硫化铜矿湿法冶金概况
湿法铜冶炼

2 FeSO4+MnO2+2H2SO4=Fe2(SO4)3+MnSO4+2H2O
Fe2(SO4)3+6H2O=2Fe(OH)3↓ +3H2SO4
3 浸出净化设备
若浸出的对象是贫矿、废矿,所得浸出液含铜 很低,难以直接提取铜,必须经过富集,萃取技 术能有效地解决从贫铜液中富集铜的问题。
浸出
浸出方式有堆浸、槽浸、地下浸等多种。 1、氧化铜矿堆浸
适用于硫酸溶液堆浸的铜矿石铜氧化率要求较高,铜 主要应以孔雀石、硅孔雀石、赤铜矿石等形态存在。脉石 成分应以石英为主,一般SiO2含量均大于80%,而碱性脉 石CaO、MgO含量低、二者之和不大于2%~3%。矿石含 铜品位从0.1%~0.2%。浸出过程的主要化学反应是:
电积时电解液温度为35~45℃,阴极周期可取7天,
Dk为150~180A/m2,所得电铜含铜为99.5~99.95%。
废液及废渣的处理
1、电解废液的处理: 电解废液最好全部返回浸出过程但 这种平衡很难达到,所以出现废液的处理问题。
处理目的:回收其中的有价金属,并回收或中和 硫酸以避免它对环境的危害。
①氧化铁硫杆菌;
②氧化硫杆菌。能在PH=1.5~细菌的直接作用:
氧化铁硫杆菌.为取得维持生命的能源而将 矿石中的低价铁和硫氧化成高价,氧化过程中破 坏了矿石的晶格,使矿石中的硫化物变为硫酸盐 而转入溶液中。
CuFeS2+4O2=CuSO4+FeSO4
(4) 焙烧设备及经济指标
硫化铜矿湿法冶金技术与进展

[ 键 词 ] 硫 化铜矿; 关 湿法冶金 ; 综述
目前 , 法炼 铜仍 然 占主 导地位 , 界上 火 世
约 7 ~8 的铜 是 通 过传 统 的 “ 炼一 吹 5 O 熔 炼 一精 炼一 电解 ” 艺 生 产 的 。但 随 着 环 境 工
的单 质硫 , 出 液 经萃 取 电积 生 产 高 质 量 的 浸
工
程
设
计
与
研
究
总第 l 2 2 期
D n tc y ae 法是 由加 拿 大 舍 利 特公 司开发
氯化 物 体 系 湿 法 冶 金 的 研 究 有 了长 足 的 发
展, 氯化 物溶 液 浸 取 黄铜 矿不 会 出现 硫 酸 盐 溶液 的那 种钝 化现 象 , 即使 在硫 的熔 点之下 ,
1 1 全压 氧化 浸 出 .
浸 出 。矿 石 中 的硫大 部分 以元 素硫 进入 浸 出 渣 , 和贵金 属 也 人 渣 。元 素硫 必 须 在 贵 金 铁
属之 前从 浸 出渣 中除去 。C S E L最 初采 用 热 滤法 脱硫 , 来 主 张 应 用 全 氯 乙烯 溶硫 。浸 后
已达 到 3 左 右 。特 别 是 “ 出一 萃 取一 电 O 浸
积” 工艺 的成 功 应 用 给 铜 的 湿法 冶金 带 来 了
炼 产 生二 氧化硫 对 大气 的污染 问题 。
12 中温 中压 氧化 浸 出 .
