切屑的形成过程
机械加工切屑形成过程及种类

机械加工切屑形成过程及种类机械加工是指利用机床进行金属材料切削、锉削、抛光等工艺,将工件加工成所需形状和尺寸的加工方法。
在机械加工过程中,由于工具与工件之间的相对运动,会产生切屑。
切屑是指在机械加工过程中,由于切削力的作用和切削部分和工件材料之间的摩擦力的作用,使金属材料脱离工件而形成的废料。
1.切削过程:在机械加工过程中,工具相对于工件进行切削。
切削过程是切屑形成的起点。
切削过程中切削刀具与工件的摩擦力和切削力作用于工件上。
2.金属切错:由于切削刀具和工件的相互作用力,金属材料会发生切削变形,切削很薄的切片和切削薄片之间的间距,即切削错觉。
这种切削错觉会导致材料分离和产生切削切,形成切削筹码。
3.切削筹码分离:随着切削过程的进行,切削刃不断深入工件的表面,形成足够深度的切削面。
在切削过程中,切削筹码被切削刃压向后方,并在切削刃之后分离。
4.切屑形成:随着切削刃逐渐深入工件,切削刃与工件接触的接触面积逐渐增加。
切削刃生成的切削面与工件表面接触,金属材料开始被分离,形成切插和切插在切削刃上的切插形成切屑。
切屑根据其形状和特点可以分为以下几类:1.螺旋卷屑:螺旋卷屑是机械加工中最常见的切屑形式之一、它的形状类似于螺旋形。
螺旋卷屑形成是因为切削刃与工件表面之间的摩擦力和切削力,使金属材料呈螺旋形状被分离。
2.螺纹形卷屑:螺纹形卷屑与螺旋卷屑类似,但具有螺纹形状。
螺纹形卷屑主要在对内螺纹切削中产生。
3.花形卷屑:花形卷屑是螺旋卷屑的一种特殊形式。
它的形状类似于花瓣,具有很高的韧性和弯曲性。
花形卷屑主要在刃具前部有圆角的切削中产生。
4.细末卷屑:细末卷屑是切削薄片脱离工件表面时变形和分离的结果。
这种切屑形态常见于高速切削和高速铣削等加工过程。
5.碎屑:碎屑是在没有明显的切削形状的情况下产生的废料。
碎屑主要在金属材料脆性较高时产生。
总结起来,机械加工切屑的形成过程可以概括为切削过程、金属切错、切削筹码分离和切屑形成。
切削铁屑形成原理

切削铁屑形成原理引言:切削铁屑形成是在金属切削过程中常见的现象,它是由切削工具与工件之间的相互作用引起的。
本文将以切削铁屑形成原理为主题,详细解析切削铁屑的形成过程以及影响因素。
一、切削铁屑的形成过程切削铁屑的形成是由于切削工具对工件进行切削时,金属材料被剪断而产生的。
具体而言,切削铁屑的形成过程可以分为以下几个阶段:1. 切削工具进入切削区域:切削工具以一定的速度和角度进入工件的切削区域,与工件表面接触。
2. 剪切力作用:切削工具施加剪切力,使工件产生塑性变形。
在这个过程中,切削工具与工件之间的摩擦力也起到了重要的作用。
3. 剪切屑的形成:在剪切力的作用下,工件的金属材料开始发生剪切断裂。
这时,金属材料从工件中剥离出来,形成切削铁屑。
4. 切削铁屑的排出:切削铁屑随着切削过程的进行,被切削液或气流带走,排出切削区域。
二、切削铁屑形态的分类切削铁屑的形态可以根据其外观和结构进行分类,常见的切削铁屑形态有以下几种:1. 连续切屑:连续切屑是切削过程中产生的一种常见切削铁屑形态。
它的形状规整,呈螺旋状或螺旋状曲线。
连续切屑的形成主要与工件材料的塑性变形特性和切削工具的几何形状有关。
2. 断续切屑:断续切屑是切削过程中产生的另一种常见切削铁屑形态。
