超精密车削时切屑形成及表面微观形貌形成机理的研究
切削过程中材料去除机制及切屑形态演化研究

切削过程中材料去除机制及切屑形态演化研究切削是一种常见的机械加工方法,通过在工件上施加切削力,去除材料以形成所需的形状和尺寸。
然而,在切削过程中,材料的去除机制以及切屑的形态演化是一个复杂而关键的问题。
研究这些问题不仅有助于深入理解切削过程的本质,还能够指导切削工艺的优化和刀具的设计。
在切削过程中,材料的去除主要通过切削刀具与工件的相对运动来完成。
刀具与工件之间形成一定的切削角,并施加一定的切削力。
切削刀具的刀尖与工件表面相交,形成一个刀尖接触区域。
在这个接触区域内,切削角与切削力共同作用下,材料开始发生塑性变形和切削磨损,从而被去除。
材料的去除机制可分为切削剪切和切削破碎两种。
切削剪切是指材料沿着刀具刃口形成的剪切面上的原子间滑动和轧制,最终导致材料的断裂。
在切削过程中,切削剪切是主要的去除机制。
在搬运切屑的同时,切削刀具也会受到一定的摩擦磨损。
切削剪切的具体机理涉及塑性变形、切削力分析以及刀具与工件接触面的应力分布等方面,仍然是切削研究的重要课题。
切削破碎是指材料在切削过程中发生裂纹和破碎,从而被去除。
切削破碎主要发生在脆性材料或强脆性材料的加工中。
在加工过程中,由于切削刀具的剧烈冲击或高应力作用下,材料发生裂纹、破碎或剥落,并随着切削过程的进行而脱离工件表面。
切削破碎的研究对于脆性材料的切削加工具有重要的指导意义。
切削过程中形成的切屑是切削去除过程的副产品,除了研究切削机理外,研究切屑形态演化也是切削研究的重要内容之一。
切屑的形态与切削工艺参数、材料性质以及刀具性能都密切相关。
切屑可以分为连续切屑、不连续切屑和层状切屑三种形态。
连续切屑具有光滑的表面和较大的形变能,是切削过程中的预期形态。
而不连续切屑和层状切屑通常是由于材料的脆性或切削参数不当引起的,会导致切削过程的变动和不稳定,影响加工质量和效率。
切削过程中材料的去除机制和切屑形态演化的研究一直是学术界关注的热点。
通过对切削剪切和切削破碎的研究,可以优化切削工艺参数、提高刀具的设计和材料的加工性能。
超精密车削表面微观形貌的几何建模与仿真研究

和进给量 / 。 ] 由几 何关 系可 知 , 型 的切 削 有 以 典
下 3 情 况 : 进 给 量 厂较 小 , 种 ① 刀尖 圆 弧半 径 r 较
大 , 时 残 留面 积 由 圆弧 刃 形 成 , 已加 工 表面 形 此 在
鉴 于 上述 情况 , 实 际 超精 密 车 削 时 , 用圆 在 采
圈 1 金 刚 石 车 刀 的 几 何 形 状
65 .
