缸体机械加工工艺设计
液压缸的结构及机械加工工艺分析
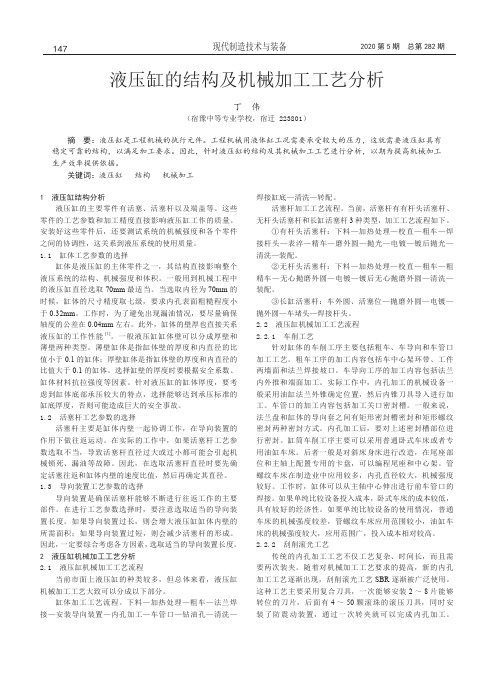
1 液压缸结构分析液压缸的主要零件有活塞、活塞杆以及端盖等。
这些零件的工艺参数和加工精度直接影响液压缸工作的质量。
安装好这些零件后,还要测试系统的机械强度和各个零件之间的协调性,这关系到液压系统的使用质量。
1.1 缸体工艺参数的选择缸体是液压缸的主体零件之一,其结构直接影响整个液压系统的结构、机械强度和体积。
一般用到机械工程中的液压缸直径选取70mm最适当。
当选取内径为70mm的时候,缸体的尺寸精度取七级,要求内孔表面粗糙程度小于0.32mm。
工作时,为了避免出现漏油情况,要尽量确保轴度的公差在0.04mm左右。
此外,缸体的壁厚也直接关系液压缸的工作性能[1]。
一般液压缸缸体壁可以分成厚壁和薄壁两种类型。
薄壁缸体是指缸体壁的厚度和内直径的比值小于0.1的缸体;厚壁缸体是指缸体壁的厚度和内直径的比值大于0.1的缸体。
选择缸壁的厚度时要根据安全系数、缸体材料抗拉强度等因素。
针对液压缸的缸体厚度,要考虑到缸体底部承压较大的特点,选择能够达到承压标准的缸底厚度,否则可能造成巨大的安全事故。
1.2 活塞杆工艺参数的选择活塞杆主要是缸体内壁一起协调工作,在导向装置的作用下做往返运动。
在实际的工作中,如果活塞杆工艺参数选取不当,导致活塞杆直径过大或过小都可能会引起机械锁死、漏油等故障。
因此,在选取活塞杆直径时要先确定活塞往返和缸体内壁的速度比值,然后再确定其直径。
1.3 导向装置工艺参数的选择导向装置是确保活塞杆能够不断进行往返工作的主要部件。
在进行工艺参数选择时,要注意选取适当的导向装置长度。
如果导向装置过长,则会增大液压缸缸体内壁的所需面积;如果导向装置过短,则会减少活塞杆的形成。
因此,一定要综合考虑各方因素,选取适当的导向装置长度。
2 液压缸机械加工工艺分析2.1 液压缸机械加工工艺流程当前市面上液压缸的种类较多,但总体来看,液压缸机械加工工艺大致可以分成以下部分。
缸体加工工艺流程。
下料—加热处理—粗车—法兰焊接—安装导向装置—内孔加工—车管口—钻油孔—清洗—焊接缸底—清洗—转配。
缸体零件通常的加工工艺流程
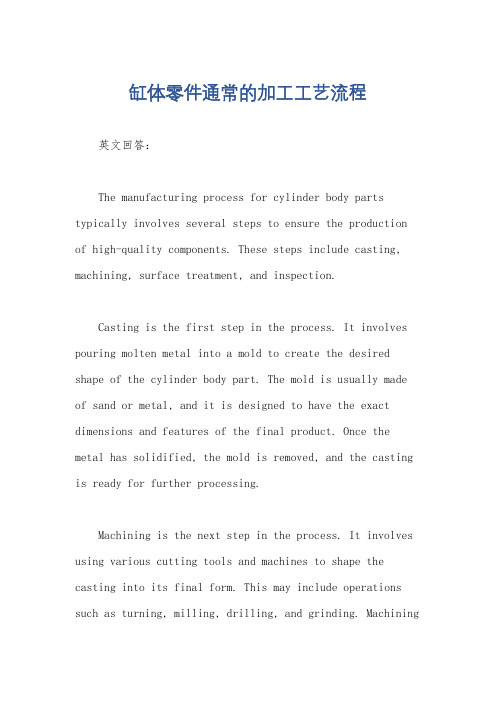
缸体零件通常的加工工艺流程英文回答:The manufacturing process for cylinder body parts typically involves several steps to ensure the production of high-quality components. These steps include casting, machining, surface treatment, and inspection.Casting is the first step in the process. It involves pouring molten metal into a mold to create the desired shape of the cylinder body part. The mold is usually made of sand or metal, and it is designed to have the exact dimensions and features of the final product. Once the metal has solidified, the mold is removed, and the casting is ready for further processing.Machining is the next step in the process. It involves using various cutting tools and machines to shape the casting into its final form. This may include operations such as turning, milling, drilling, and grinding. Machiningis essential to achieve the precise dimensions and surface finish required for the cylinder body part. It requires skilled operators and advanced equipment to ensure accuracy and consistency.After machining, the cylinder body part may undergo surface treatment to improve its performance and appearance. This can include processes such as polishing, plating, painting, or coating. Surface treatment helps to protectthe part from corrosion, enhance its durability, andprovide a visually appealing finish. Different surface treatment methods are used depending on the material and specific requirements of the cylinder body part.Finally, inspection is conducted to ensure the qualityof the cylinder body part. This involves checking the dimensions, surface finish, and overall integrity of the part. Various inspection techniques may be used, including visual inspection, measurement with precision tools, andnon-destructive testing methods. Any defects or deviations from the specifications are identified and addressed before the part is considered suitable for use.中文回答:缸体零件的加工工艺流程通常包括几个步骤,以确保生产出高质量的零件。
发动机缸盖机械加工工艺及夹具设计
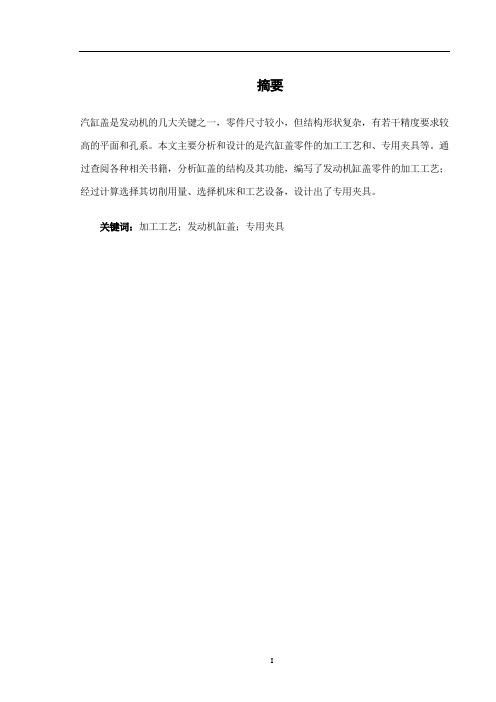
摘要汽缸盖是发动机的几大关键之一,零件尺寸较小,但结构形状复杂,有若干精度要求较高的平面和孔系。
本文主要分析和设计的是汽缸盖零件的加工工艺和、专用夹具等。
通过查阅各种相关书籍,分析缸盖的结构及其功能,编写了发动机缸盖零件的加工工艺;经过计算选择其切削用量、选择机床和工艺设备,设计出了专用夹具。
关键词:加工工艺;发动机缸盖;专用夹具AbstractThe cylinder cover is one of several toll-gates to launch the engine keys, the spare parts size is smaller, but the construction shape is complicated, how many the accuracy request the higher flat surface with the bore department. Analyze primarily here with design of is a cylinder cover the spare parts processes the craft, appropriation tongs and so on .Pass to check every kind of related book, analyze construction and its functions of an urn of covers, weave to write a cover spare parts process the craft; Passing by the calculation chooses its slice the dosage of cut, choice machine tools with craft equipments, design appropriation tongs.Key words: processing technic,Engine cylinder cover; special fixture目录摘要 (I)ABSTRACT ................................................ I I 前言.. (V)1 绪论 (1)1.1课题研究的意义及现状 (1)1.2论文主要研究内容 (3)2 发动机缸盖工艺设计 (5)2.1发动机缸盖的分析 (5)2.2发动机缸盖毛坯的设计 (9)2.3工艺路线设计 (14)2.4加工设备及工艺装备的选择 (22)2.5加工工序设计 (24)3 钻床专用夹具设计 (33)3.1问题的提出 (33)3.2机床夹具的分类 (34)3.3夹具的设计内容 (34)3.4钻床夹具特点 (40)3.5钻套与工件间的距离................................. .40 3.6夹具的对刀 (41)3.7夹具体的设计 (41)4铣床专用夹具设计 (43)4.1铣前后面专用夹具 (43)结论 (46)参考文献 (47)致谢 (48)附录 (49)前言汽缸盖是汽车发动机中一个十分重要的部件,其上部置有凸轮轴,下部与汽缸体、活塞组成燃烧室,两边是进气道和排气道,与油气进入的进气歧管件和废气排出的排气管件相接,内有贯穿的冷却水道和润滑油路。
气缸体加工工艺及夹具设计

毕业设计(论文)课题气缸体加工工艺及夹具设计院系机械工程学院专业机械制造及自动化班级姓名完成日期指导教师摘要本说明书涵盖了气缸体零件从毛坯的选择到工艺过程拟定再到各加工步骤计算的全部过程,此外,对于用到的镗床及钻床夹具也做了简要说明。
首先对于零件上的一些主要加工表面,通过查阅大量专业资料确定了其加工工艺,确保达到零件的精度要求,对于所涉及的尺寸公差也是通过各种详细的计算而得来。
为了给加工零件提供完整的书面说明,在本说明书中还对气缸体的作用及工作环境做了详细的介绍,对于所涉及到的参考文献也详尽列出。
最后,对于在加工过程中所用到的夹具设计原则也有所阐述,并给出了一套镗夹具的设计方案。
总之,本着完整,详尽,正确的原则,对于需要分析计算的地方在本说明书中都有相应的体现,最终给零件的生产加工提供最原始的数据资料。