它的形状不规则,呈不连续的碎片状。
断续切屑的形成主要与工件材料的脆性和切削工具的切削速度有关。
3. 螺旋切屑:螺旋切屑是连续切屑中的一种特殊形态,其形状呈螺旋状。
螺旋切屑的形成主要与切削工具的几何形状和切削速度有关。
4. 螺旋碎屑:螺旋碎屑是断续切屑中的一种特殊形态,其形状呈碎片状且具有螺旋结构。
螺旋碎屑的形成主要与工件材料的脆性和切削工具的切削速度有关。
三、影响切削铁屑形成的因素切削铁屑的形成受到多种因素的影响,主要包括以下几个方面:1. 切削速度:切削速度是切削铁屑形成的重要因素之一。
过高或过低的切削速度都会导致切削铁屑形态异常,影响切削质量。
2. 切削深度:切削深度对切削铁屑形态有直接影响。
第一章 金属切削过程中的基本规律讲解
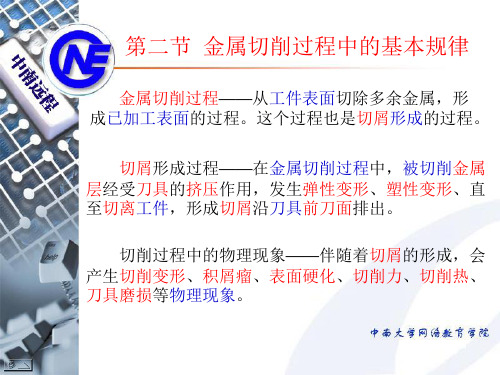
②增大前角 积屑瘤具有30°左右的前角。
③增大切削厚度 切削厚度增大了ΔhD。
④增大已加工表面粗糙度
原因:积屑瘤不规则的形状和非周期性的生成与脱 落、可能引起的振动、积屑瘤碎片残留在已加工表面 上。
积屑瘤
(3)影响积屑瘤的主要因素
在滑动区内的摩擦为外摩擦,该处的剪应力τy 由τs 逐渐减小到零。
正应力σγ 在刀刃处最大,离切削刃越远,前刀面上 的正应力越小,并逐渐减小到零。
刀-屑接触面上的摩擦特性
刀-屑接触面上的摩擦特性
前刀面上的摩擦系数μ是变化的,其计算公式如下:
s av
式中 τs ——工件材料的剪切屈服强度,随温度升 高而略有下降
响比较明显,前角γ0 对切削力的影响最大。
切削热的产生和传出
(1)切削热的产生 切削加工中,切削变形与摩擦所消耗的能量几乎全 部转换为热能,因此三个变形区就是三个发热源。如 下图所示。
切削热的产生和传出
(2)切削热的传出 由切屑、刀具、工件、周围介质传导出去。
车削钢料时,切削热被切屑带走约50% ~ 86%,传入 刀具的约占10% ~ 40%,传入工件的约为3% ~ 9%,传入 周围介质的约占1%。
相对滑移ε
切削层中m´n´线滑移至m˝n˝ ,瞬时位移为∆y , 滑移量为∆s 。
cos o
sin cos( o )
增大前角γo 和剪切角φ,则
相对滑移ε减小,即切削
变形减小。
变形系数ξ
将切削时形成的切屑与切削层尺寸比较,可知切 屑的长度缩短而厚度增加。 变形系数就是切屑厚度和 切削层厚度的比值,或者是切削层长度和切屑长度的 比值。
钻削过程切屑受力建模及有限元仿真研究

钻削过程切屑受力建模及有限元仿真研究一、概述钻削过程是金属加工中常见的加工工艺之一,其切削过程中切屑的形成和受力情况对加工质量和工件表面粗糙度有着重要影响。
本文将针对钻削过程中切屑受力建模及有限元仿真研究展开深入探讨,从宏观和微观两个角度分析切屑的形成机理和受力情况,旨在为钻削工艺提供更深入的理论基础和实用指导。
二、切屑形成机理分析1. 切屑形成的基本过程在钻削过程中,切屑的形成是由刀具对工件进行切削,其中金属材料在刀具作用下形成的薄层即为切屑。
切屑形成的基本过程可以简要概括为切屑的起始、发展和脱离三个阶段。
切屑的形成机理主要包括切削热、切削变形、切削厚度和切屑形状等因素的综合作用。
2. 切屑形成的影响因素切屑形成受到诸多因素的影响,包括工件材料性能、刀具的材料和几何形状、切削参数、冷却液的使用等。