■——. . ’
1
65 I
●—
一
l
f 2
f 3
弧刃 金 刚 石 车 刀对 铝 合 金 进 行 超精 密 车 削 , 验 实 研 究所 用 的刀 具是 英 国 C n o rFn oig公 o t u ieTo l n
石 刀 具 的 主偏 角 、 副偏 角 , 刀 尖 圆弧 半 径 r 、
角 a =7 , o 。刀尖 圆 弧 半径 r=1 5 . mm, 削 刃钝 圆 切
半 径 r≈ 1 0 m。金刚 石 车 刀 的几 何形 状 见 图 l n 9n 。
采 用 圆 弧 刃 车 刀 超 精 密 车 削 生 成 的 表 面 几
\/ /
。
1 超 精 密 车 削表 面微 观 形 貌 的形 成 机 理
在超 精密 车 削时 , 了获得 超 光 滑 表面 , 往 为 往
/一 一 一】 【
导
不 采 用 主切 削刃 和副 切 削 刃相 交 为 一 点 的尖锐 刀
尖 , 采 用 主 切 削 刃 和 副 切 削 刃 之 间具 有 直 线 过 而 渡 刃 的金 刚石 刀 具 。 削外 圆 时 , 车 当参 与切 削 的切 削 刃 与工 件轴 线平 行 , 进 给量 足够 小 时 , 已加 且 在 工 表 面形 成 理 论 残 留面 积 非 常 小 , 时 容 易 获 得 这 理 想 的超 光滑 表 面 。但 直 线刃 金 刚 石 刀具 也存 在 明显不 足 之处 : 为使 切 削 刃 与工 件 轴 线平 行 , ① 直 线 刃 刀 具对 刀时 需 要 花 费 较 长 时 间 ; 直 线 刃 金 ② 刚石 刀 具 切 削 刃 与 工件 接 触 长 度 相 对 较 大 , 削 切 时 易 产生 振动 , 间接 增大 已加 工 表面 粗糙 度 。
镍基单晶高温合金DD5_磨削成屑机理研究

镍基单晶高温合金DD5磨削成屑机理研究*于贵华1, 朱 涛1, 蔡 明1, 安志欣1, 王成静2, 罗书宝1(1. 辽宁石油化工大学 机械工程学院, 辽宁 抚顺 113001)(2. 辽宁石油化工大学 石油化工学院, 辽宁 抚顺 113001)摘要 为研究镍基单晶高温合金DD5的磨削去除机理,提高其加工效率,针对镍基单晶高温合金具有显著各向异性的特点,建立基于Hill 模型的三维有限元磨削模型,研究镍基单晶高温合金DD5的表面加工形貌和切屑形貌,分析切屑形貌演变过程及其磨削力变化,探究磨削速度对切屑形貌和切屑形成频率的影响。
研究表明:在磨削参数范围内,加工DD5容易出现锯齿形切屑;磨削力呈稳定增加并伴有一定的周期性波动,其波动情况与锯齿形切屑相对应;随着磨削速度的增大,磨粒能更快进入切削阶段,其临界成屑厚度由0.225μm 最终降为0.158 μm ,成屑阶段占比由85.0%提高到89.5%;临界划擦厚度受磨削速度变化影响不大;随着磨削速度的增加,DD5切屑形貌由锯齿分节密集堆叠的单元节状向连续型锯齿状转变,最后发展为条形带状切屑。
关键词 磨削;切屑形貌;镍基单晶高温合金DD5;有限元分析中图分类号 TG58; TH161 文献标志码 A 文章编号 1006-852X(2023)06-0760-12DOI 码 10.13394/ki.jgszz.2022.0169收稿日期 2022-10-11 修回日期 2023-01-16作为航空发动机涡轮盘、转子叶片、涡轮导向叶片等关键零部件的主要材料,镍基单晶高温合金具有优异的物理和化学性能,例如抗蠕变性能、耐高温性能、抗冲击性能等[1-2]。
然而,这些优异的力学性能也给其加工制造带来了巨大困难,使其出现加工质量差、加工成本高等缺点[3]。
和其他传统加工方式相比,磨削加工具有加工质量好、精度高等特点,能够满足镍基单晶高温合金在特殊工况下的使用条件[4]。
