焦炉气甲醇生产工艺流程
焦炉气制甲醇工艺

焦炉气制甲醇工艺工艺流程说明来自压缩工段的焦炉气(123℃,3.0MPaA)经加热炉预热后,与来自空分的经氧气加热器加热后 3.5MPaA氧气经转化炉喷嘴混合后在转化炉内发生不完全燃烧反应,放出大量的热量,气体温度迅速升高,同时CH4发生转化反应。
转化炉出口的高温转化气(CH4<0.4)直接进入中压废热锅炉,产生4.0MPaG蒸汽。
降温后的转化气进入蒸汽过热器/锅炉给水加热器,过热甲醇合成来的2.5MPaG饱和蒸汽,加热甲醇合成废锅和本工段中压废热锅炉用锅炉给水。
然后转化气经脱盐水加热器降温后进入水洗塔降温洗涤后,送至NHD脱硫工段。
水洗塔塔底分离掉的冷凝液送至造气的浊循环水系统。
脱盐水站来脱盐水经脱盐水加热器加热后送至锅炉房。
氧气加热器用本工段产的4.0MPaG饱和蒸汽加热。
中压废热锅炉产的4.0MPaG饱和蒸汽除部分供氧气加热器用,其余经加热炉加热至450℃后送至管网。
加热炉用燃料气主要为甲醇合成闪蒸气和甲醇精馏不凝气及甲醇合成非渗透气。
**焦炉煤气经过过滤器滤去油雾和预脱硫槽脱除无机硫后,经加氢转化器加氢转化进入中温脱硫槽脱除绝大部分无机硫,经过二级加氢转化器将残余的有机硫进一步转化,再经中温氧化锌脱硫槽把关,使气体中的总硫达到0.1ppm,出氧化锌脱硫槽的气体送往转化装置。
焦炉煤气和氧气分别进入转化炉上部后立即进行氧化反应放出热量,并很快进入催化剂层,反应后的转化气由转化炉底部引出经一些列管换热冷凝后,由气液分离器分离工艺冷凝液,经氧化锌脱硫槽脱除气体中残余的硫并送往合成气压缩工段。
转化气经合成压缩机一、二段压缩至5.5MPa,然后进入循环段与来自甲醇合成的循环气在缸内混合,压缩至6.0MPa后送至甲醇合成工段。
公司用电(万KWh)17145.4:主要生产14498.4,辅助2647。
甲醇生产:焦炉煤气(万m3)41268 折标0.6052电力(万KWh)10546.3蒸汽(t)511240输出驰放气(万m3)16664 产量(t)211339蒸汽(t)329591。
焦炉煤气甲醇基本工艺流程图的说明
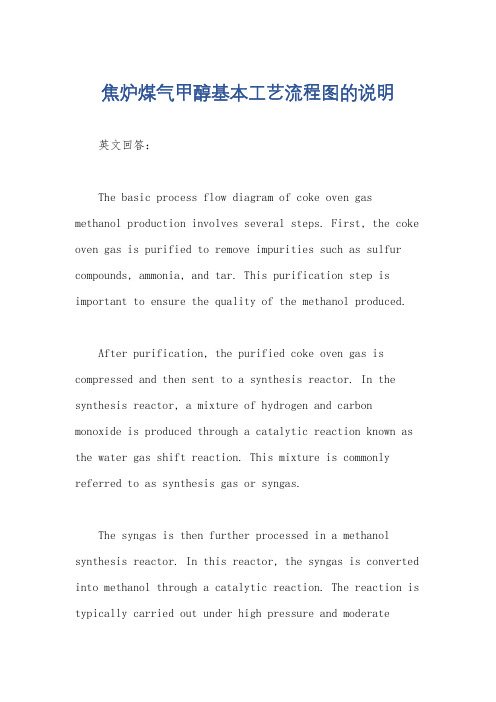
焦炉煤气甲醇基本工艺流程图的说明英文回答:The basic process flow diagram of coke oven gas methanol production involves several steps. First, the coke oven gas is purified to remove impurities such as sulfur compounds, ammonia, and tar. This purification step is important to ensure the quality of the methanol produced.After purification, the purified coke oven gas is compressed and then sent to a synthesis reactor. In the synthesis reactor, a mixture