柴油加氢
柴油加氢装置的原理

柴油加氢装置的原理
柴油加氢装置是一种利用催化剂催化反应的装置,用于将柴油中的硫、氮和其他杂质还原为较为纯净的烷烃化合物。
该装置主要由催化剂床、加氢循环系统、加氢炉和分离装置等组成。
柴油加氢装置的主要原理是通过将柴油引入加氢炉中,在高温和高压的条件下与氢气一起进入催化剂床。
催化剂床中的催化剂会催化柴油分子中的硫化物、氮化物和其他杂质与氢气发生反应,将其转化为气体。
而催化剂床中的气体会与床外的循环氢气混合后再次进入催化剂床,形成加氢循环。
在催化剂床中,硫化物会被催化剂吸附并转化为硫化氢
(H2S),氮化物会被还原为氨(NH3),氧化物则会被还原为水蒸气(H2O)。
同时,催化剂会催化柴油中的不饱和化合物和芳香化合物转化为饱和烷烃化合物,提高柴油的燃烧性能和稳定性。
经过催化反应后的气体会进入分离装置,通过冷凝、吸附和脱水等工艺,将其中的硫化氢、氨和水蒸气等杂质分离出来,以获得处理后的柴油。
分离后的杂质则经过进一步的处理或回收利用,从而实现对柴油中杂质的有效去除。
柴油加氢装置的主要目的是降低柴油中硫、氮等杂质的含量,以满足环保要求和提高柴油燃烧效率。
它不仅可以提高柴油的质量,还可以减少柴油的污染排放,对保护环境和人体健康具有重要意义。
加氢柴油 氢含量

加氢柴油氢含量
加氢柴油是一种通过加氢处理工艺得到的柴油。
在这个过程中,氢气与柴油中的杂质和不饱和烃发生反应,从而改善柴油的质量。
关于加氢柴油中的氢含量,具体数值可能会因不同的生产工艺和产品标准而有所差异。
一般来说,加氢柴油中的氢含量相对较高,这是因为加氢过程中氢气的加入使得柴油的分子结构发生了改变,提高了柴油的燃烧性能和环保性能。
较高的氢含量可以带来一些好处。
首先,氢含量的增加有助于提高柴油的燃烧效率,减少碳排放和污染物的生成,对环境更加友好。
其次,氢的存在可以改善柴油的稳定性和抗氧化性,延长柴油的使用寿命。
然而,需要注意的是,氢含量并不是衡量加氢柴油质量的唯一标准。
其他因素,如硫含量、十六烷值、芳烃含量等,也会对柴油的性能产生重要影响。
此外,加氢柴油的质量还与加氢工艺的条件、原料的选择以及生产厂家的技术水平等有关。
在实际应用中,选择合适的加氢柴油需要综合考虑多个因素,以满足发动机的要求和环保标准。
对于具体的氢含量,建议参考相关的产品规格和检测报告,以获取更准确的信息。
柴油加氢技术总结_锅炉技术总结范文

柴油加氢技术总结_锅炉技术总结范文柴油加氢技术是一种新型的能源利用技术,能够有效地降低柴油对环境的污染程度,提高燃料利用效率,具有广泛的应用前景。
经过多年技术研究和实践,目前柴油加氢技术已成熟,以下是柴油加氢技术的总结:一、柴油加氢技术概述柴油加氢技术是一种利用氢气将柴油分子中的碳氢键断裂,再与氢原子结合生成新的高氢化合物的过程。
该技术能够改善柴油的性能和组成,提高柴油的热值和燃烧效率,降低柴油的凝固点和燃烧产物中的污染物含量。
柴油加氢技术是一种改变柴油分子结构的过程,其原理是通过加氢反应将长链烃分子裂解成更短的链烃分子,降低分子量,增加分子中的氢原子含量,使其更易于燃烧。
