焦炉气制甲醇工艺
焦炉气制甲醇工艺

焦炉气制甲醇工艺工艺流程说明来自压缩工段的焦炉气(123℃,3.0MPaA)经加热炉预热后,与来自空分的经氧气加热器加热后 3.5MPaA氧气经转化炉喷嘴混合后在转化炉内发生不完全燃烧反应,放出大量的热量,气体温度迅速升高,同时CH4发生转化反应。
转化炉出口的高温转化气(CH4<0.4)直接进入中压废热锅炉,产生4.0MPaG蒸汽。
降温后的转化气进入蒸汽过热器/锅炉给水加热器,过热甲醇合成来的2.5MPaG饱和蒸汽,加热甲醇合成废锅和本工段中压废热锅炉用锅炉给水。
然后转化气经脱盐水加热器降温后进入水洗塔降温洗涤后,送至NHD脱硫工段。
水洗塔塔底分离掉的冷凝液送至造气的浊循环水系统。
脱盐水站来脱盐水经脱盐水加热器加热后送至锅炉房。
氧气加热器用本工段产的4.0MPaG饱和蒸汽加热。
中压废热锅炉产的4.0MPaG饱和蒸汽除部分供氧气加热器用,其余经加热炉加热至450℃后送至管网。
加热炉用燃料气主要为甲醇合成闪蒸气和甲醇精馏不凝气及甲醇合成非渗透气。
**焦炉煤气经过过滤器滤去油雾和预脱硫槽脱除无机硫后,经加氢转化器加氢转化进入中温脱硫槽脱除绝大部分无机硫,经过二级加氢转化器将残余的有机硫进一步转化,再经中温氧化锌脱硫槽把关,使气体中的总硫达到0.1ppm,出氧化锌脱硫槽的气体送往转化装置。
焦炉煤气和氧气分别进入转化炉上部后立即进行氧化反应放出热量,并很快进入催化剂层,反应后的转化气由转化炉底部引出经一些列管换热冷凝后,由气液分离器分离工艺冷凝液,经氧化锌脱硫槽脱除气体中残余的硫并送往合成气压缩工段。
转化气经合成压缩机一、二段压缩至5.5MPa,然后进入循环段与来自甲醇合成的循环气在缸内混合,压缩至6.0MPa后送至甲醇合成工段。
公司用电(万KWh)17145.4:主要生产14498.4,辅助2647。
甲醇生产:焦炉煤气(万m3)41268 折标0.6052电力(万KWh)10546.3蒸汽(t)511240输出驰放气(万m3)16664 产量(t)211339蒸汽(t)329591。
十万吨焦炉煤气制甲醇的操作规程
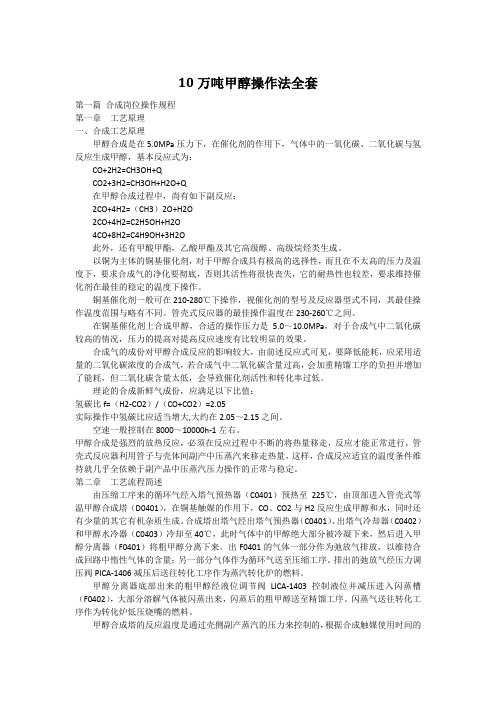
10万吨甲醇操作法全套第一篇合成岗位操作规程第一章工艺原理一、合成工艺原理甲醇合成是在5.0MPa压力下,在催化剂的作用下,气体中的一氧化碳、二氧化碳与氢反应生成甲醇,基本反应式为:CO+2H2=CH3OH+QCO2+3H2=CH3OH+H2O+Q在甲醇合成过程中,尚有如下副反应:2CO+4H2=(CH3)2O+H2O2CO+4H2=C2H5OH+H2O4CO+8H2=C4H9OH+3H2O此外,还有甲酸甲酯,乙酸甲酯及其它高级醇、高级烷烃类生成。
以铜为主体的铜基催化剂,对于甲醇合成具有极高的选择性,而且在不太高的压力及温度下,要求合成气的净化要彻底,否则其活性将很快丧失,它的耐热性也较差,要求维持催化剂在最佳的稳定的温度下操作。
铜基催化剂一般可在210-280℃下操作,视催化剂的型号及反应器型式不同,其最佳操作温度范围与略有不同。
管壳式反应器的最佳操作温度在230-260℃之间。
在铜基催化剂上合成甲醇,合适的操作压力是5.0~10.0MPa,对于合成气中二氧化碳较高的情况,压力的提高对提高反应速度有比较明显的效果。
合成气的成份对甲醇合成反应的影响较大,由前述反应式可见,要降低能耗,应采用适量的二氧化碳浓度的合成气,若合成气中二氧化碳含量过高,会加重精馏工序的负担并增加了能耗,但二氧化碳含量太低,会导致催化剂活性和转化率过低。
理论的合成新鲜气成份,应满足以下比值:氢碳比f=(H2-CO2)/(CO+CO2)=2.05实际操作中氢碳比应适当增大,大约在2.05~2.15之间。
空速一般控制在8000~10000h-1左右。
甲醇合成是强烈的放热反应,必须在反应过程中不断的将热量移走,反应才能正常进行,管壳式反应器利用管子与壳体间副产中压蒸汽来移走热量,这样,合成反应适宜的温度条件维持就几乎全依赖于副产品中压蒸汽压力操作的正常与稳定。
第二章工艺流程简述由压缩工序来的循环气经入塔气预热器(C0401)预热至225℃,由顶部进入管壳式等温甲醇合成塔(D0401),在铜基触媒的作用下,CO、CO2与H2反应生成甲醇和水,同时还有少量的其它有机杂质生成。
焦炉煤气制甲醇工艺之合成操作规程
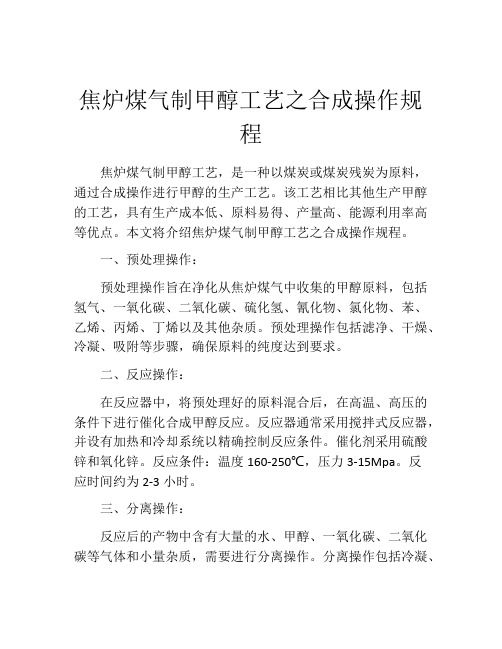
焦炉煤气制甲醇工艺之合成操作规程焦炉煤气制甲醇工艺,是一种以煤炭或煤炭残炭为原料,通过合成操作进行甲醇的生产工艺。
该工艺相比其他生产甲醇的工艺,具有生产成本低、原料易得、产量高、能源利用率高等优点。
本文将介绍焦炉煤气制甲醇工艺之合成操作规程。
一、预处理操作:预处理操作旨在净化从焦炉煤气中收集的甲醇原料,包括氢气、一氧化碳、二氧化碳、硫化氢、氰化物、氯化物、苯、乙烯、丙烯、丁烯以及其他杂质。
预处理操作包括滤净、干燥、冷凝、吸附等步骤,确保原料的纯度达到要求。
二、反应操作:在反应器中,将预处理好的原料混合后,在高温、高压的条件下进行催化合成甲醇反应。
反应器通常采用搅拌式反应器,并设有加热和冷却系统以精确控制反应条件。
