气体热扩渗技术的发展现状
表面处理第七讲热扩渗
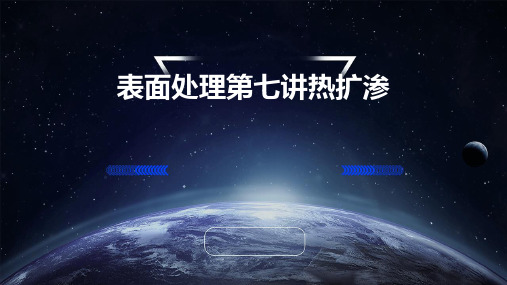
使用注意事项
选择合适的材料和工艺参数
在使用热扩渗技术时,需要根据工件的材料和性能要求选择合适的工 艺参数,以确保处理效果达到最佳。
控制环境污染
在热扩渗过程中,应采取有效的措施控制废气、废水和噪音等污染, 以符合环保要求。
专业操作和维护
热扩渗技术的操作和维护需要专业人员进行,以确保设备的正常运行 和使用效果。
安全操作规程
在热扩渗过程中,应遵守安全操作规程,防止发生意外事故。
05
热扩渗的未来发展
新材料的研究与应用
高性能陶瓷材料
研究具有优异耐热、耐磨、 耐腐蚀等性能的新型陶瓷 材料,拓展其在热扩渗领 域的应用。
纳米材料
利用纳米材料的特殊性质, 如高表面活性、高扩散性 等,提高热扩渗过程的效 率与效果。
复合材料
对基体材料的影响
热扩渗处理对基体材料的影响主要表现在对基体材料的硬 度和强度的提高。这是由于在热扩渗过程中,基体材料发 生塑性变形和相变,使材料的硬度和强度得到提高。
对基体材料的影响还包括对材料的热稳定性和抗疲劳性能 的提高。这些性能的提高可以提高零件的稳定性和可靠性 。
04
热扩渗的优缺点
优点
表面处理第七讲热扩渗
• 热扩渗原理 • 热扩渗工艺 • 热扩渗的效果与影响 • 热扩渗的优缺点 • 热扩渗的未来发展
01
热扩渗原理
热扩渗技术的定义
热扩渗技术是指在一定温度下,利用热激活的扩散作用,将一种或几种元素从固 体表面渗入内部,以改变材料表面的化学成分、组织结构和性能的一种表面处理 技术。
01
02
03
04
高效率
热扩渗技术能够在短时间内对 大量工件进行表面处理,提高
我国热处理的现状及先进热处理技术的发展和展望

我国热处理的现状及先进热处理技术的发展和展望热处理是指通过加热和冷却工艺,改变材料的组织结构和性能的一种工艺方法。
热处理广泛应用于钢铁、有色金属及其合金、塑料等材料的生产过程中,对提高材料的力学性能和使用寿命具有重要作用。
1.技术水平相对较低。
虽然我国热处理行业经过长期的发展已经取得了一定成就,但与国际先进水平相比还存在差距。
在技术设备和管理方面,我国热处理企业普遍存在缺乏投入和关注的问题。
2.信息化程度不高。
我国热处理行业在信息化方面的投入和应用较少,信息化程度相对较低,企业之间的信息共享和交流不够密切,影响了行业整体的发展。
3.环保意识不足。
我国热处理行业大部分企业在环境保护方面存在一定问题,热处理工艺中的废水、废气等排放未能得到有效处理和控制。
目前,我国热处理行业正积极推进先进热处理技术的发展,以提高产品质量、提升企业竞争力,并改善行业整体环境。
以下是我国先进热处理技术的发展和展望:1.先进的真空热处理技术。
真空热处理能够在无氧或低氧氛围中进行,减少材料表面氧化的问题,提高材料的耐腐蚀性和机械性能。
同时,真空热处理还能够实现材料的表面强化和改性,提高材料的使用寿命。
2.先进的低温热处理技术。
低温热处理技术主要包括低温渗碳、低温氮化等。
通过低温热处理可以实现材料的表面硬化和改性,提高材料的磨损和疲劳性能,同时减少材料的变形和裂纹。
3.先进的等离子体热处理技术。
等离子体热处理是一种通过等离子体化学反应实现材料表面改性的方法。
该技术具有温度低、速度快、效果好等优点,能够实现材料的表面强化和改性,提高材料的高温性能和抗腐蚀性。
