切削液的选用与维护
绿色制造机制下的切削液选择与管理

化油的粒度 , 使其粒度增大, 大的粒子又较易集合成更大的 延长切削液的使用寿命 , 降低冷却液的消耗 , 减少废液的
粒子 , 后形成乳脂或 导致油 的析 出。 最 当矿 物质含量高 时 , 会 排 放 ,提 高 工 件 的加 工 精度 和产 品 合格 率 ,达 到 提 高 效 影响可洛 I 的悬浮性 , 缩短切 削液的使用 寿命 。 生 液 这将 率, 降本 增 效 的 目的 , 现 绿色 制 造 。 实 良好 的水 质是 成 功 使用 切 削 液 的前 提 , 显然 , 制 切 配 [ 考 文献 ] 参
4, 切 削 液 水 质 的 控 制 .
47 其 他 维 护 .
在切 削 液 的成 分 中 9 %以 上是 水 ,配 制 切 削液 用 水 0 切削液 的污染源 可来 自 多方 面 ,有 泄漏 到液槽 中的 很 的质量对切 削液总体性能的影 响, 比任何其他因素都大。 液 压油 、 油 、 润滑 清洗液 、 金属切 屑等。这些污染 物能 阻隔静 因此 , 水质 是应 首 先 给予 注 意 的重 要 因素 。 对切 削 液性 能 止 的液体 和空气 的接 触 , 阻止正 常 的充气 供氧 , 氧菌 繁 使厌 影 响 最 大 的是 溶 解 于水 中 的 固体 成 份 ,即水 的 硬度 、 盐 殖 , 陛地 去除污染物 , 经常 可防止液体 散发 出腐败 味道。 类。 这些因素的变化会改变切削液的性能 , 对切削液系统 5 结 语 产生 影 响 。 它们 能 促进 不 溶性 皂 的形 成 , 成 管路 和 过滤 造 器 的堵塞 , 不溶 性 皂也 易粘 附 于机 床 表 面 。C 2 M a 、 g 和切  ̄
切削液处理方案

切削液处理方案切削液是机械加工过程中常用的润滑剂和冷却剂,可有效降低加工中的摩擦和温度,提高工件加工质量和加工效率。
然而,切削液中的污染物及其不合理使用会对工作环境、工作效率和工作人员的健康造成负面影响。
为了确保切削液的正常使用和保障工作环境的安全,我们需要制定一个切削液处理方案。
1. 切削液的选用在选择切削液时,我们需考虑以下几个因素:工作材料、切削液的用途、切削液的成本等。
根据不同的加工条件和材料,选择适合的切削液,并确保其具有良好的稳定性和抗菌性能。
2. 切削液的使用准则为了使用切削液的安全性和高效性,我们需要制定以下几点使用准则:a. 确保切削液的正确配比:不同材料和加工过程需要不同比例的切削液来实现良好的润滑和冷却效果。
因此,要在使用切削液前,对其进行正确的配比。
b. 定期检查切削液的质量:切削液在使用过程中会产生各种污染物,如金属屑、废料等。
定期检查切削液的质量,包括pH值、浓度、杂质含量等,并根据检查结果进行相应的处理。
c. 切削液的储存要求:切削液需要存放在干燥、避光、通风的场所,并与化学品隔离放置,以防止其受到污染。
同时,要定期更换储存容器,并清理储存区域。
d. 使用切削液的注意事项:在使用切削液时,应戴上防护手套、护目镜等个人防护用具,以保障人身安全。
避免切削液溅入眼睛或吸入呼吸道。
3. 建立切削液处理系统为了及时清除切削液中的污染物,我们建议建立切削液处理系统。
该系统包括以下几个关键步骤:a. 液体过滤:通过过滤设备将切削液中的固体杂质过滤掉,防止其对加工设备和工件表面造成损害。
b. 沉淀和油水分离:通过沉降和油水分离等方法,将切削液中的油污和水分离,以达到回收和再利用的目的。
c. 脱水处理:采用热蒸发、压滤等方法,将切削液中的水分去除,以保持其良好的性能和稳定性。
d. 精细过滤:通过微滤设备进一步过滤切削液,以去除微小的杂质和微生物,保证其清洁度和抗菌性能。
4. 切削液废物的处理切削液废物可能带有化学物质和金属离子等有害物质,因此需要进行妥善的处理。
关于切削液的使用
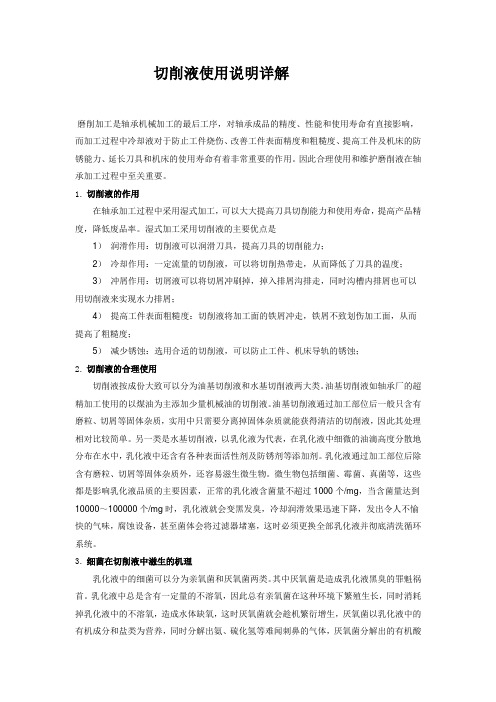
切削液使用说明详解磨削加工是轴承机械加工的最后工序,对轴承成品的精度、性能和使用寿命有直接影响,而加工过程中冷却液对于防止工件烧伤、改善工件表面精度和粗糙度、提高工件及机床的防锈能力、延长刀具和机床的使用寿命有着非常重要的作用。
因此合理使用和维护磨削液在轴承加工过程中至关重要。
1. 切削液的作用在轴承加工过程中采用湿式加工,可以大大提高刀具切削能力和使用寿命,提高产品精度,降低废品率。
湿式加工采用切削液的主要优点是1)润滑作用:切削液可以润滑刀具,提高刀具的切削能力;2)冷却作用:一定流量的切削液,可以将切削热带走,从而降低了刀具的温度;3)冲屑作用:切屑液可以将切屑冲刷掉,掉入排屑沟排走,同时沟槽内排屑也可以用切削液来实现水力排屑;4)提高工件表面粗糙度:切削液将加工面的铁屑冲走,铁屑不致划伤加工面,从而提高了粗糙度;5)减少锈蚀:选用合适的切削液,可以防止工件、机床导轨的锈蚀;2. 切削液的合理使用切削液按成份大致可以分为油基切削液和水基切削液两大类。
油基切削液如轴承厂的超精加工使用的以煤油为主添加少量机械油的切削液。
油基切削液通过加工部位后一般只含有磨粒、切屑等固体杂质,实用中只需要分离掉固体杂质就能获得清洁的切削液,因此其处理相对比较简单。
另一类是水基切削液,以乳化液为代表,在乳化液中细微的油滴高度分散地分布在水中,乳化液中还含有各种表面活性剂及防锈剂等添加剂。
乳化液通过加工部位后除含有磨粒、切屑等固体杂质外,还容易滋生微生物。
微生物包括细菌、霉菌、真菌等,这些都是影响乳化液品质的主要因素,正常的乳化液含菌量不超过1000个/mg,当含菌量达到10000~100000个/mg时,乳化液就会变黑发臭,冷却润滑效果迅速下降,发出令人不愉快的气味,腐蚀设备,甚至菌体会将过滤器堵塞,这时必须更换全部乳化液并彻底清洗循环系统。
3. 细菌在切削液中滋生的机理乳化液中的细菌可以分为亲氧菌和厌氧菌两类。
适用于数控机床的切削液选择

适用于数控机床的切削液选择数控机床作为现代制造业中不可或缺的设备之一,其切削液的选择和应用对于工件的加工质量、刀具寿命和设备性能都有着至关重要的影响。