of hydrogen and carbon monoxide is produced through a catalytic reaction known as the water gas shift reaction. This mixture is commonly referred to as synthesis gas or syngas.The syngas is then further processed in a methanol synthesis reactor. In this reactor, the syngas is converted into methanol through a catalytic reaction. The reaction is typically carried out under high pressure and moderatetemperature conditions to maximize the conversion of syngas into methanol.Once the methanol synthesis reaction is complete, the methanol is separated from the reaction mixture through distillation. Distillation is a process that utilizes the differences in boiling points of the components in the mixture to separate them. The purified methanol is then collected and further processed to meet the desired specifications.After purification, the methanol can be used as a fuel or as a raw material for the production of various chemicals and materials. It is commonly used as a solvent, antifreeze, and in the production of formaldehyde, acetic acid, and methyl tert-butyl ether (MTBE), among other products.Overall, the basic process flow diagram of coke oven gas methanol production involves purification of the coke oven gas, synthesis of syngas, methanol synthesis, and distillation of methanol. The final product can be used forvarious applications in industries such as chemicals, fuels, and materials.中文回答:焦炉煤气甲醇的基本工艺流程图涉及几个步骤。
十万吨焦炉煤气制甲醇的操作规程
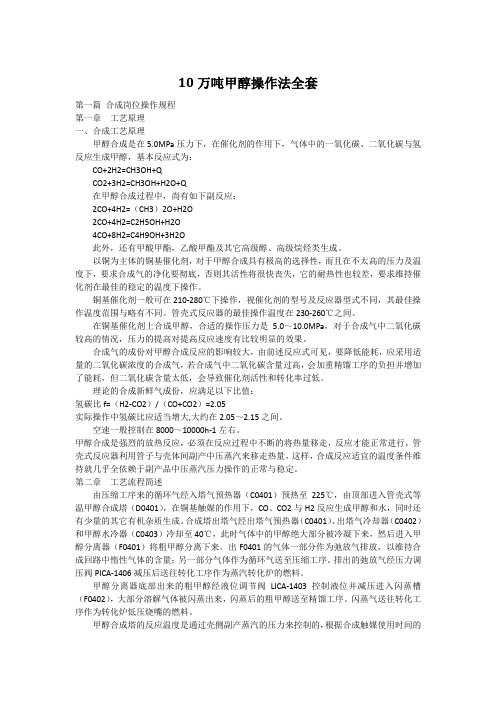
10万吨甲醇操作法全套第一篇合成岗位操作规程第一章工艺原理一、合成工艺原理甲醇合成是在5.0MPa压力下,在催化剂的作用下,气体中的一氧化碳、二氧化碳与氢反应生成甲醇,基本反应式为:CO+2H2=CH3OH+QCO2+3H2=CH3OH+H2O+Q在甲醇合成过程中,尚有如下副反应:2CO+4H2=(CH3)2O+H2O2CO+4H2=C2H5OH+H2O4CO+8H2=C4H9OH+3H2O此外,还有甲酸甲酯,乙酸甲酯及其它高级醇、高级烷烃类生成。
以铜为主体的铜基催化剂,对于甲醇合成具有极高的选择性,而且在不太高的压力及温度下,要求合成气的净化要彻底,否则其活性将很快丧失,它的耐热性也较差,要求维持催化剂在最佳的稳定的温度下操作。
铜基催化剂一般可在210-280℃下操作,视催化剂的型号及反应器型式不同,其最佳操作温度范围与略有不同。
管壳式反应器的最佳操作温度在230-260℃之间。
在铜基催化剂上合成甲醇,合适的操作压力是5.0~10.0MPa,对于合成气中二氧化碳较高的情况,压力的提高对提高反应速度有比较明显的效果。
合成气的成份对甲醇合成反应的影响较大,由前述反应式可见,要降低能耗,应采用适量的二氧化碳浓度的合成气,若合成气中二氧化碳含量过高,会加重精馏工序的负担并增加了能耗,但二氧化碳含量太低,会导致催化剂活性和转化率过低。
理论的合成新鲜气成份,应满足以下比值:氢碳比f=(H2-CO2)/(CO+CO2)=2.05实际操作中氢碳比应适当增大,大约在2.05~2.15之间。
空速一般控制在8000~10000h-1左右。
甲醇合成是强烈的放热反应,必须在反应过程中不断的将热量移走,反应才能正常进行,管壳式反应器利用管子与壳体间副产中压蒸汽来移走热量,这样,合成反应适宜的温度条件维持就几乎全依赖于副产品中压蒸汽压力操作的正常与稳定。
第二章工艺流程简述由压缩工序来的循环气经入塔气预热器(C0401)预热至225℃,由顶部进入管壳式等温甲醇合成塔(D0401),在铜基触媒的作用下,CO、CO2与H2反应生成甲醇和水,同时还有少量的其它有机杂质生成。
焦炉煤气制甲醇工艺之合成操作规程
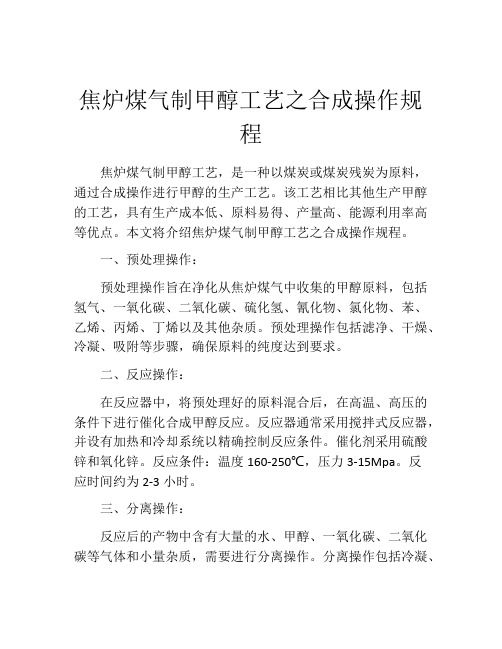
焦炉煤气制甲醇工艺之合成操作规程焦炉煤气制甲醇工艺,是一种以煤炭或煤炭残炭为原料,通过合成操作进行甲醇的生产工艺。
该工艺相比其他生产甲醇的工艺,具有生产成本低、原料易得、产量高、能源利用率高等优点。
本文将介绍焦炉煤气制甲醇工艺之合成操作规程。
一、预处理操作:预处理操作旨在净化从焦炉煤气中收集的甲醇原料,包括氢气、一氧化碳、二氧化碳、硫化氢、氰化物、氯化物、苯、乙烯、丙烯、丁烯以及其他杂质。
预处理操作包括滤净、干燥、冷凝、吸附等步骤,确保原料的纯度达到要求。
二、反应操作:在反应器中,将预处理好的原料混合后,在高温、高压的条件下进行催化合成甲醇反应。
反应器通常采用搅拌式反应器,并设有加热和冷却系统以精确控制反应条件。
