全国大学生数学建模竞赛2018年B题智能RG的动态调度策略及优秀论文精选
《2024年2016年全国大学生数学建模竞赛B题解题分析与总结》范文
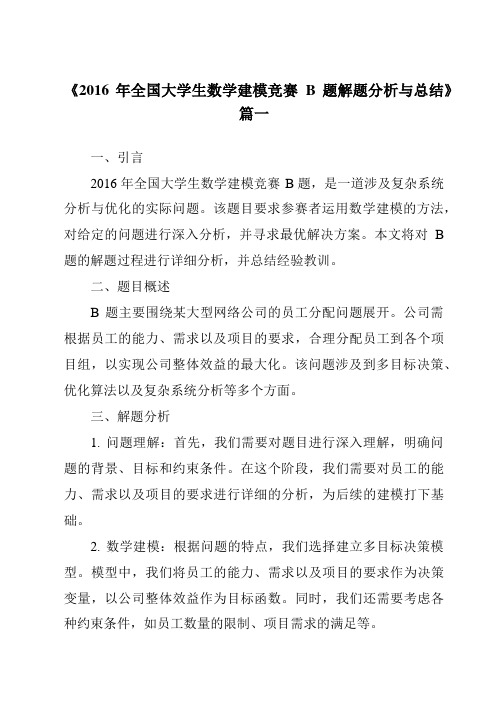
《2016年全国大学生数学建模竞赛B题解题分析与总结》篇一一、引言2016年全国大学生数学建模竞赛B题,是一道涉及复杂系统分析与优化的实际问题。
该题目要求参赛者运用数学建模的方法,对给定的问题进行深入分析,并寻求最优解决方案。
本文将对B 题的解题过程进行详细分析,并总结经验教训。
二、题目概述B题主要围绕某大型网络公司的员工分配问题展开。
公司需根据员工的能力、需求以及项目的要求,合理分配员工到各个项目组,以实现公司整体效益的最大化。
该问题涉及到多目标决策、优化算法以及复杂系统分析等多个方面。
三、解题分析1. 问题理解:首先,我们需要对题目进行深入理解,明确问题的背景、目标和约束条件。
在这个阶段,我们需要对员工的能力、需求以及项目的要求进行详细的分析,为后续的建模打下基础。
2. 数学建模:根据问题的特点,我们选择建立多目标决策模型。
模型中,我们将员工的能力、需求以及项目的要求作为决策变量,以公司整体效益作为目标函数。
同时,我们还需要考虑各种约束条件,如员工数量的限制、项目需求的满足等。
3. 算法设计:在建立模型后,我们需要设计合适的算法来求解模型。
在这个阶段,我们选择了遗传算法和模拟退火算法进行求解。
遗传算法能够在大范围内搜索最优解,而模拟退火算法则能够在局部范围内进行精细搜索,两种算法的结合能够更好地求解该问题。
4. 求解与优化:在算法设计完成后,我们开始进行求解与优化。
首先,我们使用遗传算法对模型进行粗略求解,得到一组初步的解决方案。
然后,我们使用模拟退火算法对初步解决方案进行优化,以得到更优的解决方案。
在优化过程中,我们还需要不断调整模型的参数和算法的参数,以获得更好的求解效果。
5. 结果分析:在得到求解结果后,我们需要对结果进行分析。
首先,我们需要对结果进行验证,确保结果的正确性和有效性。
然后,我们需要对结果进行敏感性分析,分析各种因素对结果的影响程度。
最后,我们需要提出一些管理建议和改进措施,以帮助公司更好地解决实际问题。
2015年全国大学生数学建模竞赛B题国一优秀论文
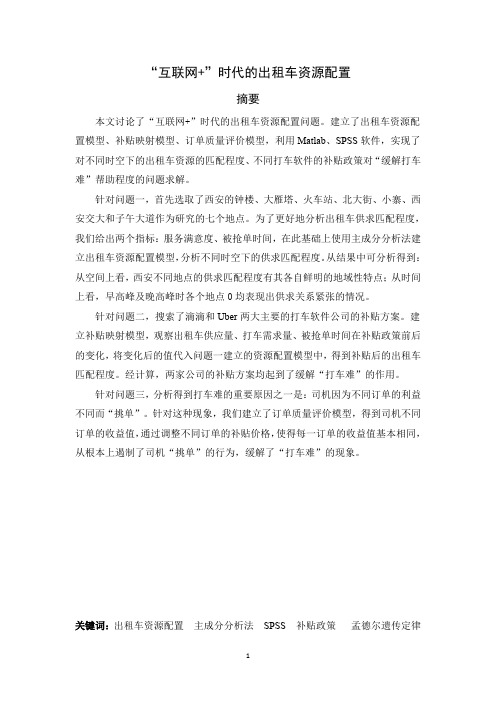
2.1 概论 目前城市“打车难”的社会问题导致越来越多的打车软件出现在市场上。以
此为背景,我们需要首先分析影响出租车资源的“供求匹配”程度的因素,进而 分析现已出台的补贴政策是否能够通过调整“供求匹配”程度进而缓解“打车难” 的现象,并在最后提出了我们自己关于补贴方案的想法。 2.2 问题一分析
0.70
0.53
0.66
0.68
0.40
0.86
0.71
0.71
0.84
0.82
0.88
0.91
0.66
0.68
0.84
0.79
6
