塑料射出成型的问题与改善对策
射出成型问题改善与解决对策指引

射出未飽模
•原因分析:
1.射出量不足 2.熔膠流動不足 3.不正確的模具設計 1.調整射出容量。 2.1.增加射出壓力; 2.2.增加料管噴嘴溫度; 2.3.增加模溫; 2.4.增加射出時間及速度。 3.1.加大入口,流道,水口; 3.2.改進入口,流道,水口的設計; 3.3.改進入口位置; 3.4.增加排氣孔。
改善對策:
2.2.增加射出壓力; 3.2.使用冷卻固定裝置;
4.2.減低模溫;
5.2.改為含有玻璃珠樹脂。
噴痕(Jetting)
•原因分析:
1.熔膠填充太快
改善對策:
1.1.降低射出速度; 1.2.改變入口位置及種類,如側面入口。
•原因分析:
收縮過度
1.加工條件問題 2.入口太小
•原因分析:
成品翹曲變形
1.前後模溫度不同 2.過份收縮 3.成品厚度不平均變化太大 4.未充分固化前頂出 5.射出方向性(尤其含玻璃纖維樹脂) 6.不夠強硬 1.1.確定模具溫度是否平均; 2.1.降低模具溫度; 2.3.增大入口。 3.1.重新設計模具; 3.3.增長冷卻時間。 4.1.增長冷卻時間; 4.3增加頂出面積。 5.1.改變入口位置; 6.1成品加肋或增加厚度。
表面線狀氣紋皺紋如魚眼
•原因分析:
1.溫度太高氣化 2.樹脂吸濕 3.料管有死角 4.入口設計不良
改善對策:
1.1.減低料管溫度; 1.2.減低噴嘴溫度; 1.3.減少成型周型或用小料管。 2.1.再幹燥; 2.2.使用包裝未破之樹脂。 3.1料管及噴嘴設計為流線形。 4.1加大入口尺寸或更改位置。
射出成形品之缺陷及改善对策
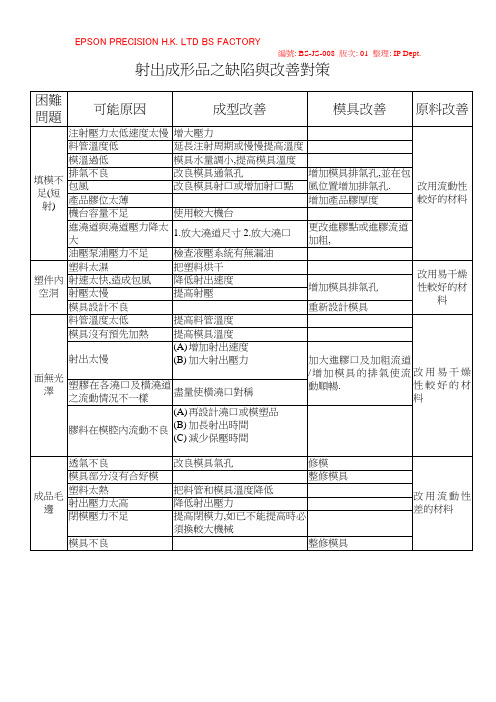
流紋和塑面起波紋
膠料不夠熱
增加膠料溫度
調整原料流動性
模具不夠熱
增加模具溫度
澆口太小,使膠料在模腔內有噴射現象
擴大澆口和降低射出壓力
加大進膠點
塑品切面厚薄不均勻
(A)再設計塑件,使切面厚薄均一.
(B)去除塑品上的突盤和凸起的線條
根據產品狀況改模
塑膠在澆口成層狀
膠料過冷
提高料管溫度
調整流動性較好的原料
射出成形品之缺陷與改善對策
困難問題
可能原因
成型改善
模具改善
原料改善
填模不足(短射)
注射壓力太低速度太慢
增大壓力
改用流動性較好的材料
料管溫度低
延長注射周期或慢慢提高溫度
模溫過低
模具水量調小,提高模具溫度
排氣不良
改良模具通氣孔
增加模具排氣孔,並在包風位置增加排氣孔.
包風
改良模ห้องสมุดไป่ตู้射口或增加射口點
產品膠位太薄
(E)澆口不對稱
(F)射出速度太慢
(G)保壓不足
(H)填充計量不足
(A)修改模具或增加注射壓力
(B)增加入料
(C)增加射出壓力
(D)增加射出時間
(E)限制熔膠全部流入最近直澆道澆口,使熔膠流入其它澆口
(F)增加射出速度
(G)增大澆口尺寸
(H)增加保壓壓力時間
增加填充計量.
根據產品膠位狀況改模,
更改進口調整一致.
