中厚板铸机动态轻压下控制系统优化
宝钢厚板轧机压下控制系统的分析与改进研究

分类号密级UDC学位论文宝钢厚板轧机压下控制系统的分析与改进研究作者姓名:汪鎏指导教师:李鸿儒教授东北大学自动化研究所副导师:李关定高级工程师宝钢股份能环部申请学位级别:硕士学科类别:专业学位学科专业名称:控制工程论文提交日期:2011年5月论文答辩日期:2011年6月学位授予日期:2011年7月答辩委员会主席:高宪文评阅人:孙克忠钱晓龙东北大学2011年5月A Thesis in Control EngineeringThe Analysis and Improvement of Screw down System of Baosteel5m Finishing millby Wang LiuSupervisor:Professor Li HongruVice Supervisor:Senior Engineer Li GuandingNortheastern UniversityMay2011独创性声明本人声明,所呈交的学位论文是在导师的指导下完成的。
论文中取得的研究成果除加以标注和致谢的地方外,不包含其他人已经发表或撰写过的研究成果,也不包括本人为获得其他学位而使用过的材料。
与我一同工作的同志对本研究所做的任何贡献均已在论文中作了明确的说明并表示诚挚的谢意。
学位论文作者签名:日期:学位论文版权使用授权书本学位论文作者和指导教师完全了解东北大学有关保留、使用学位论文的规定:即学校有权保留并向国家有关部门或机构送交论文的复印件和磁盘,允许论文被查阅和借阅。
本人同意东北大学可以将学位论文的全部或部分内容编入有关数据库进行检索、交流。
作者和导师同意网上交流的时间为作者获得学位后:半年□一年□一年半□两年□学位论文作者签名:导师签名:签字日期:签字日期:宝钢厚板轧机压下控制系统的分析与改进研究摘要宝钢5m厚板轧机是国内的第一套特宽幅现代化厚板轧机,机械供应商为德国西马克公司,电气供应商是德国西门子公司,于2005年3月全面投入生产。
轧钢工程中板厚液压自动控制系统的思考
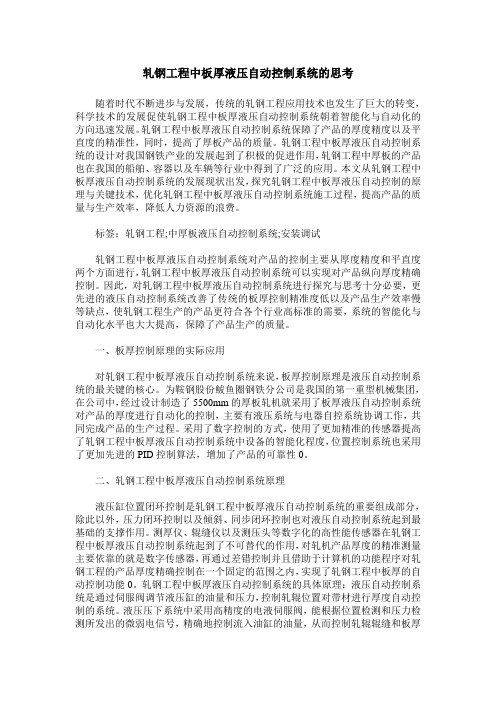
轧钢工程中板厚液压自动控制系统的思考随着时代不断进步与发展,传统的轧钢工程应用技术也发生了巨大的转变,科学技术的发展促使轧钢工程中板厚液压自动控制系统朝着智能化与自动化的方向迅速发展。
轧钢工程中板厚液压自动控制系统保障了产品的厚度精度以及平直度的精准性,同时,提高了厚板产品的质量。
轧钢工程中板厚液压自动控制系统的设计对我国钢铁产业的发展起到了积极的促进作用,轧钢工程中厚板的产品也在我国的船舶、容器以及车辆等行业中得到了广泛的应用。
本文从轧钢工程中板厚液压自动控制系统的发展现状出发,探究轧钢工程中板厚液压自动控制的原理与关键技术,优化轧钢工程中板厚液压自动控制系统施工过程,提高产品的质量与生产效率,降低人力资源的浪费。
标签:轧钢工程;中厚板液压自动控制系统;安装调试轧钢工程中板厚液压自动控制系统对产品的控制主要从厚度精度和平直度两个方面进行,轧钢工程中板厚液压自动控制系统可以实现对产品纵向厚度精确控制。
因此,对轧钢工程中板厚液压自动控制系统进行探究与思考十分必要,更先进的液压自动控制系统改善了传统的板厚控制精准度低以及产品生产效率慢等缺点,使轧钢工程生产的产品更符合各个行业高标准的需要,系统的智能化与自动化水平也大大提高,保障了产品生产的质量。
一、板厚控制原理的实际应用对轧钢工程中板厚液压自动控制系统来说,板厚控制原理是液压自动控制系统的最关键的核心。
