2钢铁企业能耗指标管理
2粗钢能耗限额

计 算
高炉工序单位产品能耗的计算 高炉工序单位产品能耗应按式(2)计算: eglz - eglh EGL = —————— ⋯⋯⋯⋯⋯⋯⋯⋯⋯⋯⋯⋯⋯⋯⋯⋯ (2) Pgl 式中: EGL——高炉工序单位产品能耗,单位为千克标准煤 每吨(kgce/t); eglz——高炉工序消耗的各种能源的折标准煤量总和, 单位为千克标准煤(kgce); eglh——高炉工序回收的能源量折标准煤量,单位为 千克标准煤(kgce); Pgl ——高炉工序合格生铁产量,单位为吨(t)。
粗钢生产工序主要能源回收量
高炉炉顶余压发电 ---TRT 在炼铁时,焦炭,铁矿石投入高炉,要 用鼓风机吹进大量热风,热风中的氧气一 旦接触焦炭中的碳,就会立即燃烧,产生 大量煤气.大部分煤气和铁矿石发生化学 反应,分离出铁.余下的煤气就像高压锅 烧开了饭菜一样,从减压阀白白放掉了。 利用这部分余压来发电,称为余压发电。 又叫高炉顶压力发电。
计 算
烧结工序单位产品能耗按式(1)计算: esjz - esjh ESJ = —————— ⋯⋯⋯⋯⋯⋯⋯⋯⋯⋯⋯⋯⋯⋯⋯⋯ (1) Psj 式中:ESJ ——烧结工序单位产品能耗,单位为千 克标准煤每吨(kgce/t); esjz——烧结工序消耗的各种能源的折标准煤量总 和,单位为千克标准煤(kgce); esjh——烧结工序回收的能源量折标准煤量,单位 为千克标准煤(kgce); Psj ——烧结工序合格烧结矿产量,单位为吨(t)
负能炼钢
转炉实现负能炼钢是衡量一个现代化炼钢 厂生产技术水平的重要标志,转炉负能炼 钢意味着转炉炼钢工序消耗的总能量小于 回收的总能量,即转炉炼钢工序能耗小于 零。 转炉炼钢工序过程中消耗的能量主要包括: 氧气、氮气、焦炉煤气、电和使用外厂蒸 汽,而转炉回收的能量主要包括:转炉煤 气和蒸汽回收。传统“负能炼钢技术”定 义是一个工程概念,体现了生产过程转炉 烟气节能、环保综合利用的技术集成。
钢铁行业钢铁企业能源消耗控制制度的建立
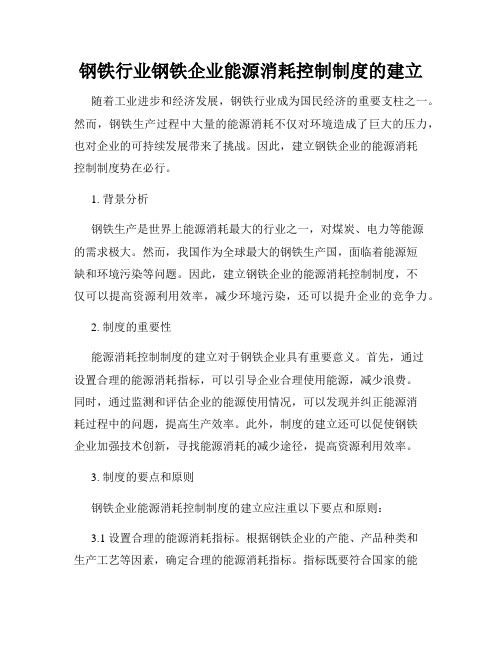
钢铁行业钢铁企业能源消耗控制制度的建立随着工业进步和经济发展,钢铁行业成为国民经济的重要支柱之一。
然而,钢铁生产过程中大量的能源消耗不仅对环境造成了巨大的压力,也对企业的可持续发展带来了挑战。
因此,建立钢铁企业的能源消耗控制制度势在必行。
1. 背景分析钢铁生产是世界上能源消耗最大的行业之一,对煤炭、电力等能源的需求极大。
然而,我国作为全球最大的钢铁生产国,面临着能源短缺和环境污染等问题。
因此,建立钢铁企业的能源消耗控制制度,不仅可以提高资源利用效率,减少环境污染,还可以提升企业的竞争力。
2. 制度的重要性能源消耗控制制度的建立对于钢铁企业具有重要意义。
首先,通过设置合理的能源消耗指标,可以引导企业合理使用能源,减少浪费。
同时,通过监测和评估企业的能源使用情况,可以发现并纠正能源消耗过程中的问题,提高生产效率。
此外,制度的建立还可以促使钢铁企业加强技术创新,寻找能源消耗的减少途径,提高资源利用效率。
3. 制度的要点和原则钢铁企业能源消耗控制制度的建立应注重以下要点和原则:3.1 设置合理的能源消耗指标。
根据钢铁企业的产能、产品种类和生产工艺等因素,确定合理的能源消耗指标。
指标既要符合国家的能源政策和环保要求,也要兼顾企业的实际情况。
同时,应将指标分解到各个生产单元,以便企业能够掌握和管理能源消耗情况。