1.改善燃油性能2.提高燃料利用效率通过柴油加氢技术,可以降低柴油的凝固点,增加柴油的可流动性,使柴油更易于燃烧,从而提高燃料利用效率。
3.降低柴油对环境的污染柴油加氢技术能够降低柴油对环境的污染程度,使其燃烧产生的污染物含量更少,具有更好的环保性能。
目前,柴油加氢技术已经得到了广泛应用。
在燃油加氢方面,一般采用常压或低压加氢工艺,通常使用的反应器有固定床反应器和流化床反应器等。
五、柴油加氢技术的优势和不足1.柴油加氢技术的优势主要体现在其能够有效地降低燃料的污染程度,提高燃料利用效率,同时也可以降低柴油的凝固点。
2.柴油加氢技术的不足主要在于其投资成本较高,而且加氢反应条件要求严格,操作难度较大。
未来柴油加氢技术的发展趋势主要包括以下几个方面:1.技术研究不断深入随着柴油加氢技术的应用越来越广泛,未来将有更多的研究机构和企业投入到该领域的技术研究中,是技术不断深入发展。
2.技术应用更加广泛未来柴油加氢技术将会在更多的领域得到应用,并且在不断发展的新能源领域中,具有较大的发展前景。
3.推广普及加氢技术未来柴油加氢技术将会得到更多的推广和普及,更多的汽车需求将使用加氢技术的柴油燃料,从而提高柴油燃油的效率和环保性能。
综上所述,柴油加氢技术是一种具有较大发展前景的新兴能源技术,尤其对于环保和低碳经济有着十分重要的作用,未来该技术将会得到更广泛的应用和推广。
柴油加氢工艺流程
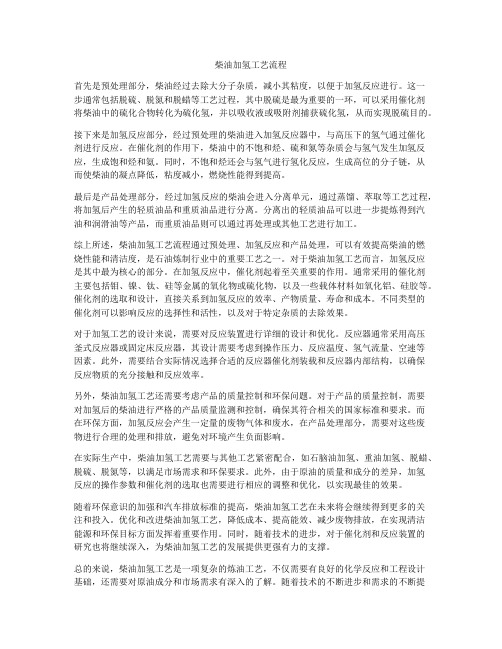
柴油加氢工艺流程首先是预处理部分,柴油经过去除大分子杂质,减小其粘度,以便于加氢反应进行。
这一步通常包括脱硫、脱氮和脱蜡等工艺过程,其中脱硫是最为重要的一环,可以采用催化剂将柴油中的硫化合物转化为硫化氢,并以吸收液或吸附剂捕获硫化氢,从而实现脱硫目的。
接下来是加氢反应部分,经过预处理的柴油进入加氢反应器中,与高压下的氢气通过催化剂进行反应。
在催化剂的作用下,柴油中的不饱和烃、硫和氮等杂质会与氢气发生加氢反应,生成饱和烃和氨。
同时,不饱和烃还会与氢气进行氢化反应,生成高位的分子链,从而使柴油的凝点降低,粘度减小,燃烧性能得到提高。
最后是产品处理部分,经过加氢反应的柴油会进入分离单元,通过蒸馏、萃取等工艺过程,将加氢后产生的轻质油品和重质油品进行分离。
分离出的轻质油品可以进一步提炼得到汽油和润滑油等产品,而重质油品则可以通过再处理或其他工艺进行加工。
综上所述,柴油加氢工艺流程通过预处理、加氢反应和产品处理,可以有效提高柴油的燃烧性能和清洁度,是石油炼制行业中的重要工艺之一。
对于柴油加氢工艺而言,加氢反应是其中最为核心的部分。
在加氢反应中,催化剂起着至关重要的作用。
通常采用的催化剂主要包括钼、镍、钛、硅等金属的氧化物或硫化物,以及一些载体材料如氧化铝、硅胶等。
催化剂的选取和设计,直接关系到加氢反应的效率、产物质量、寿命和成本。
不同类型的催化剂可以影响反应的选择性和活性,以及对于特定杂质的去除效果。
对于加氢工艺的设计来说,需要对反应装置进行详细的设计和优化。
反应器通常采用高压釜式反应器或固定床反应器,其设计需要考虑到操作压力、反应温度、氢气流量、空速等因素。
