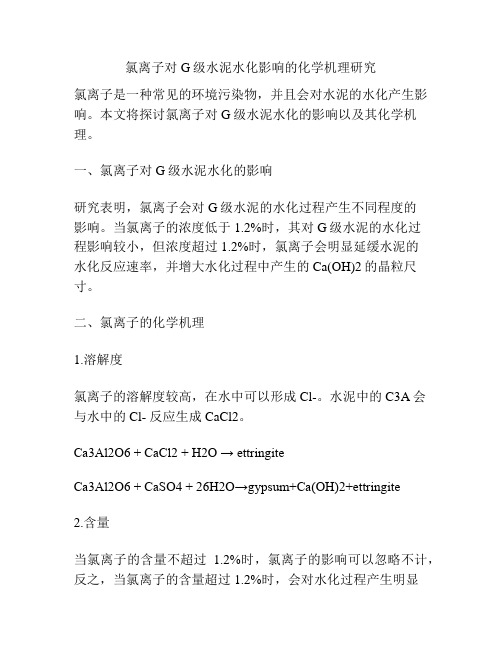
氯离子对G级水泥水化影响的化学机理研究氯离子是一种常见的环境污染物,并且会对水泥的水化产生影响。
本文将探讨氯离子对G级水泥水化的影响以及其化学机理。
一、氯离子对G级水泥水化的影响研究表明,氯离子会对G级水泥的水化过程产生不同程度的影响。
当氯离子的浓度低于1.2%时,其对G级水泥的水化过程影响较小,但浓度超过1.2%时,氯离子会明显延缓水泥的水化反应速率,并增大水化过程中产生的Ca(OH)2的晶粒尺寸。
二、氯离子的化学机理1.溶解度氯离子的溶解度较高,在水中可以形成Cl-。
水泥中的C3A会与水中的Cl- 反应生成CaCl2。
Ca3Al2O6 + CaCl2 + H2O → ettringiteCa3Al2O6 + CaSO4 + 26H2O→gypsum+Ca(OH)2+ettringite2.含量当氯离子的含量不超过 1.2%时,氯离子的影响可以忽略不计,反之,当氯离子的含量超过1.2%时,会对水化过程产生明显的影响。
3.反应氯离子和Ca(OH)2反应生成CaCl2和H2O,从而减缓了水化反应的速率。
Ca(OH)2 + 2Cl- → CaCl2 + H2O结论:氯离子会对G级水泥的水化反应产生不同程度的影响。
当氯离子浓度低于1.2%时,其对水泥水化的影响可以忽略不计,但是当浓度超过1.2%时,氯离子会明显延缓水化反应速率,并增大水化过程中产生的Ca(OH)2的晶粒尺寸。
氯离子的影响主要是通过C3A与氯离子的反应和减缓水化反应速率来实现的。
对于高氯离子污染环境中的混凝土结构,应采取相应的措施,以减小氯离子对混凝土结构的损害。
三、钙铝石膏水化产生的影响氯离子的存在会诱导氯钙铝石膏和钠钙铝石膏的形成,从而对水泥的水化过程产生影响。
这种钙铝石膏的形成通常发生在含盐土壤和海洋环境中。
钙铝石膏的产生会减缓水泥的水化反应速率,从而导致混凝土的强度下降。
”4.氯离子与水泥中的其他化学物质反应不同于一些其他的化学物质,氯离子与水泥中的多种化学物质都可能进行反应,并且不同反应的产物也不尽相同。
氯离子危害及控制措施

Cl-的危害及控制措施
1、国标要求水泥中氯离子含量不得超过0.06%,水泥企业必须严格控制,才能保证水泥合格。
2、Cl-含量比较高,容易造成预热器、分解炉、窑尾结皮、堵塞
严格控制电石渣中的Cl含量,化工厂和水泥厂必须都要重视:经分析大部分氯碱企业的电石渣中的氯离子普遍偏高,Cl-含量在0.023%-0.3%之间波动,有的氯碱企业在这方面做的很好,而有些氯碱企业的电石渣却Cl-含量居高不下。
我认为从源头上对电石渣中Cl-含量进行严格控制,从化工厂方面要控制和减少次氯酸钠循环次数、控制循环水重复使用次数等措施,因为一旦在化工厂无法降低电石渣中的Cl-含量,那么意味着会造成水泥厂无法使用或减少电石渣的掺加比例,同时会增加预热器结皮堵塞的频率,严重时使水泥生产无法进行。