2.被抢单时间 t 被抢单时间 t 表示客户使用打车软件下单后被司机接单的时间,可在一定程 度上反映打车难易程度。在滴滴快的打车智能出行平台上,基于需要研究的三个
时间段,采集西安的被抢单时间 t,制作表格如下:
火车站 121.23 142.45 219.44 161.04 210.23 231.67 278.93 240.28 198.67 245.92 221.38 221.99
北大街 67.23 107.52 98.23 90.99 72.92 82.98 187.23 114.38 63.95 145.23 98.25 102.48
小寨 62.19 78.31 103.20 81.23 136.25 178.27 162.73 159.08 83.82 103.27 121.93 103.01
西安交大 子午大道
47.21
43.98
82.34
64.53
102.34 65.92
77.30
58.14
121.94 67.74
167.42 93.03
智能RGV的动态调度策略

智能 RGV 的动态调度策略摘要:针对智能 RGV 系统一道工序的物料加工作业情况,首先,RGV根据距离就近原则选择下一操作的CNC。
在 RGV 对所有 CNC 完成一次上料操作后,不断进行上下料、清洗作业的循环操作。
考虑到物料加工时间,我们选择离 RGV 最近的 CNC 作为下一个上料对象。
模型反复按顺序进行操作,直到时间达到 8 小时。
代入各组数据计算,得到相应的RGV动态调度模型和相应的求解算法。
关键词:RGV动态调度全局搜索工作时间均衡度一、背景介绍一个智能加工系统的示意,由 8 台计算机数控机床、1 辆轨道式自动引导车、1 条 RGV 直线轨道、1 条上料传送带、1 条下料传送带等附属设备组成。
RGV 是一种无人驾驶、能在固定轨道上自由运行的智能车。
它根据指令能自动控制移动方向和距离,并自带一个机械手臂、两只机械手爪和物料清洗槽,能够完成上下料及清洗物料等作业任务。
1.任务复述与情况分析任务复述:对一般问题进行研究,给出 RGV 动态调度模型和相应的求解算法。
情况分析:要求对只加工一道工序的情况进行一般性研究。
以 8 小时内加工出最多物料为目标,我们给出了以下一道工序 RGV 动态调度模型。
考虑到RGV 移动的时间远小于物料加工时间,我们选择离 RGV 最近的 CNC 作为下一个上料对象。
模型中反复按顺序进行以下操作,直到时间达到 8 小时:1.等待直到 RGV 空闲且至少一个 CNC 空闲2.使 RGV 移动到距 RGV 当前位置最近的空闲 CNC 处3.对该 CNC 进行上下料操作,若有熟料则还需进行清洗作业三、问题求解针对于智能加工系统来说每班次工作共存在两种状态:启动阶段和稳定阶段。
启动阶段:即开始有 CNC 处于空闲状态的阶段,当所有 CNC 都有处于加工过程时,这一阶段结束,在这一阶段,RGV 不存在等待和清洗操作,CNC 只有空闲和正在加工中两个状态。
稳定阶段:即所有 CNC 都开始工作后的情况,在这一阶段 CNC 有正在加工中,成熟等待,正在上下料三个状态;RGV 有等待、移动、上下料、清洗作业四种状态。