催化剂采用硫酸锌和氧化锌。
反应条件:温度160-250℃,压力3-15Mpa。
反应时间约为2-3小时。
三、分离操作:反应后的产物中含有大量的水、甲醇、一氧化碳、二氧化碳等气体和小量杂质,需要进行分离操作。
分离操作包括冷凝、膜分离、吸附、蒸馏等步骤。
其中,蒸馏是分离操作中最为重要的一步,该步骤可将产物中甲醇的纯度提高至99.5%以上。
四、纯化操作:纯化操作是指进一步提高甲醇产品的纯度。
该操作主要采用蒸馏和吸附等方法,将残余的水、碳氢类杂质、酸类杂质、杂质甲醇等有机物和无机物从甲醇中提取出来。
纯化后的甲醇产品可以最终得到经过瓶装、桶装、罐装等方式进行包装装载。
五、安全操作:焦炉煤气制甲醇工艺是一种高温、高压、易爆等危险的工艺,因此安全操作尤为重要。
在运行过程中,需注意以下几点:必须使用标准的安全设施和防爆设备;操作工人必须接受专业的安全知识和技能培训;应定期检查设备的安全状况和参数;生产过程中应注意气体的引爆和毒性危害等问题。
六、总结:焦炉煤气制甲醇工艺之合成操作规程涉及预处理、反应、分离、纯化、安全等多个环节,其中每个环节都需要精细严谨的操作。
生产甲醇同时也要高度重视工厂的环保问题,合理规划废气、废水等排放,缩小环境污染,实现可持续发展的目标为行业健康快速发展奠定了基础。
焦炉煤气制甲醇工艺方案

焦炉煤气制甲醇工艺方案1.原料准备:焦炉煤气和一定比例的水蒸气是制备甲醇的原料。
焦炉煤气中含有一氧化碳、二氧化碳、氢气、氮气和少量烃类。
首先,对原料焦炉煤气进行预处理,除去其中的硫化物和一些杂质。
2.原料净化:焦炉煤气经过预处理后,进一步进行净化工艺。
通过冷却、除尘和脱硫等工序,去除颗粒物、酸性气体等污染物,以保证后续反应的顺利进行。
3.变换反应:焦炉煤气中的一氧化碳和二氧化碳需要经过变换反应,将其转化为甲醇。
该反应采用催化剂进行催化。
一氧化碳与水蒸气在一定温度和压力下通过催化剂反应生成甲醇。
在反应器内,采用适当的催化剂、反应温度和压力条件,可以提高甲醇的产率和选择性。
4.分离纯化:经过变换反应后,产生的反应混合物中含有甲醇、水、未反应的一氧化碳和二氧化碳等。
需要进行分离纯化工艺,将甲醇从混合物中提取出来。
常用的分离纯化方法包括蒸馏、吸附、结晶等。
5.回收利用:在分离纯化过程中,除了得到纯度较高的甲醇产品外,还会产生一些副产物和废弃物。
这些副产物和废弃物可以通过进一步处理和回收利用,以实现资源的综合利用和环境保护。
总的来说,焦炉煤气制甲醇工艺方案是将焦炉煤气中的一氧化碳和氢气转化为甲醇的过程。
通过预处理、净化、变换反应、分离纯化和废弃物处理等工序,实现了焦炉煤气的高效利用和甲醇产品的生产。
然而,在实际生产中,还需要根据具体情况进行工艺参数的调整和优化,以提高产量和甲醇的品质。
此外,还需要关注工艺过程中的能耗和环境污染问题,不断改进工艺方案,提高产能和资源利用效率,推动绿色发展。
焦炉煤气制甲醇设计说明书

焦炉煤气制甲醇设计说明书本文档旨在介绍焦炉煤气制甲醇的背景和目的。
对于需要设计焦炉煤气制甲醇的项目,该说明书将提供必要的信息和指导。
焦炉煤气制甲醇是一种利用焦炉煤气作为原料生产甲醇的工艺。
焦炉煤气是炼焦过程中产生的一种混合煤气,包含一定的一氧化碳和氢气等成分,因此适合用于甲醇的合成。
通过焦炉煤气制甲醇,可以将焦炉煤气这种副产品转化为有价值的化学品甲醇。
甲醇是一种重要的化工原料,在合成材料、医药、涂料、清洁能源等领域有广泛的应用。
该设计说明书的目的是为正在设计焦炉煤气制甲醇项目的人员提供必要的指导和参考。
本文档将包括焦炉煤气制甲醇的工艺流程、设备设计要求、操作条件、安全规范等方面的内容,以确保项目的顺利进行和甲醇生产的稳定运行。
请使用本设计说明书作为设计焦炉煤气制甲醇项目的参考,并根据具体情况进行调整和优化。
任何需要修改本文档内容的更改都应遵循合适的法律法规及技术规范,并由经验丰富的专业人员进行审核和批准。
有关焦炉煤气制甲醇的具体技术和经济参数等内容,请参考相关的可靠资料和专业意见。
祝项目顺利进行!本设计说明书旨在提供焦炉煤气制甲醇项目设计时应遵循的原则和考虑因素。
以下是设计原则的要点:安全性:设计应始终以安全性为首要考虑因素。
确保设计方案符合相关安全标准,预防和减少事故风险。
环境友好性:设计应符合环境保护要求,减少对环境的负面影响。
优选低排放和清洁能源技术,降低甲醇生产过程中的污染物排放。
能源效率:设计应追求能源效率,最大程度地利用可再生能源和能源回收技术。
优化工艺流程,减少能源浪费,提高甲醇生产效益。
可持续性:设计应注重项目的长期可持续性。
考虑材料和设备的可持续供应,合理规划和管理资源,确保项目的可持续发展。
经济性:设计应在满足安全和环境要求的前提下,最大限度减少投资和运营成本。
优化工艺设计,提高生产效率,降低生产成本。
可操作性和维护性:设计应考虑到设备的操作和维护要求,使甲醇生产过程简化和可靠。
20万吨焦炉气制甲醇操作规程
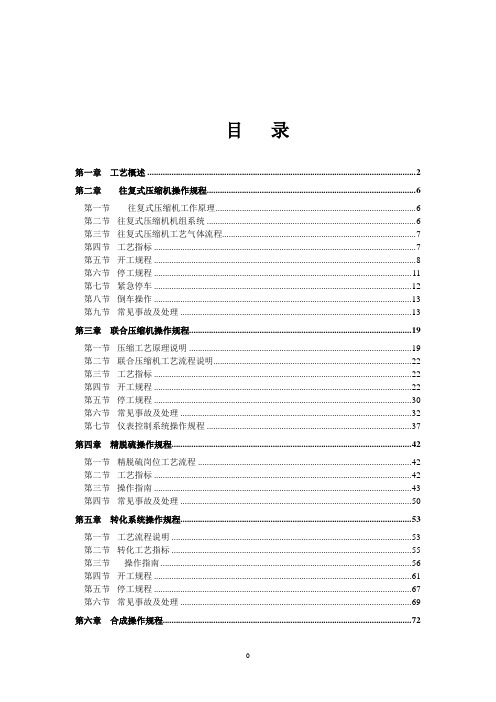
第六节
一、停车步骤
1)、接到调度停车通知后,注意检查各级压力,并做好停车准备工作,准备从高压端到低压端的顺序切气;