此外,需要结合实际情况选择合适的反应器催化剂装载和反应器内部结构,以确保反应物质的充分接触和反应效率。
另外,柴油加氢工艺还需要考虑产品的质量控制和环保问题。
对于产品的质量控制,需要对加氢后的柴油进行严格的产品质量监测和控制,确保其符合相关的国家标准和要求。
柴油加氢流程
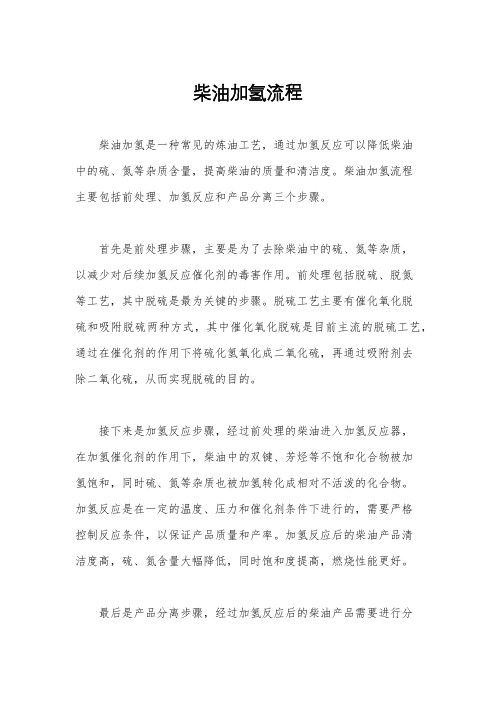
柴油加氢流程
柴油加氢是一种常见的炼油工艺,通过加氢反应可以降低柴油
中的硫、氮等杂质含量,提高柴油的质量和清洁度。
柴油加氢流程
主要包括前处理、加氢反应和产品分离三个步骤。
首先是前处理步骤,主要是为了去除柴油中的硫、氮等杂质,
以减少对后续加氢反应催化剂的毒害作用。
前处理包括脱硫、脱氮
等工艺,其中脱硫是最为关键的步骤。
脱硫工艺主要有催化氧化脱
硫和吸附脱硫两种方式,其中催化氧化脱硫是目前主流的脱硫工艺,通过在催化剂的作用下将硫化氢氧化成二氧化硫,再通过吸附剂去
除二氧化硫,从而实现脱硫的目的。
接下来是加氢反应步骤,经过前处理的柴油进入加氢反应器,
在加氢催化剂的作用下,柴油中的双键、芳烃等不饱和化合物被加
氢饱和,同时硫、氮等杂质也被加氢转化成相对不活泼的化合物。
加氢反应是在一定的温度、压力和催化剂条件下进行的,需要严格
控制反应条件,以保证产品质量和产率。
加氢反应后的柴油产品清
洁度高,硫、氮含量大幅降低,同时饱和度提高,燃烧性能更好。
最后是产品分离步骤,经过加氢反应后的柴油产品需要进行分
离和精制,以得到符合要求的成品柴油。
产品分离主要包括闪蒸、精馏、萃取等工艺,通过这些工艺可以分离出不同馏分的柴油,并对柴油进行精制,去除残留的杂质和重质组分,最终得到高品质的成品柴油。
总的来说,柴油加氢流程是一个复杂的工艺过程,需要多种工艺步骤的配合和严格的操作控制,才能实现对柴油的清洁化和提质改良。
随着环保要求的提高和市场对清洁能源的需求增加,柴油加氢技术将会得到更广泛的应用和发展,为炼油行业的可持续发展提供更多可能性。
柴油加氢工艺及催化剂
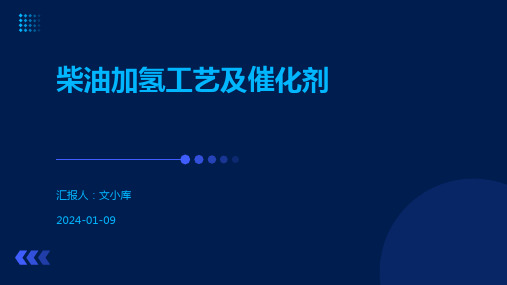
再生
催化剂在加氢反应过程中会发生失活,研究有效的再生 方法,如化学再生、热再生等,以恢复催化剂的活性, 延长其使用寿命。
回收利用
催化剂经再生后仍可继续使用,应研究催化剂的回收利 用技术,实现资源的循环利用,降低生产成本并减少环 境污染。
THANKS
谢谢您的观看
它通过在高温高压条件下,利用氢气与柴油中的硫、氮等杂质以及烃类化合物的 反应,将其转化为硫化氢、氨气和水蒸气等气体,从而脱除杂质并改善柴油的燃 烧性能。
柴油加氢工艺的原理
柴油加氢的基本原理是加氢反应,即将氢气与柴油中的硫、 氮等杂质以及烃类化合物进行反应,生成硫化氢、氨气和水 蒸气等气体,同时将烃类化合物中的不饱和烃转化为饱和烃 ,提高油品的稳定性。
探索新型制备方法
要点一
传统制备方法
采用沉淀法、溶胶-凝胶法、微乳液法等传统方法制备柴油 加氢催化剂,这些方法虽然成熟,但存在成本高、周期长 等缺点。
要点二
新型制备方法
研究新型的制备方法,如模板法、自组装法、离子液体法 等,以简化制备过程、降低成本、提高催化剂性能和缩短 研发周期。