大学生数学建模竞赛B题优秀论文

关于高等教育学费标准的评价及建议摘要本文通过对近几年来学费变化的研究,综合分析影响学费变化的五个要素,引入了三个变因:学校属性、专业类型、地域差异对学费的影响,对其合理性进行了定量的分析和评价。
首先,我们基于层次分析法建立了模型一。
模型一以五个要素,即教育市场供求关系、全国家庭支付承受力、国家财政及相关社会捐助、个人收益率、教育成本为方案层。
对于教育市场的供求关系我们用灰色预测GM(1,1)模型预测出未来几年的招生人数,用蛛网模型求解稳定的价格点为3225.51 元;对于国家财政及相关社会捐助,我们用回归分析得出其效应关系。
模型一以效率和公平两个标准作为准则层,应用极差归一化思想,构造指标函数,综合建立成对比较矩阵。
我们定义学费合理化指数为目标层,经准则层,得出五个要素对学费合理化指数的组合权重向量。
考虑到成对比较矩阵仍有一定主观因素,我们用熵值取权法修正组合权重向量。
最后,拟合出最佳学费曲线及其波动区间,其中 2007 年的结论值为 3370.75 元。
模型一的突出优点是客观可信,美中不足的是结论为一个平均最优值,没有考虑其他变因的影响,使用的局限性较大。
然后,我们基于学校属性、专业类型、地域差异三个变因对结论的影响建立了模型二。
评价了这三个变因对五个要素的综合影响,修正了五个要素对学费合理化指数的影响,使得结论更趋于合理,应用范围更加广泛。
修正后通过若干数据的检验,得出平均最佳学费约为 3000 元。
基于这两个模型,以及对高校学费现状的了解,我们提出三点主要建议: 1.鼓励高校开拓资金来源渠道,学习国外筹款方式,如发行教育彩票等; 2.建议国家增加助学贷款发放力度,并能够分类别基于不同金额的贷款,并出台一些补贴政策弥补不同地区的差异; 3.大力扶持民办高等院校发展,实现高等教育大众化,这样不仅缓解高等院校招生压力,并且能够促进高校教育健康发展。
本文的特色在于基于翔实丰富的资料,根据五个要素及三个变因的分析,建立了一种合理的高校学费评价体系,其拥有适用性广,稳定性好,灵敏度高等特点,对三个变因,即学校属性、专业类型、地域差异进行了深入定量的分析,并根据模型结论给提出了我们的一些可行性建议。
全国大学生数学建模竞赛B题优秀论文
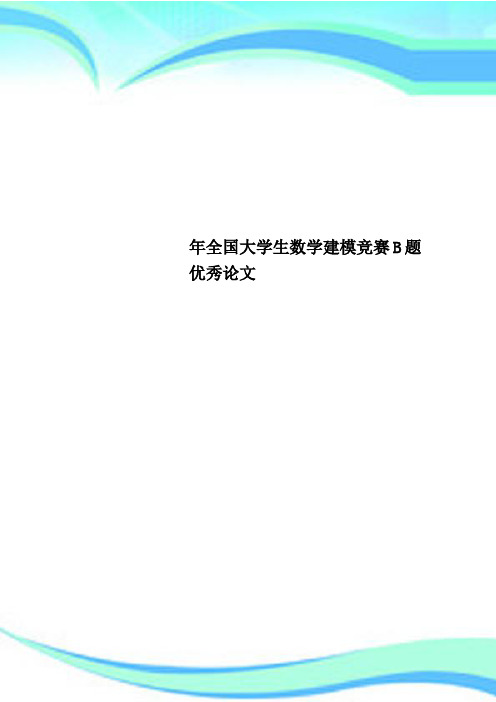
(1) 表示客流量随时间的变化值,R、RW、RG分别表示上海国际旅游入境人数本底值、外国游客入境人数本底值、港澳台游客入境人数本底值;
(2)R1表示2010年1、2、3、4、11、12月上海国际旅游入境实际人数,R2表示世博会期间上海国际旅游入境实际人数,RZ表示2010年上海国际旅游总入境实际人数;
最后,通过对模型结果的分析,量化评估上海世博会的影响力。从世博会对以上各个指标的贡献率可以看出:世博会极大地促进了旅游业的发展,并且对上海的财政收入做出了巨大的贡献。在分析所得结果的基础上,客观评价此模型,并指出其优点和缺点。
关键词:上海 世博会 影响力 本底趋势线 内插值