3.2 建立能源消耗数据监测系统。
通过建立完善的数据监测系统,对钢铁企业的能源消耗进行实时监测和评估。
监测系统应能够准确记录和统计企业的能源消耗情况,并能够提供分析和评估报告,以便企业进行决策和改进。
3.3 加强能源管理和技术创新。
钢铁企业应加强能源管理,推行能源节约技术和先进设备,提高资源利用效率。
同时,鼓励技术创新,寻找能源消耗的减少途径,降低生产成本,提高竞争力。
4. 推行制度的建议为了有效推行钢铁企业的能源消耗控制制度,可从以下几个方面着手:4.1 完善相关法律法规。
加大对钢铁企业能源消耗控制的立法力度,设立相关规章制度,明确企业的能源消耗责任,加大对不合规企业的处罚力度。
钢铁行业单位产品能耗限额标准

钢铁行业单位产品能耗限额标准
钢铁行业的单位产品能耗限额标准因不同的产品种类和生产工艺而有所不同。
在中国,针对钢铁行业,国家制定了相应的能耗限额标准,其中包括了不同的产品种类的能耗限额标准。
以下是一些常见的钢铁产品能耗限额标准:
1. 转炉钢吨钢综合能耗:≤ /t;
2. 电炉钢吨钢综合能耗:≤ /t;
3. 轧钢综合能耗:≤ /t;
4. 高炉炼铁工序单位产品能耗:≤ 437kgce/t;
5. 转炉炼钢工序单位产品能耗:≤ 122kgce/t;
6. 电炉炼钢工序单位产品能耗:≤ 120kgce/t;
7. 烧结工序单位产品能耗:≤ /t;
8. 球团工序单位产品能耗:≤ /t。
需要注意的是,这些标准是针对不同的钢铁产品种类和生产工艺而制定的,而且随着技术的不断进步和环保要求的提高,这些标准也在不断更新和调整。
因此,在实际生产中,钢铁企业需要按照最新的标准进行节能降耗,以实现可持续发展。
钢铁工业能源现状和管理

钢铁工业能源现状和管理1. 简介钢铁工业是现代工业领域中的重要组成部分,它对经济发展和社会进步具有重要意义。
然而,钢铁生产过程中对能源的需求量大、能耗高,给能源资源带来了巨大压力。
为了可持续发展和减少环境负荷,钢铁工业必须重视以及改善能源管理。
本文将从以下几个方面探讨钢铁工业能源现状和管理:能源消耗情况、环境影响、节能技术、管理措施和未来发展展望。
2. 能源消耗情况钢铁工业是能源密集型行业,对能源的需求非常大。
其主要能源消耗包括三个方面:原料预处理、高炉冶炼和炼钢。
其中,高炉冶炼占据了最大的能源消耗比重。
根据统计数据,我国钢铁工业每年消耗的能源约占全国工业总能源消耗量的15%左右。
3. 环境影响由于钢铁工业对能源的高度依赖和消耗,其对环境的影响也不可忽视。
钢铁生产过程中会产生大量的二氧化碳、氮氧化物等大气污染物,对大气质量造成了一定程度的破坏。
同时,钢铁工业在原料开采、废水排放以及废渣处理等环节也对水资源和土壤环境产生了一定程度的压力。
4. 节能技术为了减少能源消耗和降低环境负荷,钢铁工业需要采取一系列的节能技术。
以下是一些常用的节能技术:•高炉余热回收利用技术:通过回收和利用高炉煤气中的余热来提高能源利用效率。
•动态控制技术:通过实时监测和控制钢铁生产过程中的能耗和排放情况,使生产过程达到最佳能源利用效率。
•热再循环技术:将钢铁生产过程中产生的热能再循环利用,减少能源的浪费。
•新型燃料使用技术:采用新型的低碳燃料,如天然气、生物质能源等,来替代传统的煤炭、焦炭等高碳燃料,降低碳排放量。
5. 管理措施除了采用节能技术外,钢铁工业还需要建立完善的能源管理体系,强化能源管理措施。
