切削液及其选用分析资料
成形铣床的切削液选用及切削液处理技术

成形铣床的切削液选用及切削液处理技术切削液在成形铣床加工中起着至关重要的作用,它可以有效地降低摩擦、冷却和润滑切削过程,并防止切削工具与工件的磨损,从而提高加工质量和效率。
因此,正确选择适合的切削液,并采用合适的切削液处理技术,对成形铣床的加工效果具有重要影响。
首先,我们来讨论切削液的选用。
切削液的选择应根据不同加工材料、加工工艺和切削条件来确定。
一般来说,切削液可以分为油性和水性两种类型。
油性切削液适用于高速加工和重切削过程,它具有很好的润滑性和较低的揮发性。
油性切削液通常由矿物油、添加剂和抗乳化剂组成,能在高温情况下保持稳定,对切削过程中的高温可以有效保护。
水性切削液适用于低速加工和轻切削过程,它具有良好的冷却性和清洗性能。
水性切削液通常通过在水中加入添加剂来改善性能,如抗菌剂、防锈剂和抗氧化剂等。
此外,水性切削液在环境保护方面有一定的优势,易于处理和回收利用。
然而,切削液的选择不仅仅取决于加工材料和加工工艺,还与切削液的运用方式和成形铣床的设备特性有关。
因此,在选择切削液之前,必须充分了解成形铣床和加工过程的要求。
一般来说,根据不同的切削液需求,可以参考以下几个方面的考虑。
首先,成形铣床的切削液应具有良好的冷却性能。
由于成形铣床加工过程中产生大量的热量,需要切削液及时冷却刀具和工件,防止工件变形和刀具磨损。
其次,切削液应具有良好的润滑性能。
切削液的润滑性能直接影响切削过程的质量和效率。
良好的润滑性能可以减少摩擦,防止刀具与工件的粘连和磨损,同时也有利于切削液的排屑和冷却。
另外,切削液还应具有良好的清洗性能。
切削过程中会产生大量的切屑和切削渣,切削液必须能有效地将其清洗出去,防止切削渣堵塞刀具和导轨。
最后,切削液的稳定性和耐久性也是选择的关键。
稳定的切削液可以延长切削液的使用寿命,减少频繁更换和处理,节约成本。
除了选择合适的切削液,切削液的处理也是非常重要的。
成形铣床加工过程中使用的切削液会受到切削过程中金属切屑、切削渣和杂质等的污染,如果不及时处理,会影响切削液的质量和使用寿命。
适用于数控机床的切削液选择

适用于数控机床的切削液选择数控机床作为现代制造业中不可或缺的设备之一,其切削液的选择和应用对于工件的加工质量、刀具寿命和设备性能都有着至关重要的影响。
本文将就适用于数控机床的切削液选择进行详细的探讨和分析,以帮助读者更好地了解如何选用合适的切削液,提升机床加工效率和性能。
1. 切削液的基本概念和作用切削液是指在数控机床加工过程中,用于冷却、润滑和清洗切削区域的一种液体。
它能有效地降低切削温度,减少工件和刀具的磨损,并促进切屑的排出,从而提高切削效率和加工质量。
切削液的主要作用包括:1.1 冷却切削区域:切削过程中会产生大量的热量,如果不及时冷却,会导致工件变形、刀具破裂等问题。
切削液通过吸收热量并迅速散热,保持切削区域的温度在适宜范围内。
1.2 润滑切削面:切削液能有效地润滑切削面,降低切削过程中的摩擦和热量产生,减少刀具的磨损和工件的表面粗糙度。
1.3 清洗切屑:切削液可以冲洗切屑,防止切屑在切削区域堆积,影响加工质量和刀具的寿命。
2. 切削液的选择原则2.1 适应材料和切削工艺:不同的切削液适用于不同的材料和切削工艺。