1.问题重述
2010年上海世博会是首次在中国举办的世界博览会。从1851年伦敦的“万国工业博览会”开始,世博会正日益成为各国人民交流历史文化、展示科技成果、体现合作精神、展望未来发展等的重要舞台。请你们选择感兴趣的某个侧面,建立数学模型,利用互联网数据,定量评估2010年上海世博会的影响力。
2.模型的假设与符号说明
2.1模型的假设
2010年上海世博会作为一场世界级的盛宴,要对其影响力进行定量评估,尚存在一些不确定因素。故为了研究方便,我们给出以下假设:
(1)假设世博会不受偶然事件严重冲击和干扰;
(2)假设旅游人数只受主要因素影响,其他一些因素可以忽略,比如天气等因素;
(3)假设世博会期间每月游览总人数波动不大,非世博会期间每月游览总人数波动也不大。
第二步,用Excel的指数模型、乘幂模型和SPSS的指数-三角函数复合模型 、直线-逻辑线增长复合模型 、直线-三角函数复合模型 对各个指标进行拟合,确定有关参数,获得各个指标的趋势线模型和方程,并计算各年的本底值;
《2024年2016年全国大学生数学建模竞赛B题解题分析与总结》范文
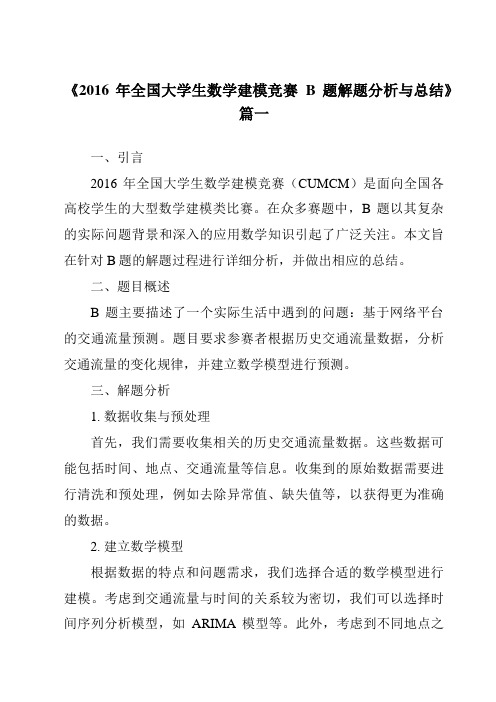
《2016年全国大学生数学建模竞赛B题解题分析与总结》篇一一、引言2016年全国大学生数学建模竞赛(CUMCM)是面向全国各高校学生的大型数学建模类比赛。
在众多赛题中,B题以其复杂的实际问题背景和深入的应用数学知识引起了广泛关注。
本文旨在针对B题的解题过程进行详细分析,并做出相应的总结。
二、题目概述B题主要描述了一个实际生活中遇到的问题:基于网络平台的交通流量预测。
题目要求参赛者根据历史交通流量数据,分析交通流量的变化规律,并建立数学模型进行预测。
三、解题分析1. 数据收集与预处理首先,我们需要收集相关的历史交通流量数据。
这些数据可能包括时间、地点、交通流量等信息。
收集到的原始数据需要进行清洗和预处理,例如去除异常值、缺失值等,以获得更为准确的数据。
2. 建立数学模型根据数据的特点和问题需求,我们选择合适的数学模型进行建模。
考虑到交通流量与时间的关系较为密切,我们可以选择时间序列分析模型,如ARIMA模型等。
此外,考虑到不同地点之间的交通流量可能存在相互影响,我们还可以引入空间相关性分析,如空间自回归模型等。
3. 模型优化与验证建立数学模型后,我们需要对模型进行优化和验证。
这包括调整模型的参数、对模型进行诊断分析等。
我们可以通过对比模型的预测值与实际值,计算误差指标(如均方误差、平均绝对误差等)来评估模型的性能。
同时,我们还可以使用交叉验证等方法来验证模型的稳定性。
4. 模型应用与结果展示最后,我们将建立的数学模型应用于实际问题中,对未来的交通流量进行预测。
我们将预测结果以图表等形式进行展示,方便评委和观众理解。
同时,我们还可以对结果进行解释和讨论,说明模型的优点和局限性。
四、总结通过本文总结:经过详细的分析与探讨,针对2016年全国大学生数学建模竞赛B题,我们采取了有效的解决策略。