加硬脂酸鋅通常需要攪攔均勻
外潤滑劑和塑料的混合不均勻
延長混和時間增加小量潤滑劑
射出速度太快
(A)模具設排氣孔
(B)減少射出壓力
(C)降低料管溫度
射出成型常见不良现象级处理措施

射出成型中常见不良现象产生原因分析及对策以下所列举的成型中产生的不良原因及对策是指在一般情况下可能出现的﹐也仅以本人在工作中的一些心得﹐体验为例﹐如有不妥或不周之处﹐还请各位行家指正﹗(一)短射(不饱模)(1)短射(不饱模)﹔即是溶融塑料未能完全填充填满成型空间(模穴)各个角落的现象(2)原因及改善对策(见下表)(二)毛边(1)毛边﹔即是在分模面﹑流道周围及模仁镶块间隙内出现的膜状或毛刺状的多余胶料(2)原因及改善对策(见下表)*注﹔成型时间过长﹐模温过低而采用高压﹐高速射出也是产生毛边的常见原因(三)银线(1)银条(银线)即是在成型产品表面或表面附近﹐沿塑料流动方向﹐呈放射状的银白色条纹。
(2)原因及改善对策(见下表)(四)成品光泽度低(1)成品光泽度低是指成品表面光泽达不到质量要求﹐表面无折光度。
(2)原因及改善对策(见下表)(五)变形(1)变形可分为对角线的扭曲及平行边沿的曲翘两种﹐是成品成型中发生的不规则弯曲现象(2)原因及发善对策(见下表)(六)顶白(1)顶白(也叫白化)是指成品在脱模之际﹐在顶针或其它脱模部位出现白色痕迹(2)原因及改善对策(见下表)(七)结合线(1)结合线是指在成型中﹐二道或多道熔融材料融合时出现的细线状(2)原因及改善对策(见下表)(八)冲料痕(1)冲料痕是指熔融材料在进料点附近﹐以浇口为中心而呈现的条纹状(2)原因及改善对策(九)异色(黑纹)(1)异色(黑纹)是指在成型过程中﹐在成品表面出现的黑色或其它深色条纹(2)原因及改善对策(见下表)(十)气泡(1)气泡是熔融塑料中的水份﹐挥发气体于成型过成中被封入内部而残留的空动现象(2)原因及改善对策(见下表)射出换料要诀在射出成型作业中﹑换料﹑换色的问题﹐值得吾入深入探讨﹒如何以最快速的方法完成换料﹑换色﹐除可节省时间外﹐并可降低一笔相当可观的生产成本﹒一﹑同一材料之换色1﹒1同一材料的换色时﹐原则上从淡色材料换为深浓色材料﹐较从不透明材料换为透明材料容易﹒一般换色作业程序如下﹔(1)关斗漏料斗下部的进料挡门(2)空射数次﹐将加热料管内的材料全部射出(3)新材料加入漏斗(4)打开进料挡门﹐螺杆前进后退十数次直到换色完成﹒从不透明材料换为透明材料时﹐尤需拆除喷嘴头部份﹐清除残留的材料﹐必要时杆亦需抽出撤底清理﹐不可有残余料积存死角处﹒二﹑不同材料之换色2.1 不同材料的更换作业﹐是利用前后各材料的熔融黏度差﹐与加热管的温度控制来施行换料手续。
射出成型不良及对策(供参考)
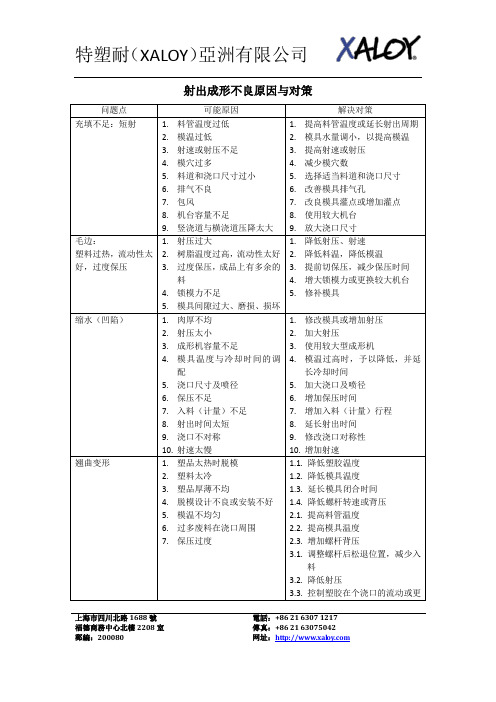
上海市四川北路1688號福德商務中心北樓2208室電話:+86 21 6307 1217傳真:+86 21 63075042 射出成形不良原因与对策问题点可能原因解决对策充填不足:短射 1.料管温度过低2.模温过低3.射速或射压不足4.模穴过多5.料道和浇口尺寸过小6.排气不良7.包风8.机台容量不足9.竖浇道与横浇道压降太大1.提高料管温度或延长射出周期2.模具水量调小,以提高模温3.提高射速或射压4.减少模穴数5.选择适当料道和浇口尺寸6.改善模具排气孔7.改良模具灌点或增加灌点8.使用较大机台9.放大浇口尺寸毛边:塑料过热,流动性太好,过度保压1.射压过大2.树脂温度过高,流动性太好3.过度保压,成品上有多余的料4.锁模力不足5.模具间隙过大、磨损、损坏1.降低射压、射速2.降低料温,降低模温3.提前切保压,减少保压时间4.增大锁模力或更换较大机台5.修补模具缩水(凹陷) 1.肉厚不均2.射压太小3.成形机容量不足4.模具温度与冷却时间的调配5.浇口尺寸及喷径6.保压不足7.入料(计量)不足8.射出时间太短9.浇口不对称10.射速太慢1.修改模具或增加射压2.加大射压3.使用较大型成形机4.模温过高时,予以降低,并延长冷却时间5.加大浇口及喷径6.增加保压时间7.增加入料(计量)行程8.延长射出时间9.修改浇口对称性10.增加射速翘曲变形 1.塑品太热时脱模2.塑料太冷3.