展望未来,我国热处理行业在发展先进热处理技术的同时,应加强与国际接轨,提高品牌影响力和核心竞争力。
同时,还应注重培养热处理人才,推动热处理行业的技术创新和进步。
此外,还需要关注环保问题,推动热处理行业的绿色发展,减少对环境的影响。
总之,我国热处理行业在发展先进热处理技术方面还存在一定的差距,但随着技术的不断进步和应用的推广,相信我国热处理行业将会迎来更好的发展机遇。
2024年渗透汽化膜市场发展现状

2024年渗透汽化膜市场发展现状引言渗透汽化膜(Pervaporation Membrane)是一种高效的分离技术,广泛应用于化工、环保、食品等领域。
本文将探讨渗透汽化膜市场的发展现状,涵盖市场规模、应用领域、技术进展以及前景展望。
市场规模渗透汽化膜市场在过去几年间迅速发展,市场规模不断扩大。
据市场研究数据显示,2019年全球渗透汽化膜市场规模达到X亿美元。
预计到2025年,市场规模将达到Y亿美元,年复合增长率为Z%。
应用领域渗透汽化膜广泛应用于以下领域:化工行业化工行业是渗透汽化膜的主要应用领域之一。
渗透汽化膜在分离反应中可以实现高效的组分分离,特别适用于分离混合物中的有机溶剂。
它被广泛应用于石油化工、精细化工等领域。
渗透汽化膜在环保领域具有广阔的应用前景。
它可以有效地分离和回收有机物、水溶液中的重金属离子等。
通过应用渗透汽化膜技术,可以实现废水处理、有害气体治理等环保目标。
食品行业渗透汽化膜在食品行业中也得到了广泛应用。
它可以用于食品加工过程中的浓缩、提纯、除臭等操作。
渗透汽化膜可以更好地保留食品的口感、营养成分和风味,提高产品质量。
技术进展渗透汽化膜技术在过去几年间获得了显著的进展。
以下是几个重要的技术进展:新型材料研究人员不断开发新型渗透汽化膜材料,以提高膜的分离性能和稳定性。
聚酯、聚醚、聚酰胺等材料被广泛应用于渗透汽化膜制备中,提高了膜的渗透性和选择性。
膜制备技术膜制备技术是渗透汽化膜技术发展中的关键环节。
传统的制备方法包括溶液浸渍法、层析法等。
近年来,浸渍-交联法、层析-交联法等新的制备方法被提出,提高了膜的性能和稳定性。
多功能渗透汽化膜是近年来的研究热点。
多功能膜不仅具有渗透分离功能,还具有其他功能,如催化、吸附等。
这种多功能膜可以实现一步法的催化分离,提高分离效率和产品纯度。
前景展望渗透汽化膜市场未来有着广阔的发展前景。
随着全球化工、环保和食品行业的快速发展,对于高效分离技术的需求不断增加。
第五篇 热扩渗技术

名称 α相 γ相 含氮铁素体 含氮奥氏体 结构 体心 面心 面心 含氮 (wt%) 590℃:0.1 室温:0.004 ≤2.86 5.30~5.70 4.55~11.0 斜方 11.07~ 11.18 特性 有铁磁性 590℃共析转变, 慢冷: γ→α+ γ’ 铁磁相,硬度较高, 脆性小 铁磁相,650℃发生 共析: ε → γ+ γ’ 具有高脆性
热浸铝工艺影响因素
5.2 液体热扩渗
铝液成分、温度、时间 基体成分: ☆钢中C、Si含量增加,浸铝层厚度下降 ☆钢中的Cr、Mn元素,浸铝层厚度下降 ☆Si提高铝液流动性,降低合金层的厚度 和硬度
渗铝
渗铝的方法很多: 液态渗铝:工件浸入铝液 固体粉末渗铝:88%AlFe粉+10%石英粉 +2%NH4Cl2膏剂,涂在工件表面3~5mm厚, 在专用密封炉内加热,使铝渗入工件。 表面喷涂铝,再扩散退火渗铝:电弧喷涂 0.7~1.2mm铝层,在920~950℃进行4~6 小时扩散退火渗铝。