但是,在磨削过程中镍基单晶高温合金仍出现磨削温度高、磨削力大、能量损耗高、加工效率低等难点[5]。
LECTURE2-超精密车削

超精密加工技术广东工业大学机电工程学院魏昕一、概述¾超精密加工技术的内涵¾超精密加工技术的地位与作用¾超精密加工技术所涉及的技术领域¾超精密加工技术的现状与发展趋势一、概述1. 超精密加工技术的内涵精密加工技术:加工精度1—0.1μm,表面粗糙度Ra <0.1 μm的加工技术;超精密加工技术:加工精度<0.1μm,表面粗糙度Ra <0.02μm的加工技术;纳米加工技术:加工精度达0.001μm(1nm),表面粗糙度Ra <0.005 μm的加工技术。
随着加工技术的不断发展,超精密加工的技术一、概述2、超精密加工技术的地位与作用(1)超精密加工技术是实现现代制造业发展目标(提高机电产品的性能、质量和发展高新技术)的重要手段。
例如,集成电路的集成度。
(2)超精密加工技术已成为国际竞争中取得成功的关键技术。
所能达到的精度水平代表了一个国家的制造业能力和水平。
(3)精密工程、微细工程和纳米技术是现代制造技术的前沿。
/序超精密机械精度要求1导弹、飞机的惯性导航系统中的气浮陀及其马达轴承尺寸精度、圆度、圆柱度要求达到亚微米级2人造卫星仪表轴承表面粗糙度达到1纳米,圆度、圆柱度达纳米级3激光陀螺反光镜表面粗糙度达纳米,平面度达0.05微米4精确制导仪表零件精度达纳米级,若其陀螺转子轴线偏离0.5纳米,就会引起100米左右射程误差5计算机硬盘驱动器、光盘、复印机的精密零件精度达100纳米6微电子芯片刻线机刻线宽度在50纳米以下7基因操作机械移动距离在纳米级,移动精度在0.1纳米(原子尺度)现代超精密机械对精度的要求超精密加工是尖端技术产品发展不可缺少的关键加工手段关系到现代飞机、潜艇、导弹性能和命中率的惯性陀螺框架;激光核聚变用的反射镜;大规模集成电路的各种基片;计算机磁盘基底及复印机磁鼓;各种高精度的光学元器件;各种硬盘及记忆体的衬底等。
×一、概述3、超精密加工技术所涉及的技术领域(1)加工技术即加工方法与加工机理。
单点金刚石车削的工艺参数对表面粗糙度影响的实验研究
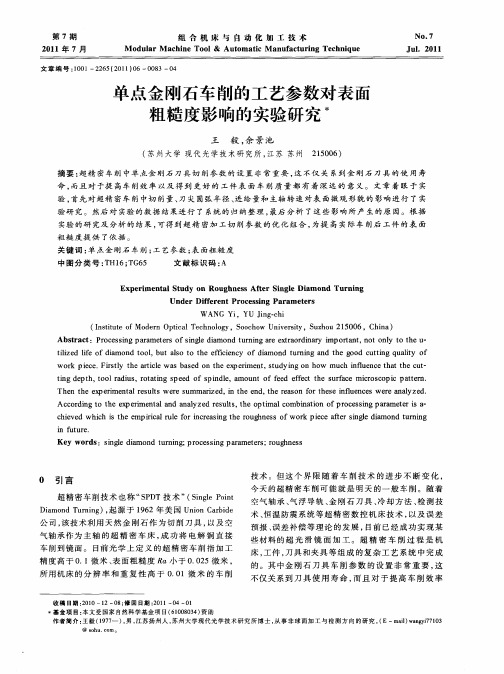
W ANG .YU i g c i Yi Jn - h
(ntueo d r pia T c n l y S oh w U iesy uh u2 0 , hn ) Istt f i MoenO t l eh o g , oco nvri ,S zo 0 6 C ia c o t 1 5
ci e i h mpr a rl frn raigteruh eso r c f r ig i o dtrig he dwhc i tee i lueo c s o gn s f kpee t nl da n nn v hs ic i e n h wo i ae s e m u
i ut r . 1 f u e l
Ke r s s g i n rig p o es gp rmees ru n s ywod : i eda dt nn ; rcsi aa tr;o g es n l mo u n h
O 引 言
超精 密 车削 技术 也 称 “ P T技 术 ” Sn l P it SD ( ige on
/2 ,
具 切 削刃 口的 圆弧 半径 , 当然 针 对不 同材 料 , 佳 工 最
艺 参数 也有 所 不 同 , 就 需 要 大 量 反 复 的 工 艺试 验 这 去 总结 。 有 关超 精密 车削 的工艺 参 数 与 工件 表 面 微 观形 貌 的研 究 , 早在 2 O世 纪 9 0年 代 , 已经展 开 。19 就 95