以下是一些常见的管理措施:•能源审计:定期对钢铁生产过程中的能源消耗情况进行审计和评估,发现问题并提出改进措施。
•员工培训:加强对员工的节能意识培养和能源管理知识培训,提高员工的能源利用效率。
•制定能源消耗指标:设定合理的能源消耗目标,对能源利用情况进行定量评价,并对能源消耗指标进行动态调整。
钢铁工业的能效评估方法与节能减排措施
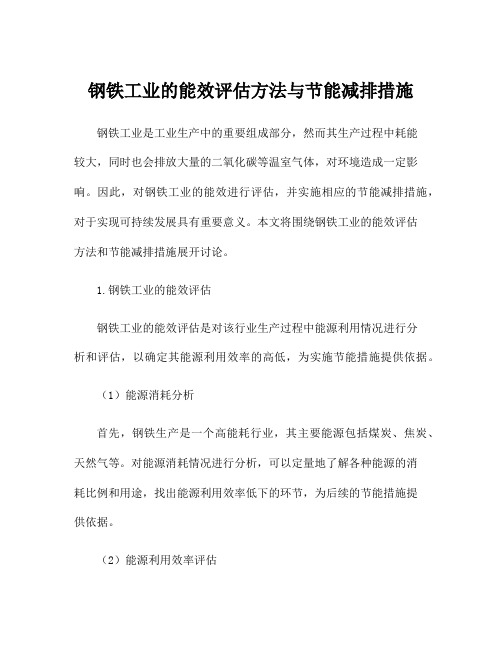
钢铁工业的能效评估方法与节能减排措施钢铁工业是工业生产中的重要组成部分,然而其生产过程中耗能较大,同时也会排放大量的二氧化碳等温室气体,对环境造成一定影响。
因此,对钢铁工业的能效进行评估,并实施相应的节能减排措施,对于实现可持续发展具有重要意义。
本文将围绕钢铁工业的能效评估方法和节能减排措施展开讨论。
1.钢铁工业的能效评估钢铁工业的能效评估是对该行业生产过程中能源利用情况进行分析和评估,以确定其能源利用效率的高低,为实施节能措施提供依据。
(1)能源消耗分析首先,钢铁生产是一个高能耗行业,其主要能源包括煤炭、焦炭、天然气等。
对能源消耗情况进行分析,可以定量地了解各种能源的消耗比例和用途,找出能源利用效率低下的环节,为后续的节能措施提供依据。
(2)能源利用效率评估评估钢铁工业的能源利用效率,可以采用各种能源利用效率的评价指标,如单位产量能耗、煤气化率、电耗等。
通过与国家标准或行业标准进行比较,以确定其能源利用效率的优劣,并分析生产过程中存在的能源浪费现象。
(3)环境影响评估能效评估还需要考虑钢铁工业生产对环境的影响。
通过对二氧化碳、二氧化硫等污染物排放情况进行分析,评估其对环境的影响程度,为节能减排措施的制定提供参考。
2.节能减排措施在进行能效评估的基础上,钢铁工业可以采取以下节能减排措施,提高生产过程中的能源利用效率,减少对环境的影响。
(1)技术改造和设备更新钢铁生产过程中存在许多能源浪费的环节,通过技术改造和设备更新,可以提高生产线的能效。
比如改进高炉煤气的利用率、优化焦炉技术、采用高效的节能设备等,都可以有效减少能源消耗。
(2)资源综合利用钢铁工业生产所需的原料和能源较为丰富,可以通过资源综合利用,实现能源的互补和循环利用。
比如利用余热发电、煤气替代燃料等,都可以减少对传统能源的依赖,降低生产过程中的能源消耗。
(3)管理优化通过优化生产计划和工艺流程,合理安排生产时间和设备运行状态,可以减少因生产计划不合理而造成的能源浪费现象。
钢铁工业主要工序能耗指标2015解析

1.1
南京
1.0
5
吨坯氩气消耗
Nm3/t
/
0.6
南京
1.0
天铁
18.22/110
汽动鼓风/电动鼓风
6
吨铁新水耗
m3/t
1.5
0.12
南昌钢厂
0.12
7
吨铁蒸汽消耗
kg/t
/
13.32
莱钢
13.32
8
高炉热风炉吨铁燃料消耗
GJ/t
/
1. 89
宝钢
1.89
二
能源回收指标
1
吨铁TRT发电量
湿法除尘
kWh/t
≥30
28
首钢
30
干法除尘
kWh/t
≥35
52
太钢
52
四
10
25
AOD炉吨钢水氧气消耗
Nm3/t
32
26
AOD炉吨钢水氮气消耗
Nm3/t
25
27
AOD炉吨钢水燃气消耗
GJ/t
0.05
四
连铸
(一)
方坯连铸
1
工序能耗
kgce/t
6.0
3.6
莱钢
5.5
2
吨坯电耗
kWh/t
/
10
南京
11/9
有/电磁搅拌
3
吨坯新水消耗
t/t
/
0.15
莱钢