加强催化剂的再生与回收利用
VS
浸渍法是一种常用的催化剂制备方法 ,通过将载体浸入含有活性组分的溶 液中,再经洗涤、干燥和煅烧等后处 理,得到催化剂。该方法操作简便, 适用于制备高分散度的催化剂。浸渍 法的优点是活性组分在载体上分布均 匀,有利于提高催化剂的活性。
溶胶-凝胶法
一种新型的催化剂制备方法
溶胶-凝胶法是一种新型的催化剂制备方法,通过将金 属盐溶液与沉淀剂反应,生成凝胶态的溶胶,再经干 燥和煅烧等后处理,得到催化剂。该方法具有操作简 便、成本低廉等优点,适用于制备高纯度、高分散度 的催化剂。溶胶-凝胶法的优点是活性组分在载体上分 布均匀,有利于提高催化剂的活性。
柴油加氢工作总结
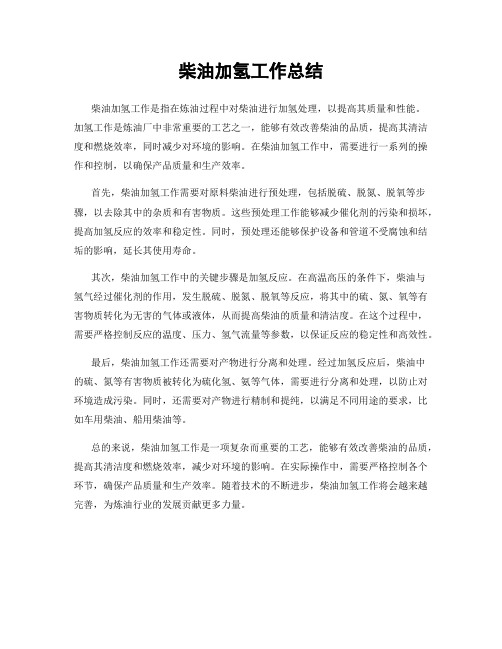
柴油加氢工作总结
柴油加氢工作是指在炼油过程中对柴油进行加氢处理,以提高其质量和性能。
加氢工作是炼油厂中非常重要的工艺之一,能够有效改善柴油的品质,提高其清洁度和燃烧效率,同时减少对环境的影响。
在柴油加氢工作中,需要进行一系列的操作和控制,以确保产品质量和生产效率。
首先,柴油加氢工作需要对原料柴油进行预处理,包括脱硫、脱氮、脱氧等步骤,以去除其中的杂质和有害物质。
这些预处理工作能够减少催化剂的污染和损坏,提高加氢反应的效率和稳定性。
同时,预处理还能够保护设备和管道不受腐蚀和结垢的影响,延长其使用寿命。
其次,柴油加氢工作中的关键步骤是加氢反应。
在高温高压的条件下,柴油与
氢气经过催化剂的作用,发生脱硫、脱氮、脱氧等反应,将其中的硫、氮、氧等有害物质转化为无害的气体或液体,从而提高柴油的质量和清洁度。
在这个过程中,需要严格控制反应的温度、压力、氢气流量等参数,以保证反应的稳定性和高效性。
最后,柴油加氢工作还需要对产物进行分离和处理。
经过加氢反应后,柴油中
的硫、氮等有害物质被转化为硫化氢、氨等气体,需要进行分离和处理,以防止对环境造成污染。
同时,还需要对产物进行精制和提纯,以满足不同用途的要求,比如车用柴油、船用柴油等。
总的来说,柴油加氢工作是一项复杂而重要的工艺,能够有效改善柴油的品质,提高其清洁度和燃烧效率,减少对环境的影响。
在实际操作中,需要严格控制各个环节,确保产品质量和生产效率。
随着技术的不断进步,柴油加氢工作将会越来越完善,为炼油行业的发展贡献更多力量。
柴油加氢
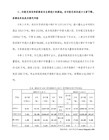
空速是指单位时间通过单位催化剂的原料量,他反应了装置的处理能力。空速达意味着单位时间通过催化剂的原料量多,原料在催化剂上停留的时间短,反应深度相应较低,因此无论是从反应速率还是反应平衡方面分析,降低空速对提高反应深度都是有利的。随着空速的增加,生成油中的硫含量成对数增加,即空速对反应深度的影响是很大的。但较低的空速意味着相同的催化剂装置的处理能力比较低,即相同的处理量下,所需要的催化剂较多,较大的反应器容积,装置的建设投资费用比较大。因此,柴油加氢装置要选择合适的空速,要根据装置投资、催化剂的活性、原料性质和产品的质量要求等多个因素进行考虑。