催化剂采用硫酸锌和氧化锌。
反应条件:温度160-250℃,压力3-15Mpa。
反应时间约为2-3小时。
三、分离操作:反应后的产物中含有大量的水、甲醇、一氧化碳、二氧化碳等气体和小量杂质,需要进行分离操作。
分离操作包括冷凝、膜分离、吸附、蒸馏等步骤。
其中,蒸馏是分离操作中最为重要的一步,该步骤可将产物中甲醇的纯度提高至99.5%以上。
四、纯化操作:纯化操作是指进一步提高甲醇产品的纯度。
该操作主要采用蒸馏和吸附等方法,将残余的水、碳氢类杂质、酸类杂质、杂质甲醇等有机物和无机物从甲醇中提取出来。
纯化后的甲醇产品可以最终得到经过瓶装、桶装、罐装等方式进行包装装载。
五、安全操作:焦炉煤气制甲醇工艺是一种高温、高压、易爆等危险的工艺,因此安全操作尤为重要。
在运行过程中,需注意以下几点:必须使用标准的安全设施和防爆设备;操作工人必须接受专业的安全知识和技能培训;应定期检查设备的安全状况和参数;生产过程中应注意气体的引爆和毒性危害等问题。
六、总结:焦炉煤气制甲醇工艺之合成操作规程涉及预处理、反应、分离、纯化、安全等多个环节,其中每个环节都需要精细严谨的操作。
生产甲醇同时也要高度重视工厂的环保问题,合理规划废气、废水等排放,缩小环境污染,实现可持续发展的目标为行业健康快速发展奠定了基础。
焦炉煤气制甲醇工艺方案

焦炉煤气制甲醇工艺方案1.原料准备:焦炉煤气和一定比例的水蒸气是制备甲醇的原料。
焦炉煤气中含有一氧化碳、二氧化碳、氢气、氮气和少量烃类。
首先,对原料焦炉煤气进行预处理,除去其中的硫化物和一些杂质。
2.原料净化:焦炉煤气经过预处理后,进一步进行净化工艺。
通过冷却、除尘和脱硫等工序,去除颗粒物、酸性气体等污染物,以保证后续反应的顺利进行。
3.变换反应:焦炉煤气中的一氧化碳和二氧化碳需要经过变换反应,将其转化为甲醇。
该反应采用催化剂进行催化。
一氧化碳与水蒸气在一定温度和压力下通过催化剂反应生成甲醇。
在反应器内,采用适当的催化剂、反应温度和压力条件,可以提高甲醇的产率和选择性。
4.分离纯化:经过变换反应后,产生的反应混合物中含有甲醇、水、未反应的一氧化碳和二氧化碳等。
需要进行分离纯化工艺,将甲醇从混合物中提取出来。
常用的分离纯化方法包括蒸馏、吸附、结晶等。
5.回收利用:在分离纯化过程中,除了得到纯度较高的甲醇产品外,还会产生一些副产物和废弃物。
这些副产物和废弃物可以通过进一步处理和回收利用,以实现资源的综合利用和环境保护。
总的来说,焦炉煤气制甲醇工艺方案是将焦炉煤气中的一氧化碳和氢气转化为甲醇的过程。
通过预处理、净化、变换反应、分离纯化和废弃物处理等工序,实现了焦炉煤气的高效利用和甲醇产品的生产。
然而,在实际生产中,还需要根据具体情况进行工艺参数的调整和优化,以提高产量和甲醇的品质。
此外,还需要关注工艺过程中的能耗和环境污染问题,不断改进工艺方案,提高产能和资源利用效率,推动绿色发展。
甲醇工艺流程介绍
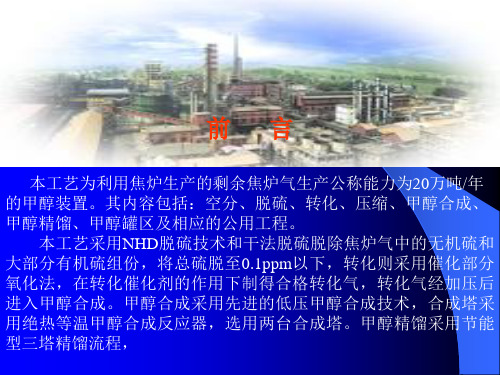
,在合成塔中发生CO+2H2=CH3OH与 CO2+3H2=CH3OH+H2O反应,经冷却分离得到粗甲 醇。
粗甲醇中含有水及其他有机杂质,需经过精馏分离得
前言