本文将就适用于数控机床的切削液选择进行详细的探讨和分析,以帮助读者更好地了解如何选用合适的切削液,提升机床加工效率和性能。
1. 切削液的基本概念和作用切削液是指在数控机床加工过程中,用于冷却、润滑和清洗切削区域的一种液体。
它能有效地降低切削温度,减少工件和刀具的磨损,并促进切屑的排出,从而提高切削效率和加工质量。
切削液的主要作用包括:1.1 冷却切削区域:切削过程中会产生大量的热量,如果不及时冷却,会导致工件变形、刀具破裂等问题。
切削液通过吸收热量并迅速散热,保持切削区域的温度在适宜范围内。
1.2 润滑切削面:切削液能有效地润滑切削面,降低切削过程中的摩擦和热量产生,减少刀具的磨损和工件的表面粗糙度。
1.3 清洗切屑:切削液可以冲洗切屑,防止切屑在切削区域堆积,影响加工质量和刀具的寿命。
2. 切削液的选择原则2.1 适应材料和切削工艺:不同的切削液适用于不同的材料和切削工艺。
在选择切削液时,要充分考虑加工材料的种类和特性,以及切削工艺的要求,确保切削液能够与工件和刀具良好相容,并且满足特定的切削要求。
2.2 具备良好的散热性能:切削液在切削过程中要能够快速吸收和散热热量,降低切削区域的温度。
因此,切削液的导热系数和热传导性能是选择切削液时需要考虑的重要指标。
2.3 具有优异的润滑性能:切削液的润滑性能直接影响切削面的摩擦系数和磨损程度。
选择具有良好润滑性能的切削液可以有效地降低切削过程中的摩擦热量和刀具磨损,提高加工质量和刀具寿命。
2.4 对环境友好:在现代制造业追求绿色环保的潮流下,选择环境友好型的切削液也是一个重要的考虑因素。
环保性能包括切削液的挥发性、毒性和可降解性等方面。
3. 常见的切削液类型及其适应性3.1 油性切削液:油性切削液是最常用的一种切削液,其主要成分是矿物油或合成油。
切削液及其选用

切削液及其选用一、前言合理选用冷却润滑液,可以有效地减小切削过程中的摩擦,改善散热条件,而降低切削力,切削温度和刀具磨损,提高刀具耐用度,切削效率和已加工表面质量及降低产品的加工成本。
随着科学技术和机械加工工业的不断发展,特别足大量的难切削材料的应用和对产品零件加工质量要求越来越高,这就给切削加工带来了难题。
为了使这些难题获得解决,除合理选择别的切削条件外,合理选择切削液也尤为重要。
二.切削液的分类1.水溶液:其主要成分是水。
由于水的导热系数是油的导热系数三倍,所以它的冷却性能好。
在其中加入一定量的防锈和汕性添加剂,还能起到一定的防锈和润滑作用。
2.乳化液:(1)普通乳化液:它是由防锈剂,乳化剂和矿物油配制而成。
清洗和冷却性能好,兼有防锈和润滑性能。
(2)防锈乳化液:在普通乳化液中,加入大量的防锈剂,其作用同上,用于防锈要求严格的工序和气候潮湿的地区。
(3)极压乳化液:在乳化液中,添加含硫,磷,氯的极压添加剂,能在切削时的高温,高压下形成吸附膜,起润滑作用。
3.切削油:(1)矿物油:有5#、7#、10#、20#、30#机械油和柴油,煤油等,适用于一般润滑。
(2)动,植油及复合油:有豆油、菜子油、棉子油、蓖麻油、猪油等。
复合油是将动、植、矿三种油混合而成。
它具有良好地边界润滑。
(3)极压切削油:它是以矿物油为基础,加入油性,极压添加剂和防锈剂而成。
具有动,植物油良好地润滑性能和极压润滑性能。
三.切削液的作用1.冷却作用:它可以降低切削温度,提高刀具耐用度和减小工件热变形,保证加工质量。
一般的情况下,可降低切削温度50~150℃。
2.润滑作用:可以减小切屑与前刀面,工件与刀具后刀面的摩擦,以降低切削力,切削热和限制积屑瘤和鳞刺的产生。
一般的切削油在200℃左右就失去润滑能力。
如加入极压添加剂,就可以在高温(600~1000℃)、高压(1470~1960MPa)条件下起润滑作用。
这种润滑叫做极压润滑。
切削液的使用、管理与机床腐蚀的防护范本

切削液的使用、管理与机床腐蚀的防护范本随着制造业的发展,切削液在机床加工中起着非常重要的作用。
切削液的正确使用和管理,不仅可以提高切削加工的效率和质量,还可以延长机床的使用寿命。
同时,机床的腐蚀防护也是非常重要的,它可以降低机床的维护成本,保证机床的正常运行。
本文将从切削液的使用、管理和机床腐蚀防护方面进行介绍。
一、切削液的使用1. 选择切削液选择合适的切削液是确保切削过程稳定进行的关键。
切削液的选择应根据加工材料、切削方式、刀具类型和机床类型等因素进行。
常见的切削液有油基切削液、水基切削液和乳化液等。
2. 切削液的配制和调整在使用切削液之前,需要将其配制成适当的浓度。
切削液的浓度过高或过低都会影响切削液的性能。
当切削液的浓度过高时,易导致切削液的粘度过大,降低切削液的冷却和润滑效果;当切削液的浓度过低时,易导致切削液的润滑效果不佳,增加切削过程的摩擦。
3. 切削液的使用注意事项在使用切削液时,需要注意以下几点:- 切削液应定期更换,并且在更换之前应进行切削液的清洁。
- 在使用切削液时,应注意切削液与工件表面的接触情况,以确保切削液能够充分润滑工件表面。
- 使用切削液时,应根据切削液的要求进行调整,以确保切削液能够发挥最佳性能。
二、切削液的管理1. 切削液的储存和保管切削液应储存在干燥、阴凉的地方,避免阳光直射。
切削液的容器应密封良好,以防止切削液的挥发和污染。
切削液的储存区域应定期清洁和消毒,以防止细菌和其他有害物质的滋生。
2. 切削液的过滤和回收切削液在使用过程中会受到切屑、油脂等杂质的污染,因此需要定期对切削液进行过滤和回收。
切削液的过滤可以减少切屑和杂质对刀具的磨损,并有效延长切削液的使用寿命。
切削液的回收可以降低成本,并且对环境友好。
3. 切削液的定期检测和维护切削液的性能随着使用时间的推移而发生变化,因此需要定期进行切削液的检测和维护。
切削液的检测可以通过测量切削液的酸碱度、粘度、浓度等指标来判断切削液是否需要更换或调整。
切削液知识与选用