为鞍钢股份鲅鱼圈钢铁分公司是我国的第一重型机械集团,在公司中,经过设计制造了5500mm的厚板轧机就采用了板厚液压自动控制系统对产品的厚度进行自动化的控制,主要有液压系统与电器自控系统协调工作,共同完成产品的生产过程。
采用了数字控制的方式,使用了更加精准的传感器提高了轧钢工程中板厚液压自动控制系统中设备的智能化程度,位置控制系统也采用了更加先进的PID控制算法,增加了产品的可靠性0。
二、轧钢工程中板厚液压自动控制系统原理液压缸位置闭环控制是轧钢工程中板厚液压自动控制系统的重要组成部分,除此以外,压力闭环控制以及倾斜、同步闭环控制也对液压自动控制系统起到最基础的支撑作用。
包钢宽厚板连铸机动态轻压下控制系统研究与设计

2 . 5 考生考试模块。进入学生考试页面,选择考试科 目,开始 考 试并 且开 始 计时 。 3 系统 实现
本 系统 主 要 采 用 三 层B / S 体 系 结构 模 型 。主 要 以AS P . N E T 为开发平 台,s Q L S e r v e r 为后 台数据库 ,采用We b 流 行的B r o w s e r / S e r v e r /  ̄式,完成核心系统的构建 整个系统 分 为 三层 构 架 :用户 层 ( 外 观表 示 层 )一一 应 用层/ 业 务逻 辑层一一数据服务层 。测试期间使用一台服务器实现所有 功 能 ,正 式 运 行期 间 ,可 以分 为We b 服 务 器和 D a t a b a s e 数 据 服 务器 , 以减 轻服 务器 的 负担 ,提 高执 行速 度 。 3 . 1 用 户 界 面层 。用户 界 面层 位 于客 户 端 ,相 当 于用 户 界 面 , ̄ P I n t e r n e t E x p l o r e 等We b 浏览 器 。实现 在客 户 端浏 览器 中显 示 的用 户 界面 ,该 层可 以调用 由业务 逻 辑 层提 供 的业 务 方法 。
参考 文献 :
本 系 统 是 根 据 宁 波 数 字 图 书 馆 多 媒 体 技 术 网络 课 程 考 试 管理 的实 际 需求进 行 设计 和 开发 的 ,设计 内容 切 合实 际 , 又很 大 的 实 用 价 值 。总 的来 说 , 本 系 统 设 计 使 用 方 便 ,便 于维 护 ,对 于管理 者来 说是 较 好 的管理 工具 。
[ 1 】 谭汉松, 侯水英. 基于局域网的通用考试 系统的设计开发 … . 中南工业大学学报, 2 0 0 0 ( 0 4 ) . . 【 2 ] 叶晓彤. 基于校 园网的分布式考试 系统模 式设计 [ J 】 . 山西师范大学学报 ( 自然科学版) , 2 0 0 3 ( 0 2 ) : 2 0 - 2 5 . [ 3 】 刘铸, 王丽娜, 董晓梅. N I T 网络化考试 阅卷系统设计与实现 [ J ] . 控制工程, 2 0 0 4 ( 0 2 ) : 1 0 8 — 1 1 O . 【 4 】 陈名松, 曾凡峰, 熊伟成. 计算机网络考试分析系统的设计与实现 [ J ] . 广西师范大学学报 ( 自然科学版) , 2 0 0 0 ( 0 4 ) : 5 2 - 5 5
中厚板连铸坯内部质量改进与提升

关键词 : 连铸机 ; 中心偏析 ; 开 口度 ; 轻压下模型
中 图分 类 号 : T F 7 7 7 . 1 文献标识码 : A
I n S l a b Co n t i n u o u s Ca s t i n g B i l l e t I n t e r n a l Qu a l i t y