本工艺为利用焦炉生产的剩余焦炉气生产公称能力为20万吨/年 的甲醇装置。其内容包括:空分、脱硫、转化、压缩、甲醇合成、 甲醇精馏、甲醇罐区及相应的公用工程。
本工艺采用NHD脱硫技术和干法脱硫脱除焦炉气中的无机硫和 大部分有机硫组份,将总硫脱至0.1ppm以下,转化则采用催化部分 氧化法,在转化催化剂的作用下制得合格转化气,转化气经加压后 进入甲醇合成。甲醇合成采用先进的低压甲醇合成技术,合成塔采 用绝热等温甲醇合成反应器,选用两台合成塔。甲醇精馏采用节能 型三塔精馏流程,
本工艺任务为:将焦炉气(CO:6.20,CO2:2.20,H2: 58.48,CH4:26.49,N2:4.00,Ar+O2:0.60,H2S: 250mg/m3(标),COS:250mg/m3(标),CmHn:2.00)通过气 体脱硫除去无机硫和有机硫,使其能够作为转化的原料气, 在转化炉内脱硫气与空分来99.99%氧气燃烧2H2+O2=2H2O 放出热供给CH4 + H2O =CO + 3H2甲烷蒸汽转化反应得到组成
去
焦
去硫回收
炉
气
闪蒸槽 换热器 富液分离槽
脱
再
硫
生
塔
塔
水冷器
换热器
煮 沸
器
贫液泵II
贫液泵I
溶液流程
从脱硫塔底部出来的NHD富液(2.6MPa,29.4℃)经过出 口的调节阀减压至0.8MPa(G),进入闪蒸槽,闪蒸出溶解的 CO、H2、CH4、CO2。闪蒸气送往压缩工段,经原料气压缩 机加压后与原料气混合送至脱硫塔入口。
焦炉煤气制甲醇工艺方案

化学Second Design Institute of Chemical Industry可行性研究4 工艺技术方案4.1 工艺技术方案的选择4。
1。
1原料路线确定的原则和依据根据焦炉气的组成及甲醇合成对原料气的要求,确定工艺路线如下。
由焦化厂送来的焦炉气是经过化产后的焦炉气,压力1000mmH2O,温度40℃,H2S含量100mmg/Nm3,有机硫250 mmg/Nm3,首先进入焦炉气压缩机压缩到2.5MPa,再进入精脱硫装置,进行有机硫加氢转化及无机硫脱除,将焦炉气中总硫脱至0。
1ppm以下,以满足转化催化剂及合成催化剂对原料气中硫含量的要求.脱硫后的焦炉气进入转化工段,在这里进行加压催化部分氧化,使焦炉气中的甲烷和高碳烃转化为甲醇合成的有效成分氢气和一氧化碳。
为保证脱硫精度,转化后仍串有氧化锌脱硫槽。
转化气经合成气压缩机提压后进行甲醇合成,生成的粗甲醇进入甲醇精馏制得符合国标GB338—2004优等品级精甲醇.甲醇合成的弛放气一部分送转化装置的预热炉作燃料,剩余的弛放气和回收氢后的尾气去焦化公司锅炉房作燃料.转化采用纯氧部分氧化,所需氧气由空分提供。
全厂方框流程图及物料平衡表见附图。
化学Second Design Institute of Chemical Industry可行性研究本文件包含化学工业第二设计院技术成果,未经本院许可不得转给第三方或复制。
4-2This document contains proprietary information of SEDIN. To be kept confidential.4.1.2工艺技术方案的比较和选择4.1.2。