目前电石渣中Cl-含量仍是制约大多数电石渣制水泥生产线正常运行的瓶颈,可以说是决定电石渣制水泥项目是否建设的或者采用部分掺加电石渣替代石灰石的工艺设计依据。
同时,我认为利用电石渣生产水泥企业,由于生料中的Cl-含量就比较高,如果窑灰全部入窑,更加容易造成预热器、分解炉、窑尾结皮、堵塞;为了降低入窑生料中的碱、氯、硫有害成份循环富集,而窑灰作为外循环部分,其中的碱、氯、硫有害成份含量很高,如果让这部分窑灰全部入窑,势必造成生产被动,结皮、堵塞在所难免。
建议在工艺设计阶段,考虑将窑灰全部外排或者部分外排、部分入窑,将外排的窑灰作为生产水泥的混合材使用。
操作中为防止生料中 Cl-偏高容易产生结皮结
圈、堵塞,可采取从C3上升烟道投料、适当降低分解炉和窑尾温度、适当提高三次风风门等措施。
、氯离子对水泥性能的影响

1、氯离子对水泥性能的影响水泥在没有C l-或C l-含量极低的情况下,由于水泥混凝土碱性很强,p H 值较高,保护着钢筋表面钝化膜使锈蚀难以深入。
氯离子在钢筋混凝土中的有害作用在于它能够破坏钢筋钝化膜,加速锈蚀反应。
当钢筋表面存在C l-、O2和H2O 的情况下,在钢筋的不同部位会发生如下电化学反应:F e +2C l-→F e C l2+2e-→F e2++2Cl-+2e-;O2+2H2O+4e-→4(O H )-。
进入水中的F e2+与O H-作用生成F e (O H )2,在一定的H2O 和O2条件下,可进一步生成F e (O H )3产生膨胀,破坏混凝土。
20世纪50年代,我国北方及国外某些国家(尤其是前苏联),为使冬季施工方便,曾普遍使用氯化钙等氯盐作混凝土早强(或防冻)剂,致使大量建筑因钢筋严重锈蚀而过早破坏,付出了昂贵的代价。
现在国内外钢筋混凝土工程施工原则上已不用氯盐早强(或防冻)剂;即使掺用氯盐,我国规定一般钢筋混凝土工程中氯盐掺量不得大于水泥重量的1%(港工钢筋混凝土中不得大于水泥重量的0.1%),并需对钢筋作防锈处理,将混凝土振捣密实。
此外,C a C l2用量较大时,还会降低混凝土抗化学侵蚀性和耐磨性及28天抗折强度。
如在生料中加入的氯化物,虽然可促进熟料煅烧,起到矿化剂的作用,对提高立窑产量有利,但有相当部分的氯离子会残留于熟料和水泥中,也会加速钢筋锈蚀。
因此,无论是水泥生料中,还是水泥中加入氯化物都应持谨慎态度,不宜掺加。
2、碱对水泥性能的影响碱溶解速度快,能增加水泥混凝土液相的碱度,可加速水泥水化速度及激发水泥中混合材的活性,通常被用作水泥的早强剂,以提高水泥的早期强度。
碱作为水泥早强剂对水泥的增强效果往往随外加剂的种类及掺量,外加剂中各激发组分的配比,混合材种类及掺量,熟料(或水泥)成分及性能,使用温度等因素的不同而不同。