切削液知识与选用一、前言合理选用冷却润滑液,可以有效地减小切削过程中的摩擦,改善散热条件,而降低切削力,切削温度和刀具磨损,提高刀具耐用度,切削效率和已加工表面质量及降低产品的加工成本。
随着科学技术和机械加工工业的不断发展,特别足大量的难切削材料的应用和对产品零件加工质量要求越来越高,这就给切削加工带来了难题。
为了使这些难题获得解决,除合理选择别的切削条件外,合理选择切削液也尤为重要。
二.切削的分类1.水溶液:其主要成分是水。
由于水的导热系数是油的导热系数三倍,所以它的冷却性能好。
在其中加入一定量的防锈和汕性添加剂,还能起到一定的防锈和润滑作用。
2.乳化液:(1)普通乳化液:它是由防锈剂,乳化剂和矿物油配制而成。
清洗和冷却性能好,兼有防锈和润滑性能。
(2)防锈乳化液:在普通乳化液中,加入大量的防锈剂,其作用同上,用于防锈要求严格的工序和气候潮湿的地区。
(3)极压乳化液:在乳化液中,添加含硫,磷,氯的极压添加剂,能在切削时的高温,高压下形成吸附膜,起润滑作用。
3.切削油:(1)矿物油:有5#、7#、10#、20#、30#机械油和柴油,煤油等,适用于一般润滑。
(2)动,植油及复合油:有豆油、菜子油、棉子油、蓖麻油、猪油等。
复合油是将动、植、矿三种油混合而成。
它具有良好地边界润滑。
(3)极压切削油:它是以矿物油为基础,加入油性,极压添加剂和防锈剂而成。
具有动,植物油良好地润滑性能和极压润滑性能。
三.切削液的作用1.冷却作用:它可以降低切削温度,提高刀具耐用度和减小工件热变形,保证加工质量。
一般的情况下,可降低切削温度50~150℃。
2.润滑作用:可以减小切屑与前刀面,工件与刀具后刀面的摩擦,以降低切削力,切削热和限制积屑瘤和鳞刺的产生。
一般的切削油在200℃左右就失去润滑能力。
如加入极压添加剂,就可以在高温(600~1000℃)、高压(1470~1960MPa)条件下起润滑作用。
这种润滑叫做极压润滑。
切削液的正确选用

切削液的正确选用正确的选用切削液;可以提高金属切削的生产率;保证被加工材料的加工精度..每种切削液都有各自的优缺点;各有各的用途..因此在加工不同的金属材料时需要选用不同的切削液;这样才能使切削液和刀具有效地结合到金属切削加工中..今天;金属切削行业已进入了系统解决方案的年代..过去那种镶嵌法选用的工艺现已被简化;如果还不能称为“科学”的话;至少可称为“技术”..各种等级的刀具、涂层及断屑装置等因素都应结合在一起统筹考虑和设计;使其适应更大的应用范围和工件材料;更有效地进行加工..然而有时候;金属切削加工中有一个问题往往容易忽略;那就是如何适当地选用切削液..将今天的系统方法应用于金属切削加工;需要正确地使用合适于金属加工的切削液;这与其它因素一样;已成为解决方案中的同样重要部分..实际上;现在至少有一家公司正在将切削液和刀具有效地结合到金属切削系统之中..当你选用以后的切削液时;应考虑到以下一些因素:四个关键问题在选用切削液时;有四大关键问题需要考虑;这些问题是:1. 你在切削加工中加工的是什么材料2. 在你使用的切削液中含有哪些化学成分3. 你现在使用的是什么切削液4. 有哪些切削液可供你选用5. 你喜欢哪种切削液6.你在切削加工的是什么材料第一个问题是:你在切削加工中加工的是什么材料回答这个问题往往是最困难的;因为在正常的情况下;大多数车间内所加工的工件材料是各种各样的..如果答案毫不含糊的说是“铝”或“不锈钢”或“铸铁”;切削液的选用就可能相当简单和直截了当..可惜在大批量生产的工厂;这样的情况极少.. 如果所切削加工的绝大部分零件为铝或有色金属;那末切削加工时就必须采用非污染型切削液..一般来说;所使用的切削液为加有特殊成分的半合成液体;可防止有色金属工件的双金属腐蚀和污染..如果有色金属占绝大部分;选用通用的半合成或混合切削液比较经济..第二个问题是:在你的切削液中含有哪些化学成分这个问题可能涉及到切削液使用的成败原因..很少有工厂会花费必要的资金;去投资安装采用等离子技术或逆向渗透技术的有效水净化系统.. 可惜在重新配制切削液的过程中;所使用水中的化学成分对切削液的性能和油箱的使用寿命会产生相当大的差别..大部分切削液生产厂将会做一些必要的用水试验;以确定溶解于水中的矿物质含量;并根据试验结果来推荐使用切削液..第三个问题是:你现在使用的是什么切削液解答这一问题有助于缩小选用切削液的范围..结合目前使用的切削液优缺点进行客观的分析;就能很快地对这一问题做出答复;使你在相对较少的、具有竞争性的各种替代切削液中选用;以满足你的切削要求.. 今天所使用的多数切削液都是以前所沿用下来的..如果一家公司永远不思进取的话;他们最终必将会被其竞争对手所取代;这是今天市场的严酷现实..第四个问题是:有哪些切削液可供你选用这个问题关系到一种切削液的最终选择..根据化学特性;切削液一般可分为4大类型;它们分别是:可溶解的油类------照字面解释;这种油可在水中溶合扩散;合成液------一种完全不含油的人造可溶性冷却液;半合成液------一种含有30 %矿物油的天然和合成润滑剂混合液;混合液------含有约15 %矿物油的特种半合成切削液..每种切削液都有各自的优缺点;因此各有各的用途..此外;在某些特殊的应用领域;各类切削液之间都提供有性/价比..例如;对某一特定的使用领域;也许混合液和半合成液都很适用;而使用混合液也许初期费用较高;但可提高油箱使用寿命;相反;一些半合成液可循环使用;或排放量少;比较经济;但油箱的使用寿命不那么长..在这种情况下;最终的决策取决于使用这种切削液车间的具体经济效益以及业主的个人喜好..可溶性油类可溶性油类是指那些加入乳化剂以后能够溶合扩散在水中的油类..这种切削液一般适合于各种有色金属、碳钢、铸钢等的中等和重型切削加工和磨削加工以及其他的应用领域;例如同时出现铝和钢等不同金属的应用场合..它们也适用于车削、钻削、攻丝、铰孔、切齿、拉削、内圆磨削和无心外圆磨削..可溶性油类对铝材和铜材具有优良的防腐蚀控制功能;良好的防腐臭控制功能;可延长切削液的使用寿命和提高无故障工作性能;其良好的浓缩性能和混合稳定性;通过微量的搅拌;可以很理想的使其与水混合..