1焦炉气压缩由焦化厂送来的焦炉气H2S小于100mg/Nm3,有机硫约250 mg/Nm3,压力为常压,在进一步处理前,必须进行气体的压缩。
本工程焦炉气量较大,可选择的压缩机有往复式和离心式两种。
往复式压缩机技术成熟,价格便宜,但单机打气量小,机器庞大,噪音高,惯性力强,需要强固的基础.此外,往复式压缩机易损件多,容易停车,检修频繁,维修费用高,必须考虑备机,如采用往复式压缩机,需两开一备,占地大,电耗稍高。
20万吨焦炉气制甲醇操作规程
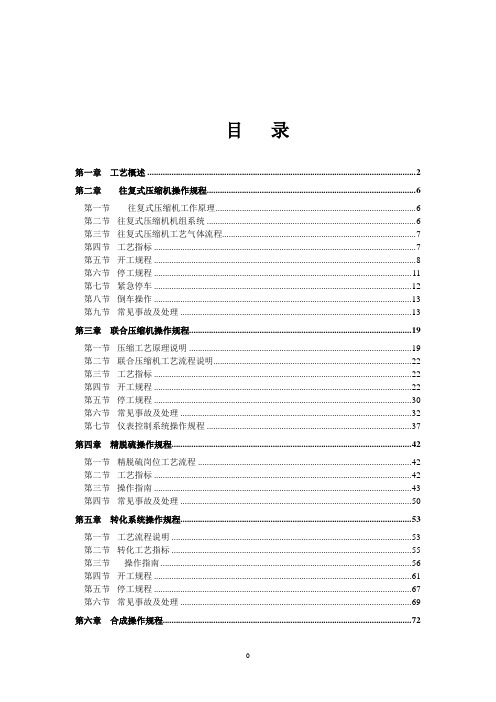
第六节
一、停车步骤
1)、接到调度停车通知后,注意检查各级压力,并做好停车准备工作,准备从高压端到低压端的顺序切气;
2)、减量:通知转化岗位准备减量,开一回一减量,当全开还需减量时,可开四回一进行大减量,减量的多少,应根据转化系统平稳状况,减到转化所需的压力时准备切气;
温度(供水/回水)
32/42℃
污垢系数
0.00034m2K/w
碳钢年腐蚀速度
<0.125mm/a
Cl-1
<100mg/L
SS
≤20 mg/L
PH值
6.5~9.5
浓缩倍数
K=3
4、生活用水和消防水
压力
0.5MPa(A)
温度
环境温度
5、精制脱盐水
压力
0.5MPa(A)
温度
≤40℃
电导率(25℃)
≤0.2us/cm
设计操作时间:8000小时/年
其工艺路线为:
1、脱油、粗脱硫、加氢串氧化锌干法脱硫
2、催化氧化
3、合成气及循环气联合压缩
4、低压法合成甲醇
5、粗甲醇3塔精馏
6、汽提法处理工艺冷凝液
二、主要工艺特点
1、采用2.3MPa(G)催化氧化制取甲醇合成气;
2、采用低压甲醇合成工艺以及副产中压蒸汽的管壳式等温甲醇合成塔,其能耗低,产品质量好,运行可靠,投资省;
7)、建立电机用油系统:由电工加入分析合格的润滑油进电机滑油系统,并保持油位2/3以上,最后检查是否有泄漏等情况,并处理至合格。
8)、建立注油系统:加入分析合格的润滑油进注油箱,保持油位1/2以上,然后用手盘动手柄数圈,无问题后开启注油器建立注油系统,并检查注油情况,如有泄漏、堵塞等现象,则停止注油,待处理合格后重新建立注油系统。
- 1、下载文档前请自行甄别文档内容的完整性,平台不提供额外的编辑、内容补充、找答案等附加服务。
- 2、"仅部分预览"的文档,不可在线预览部分如存在完整性等问题,可反馈申请退款(可完整预览的文档不适用该条件!)。
- 3、如文档侵犯您的权益,请联系客服反馈,我们会尽快为您处理(人工客服工作时间:9:00-18:30)。
焦炉气甲醇生产工艺流程
焦炉气制甲醇生产工艺
一、流程简述
来自化产车间的焦炉煤气经气柜前焦炭过滤器除油并脱除硫化氢后进入气柜缓冲稳压~经焦炉气压缩机四级压缩并分离油水后进精脱硫工段将焦炉气中的总硫脱除至0.1PPm以下进入转化工段~与空分工段来的氧气反应将焦炉气中的甲烷转化为CO、CO、H。
22
转化气经回收热量并进一步脱除总硫后进合成工段~经二合一压缩机增压后与循环气一并入甲醇合成塔进行合成反应~反应后的气体经分离粗醇后大部分进二合一机组循环~少部分放空作为燃料气使用。
合成工段产出的粗醇进精馏工段~分别在预塔采出轻组分,加压塔、常压塔采出合格精醇入罐区存放并销售,常压塔采出杂醇油入罐区储存并销售。
