铝型材加工工艺及技术方案
(工艺技术)铝材加工工艺
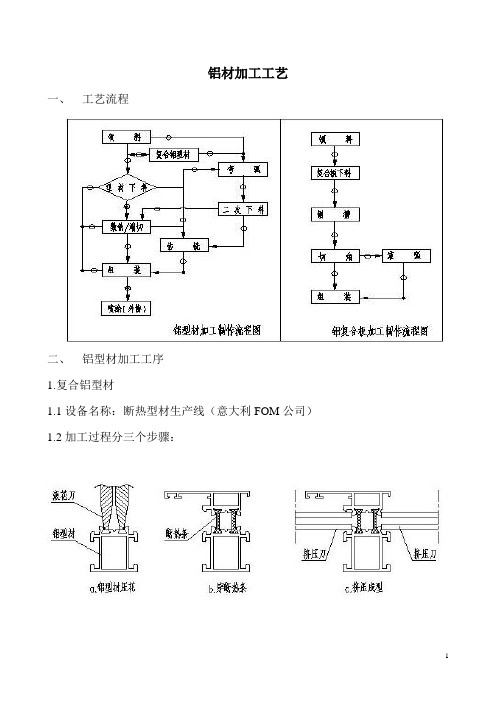
铝材加工工艺一、工艺流程二、铝型材加工工序1.复合铝型材1.1设备名称:断热型材生产线(意大利FOM公司)1.2加工过程分三个步骤:a.型材压花:用滚花刀在铝型材槽口上压花。
b.穿断热条:将断热条穿在已压花的铝型材槽口内。
c.挤压成型:将铝型材和断热条用挤压刀复合后在一起。
1.3检验1.3.1检验设备:抗剪实验机1.3.2取样:在距型材端头200mm以外取样L=100mm。
1.3.3标准:剪切力H(Kg)符合250≤H≤6001.4注意事项:1.4.1铝型材截面尺寸:宽240mm,高180mm。
1.4.2挤压刀具有效尺寸:60mm,即铝型材外端距挤压部位尺寸L<60mm。
1.4.3铝型材不能与刀具干涉,一般挤压部位应高出2mm。
2.铝型材下料2.1设备:双头锯型号:DG244适用范围:加工长度335~6000 加工角度90°~45°任意角调整范围:锯片调整角度90°~45°工作台调整角度22.5°~90°~140°加工精度:尺寸允差±0.2 角度允差±6′其他:锯片最大直径φ550 锯片升起最大高度200主要用途:铝型材切断、切角。
2.2设备:单头锯型号:MGS205适用范围:加工长度15~450 加工角度90°~45°任意角调整范围:锯片调整角度90°~45°工作台调整角度22.5°~90°~140°加工精度:尺寸允差±0.5 角度允差±15′其他:锯片最大直径φ550 锯片升起最大高度200主要用途:铝型材切断、切角。
2.3设备:单头自动送料切割机型号:SA142适用范围:加工长度5.5~150加工精度:尺寸允差±0.3主要用途:铝型材切断(自动送料、切料)。
3.铝型材端切3.1设备:端铣机型号:AKS134适用范围:最大切削高度160;最大切削深度135;最大切削长度250。
铝型材生产过程及工艺
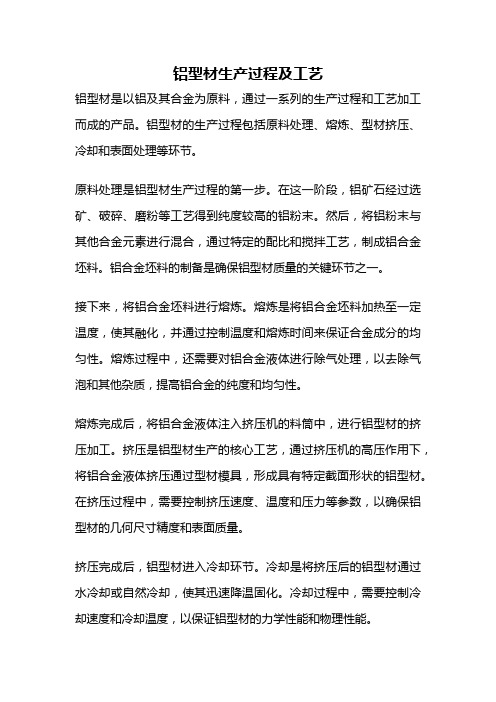
铝型材生产过程及工艺铝型材是以铝及其合金为原料,通过一系列的生产过程和工艺加工而成的产品。
铝型材的生产过程包括原料处理、熔炼、型材挤压、冷却和表面处理等环节。
原料处理是铝型材生产过程的第一步。
在这一阶段,铝矿石经过选矿、破碎、磨粉等工艺得到纯度较高的铝粉末。
然后,将铝粉末与其他合金元素进行混合,通过特定的配比和搅拌工艺,制成铝合金坯料。
铝合金坯料的制备是确保铝型材质量的关键环节之一。
接下来,将铝合金坯料进行熔炼。
熔炼是将铝合金坯料加热至一定温度,使其融化,并通过控制温度和熔炼时间来保证合金成分的均匀性。
熔炼过程中,还需要对铝合金液体进行除气处理,以去除气泡和其他杂质,提高铝合金的纯度和均匀性。
熔炼完成后,将铝合金液体注入挤压机的料筒中,进行铝型材的挤压加工。
挤压是铝型材生产的核心工艺,通过挤压机的高压作用下,将铝合金液体挤压通过型材模具,形成具有特定截面形状的铝型材。