在选择切削液时,要充分考虑加工材料的种类和特性,以及切削工艺的要求,确保切削液能够与工件和刀具良好相容,并且满足特定的切削要求。
2.2 具备良好的散热性能:切削液在切削过程中要能够快速吸收和散热热量,降低切削区域的温度。
因此,切削液的导热系数和热传导性能是选择切削液时需要考虑的重要指标。
2.3 具有优异的润滑性能:切削液的润滑性能直接影响切削面的摩擦系数和磨损程度。
选择具有良好润滑性能的切削液可以有效地降低切削过程中的摩擦热量和刀具磨损,提高加工质量和刀具寿命。
2.4 对环境友好:在现代制造业追求绿色环保的潮流下,选择环境友好型的切削液也是一个重要的考虑因素。
环保性能包括切削液的挥发性、毒性和可降解性等方面。
3. 常见的切削液类型及其适应性3.1 油性切削液:油性切削液是最常用的一种切削液,其主要成分是矿物油或合成油。
切削液培训资料

切削液的选用
-磨削加工
➢ 磨削:磨削区域温度较高(800~1000℃),易引起工 作表面局部烧伤;磨削热应力易使工件变形,产生 裂纹;影响表面质量。
➢ 选用要求:良好冷却性和润滑性,一定清洗性和防 锈性。
对应于
➢ 一般磨削-3%~5%合成乳化液 ➢ 精磨削-H-1精磨液 或 5%~10%乳化液 ➢ 超精磨-98%煤油与2%石油磺酸钡混合液 或 含氯极压
切削油 ➢ 难加工材料-极压乳化液 或 极压切削油 ➢ 磨齿磨螺纹-低黏度矿物油 或 极压切削油
切削液选用参考
结束
精加工 铜及合金和铝及合金- 10%~20%乳化 液 或 煤油 或 50%煤油及L-AN10
精加工 铸铁-7%~10%乳化液 或 煤油
切削液的选用
-半封闭加工
半封闭加工如:深孔钻、拉削、攻内螺纹等
刀具半封闭下工作,排屑困难,切削热无法 传出,易烧损刀刃,工件加工表面粗糙。
选用要求:良好的润滑性,一定的冷却性和 清洁性
少切削力、延长刀具寿命、获得较 小加工表面粗糙度
切削液的种类
-水溶性切削液
2.乳化液
➢ 组成:水+乳化油 搅拌 乳白色液体 ➢ 低浓度时以冷却为主,用于粗加工和普
通磨削加工
➢ 高浓度时以润滑为主,用于精加工和复 杂刀具加工
➢ 细分为:防锈、清洗、极压和透明乳化 液4种
切削液的种类
-水溶性切削液
3.水溶液
高温润滑性,较高化学稳定性 涂抹法涂于刀具表面 有效抑制积屑瘤、减小切削力、延长刀
具寿命、减小加工表面粗糙度
切削液添加剂
1.油性添加剂——使金属加工处于边界润滑状态。 用于低速精加工
第8章 切削液

乳化液长期使用以后,容易变质发臭,这是由于细菌繁殖的结果。只要加入 万分之几的防霉添加剂,即可起到杀菌和抑制细菌繁殖的效果。但防霉添加 剂会引起操作者皮肤起红斑、发痒等,所以一般不用。
4.抗泡沫添加剂 切削液中一般都加入防锈添加剂、乳化剂等表 面活性剂,这些物质增加了混入空气而形成泡 沫的可能性。如果泡沫过多,会降低切削液的 效果。若加入百万分之几的抗泡沫添加剂(如 二甲基硅油),可以有效地防止形成泡沫。在 高速强力磨削时,由于会产生比较多的泡沫, 所以必须在磨削液中添加适量的抗泡沫剂,并 作消泡试验。
切削液渗入的途径
见课本图8-1 1.前后刀面的毛细管现象 2.切屑和前刀面相对运动产生泵吸现象 3.第一变形区剪切面的渗透