例如Valenite公司的VNTr-650就是一种适合于重型切削加工的可溶性油类..合成液合成液是一种完全无油的溶液;由聚合体、有机和无机材料与水混合配制而成..这类透明、低泡沫和生物性稳定的冷却液对有色金属、碳钢或铸铁的机加工和磨削加工十分理想..它们的复合润滑剂使这种合成液特别适合于难以加工的材料;例如不锈钢和高温合金..某些合成液专门适用于因侧面造成磨损的初期故障状态..有些合成液虽然有许多优点;但可能会引起有色金属的污染..半合成液半合成液由油类、合成乳化剂及水混合配制而成..它们的开发主要用于航空、核电及有关工业..因此;对于各种有色金属;如钛、铝、紫铜、黄铜、青铜和不锈钢的机加工和磨削加工;它们的工作性能都非常好..半合成液也适用于黑色金属的加工..它们不含氯;因此降低了双金属腐蚀和对金属的污染..使用时;根据不同严格程度的操作要求;采用5%~8 %的水稀释液..混合液混合液是专为满足用户的特殊要求和解决特殊的问题而配制的切削液..例如Valenite公司的VNTr-800切削液是专为铸铁的机加工和磨削加工而开发的;使用这种切削液的工作环境非常干净;其在硬水中的性能比较稳定;可以很好地排斥废油;从而提高了它的生物化学特性..在机加工和磨削加工中;混合液的工作性能特别优秀;适合于对各种金属的加工..使用时;应根据不同的水质情况;混合配制成5%~7 %的水稀释液..最后一个问题是:你喜欢哪一种切削液一般在有几种切削液供你选用的情况下;才会提出这一问题..在这种情况下;还是会涉及到目前你所使用的是哪一种切削液;关键是应客观地检查一下你的喜好;特别要分清这种喜好背后的真正原因..如果你说不出为什么喜欢某种切削液而不喜欢另一种切削液的特别原因;最好还是听从专业人员对你要求的分析;采纳他们的建议..今天;选用正确的切削液要比从前容易的多;因为可接受的、能提高金属切削生产率的系统解决方法在不断增加..像今天能够很容易地正确选用镶刀片和断屑装置那样;对于切削液来说;可以同样容易地选用全套解决方案的日子也不远了..答案已经提供了;其结果将由你选用正确切削液所花的时间来证实..刀具材料对切削液选用的影响刀具钢刀具:其耐热温度约在200-300℃之间;只能适用于一般材料的切削;在高温下会失去硬度..由于这种刀具耐热性能差;要求冷却液的冷却效果要好;一般采用乳化液为宜..·高速钢刀具:这种材料是以铬、镍、钨、钼、钒有的还含有铝为基础的高级合金钢;它们的耐热性明显地比工具钢高;允许的最高温度可达600℃..与其他耐高温的金属和陶瓷材料相比;高速钢有一系列优点;特别是它有较高的坚韧;适合于几何形状复杂的工件和连续的切削加工;而且高速钢具有良好的可加工性和价格上容易被接受..使用高速钢刀具进行低速和中速切削上;建议采用油基切削液或乳化液..在高速切削时;由于发热量大;以采用水基切削液为宜..若使用油基切削液会产生较多油雾;污染环境;而且容易造成工件烧伤;加工质量下降;刀具磨损增大..·硬质合金刀具:用于切削刀具的硬质合金是由碳化钨WC、碳化钛TiC、碳化钽TaC和5-10%的钴组成;它的硬度大大超过高速钢;最高允许工作温度可达1000℃;具有优良的耐磨性能;在加工钢铁材料时;可减少切屑间的粘结现象..在选用切削液时;要考虑硬质合金对骤热的敏感性;尽可能使刀具均匀受热;否则会导致崩刃..在加工一般的材料时;经常采用干切削;但在干切削时;工件温升较高;使工件易产生热变形;影响工件加工精度;而且在没有润滑剂的条件下进行切削;由于切削阻力大;使功率消耗增大;刀具的磨损也加快..硬质合金刀具价格较贵;所以从经济方面考虑;干切削也是不合算的..在选用切削液时;一般油基切削液的热传导性能较差;使刀具产生骤冷的危险性要比水基切削液小;所以一般选用含有抗磨添加剂的油基切削液为宜..在使用冷却液进行切削时;要注意均匀地冷却刀具;在开始切削之前;最好预先用切削液冷却刀具..对于高速切削;要用大流量切削液喷淋切削区;以免造成刀具受热不均匀而产生崩刃;亦可减少由于温度过高产生蒸发而形成的油烟污染..·陶瓷刀具:采用氧化铝、金属和碳化物在高温下烧结而成;这种材料的高温耐磨性比硬质合金还要好;一般采用干切削;但考虑到均匀的冷却和避免温度过高;也常使用水基切削液..·金刚石刀具:具有极高的硬度;一般使用于切削..为避免温度过高;也象陶瓷材料一样;许多情况下采用水基切削液..切削液及其选用一、前言合理选用冷却润滑液;可以有效地减小切削过程中的摩擦;改善散热条件;而降低切削力;切削温度和刀具磨损;提高刀具耐用度;切削效率和已加工表面质量及降低产品的加工成本..随着科学技术和机械加工工业的不断发展;特别足大量的难切削材料的应用和对产品零件加工质量要求越来越高;这就给切削加工带来了难题..为了使这些难题获得解决;除合理选择别的切削条件外;合理选择切削液也尤为重要..二.切削的分类1.水溶液:其主要成分是水..由于水的导热系数是油的导热系数三倍;所以它的冷却性能好..在其中加入一定量的防锈和汕性添加剂;还能起到一定的防锈和润滑作用..2.乳化液:1普通乳化液:它是由防锈剂;乳化剂和矿物油配制而成..清洗和冷却性能好;兼有防锈和润滑性能..2防锈乳化液:在普通乳化液中;加入大量的防锈剂;其作用同上;用于防锈要求严格的工序和气候潮湿的地区..3极压乳化液:在乳化液中;添加含硫;磷;氯的极压添加剂;能在切削时的高温;高压下形成吸附膜;起润滑作用..3.切削油:1矿物油:有5、7、10、20、30机械油和柴油;煤油等;适用于一般润滑..2动;植油及复合油:有豆油、菜子油、棉子油、蓖麻油、猪油等..复合油是将动、植、矿三种油混合而成..它具有良好地边界润滑..3极压切削油:它是以矿物油为基础;加入油性;极压添加剂和防锈剂而成..具有动;植物油良好地润滑性能和极压润滑性能..三.切削液的作用1.冷却作用:它可以降低切削温度;提高刀具耐用度和减小工件热变形;保证加工质量..一般的情况下;可降低切削温度50~150℃..2.