空分工段来自大气的空气经自洁式空气过滤器过滤后进空气压缩机加压~经空气冷却塔降温并洗涤空气中的杂质后进分子筛纯化器进一步脱除空气中的杂质。
合格的空气经分馏塔产生合格氧气和氮气~分别经加压后送其他工段使用。
二、流程描述
1、气柜
从化产车间来的焦炉气~压力约400mmH2O、温度约30?~经气柜进口焦炭过滤器脱除硫化氢并除油~经入口水封进入气柜缓冲、稳压~送往焦炉气压缩工段。
2、焦炉气压缩
从气柜来的压力为400mmH2O、温度30?的焦炉气入焦炉气压缩机~分四级升压至2.5Mpa,段间采用蒸发式冷却器进行冷却并逐级分离油水,~经蒸发式冷却器冷却到40?并进分离器分离油水后送精脱硫工段。
3、精脱硫
来自焦炉气压缩机的焦炉气压力2.5Mpa~温度40?首先经过滤
3器除去焦油~然后进入予脱硫槽~将无机硫脱至3,5mg/m。
粗脱硫后的焦炉气去转化工段初预热器预热到350?后~依次经铁钼预转化器、铁钼器转化器将有机硫转化为无机硫~然后进入氧化铁脱硫槽将大部分无机硫脱除后进入二级加氢转化器进一步转化有机硫~最后由氧化锌把关~总硫控制在
0.1ppm以下。
脱硫后的焦炉气送至转化工段。
4、转化
精脱硫后的焦炉气温度350?~压力2.2MPa~烷烃含量约28,~经预热器余热到500?~与蒸汽混合后~由预热炉加热到约660?~进入转化炉。
来自空分装置的氧气温度100?、压力2.5MPa~掺入一定量的蒸汽进入转化炉~在转化炉顶部与焦炉气蒸汽混合~通过转化炉催化剂床层进行转化反应~将甲烷转化为CO、CO、H。
22
出转化炉的转化气温度约950?~甲烷含量小于0.6,~进废热锅炉副产2.5MPa 饱和蒸汽~自身温度降到650?~入焦炉气预热器、焦炉气初预热器、锅炉给水预热器、精馏加压塔再沸器、脱盐水预热器、采暖水预热器回收热量后~由蒸发式冷却器冷却到40?~经分离器分离冷凝液后进氧化锌脱硫槽将总硫控制在0.1ppm以下~去合成工段合成甲醇。
5、甲醇合成
来自转化的原料气(2.0MPa)进入二合一机组~经两级压缩后~与循环气混合进入二合一机组压缩到6.0MPa。
出压缩机组的气体经气气换热器换热升温至220?~进入甲醇合成塔~在催化剂的作用下进行甲醇合成反应。
合成塔出口气进气气换热器与合成塔入口气换热~把入口气预热到活性温度以上~然后进入蒸发式冷却器冷却到40?~最后进入甲醇分离
器进行气液分离。
出甲醇分离器气体大部分作为循环气去二合一机组增压后合成甲醇~另一部分去洗醇塔洗涤甲醇。
洗醇塔出口气一部分去转化装置作预热炉的燃料气~一部分去锅炉房作燃料。
由甲醇分离器底部出来的粗甲醇减压到0.45Mpa后进入闪蒸槽~闪蒸出的溶解气去转化、焦炉作燃料气~闪蒸槽出来的粗甲醇去甲醇精馏精制。
6、甲醇精馏及甲醇库
由甲醇合成送来的粗甲醇进入预精馏塔~在该塔进行轻组分的分离。
塔顶蒸出的气体经预塔冷凝器将甲醇、水、部分轻组分冷凝~冷凝液进入预塔回流罐~不凝气进轻组分冷却器进一步冷却~出轻组分冷却器的不凝气去转化作燃料气~冷凝液返回预精馏塔作回流液。
预精馏塔底部出来的甲醇液由甲醇给料泵加压后送入加压精馏塔~塔顶蒸出的甲醇蒸汽进入常压塔再沸器~甲醇蒸汽冷凝热作为常压精馏塔的热源~出再沸器的精甲醇液进入加压塔回流罐~一部分精甲醇由加压塔回流泵加压后送入加压精馏塔~其余部分经精甲醇冷却器冷却到40?送至精甲醇中间槽。