0.2
4
吨坯氧气消耗
Nm3/t
序号
指标名称
单位
国家标准先进值[2]
近年行业先进值
标杆指标
备注
指标
企业名称
一
钢铁工业主要工序能耗指标

附件1 钢铁行业主要生产工序能耗指标标杆值之欧侯瑞魂创作
表1-1 粗钢综合性指标标杆值
表1-2 焦化工序标杆值
表1-3 烧结工序标杆值
表1-4 球团工序标杆值
表1-5 炼铁工序标杆值
表1-6 转炉炼钢工序标杆值
表1-7 电炉炼钢工序标杆值
表1-8 轧钢工序标杆值
注[1]:国家尺度指《焦炭单位产品能源消耗限额》(GB21342-2008)
注[2]:国家尺度指《粗钢生产主要工序单位产品能源消耗限额》(GB21256-2007)、《清洁生产尺度钢铁行业(烧结)》(HJ/T426-2008)、《清洁生产尺度钢铁行业(高炉炼铁)》(HJ/T427-2008)、《清洁生产尺度钢铁行业(炼钢)》
(HJ/T428-2008)、国标《钢铁企业节能设计规范》(2010年送审稿)。
能源行业能源消耗指标

能源行业能源消耗指标随着社会的进步和发展,能源问题日益凸显。
能源消耗是一个关系到国家经济发展和社会可持续发展的重要指标。
为了提高能源利用效率、减少能源浪费,各行业都应制定相应的规范、规程和标准,以引导和规范能源消耗行为。
本文将从工业、建筑、交通、农业和生活五个行业的角度,论述各行业的能源消耗指标。
一、工业行业的能源消耗指标工业是能源消耗的主要领域,对节能减排的要求更加迫切。
针对不同行业的特点、工艺和设备情况,工业行业应根据国家相关政策,制定科学合理的能源消耗指标。
1. 钢铁行业钢铁行业是能源消耗大户,特别是高炉炼铁工艺的能源消耗占比较高。
为了提高钢铁行业的能源利用效率,可以制定以下能源消耗指标:(1)钢铁企业能源消耗总量控制指标:根据企业规模、工艺流程和产品质量要求,制定相应的能源消耗总量控制指标,引导企业在生产过程中控制能源消耗。
(2)单位产品能耗指标:根据钢铁产品的品种和规格,确定单位产品能耗指标,促进企业提高能源利用效率,降低单位产品能耗。
2. 化工行业化工行业是能源消耗和排放较大的行业,对于降低化工生产过程中的能源消耗是一个重要课题。
可以制定以下能源消耗指标:(1)单位产值能耗指标:针对不同的化工产品,制定单位产值能耗指标,鼓励企业用先进的工艺技术和设备,降低能源消耗。
(2)产品能源综合利用率指标:引导企业在生产过程中提高产品能源综合利用率,降低产品的能源消耗水平。
二、建筑行业的能源消耗指标建筑行业是能源消耗的重要领域,建筑能耗占全社会能源消耗的比重较高。
为了推动建筑行业向绿色、低碳和可持续方向发展,可以制定以下能源消耗指标:1. 建筑能耗限额指标建筑能耗限额指标是根据建筑的类型和用途,制定相应的能耗限额,要求建筑达到或低于限额。
这可以通过建筑节能设计和智能化控制系统来实现。
2. 建筑节能评价指标建筑节能评价指标考虑建筑结构、保温、通风、采光等方面的节能要求,评估建筑的节能性能。
根据评价结果,为建筑行业制定相应的节能改造和提升措施。
- 1、下载文档前请自行甄别文档内容的完整性,平台不提供额外的编辑、内容补充、找答案等附加服务。
- 2、"仅部分预览"的文档,不可在线预览部分如存在完整性等问题,可反馈申请退款(可完整预览的文档不适用该条件!)。
- 3、如文档侵犯您的权益,请联系客服反馈,我们会尽快为您处理(人工客服工作时间:9:00-18:30)。