润滑作用:可以减小切屑与前刀面;工件与刀具后刀面的摩擦;以降低切削力;切削热和限制积屑瘤和鳞刺的产生..一般的切削油在200℃左右就失去润滑能力..如加入极压添加剂;就可以在高温600~1000℃、高压1470~1960MPa条件下起润滑作用..这种润滑叫做极压润滑..3.清洗作用:可以将粘附在工件;刀具和机床上的切屑粉末;在一定压力的切削液作用下冲洗干净..4.防锈作用:防止机床、工件、刀具受周围介质水分、空气、手汗的腐蚀..四.冷却润滑液中的添加剂1.油性添加剂:动植物油、脂肪酸及其皂、脂肪醇及多元醇、酯类、酮类、胺类等化合物..2.极压添加剂:含硫、磷、氯等有机化合物..如氯化石腊、四氯化碳、硫化磷酸盐、二烷基二硫代磷酸锌等..含硫的极压切削油在切削过程中和金属起化学反应;生成硫化铁;它的熔点高1193℃;硫化膜在高温下不被破坏;在切削钢件时;能在1000℃左右的高温下;仍保持润滑性能;含氯的极压添加剂;如氯化石腊含氯量为40~50%;它的化学性能活泼;在200℃~300℃时和金属起化学反应;氯化物的摩擦系数低于硫化物;有良好地润滑性能;可耐600℃的高温;含磷极压添加剂;与钢铁接触即被吸附;生成磷酸铁化学润滑膜;降低摩擦;比硫氯的效果更为良好..如三种复合使用;润滑效果更为显着..3.防锈添加剂:1水溶性防锈添加剂:亚硝酸钠、磷酸三钠、磷酸氢二钠、苯甲酸钠、苯甲酸胺、三乙醇胺等..2油溶性防锈添加剂:石油磺酸钡、石油磺酸钠、环烷酸锌、三壬基萘磺酸钡等..4.防霉添加剂:苯粉、五氯粉、硫柳汞等化合物..加入万分之几的防霉添加剂;可杀死细菌和抑制细菌生长;以防切削液变质发臭..5.抗泡沫添加剂:二甲基硅油..以防止切削液的使用效果..6.助溶添加剂:乙醇、丁乙醇、苯二甲酸脂、乙二醇醚等..7.乳化剂:1阴离子型:石油磺酸钠、油酸钠皂、松香酸钠皂、高炭酸钠皂、磺化蓖麻油、油酸、三乙醇胺..2非离子型:聚氧乙烯脂肪醇醚平平加、聚氧乙烯烷基酚醚0P、山梨糖醇油酸酯司本、聚氧乙烯山梨糖醇油酸酯吐温..8.乳化稳定剂:乙二醇、乙醇、正丁醇、二乙二醇单正丁基醚、二甘醇、高碳醇、苯乙醇胺、三乙醇胺等..五.常用冷却润滑液的配方1.切削油:1矿物油:5、7、10、20、30机械油和轻柴油、煤油..机械油的号数越大;粘度越大..2植物油:豆油、菜子油、棉子油、蓖麻油等..3复合油:煤油50%+机械油50%;豆油50%+5..高速机油50%..4极压切削油:①氯化石腊20%+二烷基二硫代磷酸锌1%+高速机油79%..②氯化石腊40%+二烷基二硫代磷酸锌1%+石油磺酸钙1%+苯骈三氮唑0.2%+乙醇0.56~0.8%+5高速机油余量..③硫化棉子油7%+5高速机械油93%..④氯化石腊20%+5高速机械油80%..2.乳化液:1普通乳化液:3~5%乳化油70%+5机械油+22%脂肪酸及其皂+0.5%松香酸钠皂+4.5%乙醇+3%石油磺酸钠加水稀释..2极压乳化液:用5~20%极压乳化油10%石油磺酸钠+6%石油磺酸铅+4%氯化石腊+3%氯化硬脂酸+3%油酸+3%三乙酸胺+20机械油余量加水稀释..3防锈乳化液:是在普通乳化液中增加防锈剂的比例而成..3.水溶液:1用0.25~0.5%亚硝酸钠+0.25~0.3%无水碳酸钠+水余量..23%油酸钠皂+0.5%亚硝酸钠+水余量..310%癸二酸+17.5%三乙醇胺+8%亚硝酸钠+水余量..六.冷却润滑液的选择1.选择原则1.1根据工件材料选择1铸铁、青铜在切削时;一般不用切削液..精加工时;用煤油..2切削铝时;用煤油..3切削有色金属时;不宜用含硫的切削液..4切削镁合金时;用矿物油..5切削一般钢时;采用乳化液..6切削难切削材料时;应采用极压切削液..1.2根据工艺要求和切削特点选择1粗加工时;应选冷却效果好的切削液..2精加工时;应选润滑效果好的切削液..3加工孔时;应选用浓度大的乳化液或极压切削液..4深孔加工时;应选用含有极压添加剂浓度较低的切削液..5磨削时;应选用清洗作用好的切削液..6用硬质合金、陶瓷和PCD、PCBN刀具切削时;一般不用切削液..要用时;必须自始自终地供给..PCBN刀具在切削时;不能用水质切削液..固为CBN在1000℃以上高温时;会与水起化学反应而被消耗..2.选用2.1碳钢1粗加工:a3~5%乳化液..b铅油或红丹粉10%+机械油90%;用于粗车蜗杆..2精加工:a10~20%的乳化液..b10~15%极压乳化液..c硫化棉子油的切削油..d20%氯化石腊+80%变压器油或30%豆油+20%煤油+50%高速机械油;用于精车丝杠..eccl420%+80%机械油;用于精车蜗杆..3拉削、攻丝、铰孔:a10~20%极压乳化液..b含氯的切削油..c含硫;氯的切削油..d含硫化棉子油的切削油..e含硫;氯;磷的切削油..f30%煤油+70%机械油;用于光刀.. gMoS2与机械油混合;用于攻丝..4滚齿;插齿:a10~20%极压乳化液..b含硫;磷;氯的极压切削油..5钻孔:a3~5%乳化液..b5~10%极压乳化液..2.2合金钢1粗加工:a3~5%乳化液..b5~10%极压乳化液..2精加工:a10~20%乳化液..b10~15%极压乳化液..c含硫化棉子油的切削油..3拉削、攻丝、铰孔:a10~20%极压乳化液..b含硫、磷、氯极压切削油..c40机械油85%+二烷基二硫代磷酸锌5%+石油磺酸钙7%+二硫化钼1%氯化石腊1%+煤油1%..用于攻丝..