但大多数外加剂对水泥早期(1天、3天、7天)强度的促进作用比对后期(28天)强度的促进效果好,有的还对28天强度没有促进作用甚至降低28天强度;有时会使水泥发生快凝、结块及需水量增加;还容易发生碱骨料反应,产生局部膨胀,引起构筑物开裂变形,甚至崩溃。
水泥氯离子含量的报告模板

水泥氯离子含量的报告模板
1. 背景
水泥一直是建筑材料中不可或缺的一种。
然而,水泥中的氯离子含量不仅会影响水泥的性能,还可能对混凝土结构造成不利影响。
因此,在建筑施工中对水泥中的氯离子含量进行检测是非常必要的。
2. 检测方法
2.1 检测原理
水泥中氯离子的检测一般采用离子选择性电极法。
该方法通过使用氯离子选择性电极对样品进行测量,根据电位变化来计算出样品中氯离子的含量。
2.2 检测步骤
1.将水泥样品加入加热的硝酸中,加热至样品全部溶解;
2.加入氧化亚铁,还原氯离子,并使Fe(III)还原为Fe(II);
3.加入氯离子选择性电极;
4.进行电位测量,根据电位变化计算出氯离子的含量。
3. 数据处理与分析
3.1 数据处理
根据检测方法中的步骤,通过氯离子选择性电极法对水泥中的氯离子含量进行了检测。
得到检测结果如下表:
样品编号氯离子含量 (mg/L)
1 0.012
2 0.009
3 0.011
4 0.015
5 0.013
3.2 数据分析
从表中可以看出,每个样品中的氯离子含量都小于0.02 mg/L,符合国家标准要求,说明这些水泥样品可以用于混凝土构件的生产。
4. 结论
通过离子选择性电极法对水泥中的氯离子含量进行检测,得出结果表明这些水泥样品中的氯离子含量均符合国家标准要求。
因此,这些水泥样品可以用于混凝土构件的生产。
电石渣特性对新型干法水泥工艺的影响_图文(精)
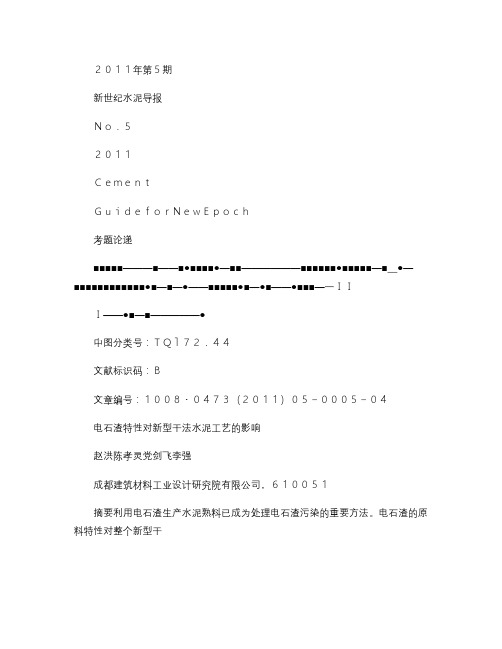
2011年第5期新世纪水泥导报No.52011CementGuideforNewEpoch考题论递■■■■■———■——■●■■■■●—■■——————■■■■■■●■■■■■—■_●—■■■■■■■■■■■■●■—■—●——■■■■■●■—●■——●■■■—一III——●■—■—————●中图分类号:TQl72.44文献标识码:B文章编号:1008・0473(2011)05-0005-04电石渣特性对新型干法水泥工艺的影响赵洪陈孝灵党剑飞李强成都建筑材料工业设计研究院有限公司,610051摘要利用电石渣生产水泥熟料已成为处理电石渣污染的重要方法。
电石渣的原料特性对整个新型干法生产工艺系统的影响较大,包括电石渣输送、电石渣烘干、生料制备、烧成系统、水泥制成系统工艺控制等,因此新型干法电石渣生产水泥熟料的工艺必须与电石渣的特性相适应。
关键词电石渣水泥熟料工艺影响0引言电石渣是电石法生产聚氯乙烯(polyvinylchloride,简称PVC)过程中电石水解反应的副产物。