在挤压过程中,需要控制挤压速度、温度和压力等参数,以确保铝型材的几何尺寸精度和表面质量。
挤压完成后,铝型材进入冷却环节。
冷却是将挤压后的铝型材通过水冷却或自然冷却,使其迅速降温固化。
冷却过程中,需要控制冷却速度和冷却温度,以保证铝型材的力学性能和物理性能。
对铝型材进行表面处理。
表面处理是为了提高铝型材的耐腐蚀性、抗氧化性和装饰性,常见的表面处理方法包括阳极氧化、电泳涂装、喷涂和机械抛光等。
表面处理过程中,需要控制处理时间、温度和涂层厚度等参数,以获得符合要求的表面效果。
铝型材的生产过程包括原料处理、熔炼、型材挤压、冷却和表面处理等环节。
每个环节都需要严格控制工艺参数,以确保铝型材的质量和性能。
铝型材作为一种重要的建筑材料和工业材料,广泛应用于建筑、交通运输、电子电器、机械制造等领域,为社会的发展和进步做出了重要贡献。
某铝业工厂加工技术及工艺知识

某铝业工厂加工技术及工艺知识1. 简介某铝业工厂是一家专注于铝材加工的企业,具有多年的生产经验和技术实力。
本篇文档将介绍该工厂的加工技术和工艺知识。
2. 铝材加工技术2.1 切割技术在某铝业工厂,常用的铝材切割技术有以下几种:•玻璃纤维刀片切割:适用于切割薄壁铝材,切割表面光滑,尺寸精准。
•钢锯刀片切割:适用于切割厚壁铝材,切割速度快,适用于大批量生产。
•激光切割:适用于复杂形状的铝材切割,切割精度高,但成本较高。
2.2 折弯技术某铝业工厂常用的铝材折弯技术有以下几种:•机械折弯:通过机械设备对铝材进行顶弯、座弯等加工,具有成本低、效率高的特点。
•液压折弯:利用液压系统对铝材进行弯曲,适用于大型和重型铝材的折弯。
•电子折弯:通过电脑控制的折弯设备对铝材进行精确的弯曲加工。
2.3 排孔技术对于需要进行排孔的铝材,某铝业工厂采用以下技术:•冲孔:通过冲压设备对铝材进行孔洞加工,成本低、效率高。
•钻孔:通过钻床对铝材进行孔洞加工,适用于特殊形状的排孔需求。
•激光排孔:采用激光设备对铝材进行孔洞加工,精度高,但成本较高。
3. 铝材加工工艺知识3.1 清洁与预处理在进行铝材加工前,必须对铝材进行清洁和预处理,以确保其表面干净、无油污和氧化物。
常用的清洁方法有:•清洗:使用清洗剂和刷子等工具将铝材表面的污垢和油污清洗干净。
•水洗:将铝材浸入清水中,以去除表面的杂质。
•酸洗:使用酸性溶液对铝材进行浸泡清洗,以去除氧化物和其他不良物质。
3.2 表面处理为了提高铝材的耐腐蚀性和表面质量,某铝业工厂进行了以下表面处理工艺:•防腐涂层:通过浸涂或喷涂一层具有防腐性能的涂料,防止铝材被腐蚀。
•电泳涂装:将铝材浸泡在含有涂装颜料的水溶液中,利用电解作用使颜料在铝材表面形成一层涂膜。
•阳极氧化:通过电解作用使铝材表面形成一层氧化膜,提高其耐腐蚀性和硬度。
3.3 加工精度控制为了保证铝材加工后的尺寸精确和质量合格,某铝业工厂进行了精度控制的工艺措施:•机械设备调整:对切割、折弯和冲孔等设备进行调试和精确定位,确保加工尺寸准确。
铝型材深加工工艺流程