Ac o dngt he e pei e a n n l e e u t ,t e o i lc mb a in o o e s gpa a t ri ‘ c r i o t x rm nt la d a ayz d r s ls h ptma o i to fpr c s i r me e s a n n
试述超精密切削时积屑瘤生产规律和它对切削过程和加工表面粗糙度的影响。

试述超精密切削时积屑瘤生产规律和它对切削过程和加工表面粗糙度的影响。
介绍如下:
1.生产规律:
•在低速切削时,h0值比较稳定;在中速时,h0值不稳定。
•在进给量f很小时,h0较大。
•在背吃刀量ap<25um时,h0变化不大;在ap>25um时,h0将随ap的值增大而增大。
•刀具的微观缺陷也将直接影响积屑瘤的高度,完整刃的积屑瘤高度比有微小崩刃的刀刃积屑瘤高度小。
2.对切削过程的影响:
•积屑瘤高时切削力大,积屑瘤小时切削力小。
•积屑瘤如生长稳定,起到了保护了刀具,提高了刀具的使用寿命的作用;如频繁脱落,则加剧了刀具的磨损,降低了刀具的使用寿命。
3.对加工表面粗糙度的影响:
•积屑瘤伸出切削刃外的部分高低不平,外形极不规则,增大了已加工表面的粗糙度,降低了表面加工质量。
钻削过程切屑受力建模及有限元仿真研究

钻削过程切屑受力建模及有限元仿真研究一、概述钻削过程是金属加工中常见的加工工艺之一,其切削过程中切屑的形成和受力情况对加工质量和工件表面粗糙度有着重要影响。
本文将针对钻削过程中切屑受力建模及有限元仿真研究展开深入探讨,从宏观和微观两个角度分析切屑的形成机理和受力情况,旨在为钻削工艺提供更深入的理论基础和实用指导。
二、切屑形成机理分析1. 切屑形成的基本过程在钻削过程中,切屑的形成是由刀具对工件进行切削,其中金属材料在刀具作用下形成的薄层即为切屑。
切屑形成的基本过程可以简要概括为切屑的起始、发展和脱离三个阶段。
切屑的形成机理主要包括切削热、切削变形、切削厚度和切屑形状等因素的综合作用。
2. 切屑形成的影响因素切屑形成受到诸多因素的影响,包括工件材料性能、刀具的材料和几何形状、切削参数、冷却液的使用等。
不同的工件材料、刀具材料和切削参数组合会导致切屑的形态、厚度和温度等特性的差异,从而影响切屑的排屑能力、切屑的排屑性能和对切屑的进一步加工。
三、切屑受力情况分析1. 切屑的受力特点切屑在形成过程中会承受来自刀具的切削力、切削热和切屑自身的重力等多种力的作用。
其中,切削力是切屑受力的主要载荷,其大小和方向直接影响切屑的形状和质量。
切屑受力还与刀具的几何形状、切削参数和切削状态等因素相关。
2. 切屑的受力模型有限元分析是研究切屑受力的有效方法之一,通过建立钻削加工的切屑受力模型,可以分析切屑在加工过程中的受力情况。
通过有限元仿真可以得到切屑的应变、应力分布以及切屑的变形情况,从而为钻削工艺的优化提供理论支持。
四、有限元仿真研究1. 切屑受力的有限元模型建立在进行有限元仿真时,首先需要建立钻削过程中切屑受力的有限元模型。
该模型需要考虑刀具、工件、切屑和切削液等多个物理对象及其之间的相互作用,同时要考虑切屑受力的非线性、瞬态和热传导等特性。
通过对切屑受力的有限元模型建立,可以准确地模拟切屑在切削过程中的受力情况。
超高速磨削表面形貌特征的模拟研究
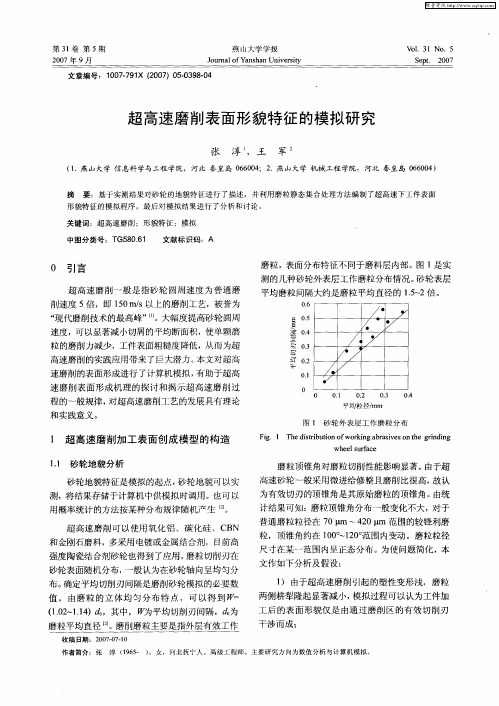
尺寸在 某一范 围内呈正态 分布 。为使 问题简化 ,本 文作如下 分析及假 设:
1 由于超 高速磨 削引起 的塑性变 形浅 ,磨粒 )
值 。 由磨 粒 的 立 体均 匀 分 布 特 点 ,可 以得 到 (.  ̄ . )d,其中 , 1 2 11 o 0 4
维普资讯
第3卷 第 5 1 期
20 0 7年 9月
燕 山 大学 学 报
J u n l f n h n Un v ri o r a s a i e st o Ya y
V.I 0 _31 O.5 N S pt 2 07 e . 0
磨粒 ,表面分布特 征不 同于磨料层 内部 。图 l 是实 测 的几种砂轮外表层 工作磨粒 分布情况 。 轮表层 砂 平均磨粒 间隔大约 是磨粒平均 直径 的 1 - . 2倍 。 5
O6 _
基 05 ,
/ y
’
差o ’
03 . 。2 一 O1 O
0 01 .
淳 (9 5 ) 16 一 ,女,河北抚 宁人 。高级工程师。主要研 究方 向为数值分析与计算机模拟 。
维普资讯
第5 期
张
淳 等
超 高速 磨 削 表面 形貌 特 征 的模 拟 研 究
39 9
2 )超 高速砂 轮结合 剂弹性 模量远 大于普 通砂 轮。 由砂轮基体 和结合剂弹 性变形 引起 的受 力退让
磨粒顶 锥角对 磨粒 切削性 能影响显著 。 由于超
高速砂轮 一般采 用微进 给修整且 磨削 比很 高, 故认 为 有效切刃 的顶锥角是其 原始磨粒 的顶锥角 。由统 计 结果可知 :磨粒顶 锥角分布一 般变化不大 ,对于
- 1、下载文档前请自行甄别文档内容的完整性,平台不提供额外的编辑、内容补充、找答案等附加服务。
- 2、"仅部分预览"的文档,不可在线预览部分如存在完整性等问题,可反馈申请退款(可完整预览的文档不适用该条件!)。
- 3、如文档侵犯您的权益,请联系客服反馈,我们会尽快为您处理(人工客服工作时间:9:00-18:30)。
上的残留区域 ,有关文献将其命名为 spanzipfel 区域。
由图 2 几何关系可知
hth = f2/ 8 R
(1)
h = R - y1 = R - R2 - x2c
(2)
又因为
tanα=
R2 - x2c xc
(3)
因此由式 (3) 可推导出
ቤተ መጻሕፍቲ ባይዱ
α= arctan
R2 - x2c xc
(4)
sinRα=
关键词 :超精密车削 , 金刚石刀具 , 微切屑 , 表面粗糙度 , 表面微观形貌
Study on Formation Mechanism of Chip and Surface Micro2topography in Ultraprecise Turning
Wang Xiaoxia et al
3 表面微观形貌的几何建模与试验研究
在超精密加工中 ,除机床本身的性能外 ,刀具切 削刃有效切除工件材料的最小切削厚度 (MTC) 的可 控性和重复性也是影响加工精度的主要因素 。最小 切削厚度不仅可反映切削刃的纳米级微观结构 ,还 可反映刀具与工件材料之间的相互作用状态 。最小 切削厚度 (MTC) 定义为能够从工件材料上有效去除 金属的最小厚度 。切削厚度越小 ,工件材料抵抗塑 性变形的能力越强 ,刀具与材料原子之间的相互作 用力越弱 。在金刚石刀具切削刃半径仅几个纳米的 特定微切削环境下 ,最终可达到的加工精度与最小 切削厚度为同一个数量级 。日本学者在具有高稳定 性的机床上使用特制的金刚石刀具切削单晶铜 ,获 得了非常微细的切屑 , 并使最小切削厚度达到了 1nm[3 ,4 ] 。
图 2 所示为在理想状态下用圆弧刃金刚石车刀 进行超精密加工时表面形成过程的几何模型 。由图 可知 :在金刚石车削过程中 ,沿车刀圆弧各点形成的 切屑厚度是变化的 ,切屑厚度理论上由零变化到最 大值 。当采用圆弧刃金刚石刀具超精密车削加工软 金属时 ,刀具圆弧半径 R 和进给量 f 是决定加工表 面粗糙度大小的主要因素[5 ,6 ] 。