加压精馏塔底部出来的甲醇液送至常压精馏塔下部~蒸出的甲醇蒸汽由常压塔冷凝器冷凝后进入常压塔回流罐~再经常压塔回流泵加压~一部分精甲醇打入常压塔回流~其余部分送至精甲醇中间槽。
精甲醇中间槽的产品化验合格后送去甲醇库。
常压精馏塔侧线采出的杂醇油冷却后送入甲醇库的杂醇贮槽。
常压精馏塔底排出的含有微量甲醇和其它高沸点醇的水经废液冷却器冷却后~由废液泵送生化处理装置。
7、空分装置
空气经自洁式过滤器除去杂质进入透平压缩机被压缩至约0.6MPa~通过空气冷却塔被经污氮冷却后的水及制冷机组来的冷水二次冷却。
冷却至约10?左右进入分
子筛纯化器除去空气中水份、二氧化碳及乙炔等杂质使空气得到净化~由于分子筛吸附热之故~空气被复热至1l-l2?~然后分二路入分馏塔~一路是绝大部分空气进入分馏塔中主换热器被返流气冷却至,172?(其中有一小部分被液化)进入下塔底部~而另一路空气经过增压机增压至0.8,O.9MPa~经冷却后进入主换热器被冷却至,l08?左右~再从主换热器中部抽出去透平膨胀机膨胀至0.14MPa左右~以,165?温度进入上塔进行精馏~得产品氧气和氮气~部分污氮作为再生分子筛使用~出塔后的氧气和氮气通过氧压机和氮压机后分别送往用户使用。
三、投资分析
以年产十五万吨甲醇计原料消耗:
3焦炉气用量37000Nm/h,
3纯氧用量8000Nm/h,
3同时外送甲醇驰放气12000 Nm/h。
,注:可以联产合成氨4万吨/年,
工程项目总投资:约46000万元,
3以甲醇2500元/吨~焦炉气0.5元/Nm计,
年均利润总额:5000万元。
投资回收期,不含建设期,8年。
序号项目单位数量备注
1 装置规模
1.1 甲醇万吨/年 15
331.2 空分制氧气万m/年 6400 制氮气9600m/年
2 主要原料消耗
32.1 焦炉气万m/年 29600
序号项目单位数量备注 3 商品量 3.1 甲醇万吨/年 15 3.2 杂醇油
万吨/年 0.117
33.3 甲醇驰放气外送万m/年 9600 4 公用工程消耗
34.1 生产用水万m/年 32
34.2 生活水万m/年 1 4.2 电万KWH/年 20301
34.4 脱盐水万m/年 70 4.5 蒸汽,副产, 万吨/年 4 5 总图运输 5.1 工程总占地公顷 8 120亩 5.2 总运输量万吨/年 15.1
其中:运入万吨/年 0.1
运出万吨/年 15 6 “三废”排放量
36.1 废气 m/h
36.2 废水 m/h 6.3 废渣吨/年 13 7 工程总定员人 160 8 工程建设期年1 9 工程总投资万元 46000 9.1 建设投资万元 45000 9.2 建设期利息万元500 9.3 流动资金万元 10 财务评价主要指标 10.1 年均销售收入万元 37500 10.2 年均销售总成本万元 32500 10.3 年均利税总额万元 5000
序号项目单位数量备注 10.4 年均税后利润万元 4000 10.5 年均所得税金万元 1000 10.6 税前投资回收期年 9.0 含建设期 10.7 税后投资回收期年 8.5 含建设期 10.8 贷款偿还期年 4 含建设期。