2)、减量:通知转化岗位准备减量,开一回一减量,当全开还需减量时,可开四回一进行大减量,减量的多少,应根据转化系统平稳状况,减到转化所需的压力时准备切气;
温度(供水/回水)
32/42℃
污垢系数
0.00034m2K/w
碳钢年腐蚀速度
<0.125mm/a
Cl-1
<100mg/L
SS
≤20 mg/L
PH值
6.5~9.5
浓缩倍数
K=3
4、生活用水和消防水
压力
0.5MPa(A)
温度
环境温度
5、精制脱盐水
压力
0.5MPa(A)
温度
≤40℃
电导率(25℃)
≤0.2us/cm
设计操作时间:8000小时/年
其工艺路线为:
1、脱油、粗脱硫、加氢串氧化锌干法脱硫
2、催化氧化
3、合成气及循环气联合压缩
4、低压法合成甲醇
5、粗甲醇3塔精馏
6、汽提法处理工艺冷凝液
二、主要工艺特点
1、采用2.3MPa(G)催化氧化制取甲醇合成气;
2、采用低压甲醇合成工艺以及副产中压蒸汽的管壳式等温甲醇合成塔,其能耗低,产品质量好,运行可靠,投资省;
7)、建立电机用油系统:由电工加入分析合格的润滑油进电机滑油系统,并保持油位2/3以上,最后检查是否有泄漏等情况,并处理至合格。
8)、建立注油系统:加入分析合格的润滑油进注油箱,保持油位1/2以上,然后用手盘动手柄数圈,无问题后开启注油器建立注油系统,并检查注油情况,如有泄漏、堵塞等现象,则停止注油,待处理合格后重新建立注油系统。
焦炉气制甲醇工艺介绍
焦炉气制甲醇工艺介绍摘要:焦炉煤气制甲醇是资源合理利用的变废为宝项目,具有广阔的前景,本文重点分析了焦炉气制甲醇工艺中的关键技术。
关键词:焦炉煤气净化脱硫催化转化催化剂氢碳比1 焦炉煤气1.1 焦炉煤气的组成与杂质含量一般焦炉煤气的主要成份为H2、CO、CH4、CO2等,各成份所占比例如表1所示。
同时也含有一些杂质。
1.2 焦炉煤气的利用焦炉煤气是极好的气体燃料,同时又是宝贵的化工原料气,焦炉煤气被净化后可以作为城市燃气来使用,从其成份上来看也是制造甲醇、合成氨、提取氢气的很好的原料。
2 焦炉煤气制甲醇的基本工艺流程为焦炉煤气制造甲醇最基本的工艺流程,净化与转化在整个焦炉煤气制甲醇流程中的关键技术。
3 焦炉煤气的净化工艺焦炉气的净化总的来说有三大步骤:(1)焦炉气经过捕捉、洗涤、脱酸蒸氨等化工过程,将有害的物质脱除到甲醇合成催化剂所要求的精度,进入焦炉气柜;(2)脱硫,分无机硫的脱除和有机硫的脱除,具体的方法根据系统选择工艺方案而改变;(3)焦炉煤气的深度净化,在精脱硫后再深度脱除氯离子和羰基金属,防止其对甲醇合成催化剂的毒害。
脱硫工艺技术方案:(1)几乎全部的无机硫和极少部分的有机硫能够在焦化厂化产湿法脱硫时脱掉;(2)绝大部分的有机硫的脱除采用的是干法脱除,具体的有分为4种:吸收法、水解法、热解法和加氢转化法,其中水解法和加氢转化法在国内外化工工艺上用的最为普遍。
4 焦炉煤气的烷烃转化技术目前具体的方法有:蒸汽转化工艺、纯氧非催化部分氧化转化工艺、纯氧催化部分氧化转化工艺。
4.1 蒸汽转化工艺其原理类似于天然气制甲醇两段转化中的一段炉转化机理,不过考虑到焦炉煤气的甲烷含量只有天然气的1/4,所以在焦炉煤气制造甲烷的实际工艺选择中,该方法一般不被采用。
4.2 纯氧非催化部分氧化转化工艺从理论上分析,该工艺具有以下几个优点:(1)该工艺能够生成的合成气比较接近于最佳氢碳比;(2)合成甲醇时循环气中含有的惰性气比例较小,便于节能减排;(3)该工艺在转化时没有催化剂要求,所以对原料气要求不是太严格,焦炉煤气转化前不需要进行深度脱硫净化;(4)非催化部分氧化转化工艺大大简化了脱硫净化过程,而且脱硫精度高,降低了原料气净化成本,转化过程中排放硫化物对环境的二次污染明显降低,是将来焦炉煤气净化与转化的发展方向。
焦炉气制甲醇工艺
焦炉气的精制是以炼焦剩余的焦炉气为生产原料,经化工产品回收焦炉气的粗制;再经压缩后,进入脱硫转化工段,脱硫采用NHD湿法脱硫和干法精脱硫技术,总硫脱至×10-6,转化采用烃类部分氧化催化技术;制得合格的甲醇合成新鲜气又称精制气,送去压缩工段合成气压缩机,最后进入甲醇合成塔制得甲醇;第1章焦炉气成分分析典型焦炉气的组成焦炉气的主要成分为甲烷%、氢气%、一氧化碳%和二氧化碳%等,还有少量的氮气、不饱和烃、氧气、焦油、萘、硫化物、氰化物、氨、苯等杂质;焦炉气基础参数:流量62967m3/h2台焦炉生产的剩余焦炉气;温度25℃;压力a煤气柜压力;焦炉气的回收利用焦炉气是良好的合成氨、合成甲醇及制氢的原料;根据焦炉气组成特点,除H2、CO、CO2为甲醇合成所需的有效成分外,其余组分一部分为对甲醇合成有害的物质如多种形态的硫化物,苯、萘、氨、氰化物、不饱和烃等;如焦炉气中的硫化物不仅会与转化催化剂的主要活性成分Ni迅速反应,生成NiS使催化剂失去活性,而且还会与甲醇合成催化剂的主要活性组分Cu迅速反应,生成CuS,使催化剂失去活性,并且这两种失活是无法再生的;又如,不饱和烃会在转化催化剂表面发生析碳反应,堵塞催化剂的有效孔隙及表面活性位,使催化剂活性降低;另一部分为对甲醇合成无用的物质对甲醇合成而言为惰性组分,如CH4、N2等;惰性气体含量过高,不仅对甲醇合成无益,而且会增加合成气体的功耗,从而降低有效成分的利用率;第2章焦炉气的精制硫的脱除及加氢净化焦炉气制甲醇工艺中,焦炉气精制的首要工作是“除毒”,将对甲醇合成催化剂有害的物质脱除到甲醇合成催化剂所要求的精度;这是因为甲醇合成催化剂对硫化物的要求要高于转化催化剂;甲醇合成催化剂要求总硫<×10-6,转化催化剂要求总硫<0.