塑品厚薄不均4.脱模设计不良或安装不好5.模温不均匀6.过多废料在浇口周围7.保压过度1.1.降低塑胶温度1.2.降低模具温度1.3.延长模具闭合时间1.4.降低螺杆转速或背压2.1. 提高料管温度2.2. 提高模具温度2.3. 增加螺杆背压3.1. 调整螺杆后松退位置,减少入料3.2. 降低射压3.3. 控制塑胶在个浇口的流动或更上海市四川北路1688號福德商務中心北樓2208室電話:+86 21 6307 1217傳真:+86 21 63075042改4. 修改设计或调整5. 修改模具冷却水路6.1. 调整射出时间6.2. 减少或增加浇口尺寸7. 缩短保压时间,降低保压压力射嘴流涕 1.塑料含水份太多2.射嘴或料管温度过热3.射嘴孔太大、太短1.充分干燥塑料2.1. 降低料温或射嘴温度2.2. 降低背压2.3. 减少计量段之有效流量3. 射嘴孔改小或加长气泡:成品内部残留气泡,原因与凹陷相同1.塑料含有水份、挥发份或添加剂,因热分解,在射入模腔内因压力降而形成大量之气泡2.真空气泡:成品厚薄不一,易造成厚薄面之固化速度不同,使较厚之部位凹塌形成真空的空洞3.入料不足4.射出时间太短1.塑料充分干燥,增加入料量,螺杆设计提高内压2.1. 增加塑料温度,提高模温2.2. 清洁模具表面2.3. 加大浇道及浇口尺寸,并降低射速2.4. 加大射压,增加保压时间3. 增加进料速度,调整射出速度的变化位置4. 延长射出时间成品烧焦(变黄)、塑料变色:射出压力太大所引起之压缩烧焦斑点PS:20℃空气瞬间压缩至200kgf/cm^2时,空气温度会达到1058℃使得塑胶高温碳化1.空气在料管内受压缩时放热,造成塑胶烧焦2.因卡料而造成塑化过度3.模具排气不良,模腔内空气来不及挤出模具外,造成空气被隔热缩成高温,使得成品烧焦4.螺丝缸压设有滞留部5.压缸喷嘴螺杆头等螺纹部有树脂渗入6.成形机压缸内滞留时间长7.螺杆中卷入空气产生压缩而发热8.螺杆不适当1.1.降低料管及射嘴温度1.2.降低背压、转数1.3.充分干燥塑料2.检视料管、螺杆是否刮伤3.1.降低射压及射速3.2.浇口加大,加设排气孔4.消除死角以防止材料滞留5.避免螺纹部的损伤改善密著性6.检视温控系统,减少塑料滞留时间7.减少漏斗内的材料,并增高背压8.更换合适的螺杆浇口部的模糊 1.射速太快2.浇口尺寸过小1.降低射速2.加大浇口成品脆化(龟裂):强度不足1.干燥不确定,造成塑料水解现象,降低分水量,例如PC、PETP、聚芳酯1.预备干燥塑料要完全2.1.降低料管温度及射嘴温度2.2.减少树脂滞留料管时间上海市四川北路1688號福德商務中心北樓2208室電話:+86 21 6307 1217 傳真:+86 21 630750422.树脂温度过高,导致热分解,降低分子量3.残留变形量4.塑化不足,造成塑胶无法在模腔内完全相熔合5.模具温度不均匀,填模太实6.模具温度太低7.脱模设计不当(倒扣位、角度斜位)8.顶针或环定位不当2.3.减少次数使用比例2.4.使用适当大小之射出机3.使用减少残留变形量的成形条件4.1.提高料管温度4.2.延长加料时间4.3.降低背压5.修改模具冷却水管配置,减少入料速度,降低射压6.提高模温7.修改模温8.重新安放顶针裂纹、破裂 1. 成品表面残留应力,经一段时间后,表面发生微小破裂1.1. 降低射压或保压1.2. 提高射出机能力射嘴牵丝 1. 温度过高 1.1. 降低料管温度或射嘴温度1.2. 降低转速1.3. 增加松退吃料噪音 1.机台问题2.料管与螺杆间隙太小3.料管螺杆排气不良1.更换机台生产2.加大间隙3.增加排气效果银条:成品沿塑料流动表面,呈现银白色条纹1.塑料含有水份或挥发性物质,因受压缩而呈现液态状,当挤出射嘴进入模具后压力突然下降而使液态状被蒸发而成气态,使得塑胶在与模具表面接触时,固化后因表面细泡而形成银白色条纹2.粉粒熔融时其间空气亦随着一起射出3.塑料过冷,模温过低,造成慢速充填,因而射嘴温度过高使得有冷料问题1.1.改善机台底压、背压之控制,增加塑化并同时减少入料时有效流量,用以降低待射区之内压1.2.充分干燥塑料2.1.加大背压,可改善排出气体2.2.降低射压3.