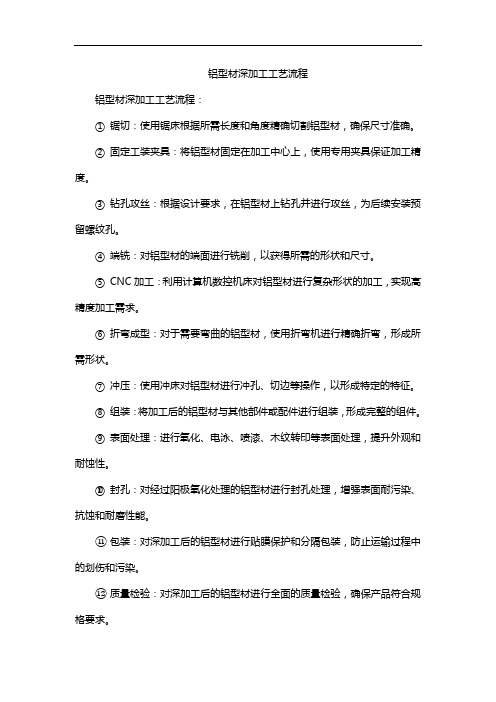
铝型材深加工工艺流程
铝型材深加工工艺流程:
①锯切:使用锯床根据所需长度和角度精确切割铝型材,确保尺寸准确。
②固定工装夹具:将铝型材固定在加工中心上,使用专用夹具保证加工精度。
③钻孔攻丝:根据设计要求,在铝型材上钻孔并进行攻丝,为后续安装预留螺纹孔。
④端铣:对铝型材的端面进行铣削,以获得所需的形状和尺寸。
⑤CNC加工:利用计算机数控机床对铝型材进行复杂形状的加工,实现高精度加工需求。
⑥折弯成型:对于需要弯曲的铝型材,使用折弯机进行精确折弯,形成所需形状。
⑦冲压:使用冲床对铝型材进行冲孔、切边等操作,以形成特定的特征。
⑧组装:将加工后的铝型材与其他部件或配件进行组装,形成完整的组件。
⑨表面处理:进行氧化、电泳、喷漆、木纹转印等表面处理,提升外观和耐蚀性。
⑩封孔:对经过阳极氧化处理的铝型材进行封孔处理,增强表面耐污染、抗蚀和耐磨性能。
⑪包装:对深加工后的铝型材进行贴膜保护和分隔包装,防止运输过程中的划伤和污染。
⑫质量检验:对深加工后的铝型材进行全面的质量检验,确保产品符合规格要求。
铝材加工工艺及技术方案

铝材加工工艺及技术方案1、铝材加工工艺及技术方案铝材各工序加工要领:1.1接单1)接到加工单后,应认真仔细地审单,如单属正常,必须按照单上所规定日期内保质保量完成。
反之,如单出现问题,应及时向生产部反映得以正确处理才能继续加工。
2)加工单的统计、算料有搭配必须与材料部相互配合,事先计划需用材料。
1.2材料领用1)经仔细复核后,确实无误,按材料的规格、型号、数量、颜色的要求,到材料部办理领料手续。
2)未办理领料手续,又未经材料部的允许,不得私自到仓库乱拿材料。
3)原材料领用搬运时,必须按随之渐进的方式,由上至下,避免材料混乱和铝材装饰面划伤现象。
1.3切割1)机械使用前检查,首先打开空气压缩机的排水阀排水,然后打开接电开关和机械开关,让机械空转一段时间检查机械无异常现象,即可准备切割。
2)切割时注意保护铝材装饰面。
3)铝材切割,尺寸误差不能超过Imm。
4)切割后的半成品应堆放整齐,标明需用区域及规格、数量,以便下一道工序的使用。
5)注意切割机的保养,切割机使用时锯片必须经常打油。
6)工作台面必须保持干净,避免切割时的铝屑与铝材磨擦,造成伤痕。
1.4铝材冲孔1)机械使用前应检查机械运转是否正常,接上电源开关让设备空转观察机械确实无异开始下一步的工作。
2)模具安装必须由专业人员安装,安装完毕须检查模具与机械是否配合得当,再进行下一道工序的工作。
3)进行冲孔前必须核实后确实无异开始铝材的冲孔工作。
4)冲孔后的铝材,切口必须是平整、光滑。
5)连续冲料时,应检查上模中的屎料是否退出,模具有没有松动,如有问题必须做好相应措施解决。
6)加工后的成品,堆放必须整齐,周围必须保持清洁。
7)以上程序完成之后,切断电源开关。
1.5包装、过塑1)铝材过塑前检查站过塑机是否正常,如正常首先打开电源开关接通电源,开动风扇及传送带打开,待温度调至180C左右时,方能过塑。