×10-6;第二就是要减少惰性组分的含量;脱除“毒物”的方法,根据系统选择工艺方案的不同而有所差别;而降低惰性气体的组分含量主要是采用将烃类部分氧化催化转化的方法,使其转化为甲醇合成有用的CO和H,同时达到降低合成气中惰性组分的目的;22.1.1无机硫的脱除焦炉气中硫质量浓度高达6g/m3,氰化物质量浓度约为m3;在焦炉气净化工艺中设有脱硫、脱氰、蒸苯、焦油电捕捉等一系列净化装置,除为了减轻硫化氢和氰化物对后续装置的腐蚀,另一方面是减轻焦炉气作燃料气时对大气的污染,或作化工原料时,对催化剂的毒害;煤气净化装置是将焦炉气经过捕捉、冷却、分离、洗涤等多种化工操作,脱除焦炉气中的焦油、萘、硫化氢、氰化氢、氨、苯等物质,以满足后续装置对气体质量的要求,并回收焦油、硫、氨、苯等;S质量浓度在15mg/m3左右,同时可脱除本系统采用NHD湿法脱硫后,焦炉气中的H2焦炉气中部分有机硫;但有机硫含量仍然很高,达95mg/m3左右;如不经过精脱硫直接送入下工段,将使转化系统催化剂很快因硫中毒而失活,所以必须采用精脱硫工艺对焦炉气进行处理;2.1.2有机硫的脱除精脱硫根据对国内现有焦炉气净化技术的分析和比较,考虑到COS低温水解工艺路线存在的缺陷,对焦炉气的精脱硫采用高温加氢转化技术路线;这是因为焦炉气中含有的硫化物形态较为复杂,如:硫醇、硫醚、噻酚等硫化物在低温水解环境下很难脱除;本系统采用铁-钼加氢脱硫转化剂,在高温环境下,将气体中的有机硫转化,生成易于脱除的硫化氢,然后再采用固体铁-锰脱硫剂吸收转化后气体中的硫化氢;这样可使有机硫加氢转化完全,净化度大为提高,而且配套干法脱硫剂的硫容也高,并且可将不饱和烯烃进行加氢饱和;氧气加氢燃烧,达到对毒物的脱除,满足转化甲醇合成气对气体“毒物”的净化要求;本工艺克服了COS低温水解催化剂对氧敏感的弱点,以及二氧化碳含量影响有机影响水解反应进行,以及无法脱除复杂硫化物的难题; 硫水解的缺陷,解决了高浓度CO2现有焦炉气净化工艺的有机硫的加氢转化,一般采用铁-钼加氢催化剂,在350℃-430℃下使有机硫加氢转化为硫化氢,固体脱硫剂使用便宜的但硫容低的铁-锰脱硫剂,最后使用价格较贵但硫容较高的氧化锌把关;2.1.3关键技术高浓度CO、CO2的焦炉气加氢净化时,遇到的问题:1如何避免CO、CO2在加氢催化剂上产生甲烷化反应;2如何避免CO歧化析碳和甲烷的分解析碳;3如何防止铁钼催化剂床层产生的温升;2.1.4解决方法在加氢过程的主要反应中,含有烯烃、有机硫化物及氧的焦炉气在催化剂上进行的主要反应有:2H2+O2=2H2O+Q 1C 2H2+2H2→C2H62C 3H6+H2→C3H83COS+H2→CO+H2S 4COS+H2O→CO2+H2S 5RSH硫醇+H2→RH+H2S 6R 1SR2硫醚+2H2→R1H+R2H+H2S 7CS2+4H2→2H2S+CH4+Q 8C 4H4S噻酚+4H2→C4H10+H2S 9可能出现的副反应有:2CO→C+CO2+Q 10CO+3H2→CH4+H2O 11CH4→C+2H2+Q 12反应1、8、10为强放热反应,可能会引起催化剂床层“飞温”;反应10所出现的歧化积碳反应产生的碳会堵塞催化剂孔道,导致催化剂活性位减少,因此应设法避免上述反应;另外,焦炉气体中的油类由于焦炉气压缩机气缸采用少油润滑,可能在焦炉气中带有少量的润滑油、苯和焦油在加氢转化器内,经加氢裂解、饱和,避免了这些微量物质对后续工段的不利影响;我们在工艺设置上,采用严格的350℃控制,设有冷激副线,及时调整加氢转化器床层温度;通过监测床层压差变化,及时调整床层温度以及分析槽内积碳程度,达到抑制析碳的目的;烃类的部分氧化催化转化烃类的转化是将焦炉气中的甲烷转化成合成甲醇所用的有效气体CO和H2;为使甲醇合成气的氢碳比尽量靠近甲醇合成所需要的最佳氢碳比,本装置焦炉气中烃类的转化选用部分氧化纯氧+蒸汽催化转化;2.2.1部分氧化催化转化原理焦炉气部分氧化催化转化法,是将焦炉气中的烃类甲烷、乙烷等进行部分氧化和蒸汽转化反应,在转化炉中首先发生H2、CH4与O2的部分氧化燃烧反应,然后气体进入催化剂层进行甲烷、乙烷等与蒸汽的转化反应,所以这个方法也称为自热转化法;生产原理可以简单解释为甲烷、蒸汽、氧混合物的复杂的相互作用:第一阶段为部分氧化反应,主要是氢气与氧接触发生燃烧氧化反应,生成H2O;该反应是剧烈的放热反应:2H2+O2=2H2O+Q 13在这个阶段,焦炉气体中微量的氧与配入的氧完全反应,反应后的气体中氧体积分数仅为%,不会对转化催化剂活性造成影响;第二阶段为水蒸气和二氧化碳氧化性气体在催化剂的作用下,与CH4进行蒸汽转化反应,该反应是吸热反应:CH4+H2O→CO+3H2-Q 14CH4+CO2→2CO+2H2-Q 15上述两阶段的反应可合并成一个总反应式:2CH4+CO2+O2→3CO+3H2+H2O 