充分干燥塑料,加强螺杆排气,提高背压,降低射压成品表面银痕:成品表面出现银色斑纹1.水汽太多2.冷料头3.螺杆排气不良4.模具设计不良5.射出速率不足1.干燥塑料2.该用长射嘴,改成形条件3.重新设计螺杆4.改模具,浇口加大,加设排气孔5.改用射出速率快的机台喷痕(喷射激流现 1.射速过快 1.降低射速上海市四川北路1688號福德商務中心北樓2208室電話:+86 21 6307 1217 傳真:+86 21 63075042象):从浇口出来的塑料蛇形做不安定流动的结果2.射压过大3.浇口尺寸不足4.浇口制品及接续部不良PS:最佳的塑料流动形:从浇口流出来的材料先碰壁然后整体流动2.降低射压3.加大浇口尺寸约为肉厚1/3以上4.接续部设置角隅R成品波流痕(流痕):与射出方向呈垂直的表面流痕,塑料须在固化前全部射入模腔内1.先流进模具之塑料表面冷却固化,被后来之塑料推进成条纹状,造成塑料与模具表面断续接触而形成或于浇口附近形成2.浇口尺寸太小1.1.增加料温及模温1.2.提高射压及射速,但须注意激流现象2.浇口尺寸加大表面蛇纹模具浇口为小灌点,料进入模穴后没有受到阻挡直接跑到成品后端,造成先进去的料提早冷却而无法散开所形成改变灌点方向及浇口改扁平状表面波纹塑料过冷,模温过冷,射压过低,射速过低提高料温及模温提高射压及射速熔合痕迹 1.浇口位置不适当2.模具排气不完全3.射速太慢4.树脂温度过低5.射压不足6.塑品厚薄差异过大7.熔合线形成后,离完全充填时间太长8.熔合线离浇口太远1.变更浇口位置2.熔合部设置排气孔,最先设置树脂滞留处3.提高射速4.提高料及模温,增加模塑周期5.加大射压6.修改模具设计,浇口定位适当7.缩短射出时间,增加射压,改浇口位置8.再定位浇口位或该用对称浇口胶品尺寸性改变 1.模塑情况不稳定2.变更成形条件3.检查塑件时,周围的空气温度不固定1.调整成形条件2.检查胶料温度、胶料压力、模具温度、循环时间、入料、电压、温度调节表、压力系统、放入漏斗时材料温度3.1.保持周围空气温度固定3.2.在中午及午夜换班时,关闭窗户3.3.电风扇冷气不能吹到成品脱模不良粘模 1.脱模斜度不足表面精度不够1.加大脱模斜度(脱模方向的研磨要确实)上海市四川北路1688號福德商務中心北樓2208室電話:+86 21 6307 1217 傳真:+86 21 630750422.顶出销位置不适当且数量销径均不足3.射压、保压过大或料管温度过高4.冷却时间不足5.进料太多6.注射时间过长7.模具内倒扣位8.模腔深入部分空气压力小9.开模时间变动不定10.模具内壁光洁不够2.增加顶出销数量,并变更位置3.1.降低射压或料管温度3.2.降低螺杆转速或螺杆背压,降低射压及保压4.增加冷却时间5.减少入料6.缩短射出时间7.出去倒扣位打研磨抛光增加脱模部分的斜度8.设立适宜的排气孔9.使用计时器,保持固定开模时间10.模腔壁抛光成品凹陷:成品表面凹陷缩水成品厚薄不均,造成薄处固化压力无法传至肉厚处,造成肉厚处凹陷(结晶性塑料容易发生)1.1.改塑料1.2.不用次料1.3.提高射压射速1.4.改成品外型,改流道过IR RE-FLOW后翘曲1.产品没有完全结晶甚至没有结晶,故单面受热造成单面再度结晶,结晶面缩收变形2.射压过大,造成内应力大,当受热软化应力释放变形3.入料点烧焦变大,造成模压不足,剪切热低,压缩纤维排列不良,造成无纤维变形1.增加模具温度,增加结晶2.减少进料点尺寸,使其降低射压,增加模压3.加强透气孔,降低射压混炼不均 1.螺杆压缩比太小2.螺杆设计配套不适当1.螺杆压缩比加大2.增加混炼设计塑料未融 1. 螺杆设计不适当 1. 修改螺杆设计成品白纹:成品透明中夹有白色物状或整个乳白状1.水汽太多2.含有别种塑料3.塑化不好1.干燥塑料2.彻底洗料管3.1.加温,加背压或压缩比3.2.改塑料3.3.不用次料成品白点:透明成品中夹有白色小点粉末造成不用次料,强力抽风,设计螺杆气疮 1.塑料含水分2.夹杂空气1.塑料加强干燥2.增加背压表面不光泽(粗糙) 1.模温过低 1.提高模温上海市四川北路1688號福德商務中心北樓2208室電話:+86 21 6307 1217 傳真:+86 21 630750422.塑胶粒含水量过高3.