2)铝材包装过塑前,应将表面擦拭干净,热收缩膜套到铝材的两端各超出80mm-IOOmm,不得超出过长,以免造成浪费。
铝型材制造工艺

铝型材制造工艺引言:铝型材是一种常见的金属制品,广泛应用于建筑、交通运输、电子、机械制造等领域。
铝型材制造工艺是指将铝材料通过一系列的加工工艺,制成具有特定形状和尺寸的铝型材的过程。
本文将介绍铝型材制造的主要工艺流程和相关技术。
一、原材料准备:铝型材的制造首先需要准备合适的原材料。
常用的铝合金材料有6061、6063、6082等,这些铝合金具有良好的机械性能和耐腐蚀性能。
在原材料准备阶段,需要对铝材进行切割、锯切等加工,以便后续的加工工艺。
二、型材挤压:型材挤压是铝型材制造的核心工艺。
在挤压过程中,将预热的铝坯料放入挤压机的料筒中,通过挤压机的压力和模具的作用,使铝坯料通过模具的孔口挤出,形成具有特定截面形状的铝型材。
挤压过程中,需要控制好挤压速度、温度和压力等参数,以确保铝型材的质量。
三、热处理:热处理是铝型材制造中的重要工艺环节。
通过热处理可以改善铝合金的力学性能和耐腐蚀性能。
常用的热处理方法有固溶处理和时效处理。
固溶处理是将铝型材加热至一定温度,使合金元素溶解在铝基体中,然后快速冷却,以获得均匀的固溶体。
时效处理是在固溶处理的基础上,将铝型材再次加热至一定温度,保持一段时间,使合金元素析出,形成强化相,提高铝型材的强度和硬度。
四、表面处理:铝型材的表面处理是为了提高其耐腐蚀性和装饰效果。
常用的表面处理方法有阳极氧化、喷涂、电泳涂装等。
阳极氧化是将铝型材浸泡在含有电解质的酸性溶液中,通过电解作用,在铝表面形成一层氧化膜,增加铝型材的耐腐蚀性和表面硬度。
喷涂和电泳涂装是将涂料喷涂或涂覆在铝型材表面,形成一层保护膜,提高铝型材的装饰效果和耐候性。
五、切割和加工:铝型材制造完成后,还需要进行切割和加工,以满足不同的使用要求。
常用的切割方法有锯切、剪切和冲孔等。
加工工艺包括铣削、钻孔、焊接等,可以根据需要对铝型材进行进一步的加工和组装。
六、质量检测:铝型材制造完成后,需要进行质量检测,以确保产品符合相关标准和要求。
铝型材生产工艺流程
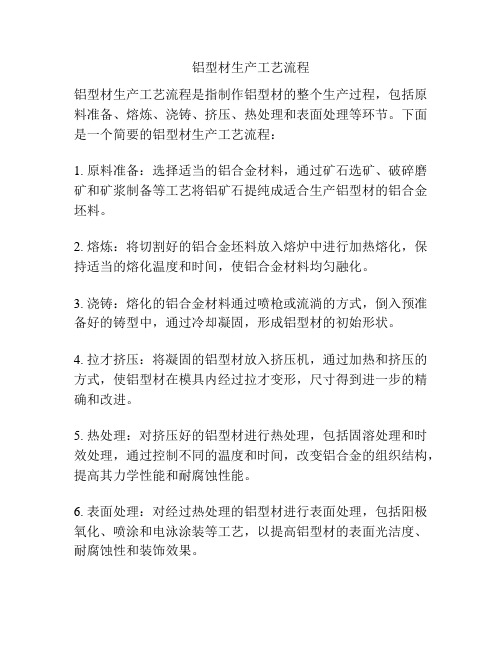
铝型材生产工艺流程
铝型材生产工艺流程是指制作铝型材的整个生产过程,包括原料准备、熔炼、浇铸、挤压、热处理和表面处理等环节。
下面是一个简要的铝型材生产工艺流程:
1. 原料准备:选择适当的铝合金材料,通过矿石选矿、破碎磨矿和矿浆制备等工艺将铝矿石提纯成适合生产铝型材的铝合金坯料。
2. 熔炼:将切割好的铝合金坯料放入熔炉中进行加热熔化,保持适当的熔化温度和时间,使铝合金材料均匀融化。
3. 浇铸:熔化的铝合金材料通过喷枪或流淌的方式,倒入预准备好的铸型中,通过冷却凝固,形成铝型材的初始形状。
4. 拉才挤压:将凝固的铝型材放入挤压机,通过加热和挤压的方式,使铝型材在模具内经过拉才变形,尺寸得到进一步的精确和改进。