关键词:气缸体工艺过程镗床钻床AbstractThis specification covers the gas cylinder body parts from blank selection to process to the processing steps for calculating all the process, in addition, for use in the boring and drilling fixture also do a brief explanation.First of all for the parts on some of the main processing surface, access to a large number of professional material to decide its processing technology, ensure the precision of parts, demands for dimensional tolerance is also involved through various detailed calculation and evolve. In order to give processing components to provide complete written explain, in this manual of the role of the cylinder block and working environment of a detailed introduction, involved in the reference also detailed list. Finally, in the course of processing for the kind of fixture design principles will be discussed, and gives a boring and fixture design scheme.In short, in line with complete, detailed, correct principles, the need for analysis and calculation of the place in this manual all has the corresponding reflect, and finally to the production and processing of parts provide the original data.目录绪论 (5)(1)课题背景及发展趋势 (5)(2)夹具的基本结构及夹具设计的内容 (5)第一章零件的分析 (7)1.1零件的作用 (7)1.2零件的工艺分析 (8)第二章确定毛坯 (9)第三章工艺规程设计 (10)3.1 定位基准的选择 (10)3.2 制定工艺路线 (11)3.3选择加工设备及刀,夹,量具 (13)3.4 加工工序设计 (14)3.4.1 切削用量的确定 (14)3.4.2 基本时间的确定 (18)第五章夹具设计 (19)5.1 夹具的基本要求与设计步骤 (19)5.2 定位机构的确定 (20)5.3 定位方案的论证 (20)总结 (22)参考文献 (24)感谢 (25)绪论机械制造与自动化专业毕业设计是对所学专业知识的一次巩固,是在进行社会实践之前对所学各课程的一次深入的综合性的总复习,也是理论联系实际的训练。
缸体机械加工工艺设计
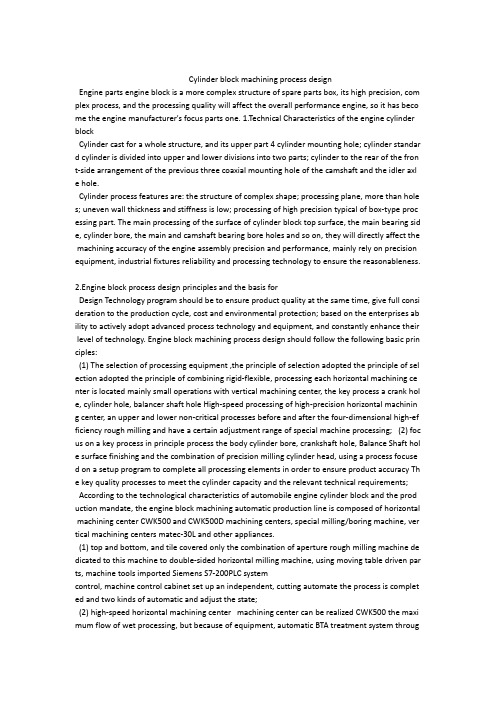
Cylinder block machining process designEngine parts engine block is a more complex structure of spare parts box, its high precision, com plex process, and the processing quality will affect the overall performance engine, so it has beco me the engine manufacturer's focus parts one. 1.Technical Characteristics of the engine cylinder blockCylinder cast for a whole structure, and its upper part 4 cylinder mounting hole; cylinder standar d cylinder is divided into upper and lower divisions into two parts; cylinder to the rear of the fron t-side arrangement of the previous three coaxial mounting hole of the camshaft and the idler axl e hole.Cylinder process features are: the structure of complex shape; processing plane, more than hole s; uneven wall thickness and stiffness is low; processing of high precision typical of box-type proc essing part. The main processing of the surface of cylinder block top surface, the main bearing sid e, cylinder bore, the main and camshaft bearing bore holes and so on, they will directly affect the machining accuracy of the engine assembly precision and performance, mainly rely on precision equipment, industrial fixtures reliability and processing technology to ensure the reasonableness.2.Engine block process design principles and the basis forDesign Technology program should be to ensure product quality at the same time, give full consi deration to the production cycle, cost and environmental protection; based on the enterprises ab ility to actively adopt advanced process technology and equipment, and constantly enhance their level of technology. Engine block machining process design should follow the following basic prin ciples:(1) The selection of processing equipment ,the principle of selection adopted the principle of sel ection adopted the principle of combining rigid-flexible, processing each horizontal machining ce nter is located mainly small operations with vertical machining center, the key process a crank hol e, cylinder hole, balancer shaft hole High-speed processing of high-precision horizontal machinin g center, an upper and lower non-critical processes before and after the four-dimensional high-ef ficiency rough milling and have a certain adjustment range of special machine processing; (2) foc us on a key process in principle process the body cylinder bore, crankshaft hole, Balance Shaft hol e surface finishing and the combination of precision milling cylinder head, using a process focused on a setup program to complete all processing elements in order to ensure product accuracy The key quality processes to meet the cylinder capacity and the relevant technical requirements; According to the technological characteristics of automobile engine cylinder block and the prod uction mandate, the engine block machining automatic production line is composed of horizontal machining center CWK500 and CWK500D machining centers, special milling/boring machine, ver tical machining centers matec-30L and other appliances.