射压太低或保压不足4.浇口尺寸过小5.模具研磨太粗糙6.模壁有水份7.脱模剂过多8.射速太慢2.烘干塑胶粒,以降低含水量3.提高射压或保压4.增加浇口尺寸5.加强模具研磨6.清洁和修理漏水裂痕防止水汽在壁面凝结7.清洁模具及用少量脱模剂8.增加射速及溶胶温度,增加背压表面浮纤白痕 1.料温或模温过冷2.塑料除湿不完全或次料比过高3.保压不足及射速不足4.透气孔不足或透气孔堵塞5.塑料过热1.提高料温或模温2.加强塑料干燥,控制次料比3.增加保压时间、压力及增加射速4.清洁透气孔及检查是否有做完整透气孔,做冷料袋加强排气效果5.减少塑料滞留时间表面浮纤流痕 1.料温或模温偏低2.单灌点造成模流转拆后的接触面极易产生浮纤流纹3.浇口太小使胶料在模腔内有喷射现象1.提高料温或模温2.改双灌点避免造成模流转拆,亦可增加充填效率3.浇口加大及降低射压浇口成层状 1.胶料或模具过冷2.射速太慢或射压不足3.射出时间过长4.胶料污染5.模具润滑剂过多6.水口太大或太小7.模具过热1.提高料及模具温度2.增加射速或射压3.缩短射出时间4.清洁料管,避免混入其它不同塑料5.清洁模具腔壁,用小量润滑剂6.调节水口大小,使得良好压力控制7.在模具过热部分增加冷却包风:1.白雾不光泽现象2.灌点对称边有明显的排气不良所产生包风现象1.可能在长时间使用后排气口已阻塞2.灌点切入成品的方向,朝向肉厚区域充填,导致肉厚部位先充填完成,而90℃弯角处较晚充填,且该弯角处又没有排气口,导致气体包在90℃弯角处3.部分模穴灌点较小,充填速1.保养模具,清理排气口2.调整灌点灌入的角度,使其先填满90℃弯角,再去充填肉厚部分3.调整模穴灌点大小,以减慢充填速度,提高排气效率4.烘干塑料5.降低射速6.提高射压上海市四川北路1688號福德商務中心北樓2208室電話:+86 21 6307 1217傳真:+86 21 63075042 度较快,则空气较不易即时排出4.塑料太湿5.射速太快6.射压太慢7.模具设计不良7.变更模具设计顶出拉痕 1.入口肉薄处易产生射压过高,头尾收缩不均,不易顶出2.灌点位置不适当,造成进胶直冲模仁,产生阻力过大1.1.增加入口处之肉厚1.2.增加透气孔或增加溢料袋2. 改变进料位置或增加进胶口顶出困难 1.模具冷却不足2.模具斜度不够3.塑件缩水而粘住公模4.射压过大5.单边顶出6.过度保压1.加大水量或延长冷却时间2.增加退模位的锥度3.升高模温或缩短冷却时间4.降低射压5.顶出销强度不正确6.降低射压或缩短保压时间成品黑点:成品表面或内部随机性发生黑点1.每模均发生:塑料裂解,油气,色粉再料管及螺杆表面或接触平面未锁紧发生死料情形,黑点大于0.05mm者2.频率性发生:过胶头未锁紧,黑点大于0.05mm3.每模均发生:空气中灰尘造成,黑点小于0.05mm者1.检查料管及螺杆上接触平面是否锁紧,改使用油,改善料管及螺杆表面光洁度,设计上避免死角,重新设计螺杆,注意换料过程2.锁紧接触平面3.改善环境,彻底清理机台成品黑纹:成品表面产生烟雾黑色纹路接触平面未锁紧,不正常加热,水汽太多,射压太大锁紧接触平面,检查电热是否异常,充分干燥,降低熔胶温度,降低射出压力吐黑:ABS吐黑、PC吐黑、黑条纹1.螺杆压缩比不适当2.螺杆固色粉附着过火变黑3.射嘴口径过小,造成塑料滞留在料内太久而过火4.塑料过热或添加耐燃剂之分解5.螺杆与料管表面滞留有烧焦之塑料6.螺杆与料管不同心圆摩擦7.温控有问题,造成难入料1.修改压缩比2.螺杆射嘴法兰拆下清理,螺杆抛光3.射嘴口径加大或模具进浇口加大4.降低料温5.料管及螺杆重新抛光6.检查料管及螺杆是否同心圆,并修改7.检查温控,改善入料小黑点塑料裂解烧焦脱落 1.清洗料管内壁上海市四川北路1688號福德商務中心北樓2208室電話:+86 21 6307 1217傳真:+86 21 630750422.用较硬的塑料进入,以擦净料管面3.避免胶料长时间受高温黑点 1.工作环境太脏2.模腔内有空气,引起焦化1.封盖料斗,胶料亦要封好2.1.增加模具排气效果2.2.修改浇口位置2.3.降低射压或射速2.4.增加或降低料管和模具温度,以改变胶料在模内的流动形态黑线黑点 1.逆流环磨损2.