钢铁企业能耗指标管理钢铁企业能源统计指标体系是钢铁企业能源管理的重要基础工作,研究能源统计指标体系有助于企业间能效对标,制定切实可行的措施,通过加强能源精细化管理和实施节能技术改造,并促进和推动企业能源管理水平和能效指标的持续改善。
技术经济指标是指与生产技术密切相关,反映企业对原材料、能源、人力、设备等资源的利用状况及其效果的指标。
能源消耗是钢铁企业生产中最重要的资源消耗之一,费用占钢铁生产成本的25%~35%,不仅关系到企业的生产经营和成本效益,而且涉及到整个国家的资源有效利用问题,因此,钢铁企业能源消耗指标是一个非常重要的技术经济指标。
一、企业能源消耗指标能源消耗指标管理是企业能源标准化管理的重要内容之一,也是用行业统一控制的能源检测计算方法、能源消耗指标管理企业生产的手段,是正确确定企业能源需要量,编制能源供需量的重要依据,同时也是产品成本核算的重要基础。
对于降低消耗,节约能源,提高经济效益,具有重要的意义。
(一)能源消耗指标的管理内容能源消耗指标包括单位能源消耗量和用能总量指标两种。
单位能源消耗量指标是指在一定的生产工艺、技术装备和组织管理条件下,生产单位产品所规定的能源消耗量。
用能总量指标是对能源消耗量如产品产量关系不大的工序所规定的能源消耗总量。
根据能源消耗管理的需要和用能单位的实际情况,可采取单项能源消耗指标、工艺消耗指标、综合能源消耗指标、用能总量指标等不同种类。
能源消耗管理的内容:1.建立能源消耗管理体系;2.适时修订能源指标;3.采取有效的技术措施,保证能源消耗指标的实现;4.考核分析能源消耗指标完成情况,总结经验,提出改进措施。
(二)能源消耗指标管理的作用能源消耗指标是编制能源供需计划的重要依据。
企业实行了先进合理的能源消耗指标管理,才能正确计算企业能源需要量,编制出准确的、科学的能源供需计划,预算企业能源成本。
能源消耗指标是科学地组织能源供应的重要基础。
企业制定先进合理的能源消耗指标,才能严格地按质、按量、按时组织能源供应计划,做好各项能源的平衡计划,并对消耗情况实施控制,从而保证生产的正常进行。
能源消耗指标是监督和促进企业内部开展节能工作的有力工具。
企业为了使其能源消耗指标经常保持在先进合理的水平上,就必须不断提高用能技术水平和能源管理水平。
能源消耗指标是企业加强经济核算和节能奖惩的依据。
(三)能源消耗指标的制定及制定方法1.能源消耗指标制定的原则“定质”与“定量”相统一的原则。
能源消耗指标的制订应该包括“定质”与“定量”两个方面。
定质,是确定所需要能源的品种、规格和质量要求,定量,是确定能源消耗的数量。
先进性和合理性相统一原则。
能源消耗指标必须反映生产过程中的技术水平和生产组织管理水平。
能源消耗指标的先进性,是指在满足工艺需要的前提下,充分考虑所能实现的各项节能措施效果,使制定的能源消耗指标能够比已达到的实际水平先进。
能源消耗指标合理性,是指指标必须是切合实际可行的、有科学依据的,是经过努力可以达到的。
因此,用能单位按照本单位能源消耗的历史最好水平和现行的生产工艺状况,核定能源消耗指标。
能源消耗指标的制订必须遵循从实际出发,深入生产第一线,进行调查研究,了解情况,掌握资料,实际测算,适当的科学分析,精确的核算等原则;制定的能源消耗指标应迅速及时,走在生产之前,对生产起指导和促进作用;依靠长期的指标资料积累和经常了解分析生产情况,使能源消耗指标准确;钢铁企业按照可计量性、工艺要求性以及便于核算考核性制定能源消耗指标;能源消耗指标制定既具有先进性,又要切实可行,对能源消耗尚未达到行业平均水平的,其指标要从严核定,以利于调动一切积极因素。