革命 性 的变 化 , 许 多原 来 困扰 硫 化 铜 矿 采 使
用 湿法 冶金技 术 的难题 得 到解决 或 缓解 。
阴极铜 , 渣 中的贵 金属 用 氰化法 回收 , 获 残 可 得 很 高的铜 和 贵金属 回收率 。全 压氧 化法 是 美 国费尔普 斯 道奇 ( h lsD d e 公 司在亚 P ep o g ) 利 桑那 州 巴 格 达 ( a d d 铜 矿 开 发 成 功 并 B g a) 用 于 生产 实践 的新 方法 。该公 司已在 巴格达
铜矿湿法厂工艺简介
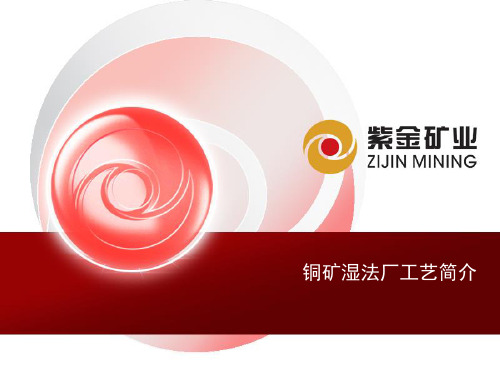
浸
出
萃余液返回 Cu0.4g/l Fe5~6g/l H2SO49.0g/l 再生有机相 Cu2.5g/l
开路萃余液 Cu0.08g/l
萃
取
反 萃 电积前液 Cu 45~50g/l Fe ≤4g/l H2SO4160~180g/l
硫酸 电积后液 Cu ≥35g/l Fe 2~3g/l H2SO4 160~180g/l
电 沉 积
电 铜
开路废电积液
4
堆浸车间简介
•
•
堆浸车间共有筑堆、接拆管道、喷淋、溶液调度四道工序。
喷淋工段:堆场粒度≤70mm,堆场高度8-10m,浸出液自流至富液池和贫液 池,富液抽到萃取工段,贫液重新返回堆场。
含铜矿石成分: • 蓝辉铜矿、黄铜矿、铜蓝、硫砷铜矿及少量辉铜矿、斑铜矿等。
工业类型: • 属含硫砷铜矿的单一硫化铜矿石,易于湿法选冶加工。
铜矿生物湿法提铜技术属清洁型工艺,具有投资省、成本低、流程短、易操 作、反应温和、对环境友好、能耗低,能获得高纯金属铜,可适应成分更贫、 更难提取的非传统矿产资源开发利用等特点
铜湿法厂共有四个生产车间:堆浸车间、选冶车间、环保车间和机电车间
3
微生物湿法炼铜工艺流程
微生物+酸性溶液 矿 石
浸出液 Cu 1.8~2g/l Fe 5~6g/l H2SO4 8.0g/l 负载有机相 Cu5.53g/l
铜矿生物浸出菌种: • • 氧化亚铁硫杆菌 氧化硫硫杆菌
5
堆浸系统建设
堆浸防渗措施简介
7杆菌或铁硫杆菌 FeS2 + 7O2 + 2H2O ==== 2FeSO4 + 2H2SO4
•
氧化亚铁杆菌或铁硫杆菌 Fe2(SO4)3 + Cu2S + 2O2 ===== 2FeSO4 + CuSO4
湿法冶金简介

二、矿物浸出特性和浸出剂的选择
1、矿物浸出特性 1)酸性浸出的矿物特性 ◆大部分金属的氧化物和含氧酸盐都能溶于酸中; ◆大部分金属硫化物都不易与酸作用,只有少数硫化物
(如FeS、NiS、CoS、MnS等),但是在有氧化剂存在 时,几乎所有硫化物在酸中都不稳定。 ◆脉石矿物中,碳酸盐、钙镁氧化物等在低酸和室温下 都容易与酸反应,游离态的二氧化硅则在酸中不溶解, 铁、铝氧化物在酸中也较稳定,但水和黏土和其它酸溶 性硅酸盐则能部分溶于酸,溶解度随酸度和温度提高而 增大。
仰韶文化彩陶 公元前5000年至前3000年
铜器时代 公元前4000年至公元初年
湿法冶金
CHAPTER 2
冶金分类
电冶金
电冶金是利用电能提取金属的方法。根据利用电能效应的不同,电冶金又分为电热冶金和电化冶金。 1、电热冶金是利用电能转变为热能进行冶炼的方法。 在电热冶金的过程中,按其物理化学变化的实质来说,与火法冶金过程差别不大,两者的主要区别只是冶炼 时热能来源不同。 2、电化冶金(电解和电积)是利用电化学反应,使金属从含金属盐类的溶液或熔体中析出。前者称为溶液 电解,如锕的电解精炼和锌的电积,可列入湿法冶金一类;后者称为熔盐电解,不仅利用电能的化学效应, 而且也利用电能转变为热能,借以加热金属盐类使之成为熔体,故也可列入火法冶金一类。从矿石或精矿中 提取金属的生产工艺流程,常常是既有火法过程,又有湿法过程,即使是以火法为主的工艺流程,比如,硫 化锅精矿的火法冶炼,最后还须要有湿法的电解精炼过程;而在湿法炼锌中,硫化锌精矿还需要用高温氧化 焙烧对原料进行炼前处理。