松退太长,致料管内有气体3.排气不良4.螺杆、逆流环不干净1.更换逆流环2.缩短松退或不要松退3.增加排气口4.清理料筒,螺杆逆流环镀硬铬处理黄点、黄线 1.料管温度太高或内部局部过热2.胶料在料管内停留太久3.料管内存有死角1.降低料管温度2.缩短循环时间3.更换料管螺杆棕色条纹 1.料管全面或局部过热2.胶料粘着料管或射嘴,以至烧焦1.1.降低发热器温度1.2.降低螺杆转速1.3.降低螺杆背压2. 清理射嘴或料管黑纹 1.射嘴孔与模具碰撞变形,孔变小或缺角凹陷2.过胶头被过胶圈严重磨损1.更换射嘴2.更换过胶头组(尖圈套)黑色条纹 1.冷胶料互相摩擦或与料管摩擦时烧焦2.螺杆与料管真圆度偏差引起摩擦烧焦熔胶3.射嘴过热,烧焦胶料4.射嘴温度变化范围大1.1.加入有外润滑剂的塑胶1.2.加入润滑剂1.3.增加料管后端温度2.1.再次使用活塞定位活塞与料管壁有足够距离使空气能顺利排出料管外2.2.避免用幼细磨料因其位于活塞与料管壁面间3.降低射嘴温度4.不要用开闭式温度控制器,该用变压器料头及进料点周围有黑色过胶头组设计不良重新设计过胶头组射胶(出)不稳定逆 1.过胶头组有切角破损 1.更换过胶头组上海市四川北路1688號福德商務中心北樓2208室電話:+86 21 6307 1217 傳真:+86 21 63075042料 2.过胶头组设计不良3.过胶圈磨损4.料管磨损2.重新设计过胶头组3.更换过胶圈4.更换料管塑料熔胶塑化不全 1.料管温度过低2.成型周期过快,塑料来不及完全熔胶塑化3.料管加料量无法控制4.螺杆转速过低5.熔胶温度分布不均1.1.提高料管温度1.2.提高螺杆背压2.1.延长成型周期2.2.变更螺杆设计,增加入料段行程3.改用有调节塑料流量之弹簧射嘴4.提高螺杆转速5.改用障避螺杆成型时间周期不稳定1.开关模时间长短不一2.不稳定压力3.料管温度不稳定4.模具温度不均匀5.入料不稳定1.用计时器控制模具开关模时间2.1.射胶压力要足够温度2.2.检查压力系统是否正常是否有裂痕3.1.检查温度控制器是否正常3.2.选用较好温度控制器3.3.检查电压是否正常3.4.检查电热片是否接触不良或损坏3.5.检查由窗户、冷气或风扇吹来的风向情况4.1.使用模具温度控制器4.2.检查或调整模具内的入水管4.3.检查模具排气是否正常5. 检查进料系统射嘴漏胶 1.胶料过热2.射嘴不适合3.背压过大1.降低料管或射嘴温度2.更换合适的射嘴3.降低背压或松退螺杆无法回转后退(吃料困难)(吃料空转)(无法松退)1.压缸温度过低2.背压过大3.回转数太少4.成形机能力不足1.提高压缸温度(特别是漏斗温度)约230℃以上2.降低背压3.降低回转数4.使用射出容量为模蓄容量2倍以上之成形机模具漏胶 1.锁模力不够2.胶料过热3.射出压力过高4.入料过多1.1.增加锁模力1.2.改用锁模力较大的注塑机2.1.降低胶料温度2.2.降低模具温度上海市四川北路1688號福德商務中心北樓2208室電話:+86 21 6307 1217 傳真:+86 21 630750425.入料不稳定6.模具凹凸面接触线不良7.成型周期不稳定2.3.降低螺杆转速或螺杆背压3.1.降低射出压力3.2.缩短保压时间4.减少入料(减少射出量)5.保持定量胶量落入柱塞前头6.研磨凹凸面接触线7.保持一模时间固定束管 1.熔融不够2.入料不顺3.马力不够4.转速不够1.提高熔融能力2.变更设计3.提高吃料压力4.提高转速料管升温 1.温度太低2.螺杆设计不良3.转速过高1.提高温度2.变更螺杆或螺杆公差太小3.降低转速。
射出成形问题改善与解决对策指引d
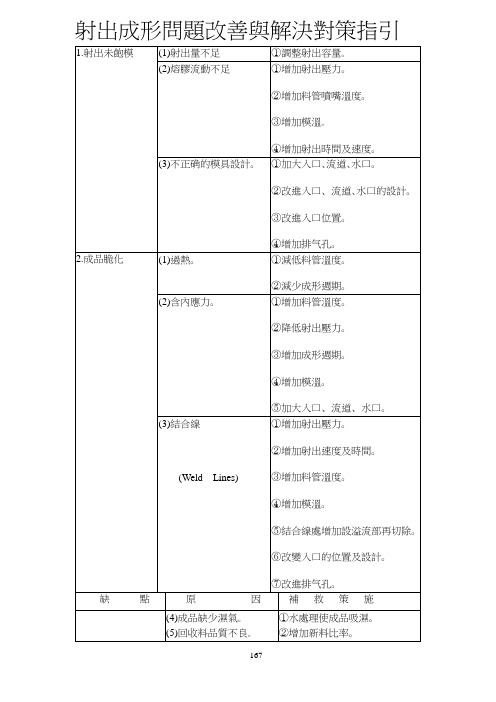
可能的決解辦法
9.多模穴中材料塑流不平均。
9.修正平衡狀況。
10.射料速度不足。
10增加射料速度。
11.進料口太小。
11.加大進料口。
12.射料量大於機器的能量。
12.換機器或減少模穴。
棕色流紋
(BROWN
STREAKS)
1.整個的或部分的料筒過熱。
1.降低加溫器的溫度。
2.料筒或射料咀堵塞。
2.清洗料筒,清洗射料咀,如果必要將料筒拆下並清洗之。
D儘可能使產品的厚度一致。