不同的工件材料、刀具材料和切削参数组合会导致切屑的形态、厚度和温度等特性的差异,从而影响切屑的排屑能力、切屑的排屑性能和对切屑的进一步加工。
三、切屑受力情况分析1. 切屑的受力特点切屑在形成过程中会承受来自刀具的切削力、切削热和切屑自身的重力等多种力的作用。
其中,切削力是切屑受力的主要载荷,其大小和方向直接影响切屑的形状和质量。
切屑受力还与刀具的几何形状、切削参数和切削状态等因素相关。
2. 切屑的受力模型有限元分析是研究切屑受力的有效方法之一,通过建立钻削加工的切屑受力模型,可以分析切屑在加工过程中的受力情况。
通过有限元仿真可以得到切屑的应变、应力分布以及切屑的变形情况,从而为钻削工艺的优化提供理论支持。
四、有限元仿真研究1. 切屑受力的有限元模型建立在进行有限元仿真时,首先需要建立钻削过程中切屑受力的有限元模型。
该模型需要考虑刀具、工件、切屑和切削液等多个物理对象及其之间的相互作用,同时要考虑切屑受力的非线性、瞬态和热传导等特性。
通过对切屑受力的有限元模型建立,可以准确地模拟切屑在切削过程中的受力情况。
机械加工工艺基础培训课件
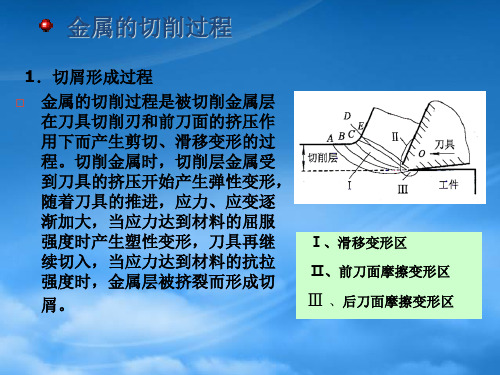
工艺路线的拟定
经济精度:在正常加工条件下所能达到的加工精度及表面粗糙度
各种表面不同加工方法的经济精度及表面粗糙度
加工 表面
加工 方法
外圆柱面 和端面
粗车 半精车 精车 粗磨 精磨 研磨 超精加工 金刚车
平面
粗刨(铣) 精刨(铣) 粗磨
经济精度 等级IT
11~13 9~10 7~8 8~9 6 5 5~6 6
Kr =νc60 /(νc60)j Kr越大,性能越好.
机加工工艺过程的基本概念
1.生产过程和工艺过程 生产过程:将原材料转变为成品的全过程。 工艺过程:改变生产对象的形状、尺寸、相对位置和性质,
使其成为成品或半成品的过程。
工艺过程是生产过程的主要部分,其余为辅助过程。
2.工艺过程的组成
工序
安装1 安装2
精磨 刮研 研磨
经济精度 等级IT
11~12 11~12 8~9 7~8 7~8 6~7 6~7 5~6
6~7 6~7 5
表面粗 糙度
μm
12.5~25 6.3~12.5 1.6~3.2 0.8~1.6 0.2~0.8 0.1~0.2 0.025~0.1 0.025~0.1
0.16~1.25 0.16~1.25 0.006~0.1
11~13 8~10 8~9
表面粗 糙度
μm
12.5~50 3.2~6.3 0.8~1.6 0.4~0.8 0.1~0.4 0.012~0.1 0.012~0.1 0.025~0.4
12.5~50 1.6~6.3 1.25~5
加工 表面
圆柱 孔
平面
加工 方法
钻孔 粗镗 半精镗 精镗、铰 粗磨 精磨 珩磨 研磨
正常磨损阶段: 此阶段磨损速度减慢,磨损量随时间的增加均 匀增加,切削稳定,是刀具的有效工作阶段。
机械制造技术PPT课件第二章金属切削基本原理

合理副偏角值的选择
添加标题
一般较小
添加标题
—5°~10°
添加标题
精加工
添加标题
—小,0°
添加标题
加工高强高硬材料或断续切削
添加标题
—小,4°~6°
添加标题
切断刀、锯片、槽铣刀
添加标题
—小,1°~2°