根据金刚石刀具超精密车削试验结果 ,分析了 微切屑的形成过程 ,讨论了加工过程中刀具切削刃 半径和被加工材料的塑性变形 、弹性恢复变形对加 工表面粗糙度的影响 ,并据此建立了最小切削厚度 与表面粗糙度之间关系的几何模型 ,同时提出一种 通过估算最小切削厚度来预测金刚石车削加工所能
获得的加工表面粗糙度的新方法 。大量试验表明 , 使用该方法估算出的表面粗糙度值与实测表面粗糙 度值具有很好的一致性 。
Keywords : ultraprecise turning , diamond cutter , micro chip , surface roughness , surface micro2topography
1 引言
随着超精密切削机床及其控制技术的迅速发 展 ,切削加工范围已由金属等塑性材料逐渐延伸到 玻璃 、陶瓷等各种难加工材料 。由于金刚石刀具的 物理化学性能以及极薄切削层特性等的影响 ,使超 精密切削具有与普通切削不同的特殊规律 。早在几 十年前 ,国外许多学者就对超精密加工表面形成机 理进行了理论探讨和试验研究 ,但受当时条件的局 限 ,对超光滑表面微观形貌形成机理的解释还具有 一定的片面性 。本文通过用单晶金刚石刀具对铜合 金和铝合金材料进行超精密微切削试验 ,在试验结 果的基础上系统研究了最小切削厚度与表面粗糙度 之间的关系 ,并从微切屑的形成、最小切削厚度、变形 等方面研究了超光滑加工表面微观形貌的形成机理 。
度与切削刃半径之间的关系 ,我们进行了一系列车
削试验 。试验车床为哈尔滨工业大学研制的 HCM21
型亚微米级超精密车床 ;工件材料为铝合金 ;切削深 度为 3μm , 进 给 量 为 10 ~ 50μm/ r , 主 轴 转 速 为
1500r/ min ;刀具切削刃半径约为 175nm。车削铝合
金时 ,最小切削厚度约为采用的刀具切削刃半径的
2001 年第 35 卷 №9
15
加工表面的完整性在很大程度上受到每一晶粒的晶 向和结构的影响 ;当切削深度与刀具刃口半径尺寸 相当时 ,由刀具刃部的磨光和挤压作用产生的塑性 变形在切削中占据主导作用 ,此时在连续切削加工 过程中加工表面将产生不规则变形层 ,这是造成加 工表面和切屑表面金属晶粒边界不明显的主要原 因[1 ,2 ] 。
Abstract :The cutting tests with single crystal diamond tools are carried out on a submicron CNC ultraprecise lathe. According to test results , the chip formation mechanism and the relationship between the minimum cutting thickness and surface roughness are analyzed , and the model of micro2topography on the machined surface is established. The investigation shows that it is possible to predict the surface roughness obtained in the diamond turning by calculating the minimum cutting thickness.