2.能源消耗指标制定的依据(1)国家和地方有关能源消耗限额标准;(2)近三年能源消耗计量统计资料和历史最好水平资料;(3)近三年生产技术经济指标,如产量、品种、质量等;(4)年度生产计划、技术经济指标;(5)所耗能源的品种、品质、规格;(6)生产技术及工艺的发展趋势,实施节能技改的情况;(7)国内外同类产品单位能耗先进水平。
3.能源消耗指标制定的方法制定能源消耗指标的主要方法有:技术计算、实际测定和统计分析三种。
钢铁企业目前基本上是用统计分析法辅以技术计算法、实际测定法来确定指标,统计分析法与实际接近,涵盖环境和计量偏差影响因素,便于管理与考核。
为了提高能源消耗指标的准确性和可靠性,应以技术计算法和实际测定法制定能源消耗指标。
技术计算法。
技术计算法是根据产品设计、工艺过程、管理水平等各方面因素,通过精确计算,并考虑达到的先进能耗指标水平和采用节能技术措施等因素后制定能源消耗指标的一种方法。
实际测定法。
实际测定法是根据现场能源消耗的条件,通过能源消耗测定,用实际计算方法确定能源消耗指标。
实际测定法也可以通过对现有设备(工序)进行能量平衡测试,计算出该工序或设备的某种能源实际数量,再结合设备改造,改进操作和其他节能措施的实施,最后确定该设备(工序)的能源消耗指标。
统计分析法。
统计分析法是指在分析研究资料,并全面考虑有关工艺技术、操作技术水平、能源供应质量等因素的基础上制定出来的能源消耗指标。
(四)能源消耗指标的修订由于影响能源消耗指标的各种因素是在不断变化的,因此能源消耗指标必须定期修改或临时修改,一般单项指标每年修改一次,遇到下述情况时,可做必要的临时修改:1.能源消耗执行过程中,发现能源消耗指标脱离实际或计算错误时;2.产品结构、用能设备和生产工艺有重大改变时;3.提高生产或改进操作时;4.能源品种、规格、质量等发生重大改变时。
由于能源消耗规律的作用,要求能源消耗指标具有相对稳定性。
因此,能源消耗指标一经确定,不宜经常改动,只做定期(如一年)修订,以便于贯彻执行。
(五)能源消耗指标的执行与考核能源消耗指标考核是指标管理的又一重要环节,将制定的能源消耗指标与执行消耗指标的实际结果经常进行比较,找出偏差,并分析研究产生偏差的原因,以便及时贯彻执行。
1.考核的目的与意义(1)通过生产实践的检验,考核制定的能源消耗指标是否合理。
(2)通过能源消耗指标的考核,与历史最好水平,与国内外先进水平对标,找出差距,努力改进。
(3)通过能源消耗考核,积累完整的历史资料,为指导生产和有效地进行能源管理提供科学依据。
2.考核方式由于能源消耗指标管理采取分级管理制,所以能源消耗指标的考核应与能源消耗指标的制定、贯彻执行相一致,进行分级考核。
即由公司对厂部,厂部对车间,车间对班组考核,或按工艺流程实行“一条龙”考核。
随着能源消耗指标的细化,考核工作也将越来越细。
3.考核内容能源消耗指标考核的主要内容和深度大体上分以下三级:(1)考核到单项产品的单项能耗(2)考核到单项产品的综合能耗(3)考核到单项工艺的单项能耗和综合能耗应当指出,国家《“十二五”节能减排综合性工作方案》把“合理控制能源消费总量”提升到很高的高度,把合理控制能源消费总量作为转变经济发展方式的重要着力点。
能源总量控制将对各地的经济增长速度产生重大影响,将比节能指标更加严厉。
这也标志着政府从“十一五”单纯的能耗强度控制转变到强度和总量双控制、绝对指标和相对指标想结合的考核方式。