(1) top and bottom, and tile covered only the combination of aperture rough milling machine de dicated to this machine to double-sided horizontal milling machine, using moving table driven par ts, machine tools imported Siemens S7-200PLC systemcontrol, machine control cabinet set up an independent, cutting automate the process is complet ed and two kinds of automatic and adjust the state;(2) high-speed horizontal machining center machining center can be realized CWK500 the maxi mum flow of wet processing, but because of equipment, automatic BTA treatment system through the built-in tray under the wide-type chip conveyor and the completion of the machining center can be dry processing; machine tool spindle speed 6000r/min,rapid feeding speed 38m/min;(3) The combination of front and rear face rough milling machine tool using hydraulic transmissi on; control system imported Siemens S7-200PLC system control, machine tools have a certain fle xibility;(4) The special machine TXK1500 this machine vertical machining center by the modification of shape, with vertical machining center features and performance, this machine has high strength, high wear-resistant, high stability, high accuracy, high-profile etc.;(5) high-speed vertical machining center matec-30L of the machining center spindle high speed 9000r/min.Control system uses Siemens SINUMERIK840D control system;(6) high-speed horizontal machining center spindle CWK500Dhighest speed 15000r/min.3.Engine block machining process design the main contentEngine block complex structure, high precision, arge size, is thin-walled parts, there are a numb er of high precision plane and holes. Engine block machining process characteristics; mainly flat a nd the hole processing, processing of flat generally use planing, milling methods such as processi ng, processing of hole used mainly boring, processing and multi-purpose drilling holes. As the cyli nder complex structure. so how to ensure that the mutual position of the surface processing prec ision is an important issue.3.1 The selection of blankEngine block on the materials used are generally gray cast iron HT150,HT200,HT250,there is also cast aluminum or steel plate, this engine block using high-strength alloy cast iron. Cylinder in the processing prior to aging treatment in order to eliminate stress and improve the rough casting m echanical properties.Improve the rough accuracy, reduction of machining allowance, is to improve the automated pro duction line system productivity and processing quality of the important measures. As the foreign box-type parts of rough quality and high precision, and its production-line system has been imple mented directly on the blank line, not only eliminating the need for blank check device also saves the rough quality problems due to waste of machining time, increase overall efficiency. Therefor e, the refinement of rough is to improve the productivity of the most promising way out. For the engine block production line, can be rough in parts on-line pre-milling six face, removing most of the margin, to facilitate direct on-line parts.3.2 Machining process selection and processing of the benchmarkChoose the right processing technology base is directly related to the processing quality can ens ure the parts. Generally speaking, process benchmarking can bedivided into coarse and fine reference base.(1) The baseline for the on-line thick rough, which is particularly important the choice of bench mark crude, if crude benchmark choice unreasonable, will the uneven distribution of machining a llowance, processing and surface offsets, resulting in waste. In the cylinder production line, we ha ve adopted for the coarse side of the base;(2) Refined the base of this box for the engine block parts, the general use of "side two sales "fora full range of uniform benchmarks, For the longer automated production positioning, therefore, will be divided into 2-3 segment pin holes used. In the cylinder pin hole of the process, we have adopted to the side, bottom and the spindle hole positioning, in the processing center on the pro cess. 3.3 Machining Processing Stages and processes of the arrangementsOften a part of many apparent need for processing, of course, the surface machining accuracy ar e different. Processing of high precision surface, often after repeated processing; As for the proce ssing of the surface of low precision, only need to go through one or two on the list. Thus, when t he development process in order to seize the "processing high precision surface, "this conflict, th e reasonable arrangement processes and rational division stage of processing. Arrange the order of the principle of process is: after the first coarse refined, the first surface after the hole, the first benchmark other. In the engine block machining, the same should follow this principle.