从数据收集与预处理到模型建立与优化,每一步都紧密联系实际,充分考虑了交通流量数据的特性和问题需求。
在建模过程中,我们选择了合适的时间序列分析模型和空间相关性分析模型,旨在捕捉交通流量的变化规律。
2018数学建模国赛B题
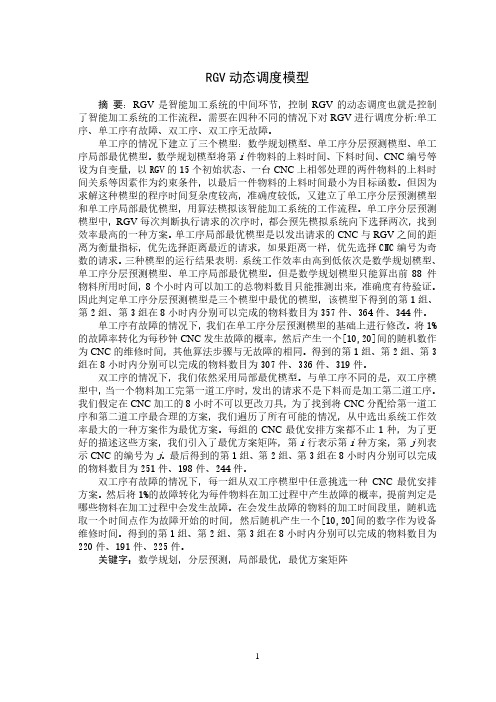
RGV动态调度模型摘要:RGV是智能加工系统的中间环节,控制RGV的动态调度也就是控制了智能加工系统的工作流程。
需要在四种不同的情况下对RGV进行调度分析:单工序、单工序有故障、双工序、双工序无故障。
单工序的情况下建立了三个模型:数学规划模型、单工序分层预测模型、单工序局部最优模型。
数学规划模型将第i件物料的上料时间、下料时间、CNC编号等设为自变量,以RGV的15个初始状态、一台CNC上相邻处理的两件物料的上料时间关系等因素作为约束条件,以最后一件物料的上料时间最小为目标函数。
但因为求解这种模型的程序时间复杂度较高,准确度较低,又建立了单工序分层预测模型和单工序局部最优模型,用算法模拟该智能加工系统的工作流程。
单工序分层预测模型中,RGV每次判断执行请求的次序时,都会预先模拟系统向下选择两次,找到效率最高的一种方案。
单工序局部最优模型是以发出请求的CNC与RGV之间的距离为衡量指标,优先选择距离最近的请求,如果距离一样,优先选择CNC编号为奇数的请求。
三种模型的运行结果表明:系统工作效率由高到低依次是数学规划模型、单工序分层预测模型、单工序局部最优模型。
但是数学规划模型只能算出前88件物料所用时间,8个小时内可以加工的总物料数目只能推测出来,准确度有待验证。
因此判定单工序分层预测模型是三个模型中最优的模型,该模型下得到的第1组、第2组、第3组在8小时内分别可以完成的物料数目为357件、364件、344件。
单工序有故障的情况下,我们在单工序分层预测模型的基础上进行修改。
将1%的故障率转化为每秒钟CNC发生故障的概率,然后产生一个[10,20]间的随机数作为CNC的维修时间,其他算法步骤与无故障的相同。
得到的第1组、第2组、第3组在8小时内分别可以完成的物料数目为307件、336件、319件。
双工序的情况下,我们依然采用局部最优模型。
与单工序不同的是,双工序模型中,当一个物料加工完第一道工序时,发出的请求不是下料而是加工第二道工序。
全国大学生数学建模竞赛赛题综合评析
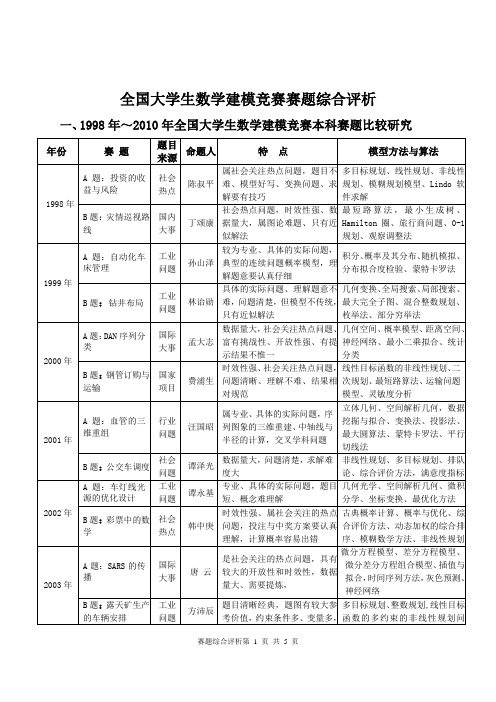
社会热点
叶其孝、周义仓
开放性强、社会关注性强,突出数据来源的可靠性、结论解释的合理性
数据收集与处理、问题的分析与假设,初等数学方法、一般统计方法、多目标规划、回归分析、综合评价方法、灰色预测
2009年
A题:制动器试验台的控制方法分析
工业问题
方沛辰、刘笑羽
问题具体、专业性强,要花时间读懂、理解清楚问题
出版社的资源配置
孟大志
艾滋病疗法的评价及疗效的预测
边馥萍
易拉罐形状和尺寸的最优设计(C题)
叶其孝
煤矿瓦斯和煤尘的监测与控制(D题)
韩中庚
2007年
中国人口增长预测