边界润滑一般分为低温低压边界润滑、高温 边界润滑、高压边界润滑和高温高压边界润 滑四种。 一般的切削油在200℃左右即失去其润滑能力, 因此只适用于低温低压边界润滑摩擦。 而在某些切削条件下,切屑、刀具界面间可 达到600—1000℃左右的高温和1.5— 2.0GPa(150—200kgf/mm2)的高压,这就 形成了高温高压边界润滑,或称极压润滑。
(2)油溶性防锈添加剂:
油溶性防锈添加剂主要应用于防锈乳化液,也有用于切削油的。在
切削液的选择和使用维护 ppt课件

切削液的选择和使用维护
18
4.客户加工方法(如车削、铣削、钻削、 攻螺纹等)
不同的加工方式对切削液的要求不一样。 即使是同一种加工方法,但是加工的精度 可能会是不一样,所以在反馈加工方式时 要反馈具体的加工方式。如车削就分为粗 车,半精车,精车。
切削液的选择和使用维护
19
下面为加工方式的一些简单分类
2
总体上切削液的选择依据有以下几点:
• 加工机床所要求选用 • 加工方式所决定 • 成本(维护,使用等) • 加工材料及刀具 • 加工精度要求 • 润滑性 • 冷却性 • 防锈,清洗 • 水基切削液需求具备废液处理设施
切削液的选择和使用维护
3
2. 选择步奏:
第一步选择:
由安全卫生(起火、冒烟对人体健康的危害 性)、机床、加工工序、前后加工工序为 水基还是油基加工液,废液处理设施来大 概确定选用油基还是水基加工液
切削液的选择和使用维护
11
下面例举了在不同的切削加工中切 削油的水基切削液应用选择情况:
切削液种类 车削、镗削 多轴车削 多工位切削钻削 深孔钻削
水基切削液 切削油
最常用
很少用
很少用
最常用
很少用
最常用
常用
常用
切削液的选择和使用维护
12
滚齿、插齿、刨齿、剃齿 内外圆磨削,平面磨削 高速磨削、强力磨削 槽沟磨削、螺纹磨削 研磨、珩磨 冼削 拉削、绞削 攻丝
切削液的选择和使用维护
312Biblioteka 切削液的一般维护程序1)定期检测切削液使用浓度和pH值等常规项目 2)检查菌落数抑制细菌的生长 3)确保切削液循环管路的畅通并及时排屑,并及时
净化切削液 应及时清除循环管路中的金属屑、金属粉末、霉
切削液知识与选用

切削液知识与选用一、前言合理选用冷却润滑液,可以有效地减小切削过程中的摩擦,改善散热条件,而降低切削力,切削温度和刀具磨损,提高刀具耐用度,切削效率和已加工表面质量及降低产品的加工成本。
随着科学技术和机械加工工业的不断发展,特别足大量的难切削材料的应用和对产品零件加工质量要求越来越高,这就给切削加工带来了难题。
为了使这些难题获得解决,除合理选择别的切削条件外,合理选择切削液也尤为重要。
二.切削的分类1.水溶液:其主要成分是水。
由于水的导热系数是油的导热系数三倍,所以它的冷却性能好。
在其中加入一定量的防锈和汕性添加剂,还能起到一定的防锈和润滑作用。
2.乳化液:(1)普通乳化液:它是由防锈剂,乳化剂和矿物油配制而成。
清洗和冷却性能好,兼有防锈和润滑性能。
(2)防锈乳化液:在普通乳化液中,加入大量的防锈剂,其作用同上,用于防锈要求严格的工序和气候潮湿的地区。
(3)极压乳化液:在乳化液中,添加含硫,磷,氯的极压添加剂,能在切削时的高温,高压下形成吸附膜,起润滑作用。