p l a n t o f J i n a n I r o n a n d S t e e l i s u n s t a b l e wi t h s e i r o u s s e g r e g a t i o n i n t h e c e n t e r ,wh i c h a f f e c t s t h e q u a l i  ̄ o f r o l l i n g . T h e i n t e r -
第3 9卷第 6期
2 0 1 7年 l 2月 甘来自肃冶金
V o 1 . 3 9 N o . 6
De c . , 2 01 7
GANS U METALLURGY
文章编号 : 1 6 7 2 — 4 4 6 1 ( 2 0 1 7 ) 0 6 — 0 0 2 7 — 0 2
中厚 板 连 铸 坯 内部 质 量 改 进 与 提 升
I mp r o v e me n t a n d I mp r o v e
ZHANG L i — b i a o
( S h a n d o n g I r o n a n d S t e e l G r o u p J i n a n B r a n c h ,J i n a n 2 5 0 1 0 1 , C h i n a )
p i p e l i n e s a n d o t h e r s ,a n d c r e a t i n g g o o d e c o n o mi c a n d s o c i a l b e n e f i t s .
动态二冷水与轻压下资料

动态二冷水与轻压下技术在中厚板铸机上的应用实践李超二冷水量对铸坯质量有重大影响,而大多数模型都是离线的,即采用水表方法,不能对工艺过程变化响应,因此影响质量。
DYNCOOL是在不同铸造条件下动态控制二冷水,从而获得理想铸流表面温度分布,以保证不出现有缺陷的产品。
它应用在线数据,实时计算铸流表面温度分布、铸坯壳厚度和每段二冷水流量,使目标温度分布和计算所得温度分布之间差别最小。
模型用边界条件法解辐射和对流方程式来计算通过铸流中部纵断面的温度场,这些方程式的近似数值是用有限空间法和时间有限差分法进行运算的。
在所开发的热传导模型能用于工业计算以前,必须得出每个冷却区的冷却参数与热传导系数之间的关系,为了确定热传导系数,开发了一个两维程序,在热传导系数计算中,采用辐射和对流方程式,并做了各种稳态铸造参数的仿真,用这些仿真导出每段二冷区的水流量Q与热传导系数H的关系式:H=a×Qb式中a和b为系数。
程序的材料数据由用户或IDS模型给出,后者计算作为钢成分和冷却速度函数的相变温度和其他物理参数。
为执行上述实时仿真和各种计算,并保证精度和计算时间,使用大型计算机太昂贵,本系统使用带两个协处理器的微型计算机,并行地进行仿真和从自动化系统传送数据。
DYNCOOL模型在实际应用中获得了良好效果,与过去常规模型相比,它能在各种铸造条件下,使铸坯表面温度均保持稳定、钢坯的质量更好并减少板坯清理的损耗。
1994年要清理的板坯降低了30%,与1985年相比,降低了板坯缺陷,使冷轧品种报废率由1%降低到0.13%,对热轧板则由2.4%降低到0.4%。
动态二冷水控制(DYNACS):与钢种、钢水温度、拉速等因素相匹配的动态二冷水控制模型对ASTC和无缺陷铸坯的生产至关重要。
通过动态计算铸坯凝固末端并快速调节扇形段辊缝锥度来实现液芯软压下,以改善中心偏析,提高铸坯内部质量。
铸流导向系统罗德洛基的6号连铸机是世界上第一套装备了由15个SMART○R扇形段组成的全动态铸流导向系统的板坯连铸机(图2)。
板坯连铸机动态轻压下过程控制系统的高可用性实现

板坯连铸机动态轻压下过程控制系统的高可用性实现阐述了梅钢2#板坯连铸机动态轻压下过程控制系统的高可用性架构过程,提出了一种软件故障自主恢复与硬件热备冗余相结合的高可用性系统架构方案,并结合实际生产过程分析了备机切换过程中检查点数据的可用性,最后给出了系统故障测试结果。