7.外著脫模劑不足。
7.加入硬酯酸鋅(每一百磅15克),尤其是使用回收料時。
8.外著脫模劑不一致。
8.拉長混料時間,或多加入少許潤滑劑予以混合之。
9.射出速度太快。
9.A增加排气孔。
B減少射出壓力。
C降低料筒溫度。
D降低射料速度。
10.外著脫模劑過多。
10.增加回收料或加入無脫模劑的材料與其混合。
(1)熔膠填充太快。
①降低射出速度。
②改變入口位置及種類,如側異入口。
缺點
原因
補救策施
11.收縮過度
(1)加工條件。
①降低模具溫度。
②增加射出壓力。
(2)入口太小。
①增大入口。
12.層狀分離
(LAMINATION)
(1)含有不相熔的異物。
①檢查樹脂,特別是使用回收料時。
(2)充填模穴導致高應力。
①增加模溫、料管溫度。
5.限制流經進料口的塑料儘可能在接近主流道處限壓。
6.頂出系統設計不良或操作不良。
6.重新設計。
7.模溫不一致。
7.維持模面於同一溫度。
8.進料口周圍填擠材料太多。
塑料注塑射出成型不良现象及对策-青岛中新华美
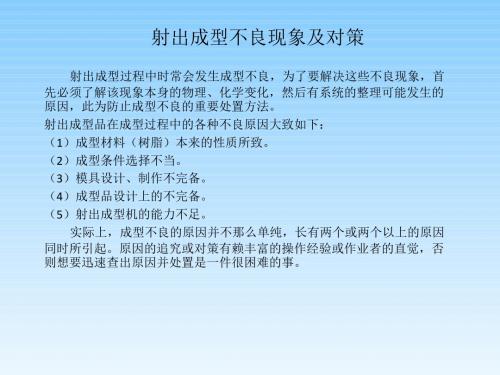
射出成型不良现象及对策
射出成型过程中时常会发生成型不良,为了要解决这些不良现象,首 先必须了解该现象本身的物理、化学变化,然后有系统的整理可能发生的 原因,此为防止成型不良的重要处置方法。 射出成型品在成型过程中的各种不良原因大致如下: (1)成型材料(树脂)本来的性质所致。 (2)成型条件选择不当。 (3)模具设计、制作不完备。 (4)成型品设计上的不完备。 (5)射出成型机的能力不足。 实际上,成型不良的原因并不那么单纯,长有两个或两个以上的原因 同时所引起。原因的追究或对策有赖丰富的操作经验或作业者的直觉,否 则想要迅速查出原因并处置是一件很困难的事。
成形条件 成型机械
1、降低树脂温度 2、提高螺杆背压 3、降低射出速度 4、加大螺杆压缩 比 5、减少螺杆回转 数及延长计量时间
成型品设计 模型
1、排气要好 2、尽量避免直角方 向的补强和肉厚产 生急剧变化 3、修正射出嘴和模 型浇口结合处是否 紧密
材料(树脂)
1、充分干燥 2、使用低挥发份 材料 3、加入热安定剂 4、注意添加剂本 身是否有吸湿性
原因
1、异物混入 2、配向性过大
成形条件 成型机械
1、降低射出压力 2、提高树脂温度 和模温 3、调整射出速度
成型品设计 模型
1、调整浇口的位 置和数目
材料(树脂)
1、避免相容性差的 他种树脂混入
埋入:
原因 成形条件 成型机械 成型品设计 模型
1、注意结合的精 度 2、避免埋入物周 围的应力集中在 一起
黑纹、焦斑、变色:
原因
1、树脂热分解 2、添加剂热分解 3、挥发气体在加 热刚筒内的压缩
成形条件 成型机械
1、降低成型温度 和模温 2、减少螺杆回转 速 3、降低射出压力 和射出速度 4、降低背压 5、清除螺杆内之 残留树脂
射出成形不良原因及对策

1. 流痕在成品表面或透視成品時,可以看到流動的痕跡。
例如:冰線、橘皮及結合線。
註:其它成品表面的缺失請參考:銀線、凹陷、噴痕及光澤。
原因解決方法/檢查要點1. 調整料管溫度曲線。
2. 提高噴嘴溫度設定。
3. 提高熱澆道溫度設定。
4. 提高背壓。
5. 提高螺桿轉速。
6. 如果冷卻時間比塑化時間長的話,降低螺桿轉速。
7. 檢查螺桿與料管之間的間隙。
註:如果必要的話,更換料管和螺桿。
A.融膠溫度太低或不均勻。
8. 在射出單元中增加混料裝置。
1. 提高保壓壓力。
2. 延長保壓時間。
B.保壓壓力太低或無效。
3. 檢查澆口是否阻塞(污染)。
註:如果必要的話,加大澆口。
1. 調整射出速度。
2. 調整射出速度曲線。
3. 調整射出壓力。
4. 調整射出壓力曲線。
C.射出速度/壓力不正確。
5. 檢查澆口是否阻塞(污染)。
註:如果必要的話,加大澆口。
D.塑料流動不足。
檢查澆口位置。
註:如果必要的話,增加或重新安排澆口位置(平衡)1. 提高模具溫度。
E.模具太冷或冷卻不均勻而造成塑料流動不良或不規則。
2. 檢查模具冷卻是否均勻或阻塞。
1. 檢查模具的合模面是否污染。
註:如果必要,清潔並拋光。
F.模具污染,如:過度潤滑。