(1) roughing stage engine block machining process, the arrangements for roughing process, to fu lly carry out rough rough, trim most of the margin in order to ensure production efficiency;(2) semi-finishing phase of the engine block machining, in order to ensure the accuracy of the mi ddle of some important surface processing, and arrange some semi-finishing operations, will be r equired accuracy and surface roughness of the surface of the middle of some processing to comp lete, while demanding the surface of semi-finished, to prepare for future finishing;(3) The finishing stage of requiring high accuracy and surface roughness of the surface processin g;(4) secondary processing, such as small surface screw holes, you can finish of the major surface after the one hand, when the workpiece deformation process little impact at the same time also r educed the rejection rate;In addition,if the main surface of a waste,these small the surface will n ot have to be processed,thus avoiding a waste of man-hours.However,if the processing is very eas y for a small surface bumps the main surface,it should be placed on a small surface finish prior to the main surface finishing;(5) should make proper arrangements for secondary processes such as product inspection proce ss,in part roughing stage,the key process before and after processing,spare parts all the processin g has been completed,should be appropriate arrangements.Stage of processing division,has the following advantages:First,it can take measures to eliminate the rough workpiece after the stress,to ensure accuracy; second,finishing on the back,and will no t damage during transport the surface of theworkpiece has been processed;again,first roughing the surface defects can be detected early and promptly deal with rough,do not waste working hours.But most small parts,do not sub very thin.3.4 cylinder surface of the main processing and secondary processes Cylinder surface and suppo rt the main processing operations are:(1) plane processing at present, the milling of engine blocks is the primary means of planar proc essing,domestic milling feed rate is generally 300-400mm/min,and foreign 2000-4000mm/min mi lling feed rate compared to far cry,to be on increasing,therefore,improve the milling feed rate,red uce overhead time is to improve the productivity of the major means of finishing a number of pla ne engine block when the milling feed rate to reach 2399mm/min,greatly improved efficiency; Top surface of the cylinder milling is a key process in the process,the flatness requirements for 0. 02/145mm,the surface roughness of Ra1.6um.Processing in the cylinder,the use of side and spind le bearing bore positioning,top,bottom and middle vagay only aperture while processing used in t he processing line outside of the knife device can better meet the engine block machining accura cy;(2) General holes machining holes in general are still using the traditional processing of drilling, expansion,boring,reaming,tapping and other craft approach. Issues in the design process of speci fic programs,use of coated cutting tools,cutting tools and other advanced tools within the cooling,and using a large flow of cooling systems,greatly improving the cutting speed,improved producti vity;(3) deep hole processing of the traditional processing method is used to grade twist drill feed,lo w efficiency of their production,processing and quality is poor.The deep hole in the engine block processing,the use of gun drilling process;(4) The three-axis machining holes for the cylinder-axis machining holes holes of high precision, long working hours of the restrictive process.Thus,work arrangements,processing methods,tools and so on should be special attention.All cover pre-processing,that is,semi-circular hole and the c ylinder block main bearing cap of the shortage of processing,its main purpose is to remove blank margin,release stress,to prepare for the post-order processing;in crankshaft machining processin g center hole,using double-sided Boring,boring the first holes in the crankshaft hole at one end to 1/2 length,and then turn 180 degrees workbench,form the other end and then bore another 1/2 length.