直馏柴油中非噻吩硫的含量很高,占硫含量的1/3;裂化馏分中非噻吩硫的含量很少,占硫含量的2%。
裂化馏分中的硫化物基本上都是杂环硫化物。
从柴油中脱除二苯并噻吩的烷基二苯并噻吩通常可以通过两种途径来完成,一是芳烃的不加氢的直接加氢脱硫;二是脱硫前的芳环加氢饱和。不同硫化物的结构,其经过不同途径的比利是不相同的。
在柴油深度加氢脱硫时,原料油性质对产品油中硫含量有着决定性的作用。原料油的反应性能取决于原料油中反应活性差和反应活性高的硫化物的相对含量,这些硫化物的含量又决定于原料油的种类、催化柴油和焦化柴油的掺入量以及柴油馏分的切割点。原料油中重组分含量和催化及焦化柴油的掺入量,对超深度脱硫的操作条件有重大的影响。对于柴油的超深度脱硫,具有位阻效应的芳香族化合物对反应性能的影响很大。原料油中的大分子碱性氮化物对生产超低硫柴油也是一个关键因素,像有些大分子的碱氮化合物会合硫化物争夺活性中心。传统的加氢脱硫生产含硫350PPm的柴油是直接脱硫或氢解(C-N键断裂),所有的反应活性较高的硫化物和无取代基的二苯并噻吩都被脱出,但要生产含硫为10PPm或50PPM以下的柴油,反应活性差, 分子较大、又两个取代基的二苯并噻吩(如4,6-二甲基二苯并噻吩)也必须脱除,这些硫化物的含量随着原料油的沸点生高和裂化组分的掺入量增加而增加,脱除这些硫化物必须先加氢饱和一个芳环,然后才能使C-S键断开。
- 1、下载文档前请自行甄别文档内容的完整性,平台不提供额外的编辑、内容补充、找答案等附加服务。
- 2、"仅部分预览"的文档,不可在线预览部分如存在完整性等问题,可反馈申请退款(可完整预览的文档不适用该条件!)。
- 3、如文档侵犯您的权益,请联系客服反馈,我们会尽快为您处理(人工客服工作时间:9:00-18:30)。
第一章绪论生产低硫、低芳烃、低密度、高十六烷值的清洁柴油是今后世界范围内的柴油生产的总趋势,如何满足符合日趋苛刻的车用柴油标准,生产出符合环保要求的清洁柴油将成为炼油技术进步的一个重要课题。
欧洲和世界清洁柴油规范发展趋势见表1、表2。
柴油燃料质量升级的趋势与汽油类似,最主要的是对于硫含量的控制,同时对于柴油产品指标中的十六烷值(或十六烷指数)、芳烃含量、冷流动性能、90 或95 馏出温度( T90或T95)、密度等也都提出了更为严格的要求。
而二次加工的柴油,比如催化裂化柴油,含有相当多的硫、氮及烯烃类物质,油品质量差,安定性不好,储存过程容易变质,掺炼重油的催化裂化柴油尤其明显。
对直馏柴油而言,由于原油中硫含量升高、环保法规日趋严格,已经不能直接作为产品出厂,也需要经过加氢精制处理。
柴油中含有的硫化物使油品燃烧性能变坏、气缸积碳增加、机械磨损加剧、腐蚀设备和污染大气,在与二烯烃同时存在时,还会生成胶质。
硫醇是氧化引发剂,生成磺酸与金属作用而腐蚀储罐,硫醇也能直接与金属反应生成硫酸盐,进一步促进油品氧化变质。
柴油中的氮化物,如二甲基吡啶及烷基胺类等碱性氮化物,会使油品颜色和安定性变坏,当与硫醇共存时,会促进硫醇氧化和酸性过氧化物的分解,从而使油品颜色和安定性变差;硫醇的氧化物-磺酸与吡咯缩合生成沉淀。