3.切削油:(1)矿物油:有5#、7#、10#、20#、30#机械油和柴油,煤油等,适用于一般润滑。
(2)动,植油及复合油:有豆油、菜子油、棉子油、蓖麻油、猪油等。
复合油是将动、植、矿三种油混合而成。
它具有良好地边界润滑。
(3)极压切削油:它是以矿物油为基础,加入油性,极压添加剂和防锈剂而成。
具有动,植物油良好地润滑性能和极压润滑性能。
三.切削液的作用1.冷却作用:它可以降低切削温度,提高刀具耐用度和减小工件热变形,保证加工质量。
一般的情况下,可降低切削温度50~150℃。
2.润滑作用:可以减小切屑与前刀面,工件与刀具后刀面的摩擦,以降低切削力,切削热和限制积屑瘤和鳞刺的产生。
一般的切削油在200℃左右就失去润滑能力。
如加入极压添加剂,就可以在高温(600~1000℃)、高压(1470~1960MPa)条件下起润滑作用。
这种润滑叫做极压润滑。
切削液的选择和使用
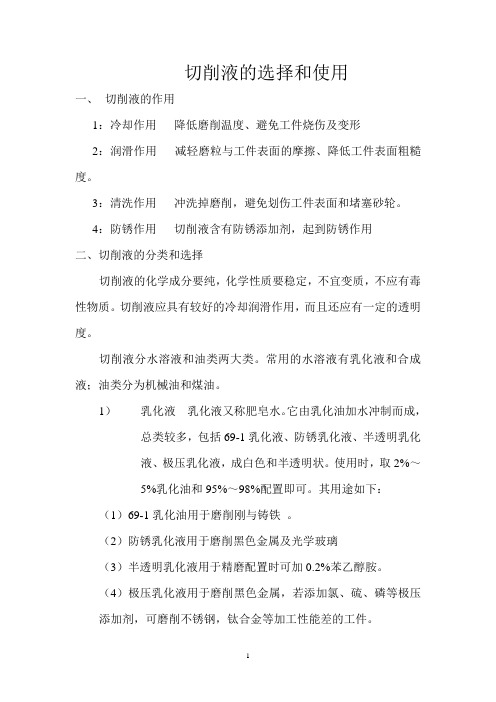
切削液的选择和使用一、切削液的作用1:冷却作用降低磨削温度、避免工件烧伤及变形2:润滑作用减轻磨粒与工件表面的摩擦、降低工件表面粗糙度。
3:清洗作用冲洗掉磨削,避免划伤工件表面和堵塞砂轮。
4:防锈作用切削液含有防锈添加剂,起到防锈作用二、切削液的分类和选择切削液的化学成分要纯,化学性质要稳定,不宜变质,不应有毒性物质。
切削液应具有较好的冷却润滑作用,而且还应有一定的透明度。
切削液分水溶液和油类两大类。
常用的水溶液有乳化液和合成液;油类分为机械油和煤油。
1)乳化液乳化液又称肥皂水。
它由乳化油加水冲制而成,总类较多,包括69-1乳化液、防锈乳化液、半透明乳化液、极压乳化液,成白色和半透明状。
使用时,取2%~5%乳化油和95%~98%配置即可。
其用途如下:(1)69-1乳化油用于磨削刚与铸铁。
(2)防锈乳化液用于磨削黑色金属及光学玻璃(3)半透明乳化液用于精磨配置时可加0.2%苯乙醇胺。
(4)极压乳化液用于磨削黑色金属,若添加氯、硫、磷等极压添加剂,可磨削不锈钢,钛合金等加工性能差的工件。
2)化学合成液是一种新型的切削液,呈透明和半透明状,它是由添加剂、防锈剂、低泡油性剂和清洗剂配置而成。
与乳化液相比能得到更低的工件表面粗糙度值,可达Ra0.025um,并能提高砂轮的耐用度(1)420号切削液用于高速磨削与缓进给磨削。
(2)H-1精磨液用于精密磨削,也适于普通磨削,可代替乳化液(3)透明水溶液用于无心磨床与外圆磨床(4)101切削液可代替油性切削液及乳化液(5)苏打水用于黑色金属与有色金属的磨削3)常用的N7、N10号高速机械油及轻质柴油和煤油(1)极压切削油主要用于超精密磨削,磨削难加工材料,可代替硫化油使用。
(2)F-43极压油由于磨削耐热钢,耐热合金钢及耐腐蚀钢。
(3)N10和N32机械油用于磨削螺纹、齿轮及成型磨削等。
(4)复合油用于珩磨钢、铸铁、青铜、铝合金等材料。
(5)煤油加少量四氯化碳和N15机械油配置,用于磨削铝制工件。
金属加工中的切削液选择与使用

金属加工中的切削液选择与使用金属加工是制造业中的重要环节,其中切削液是不可或缺的助剂。