(5) The cylinder bore machining cylinder hole cylinder machining processing is a key process in the one,under normal circumstances,the machining process as a rough boring,semi-fine boring,pr ecision boring and honing.Cylinder bore wall for the early detection of casting defects,eliminate s tress,should be thick cylinder boring holes in advance;due to the structural characteristics of the different cylinder bore,must be in honing process to improve the cylinder bore surface quality.In t he high-volume production,the cylinder bore honing generally use the multi-axis grinding machin e or honing Automatic Line.Here we use honing automatic lines,from the coarse-heng.Fine-heng and testing equipment,composed of three;(6) Cleaning cleaning isdivided into wet cleaning and dry cleaning.Machining cylinder automatic production line using a large flow of wet cleaning;(7) Detect points outside the line detection and line detection of two kinds. Quality inspection in the engine block,according to the actual situation with lines outside the detection,the main use o f coordinate measuring machine integrated measurements of the cylinder,each 200 samples 1-5 pieces,each class random one. 4.SummaryThrough the engine block of the structure and process characteristics of the analysis,discusses t he engine block machining process design principles and basis of the choice of cutting parameter s,and U-turn at high speed milling and boring,for example,design,analysis of the engine cylinder b ody of high-speed milling and turnover boring process,and in the processing need to pay attentio n to.缸体机械加工工艺设计发动机缸体是发动机零件中结构较为复杂的箱体零件,其精度要求高,加工工艺复杂,并且加工加工质量的好坏直接影响发动机整个机构的性能,因此,它成为各个发动机生产厂家所关注的重点零件之一。
缸体的机械加工工艺与设计

缸体的机械加工工艺与设计发动机缸体在发动机零件中属于结构较为复杂的箱体类零件,它精度要求高,加工工艺较复杂,其加工质量的优良影响发动机整体性能,因此,它是发动机生产厂家所需注意的重点零件。
1,发动机缸体的工艺特性发动机缸体为发动机的骨架和基础零件,又是发动机装配时用到的基准零件。
缸体作用:支承活塞、曲轴、连杆等活动部件,保证工作时位置准确:保证发动机冷却、润滑和换气:提供各类辅助系统、组成部件以及发动机安装。
1.1工艺特性缸体是整体铸造结构,其上有四个缸套安装孔,缸体的水平隔板将其分成两部分,缸体的前端面排列有三个同轴线的惰轮轴孔和凸轮轴安装孔。
缸体工艺特点:形状、结构复杂:加工的孔、平面多:壁厚不均匀,刚度较低;加工精度要求较高,是典型的箱体类零件。
缸体主要加工面包括顶面、缸孔、主轴承座侧面、凸轮轴孔及主轴承孔等,它们的加工精度影响发动机的工作性能和装配精度,主要靠设备的精度、工夹具的可靠性及加工工艺的合理性来确保。
2.发动机缸体工艺设计方案的原则与依据工艺设计方案是工艺准备工作的前提,是工艺规程的设计以及工艺装备设计过程中的指导文件。
合理的工艺方案,有利于系统运用新型科学成果与先进的生产经验,从而保证产品质量,有效改善劳动条件,提高了工艺管理水平及工艺技术。
2.1艺的方案设计原则设计工艺方案在保证产品质量的同时,要考虑生产周期、成本与环境保护,根据企业能力,采用国内外先进的工艺装备与技术,提高企业的工艺水平。
发动机缸体的工艺设计应遵循以下准则:(1)加工设备选用原则:采取刚柔结合原则,选用加工设备,加工设备以卧式机床加工为主,少量工序用立式机床加工,关键工序一一用具有高精度的高速卧式加工中心加工缸孔、曲轴孔、平衡轴孔:非关键工序一一使用高效且有一定调动范围的专用机床铣削上下前后四个平面:(2)工序集中原则:关键工序一一精加工发动机缸孔、平衡轴孔、曲轴孔以及精铣缸盖结合面,用工序集中,装夹一次,一道工序就完成全部的加工内容,确保产品精度符合缸体关键性能的工艺能力及相关要求:(3)所有夹具采用美国或德国产的优质可靠液压装置,夹紧元件、液压泵以及液压控制元件:(4)整线均采用湿式加工,使用单机独立排屑,卧式加工中心关键的高精度加工使用恒温冷却并且其精过滤系统附加有高压高精度双回路带旁通,加工中心均带有高压内冷。
A7V型泵缸体壳体零件机械加工工艺及铣上端面夹具设计

摘要通过对壳体零件的加工工艺路线的确定,该零件的加工以底面作为基准是合适的,本加工工艺方案满足粗基准选择的基本要求及精基准选择的四项原则。
本夹具为专用夹具,该夹具的特点是针对性强、结构紧凑、操作简便、生产率高。
在本次设计中,夹具的设计满足机床夹具总体方案设计的基本要求,充分保证零件加工质量,具有较高的生产效率和较低的制造成本以及具有良好的结构工艺性。
本次毕业设计的主要内容是机械加工工艺规程编制和铣上端面工序专用夹具设计。
综合运用机械制造技术基础和其它课程的基本理论和方法,为了能够完成壳体零件机械加工工艺及铣床夹具的设计任务,综合运用所学的知识,应用正确的设计方法,制订了壳体零件的机械加工工艺规程。
结合工艺设计内容,熟练应用工艺计算方法,对相关工艺内容进行了正确的分析设计和计算,如切削力、切削功率、切削速度、工艺参数、定位误差、夹紧力等。
关键词:机械加工工艺规程专用夹具壳体AbstractDetermined by the process route of shell parts, the parts processing to the bottom as the benchmark is appropriate, the processing technology solutions to meet the four basic requirements of the principle of coarse and fine reference datum. The fixture is a special clamp, and the fixture is characterized by strong pertinence, compact structure, simple operation and high productivity. In this design, fixture design and meet the basic requirements of overall design of the fixture, and fully guarantee the quality of machining and has high production efficiency and low manufacturing cost and good structure technology. The main content of this graduation project is the design of machining process regulations and the design of special fixture for milling end face process. The basic theory and method of comprehensive use of machinery manufacturing technology and other courses, in order to design the task to complete the shell parts machining and milling fixture, the integrated use of knowledge and apply the correct design method, the machining process planning for shell parts. With the content of process design, calculation method of skilled application process, the process of content analysis and design calculation of the right, such as cutting force, cutting power, cutting speed, process parameters, positioning error the clamping force and so on.Key words: machining; process specification; special clamp shell目录摘要 (I)Abstract (II)目录 (III)第1章绪论 (1)第2章零件的机械加工工艺规程设计 (2)2.1壳体零件的工艺分析 (2)2.1.1零件的作用 (2)2.1.2零件的工艺分析 (2)2.2零件的生产纲领 (3)2.3选择毛坯 (3)2.4设计毛坯图 (3)2.5机械加工工艺路线的制订 (5)2.5.1选择定位基准 (5)2.5.2加工方法 (5)2.5.3制订工艺路线 (7)2.5.4加工工艺过程的分析 (9)2.5.5选择加工设备与工艺装备 (9)2.5.6确定切削用量及基本时间 (10)第3章铣上端面夹具设计 (21)3.1指出存在的问题 (21)3.2夹具设计 (21)3.2.1夹具体设计 (21)3.2.2定位基准的选择 (21)3.2.3定位方案和元件设计 (21)3.2.4夹紧机构的设计 (22)3.2.5定位误差的计算 (22)3.2.6对刀装置设计 (24)3.2.7确定夹具体结构尺寸和总体结构 (24)结论 (26)致谢 (28)参考文献 (29)第1章绪论机械制造业指从事各种动力机械、起重运输机械、农业机械、冶金矿山机械、化工机械、纺织机械、机床、工具、仪器、仪表及其他机械设备等生产的行业。
总泵缸体的机械加工工艺及工装夹具设计

学科门类:单位代码:毕业设计说明书(论文)总泵缸体的加工工艺及夹具设计学生姓名所学专业班级学号指导教师XXXXXXXXX系二○**年X X月目录摘要:................................................................................................. 错误!未定义书签。
前言 . (3)绪言 (4)1 毕业设计的目的 (4)2 毕业设计的基本任务与要求 (4)2.1 设计基本任务 (4)2.2 设计要求 (5)3 毕业设计说明书的编写 (5)总泵缸体工艺设计与工装设计 ........................................... 错误!未定义书签。
1. 总泵缸体的毛坯和工艺分析:........................................ 错误!未定义书签。