16由于第二个阶段反应是吸热反应,当转化温度越高时,甲烷转化反应就越完全,反应后气体中的残余甲烷就越低;甲烷部分氧化通常加入一定量的蒸汽,目的是避免焦炉气在受热后发生析碳的反应,使甲烷进行蒸汽转化反应,在转化反应的同时,也起到抑制炭黑的生成;转化反应在镍催化剂作用下,反应速度加快,反应温度降低,反应平衡温距减小到1℃-5℃,在960℃残余CH4<%;转化后的气体成分见表;表转化后的气体成分由表可见,焦炉气催化纯氧转化制得甲醇合成气中虽然氢气过剩,但其他组分比例较好,完全能够满足甲醇合成需要;2.2.2工艺流程焦炉气中烃类部分氧化催化转化工艺流程示于图;图焦炉气部分氧化催化转化工艺流程示意图2.2.3过程特点转化催化剂的主要活性组分为Ni,对硫化物非常敏感,因此,焦炉气进入转化炉之前,必须将其中大量的硫化物脱除到转化催化剂和甲醇合成催化剂对硫精度的要求;焦炉气和氧气在进入转化炉之前,与一定比例的蒸汽混合,为防止水蒸气冷凝,焦炉气和氧气需在加热炉中加热,一方面防止蒸汽冷凝,另一方面加热后的焦炉混合气与氧气在进入转化炉后,能迅速发生燃烧反应;为防止液状或固体颗粒进入高速运转的离心机合成气压缩机,损坏转子,本装置在焦炉气压缩前,对焦炉气进行洗涤,利用焦炭过滤,采用4台往复活塞式压缩机,提高气体压力至脱硫系统所需压力;焦炉气中的硫形态比较复杂,转化前采取一系列脱硫,直至总硫<×10-6;实践证明,转化前未脱除的硫主要是噻吩,经过铁钼加氢转化,在高温环境下,已经全部转化为易于脱除的H2S和C4H10,此时将转化气中总硫脱除到所需精度很容易;甲醇系统驰放气主要用作转化加热炉燃料,剩余的返回燃料气管网,顶替部分炼焦用燃料焦炉气,把焦炉气送回甲醇生产系统进行脱硫转化,压缩合成;本装置设置大型加热炉,除加热转化系统物料外,还将转化副产、282℃次高压饱和蒸汽,加热至480℃;经降温降压至、450℃的过热蒸汽,作为空压和合成气压缩汽轮机透平动力蒸汽;全系统蒸汽完全自给;系统副产蒸汽压力等级较多,能够适应不同需要;本装置主要副产饱和蒸汽加热后减压,450℃过热蒸汽;过热蒸汽由高压汽包直接降压获得,并入管网,与来自甲醇合成的过热蒸汽作为甲醇精馏和溶液再生的热源;低压蒸汽主要作除氧热源和厂区冬季采暖;冷凝液的回收利用;全系统冷凝液可回收利用,增设一气体饱和塔,用系统冷凝液通过加热炉加热,进行饱和增湿;既可减少系统蒸汽用量,又合理利用了冷凝液,省略了工艺冷凝液的排放和处理,消除了环境的污染因素,这是一项节能环保的技术;三废治理及环境保护与实际效果;本装置在设计中严格执行国家有关标准、地方规定,具有完善的“三废”及噪声治理措施;1废气治理在开停车及事故工况下,转化工段和脱硫工段排放的工艺废气焦炉气和合成气送本工程火炬系统焚烧后排放;甲醇合成系统的驰放气和膨胀气,甲醇精馏预塔不凝气作为加热炉燃料全部消耗,不排放到空气中;浓度达标排NHD脱硫系统产生的含硫化氢废气,送入Cluas硫回收装置,尾气中SO2放;2废水治理甲醇装置的废水量不大,甲醇精馏废水采用汽提预处理回收甲醇,而后送污水处理站进行生化处理;3废渣治理各类废催化剂分类送催化剂制造厂回收,不能回收的并无毒害作用的如:废锰矿石用于铺路或填坑,不存在废固堆放现象;因此,本装置废渣对环境影响不大;第3章关键的工艺技术和设备焦炉气湿法脱硫NHD脱硫技术主要是脱除焦炉气中的大部分无机硫HS和少量有机硫COS,并将脱2硫回收的酸性气体送回硫回收;焦炉气精脱硫干法脱硫是将经过湿法脱硫的焦炉气中的有机硫,利用铁钼触媒进行加氢反应,转化成易于脱除的无机硫,同时也使不饱和烃加氢饱和,而后通过锰矿脱硫剂和氧化锌脱硫剂,将硫化氢脱除,使经过干法脱硫的焦炉气中总硫<×10-6,达到甲醇合成触媒要求的精度;焦炉气部分氧化催化转化转化是将脱硫后焦炉气中的CH4及其他烃类在转化炉内,与纯氧进行部分氧化及蒸汽转化反应,生产H2、CO、CO2等甲醇合成气,同时回收转化反应余热,副产蒸汽;主要设备3.4.1加热炉加热炉采用两段辐射、一段对流设计,辐射段主要加热焦炉气混合气和高压废锅产次高压饱和蒸汽;对流段共加热4种介质:饱和塔循环热水、富氧蒸汽、NHD湿脱硫气和预热加热炉助燃空气;3.4.2转化炉转化炉采用圆筒式纯氧转化炉,炉体为钢结构+耐火绝热材料+冷却水夹套;炉内装二段转化催化剂,顶部为蒸汽冷却套中心管式烧嘴,转化所需热量通过氧气与焦炉气中氢气发生部分燃烧反应提供,燃烧后的高温气体在催化剂床层发生甲烷与蒸汽的转化反应;转化炉出口温度控制为960℃-980℃,残余CH4的体积分数为<%;3.4.3高压废锅高压废锅是转化生产中最重要的设备,本装置采用的高压废锅温差达到600℃以上出高压废锅工艺气体温度达340℃,并且高压废锅与转化炉直连,管道内浇筑2层刚玉浇筑料,与高压废锅的浇筑料在烘炉时,需形成一体耐火隔热层;高压废锅共分2端,一端为高热端,有4根汽液上升管和热水下降管,内筑有耐火浇筑料;另一端为低热端,有2根汽液上升管和热水下降管;另配有汽包1个,供应高压锅炉给水,并实现汽液分离;本系统考虑到COS低温水解工艺路线存在的缺陷,对焦炉气的精脱硫采用高温加氢转化技术路线;采用铁-钼加氢脱硫转化剂,在高温环境下,将气体中的有机硫转化,生成易于脱除的硫化氢,然后再采用固体铁-锰脱硫剂吸收转化后气体中的硫化氢;这样可使有机硫加氢转化完全,净化度大为提高 ,并且可将不饱和烯烃进行加氢饱和;氧气加氢燃烧,达到对毒物的脱除,满足转化甲醇合成气对气体“毒物”的净化要求;本工艺克服了COS低温水解催化剂对氧敏感的弱点,以及二氧化碳含量影响有机影响水解反应进行,以及无法脱除复杂硫化物的难题; 硫水解的缺陷,解决了高浓度CO2参考文献:1 裴雪国.焦炉气制甲醇J.煤化工,2006,6:32-342 李建锁.焦炉煤气制甲醇技术M.北京:化学工业出版社20093 谢克昌,房鼎业.甲醇工艺学M.北京:化学工业出版社20104 张子锋.甲醇生产技术M.北京:化学工业出版社2008谢辞感谢各位老师三年来的教诲,感谢胡德双老师毕业论文的指导;。