柴油加氢精制的生产原理就是在一定的温度、压力、氢油比、空速条件下,借助加氢精制催化剂的作用,有效的使油品中的硫、氮、氧非烃类化合物转化为相应的烃类和H2S、NH3和H2O。
另外,少量的重金属则截留在催化剂中;同时使烯烃和部分芳烃饱和,从而得到安定性、燃烧性、清洁性都较好的优质柴油产品和重整原料。
第二章工艺流程2.1 反应部分原料油自罐区由泵送入本装置(D-101),经过泵(P-101)送进入柴油反冲洗过滤器(SR101)除去原料油中大于25μm的颗粒,过滤后的原料油进入滤后原料油缓冲罐(D-102),原料油经反应进料泵(P-102)抽出升压进入反应系统。
由外装置来的提纯氢气进入新氢压缩机入口分液罐(D-105),再经新氢压缩机(K-101)升压后,然后分成两路,一路经循环水冷却(E-104)重回分液罐(D-105),另一路与来自循环氢压缩机(K-102)的循环氢混合,再与升压后的原料油混合。
混氢油经混氢油与反应产物换热器换热(E-103、E-101)后进入反应进料加热炉(F-101),加热至反应需要的温度后进入加氢精制反应器(R-101)。
在反应器中,混合原料在催化剂作用下,进行加氢脱硫、脱氮等精制反应。
在催化剂床层间设有控制反应温度的冷氢点。
反应产物经与混氢原料油、低分油换热降温至140℃左右进入高压空冷器(A-101),在空冷器入口注入除盐水,以溶解掉反应过程中所产生的胺盐,防止堵塞管道和空冷器。
反应产物经空冷器冷却到50℃左右进入高压分离器(D-103),进行气、油、水三相分离。
分离出来的气体作为循环氢经循环氢分液罐分液(D-106),循环氢压缩机(k-102)升压返回反应系统;分离出来的油经减压后进入低压分离器(D-104);高压分离器分离出来的含硫含氨污水减压后与低压分离器分离出来的污水一起送至装置外的酸性水汽提装置处理;经分离气体后的低分油与分馏产品及反应产物换热后进入分馏塔。
2.2 分馏部分从低压分离器出来的低分油和柴油产品换热(E-201)后,再与反应产物换热(E-102)后,进入分馏塔。
分馏塔顶气相经分馏塔顶空冷器及水冷(E-202)冷却后进入分馏塔顶回流罐(D-201),气液分离后,酸性气体送出装置;液体一部分作为塔顶回流经分馏塔顶回流泵(P-202)送到分馏塔塔顶;一部分作为石脑油产品送出装置。
分馏塔底柴油经汽提蒸汽汽提后由P-201抽出,P-201抽出柴油与低分油换热(E-201)换热,再与冷水换热,最后经空冷器(A-202)冷却后送出装置。
本装置中大量循环氢的存在能保证气相为连续相,液相为分散相,被气相打散的液相在固定床催化剂上从上至下以液滴的形态流过催化剂床层,从而发生一系列的加氢反应。
循环氢在其中的关键作用是:(1)维持反应所需的氢分压,用来维系气相中的氢气向油相溶解的推动力。
(2)控制催化剂床层的温升。
(3)稀释反应物流杂质的浓度,促进深度脱杂质的反应。
工程计算表明,较少的循环氢就能建立较高的氢分压;但由于循环氢的热容较小,在反应放热量一定的前提下要控制催化剂床层的温升,则需较大流量的循环氢。
连续液相加氢技术通过对反应产物的液相进行循环来降低反应器的温升,并不断补充溶解反应所需的氢气,从而为反应系统取消循环氢系统提供了技术支持。