渗氮厚度与时间、温度的关系(95%N2+5%H2)
第五章 热扩渗技术
热扩渗工艺分类 按渗剂状态分:气体法、液体法、固体法 和等离子法。 按渗入元素分:渗碳、渗氮、渗硫、渗硼、 浸铝、浸锌、碳氮共渗、氮碳共渗等。 按工作温度分:高温( ≥910 ℃)、中温和 低温热(≤720 ℃)热扩渗。
5.1 气体热扩渗
第五章 热扩渗技术
热扩渗层的组织: 形成单相固溶体,如渗碳层中的α-Fe。 形成化合物,如渗氮层中的ε相(Fe2-3N), 渗硼层中的Fe2B等 。 形成固溶体和化合物的混合组织,并形成 梯度分布。
第五章 热扩渗技术
40CrNiMo钢 (a)渗碳:层深0.5mm 左右,表面碳势0.9 %。 表层为高碳马氏体+ 颗粒状碳化物+ 残留 奥氏体;心部为中碳 马氏体。 (b)渗氮:表层碳氮 化合物+ 含氮马氏体 + 残留奥氏体,心部 是回火索氏体。
热扩散的发展趋势
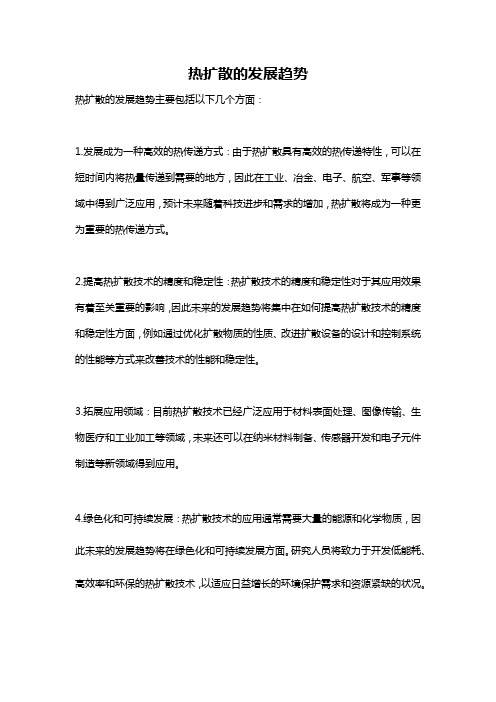
热扩散的发展趋势
热扩散的发展趋势主要包括以下几个方面:
1.发展成为一种高效的热传递方式:由于热扩散具有高效的热传递特性,可以在短时间内将热量传递到需要的地方,因此在工业、冶金、电子、航空、军事等领域中得到广泛应用,预计未来随着科技进步和需求的增加,热扩散将成为一种更为重要的热传递方式。
2.提高热扩散技术的精度和稳定性:热扩散技术的精度和稳定性对于其应用效果有着至关重要的影响,因此未来的发展趋势将集中在如何提高热扩散技术的精度和稳定性方面,例如通过优化扩散物质的性质、改进扩散设备的设计和控制系统的性能等方式来改善技术的性能和稳定性。
3.拓展应用领域:目前热扩散技术已经广泛应用于材料表面处理、图像传输、生物医疗和工业加工等领域,未来还可以在纳米材料制备、传感器开发和电子元件制造等新领域得到应用。
4.绿色化和可持续发展:热扩散技术的应用通常需要大量的能源和化学物质,因此未来的发展趋势将在绿色化和可持续发展方面。
研究人员将致力于开发低能耗、高效率和环保的热扩散技术,以适应日益增长的环境保护需求和资源紧缺的状况。
我国离子化学热处理技术的现状与展望概要

我国离子化学热处理技术的现状与展望一、概述离子化学热处理是置于低压容器内的工件,在辉光放电的作用下,带电离子轰击工件表面,使其温度升高,实现所需原子渗扩进入工件表层的一种化学热处理方法。
与常规化学热处理相比,离子化学热处理具有许多突出的特点:渗层质量好、工艺可控性强、工件变形小、处理温度范围宽、易于实现局部防渗;渗速快、生产周期短,可节约时间15%~50%;热效率高、工作气体耗量少,一般可节能30%以上、省气70%~90%;无烟雾、废气污染,处理后工件和夹具洁净,工作环境好;柔性好,便于生产线组合,实现自动化。
正因为如此,离子化学热处理一直是近几十年来热处理技术发展的一个热点,并在不太长的时间内迅速得到了推广应用。
20世纪30年代,德国学者B.Berghous首先发现了在辉光放电电场(即等离子区进行表面硬化的优越性,并采用此工艺进行了渗氮处理,取得了第一个离子渗氮发明专利;40年代,该技术在军事领域获得应用;50年代后,经原西德学者的进一步研究,KlöcknerIonon 公司(原西德于1967年实现工业应用。