过渡刃的型式
①直线刃
—粗车、强力车 κrε=κr/2
②圆弧刃
—粗糙度值小
冷却作用 清洗与防锈作用
常用切削液及其选用 =乳化油+水 切削油 = 矿物油、+动植物油 极压切削油 =切削油+硫、氯和磷极压添加剂 难加工材料的精加工
=水+防锈剂、清洗剂、油性添加剂 磨削、粗加工
①水溶液
01
车削、钻削、攻螺纹 滚齿、插齿、车螺纹、一般精加工
②乳化液
02
刀具磨损与刀具耐用度
4
磨屑形态
带状切屑
直线刃、折线刃、圆弧刃、波形刃
刀具合理几何参数选择应考虑的因素
—化学成分、制造方法、热处理状态 性能,表层情况等
①工件材料
壹
—化学成分、性能,刀具结构形式
②刀具材料及结构
—机床、夹具,系统刚性,功率 切削用量和切削液
③加工条件
叁
贰
各参数间的联系 —综合考虑相互作用与影响
刀具角度的选择
大后角→减小摩擦、提高寿命、改善表面质量 强度降低、散热差、磨损加快
后角的选择原则
工艺系统刚性 刚性差—振动 → 小后角 精度要求高 —重磨 → 小后角
切削层厚度hD小 → 大后角 切削层厚度hD大 → 小后角
强度、硬度高 → 小后角 塑性大 → 大后角
金属工艺学第一章 金属切削基础知识
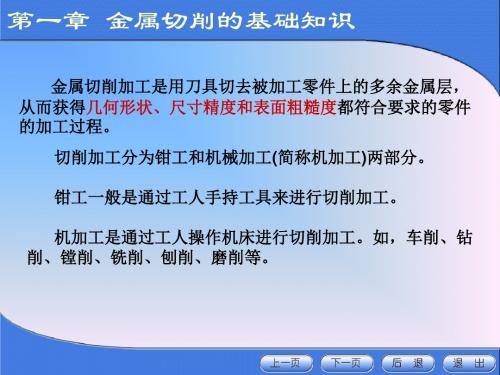
主要的影响因素
切削速度 (切中碳钢) <5m/min不产生 5~50m/min形成
控 制 措 降低塑性 施
(正火、调质)
>100 m/min不形成 选用低速或高速
冷却润滑条件
300~500oC最易产 生 >500oC趋于消失
选用切削液
第三节 金属切削过程
三、切削力与切削功率
1、切削力的构成与分解
切削力的来源
热处理变形 不需要
用途
各种刀片
1200
(12~14)
高硬度钢材 精加工
人造金刚石
HV10000 (硬质合金为 HV1300~1800)
700~800
不宜加工钢铁材 料
第二节 刀具材料及刀具构造
三、刀具角度
各种刀具的切削部分形状
第二节 刀具材料及刀具构造
二、刀具角度
1、车刀切削部分的组成
三面
两刃 一尖
(2)作用 ①冷却 ②润滑
第三节 金属切削过程
五、刀具磨损和刀具耐用度
1、刀具磨损形式
(1)前刀面磨损 (2)后刀面磨损 (通常以后刀面磨损值VB表示刀具磨损程度) (3)前后刀面同时磨损
2、刀具磨损过程:
前面磨损、后面磨损、前后面同时磨损 。 刀具磨损过程: 初期磨损阶段、正常磨损阶段、急剧磨损阶段
刀尖高低对刀具工作角度的影响
车刀刀杆安装偏斜对刀具角度的影响
② 进给运动的影响
第二节 刀具材料及刀具构造
三、刀具结构
刀具的结构形式很多,有整体式、焊接式、机夹 不重磨式等。
目前一般整体式的多为高速钢车刀,其结构简单, 制造、使用都方便。而对于贵重刀具材料,如硬质合 金等,可采用焊接式或机夹不重磨式。焊接式车刀结 构简单、紧凑、刚性好,可磨出各种所需角度,应用 广泛。
切屑的形成过程ppt课件
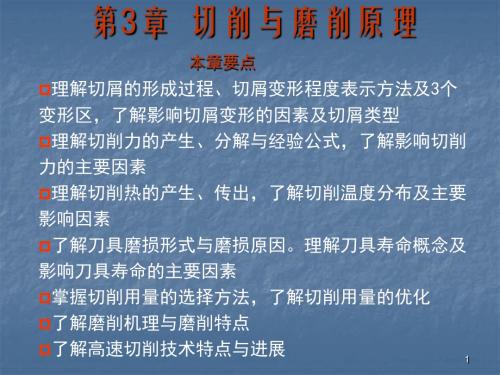
机械制造技术基础
第3章 切削与磨削原理 Cutting and Grinding Theory
3.1 切屑的形成过程 Cutting process
2
3.1.1 切削的形成过程
直角自由切削
没有副刃参加切削,且λs = 0°。