2. 分析总泵缸体零件图: ..................................................... 错误!未定义书签。
3. 缸体的材料、毛坯及热处理:........................................ 错误!未定义书签。
3.1 毛坯的材料热处理 (7)3.2 总泵缸体加工定位基准的选择 (8)4. 总泵缸的加工工艺过程 (9)4.1 机械加工余量、工序尺寸及毛坯尺寸的确定 (10)4.2 定切削用量及基本工时 (11)4.3 时间定额计算及生产安排 (29)4.4夹具设计 (34)4.5 夹具配重设计 (34)4.6 夹紧装置的设计 (34)4.7 夹具精度分析与计算 (35)4.8 结束语: (38)结论 (38)参考文献项目 (39)前言本设计的课题,不仅让我们系统全面的巩固了三年来所学的的理论知识,还使我们把所学的理论知识运用到实际操作中。
- 1、下载文档前请自行甄别文档内容的完整性,平台不提供额外的编辑、内容补充、找答案等附加服务。
- 2、"仅部分预览"的文档,不可在线预览部分如存在完整性等问题,可反馈申请退款(可完整预览的文档不适用该条件!)。
- 3、如文档侵犯您的权益,请联系客服反馈,我们会尽快为您处理(人工客服工作时间:9:00-18:30)。
Cylinder block machining process designEngine parts engine block is a more complex structure of spare parts box, its high precision, com plex process, and the processing quality will affect the overall performance engine, so it has beco me the engine manufacturer's focus parts one. 1.Technical Characteristics of the engine cylinder blockCylinder cast for a whole structure, and its upper part 4 cylinder mounting hole; cylinder standar d cylinder is divided into upper and lower divisions into two parts; cylinder to the rear of the fron t-side arrangement of the previous three coaxial mounting hole of the camshaft and the idler axl e hole.Cylinder process features are: the structure of complex shape; processing plane, more than hole s; uneven wall thickness and stiffness is low; processing of high precision typical of box-type proc essing part. The main processing of the surface of cylinder block top surface, the main bearing sid e, cylinder bore, the main and camshaft bearing bore holes and so on, they will directly affect the machining accuracy of the engine assembly precision and performance, mainly rely on precision equipment, industrial fixtures reliability and processing technology to ensure the reasonableness.2.Engine block process design principles and the basis forDesign Technology program should be to ensure product quality at the same time, give full consi deration to the production cycle, cost and environmental protection; based on the enterprises ab ility to actively adopt advanced process technology and equipment, and constantly enhance their level of technology. Engine block machining process design should follow the following basic prin ciples:(1) The selection of processing equipment ,the principle of selection adopted the principle of sel ection adopted the principle of combining rigid-flexible, processing each horizontal machining ce nter is located mainly small operations with vertical machining center, the key process a crank hol e, cylinder hole, balancer shaft hole High-speed processing of high-precision horizontal machinin g center, an upper and lower non-critical processes before and after the four-dimensional high-ef ficiency rough milling and have a certain adjustment range of special machine processing; (2) foc us on a key process in principle process the body cylinder bore, crankshaft hole, Balance Shaft hol e surface finishing and the combination of precision milling cylinder head, using a process focused on a setup program to complete all processing elements in order to ensure product accuracy The key quality processes to meet the cylinder capacity and the relevant technical requirements; According to the technological characteristics of automobile engine cylinder block and the prod uction mandate, the engine block machining automatic production line is composed of horizontal machining center CWK500 and CWK500D machining centers, special milling/boring machine, ver tical machining centers matec-30L and other appliances.(1) top and bottom, and tile covered only the combination of aperture rough milling machine de dicated to this machine to double-sided horizontal milling machine, using moving table driven par ts, machine tools imported Siemens S7-200PLC systemcontrol, machine control cabinet set up an independent, cutting automate the process is complet ed and two kinds of automatic and adjust the state;(2) high-speed horizontal machining center machining center can be realized CWK500 the maxi mum flow of wet processing, but because of equipment, automatic BTA treatment system through the built-in tray under the wide-type chip conveyor and the completion of the machining center can be dry processing; machine tool spindle speed 6000r/min,rapid feeding speed 38m/min;(3) The combination of front and rear face rough milling machine tool using hydraulic transmissi on; control system imported Siemens S7-200PLC system control, machine tools have a certain fle xibility;(4) The special machine TXK1500 this machine vertical machining center by the modification of shape, with vertical machining center features and performance, this machine has high strength, high wear-resistant, high stability, high