唐云
乘公交,看奥运
方沛辰、吴孟达
手机“套餐”优惠几何(C题)
韩中庚
体能测试时间安排(D题)
刘雨林
2008年
数码相机定位
谭永基
高等教育学费标准探讨
叶其孝、周义仓
地面搜索(C题)
肖华勇
NBA赛程的分析与评价(D题)
姜启源
2009年
制动器试验台的控制方法分析
方沛辰、刘笑羽
眼科病床的合理安排
吴孟达、毛紫阳
卫星和飞船的跟踪测控(C题)
周义仓
会议筹备(D题)
王宏健
2010年
储油罐的变位识别与罐容表标定
韩中庚
2010年上海世博会影响力的定量评估
杨力平
输油管的布置(C题)
1
6
8
付鹂
重庆大学
1
6
9
姜启源
清华大学
4
3
10
陈叔平
浙江大学、贵州大学
2
5
11
- 1、下载文档前请自行甄别文档内容的完整性,平台不提供额外的编辑、内容补充、找答案等附加服务。
- 2、"仅部分预览"的文档,不可在线预览部分如存在完整性等问题,可反馈申请退款(可完整预览的文档不适用该条件!)。
- 3、如文档侵犯您的权益,请联系客服反馈,我们会尽快为您处理(人工客服工作时间:9:00-18:30)。
1. 问题的重述
现有一个智能加工系统,由 8 台 CNC、1 辆 RGV 以及其他附属设备组成。
RGV 能够根据指令与决策,在水平的轨道上自动控制移动的方向和距离,并通
过机械手爪、机械臂等部件完成“上下料”、“清洗作业”等诸多过程。
对于以下三种情况:
①加工过程包含 1 道工序且每台 CNC 都可以进行加工;
请你们团队完成下列两项任务:
任务 1:对一般问题进行研究,给出 RGV 动态调度模型和相应的求解算法;
任务 2:利用表 1 中系统作业参数的 3 组数据分别检验模型的实用性和算法的有效性,给出 RGV
的调度策略和系统的作业效率,并将具体的结果分别填入附件 2 的 EXCEL 表中。
表 1:智能加工系统作业参数的 3 组数据表
378
500
182
RGV 为 CNC1#,3#,5#,7#一次上下料所需时间
28
30
27
RGV 为 CNC2#,4#,6#,8#一次上下料所需时间
31
35
32
RGV 完成一个物料的清洗作业所需时间
25
30
25
系统作业参数
注:每班次连续作业 8 小时。
附件 1:智能加工系统的组成与作业流程
附件 2:模型验证结果的 EXCEL 表(完整电子表作为附件放在支撑材料中提交)
工完成;
(2)两道工序的物料加工作业情况,每个物料的第一和第二道工序分别由两台不同的 CNC 依
次加工完成;
(3)CNC 在加工过程中可能发生故障(据统计:故障的发生概率约为 1%)的情况,每次故障
排除(人工处理,未完成的物料报废)时间介于 10~20 分钟之间,故障排除后即刻加入作业序列。
要求分别考虑一道工序和两道工序的物料加工作业情况。
从被放入 CNC 开始,直至被取出 CNC,所经历的时间至少为加工时间0 与“上
()
统可加工完成的物料数量级为 102,所以准备 103 个生料一定足够。因此,参数
取值范围可以取为 = 1, 2, …, 1000.