a)直角切削
b)斜角切削
c)不自由切削
图3-1 直角、斜角自由切削与不自由切削
F
B
O
a)正挤压
45° M A F
BO
b)偏挤压
切削:与偏挤压情况类似。弹性变
M
形→剪切应力增大,达到屈服点→产 生塑性变形,沿OM线滑移→剪切应
O F
力与滑移量继续增大,达到断裂强度
c)切削
→切屑与母体脱离。
图3-3 金属挤压与切削比较4
3.1.1 切削的形成过程
金属切削变形过程
切削变形实验设备与录像装置
第3章 切削与磨削原理
本章要点
理解切屑的形成过程、切屑变形程度表示方法及3个 变形区,了解影响切屑变形的因素及切屑类型 理解切削力的产生、分解与经验公式,了解影响切削 力的主要因素 理解切削热的产生、传出,了解切削温度分布及主要 影响因素 了解刀具磨损形式与磨损原因。理解刀具寿命概念及 影响刀具寿命的主要因素 掌握切削用量的选择方法,了解切削用量的优化 了解磨削机理与磨削特点 了解高速切削技术特点与进展
图3-10 积屑瘤
13
积屑瘤高度
3.1.3 前刀面上刀-屑的摩擦与积屑瘤
切削速度
切削速度对积屑瘤的影响
14
3.1.4 影响切削变形的因素
工件材料
工件材料强度和硬度越大,变形系数Λh越小,即切屑变形越小。图3-11
- 1、下载文档前请自行甄别文档内容的完整性,平台不提供额外的编辑、内容补充、找答案等附加服务。
- 2、"仅部分预览"的文档,不可在线预览部分如存在完整性等问题,可反馈申请退款(可完整预览的文档不适用该条件!)。
- 3、如文档侵犯您的权益,请联系客服反馈,我们会尽快为您处理(人工客服工作时间:9:00-18:30)。
积屑瘤影响
◆ 增大前角,保护刀刃 ◆ 影响加工精度和表面 粗糙度
积屑瘤的动态演示1 积屑瘤的动态演示2 积屑瘤的动态演示3
积屑瘤
刀具
图3-10 积屑瘤
郭德伟
13
3.1.3 前刀面上刀-屑的摩擦与积屑瘤
积屑瘤高度
切削速度
切削速度对积屑瘤的影响
郭德伟
14
3.1.4 影响切削变形的因素
工件材料
工件材料强度和硬度越大,变形系数Λh越小,即切屑变形越小。图3-11
Flash 演示Biblioteka Flash 演示郭德伟
24
郭德伟
4
3.1.1 切削的形成过程
金属切削变形过程
切削变形实验设备与录像装置
郭德伟
5
3.1.1 切削的形成过程
金属切削变形过程
切屑 M 终滑移线
A
Φ剪切角 始滑移线:τ=τs O
刀具
图3-4 切屑根部金相照片
郭德伟
6
3.1.1 切削的形成过程
三个变形区分析
第Ⅰ变形区:即剪切变形区 ,金属剪切滑移,成为切屑。 金属切削过程的塑性变形主要 集中于此区域。
断屑是对已变形的切屑再附加一次变形(常需有断屑装置, 图3-17b)
图3-7 切屑的卷曲
郭德伟
21
3.1.6 硬脆非金属材料切屑形成机理
脆性断裂条件
G>GC
(3-7)
式中 G —— 裂纹扩展单位长度时释放的能量(应变能 释放率); GC ——裂纹扩展单位长度时所需的能量(裂纹扩 展阻力)。 对于Ⅰ型(张开型)裂纹,在平面应变条件下,脆性断 裂条件为: K1>K1C 式中 K1 —— 应力强度因 子; K1C —— K1临界值。
σn
τ
已加工表面变形
应力分布
A点前方正应力最大,剪应力为 0。 A点两侧正应力逐渐减小,剪应力逐渐增大,继而减小。