连续液相加氢技术的总体思路是反应、氢气溶解、反应产物杂质脱除各司其职,优势互补,工艺原理是:(1)少量的过剩氢在反应器出口以气相形态存在,保证了加氢反应所需的氢分压和循环油中的溶解氢始终处于饱和状态。
(2)少量的过剩氢使热高分气流量小,远低于传统滴流床加氢技术的循环氢流量,减小了高压(或低压)气路系统设备、管线的尺寸和能耗。
(3)设置循环油系统解决了控制催化剂床层温升的问题,同时保证了液相为连续相,气相为分散相,使反应器内介质流动稳定。
(4)在必要时循环油经热氢气汽提脱除硫化氢后解决了稀释反应物流杂质的问题。
(5)适量的汽提氢能有效降低循环油携带的H2S与NH3 量,减少补充氢压缩机的能量消耗。
(6)少量的理论塔盘数就可满足汽提分离H2S与NH3 的要求,降低了热高压汽提分离器的投资。
第三章工艺原理及影响因素3.1 加氢精制加氢精制主要反应为加氢脱硫、加氢脱氮、加氢脱氧、烯烃与芳烃的饱和加氢,以及加氢脱金属。
其典型反应如下:3.1.1 加氢脱硫反应(HDS)硫是普遍存在于各种石油中的一种重要杂元素,原油中的硫含量因产地而异,可低至0.1m%,亦可高达2-5m%。
柴油馏分中含硫化合物根据其加氢脱硫难易可以分成两类:一类是链状含硫化合物、噻吩类化合物、含有一个或两个芳环的苯并噻吩类化合物,这类化合物位阻较小,用常规的加氢精制手段很容易脱除其中的硫:主要的化学反应方程式为:二硫化物加氢反应转化为烃和H2S,要经过生成硫醇的中间阶段,即首先S-S键上断开,生成硫醇,再进一步加氢生成烃和硫化氢,中间生成的硫醇也能转化成硫醚。
噻吩与四氢噻吩的加氢反应:噻吩加氢产物中观察到有中间产物丁二烯生成,并且很快加氢成丁烯,继续加氢成丁烷苯并噻吩在50-70大气压和425℃加氢生成乙基苯和硫化氢:对多种有机含硫化物的加氢脱硫反应进行研究表明:硫醇、硫醚、二硫化物的加氢脱硫反应多在比较缓和的条件下容易进行。
这些化合物首先在C-S键,S-S键发生断裂,生成的分子碎片再与氢化合。
另外一类就是含有多个芳环,并且芳环上有取代基的多苯并噻吩类化合物,例如4,6-二甲基二苯并噻吩(4,6-DMDBT)、4,6,8-三甲基二苯并噻吩(4,6,8-TMDBT)等,这类化合物的特点是在硫原子的附近有取代基,位阻较大,硫原子与催化剂活性位接触困难,并且具有很高的沸点(一般大于350℃),这些化合物是超深度脱硫的最大障碍。
图1表明了柴油中硫的复杂性及经过脱硫反应后残留的含硫化合物组成。
图3.1 柴油中硫的复杂性及经过脱硫反应后残留的含硫化合物组成4,6-DMDBT 加氢脱硫反应的可能途径如图3.2。
反应机理研究表明,4,6-DMDBT 是通过直接氢解和加氢两条路径实现的,其中加氢路径的反应速率是氢解路径的十倍以上。
原因是因为位于 4 和 6 位的两个甲基的空间位阻效应,使得硫原子难于接触催化剂活性表面,氢解脱硫路径受到抑制,但若是有一个芳环被加氢则甲基处于环烷环的轴向位置,通过分子的扭曲,甲基的空间位阻效应被削弱,因而使硫原子与催化剂表面的活性位接触,发生脱硫反应。