随着经济的发展,我国的PVC工业保持着快速增长的势头,生产装置能力不断扩大,装置规模日趋结构合理化.工艺技术水平不断提高。
目前我国生产PVC树脂的原料有70%以上来自电石.因电石法PVC生产的发展,电石渣的排放量也逐渐增多,给环境带来的压力日益加剧。
将电石渣用于制水泥是大量处理电石渣的有效途径,但电石渣的特性对水泥生产过程有较大的影响,怎样针对这些特性合理有效地配置水泥生产系统是此项技术的关键,电石渣特性对新型干法电石渣制水泥工艺的影响研究也是解决水泥生产应用的课题之一。
1电石渣特性1.1电石渣的基本特性电石渣的特性与电石法乙炔的生产过程、电石的性质、生产电石的石灰石质量、生产电石所使用的焦炭质量等诸多因素有关。
其主要特性包括:电石渣的脱水性能,电石渣的粒度。
电石渣的储存输送性能,电石渣粉体的容重、真密度。
电石渣的热性能,电石渣的化学性能(包括主要化学成分、电石渣中氯、硫、碱等有害元素的含量、有刺激性气体的释放、水蒸汽的影响),电石渣的烧结性能等。
氯在水泥生产和使用中的影响
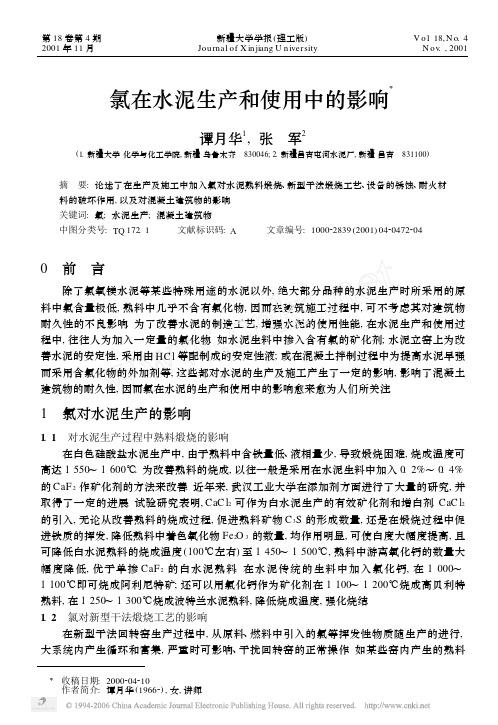
1. 1 对水泥生产过程中熟料煅烧的影响 在白色硅酸盐水泥生产中, 由于熟料中含铁量低、液相量少, 导致煅烧困难, 烧成温度可
高达 1 550~ 1 600℃. 为改善熟料的烧成, 以往一般是采用在水泥生料中加入 0. 2%~ 0. 4% 的 CaF 2 作矿化剂的方法来改善. 近年来, 武汉工业大学在添加剂方面进行了大量的研究, 并 取得了一定的进展. 试验研究表明, CaC l2 可作为白水泥生产的有效矿化剂和增白剂. CaC l2 的引入, 无论从改善熟料的烧成过程, 促进熟料矿物 C3S 的形成数量, 还是在煅烧过程中促 进铁质的挥发, 降低熟料中着色氧化物 Fe2O 3 的数量, 均作用明显, 可使白度大幅度提高, 且 可降低白水泥熟料的烧成温度 (100℃左右) 至 1 450~ 1 500℃, 熟料中游离氧化钙的数量大 幅度降低, 优于单掺 CaF2 的白水泥熟料. 在水泥传统的生料中加入氯化钙, 在 1 000~ 1 100℃即可烧成阿利尼特矿; 还可以用氯化钙作为矿化剂在 1 100~ 1 200℃烧成高贝利特 熟料, 在 1 250~ 1 300℃烧成波特兰水泥熟料, 降低烧成温度, 强化烧结. 1. 2 氯对新型干法煅烧工艺的影响
473
结大块现象, 严重地影响生产的正常运行; 在预热系统内物料产生不同程度的结皮, 导致系 统的堵塞, 严重时需停窑处理. 因此, 窑尾预热干法生产中通常要求原、燃料中氯、碱、硫含量
应控制在比较安全的含量以下, 同时采取一定的防止结皮的措施, 以保证回转窑系统的长 期、安全运转. 不同水泥设备制造公司生产的设备对生料中氯含量均有不同的限定范围, 见
3 结束语