3)单质金属矿物的浸出特性
自然金属以及在冶金过程中产生的金属,如阳极泥副产品或还原 氧化矿得到的铜、镍等金属单质。它们的浸出特点是必须氧化成一 定价态后才能溶于水溶液中。(见表5-2)
湿法炼铜技术

湿法炼铜用溶剂浸出铜矿石或精矿,而后从浸出液中提取铜。
主要过程包括浸出(见浸取)、净化、提取等工序。
目前世界上湿法炼铜的产量约占总产量的12%。
20世纪60年代以来,为了消除SO2污染,对用湿法冶炼硫化铜矿进行了许多研究,但因经济指标尚不如火法,湿法工艺大多停留在试验和小规模生产阶段。
湿法炼铜目前主要用于处理氧化铜矿。
有氧化铜矿直接酸浸和氨浸(或还原焙烧后氨浸)等法;酸浸应用较广,氨浸限于处理含钙镁较高的结合性氧化矿。
处理硫化矿多用硫酸化焙烧-浸出或者直接用氨或氯盐溶液浸出等方法。
①硫酸化焙烧-浸出法是将精矿中的铜转变为可溶性硫酸铜溶出;②氨液浸出法是将铜转变为铜氨络合物溶出,浸出液在高压釜内用氢还原,制成铜粉,或者用溶剂萃取-电积法制取电铜;氯盐浸出法是将铜转变为铜氯络合物进入溶液,然后进行隔膜电解得电铜。
氧化铜矿酸浸法流程氧化铜矿一般不易用选矿法富集,多用稀硫酸溶液直接浸出,所得溶液含铜一般为1~5g/L,可用硫化沉淀、中和水解、铁屑置换以及溶剂萃取-电积等方法提取铜。
近年来,萃取-电积法发展较快。
其主要过程包括:①用对铜有选择性的肟类螯合萃取剂(LiX-64 N,N-510,N-530等)的煤油溶液萃取铜,铜进入有机相而与铁、锌等杂质分离。
②用浓度较高的H2SO4溶液反萃铜,得到含铜约50g/L的溶液。
反萃后的有机溶剂,经洗涤后,返回萃取过程使用。
③电积硫酸铜溶液得电铜,电解后液返回用作反萃剂。
生产流程见图。
硫化铜精矿焙烧浸出法硫化铜精矿经硫酸化焙烧后浸出,得到的含铜浸出液,经电积得电铜。
此法适于处理含有钴、镍、锌等金属的硫化铜精矿,但铜的回收率低,回收贵金属较困难,电能消耗大,电解后液的过剩酸量须中和处理,所以一般不采用。
从贫矿石和废矿中提取铜铜矿开采后坑内的残留矿、露天矿剥离的废矿石和铜矿表层的氧化矿,含铜一般较低,多采用堆浸、就地浸出和池浸等方法,浸出其中氧化形态的铜,而所含硫化铜则利用细菌的氧化作用,使之溶解。
氯化物体系中铜的湿法冶金及萃取

氯化物体系中铜的湿法冶金及萃取1、氯化物体系中硫化铜矿的浸取氯化物体系中浸取铜矿石多采用FeCl3为氧化剂,有时也用Cu Cl2。
黄铜矿是最常见的铜矿物,性质十分稳定,它的浸取反应可如下表示:Cu FeS2+(4-x)FeCl3 = xCu Cl+(1-x)Cu Cl2+(5-x)FeCl3+2S 反应取决于FeCl3的用量,式中的x在0到1之间。
FeCl3 浸取液含Fe 50~200 g/L,浸取反应在80℃以上即可进行,但最好在95~106℃之间,浸取时间需8~12h。
其他硫化铜矿比黄铜矿易于浸出,而黄铁矿基本不被氧化。
最终浸出液可达含铜80 g/L.生成的FeCl2 需经氧化返回作为浸取剂。
氧化可在电解槽的阳极室中籍阳极氧化来完成。
根据这个原理,有的氯化浸取可在一个电解槽中进行,阳极室用于浸取而阴极室用于电解铜,这称之为电氯化方法。