相对应地,将尚为生料的 被 RGV 放入号机床(“上料”过程完成)的时
刻,记为 ;将已加工为熟料的 被 RGV 取出号机床(“下料”过程完成)
优。此外,第一组数据和第三组数据的作业效率一样高,均为 30.125 件/h.
针对情况三:同时考虑单工序流程与双工序流程。构造了随机变量“是否故
障”、“故障发生时间”和“故障排除时间”,并将它们融合进入规划模型。求解
结果显示,遭遇故障后,单工序流程系统效率最多下降了 2.25 件/h,而双工序流
程系统效率最多下降了 1.875 件/h.
“FIFO
原则”和“HRRN 原则”更优,最终加工出 212 件物料;第三组数据的各台 CNC
最优工序分配为 1-1-2-1-2-1-1-2,
“就近原则”最优,最终加工出 241 件物料。此
外,所有的调度方案均呈现有规律的循环状态。
然后,利用“基于蒙特卡洛的学习算法”,在构造正反馈的前提下“随机”
地尝试以获得更优解。结果反映了,三种原则中的最优原则,已非常接近全局最
8. 考虑到机床安放的位置关系——偶数号码机床位于系统左侧,奇数号码机床
位于系统右侧——则 RGV 从机床移动到机床的时间为:
+ 1
+ 1
⎧ 0,
��
�−�
�� = 0
�
2
2
�
�
+�
�−�
�� = 1
� 1
2
2
=
⎨
+ 1
+ 1
于某个物料的加工,是否发生故障,故障发生的时间,以及故障排除时间这三个
随机变量。
本文拟构建一般性的规划,理清系统内部的机理关系。然后,通过提出不同
的原则,编写算法,解决该规划问题;并通过“基于蒙特卡洛的学习算法”,比
较、检验不同原则的优劣。
3. 模型的假设与符号的说明
3.1 模型的假设
(1)生料的供应是无限的。
符号的说明
符号
说明
单位
RGV 移动个单位所需时间
秒
RGV 从机床移动到机床的时间
秒
号机床所加工的第 个物料
件
0
物料加工时间
秒
1
物料清洗时间
秒
2
()
第台机床“上下料”时间
秒
生料 “上料”完成时刻
秒
2018 年高教社杯全国大学生数学建模竞赛题目
(请先阅读“全国大学生数学建模竞赛论文格式规范”
)
问题 B
智能 RGV 的动态调度策略
图 1 是一个智能加工系统的示意图,由 8 台计算机数控机床(Computer Number Controller,CNC)、
1 辆轨道式自动引导车(Rail Guide Vehicle,RGV)、1 条 RGV 直线轨道、1 条上料传送带、1 条下
过程。
此外,双工序流程中各台 CNC 所负责的工序也是不确定的;因此,本文对
256 种工序布局方案,结合三种选取原则,进行了遍历。得到的结果是:第一组
数据的各台 CNC 最优工序分配为 1-2-1-2-1-2-1-2,三种原则结果一致,最终加工
出 253 件物料;第二组数据的各台 CNC 最优工序分配为 2-1-2-1-2-1-2-1,
基于多原则比较和蒙特卡洛模拟的 RGV 动态调度模型
摘要
本文从规划模型、多原则求解的角度,综合了蒙特卡洛模拟与机器学习的思
想,研究了由 8 台 CNC、1 辆 RGV 以及其他附属设备组成的智能加工系统的动
态调度问题,并给出了不同工序情况下的具体调度方案。
针对情况一:单工序的作业流程较为简单。首先,利用规划的各个约束条件,
(2)两个步骤,周而复始,直至 8 个小时
结束。