水泥工业生产中, 无论在原料、燃料中引入的, 还是在生产过程中由矿化物引入的氯, 不 可避免地影响熟料的煅烧过程及熟料的质量; 同时, 气态的氯化物在水泥窑内挥发和富集必 然会损伤窑内耐火材料、筒体以及其它的钢铁设备; 在工程施工中, 适当时可提高混凝土的 早强, 但过多则会产生不利的影响, 使钢筋发生锈蚀, 导致结构破坏. 因此, 无论是在生产中 原料、燃料引入的, 还是人为添加的, 或者作为混凝土外加剂加入的, 都有其有益的一面, 也 有其不利的一面, 必须按照有关技术规范规定添加, 以确保水泥生产、建筑物的耐久及安全.
- 1、下载文档前请自行甄别文档内容的完整性,平台不提供额外的编辑、内容补充、找答案等附加服务。
- 2、"仅部分预览"的文档,不可在线预览部分如存在完整性等问题,可反馈申请退款(可完整预览的文档不适用该条件!)。
- 3、如文档侵犯您的权益,请联系客服反馈,我们会尽快为您处理(人工客服工作时间:9:00-18:30)。
电石渣中氯离子对水泥窑生产的影响的报告我公司从5月份起,频繁出现预热器堵塞事故,针对这种情况,公司组织技术人员进行分析,从原材料和操作多方面进行分析研究,发现造成预热器频繁堵塞主要原因是生料中氯离子严重超过行业内控制范围,针对生料中氯离子来源做调查,发现主要是电石渣带来的。
利用电石渣生产水泥,需要严格控制电石渣中氯离子含量,大量研究结果表明,原料中过高的氯离子含量会严重影响预分解窑的稳定生产,其主要表现为预热器系统的频繁堵料,窑尾烟室结皮堵塞,甚至下料溜筒结皮,窑内长厚窑皮,结圈等,经过长期试验和生产经验,水泥窑生产中生料的氯离子含量要小于0.015%到0.020%,如果超过0.020%就会容易出现预热器堵塞,大连小野田公司和山西新绛威顿水泥都遇到该种情况,其生料氯离子含量在0.020%到0.025%。
目前我公司就面临这个问题,由于电石渣中的氯离子含量严重超过设计院给定指标0.03%,导致生料中氯离子也超过0.015%到0.020%多倍,导致目前预热器频繁出现堵塞,严重影响生产线的运行。
对于5月份到目前的数据进行统计如下:
表一我公司5月份进厂电石渣中氯离子含量
表二5月份预热器堵塞情况
表三我公司6月份12日进厂电石渣中氯离子含量
表四预热器堵塞及堵塞物料氯离子含量
由于原材料电石渣带入的氯离子过高,再生产过程又出现富集,
造成入窑生料的氯离子含量比行业内控制要求都高很多,具体如下:表五入窑生料氯离子含量
国外部分重要水泥设计和水泥公司对生料中氯离子有害成分含量的规定
生料中的氯离子在预热器中与碱形成氯化碱,氯化碱的熔点低,最低熔点在650到700度,其以熔融态粘附在物料表面形成液相粘膜,
并与生料和飞灰一起构成粘聚物质,阻碍生料的颗粒流动,从而使物料在预热器中流动不畅和粘附性结皮堵塞。
并且氯化碱沸点低,挥发率高,再次富集的浓度高,从而导致氯化碱和碱的大量循环富集,成为了预热器粘结性结皮堵塞的矿化剂和促进剂。