60年代末期,我国开始了离子渗氮技术的研究,内容涉及工艺、设备、性能及基础理论等广泛的领域,并实现了试制设备到生产应用设备的过渡,到1980年,我国已拥有离子渗氮炉400余台,居世界第一。
目前,我国离子渗氮炉的保有量已超过1700台,并仍以每年60~80台的速度递增。
总的来讲,在离子化学热处理领域,我国已跻身于国际先进水平行列。
涉及到离子化学热处理研究开发的内容较多,既有基础理论、组织和性能,也有设备开发;在工艺上的内容更多,几乎化学热处理中所需渗入的元素,都可在离子轰击条件下实现。
世界上不同的国家根据所处的工业状况和投资背景,在离子化学热处理的各个方面做了大量的工作。
据资料统计,前苏联、中国、美国、英国、德国、日本和法国的研究工作处于领先地位。
特别是美国和英国在离子渗碳、钛合金离子渗氮研究方而一路领先;前苏联在离子渗硼方面尤为突出;而我国在离子多元共渗、离子渗金属方面处于领先地位。
热扩渗技术

热扩渗技术
热扩渗是用加热扩散的方式使欲渗金属或非金属元素渗入模具 的表面,形成表面合金层,从而提高模具表面的耐磨性、耐腐蚀性 以及疲劳强度等性能。热扩渗技术又称为热渗镀技术或化学热处理 技术,其突出特点是扩渗层与基材之间是靠形成合金来结合的(即 所谓冶金结合),具有很高的结合强度,这是其他涂层方法如电镀、 喷镀或化学镀、甚至物理气相沉积技术所无法比拟的。
热扩渗可分为固体热扩渗、液体热扩渗、气体热扩渗。常用 的热扩渗技术有渗碳、渗氮、碳氮共渗等。
2020年12月29日星期二
返回目录
2020年12月29日星期二
1.1 固体热扩渗工艺及应用
1.固体渗碳 固体渗碳是将工件和固体渗碳剂装入渗碳箱中,用盖子和耐火泥封
好,然后放在炉中加热至900~950 ℃,保温足够长时间后,得到一定厚 度的渗碳层。固体渗碳剂通常2CO3)的混合物。木炭提供固体渗碳所需要的活性碳原子, 碳酸盐起催化作用。 2.固体渗硼
工件在密封的渗碳炉中,加热到900~950 ℃后,向炉内滴入易分解 的有机液体(如煤油、苯、甲醇等),或直接通入渗碳气体(如煤气、 石油液化气等),经一系列反应后产生活性碳原子,使钢件表面渗碳。
气体渗碳的特点是生产效率高,劳动条件好,渗碳过程中可以控制, 渗碳层的质量和机械性能较好。 2)气体渗碳后的热处理
固体渗硼可在650~1000 ℃内进行,常用于850~950 ℃,可保温 2~6 h,不同钢种可获得50~200 m深的固体渗硼层。固体渗硼工艺应用 较广,适用于几何形状复杂,包括带有小孔、螺纹和盲孔的零件。中、 小零件的固体渗硼采用粒状和粉末状介质,大件及其局部的渗硼采用膏 剂。这些介质均由供硼剂(B4C、B-Fe、非晶态硼粉)、催渗剂(KBF4、 NH4Cl、NH4F等)以及调节活性、支承工件的填料(Al2O3、SiC、SiO2)组 成。 3.固体渗铬
第10章 热扩渗技术-用

能进行热扩渗的材料包括:碳、氮、硼、锌、铝、铬、钒、铌、钛、硅、 硫等和这些元素的多元共渗。
10.1 热扩渗的基本原理 及分类
一、热扩渗层形成的基本条件
渗入元素的原子存在于扩渗层的形式:
与基体金属形成:固溶体或金属间化合物层,或固溶体+化 合物的复合层
形成渗层基本条件:
1.渗入元素必须能够与基体金属形成固溶体或金属间化合物。 2.欲渗元素与基材之间必须有直接接触。 3.被渗元素在基体金属中要有一定的渗入速度。 4.(对靠化学反应提供活性原子的热扩渗工艺)该反应必须满 足热力学条件。 (产生活性原子;反应平衡常数>1%。)