图3.2 4,6-二甲基二苯噻吩加氢脱硫反应途径在工业反应条件下,大多数脱硫反应从热力学上来讲,是可以进行到底的。
而对于4,6-DMDBT类化合物的超深度脱硫主要反应途径是一个芳环先加氢然后C-S键断裂脱硫,具有“硫层效应”,存在热力学平衡的问题有机硫化物的HDS是放热反应(见表3)。
在工业反应条件(340-425℃,5~17MPa)下,HDS反应基本上是不可逆的,不存在热力学限制,表4列出了一些HDS反应的化学平衡常数[6],其中427℃的lgK均大于0。
只有在比常用工艺条件高得多的温度下,lgK值才小于1。
随着温度升高,平衡常数变小,这与放热反应特性一致,也说明从热力学角度看,较低的温度(和较高的压力)有利于HDS反应。
表3.1 典型硫化物HDS反应的焓变表3.2 一些加氢反应的化学平衡常数3.1.2 加氢脱氮反应(HDN)石油馏分中的含氮化合物可分为三类:(1) 脂肪胺及芳香胺类(2) 吡啶、喹啉类型的碱性杂环化合物(3) 吡咯、咔唑型的非碱性氮化物在各族氮化物当中,脂肪胺类的反应能力最强,芳香胺(烷基苯胺)等较难反应。
无论脂肪族胺或芳香族胺都能以环状氮化物分解的中间产物形态出现。
碱性或非碱性氮化物都是比较不活泼的,特别是多环氮化物更是如此。
这些杂环化合物存在于各种中间馏分,特别是重馏分,以及煤及油母页岩的干馏或抽提产物中。
在石油馏分中,氮化物的含量随馏分本身分子量增大而增加。
在石油馏分中,氮含量很少,一般不超过几个ppm。
在加氢精制过程中,氮化物在氢作用下转化为NH3和烃。
几种含氮化物的氢解反应如下:根据发表的有关加氢脱氮反应的热力学数据,至少对一部分氮化物来说,当温度在300-500℃范围内,需要较高的氢分压才能进行加氢脱氮反应。
从热力学观点来看,吡啶的加氢脱氮比其它氮化物更困难。
为了脱氮完全,一般需要比脱硫通常采用的压力范围更高的压力。
在几种杂原子化合物中,含氮化合物的加氢反应最难进行,或者说它的稳定性最高。
当分子结构相似时,三种杂原子化合物的加氢稳定性依次为:含氮化合物>含氧化合物>含硫化合物例如:焦化柴油加氢时,当脱硫率达到90%的条件处,其脱氮率仅为40%。
3.1.3 烃类的加氢反应在加氢精制条件下,烃类的加氢反应主要是不饱和烃和芳烃的加氢饱和。
这些反应对改善油品的质量和性能具有重要意义。
例如烯烃,特别是二稀烃的加氢可以提高油品的安定性;芳烃加氢可提高柴油的十六烷值。
3.1.3.1 不饱和烃的加氢饱和反应直馏馏分中,一般不含有不饱和烃,但二次加工产品如催化柴油、焦化柴油中,则含有大量的不饱和烃,这些不饱和烃在加氢精制条件下很容易饱和,代表性反应如下:值得注意的是稀烃饱和反应是一个放热反应,对不饱和烃含量较高的原料油(焦化汽、柴油)加氢,要注意控制床层温度,防止超温,加氢反应器一般都设有冷氢盘,可以通过注入冷氢来控制温升。
3.1.3.2 芳烃的加氢饱和反应(HDA)现代分析手段(如高压液相色谱、13C 核磁共振、色质联用以及紫外、红外技术等)的分析结果表明,石油馏分中的芳烃主要有四类:单环芳烃,包括苯和烷基苯、苯基(或苯并)环烷烃;双环芳烃,包括萘和烷基萘、联苯和萘并环烷烃;三环芳烃,如蒽、菲和芴及其烷基化物;多环芳烃,如芘、萤蒽。