实际说明,系统投产以后运行稳定,到达了预期目标。
连铸过程对连铸坯实施轻压下操作是消除中心偏析、提高连铸坯内部质量的有效手段。
在着力开发此技术的工艺控制核心模型的同时,控制系统的稳定性和安全性问题也显得尤为重要。
针对连铸生产过程的实时性和连续性,在****集团梅山钢铁股份公司2#连铸机动态轻压下过程控制系统开发过程中,通过高可用性架构,将系统故障时间控制在lh∕a 内。
在系统硬件架构方面采用两台服务器和磁盘阵列柜建立双机热备系统;软件架构方面利用系统管理模块,对系统开展监控和管理,增加了软件本身的自主恢复能力。
1系统的高可用性架构动态轻压下过程控制系统采用双节点群集模式架构:当系统工作时,工作节点对外提供服务,备用节点监控工作节点运行情况,不参与对外服务。
当工作节点出现异常时,备用节点主动接收工作机的工作,继续对外提供服务,从而保证系统的不间断运行。
原来的工作节点开展故障处理后,根据预先设定的配置命令以人工或自动的方式切回系统,经过与当前工作节点数据同步后,以备用节点身份继续运行,与工作节点开展心跳信息交互。
系统的硬件架构见图1,由两台配置一样的IBMXSerieS 346服务器构成群集服务节点。
节点间通过千兆以太网心跳线直连,传递心跳信息互相检测。
两台服务器在本地磁盘上各自运行操作系统(Windows Sever 20**),用户文件和数据保存在独立于节点之外的IBMDS400磁盘阵列柜中。
此外, 服务器磁盘子系统和DS400内磁盘阵列均按RAID 5方式架构,保证了数据存储的安全性。
二冷水量设定值采用平均拉速控制,平均拉速计算方法为:将二冷区内各跟踪单元的“坯龄”相加,除以该区中间位置距结晶器液面的距离。
韶钢中板厂厚控系统存在的问题及改进措施

韶钢中板厂厚控系统存在的问题及改进措施随着技术的日新月异,工业自动化技术的飞速发展,对于厂家的要求也越来越高,控制技术的发展也变得复杂。
韶钢中板厂也不例外,厚度控制是中板厂控制的重要环节,其厚度控制系统显得至关重要。
本文将探讨韶钢中板厂厚度控制系统存在的问题及改进措施。
首先介绍韶钢中板厂厚度控制系统的构成及原理。
厚度控制系统是一个由计算机、传感器、减速机、电动执行机构和控制系统组成的机械-电子系统,其原理是通过检测滚轧机轧制薄板的厚度,将检测出来的数据传输到控制系统,然后控制系统按照设定的参数,控制减速机和电动执行机构,调节滚轧机变动压力,实现对厚度的控制。
在实际运行中,韶钢中板厂厚度控制系统存在一些问题,主要表现在以下几个方面:首先是技术实现的问题。
由于韶钢中板厂厚度控制系统采用的是传统的电气控制方案,缺少现代计算机技术的应用,尤其是在数据采集和计算处理方面,存在一定的技术滞后问题,不能有效的检测厚度,控制准确度不高。
其次,传感器精度不高的问题。
由于韶钢中板厂采用的传感器技术较为老旧,精度较低,无法提供精确的数据,以致厚度控制精度较低。
最后是设备老化的问题。
由于厚度控制系统的设备本身质量不高,容易老化,使用寿命短,导致实际控制精度低,有时甚至无法正常运行。
为了解决这些问题,应采取以下措施:首先,加强技术改造。
韶钢中板厂应改进传统的控制系统,采用现代的非接触式数据采集和计算处理技术,以提高控制精度和提高效率。
其次,改进传感器精度。
韶钢中板厂应采用更新更精准的传感器,以提高厚度检测的精度。
最后,保养维护设备。
韶钢中板厂应定期为厚度控制系统设备进行保养和维护,更换老化的部件,以延长其使用寿命,提高系统的可靠性。