切削液的作用是冷却和润滑工具与工件表面的接触区域,减少摩擦、磨损和热量积聚,从而延长刀具使用寿命,提高工件精度和表面质量。
本文将从切削液的种类、应用范围、选择标准及使用方法等方面进行探讨。
一、切削液的种类按照成分和用途可将切削液分为机械式、化学式和生物式三种类型。
机械式切削液是以提高冷却效果为主要目的的。
它的主要成分是水和滑动增强剂。
它的优点是价格便宜,易于加工和清洁,但缺点是易挥发,低温冻结,不适合高速加工。
化学式切削液是以提高冷却效果和防锈性能为主要目的。
它可以分为合成切削液、半合成切削液和矿物油基切削液三类。
三者的特点各不相同,如:合成切削液使用寿命长,环境污染小,半合成切削液结合了合成和矿物油基的优点,价格适中,但味道刺鼻,适合低速加工;矿物油基切削液价格低,但易污染环境,应尽量避免使用。
生物式切削液是一种新型环保液体。
它以天然植物油和微生物发酵产生的菌液为基础,添加其他化学物质制成。
生物式切削液的主要特点是生态友好、无毒无害、无刺激性和价格适中。
但是生物式切削液的耐用性不强,应适当增加更换次数,而且需要控制水的硬度和PH值,以保证其稳定性。
二、切削液的应用范围切削液的应用范围很广,适用于各种金属材料的加工,如铁、铜、铝、钢、不锈钢、黄铜等。
不同材料需要使用不同种类的切削液,并在使用过程中不断进行调整。
同时,加工方式也需要考虑,如精密加工和重载加工的切削液需求不同。
切削液选用的关键在于根据工件材料、加工方式和切削液性能等方面进行综合考虑。
不同类型的切削液对不同的金属有不同的应用效果,因此在选择时要多加考虑,以确保加工效果和稳定性。
三、切削液的选择标准在选择切削液时,需要考虑以下几个方面:1.工件材质:不同材质的工件,选用的切削液类型都不相同。
例如,对于易生锈的材料,需要选择具有防锈性能的切削液。
2.加工方式:不同的加工方式,切削液的特性和性能也有所不同。
- 1、下载文档前请自行甄别文档内容的完整性,平台不提供额外的编辑、内容补充、找答案等附加服务。
- 2、"仅部分预览"的文档,不可在线预览部分如存在完整性等问题,可反馈申请退款(可完整预览的文档不适用该条件!)。
- 3、如文档侵犯您的权益,请联系客服反馈,我们会尽快为您处理(人工客服工作时间:9:00-18:30)。
切削液及其选用分析一、前言合理选用冷却润滑液,可以有效地减小切削过程中的摩擦,改善散热条件,而降低切削力,切削温度和刀具磨损,提高刀具耐用度,切削效率和已加工表面质量及降低产品的加工成本。
随着科学技术和机械加工工业的不断发展,特别足大量的难切削材料的应用和对产品零件加工质量要求越来越高,这就给切削加工带来了难题。
为了使这些难题获得解决,除合理选择别的切削条件外,合理选择切削液也尤为重要。
二.切削的分类1.水溶液:其主要成分是水。
由于水的导热系数是油的导热系数三倍,所以它的冷却性能好。
在其中加入一定量的防锈和汕性添加剂,还能起到一定的防锈和润滑作用。
2.乳化液:(1)普通乳化液:它是由防锈剂,乳化剂和矿物油配制而成。
清洗和冷却性能好,兼有防锈和润滑性能。
(2)防锈乳化液:在普通乳化液中,加入大量的防锈剂,其作用同上,用于防锈要求严格的工序和气候潮湿的地区。
(3)极压乳化液:在乳化液中,添加含硫,磷,氯的极压添加剂,能在切削时的高温,高压下形成吸附膜,起润滑作用。