4.1.2 单工序的调度模型
考虑到模型的一般化问题,此处本文拟利用规划的方法,寻找并构建各台
CNC 以及生产物料的数量关系。
1. RGV 在 CNC 之间运动时间的刻画
不妨设,现有任意两台 CNC,分别记作,,其中 = 1, 2, …, 8; = 1, 2, …,
这样的规划是一个 NP 问题,无法通过传统的方法求解,所以进而寻求模拟的方
法求得局部最优解。
本文选取了“就近原则”——构造时间代价函数,
“FIFO 原则”——考虑各
台 CNC 的等待时间,以及“HRRN 原则”——将时间代价与等待时间进行综合
考虑,分别对情况一进行了模拟。事实上,每种原则的结果相同:第一组数据加
2
(2)不考虑 RGV 转向的时间,即 RGV 从 CNC1#到 CNC2#,从 CNC3#到
CNC4#,从 CNC5#到 CNC6#,从 CNC7#到 CNC8#的时间全部为 0.
(3)上料传送带可以及时将生料运往需要的 CNC 正前方,下料传送带可以
及时将成料运出整个系统。
3.2 符号的说明
表 1
的时刻,记为 .
此外,物料加工时间记为0 ,清洗时间记为1 ,第台机床“上下料”时间记
()
为2 .
()
2
⎧(1)
�2 ,
=
⎨ (2)
�2 ,
⎩
mod( ) ≠ 0
2
.
mod( ) = 0
2
(1)
(2)
其中,2 为 RGV 为 CNC1#,3#,5#,7#进行一次上下料所需时间,2 为
生料经过 CNC 的加工成为熟料,而熟料经过 RGV 的清洗成为成料。从 RGV 的
作业过程来看,RGV 首先需要选取一台候选 CNC,然后移动至该 CNC,放入生
料,取出熟料,再将熟料进行清洗使之变为成料(包括送出系统)——最终 RGV
将进入下一轮选择 CNC 的阶段。
生料
熟料
图 1
成料
情况(1)物料的形态演化
本文的亮点在于:首先,利用一般化的公式对系统调度进行了较为细致的机
理分析,使得模型具有普适性;其次,给出了多个调度原则相互比较,从而有利
于结果更优;最后,将蒙特卡洛模拟与机器学习的思想相结合,对上述调度原则
的有效性进行验证,增强了模型的说服力。
关键词
规划模型;多原则比较;蒙特卡洛模拟;机器学习;动态调度
�2 ,
��
�−�
�� = 2
�
2
2
�
�
+ 1
+ 1
�3 ,
��
�−�
�� = 3
⎩
2
2
其中, 为 RGV 移动个单位所需时间。
2. 基于单个物料加工过程的刻画
Step 1.
将号机床所加工的第 个物料记为 . 经过粗略的计算,在 8 小时内该系
刻画了 RGV 在 CNC 之间的运动过程、单个物料的加工过程、
“上下料”时 RGV
手爪的旋转过程、清洗作业的过程、RGV 移动至下一个机床进行加工的过程等
等。此外,还刻画了物料加工与运送的“唯一性”,以及利用 0-1 变量构造的目
标函数。规划的目的是,在给定的时间内,使得加工出的物料数量最多。然而,
RGV 为 CNC2#,4#,6#,8#进行一次上下料所需时间。
4
Step 2.
基于上述符号的定义,可以得到:
()
− ≥ 0 + 2 ,
�
= 0,
≤ 8 × 60 × 60 − 1
其他
(1)
(1)式的意义为,若物料 加工完成时间在 8 小时终止以前,那么物料
(1)上下料:将熟料取出 CNC,并向 CNC 放入新的生料,这两步同时完