综上所述,韶钢中板厂厚度控制系统存在一些问题,主要表现在技术滞后、传感器精度较低以及设备易老化等方面。
为此,采取加强技术改造、升级传感器精度以及定期保养维护设备等措施,有助于提高厚度控制系统的可靠性,提高控制精度,实现高效生产。
中厚板热处理炉自动控制系统优化研究

科技与创新┃Science and Technology&Innovation2020年第19期文章编号:2095-6835(2020)19-0062-02中厚板热处理炉自动控制系统优化研究武秀琪(广东松山职业技术学院,广东韶关512100)摘要:中厚板是指厚度为5~120mm的各类钢板,其生产水平是衡量一个国家钢铁工业水平的标志之一。
随着行业的调整和产业结构的提高,对高等级、高强度、高附加值的中厚钢板的需求变得与日俱增。
这些高等级钢板来源于热处理炉对钢板进行的二次加热处理,通过将钢板加热到预定的温度并保持一定的时间后,控制钢板的冷却速度,使钢板内部的结构组织发生物理和化学的变化,来改善钢板的性能,从而生产出不同种类的高附加值钢板。
而对加热炉过程自动控制技术的优化研究可以大大改善中厚板产品质量,丰富生产品种。
关键词:中厚板;自动控制;冷却控制;械加工业中图分类号:TG155.1文献标志码:A DOI:10.15913/ki.kjycx.2020.19.0231背景分析目前,中国钢铁工业虽然已经实现了量的突破,但是对于重点工程急需的优质、高附加值钢材依然依赖进口。
因此,现阶段中国处于从钢铁大国向钢铁强国过渡的关键时期[1],重点在于提高钢铁工业的生产水平、技术装备水平、管理水平。
中厚板是指厚度为5~120mm的各类钢板,其生产水平是衡量一个国家钢铁工业水平的标志之一。
在造船业、机械加工业、石油化工、桥梁建筑等行业方面中厚板都发挥着举足轻重的作用。
但是随着行业的调整和产业结构的提升,普通钢板已经难以满足日益增长的工业发展需求,而对高等级、高强度、高附加值的中厚钢板的需求变得与日俱增[2],比如性能均匀的高强度船板、海上石油平台用板、大跨度公路和铁路两用的桥梁板、高强度低焊接裂纹的低温压力容器板、高强度的石油储罐用钢以及用于国防业的军工钢等都是有着非常广阔的市场空间。
这些高等级钢板来源于热处理炉对钢板进行的二次加热处理,通过将钢板加热到预定的温度并保持一定的时间后,控制钢板的冷却速度,使钢板内部的结构组织发生物理和化学的变化,从而改善钢板的性能,生产出不同种类的高附加值钢板[3]。
- 1、下载文档前请自行甄别文档内容的完整性,平台不提供额外的编辑、内容补充、找答案等附加服务。
- 2、"仅部分预览"的文档,不可在线预览部分如存在完整性等问题,可反馈申请退款(可完整预览的文档不适用该条件!)。
- 3、如文档侵犯您的权益,请联系客服反馈,我们会尽快为您处理(人工客服工作时间:9:00-18:30)。
中厚板铸机动态轻压下控制系统优化
摘要:介绍了中厚坯连铸过程中的液芯压下位置反馈的控制优化,通过增加压力反馈调节系统,实现液芯位置的在线跟踪控制。
关键词:液芯压下计算方法控制系统优化
Abstract:It is described that the control optimization on position feedback of LCR (Liquid Core Reduction) during casting with heavy plate.By means of adding up the control system with force feedback it is realized the online tracking control on position with LC (Liquid Core).