效果:Vc从1m/min提高到7m/min;丝锥耐用度提高1~3倍;表面粗糙度由Ra6.3降低为Ra3.2..4滚齿、插齿:a10~20%极压乳化液..b极压切削油..5钻孔:a3~5%乳化液..b5~10%极压乳化液..cccl4和煤油的混合液钻膜具钢小孔..d氯化石腊20%+二烷基二硫代磷酸锌1%+高速机油79%..2.3不锈钢1粗加工:a3~5%乳化液..b10~15%极压乳化液..c极压切削油..d硫化油含硫2%的机械油..2精加工:a极压切削油..b10~15%乳化液..c15~20%极压乳化液..d硫化油或硫化油80~85%+ccl415~20%..e矿物油78~80%+黑机油或植物油和猪油18%+硫1.7%..f机械油90%+ ccl410%..h煤油50%+油酸25%或植物油25%..i煤油60%+松节油20%+油酸20%..3拉削、攻丝、铰孔:a15~20%极压乳化液..b极压切削油..c硫化豆油或植物油..d在硫化油中加ccl410~20%或在猪油中加20~30%ccl4或在硫化油中加10~15%煤油用于铰孔..e在硫化油中加入15~20%ccl4或白铅油加机械油或煤油稀释氯化石腊或MoS2切削膏用于攻丝..4滚齿、插齿:a20~25%极压乳化液..b极压切削油..5钻孔:a10~15%乳化液..b10~20%极压乳化液..c极压切削油..d硫化油..eMoS2切削剂..f用肥皂涂抹在小钻头上;用于在台钻小孔..2.4高温合金1粗加工:a3~5%乳化液..b10~15%极压乳化液..c极压切削油..d硫化油..e硫酸钾2%+亚硝酸钾1%+三乙醇胺7%+硼酸7~10%+甘油7~10%+水余量..f葵二酸7~10%+亚硝酸钠5%+三乙醇胺7~10%+硼酸7~10%+甘油7~10%+水余量..2精加工:a10~25%乳化液..b15~20%极压乳化液..c极压切削油..d煤油75%+油酸25%..3拉削、攻丝、铰孔:a10~20%极压乳化液..b极压切削油..c参照不锈钢所用切削液..d防锈和电解切削液也适合于拉削和铰孔..4钻孔:a10~15%乳化液..b10~20%极压乳化液..c极压切削油..d硫化油..eMoS2切削剂..2.5钛合金1粗加工:a3~5%乳化液..b极压乳化液..2精加工:a极压切削油石油磺酸钠10%+油酸3%+石油磺酸铅6%+三乙醇胺3.5%氯化石腊4%+氯化硬脂酸3%+20机械油70.5%..b极压水溶液氯化脂肪酸;聚氯乙烯0.5~0.8%+磷酸三钠0.5%+三乙醇胺1~2%+亚硝酸钠1.2%+水余量..cCCl4+等量的酒精..3拉削、攻丝、铰孔:a极压切削油..b蓖麻油..c油酸..d硫化油..e氯化油f蓖麻油60%+煤油40%g聚醚30%+酯类油30%+7机械油30%+防锈剂与抗泡剂10%;用于拉削..4钻孔:a极压乳化液..b极压切削油..c电解切削液癸二酸7~10%+三乙醇胺7~10%+甘油7~10%+硼酸7~10%亚硝酸钠3~5%+余下水..d硫化油..e30机械油60%+煤油40%或30机械油70%+煤油30%..2.6铸铁、黄铜1粗加工:a10~15%乳化液..2精加工:a煤油..b煤油与矿物油的混合油..3拉削、攻丝、铰孔:a10~15%乳化液..b10~20%极压乳化液..c煤油..d煤油与矿物油的混合油..2.7紫铜1粗、精加工:a3~5%乳化液..b煤油..c煤油与矿物油的混合油..d菜子油..2滚齿、插齿:a10~25%乳化液..b10~20%极压乳化液..c煤油..d煤油与矿物油的混合油..3钻孔:a3~5%乳化液..b煤油..c煤油与矿物油的混合油..2.8铝及其合金1粗、精加工:a3~5%乳化液..b煤油..c煤油与矿物油的混合油..d菜子油..2拉削、攻丝、铰孔、滚齿、插齿:a10~15%乳化液..b10~15%极压乳化液..c煤油..d煤油与矿物油的混合油..3钻孔:a3~5%乳化液..b煤油与矿物油的混合油..C煤油..2.9青铜1粗精加工及钻孔:a一般不用切削液..可用3~5乳化液..2拉削、攻丝、铰孔、滚齿、插齿a10~20%乳化液..b10~15%极压乳化液..c含氯的切削油..2.10高强度钢采用合金钢的切削液..用豆油或菜子油攻丝较好..2.11钼用ccl4加20机械油或用MoS2润滑脂..2.12纯铁用碳素钢的切削液..精加工时;可用酒精稀释蓖麻油作切削剂..2.13橡胶切削时用酒精或蒸馏水..磨削时;用苏打1%+亚硝酸钠0.25~0.5%+甘油0.5~1%+余下水..附:一.固体润滑剂——MoS21.特点:MoS2的摩擦系数很小;仅0.05~0.09;它的润滑膜有很高的抗压能力及附着能力;粘附在金属表面的二硫化钼薄膜;能承受3500MPa的压力不被破坏;有很高的化学稳定性;不易与酸碱起作用;温度稳定性好;在400℃左右才分解;当二硫化铝混于油或脂中;与空气接触不充分;氧化温度还可以提高..2.应用:它有油剂;水剂和润滑脂三种;也可将二硫化钼与硬脂酸和石腊制成腊笔..用时将二硫化钼润滑剂涂在刀具表面上;可以成倍地提高刀具耐用度和降低工件表面粗糙度;降低切削力;切削热;抑制积屑瘤的产生..二.MoS2在切削中的作用1.在车削方面:1在刀具上涂MoS2;刀具耐用度可提高一倍以上..2在精车蜗杆时;在切削剂中加2%的MoS2;可降低工件表面粗糙度..3铰65Mn孔时;在乳化液中加1%MoS2或铰不锈钢孔时;在乳化液中加3%MoS2;不仅工件表面粗糙度低;而且刀具耐用度高..2.在磨削方面:在砂轮表面上涂上MoS2;工件表面粗糙度可降低一级..3.在切削齿轮方面:在硫化油中加0.5~1%MoS2油剂后;切屑瘤可消除..4.在复杂刀具方面:在拉削和推削加工时;在原切削液中添加15~20%的MoS2油剂后;刀具寿命提高近60倍;工件表面粗糙度可降一级..5.在攻丝方面:它是润滑性能良好的攻丝切削剂..特别是在挤压攻丝时;唯有MoS2的润滑效果最好..6.在锯切方面:在锯条上涂上MoS2后;锯切时噪音小;锯条不易损坏..7.在难切削材料方面:如切削钛合金;高温合金;不锈钢时;在刀具上涂MoS2;效果也十分好根据工件材料选用切削液工件材料的性能对切削液的选择很重要..据文献介绍;可把被加工材料按其可切削性的难易划分为不同级别;以此作为选择切削液的依据..将铜在固定条件下的可切削性指数定为100;将其他材料的相同的条件下进行切削;按得出的刀具相对耐用度进行排列..