3.切削油:(1)矿物油:有5#、7#、10#、20#、30#机械油和柴油,煤油等,适用于一般润滑。
(2)动,植油及复合油:有豆油、菜子油、棉子油、蓖麻油、猪油等。
复合油是将动、植、矿三种油混合而成。
它具有良好地边界润滑。
(3)极压切削油:它是以矿物油为基础,加入油性,极压添加剂和防锈剂而成。
具有动,植物油良好地润滑性能和极压润滑性能。
三.切削液的作用1.冷却作用:它可以降低切削温度,提高刀具耐用度和减小工件热变形,保证加工质量。
一般的情况下,可降低切削温度50~150℃。
2.润滑作用:可以减小切屑与前刀面,工件与刀具后刀面的摩擦,以降低切削力,切削热和限制积屑瘤和鳞刺的产生。
一般的切削油在200℃左右就失去润滑能力。
如加入极压添加剂,就可以在高温(600~1000℃)、高压(1470~1960MPa)条件下起润滑作用。
这种润滑叫做极压润滑。
3.清洗作用:可以将粘附在工件,刀具和机床上的切屑粉末,在一定压力的切削液作用下冲洗干净。
4.防锈作用:防止机床、工件、刀具受周围介质(水分、空气、手汗)的腐蚀。
四.冷却润滑液中的添加剂1.油性添加剂:动植物油、脂肪酸及其皂、脂肪醇及多元醇、酯类、酮类、胺类等化合物。
2.极压添加剂:含硫、磷、氯等有机化合物。
如氯化石腊、四氯化碳、硫化磷酸盐、二烷基二硫代磷酸锌等。
含硫的极压切削油在切削过程中和金属起化学反应,生成硫化铁,它的熔点高(1193℃),硫化膜在高温下不被破坏,在切削钢件时,能在1000℃左右的高温下,仍保持润滑性能;含氯的极压添加剂,如氯化石腊(含氯量为40~50%),它的化学性能活泼,在200℃~300℃时和金属起化学反应,氯化物的摩擦系数低于硫化物,有良好地润滑性能,可耐600℃的高温;含磷极压添加剂,与钢铁接触即被吸附,生成磷酸铁化学润滑膜,降低摩擦,比硫氯的效果更为良好。
如三种复合使用,润滑效果更为显著。
3.防锈添加剂:(1)水溶性防锈添加剂:亚硝酸钠、磷酸三钠、磷酸氢二钠、苯甲酸钠、苯甲酸胺、三乙醇胺等。
(2)油溶性防锈添加剂:石油磺酸钡、石油磺酸钠、环烷酸锌、三壬基萘磺酸钡等。
4.防霉添加剂:苯粉、五氯粉、硫柳汞等化合物。
加入万分之几的防霉添加剂,可杀死细菌和抑制细菌生长,以防切削液变质发臭。
5.抗泡沫添加剂:二甲基硅油。
以防止切削液的使用效果。
6.助溶添加剂:乙醇、丁乙醇、苯二甲酸脂、乙二醇醚等。
7.乳化剂:(1)阴离子型:石油磺酸钠、油酸钠皂、松香酸钠皂、高炭酸钠皂、磺化蓖麻油、油酸、三乙醇胺。
(2)非离子型:聚氧乙烯脂肪醇醚(平平加)、聚氧乙烯烷基酚醚(0P)、山梨糖醇油酸酯(司本)、聚氧乙烯山梨糖醇油酸酯(吐温)。
8.乳化稳定剂:乙二醇、乙醇、正丁醇、二乙二醇单正丁基醚、二甘醇、高碳醇、苯乙醇胺、三乙醇胺等。
五.常用冷却润滑液的配方1.切削油:(1)矿物油:5#、7#、10#、20#、30#机械油和轻柴油、煤油。
机械油的号数越大,粘度越大。
(2)植物油:豆油、菜子油、棉子油、蓖麻油等。
(3)复合油:煤油50%+机械油50%;豆油50%+5。
高速机油50%。
(4)极压切削油:①氯化石腊20%+二烷基二硫代磷酸锌1%+高速机油79%。