甲醇工艺流程说明
目录绪论:第一章工艺流程综述一、焦炉气生产流程二、甲醇生产工艺流程1、空分工艺流程2、精脱硫工艺流程3、转化工艺流程4、合成工艺流程5、甲醇精馏工艺流程第二章基本理论及操作原理1、空分部分2、精脱硫部分3、转化部分4、合成部分5、甲醇精馏部分6、离心式压缩机7、往复式压缩机8、泵类第三章岗位操作法(依据建滔甲醇工艺流程)1、空分岗位2、净化岗位3、合成岗位4、精馏岗位5、空气压缩机6、氧气压缩机7、焦炉气压缩机8、氮气压缩机9、合成气压缩机用焦炉气作原料生产甲醇操作培训教材绪论:焦炭生产过程中,必然伴生出大量荒煤气,荒煤气的主要成分为:H2、CH4、CnHm、CO、CO2,以及少量的N2、O2.焦油、苯,萘、硫化物……。
过去,荒煤气经脱焦油、苯、萘,和粗脱硫后,一部分作为炼焦燃料;其余大部分或做城市燃气,或用做发电厂燃料。
有些地方干脆白白放空燃烧掉了,给周围环境造成严重污染。
我国最重要的煤炭及炼焦生产省份——山西省,目前就处在处处“狼烟”,城乡环境不堪重负的状况。
为使宝贵的煤炭资源得到充分合理的利用,改变我国中西部地区的落后面貌,扭转炼焦企业污染环境的局面,变废为宝,利用焦炉气做化工原料是最佳选择。
根据焦炉煤气的成分,用焦炉煤气生产甲醇、合成氨,应该是成熟的工艺。
他们与用煤、油气,用天然气转化生产甲醇、合成氨,在气体成分比例上有差别,但基本组成上并无差异。
由化工部的二设计院设计,建滔(河北)焦化厂使用的百万吨、/年甲醇装置已为焦炉气综合利用探索出了成功经验。
必将在全国各地兴建起一大批更为先进的企业,结出更加丰硕的成果。
为适应迅速发展的焦炉气生产甲醇操作需要,培养系统综合性的人才,我们把工艺基本原理知识和操作经验教训相结合,汇编成下面的培训教材,并期待在今后的生产实践中不断补充完善。
第一章工艺流程综述一、焦炉气生产流程焦炉气生产流程是指焦炉气的生产、收集、再经过气液分离、洗涤,电捕除焦油,脱硫,除氨,洗脱笨等工序生产出合格焦炉气的工艺过程。
焦炉煤气制甲醇工艺方案
4 工艺技术方案工艺技术方案的选择4.1.1 原料路线确定的原则和依据根据焦炉气的组成及甲醇合成对原料气的要求,确定工艺路线如下。
由焦化厂送来的焦炉气是经过化产后的焦炉气,压力1000mmH2O,温度40℃,H2S含量100mmg/Nm3,有机硫250 mmg/Nm3,首先进入焦炉气压缩机压缩到,再进入精脱硫装置,进行有机硫加氢转化及无机硫脱除,将焦炉气中总硫脱至以下,以满足转化催化剂及合成催化剂对原料气中硫含量的要求。
脱硫后的焦炉气进入转化工段,在这里进行加压催化部分氧化,使焦炉气中的甲烷和高碳烃转化为甲醇合成的有效成分氢气和一氧化碳。
为保证脱硫精度,转化后仍串有氧化锌脱硫槽。
转化气经合成气压缩机提压后进行甲醇合成,生成的粗甲醇进入甲醇精馏制得符合国标GB338-2004优等品级精甲醇。
甲醇合成的弛放气一部分送转化装置的预热炉作燃料,剩余的弛放气和回收氢后的尾气去焦化公司锅炉房作燃料。
转化采用纯氧部分氧化,所需氧气由空分提供。
全厂方框流程图及物料平衡表见附图。
4.1.2 工艺技术方案的比较和选择4.1.2.1焦炉气压缩由焦化厂送来的焦炉气H2S小于100mg/Nm3,有机硫约250 mg/Nm3,压力为常压,在进一步处理前,必须进行气体的压缩。
本工程焦炉气量较大,可选择的压缩机有往复式和离心式两种。
往复式压缩机技术成熟,价格便宜,但单机打气量小,机器庞大,噪音高,惯性力强,需要强固的基础。
此外,往复式压缩机易损件多,容易停车,检修频繁,维修费用高,必须考虑备机,如采用往复式压缩机,需两开一备,占地大,电耗稍高。
离心式压缩机体积与重量都小而流量很大,占地少,供气均匀、运转平稳、易损件少、维护方便,可以长周期安全运行,不考虑备机。
更为有利的是可以用蒸汽透平驱动压缩机,从而合理地利用热能。
但离心式压缩机价格远高于往复式压缩机,投资为往复式压缩机投资的两倍,此外,焦炉气含尘、含硫,容易造成离心式压缩机叶轮通道的堵塞,更为致命的是焦炉气中H2含量高,气体平均分子量小,如采用离心式压缩机设备加工难度大。
- 1、下载文档前请自行甄别文档内容的完整性,平台不提供额外的编辑、内容补充、找答案等附加服务。
- 2、"仅部分预览"的文档,不可在线预览部分如存在完整性等问题,可反馈申请退款(可完整预览的文档不适用该条件!)。
- 3、如文档侵犯您的权益,请联系客服反馈,我们会尽快为您处理(人工客服工作时间:9:00-18:30)。