·普通可切削钢;包括非合金钢、低合金钢及其淬火钢15;35;15CrMn、易切削钢Y12;Y12Mn、建筑钢材35;60;可切削系数为80;较难切削钢;包括高合金钢及其淬火钢20CrMo;42CrMo、高铬合金钢1Cr17;4Cr13、高铬镍合金钢12CrNi2、耐腐蚀耐酸的铬镍钢0Cr18Ni9;1Cr18Mo10Nb、铸钢;可切削系数为50;·难切削钢;包括镍和镍合金Ni10Cr10;Ni18Cr20、锰和镍硅钢40CrMn2;60Si2Mn、铬钼钢20CrMo、硅钢38Si2Mn、钛和钛合金;可切削系数为25;·灰铸铁和可锻铸件HT250;KTZ450-06;可切削系数为60-110;·有色金属;铜和铜合金ZCu Sn10Pbl;可切削系数为100-600;轻金属;铝和镁合金LF5;LF10;LDI;可切削系数为300-2000..切削指数越小的材料越难加工..在选择切削液时;对于难加工的材料应选择活性度高的含抗磨极压添加剂的切削液;对于易加工材料;可选用纯矿油或其他不含极压添加剂的切削液..切削加工是一个复杂过程;尽管是切削一种材料;但当切削速度改变或切削工件的几何形状改变时;切削液显示的效果就完全不同;所以在选择切削液时要结合加工工艺和加工工件的特点来综合考虑..。
- 1、下载文档前请自行甄别文档内容的完整性,平台不提供额外的编辑、内容补充、找答案等附加服务。
- 2、"仅部分预览"的文档,不可在线预览部分如存在完整性等问题,可反馈申请退款(可完整预览的文档不适用该条件!)。
- 3、如文档侵犯您的权益,请联系客服反馈,我们会尽快为您处理(人工客服工作时间:9:00-18:30)。
切削液的选用与维护1概述切削液作为一种金属切削加工介质,由于其属于边缘、交叉学科范畴,常常被忽视,但它在金属切削加工中被广泛采用,且起着十分重要的作用。
它能帮助提高切削加工的质量和生产效率,降低生产成本,改善加工环境。
随着切削加工效率、切削加工材料及加工质量的不断提高,切削液的作用显得越来越很重要,对切削液的要求越来越高。
近年,我国机械制造业,特别是汽车行业的发展迅速,对切削液的数量需求大增,它带动了切削液技术的快速进步与发展。
目前,市场上国内和国外品牌切削液品种繁多,其性能、价格差异很大,如同类国产与国外品牌切削液之间价格相差4-6倍,不同类型国产或国外品牌切削液之间价格相差1-4倍。
选用合适的切削液,能在提高金属切削加工质量,降低加工成本,改善加工环境方面,取得最大的效益。
此外,切削液在使用过程中有许多参数需要控制,如切削液浓度1%的变化即可在加工零件上明显地表现出来,能直接导致零件加工质量的下降或刀具的异常消耗。
因此,如何正确选择使用切削液,并做好切削液使用中的维护工作,是我们在金属切削加工中不容忽视的重要课题。
2切削液的功能与类型(1)切削液的功能切削液的主要功能是润滑与冷却。
它可以减缓刀具(砂轮)的磨损,提高刀具耐用度,降低加工工件的表面粗糙度值,减少工件的热变形,提高加工效率。
切削液的另两项重要功能是清洗与防锈。
即它可以冲走加工区域的切屑,减少切屑及灰尘的粘结,改善和提高加工表面的清洁度,防止工件、刀具、机床生锈或腐蚀。
此外,考虑到切削加工的经济性和环境方面要求,切削液还需具备下列功能:贮存稳定性、乳化稳定性、泡沫抑制性,与机床密封材料、油漆等的相容性,对人体、环境无害或损害少等。
(2)切削液的类型切削液的分类方法很多,最主要,也是被各国普遍采用的是ISO6743/7分类法,它将切削液分为油基型和水基型,水基型可进一步分为乳化液、半合成液(或微乳液)及合成液。
它们的主要区别如表一所示。
油基切削液由纯矿物油、动植物油或以油为主体,添加极压剂调合而成。
油基切削液润滑性能好,冷却性能差,水基切削液则相反,但其成本低,操作环境安全、干净。
随着水基切削液性能的不断提高,其使用范围逐渐扩大。
乳化液由矿物油加入乳化剂和其它添加剂组成,其含油量>60%,溶于水后形成乳白色乳状液。
合成切削液可分为无机盐型和全合成型,它不含油,添加剂含量可达50%以上,具有极好的冷却性和清洗性。
无机盐型合成切削液以无机盐为主,润滑性差;全合成切削液全部采用合成添加剂,各项性能都较优异,是有发展前途的一类切削液。
半合成切削液以水为载体,加入5-30%的油和大量表面活性剂及多种添加剂调合而成,它兼有乳化液和合成切削液的优点,是目前研究最多,应用最广的一类切削液。
不同类型切削液具有各自的特征,但决定切削液性能优劣的是各种添加剂。
常用的添加剂有:油性剂、极压剂、表面活性剂、乳化剂和乳化稳定剂、防锈剂、杀菌剂、消泡剂、抗氧剂等。
一种添加剂能解决一方面的问题,必须同时添加多种添加剂才能赋予切削液优良的综合性能。
如半合成切削液除添加大量表面活性剂外,还需添加油性剂、极压剂、防锈剂、杀菌剂、消泡剂、PH值调整剂等多种添加剂。
3切削液的选用选用切削液主要应从切削加工要求、切削液自身性能质量、环境适应性、管理方便性、综合应用成本等五个方面进行考虑。
(1)根据切削加工要求选用切削液对一般材料的粗加工,以减少切削力和刀具磨损为主,可选用有一定润滑性、冷却性好的切削液;精加工以改善工件表面粗糙度为主,应选用润滑性好的切削液;对高速加工,刀具常处于边界润滑状态,应选用润滑性、渗透性好,极压性高的切削液,如加工中心,适宜选用含油量>20%、表面张力<35dyn∕cm2、PB值>900N的半合成切削液。
对重负荷加工,如滚齿、拉削等,则适宜选用含极压剂的油基切削液。
对内孔、深孔加工,由于切削液不易浇注到加工表面,要求切削液有极好的渗透性,应选用表面张力<30dyn∕cm2,且有良好润滑性的切削液。
磨削产生热量大,要采用冷却性好的切削液;对CBN磨,由于CBN易于水解,要求切削液易在砂轮表面形成油膜以抑制水解,应选用具有良好润滑性、冷却性的切削液。
(2)根据切削液自身性能质量选用切削液能满足同一加工方式要求的切削液可能不只一种,这时我们要研究不同类型或品种切削液的性能差异,选用性能质量较好的切削液。
如对磨削加工,乳化液、半合成切削液、无机盐型合成液,全合成切削液都可采用,其中乳化液清洗性较差,无机盐型合成液易析出固体颗粒而影响机床导轨运行,采用含油量低的半合成切削液和全合成切削液效果最好。