5. 热处理:对挤压好的铝型材进行热处理,包括固溶处理和时效处理,通过控制不同的温度和时间,改变铝合金的组织结构,提高其力学性能和耐腐蚀性能。
6. 表面处理:对经过热处理的铝型材进行表面处理,包括阳极氧化、喷涂和电泳涂装等工艺,以提高铝型材的表面光洁度、耐腐蚀性和装饰效果。
7. 产品检验:对生产好的铝型材进行外观质量、尺寸精度、力学性能和耐腐蚀性能等方面的检验,确保产品质量符合要求。
8. 包装和运输:符合质量要求的铝型材经过包装后,安全、准确地进行运输,以满足客户的需求。
以上就是铝型材生产工艺流程的一个简要描述,具体工艺流程可能因不同的铝型材类型和生产厂家而有所不同,但总体步骤相似。
铝型材生产工艺的每个环节都需要严格的控制和操作,以确保产品质量的稳定和可靠。
铝型材加工流程和工艺
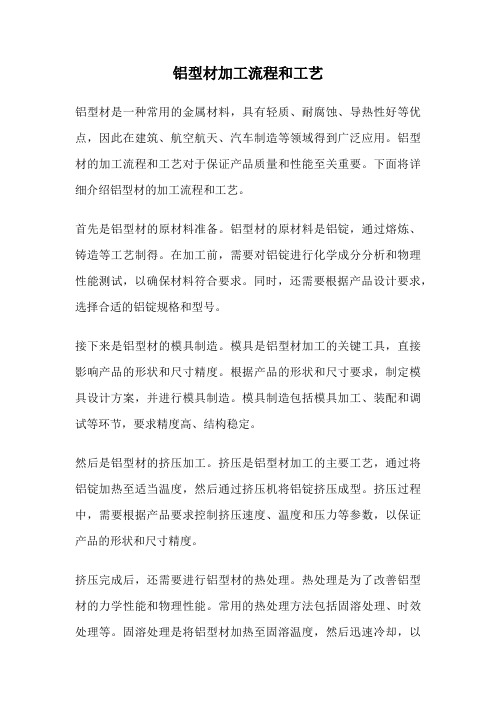
铝型材加工流程和工艺铝型材是一种常用的金属材料,具有轻质、耐腐蚀、导热性好等优点,因此在建筑、航空航天、汽车制造等领域得到广泛应用。
铝型材的加工流程和工艺对于保证产品质量和性能至关重要。
下面将详细介绍铝型材的加工流程和工艺。
首先是铝型材的原材料准备。
铝型材的原材料是铝锭,通过熔炼、铸造等工艺制得。
在加工前,需要对铝锭进行化学成分分析和物理性能测试,以确保材料符合要求。
同时,还需要根据产品设计要求,选择合适的铝锭规格和型号。
接下来是铝型材的模具制造。
模具是铝型材加工的关键工具,直接影响产品的形状和尺寸精度。
根据产品的形状和尺寸要求,制定模具设计方案,并进行模具制造。
模具制造包括模具加工、装配和调试等环节,要求精度高、结构稳定。
然后是铝型材的挤压加工。
挤压是铝型材加工的主要工艺,通过将铝锭加热至适当温度,然后通过挤压机将铝锭挤压成型。
挤压过程中,需要根据产品要求控制挤压速度、温度和压力等参数,以保证产品的形状和尺寸精度。
挤压完成后,还需要进行铝型材的热处理。
热处理是为了改善铝型材的力学性能和物理性能。
常用的热处理方法包括固溶处理、时效处理等。
固溶处理是将铝型材加热至固溶温度,然后迅速冷却,以使合金元素溶解在铝基体中。
时效处理是将铝型材在适当温度下保温一段时间,使合金元素析出,形成均匀的弥散相。
热处理完成后,还需要进行铝型材的表面处理。
铝型材的表面处理主要是为了改善其耐腐蚀性能和装饰效果。
常用的表面处理方法包括阳极氧化、电泳涂装、喷涂等。
阳极氧化是将铝型材浸泡在电解液中,通过电解作用形成氧化膜。
电泳涂装是将铝型材浸泡在涂料中,通过电场作用将涂料均匀附着在表面。
喷涂是将涂料喷洒在铝型材表面,形成一层保护膜。
最后是铝型材的切割和加工。
根据产品要求,将铝型材切割成合适的长度,并进行钻孔、铣削、焊接等加工工艺,以满足不同产品的需求。
切割和加工过程中,需要使用合适的切割工具和加工设备,保证产品的尺寸精度和加工质量。
- 1、下载文档前请自行甄别文档内容的完整性,平台不提供额外的编辑、内容补充、找答案等附加服务。