郭德伟
Δh
12
3.1.3 前刀面上刀-屑的摩擦与积屑瘤
积屑瘤成因
◆ 一定温度、压力作用下,切屑底层与前刀面发生粘接 ◆ 粘接金属严重塑性变形,产生加工硬化
积屑瘤形成过程
滞留—粘接—长大
郭德伟
1
机械制造技术基础
第3章 切削与磨削原理 Cutting and Grinding Theory
3.1 切屑的形成过程 Cutting process
郭德伟
2
3.1.1 切削的形成过程
直角自由切削
没有副刃参加切削,且λs = 0°。
a)直角切削
b)斜角切削
c)不自由切削
图3-1 直角、斜角自由切削与不自由切削
郭德伟
16
3.1.4 影响切削变形的因素
切削用量
有积屑瘤的情况 vc通过积屑瘤前角γb(即实际工作前角γoe)来影响变形系数Λh,图314所示。 背吃刀量ap对变形系数Λh基本无影响。
郭德伟
17
3.1.5 切屑类型及切屑控制
表3-1 切屑类型及形成条件
名称 带状切屑 挤裂切屑 单元切屑 崩碎切屑
变形系数
切削层经塑性变形后,厚度增加,长度缩小,宽度基本 不变。可用其表示切削层的变形程度。 ◆ 厚度变形系数 hch (3-3a) ha hD ◆ 长度变形系数 Lc hl Lch
Lch Lc
(3-3b)
因为体积相同,切削层宽度近似相同
图3-8 切屑与切削层尺寸 h称变形系数,h愈大,说 明切屑的变形程度愈大。
第3章 切削与磨削原理
本章要点
理解切屑的形成过程、切屑变形程度表示方法及3个
变形区,了解影响切屑变形的因素及切屑类型 理解切削力的产生、分解与经验公式,了解影响切削 力的主要因素 理解切削热的产生、传出,了解切削温度分布及主要 影响因素 了解刀具磨损形式与磨损原因。理解刀具寿命概念及 影响刀具寿命的主要因素 掌握切削用量的选择方法,了解切削用量的优化 了解磨削机理与磨削特点 了解高速切削技术特点与进展
郭德伟
3
3.1.1 切削的形成过程
挤压与切削
切屑的形成与切离过程,是切削 层受到刀具前刀面的挤压而产生以 滑移为主的塑性变形过程。 正挤压:金属材料受挤压时,最大 剪应力方向与作用力方向约成45°
45° M A F
O B a)正挤压
45° M A B O F
偏挤压:金属材料一部分受挤压时 b)偏挤压 , OB 线以下金属由于母体阻碍,不 能沿AB线滑移,而只能沿OM线滑移 M 切削:与偏挤压情况类似。弹性变 O 形→剪切应力增大,达到屈服点→产 F 生塑性变形,沿 OM 线滑移 → 剪切应 c)切削 力与滑移量继续增大,达到断裂强度 →切屑与母体脱离。 图3-3 金属挤压与切削比较
简图
形态 变形 形成 条件
带状,底面光滑 ,背面呈毛茸状 剪切滑移尚未达 到断裂程度
节状,底面光滑有裂 纹,背面呈锯齿状
粒状
不规则块状颗粒
未经塑性变形即 被挤裂 加工硬脆材料, 刀具前角较小
局部剪切应力达到断 剪切应力完全达 到断裂强度 裂强度
加工塑性材料, 切削速度较高, 进给量较小, 刀具前角较大
郭德伟
23
(3-8)
3.1.5 硬脆非金属材料切屑形成机理
脆性材料切削过程
◆ 大规模挤裂与小规模挤裂交替进行
a)
b)
c)
d)
e)
图3-13 硬脆材料切削过程
a)大规模挤裂(大块破碎切除) b)空切 c)小规模挤裂(小块破碎切除) d)小规模挤裂(次小块破碎切除) e)重复大规模挤裂(大块破碎切除)