三、热扩渗速度的影响因素
热扩渗层的形成速度是由形成渗层的三个过程中最慢的一个来制约。 在初始阶段:化学介质分解化学反应速度 在中后期:扩散速度 能影响化学反应速度和扩散速度的因素,均将影响热扩渗层的形成速 度:增加反应物浓度、提高反应温度、加入适当催化剂等均能使反应 速度成倍提高。在扩散过程中,升高温度就更有效。
基材心部
10.1.2 热扩渗工艺的分类
按热扩渗温度:高温(高于910℃)、中温和低温(低于720℃)热扩渗 按渗入元素:非金属元素热扩渗、金属元素热扩渗、金属一非金属元素多元共渗、扩
散退火(均匀化退火)。
按渗剂在工作温度下物质状态:
气体热扩渗 液体热扩渗 固体热扩渗 等离子体热扩渗 复合热扩渗
热浸镀:
常见:钢铁制品的热浸锌、热浸铝、热浸锡等。 2. 特点:生产效率高。渗层厚度不易均匀,且只适于浸 渗熔点较低的金属。
1.
10.2.1
热浸镀原理
热浸镀时,被镀的基体材料与熔融金属的接触面上发生界面 反应,是一个冶金过程,按相应的相图形成不同相构成的合 金层,所以热浸镀层是由合金层和浸镀金属构成的复合镀层。 钢铁的热浸镀过程
- 1、下载文档前请自行甄别文档内容的完整性,平台不提供额外的编辑、内容补充、找答案等附加服务。
- 2、"仅部分预览"的文档,不可在线预览部分如存在完整性等问题,可反馈申请退款(可完整预览的文档不适用该条件!)。
- 3、如文档侵犯您的权益,请联系客服反馈,我们会尽快为您处理(人工客服工作时间:9:00-18:30)。
气体热扩渗技术的发展现状
摘要:气体热扩渗是应用较广泛的一种化学热处理方法。
但是,随着对气体热扩渗机理研究和生产应用实践的深化,近几年来在常规气体热扩渗工艺的改进、新工艺的发展以及拓宽热扩渗工艺的应用领域等方面,都取得了新的进展。
本文综述这方面的主要成果。
关键词:气体,热扩渗,发展
1前言
气体热扩渗是把工件置于含有渗剂原子的气体介质中加热到有利于渗剂原子在基体中产生显著扩散的温度。
使工件表面获得该渗剂元素的工艺过程。
产生活性原子气体的渗剂可以是气体、液体、固体。
但在扩渗炉内都成为气体;在气体热扩渗过程中,渗剂可以不断补充更新,使活性原子的供给、吸收和内部扩散的过程持续维持:可以随时调整炉内气氛,实现可控热扩渗[1]。
气体热扩渗包括气体渗碳、气体渗氮、气体碳氮共渗和气体氮碳共渗。
2气体渗碳的发展现状
近几年国内气体渗碳技术发展很快。
为了提高零件的质量,使产品进入国际市场,国内许多企业引进了国外的先进设备和先进工艺。
同时,国内一些大专院校和科研单位也对渗碳设备和渗碳工艺进行了研制和创新。
这使得国内气体渗碳处理技术处在一个非常活跃的时期,新成果、新经验、新工艺不断出现,对产品质量的提高,起了巨大的推动作用[2]。
2.1广泛使用先进的渗碳设备
先进的渗碳设备普遍采用微机按输入的预定程序,对渗碳过程自动控制,从设备的类型看主要是两大类,一是连续生产线,二是大型井式渗碳炉。
这些设备大部分是从国外购进的,也有一部分是国产的。
先进的渗碳设备的特点是技术先进、气氛可控、性能稳定、质量可靠、机械化自动程度高,体现了生产发展水平。
2.2合理选择渗碳用钢
现在世界各国正从微观上研究提高渗碳钢使用的合理性。
从渗碳用钢角度来看,主要是钢的含碳量和合金元素的含量这两个方面。
有研究表明,为了获得最高的弯曲抗力和疲劳极限以及合理的应力分布,钢的含碳量(指未渗碳前钢的原始含碳量)不能高于0.25%C。