②氯化石腊40%+二烷基二硫代磷酸锌1%+石油磺酸钙1%+苯骈三氮唑0.2%+乙醇0.56~0.8%+5#高速机油余量。
③硫化棉子油7%+5#高速机械油93%。
④氯化石腊20%+5#高速机械油80%。
2.乳化液:(1)普通乳化液:3~5%乳化油(70%+5#机械油+22%脂肪酸及其皂+0.5%松香酸钠皂+4.5%乙醇+3%石油磺酸钠)加水稀释。
(2)极压乳化液:用5~20%极压乳化油(10%石油磺酸钠+6%石油磺酸铅+4%氯化石腊+3%氯化硬脂酸+3%油酸+3%三乙酸胺+20#机械油余量)加水稀释。
(3)防锈乳化液:是在普通乳化液中增加防锈剂的比例而成。
3.水溶液:(1)用0.25~0.5%亚硝酸钠+0.25~0.3%无水碳酸钠+水余量。
(2)3%油酸钠皂+0.5%亚硝酸钠+水余量。
(3)10%癸二酸+17.5%三乙醇胺+8%亚硝酸钠+水余量。
六.冷却润滑液的选择1.选择原则1.1根据工件材料选择(1)铸铁、青铜在切削时,一般不用切削液。
精加工时,用煤油。
(2)切削铝时,用煤油。
(3)切削有色金属时,不宜用含硫的切削液。
(4)切削镁合金时,用矿物油。
(5)切削一般钢时,采用乳化液。
(6)切削难切削材料时,应采用极压切削液。
1.2根据工艺要求和切削特点选择(1)粗加工时,应选冷却效果好的切削液。
(2)精加工时,应选润滑效果好的切削液。
(3)加工孔时,应选用浓度大的乳化液或极压切削液。
(4)深孔加工时,应选用含有极压添加剂浓度较低的切削液。
(5)磨削时,应选用清洗作用好的切削液。
(6)用硬质合金、陶瓷和PCD、PCBN刀具切削时,一般不用切削液。
要用时,必须自始自终地供给。
PCBN刀具在切削时,不能用水质切削液。
固为CBN在1000℃以上高温时,会与水起化学反应而被消耗。
2.选用2.1碳钢(1)粗加工:a)3~5%乳化液。
b)铅油或红丹粉10%+机械油90%,用于粗车蜗杆。
(2)精加工:a)10~20%的乳化液。
b)10~15%极压乳化液。
c)硫化棉子油的切削油。
d)20%氯化石腊+80%变压器油或30%豆油+20%煤油+50%高速机械油,用于精车丝杠。
e)ccl420%+80%机械油,用于精车蜗杆。
(3)拉削、攻丝、铰孔:a)10~20%极压乳化液。
b)含氯的切削油。
c)含硫,氯的切削油。
d)含硫化棉子油的切削油。
e)含硫,氯,磷的切削油。
f)30%煤油+70%机械油,用于光刀。
g)MoS2与机械油混合,用于攻丝。
(4)滚齿,插齿:a)10~20%极压乳化液。
b)含硫,磷,氯的极压切削油。
(5)钻孔:a)3~5%乳化液。
b)5~10%极压乳化液。
2.2合金钢(1)粗加工:a)3~5%乳化液。
b)5~10%极压乳化液。
(2)精加工:a)10~20%乳化液。
b)10~15%极压乳化液。
c)含硫化棉子油的切削油。
(3)拉削、攻丝、铰孔:a)10~20%极压乳化液。
b)含硫、磷、氯极压切削油。
c)40#机械油85%+二烷基二硫代磷酸锌5%+石油磺酸钙7%+二硫化钼1%氯化石腊1%+煤油1%。
用于攻丝。
效果:Vc从1m/min提高到7m/min,丝锥耐用度提高1~3倍,表面粗糙度由Ra6.3降低为Ra3.2。