2 切屑的形成机理
通过研究微切屑的形成与加工表面粗糙度之间 的关系 ,可以揭示刀具几何形状和切削参数对加工 表面粗糙度的影响 。为此 ,我们在哈尔滨工业大学 自行研制的 HCM21 型亚微米级超精密车床上进行 了一系列切削试验 。试验材料为铜合金 ;切削深度 为 1 ~ 10μm ; 进 给 量 为 3μm/ r ; 主 轴 转 速 为
14
工具技术
超精密车削时切屑形成及表面微观形貌形成机理的研究
黑龙江佳木斯大学 (154007) 王晓霞 哈尔滨工业大学 (150001) 王洪祥 中国人民解放军防化指挥工程学院 李明洪
摘 要 :在亚微米级 CNC 超精密车床上进行了单晶金刚石刀具切削试验 ,根据试验结果分析了切屑形成机理 和最小切削厚度与表面粗糙度之间的关系 ,建立了加工表面微观形貌的几何模型 。研究结果表明 :通过计算最小 切削厚度值可预测金刚石车削加工可获得的表面粗糙度值 。
图 2 超精密车削表面形成过程几何模型
图 2 中 , hth为理想状态下加工表面形成的轮廓 峰与轮廓谷之间的距离 ,即理论粗糙度值 。在加工 过程中 ,由于最小切削厚度的存在 ,在实际加工表面
形成的轮廓峰与轮廓谷之间的距离 h 通常与理论粗
糙度值 hth不同 。tmin为最小切削厚度 ,它是决定最终 加工精度的主要因素之一 。图中阴影表示加工表面
0. 4~0. 6 倍 ,这一比值随着被加工材料和切削条件
(如进给量 、刀具圆弧半径等) 的不同而略有差异 。
利用上述公式中的中间变量 xc 建立起加工表 面形成的轮廓峰与轮廓谷之间距离 h 与最小切削
厚度 tmin之间的关系 ,利用这一几何关系仿真出的表 面形貌在形状上与较理想状态下形成的表面微观形
2001 年 8 月 16 日 ,机床杂志社在中国科技会堂举行了 《制造技术与机床》杂志创刊 50 周年庆典 ,全国政协委员 、提 案委员会主任 、中国机械工程学会理事长 、原机械工业部部 长何光远和中国机床工具工业协会名誉理事长梁训王宣等 140 余位领导 、专家学者和企业代表到会祝贺 。
2 T Nishiguchi. Mechanism of micro chip formation in diamond turning of Al2Mg alloy. Annals of the CIRP ,1986 ,37 (1) :117~ 120
3 Naoya Ikawa , Shoichi Shimada. Minimum thickness of cut in micromachining. Nanotechnology , 1992 , 3 :6~9
(a) 切屑全貌 (b) 切屑表面形貌 (c) 切屑边部 图 1 超精密车削铜合金时形成切屑的 SEM 照片
观察加工表面微观形貌的 AFM 照片和切屑的 SEM 照片可以发现 :因刀具磨损造成的切削刃不完 整性复映到加工表面上 ,从而产生平行于切削方向 的刀具刮痕 。当采用较大切削深度时 ,加工表面和 切屑表面的晶粒边界比较清晰 ;采用较小切削深度 时 ,可观察到的金属晶粒边界也较小 (从切屑的 SEM 照片中几乎观察不到金属晶粒边界) 。由此可得出 结论 :当切削深度大于刀具刃口半径尺寸时 ,工件材 料主要以传统切削方式被切除 ,形成的切屑表面和
5 S Asai. Observation of chip producing behaviour in ultra2preci2 sion diamond machining and study on mirror2like surface gene2 rating mechanism. Precision Engineering , 1990 ,12 (3) :137~ 143
收稿日期 :2001 年 4 月
1500r/ min 。从局部放大的切屑 SEM 照片上可以看 出 :切削铜合金时产生的切屑是由剪切滑移的层状 薄片堆积形成 ,且卷曲成螺旋状 。试验表明 :沿圆弧 刀具切削刃的有效切削厚度是一个变量 ,在切削刃 与待加工表面接触点处切削厚度达到最大值 。当切 削厚度较大时 ,切屑的表面结构较紧密 ;切削厚度较 小时 ,切屑的表面结构则较疏松 ;同时 ,随着切削深 度的减小 , 切屑的卷曲半径增大 。当切削深度为 1μm 时所形成切屑的 SEM 照片如图 1 所示 。