焦炉气的精制是以炼焦剩余的焦炉气为生产原料,经化工产品回收(焦炉气的粗制);再经压缩后(2.55MPa),进入脱硫转化工段,脱硫采用NHD湿法脱硫和干法精脱硫技术,总硫脱至0.1×10-6,转化采用烃类部分氧化催化技术;制得合格的甲醇合成新鲜气(又称精制气),送去压缩工段合成气压缩机,最后进入甲醇合成塔制得甲醇。
第1章焦炉气成分分析1.1典型焦炉气的组成焦炉气的主要成分为甲烷26.49%、氢气58.48%、一氧化碳6.20%和二氧化碳2.20%等,还有少量的氮气、不饱和烃、氧气、焦油、萘、硫化物、氰化物、氨、苯等杂质。
焦炉气基础参数:流量62967m3/h(2台焦炉生产的剩余焦炉气);温度25℃;压力0.105MPa(a)(煤气柜压力)。
1.2焦炉气的回收利用焦炉气是良好的合成氨、合成甲醇及制氢的原料。
根据焦炉气组成特点,除H2、CO、CO2为甲醇合成所需的有效成分外,其余组分一部分为对甲醇合成有害的物质(如多种形态的硫化物,苯、萘、氨、氰化物、不饱和烃等)。
如焦炉气中的硫化物不仅会与转化催化剂的主要活性成分Ni迅速反应,生成NiS使催化剂失去活性,而且还会与甲醇合成催化剂的主要活性组分Cu迅速反应,生成CuS,使催化剂失去活性,并且这两种失活是无法再生的。
又如,不饱和烃会在转化催化剂表面发生析碳反应,堵塞催化剂的有效孔隙及表面活性位,使催化剂活性降低。
另一部分为对甲醇合成无用的物质(对甲醇合成而言为惰性组分),如CH4、N2等。
惰性气体含量过高,不仅对甲醇合成无益,而且会增加合成气体的功耗,从而降低有效成分的利用率。
第2章焦炉气的精制2.1硫的脱除及加氢净化焦炉气制甲醇工艺中,焦炉气精制的首要工作是“除毒”,将对甲醇合成催化剂有害的物质脱除到甲醇合成催化剂所要求的精度。
这是因为甲醇合成催化剂对硫化物的要求要高于转化催化剂。
甲醇合成催化剂要求总硫<0.1×10-6,转化催化剂要求总硫<0.×10-6。
第二就是要减少惰性组分的含量。
脱除“毒物”的方法,根据系统选择工艺方案的不同而有所差别。
而降低惰性气体的组分含量主要是采用将烃类部分氧化催化转化的方法,使其转化为甲醇合成有用的CO和H,同时达到降低合成气中惰性组分的目的。
22.1.1无机硫的脱除焦炉气中硫质量浓度高达6g/m3,氰化物质量浓度约为1.5g/m3。
在焦炉气净化工艺中设有脱硫、脱氰、蒸苯、焦油电捕捉等一系列净化装置,除为了减轻硫化氢和氰化物对后续装置的腐蚀,另一方面是减轻焦炉气作燃料气时对大气的污染,或作化工原料时,对催化剂的毒害。
煤气净化装置是将焦炉气经过捕捉、冷却、分离、洗涤等多种化工操作,脱除焦炉气中的焦油、萘、硫化氢、氰化氢、氨、苯等物质,以满足后续装置对气体质量的要求,并回收焦油、硫、氨、苯等。
S质量浓度在15mg/m3左右,同时可脱除本系统采用NHD湿法脱硫后,焦炉气中的H2焦炉气中部分有机硫。
但有机硫含量仍然很高,达95mg/m3左右。
如不经过精脱硫直接送入下工段,将使转化系统催化剂很快因硫中毒而失活,所以必须采用精脱硫工艺对焦炉气进行处理。
2.1.2有机硫的脱除(精脱硫)根据对国内现有焦炉气净化技术的分析和比较,考虑到COS低温水解工艺路线存在的缺陷,对焦炉气的精脱硫采用高温加氢转化技术路线。
这是因为焦炉气中含有的硫化物形态较为复杂,如:硫醇、硫醚、噻酚等硫化物在低温水解环境下很难脱除。
本系统采用铁-钼加氢脱硫转化剂,在高温环境下,将气体中的有机硫转化,生成易于脱除的硫化氢,然后再采用固体铁-锰脱硫剂吸收转化后气体中的硫化氢。
这样可使有机硫加氢转化完全,净化度大为提高,而且配套干法脱硫剂的硫容也高,并且可将不饱和烯烃进行加氢饱和。
氧气加氢燃烧,达到对毒物的脱除,满足转化甲醇合成气对气体“毒物”的净化要求。
本工艺克服了COS低温水解催化剂对氧敏感的弱点,以及二氧化碳含量影响有机硫水解的缺陷,解决了高浓度CO2影响水解反应进行,以及无法脱除复杂硫化物的难题。
现有焦炉气净化工艺的有机硫的加氢转化,一般采用铁-钼加氢催化剂,在350℃-430℃下使有机硫加氢转化为硫化氢,固体脱硫剂使用便宜的但硫容低的铁-锰脱硫剂,最后使用价格较贵但硫容较高的氧化锌把关。
2.1.3关键技术高浓度CO、CO2的焦炉气加氢净化时,遇到的问题:(1)如何避免CO、CO2在加氢催化剂上产生甲烷化反应。
(2)如何避免CO歧化析碳和甲烷的分解析碳。
(3)如何防止铁钼催化剂床层产生的温升。
2.1.4解决方法在加氢过程的主要反应中,含有烯烃、有机硫化物及氧的焦炉气在催化剂上进行的主要反应有:2H2+O2=2H2O+Q (1)C 2H2+2H2→C2H6(2)C 3H6+H2→C3H8(3)COS+H2→CO+H2S (4)COS+H2O→CO2+H2S (5)RSH(硫醇)+H2→RH+H2S (6)R 1SR2(硫醚)+2H2→R1H+R2H+H2S (7)CS2+4H2→2H2S+CH4+Q (8)C 4H4S(噻酚)+4H2→C4H10+H2S (9)可能出现的副反应有:2CO→C+CO2+Q (10)CO+3H2→CH4+H2O (11)CH4→C+2H2+Q (12)反应(1)、(8)、(10)为强放热反应,可能会引起催化剂床层“飞温”。
反应(10)所出现的歧化积碳反应产生的碳会堵塞催化剂孔道,导致催化剂活性位减少,因此应设法避免上述反应。