刀具几何参数
刀具几何参数中影响最大的是前角。刀具前角γo越大,剪切角φ变 大,变形系数Λh就越小图3-12
郭德伟
15
3.1.4 影响切削变形的因素
切削用量
无积屑瘤的情况 切削速度vc越高,变形系数Λh越小。
进给量 f 越大,hD增大,前刀面上的σav 增大,切应力减小,摩擦系数减小,剪
切角φ加大,变形系数Λh越小。
郭德伟
9
hch Lc (3-3) h hD Lch
3.1.2 切屑变形程度的表示方法
变形系数
h hch OM sin(90 0 ) hD OM sin
hch K N
γ0
h
cos( 0 ) (3-4) sin
0P
M hD
18
3.1.5 切屑类型及切屑控制
切屑类型
带状 切屑
挤裂 切屑
粒状 切屑
图3-16 切屑形态照片
崩碎 切屑
郭德伟
19
3.1.5 切屑类型及切屑控制
国际标准化组织的切屑分类法
郭德伟
20
切屑控制
3.1.5 切屑类型及切屑控制
为使切削过程正常进行和保证已加工表面质量,应使切 屑卷曲和折断。 切屑的卷曲是切屑基本变形或经过卷屑槽使之产生附加 变形的结果(图3-17a)
切削过程平稳, 表面粗糙度小, 妨碍切削工作, 应设法断屑
加工塑性材料, 切削速度较低, 进给量较大, 刀具前角较小
切削过程欠平稳, 表面粗糙度欠佳
工件材料硬度较 高,韧性较低, 切削速度较低
影响
切削力波动较大, 切削力波动大,有 切削过程不平稳, 冲击,表面粗糙度 表面粗糙度不佳 恶劣,易崩刀
郭德伟
lf1 lf2
图3-9 切屑与前刀面的摩擦
郭德伟
11
3.1.3 前刀面上刀-屑的摩擦与积屑瘤
加工表面变形原因
切削刃存在刃口圆弧, 导致挤压和摩擦,产生 第Ⅲ变形区。
hD ΔhD
变形情况
A 点以上部分沿前刀面 流出,形成切屑; A 点 以下部分受挤压和摩擦 留在加工表面上,并有 弹性恢复。
τ
A
C E F
Ⅱ
Ⅰ
Ⅲ
第Ⅱ变形区:靠近前刀面处 图3-6 切削部位三个变形区 ,切屑排出时受前刀面挤压与 摩擦。此变形区的变形是造成前刀面磨损和产生积屑瘤的 主要原因。 第Ⅲ变形区:已加工面受到后刀面挤压与摩擦,产生变 形。此区变形是造成已加工面加工硬化和残余应力的主要 原因。
郭德伟
7
3.1.2 切屑变形程度的表示方法
剪应变(相对滑移系数)
S y
hch
γ0
NK KP
0P
M hD
K N
MK cot tan( 0) cos 0 sin cos( 0)
φ
O
(3-2)
剪切角愈小,前角愈小—>剪切变形量愈大
图3-7 剪应变的计算
郭德伟
8
3.1.2 切屑变形程度的表示方法
变形为
φ
O
cos 0 t an h sin 0
2 2 h sin 0 1 h h cos 0
郭德伟
10
3.1.3 前刀面上刀-屑的摩擦与积屑瘤
摩擦特点
在高温高压作用下,切屑底层与前刀面发生沾接,切屑 与前刀面之间既有外摩擦,也有内摩擦。
两个摩擦区
粘结区:高温高压使切屑底 层软化,粘嵌在前刀面高低不 平的凹坑中,形成长度为lf1的 粘接区。切屑的粘接层与上层 金属之间产生相对滑移,其间 的摩擦属于内摩擦。 滑动区:切屑在脱离前刀面 之前,与前刀面只在一些突出 点接触,切屑与前刀面之间的 摩擦属于外摩擦。