accuracy, high-profile etc.;(5) high-speed vertical machining center matec-30L of the machining center spindle high speed 9000r/min.Control system uses Siemens SINUMERIK840D control system;(6) high-speed horizontal machining center spindle CWK500Dhighest speed 15000r/min.3.Engine block machining process design the main contentEngine block complex structure, high precision, arge size, is thin-walled parts, there are a numb er of high precision plane and holes. Engine block machining process characteristics; mainly flat a nd the hole processing, processing of flat generally use planing, milling methods such as processi ng, processing of hole used mainly boring, processing and multi-purpose drilling holes. As the cyli nder complex structure. so how to ensure that the mutual position of the surface processing prec ision is an important issue.3.1 The selection of blankEngine block on the materials used are generally gray cast iron HT150,HT200,HT250,there is also cast aluminum or steel plate, this engine block using high-strength alloy cast iron. Cylinder in the processing prior to aging treatment in order to eliminate stress and improve the rough casting m echanical properties.Improve the rough accuracy, reduction of machining allowance, is to improve the automated pro duction line system productivity and processing quality of the important measures. As the foreign box-type parts of rough quality and high precision, and its production-line system has been imple mented directly on the blank line, not only eliminating the need for blank check device also saves the rough quality problems due to waste of machining time, increase overall efficiency. Therefor e, the refinement of rough is to improve the productivity of the most promising way out. For the engine block production line, can be rough in parts on-line pre-milling six face, removing most of the margin, to facilitate direct on-line parts.3.2 Machining process selection and processing of the benchmarkChoose the right processing technology base is directly related to the processing quality can ens ure the parts. Generally speaking, process benchmarking can bedivided into coarse and fine reference base.(1) The baseline for the on-line thick rough, which is particularly important the choice of bench mark crude, if crude benchmark choice unreasonable, will the uneven distribution of machining a llowance, processing and surface offsets, resulting in waste. In the cylinder production line, we ha ve adopted for the coarse side of the base;(2) Refined the base of this box for the engine block parts, the general use of "side two sales "fora full range of uniform benchmarks, For the longer automated production positioning, therefore, will be divided into 2-3 segment pin holes used. In the cylinder pin hole of the process, we have adopted to the side, bottom and the spindle hole positioning, in the processing center on the pro cess. 3.3 Machining Processing Stages and processes of the arrangementsOften a part of many apparent need for processing, of course, the surface machining accuracy ar e different. Processing of high precision surface, often after repeated processing; As for the proce ssing of the surface of low precision, only need to go through one or two on the list. Thus, when t he development process in order to seize the "processing high precision surface, "this conflict, th e reasonable arrangement processes and rational division stage of processing. Arrange the order of the principle of process is: after the first coarse refined, the first surface after the hole, the first benchmark other. In the engine block machining, the same should follow this principle.(1) roughing stage engine block machining process, the arrangements for roughing process, to fu lly carry out rough rough, trim most of the margin in order to ensure production efficiency;(2) semi-finishing phase of the engine block machining, in order to ensure the accuracy of the mi ddle of some important surface processing, and arrange some semi-finishing operations, will be r equired accuracy and surface roughness of the surface of the middle of some processing to comp lete, while demanding the surface of semi-finished, to prepare for future finishing;(3) The finishing stage of requiring high accuracy and surface roughness of the surface processin g;(4) secondary processing, such as small surface screw holes, you can finish of the major surface after the one hand, when the workpiece deformation process little impact at the same time also r educed the rejection rate;In addition,if the main surface of a waste,these small the surface will n ot have to be processed,thus avoiding a waste of man-hours.However,if the processing is very eas y for a small surface bumps the main surface,it