最近由于对材料内氧化机理的研究,人们认识到内氧化是影响渗碳零件寿命的一个重要因素,法国已把内氧化作为渗碳质量检验的一项内容。
这里讲的内氧化是指在渗碳过程中,氧原子扩散到零件内部,与某些合金元素形成氧化物。
易形成氧化物的合金元素有Mn、Cr、Ti、B等,难于形成氧化物的合金元素有Ni、Mo等。
大家都已经了解,Cr、Ni共同使用能提高材料的综合性能[3]。
2.3稀土在渗碳钢上的应用
目前很多单位在研究稀土元素对渗碳钢组织和性能的影响。
综合起来讲,稀土元素能细化奥氏体晶粒。
2.4真空渗碳
在真空炉中进行的渗碳是一种高温气体渗碳工艺,由于渗碳是在真空高温状态下进行,因此具有净化零件表面,金相组织均匀,消除渗碳过程中内氧化等优点,并且渗碳时间比一般渗碳时间缩短一半。
2.5离子渗碳
离子渗碳过程简述如下,零件在真空炉中被加热到920℃,然后导入丙烷或丙烯,并在零件上加以10KV/cm的电场,使炉内气体发生辉光放电,产生碳离子,碳离子向零件表面轰击引起碳原子向零件内部的扩散。
离子渗碳具有渗碳速度快、渗碳质量易控制、不产生内氧化等优点。
2.6中温气体渗碳
为了减少零件的变形、延长设备的使用寿命、提高生产率,国内许多厂家研制并开始使用中温气体渗碳工艺。
所谓的中温气体渗碳工艺是在催渗剂的作用,渗碳过程在860~900℃温度下完成。
其工艺具有渗碳组织细小,淬火变形小、节约电能、延长设备使用寿命等优点。
陕西机械学院研制成功的《微氮中温渗碳技术》已获国家专利。
第二汽车制造厂模具分厂已把这项技术应用生产,收到了较好的经济效益[4]。
其实稀土渗碳工艺也是中温渗碳技术。
3气体渗氮的发展现状
近年来,由于气体渗氮温度低、变形小、工序少等诸多优点,在精密齿轮的制造中,渗氮处理已逐渐取代了传统的气体渗碳淬火处理[5]。
现今发展起来的有快速深层渗氮工艺,在快速深层渗氮工艺利用稀土催渗,快速渗氮新技术包括表面预氧化,表面预变形,表面纳米化预处理,激光表面氮化及其他新技术。
各种快速渗氮技术都能在一定程度上提高渗氮速度。
渗氮优化工艺能在20h以内使渗氮层厚度达0.8mm,较普通渗氮时间缩短了2/3;若能将不同的优化渗氮工艺的方法与各种新技术相结合,那么一定能进一步缩短渗氮时间,增加渗氮层的厚度。
若能进一步缩短深层渗氮的时间,那么将大大降低精密齿轮的加工成本,提高经济效益,为齿轮加工业的发展创造更广阔的前景[6-7]。
4气体碳氮共渗发展现状
气体碳氮共渗是在20世纪60年代被大量研究,70年代得到广泛使用的一项传统热处理技术。
该技术由于氮的渗入使钢的临界点(A1、A3)下移,可以适当降低淬火温度,提供了进一步减少淬火变形的可能。
氮的渗入还使淬透性增加,所以除合金钢外,碳素钢也可以实施碳氮共渗及油淬处理,从而提高硬度和表面耐磨性,这两个特点也正是该技术被广泛应用的原因。
20世纪末到本世纪初以来,出现了一种预抽真空式碳氮共渗技术。
从C、N 来源和使用渗剂方法来看,共渗机理、结果和气体碳氮共渗是一样的,渗剂中仍有含氧介质。
渗层组织中仍有表面晶界氧化层,并无法杜绝。
不过此法由于使用
了真空排气和密封技术,不仅工艺过程缩短,效率提高,渗剂使用量略有减少,而且晶界氧化层深度也有所减轻。
本世纪以来,H.Altena和F.Schrank介绍了往真空炉中通入丙烷、氨气的新技术来提高合金钢和非合金钢的表面硬度,借助真空中工艺过程的控制来影响金属表层碳、氮浓度及渗层的深度,说明了碳、氮渗入的过程和影响因素,报道了关于设备的构想。