同一类型的不同品种切削液之间性能质量差异很大,要从其理化性能评定和工艺应用试验中找出差异,正确选用。
如半合成切削液不同品种之间,由于采用油性剂和极压剂的不同,其PB值低的只有700N,高的高达1200N,低PB值的只适于磨削加工,高PB值的则适用范围很广。
所采用稳定剂不同,切削液的贮存和使用稳定性不一样,稳定性好适用水质范围广,易发挥出其各项性能,稳定性差的则易分解、使用寿命短;所采用防锈剂不同,有时在理化性能分析和使用初期可能看不出差异,由于不同防锈剂与Fe2+等加工中产生或水中存积的金属离子结合速度大不一样,结合速度快的,会使切削液的防锈性快速下降,造成切削液消耗量高。
(3)根据环境适应性选用切削液不论何种切削液都对环境有一定的负面影响。
油基切削液使用中产生的油污、油雾危害操作工人的身体健康,还有着火的危险;水基切削液的一些添加剂有毒,废水排放污染环境。
在选用切削液过程中,对其环境适应性应充分重视。
特别是十堰是南水北调的源头,对企业的排放在不久会加大限制,我们要早作准备。
油基切削液应逐步减少使用,乳化液使用寿命短、排放量大,要限制使用,含亚硝酸盐等致癌或毒性大物质的切削液要禁止使用,半合成切削液和全合成切削液相对排放量少、污染轻,应扩大使用。
在保证切削液综合性能的基础上,研发和推广使用低毒或无毒、长寿命、易降解的绿色切削液是未来的发展方向。
(4)根据管理维护的方便性选用切削液一个工厂或车间内,会有许多不同的机床和加工方式,对切削液的要求会不一样,甚至差别很大。
如果我们采用的切削液品种太多,使用和管理很麻烦。
应尽可能减少应用切削液品种,选用适用范围广的切削液以满足不同加工方式的要求。
如在我厂的连杆车间有40余台使用切削液的机床,加工方式包括磨、钻、拉、锪、铣、扩、铰、镗、珩磨等9种,连杆材料难加工,以前使用切削液多达6种,错领错用现象时有发生;后经选用高性能的全合成切削液,能满足大多数加工要求,使应用切削液品种降为3种,只有3台机床使用不同的切削液,因此其管理维护大为方便,应用2年多来没有发生错领错用现象。
(5)根据综合应用成本选用切削液降低生产成本是企业永恒的主题,选用切削液也必须考虑成本因素。
但我们不应只考虑切削液本身的价格,应还考虑切削液的寿命、使用维护成本、加工件质量、刀具消耗、废液处理成本等因素。
如对集中冷却系统,若系统功能完备,采用性能优良,寿命长,价格较高的切削液经济些;若系统无过滤功能或过滤功能差,则应选择能满足加工要求,价格较低的切削液。
对我厂的不同冷却系统,都是根据这一原则选用切削液,均取得了较好的经济效益。
总之,选用切削液,应综合考虑上述五方面的因素,满足加工要求是选用的基础,切削液自身性能质量是选用的保证,满足环境适应性和管理维护的方便是发展的需要,降低切削液的综合应用成本是我们追求的目标。
4切削液的维护切削液在使用过程中,除自身性能外,有许多因素会影响使用效果,只有辅以良好、正确的维护,才能充分发挥出切削液的各项性能优势,延长切削液的寿命,降低成本。
冷却系统一般分为单机冷却系统和集中冷却系统两种方式,对两者的维护方式有些差别。
(1)单机冷却系统的切削液维护单机冷却系统指为一台机床供液的冷却系统,一般冷却箱体积<1.5m3。
由于冷却箱体积小,补充切削液和水的周期短,由专业人员维护很难做到,一般由机床操作工维护。
为便于维护,一般在切削液原液中加入足量的杀菌剂、消泡剂等助剂,以减少维护难度,操作工仅控制切削液浓度。
比较好的,也是在我厂应用中行之有效的两种控制切削液浓度方式是:1)为车间配备一个加液小车,操作工按固定的比例在小车内配液,再将配置好的切削液加到机床冷却箱。
2)由集中冷却系统或集中配液箱将配置好的切削液泵送到各机床冷却箱。
切削液使用一段时间后,出现产生发臭等异味、颜色变深变灰暗、加工质量下降或刀具消耗异常等一个多个问题时,应更换切削液。
换液前要对冷却箱、排屑机构、机床进行彻底清洁。
(2)集中冷却系统的切削液维护集中冷却系统是指为多台设备集中供液的冷却系统,一般指冷却箱体积>5m3的系统。
由于系统冷却箱容积大,便于浓度等指标的控制,一般由专业人员进行维护。
切削液的使用周期可达几个月到几年,维护过程包括加液前冷却系统的清洁,使用中现场的管理控制和实验室控制。
1)加液前冷却系统的清洁切削液在使用一个周期排放后,冷却箱、回液沟和机床尾部残存有大量的污泥与残液。
这些污泥与残液中藏有大量的细菌,若不彻底清除,加切削液后,细菌会快速繁殖,从而降低切削液的使用寿命。
应在集中冷却系统排空后,先铲除干净冷却箱、地沟、机床中残留的金属屑、油污和淤泥,然后在系统冷却箱中加入其容积30-50%左右的水和2%浓度的清洗剂及一定量的杀菌剂,循环清洗1-3个小时,若一次清洗不干净,应再次加清洗剂清洗,直到彻底清洗干净集中冷却系统和机床的各个区域的杂质并杀死残留细菌,再用适量(能满足系统水泵正常工作)的清水循环清洗半水时左右,将残留清洗液漂洗干净。
有些集中冷却系统由于设计上的缺陷,致使系统无法彻底排空和清洗干净,这会大大降低切削液的正常使用寿命。
如我厂491发动机生产线中有几个系统即是如此,在同样维护条件下,切削液在其中的使用寿命只及在其它系统中的1/3。
因此在设备订货时对冷却系统的便于维护性应作充分考虑。
2)使用中现场的管理控制集中冷却系统的现场管理控制应在专业人员的指导下专人进行,具体应做好如下几点:①遵守调配程序和要求。
切削液调配时应在箱体内先加水,再加切削液,不能反向操作,同时要严格按检验人员的要求及时补加切削液和其它添加剂。
②定期监控。
对系统中切削液的液位、污染程度等要定期观察,液位低应及时补水补液,油污重则应及时除油,有异常情况及时反馈给技术人员。
定期查看冷却系统设备各部份的运行状况,有设备故障要及时排除,否则会影响到切削液的使用寿命或供液质量。
如若周末循环系统出问题,停机时间过长,会使厌氧菌大量繁殖;排屑过滤装置出现故障会使供液的杂质量增加,既影响零件加工精度、增加刀具磨损,又增加了细菌的栖身点。