这不仅要靠企业内部管理、节能措施等节能手段,还要靠淘汰落后,工艺改进等措施控制能源消费量。
二、企业节能量节约能源的目的在于充分有效地发挥现有能源的作用,使相同的能源消耗,生产出更多符合市场和用户需求的产品,也就是以最少的能源消费取得更大的经济效益。
能源节约量的计算就是反映能源在使用过程中的节约和浪费情况,研究提高能源利用率的有效途径。
(一)节能量概念与计算1.节能量的概念节能量是指报告期内实际能源消耗量与某个基准值总量之间的相对差值。
因此,节能量是个相对的量,随着选择作为对比用的基准量不同,其数值亦不相同。
节能量有两类,一类是与自身比较的节能量,如与上年同期相比的节能量,它反映了企业在能量利用水平上的提高与进步,是一种实际节能量;一类是与他人相比较的节能量,如与标准能耗指标相比或与标杆企业指标对比的节能量,反映了企业的实际用能水平,是一种名义节能量。
钢铁企业节能量是指在一定时期内,通过加强生产经营管理,提高生产技术水平、调整生产结构、进行节能技术改造等措施,所节约的能源数量,综合反映企业直接节能和间接节能的总成果,是考核企业节能工作的重要指标。
企业节能量可分为产品节能量、产值节能量、技术节能量、产品结构节能量和单项能源节能量等。
计算时,根据不同的目的和要求,采用不同的比较基准。
2.节能量的计算(1)综合节能量吨钢综合能耗节能量=(报告期吨钢综合能耗-基期吨钢综合能耗)×报告期钢产量(2)单位产品能耗节能量某种产品单位能耗节能量=(报告期该种产品单位能耗-基期该种产品单位能耗)×报告期该种产品产量(3)技术措施节能量指企业在生产同样数量和质量的产品或提供同样的工作量的条件下,采用某项节能技术措施后所减少的能源消费量。
它是评价描述技术项目节能效果的指标。
计算公式:技术措施节能量=[-]×采取技术措施后的产品产量采取技术措施前的能源消费量是指企业在技术改造措施项目开工之前一种或几种能源综合的实际消费量。
技术措施后的能源消费量是指企业在进行了某项技术改造措施后而实际消费的一种或几种综合能源数量。
(4)提高产品质量的节能量。
指企业生产同样数量的产品,在提高产品质量的情况下,而减少的能源消费量。
计算公式:提高产品质量的节能量=(报告期生产定额能耗量-基期生产定额能耗量)×报告期比基期减少的废品量(5)降低损失的节能量。
指企业在报告期,由于实际损失率比计划规定的损失率低,所节约的能源数量。
计算公式:降低损失的节能量=(实际损失率-计划规定的损失率)×报告期能源消耗量(6)提高能源利用率的节能量。
是指企业报告期内的能源利用率高于基期的能源利用率,所节约的能源数量。
计算公式:提高利用率的节能量=(-)×报告期能源消耗量(7)产品结构节能量。
指假定在企业单位综合能源消费量不变的情况下,由于企业产品生产结构变化而少用(或超用)的能源数量。
计算公式:结构节能=Σ[(报告期某产品产量占全部产量-基期某产品产量占全部产量的比重)×基期该产品单位综合能源消费量]×报告期全部产品产量(8)单一能源品种节约量。
指根据单位产品产量单项能耗计算的节能量,反映企业某一种能源(如煤、油、电等)的节约量。
如单位产品节煤量计算公式:单位产品产量节煤量=(报告期某单位产品产量煤炭消耗量-基期某单位产品产量煤炭消耗量)×报告期该产品产量单位产品产量节电量、节油量计算公式类似。
(二)节能率、年平均节能率计算节能率指在一定时间范围内单位产出能耗的降低速率。