2004年日本专利公开,该专利提到的新技术特征:在真空炉内,工件被加热至渗碳温度,通入渗碳气体进行渗碳、扩散,然后降低温度,再向真空状态的炉内通入渗氮气体,进行渗氮。
碳钢或表面硬化钢用这种新技术都可以得到要求的表面硬度、层深和韧性[8]。
5气体氮碳共渗的发展现状
气体氮碳共渗的应用范围仅次于气体渗碳。
以日本为例,在日本工业中,氮碳共渗占了化学热处理市场总量的30%。
随着应用范围的进一步扩广,气体氮碳共渗将进一步得到发展[9]。
5.1气体稀土氮碳共渗
稀土元素在化学热处理中的应用研究起始于80年代初期,但发展很快。
稀土元素对气体氮碳共渗的影响80年代末、90年代初人们进行了大量的研究。
研究结果表明:无论稀土化合物还是稀土单质当添加量适当时,对氮碳共渗有明显的催渗作用,可提高渗速30%左右,适量稀土能有效提高氮碳共渗后的硬度、耐磨性、冲击韧性和抗腐蚀性能。
应用于自行车冷作模具,其使用寿命比常规氮碳共渗提高35%以上。
5.2气体铁素体合金化氮碳共渗
气体铁素体合金化氮碳共渗(简称合金化渗氮)是一种新的表面硬化技术。
它在渗氮(碳)同时,使工件表面渗人所添加的元素(如Al、Cr、Ti和V等)其实它是低温金属元素一氮一(碳)共渗。
合金化渗氮可形成高硬度(比常规气体氮碳共渗高l00~500HV)、低脆性(I级)和致密的渗层;渗速比气体氮碳共渗高10~20%。
本技术解决了铁素体氮碳共渗后表面硬度不够高的问题。
在合金化渗氮基础上西安理工大学又进行了室温形变合金化渗氮研究,结果表明:(l)室温形变使合金化渗氮层深度随形变量增加而增加,当形变量超过一定值(该值随材质而异)后,渗氮层探度随形变量增加而减小。
(2)合金化渗氮硬度随形变量增加而增加。
5.3加压气体氮碳共渗
南昌航空工业学院试验研究了加压气体氮碳共渗的工艺特性,结果表明,铁素体氮碳共渗随着炉压的增加,渗层的表面硬度、化合物层和扩散层厚度均有所增加。
奥氏体氮碳共渗采用加压脉冲工艺,在680℃工艺温度下,能将氨分解率控制在75%左右,容易实施以氨为渗剂的奥氏体氮碳共渗,并且加压奥氏体氮碳共渗后化合物层较致密,基本上无疏松[10]。
参考文献:
[1]钟厉,孙艳鹏.热扩渗工艺的研究应用及进展[J].热加工工艺,2007,(22)
[2]夏期成.渗碳工艺的发展和应用[J].山西机械,1996,(01)
[3]横濑敬二,蔡千华.渗碳技术的进展[J].国外机车车辆工艺,2007,(04)
[4]张伯英.气体渗碳技术发展概况[J].内燃机配件,1996,(03)
[5]陈玮,王蕾,周磊,王君.钢的快速渗氮技术研究现状[J].武汉科技大学学报(自然科学
版),2006,(03)
[6]周上祺,范秋,林任勤,胡振纪.快速深层渗氮工艺的设计[J].金属热处理,1998,(03)
[7]孟力凯,齐义辉.快速气体渗氮工艺[J].辽宁工学院学报(自然科学版),2002,(06)
[8]安峻岐,刘新继,何鹏.渗碳与碳氮共渗催渗技术的发展与现状[J].金属热处理,2007,(05)
[9]A.kurz,SHU UIm,D.Joritz,曾国屏.用一体化全自动氮碳共渗设备进行可控气体渗氮的经
验[J].国外金属热处理,2004,(05)
[10]石淑琴.气体氮碳共渗的发展[J].高等职业教育-天津职业大学学报,1999,(03)。