(4)滚齿、插齿:a)10~20%极压乳化液。
b)极压切削油。
(5)钻孔:a)3~5%乳化液。
b)5~10%极压乳化液。
c)ccl4和煤油的混合液钻膜具钢小孔。
d)氯化石腊20%+二烷基二硫代磷酸锌1%+高速机油79%。
2.3不锈钢(1)粗加工:a)3~5%乳化液。
b)10~15%极压乳化液。
c)极压切削油。
d)硫化油(含硫2%的机械油)。
(2)精加工:a)极压切削油。
b)10~15%乳化液。
c)15~20%极压乳化液。
d)硫化油或硫化油80~85%+ccl415~20%。
e)矿物油78~80%+黑机油或植物油和猪油18%+硫1.7%。
f)机械油90%+ ccl410%。
h)煤油50%+油酸25%或植物油25%。
i)煤油60%+松节油20%+油酸20%。
(3)拉削、攻丝、铰孔:a)15~20%极压乳化液。
b)极压切削油。
c)硫化豆油或植物油。
d)在硫化油中加ccl410~20%或在猪油中加20~30%ccl4或在硫化油中加10~15%煤油用于铰孔。
e)在硫化油中加入15~20%ccl4或白铅油加机械油或煤油稀释氯化石腊或MoS2切削膏用于攻丝。
(4)滚齿、插齿:a)20~25%极压乳化液。
b)极压切削油。
(5)钻孔:a)10~15%乳化液。
b)10~20%极压乳化液。
c)极压切削油。
d)硫化油。
e)MoS2切削剂。
f)用肥皂涂抹在小钻头上,用于在台钻小孔。
2.4高温合金(1)粗加工:a)3~5%乳化液。
b)10~15%极压乳化液。
c)极压切削油。
d)硫化油。
e)硫酸钾2%+亚硝酸钾1%+三乙醇胺7%+硼酸7~10%+甘油7~10%+水余量。
f)葵二酸7~10%+亚硝酸钠5%+三乙醇胺7~10%+硼酸7~10%+甘油7~10%+水余量。
(2)精加工:a)10~25%乳化液。
b)15~20%极压乳化液。
c)极压切削油。
d)煤油75%+油酸25%。
(3)拉削、攻丝、铰孔:a)10~20%极压乳化液。
b)极压切削油。
c)参照不锈钢所用切削液。
d)防锈和电解切削液也适合于拉削和铰孔。
(4)钻孔:a)10~15%乳化液。
b)10~20%极压乳化液。
c)极压切削油。
d)硫化油。
e)MoS2切削剂。
2.5钛合金(1)粗加工:a)3~5%乳化液。
b)极压乳化液。
(2)精加工:a)极压切削油(石油磺酸钠10%+油酸3%+石油磺酸铅6%+三乙醇胺3.5%氯化石腊4%+氯化硬脂酸3%+20#机械油70.5%)。
b)极压水溶液(氯化脂肪酸,聚氯乙烯0.5~0.8%+磷酸三钠0.5%+三乙醇胺1~2%+亚硝酸钠1.2%+水余量)。
c)CCl4+等量的酒精。
(3)拉削、攻丝、铰孔:a)极压切削油。
b)蓖麻油。
c)油酸。
d)硫化油。
e)氯化油f)蓖麻油60%+煤油40%g)聚醚30%+酯类油30%+7#机械油30%+防锈剂与抗泡剂10%,用于拉削。
(4)钻孔:a)极压乳化液。
b)极压切削油。
c)电解切削液(癸二酸7~10%+三乙醇胺7~10%+甘油7~10%+硼酸7~10%亚硝酸钠3~5%+余下水)。
d)硫化油。
e)30#机械油60%+煤油40%或30#机械油70%+煤油30%。
2.6铸铁、黄铜(1)粗加工:a)10~15%乳化液。