FeCl2 的氧化也可用空气在塔式反应器中进行。
浸取液中的硫可以用有机溶剂提取,也可以用硫化铵与硫反应生成多硫化铵使其溶解在水溶液中,与渣分离后,再加热使之分解析出元素硫。
2、中性含氧萃取剂萃取铜在浓的氯化物-盐酸溶液中长链醇对铜离子有一定的萃取能力,如异戊醇在O/A=1/1,从Ca Cl2 500g/L,HCl 90g/L及Cu5.5g/L的溶液中萃取铜,铜的分配比可达到0.48。
醚、酯的萃取能力则更弱。
TBP的萃取能力则强得多。
在1mol/LCl- 及(2~5)×10-3mol/L的酸性溶液中同时通过含二氧化硫0.9% ~ 1.2%(V/V)的燃烧气TBP负荷铜可达40~60g/L。
并建议用氢气直接加压还原得铜粉。
3、胺及季铵盐类萃取铜叔胺在酸性溶液中加合氢离子形成阳离子,可以和铜的阴配离子相结合而萃取,这种机理称为离子对萃取。
由于盐酸也能被萃取而与铜阴配离子发生竞争,因此在盐酸溶液中铜的萃取出现一最高值,而在盐中不存在这一最高值。
季铵盐如氯化季铵R4NCl系由R4N+及Cl-两部分组成,因此与叔胺相似,也可以进行阴离子交换生成离子对。
第8章 硫化铜矿的细菌浸出

1992~ 1997 1993至今 1993至今 1994至今 1994至今 1994一 1995一
澳大利亚 辉铜矿,含Cu 2.5%(堆浸) 澳大利亚 辉铜矿,含Cu 2.5%(堆浸) 智 利 智 利 秘 鲁 辉铜矿,含Cu l.3%(堆浸) 原生硫化铜矿,含Cu 0.35% 次生与原生,含Cu 0.17%
此外,矿石中碱性脉石 (CaC03,MgC03) 含 量不宜高。这些碱性脉石在浸 出时要消耗硫酸,增加作业成 本,而且使浸矿液中CaS04达 到饱和,在矿块表面沉积析出, 从而妨碍浸矿的进一步进行。
8.4.2 矿块的粒度 从动力学的角度,矿块愈小浸 出效果愈好。试验表明,在氧化亚 铁硫杆菌参与下浸出黄铜矿、闪锌 矿与黄铁矿时,矿块直径在50mm以 上,铜锌浸出极少。50mm时,铜的 每周浸出率仅为0.015%,只有块矿 直径到19mm以下时,浸出率才显著 上升。
8.2.2 黄铜矿的浸出 8.2.2.1 黄铜矿的晶体结构 黄铜矿属N型半导体,电阻率为10- 3Ω·m,禁带为0 。黄铜矿的价电子带由金
属原子轨道与硫原子轨道共同给出。
8.2.2.2 黄铜矿溶解机理 黄铜矿的阳极溶解靠的是价带的空穴与导 带电子的转移,溶解的开始阶段是空穴的 填充。与金属依靠自由电子导电不同,半 导体中可以区分出两类载流子(电子和空穴) 导电机理,如图所示。由于半导体禁带较 窄,不要太多的能量就能使至少有少数具 有足够热能的电子从满带(又称为价带)激 发到空带(又称为导带),而在价带中留下 空穴。因为价带中的电子原来已满,是定 域的,不能在晶体中自由运动,所以不起 导电作用,而导带中的电子几乎可以自由 地在晶体中运动而传导电流。
硫化铜精矿湿法冶金工艺研究及混合精矿金铜回收试验

硫化铜精矿湿法冶金工艺研究及混合精矿金铜回收试验湿法炼铜由于具有生产率高、能耗低等优点成为处理硫化铜矿的一种重要方法。
本试验针对吉林省某高硫铜矿,结合企业需要提出并确定了硫酸化焙烧-酸浸工艺提取该硫化铜精矿中的铜;比较了富氧气氛与空气气氛条件下硫酸化焙烧动力学过程,计算了反应表观活化能;并对该硫化铜精矿与高碳金精矿混合矿采用硫酸化焙烧-硫酸浸出-氯化浸金工艺同时提取金和铜做了初步试验。
本文主要研究了焙烧和浸出工艺参数对硫化铜精矿中铜浸出率的影响。