Key Words:Liquid Core Reduction;Calculation Methon;Control System Optimization
包钢薄板厂宽厚板生产线于2007年10月投产,为了提高板坯质量在扇形段采用了动态轻压下技术,动态轻压下技术是根据不同的钢种、钢水温度、连铸机拉速、二冷水的冷却模型以及板坯内部液芯的位置来控制扇形段的压下量。
[1]生产过程中发现宽厚板铸机的动态轻压控制是根据铸机拉速来控制,当铸机拉速发生改变时,轻压下的位置便根据模型设定发生改变,由于没有考虑铸坯的液芯的位置的动态变化,因此,在拉速发生变化时轻压下的压下位置并不合适,这对铸坯的质量有影响。
通过修改轻压下控制程序,引入液芯位置的动态判断,实现板坯铸机动态轻压下的优化。
通过合理的液芯轻压下不仅能解决连铸与连轧之间的厚度匹配问题,而且能细化铸坯内部组织,进一步减
轻铸坯中心偏析,这对于板坯连铸生产的产品尤为重要。
动态轻压下功能用一组铸流扇形段辊缝是动态计算的来控制板坯的先后顺序。
此计算是基于从过程控制系统下载的压下路径和最终位置,以及由板坯凝固模型计算的液芯长度。
一个闭路PID功能用于比较实际位置与要求的位置,并为控制辊子位置的伺服阀生成一个基准数。
辊子的所有打开和关闭程序是由板坯的“跟踪”功能在浇铸的过程中检查和控制的。
扇形段辊缝通过HMI控制系统设定。
轻压下区域内压下量(减少辊缝设定值)应设定为0.8~1.0 mm/导向段(米)(实际的数值由软件计算)。
设计时考虑扇形段的软压下速度为1.5 mm/m。
辊子几何形状内的软压下区域位置根据拉速和钢种由铸坯的凝固程度确定的。
根据DDDL经验和采用软压下的钢厂的经验,对于所有钢种,软压下区域最佳的起始位置与凝固系数Fs=0.3/0.4和Fs=0.7/0.8有关。
必须考虑不同的钢种要求、中间包过热度、二次冷却和辊间距等因素,以便根据上述要求对软压下参数进行调节来获取最优化的质量。
为了满足3种不同厚度的要求,在扇形4-17段采用轻压下。
根据不同的钢种、厚度和拉速,带软压下(基于软压下速度1 mm/m)的辊缝缩小量应为4 mm(2个扇形段)-6 mm(3个扇形段)。
如图1。
DANIELI公司的动态轻压下采用液态溶池控制系统的数学模型,通过连续计算铸流液芯端部的实际位置来完成的。
为了满足不同拉速的生产要求,在铸流中的不同位置上采用轻压下。
在轻压下区的辊缝是通过4个液压缸驱动的扇形段支架的自动调节而确定的。
每个液压缸的动作通过线性变送器和伺服阀控制(如图2)。
通过对驱动力和位置进行控制而确定辊缝的大小。
并根据液压系统上安装的压力传感器给出的测量信号可以确定液芯的端部位置。
在现场工作实践中发现,当生产拉速调节变化频繁时,模型计算的液芯位置与实际液芯位置发生偏移,轻压下的位置不合适,影响铸坯的质量。
在实际生产过程中液压缸的调节包括压力调节和位置调节,位置调节主要依据于液压缸中的位置传感器的反馈进行调节,压力调节主要依据于液压缸中的两个压强传感器的反馈进行调节。
[2]
我们考虑改进程序中液芯端部的实际位置的计算方法,通过在液压缸管路顶部的压力传感器反馈的压力值来优化拉速调节变化频繁时,液芯实际位置的计算。
当6#扇形段压力传感器反馈的压力值小于102 BAR时,我们认为液芯位置是在这段扇型段内,通过实际压力和设定最大压的比较,校准模型计算的液芯位置。
我们自主设计一种基于压力反馈的动态辊缝调节系统,利用入口两侧液压缸与出口两侧液压缸压力值计算平均压力,同一个基准压力范围进行比较,小于这个压力范围就增加一定的压下量;大于这个压力范围就减小一定的压下量(模型计算方式如图3)。
动态辊缝调节系统已经在6#到9#扇形段进行实践,完全能够校准模型计算的液芯位置,实现液芯位置的实际跟踪控制,
提高了产品的质量。
中厚板坯动态液芯压下的控制系统优化,在提高产品质量、降低成本方面有明显的改善效果,而且它可以调节中厚板坯连铸机之间的厚度匹配,进一步改善铸坯的内部质量和组织缺陷。
参考文献
[1] 孟庆辉,李秉强.薄板坯连铸机动态软压下控制技术的分析
[C]//薄板坯连铸连轧协会论文集.2006.
[2] 柳万鹏.浅谈动态软压下技术在板坯连铸的应用[C]//全国第十四届自动化应用学术交流会暨中国计量学会冶金分会2009年会论文集.2009.。