- 2、"仅部分预览"的文档,不可在线预览部分如存在完整性等问题,可反馈申请退款(可完整预览的文档不适用该条件!)。
- 3、如文档侵犯您的权益,请联系客服反馈,我们会尽快为您处理(人工客服工作时间:9:00-18:30)。
铝型材加工工艺及技术方案
1接单
1.1接到加工单后,应认真仔细地审单,如单属正常,必须按照
单上所规定日期内保质保量完成。
如单有问题,应及时反
映得以正确处理后才能继续加工。
2.1加工单的统计、算料及搭配必须与采购供应部相互配合,事先计划需用材料。
2材料领用
2.1经仔细复核,确实无误后,按材料的规格、型号、数量、颜
色的要求,到仓库办理领料手续。
2.2未办理领料手续,又末经采购供应部的允许,不得私自到仓库乱拿材料。
2.3原材料领用搬运时,必须按循序渐进的方式,由上至下,避
免材料混乱和铝材装饰面划伤现象。
3切割
3.1机械使用前检查,首先打开空气压缩机的排水阀排水,然后
打上接电开关,让机械空转一段时间检查机械无异常现
象,即可准备切割。
3.2切割时注意保护铝材装饰面。
3.3铝材切割,尺寸误差不超过1mm。
3.4切割后的半成品应堆放整齐,标明需用工地及规格、数量,以便下一道工序的使用。
3.5注意切割机的保养,切割机使用时锯片必须经常打油。
3.6工作台面必须保持干净,避免切割时的铝屑与铝材磨擦,造成伤痕。
4铝材冲孔
4.1机械使用前应检查机械运转是否正常,接上电源开关让设备
空转观察机械确实无异,开始下一步的工作。
4.2模具安装时,必须由专业人员安装,安装完毕必须检查模具
与机械是否配合得当,再进行下一道工序的工作。
4.3进行冲压孔前必须复核,确实无异后,开始铝材的冲孔工作。
4.4冲孔后的铝材,切口必须平整、光滑。
4.5连续冲料时,应检查上模中的料是否退出,模具有没有松动,
如有问题必须做好相应措施解决。
4.6加工后的成品,必须堆放整齐,周围必须保持清洁。
4.7所有工作完成之后,切断电源开关。
5包装、过塑
5.1铝材过塑前应检查过塑机是否正常,如正常则首先打开电源
开关接通电源,开动风扇及传送带,待温度调至180℃左
右时,方能过塑。
5.2铝材包装过塑前,应将表面擦拭干净,热收缩膜套到铝材的
两端各超出80mm-100mm,不得超出过长,以免造成浪费。
5.3过塑后的铝材,必须保持表面光滑,避免出现皱痕与裂口等现象。
5.4过塑完毕,关掉过塑机的加热温度开关,待温度降至常温时,
方能关掉电源开关,温度未降下时,严禁关电源开关,否
则会造成过塑机电阻丝烧断。
6质量检查
6.1质检员检查所生产的半成品是否按要求加工生产,如检查出
有质量不合格产品。
要求返工时,应无条件执行。
6.2对人为造成质量不合格的,必须按质量手册条款执行。
7成品入库
7.1成品入库前,应提供成品的作业单号、数量、规格、型号及
需用工地给仓管,配合仓管做好成品入库。
7.2入库后的成品,需堆放整齐,规格、型号要一致,避免各种成品混乱的现象。