关键研究参数有:焙烧温度、焙烧时间、钠盐添加量及种类;浸出剂酸度、浸出温度、浸出时间、搅拌速率和液固比。
实验结果表明:焙烧温度和焙烧时间是影响硫化铜精矿硫酸化焙烧效果的重要因素,在500℃焙烧2h条件下,铜的浸出率达到95.28%。
焙烧温度在550℃以上时,焙烧前添加亚硫酸钠能有效提高铜的浸出率;而降低焙烧温度到550℃以下亚硫酸钠的添加对铜的浸出效果没有明显改善作用。
焙烧前加入硫酸钠,能将铜浸出率提高至99%左右。
浸出过程中浸出剂酸度、浸出温度和浸出时间是影响铜浸出率的三个重要因素,改变搅拌速率和液固比则对铜浸出率影响不大。
试验最佳浸出工艺参数确定为:浸出剂中硫酸浓度5%;液固比4:1;搅拌速率400r/min;浸出时间2h;浸出温度室温(25℃)。
通过空气气氛和富氧气氛焙烧时二氧化硫的逸出率计算硫的氧化率,以此为依据做表观动力学研究。
在空气气氛焙烧时,求得反应表观活化能为43.14kJ/mol,过程受界面化学反应控制;当通入50%氧气时,二氧化硫逸出最大值所需时间大大缩短,且求得表观活化能比空气气氛时降低,反应动力学过程转为混合反应控制,说明富氧焙烧能改善焙烧效果,减少反应时间。
在理论上证明了对该硫化铜精矿进行富氧焙烧可以提高焙烧效率。
本论文在以上实验的基础上,对硫化铜精矿与高碳金精矿的混合精矿进行了硫酸化焙烧-酸浸-氯化浸金试验来综合回收元素金和铜,试验对比了焙烧前添加亚硫酸钠与不添加时焙烧的效果,结果表明,添加1%亚硫酸钠后进行焙烧能够将金的浸出率提高4.87%,铜的浸出率提高5.14%。
- 1、下载文档前请自行甄别文档内容的完整性,平台不提供额外的编辑、内容补充、找答案等附加服务。
- 2、"仅部分预览"的文档,不可在线预览部分如存在完整性等问题,可反馈申请退款(可完整预览的文档不适用该条件!)。
- 3、如文档侵犯您的权益,请联系客服反馈,我们会尽快为您处理(人工客服工作时间:9:00-18:30)。
书山有路勤为径,学海无涯苦作舟
硫化铜矿湿法冶金概况
1998 年7 月,第一家用加压酸浸处理硫化铜矿的澳大利亚高尔峒山(Mt. Gordon)厂投产,打破了硫化铜矿湿法冶金的沉寂。
由于处理的是比较容易浸取的辉铜矿,这个流程的浸取条件比较温和,两年生产实践证明投资和生产成本均低于熔炼流程。
处理辉铜矿的另一个例子是智利依斯康迪达(Escondida)矿,他们采用氨浸流程,在空气氧化,40℃的浸取条件下,辉铜矿的一部分铜很易浸出,余下的为铜蓝。
浸取渣经浮选后得到的精矿含铜41.3%是良好的铜精矿,适合火法冶炼。
这本是一个发挥湿法和火法各自优势的好途径,但是该厂由于严重的技术和经济问题已经停产。
硫化铜矿以黄铜矿最为重要,黄铜矿的浸取是硫化铜矿湿法冶金的核心,三十多年来,做了大量的研究、开发工作,取得很大的进展,工艺、技术、设备设计均已臻成熟,但是至今尚未工业化有可能加压氧化的湿法技术将首先应用于共生元素多、成分复杂但是含银少、品位低的黄铜矿类矿石。
20 世纪60 年代兴起的铜精矿硫酸化焙烧-浸取-电积流程曾风行一时。
精矿浸取液含铜a 以满足电积的要求,但每升多含有几克铁,电积电流效率一般在87%以下。
而且,由于未经除杂,铜产品质量不高。
不过,最大的问题还是焙烧时生成了硫酸铜,焙砂浸取耗酸很少,而电积时总是产生与铜等当量的酸,电积贫液返回浸取酸用不完,整个流程总是“酸过剩”。
因而,不得不将电积贫液脱铜后中和,产生大量含铜石膏,既增加生产成本,还造成污染。
加之,焙烧和火法一样产生二氧化硫,难以彻底避免大气污染。
国内外的这类厂最迟到80 年代多已纷纷关闭。