should be placed on a small surface finish prior to the main surface finishing;(5) should make proper arrangements for secondary processes such as product inspection proce ss,in part roughing stage,the key process before and after processing,spare parts all the processin g has been completed,should be appropriate arrangements.Stage of processing division,has the following advantages:First,it can take measures to eliminate the rough workpiece after the stress,to ensure accuracy; second,finishing on the back,and will no t damage during transport the surface of theworkpiece has been processed;again,first roughing the surface defects can be detected early and promptly deal with rough,do not waste working hours.But most small parts,do not sub very thin.3.4 cylinder surface of the main processing and secondary processes Cylinder surface and suppo rt the main processing operations are:(1) plane processing at present, the milling of engine blocks is the primary means of planar proc essing,domestic milling feed rate is generally 300-400mm/min,and foreign 2000-4000mm/min mi lling feed rate compared to far cry,to be on increasing,therefore,improve the milling feed rate,red uce overhead time is to improve the productivity of the major means of finishing a number of pla ne engine block when the milling feed rate to reach 2399mm/min,greatly improved efficiency; Top surface of the cylinder milling is a key process in the process,the flatness requirements for 0. 02/145mm,the surface roughness of Ra1.6um.Processing in the cylinder,the use of side and spind le bearing bore positioning,top,bottom and middle vagay only aperture while processing used in t he processing line outside of the knife device can better meet the engine block machining accura cy;(2) General holes machining holes in general are still using the traditional processing of drilling, expansion,boring,reaming,tapping and other craft approach. Issues in the design process of speci fic programs,use of coated cutting tools,cutting tools and other advanced tools within the cooling,and using a large flow of cooling systems,greatly improving the cutting speed,improved producti vity;(3) deep hole processing of the traditional processing method is used to grade twist drill feed,lo w efficiency of their production,processing and quality is poor.The deep hole in the engine block processing,the use of gun drilling process;(4) The three-axis machining holes for the cylinder-axis machining holes holes of high precision, long working hours of the restrictive process.Thus,work arrangements,processing methods,tools and so on should be special attention.All cover pre-processing,that is,semi-circular hole and the c ylinder block main bearing cap of the shortage of processing,its main purpose is to remove blank margin,release stress,to prepare for the post-order processing;in crankshaft machining processin g center hole,using double-sided Boring,boring the first holes in the crankshaft hole at one end to 1/2 length,and then turn 180 degrees workbench,form the other end and then bore another 1/2 length.(5) The cylinder bore machining cylinder hole cylinder machining processing is a key process in the one,under normal circumstances,the machining process as a rough boring,semi-fine boring,pr ecision boring and honing.Cylinder bore wall for the early detection of casting defects,eliminate s tress,should be thick cylinder boring holes in advance;due to the structural characteristics of the different cylinder bore,must be in honing process to improve the cylinder bore surface quality.In t he high-volume production,the cylinder bore honing generally use the multi-axis grinding machin e or honing Automatic Line.Here we use honing automatic lines,from the coarse-heng.Fine-heng and testing equipment,composed of three;(6) Cleaning cleaning isdivided into wet cleaning and dry cleaning.Machining cylinder automatic production line using a large flow of wet cleaning;(7) Detect points outside the line detection and line detection of two kinds. Quality inspection in the engine block,according to the actual situation with lines outside the detection,the main use o f coordinate measuring machine integrated measurements of the cylinder,each 200 samples 1-5 pieces,each class random one. 4.SummaryThrough the engine block of the structure and process characteristics of the analysis,discusses t he engine block machining process design principles and basis of the choice of cutting parameter s,and U-turn at high speed milling and boring,for example,design,analysis of the engine cylinder b ody of high-speed milling and turnover boring process,and in the processing need to pay attentio n to.缸体机械加工工艺设计发动机缸体是发动机零件中结构较为复杂的箱体零件,其精度要求高,加工工艺复杂,并且加工加工质量的好坏直接影响发动机整个机构的性能,因此,它成为各个发动机生产厂家所关注的重点零件之一。