另外,焦炉气体中的油类(由于焦炉气压缩机气缸采用少油润滑,可能在焦炉气中带有少量的润滑油)、苯和焦油在加氢转化器内,经加氢裂解、饱和,避免了这些微量物质对后续工段的不利影响。
我们在工艺设置上,采用严格的350℃控制,设有冷激副线,及时调整加氢转化器床层温度。
通过监测床层压差变化,及时调整床层温度以及分析槽内积碳程度,达到抑制析碳的目的。
2.2烃类的部分氧化催化转化烃类的转化是将焦炉气中的甲烷转化成合成甲醇所用的有效气体CO和H2。
为使甲醇合成气的氢碳比尽量靠近甲醇合成所需要的最佳氢碳比,本装置焦炉气中烃类的转化选用部分氧化(纯氧+蒸汽)催化转化。
2.2.1部分氧化催化转化原理焦炉气部分氧化催化转化法,是将焦炉气中的烃类(甲烷、乙烷等)进行部分氧化和蒸汽转化反应,在转化炉中首先发生H2、CH4与O2的部分氧化燃烧反应,然后气体进入催化剂层进行甲烷、乙烷等与蒸汽的转化反应,所以这个方法也称为自热转化法。
生产原理可以简单解释为甲烷、蒸汽、氧混合物的复杂的相互作用:第一阶段为部分氧化反应,主要是氢气与氧接触发生燃烧氧化反应,生成H2O。
该反应是剧烈的放热反应:2H2+O2=2H2O+Q (13)在这个阶段,焦炉气体中微量的氧与配入的氧完全反应,反应后的气体中氧体积分数仅为0.05%,不会对转化催化剂活性造成影响。
第二阶段为水蒸气和二氧化碳氧化性气体在催化剂的作用下,与CH4进行蒸汽转化反应,该反应是吸热反应:CH4+H2O→CO+3H2-Q (14)CH4+CO2→2CO+2H2-Q (15)上述两阶段的反应可合并成一个总反应式:2CH4+CO2+O2→3CO+3H2+H2O (16)由于第二个阶段反应是吸热反应,当转化温度越高时,甲烷转化反应就越完全,反应后气体中的残余甲烷就越低。
甲烷部分氧化通常加入一定量的蒸汽,目的是避免焦炉气在受热后发生析碳的反应,使甲烷进行蒸汽转化反应,在转化反应的同时,也起到抑制炭黑的生成。
转化反应在镍催化剂作用下,反应速度加快,反应温度降低,反应平衡温距减小到1℃-5℃,在960℃残余CH4<0.4%。
转化后的气体成分见表2.1。
表2.1转化后的气体成分由表2.1可见,焦炉气催化纯氧转化制得甲醇合成气中虽然氢气过剩,但其他组分比例较好,完全能够满足甲醇合成需要。
2.2.2工艺流程焦炉气中烃类部分氧化催化转化工艺流程示于图2.1。
图2.1焦炉气部分氧化催化转化工艺流程示意图2.2.3过程特点转化催化剂的主要活性组分为Ni,对硫化物非常敏感,因此,焦炉气进入转化炉之前,必须将其中大量的硫化物脱除到转化催化剂和甲醇合成催化剂对硫精度的要求。
焦炉气和氧气在进入转化炉之前,与一定比例的蒸汽混合,为防止水蒸气冷凝,焦炉气和氧气需在加热炉中加热,一方面防止蒸汽冷凝,另一方面加热后的焦炉混合气与氧气在进入转化炉后,能迅速发生燃烧反应。
为防止液状或固体颗粒进入高速运转的离心机(合成气压缩机),损坏转子,本装置在焦炉气压缩前,对焦炉气进行洗涤,利用焦炭过滤,采用4台往复活塞式压缩机,提高气体压力至脱硫系统所需压力2.55MPa。
焦炉气中的硫形态比较复杂,转化前采取一系列脱硫,直至总硫<0.1×10-6。
实践证明,转化前未脱除的硫主要是噻吩,经过铁钼加氢转化,在高温环境下,已经全部转化为易于脱除的H2S和C4H10,此时将转化气中总硫脱除到所需精度很容易。
甲醇系统驰放气主要用作转化加热炉燃料,剩余的返回燃料气管网,顶替部分炼焦用燃料焦炉气,把焦炉气送回甲醇生产系统进行脱硫转化,压缩合成。
本装置设置大型加热炉,除加热转化系统物料外,还将转化副产6.4MPa、282℃次高压饱和蒸汽,加热至480℃。
经降温降压至3.82MPa、450℃的过热蒸汽,作为空压和合成气压缩汽轮机透平动力蒸汽。
全系统蒸汽完全自给。
系统副产蒸汽压力等级较多,能够适应不同需要。
本装置主要副产6.4MPa饱和蒸汽(加热后减压3.82MPa,450℃过热蒸汽)。
1.2MPa过热蒸汽由高压汽包直接降压获得,并入1.2MPa管网,与来自甲醇合成的1.2MPa过热蒸汽作为甲醇精馏和溶液再生的热源。
0.3MPa低压蒸汽主要作除氧热源和厂区冬季采暖。
冷凝液的回收利用。
全系统冷凝液可回收利用,增设一气体饱和塔,用系统冷凝液通过加热炉加热,进行饱和增湿。
既可减少系统蒸汽用量,又合理利用了冷凝液,省略了工艺冷凝液的排放和处理,消除了环境的污染因素,这是一项节能环保的技术。
三废治理及环境保护与实际效果。
本装置在设计中严格执行国家有关标准、地方规定,具有完善的“三废”及噪声治理措施。
(1)废气治理在开停车及事故工况下,转化工段和脱硫工段排放的工艺废气(焦炉气和合成气)送本工程火炬系统焚烧后排放。
甲醇合成系统的驰放气和膨胀气,甲醇精馏预塔不凝气作为加热炉燃料全部消耗,不排放到空气中。
浓度达标排NHD脱硫系统产生的含硫化氢废气,送入Cluas硫回收装置,尾气中SO2放。
(2)废水治理甲醇装置的废水量不大,甲醇精馏废水采用汽提预处理回收甲醇,而后送污水处理站进行生化处理。
(3)废渣治理各类废催化剂分类送催化剂制造厂回收,不能回收的并无毒害作用的(如:废锰矿石)用于铺路或填坑,不存在废固堆放现象。