2. 減少使用或不使用潤滑劑,不管是內部(在塑膠中)或外部(離型劑)的潤滑劑。
2. 縮水造成的空洞空洞的地方產生在壁厚最大的地方,如果將成品切開,就可以看到許多空洞地方。
原因解決方法/檢查要點A.由於壁厚太厚造成成品內空洞。
增加料量,並且經常秤成品重量(檢查重量)1. 增加射出速度。
B.射出速度/壓力不對。
2. 調整射出速度曲線。
3. 加大射出壓力。
4. 調整射出壓力曲線。
1. 提高保壓壓力。
2. 增長保壓時間。
C.保壓壓力太低或不足以補償塑膠3. 檢查澆口是否阻塞(污染)。
的收縮。
4. 檢查澆口尺寸。
註:如果必要的話,加大或重新安排澆口位置(以求平衡)。
D.由於料溫度太高,造成過度收縮。
降低料管溫度。
射出成型常见不良现象及对策
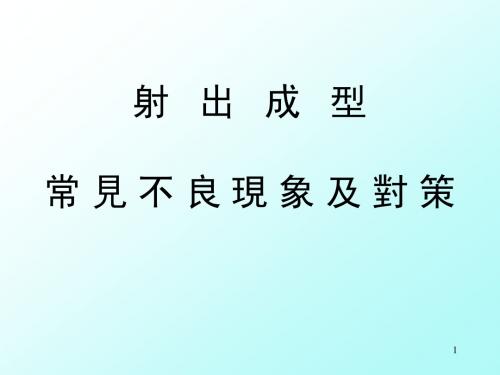
成型不良原因及對策
(六)噴射流 現象:在成形品表面,沿著澆口産生帶狀條紋; 原因:在塑料由澆口射入模內時,邊冷卻,邊射入而
産生塑料固化現象;
對策:加大澆口,或檢查修正澆道之計使用低速射
出,模具加模溫控制。
19
成型不良原因及對策
(七)白化、裂痕
現象:
白化---承受變曲形量大時,顔色變白的,此易 發生在ABS料上。 裂痕---成形品破裂,或經過長時間後産生裂痕
射 出 成 型 常見不良現象及對策
1
目
录
成型不良对策条件调整原则 利用射程控制的不良對策 常见不良现象的防止与对策
成型不良对策条件调整原则
均应先有成型三观念为前提。 改一不改二。一次性调整尽量只调一个要素。 温度的调整一次性调高或调低应5℃~6℃为宜, 并须正常射出5~10模后确认。 压力或速度的调整一次性的调整应为其原来 前值的10%作微调。 位置的调整宜配合压力与速度的控制来作业。
V3 V4 V2
V1
提高充填速度(或充填壓力)
9
利用射程控制的不良對策
凹陷
尺寸不足
P1 P2 P3 P4
提高保持壓力(或延長保持時間)
10
利用射程控制的不良對策
接合線明顯
V2
V1
V2 V4
通過接合線部位快速通過 (或其切換位置前後移動)
11
成型不良原因及對策
(一)充填不足 現象:在成品上産生缺角 原因:塑料注入模穴內,末端尚未填滿之前産 生冷卻固化現象或是塑料本身流動性不 良,計量不足,模內排氧不良,沇動陰 抗太大,鎖模力不足,均會産生此現象。 對策:針對上述個別原因,找出真正毛病予以 改善。
- 1、下载文档前请自行甄别文档内容的完整性,平台不提供额外的编辑、内容补充、找答案等附加服务。
- 2、"仅部分预览"的文档,不可在线预览部分如存在完整性等问题,可反馈申请退款(可完整预览的文档不适用该条件!)。
- 3、如文档侵犯您的权益,请联系客服反馈,我们会尽快为您处理(人工客服工作时间:9:00-18:30)。
增加模温
压力不足
增加压力
模温不均一
重新排列冷却水管
入料不足
增加入料,并保持固定料量注入工模内
空气不能排出模腔
增加排气道数目和尺码
外润滑剂不足
加外润滑剂
射料时间不足
增加射料时间
流入多模腔工模的熔胶流态不能适当平衡
改正不平衡情形
浇口(Gate)小
扩大浇口
模腔容胶量大过注塑机射胶量
用较大注塑机或减少工模内模腔数目
用脱模剂过多
清洁工模及用少量的脱模剂
非全部熔胶在模腔内与腔壁接触
A.增大注射压力
B.提高磨温
C.增加入料
注射速度慢
A.增大注射速度
B.增加熔胶温度
C.用最大压力;减少熔胶缓冲垫
D.增大螺杆背
使用过多的内或外润滑剂
检查材料和选用适当品种
工模腔壁粗糙
再次抛光模壁
31.射胶不足
材料不够热
增加熔胶筒各种温度
再定浇口位置或用几个相同的对称浇口代替
空气逃离工模不够快
A.增设足够排气孔
B.顶针中间设排气空
塑品切面厚薄变化大
A.再设计塑件
B.浇口定位要适当
工模过冷
提高模温
射料压力不够
增大压力
注射速度慢
增大注射速度
30.塑件表面粗糙
模温太冷
提高模温
注射压力太低
增大注射压力
模壁有水分
清洁和修理漏水裂痕或防止水汽在壁面凝结
塑料射出成型的问题与改善对策
困难问题
原因分析
改善方法
1.塑件面呈银纹
胶粒潮湿
预先干燥材料或用料斗干燥器;避免材料在模塑前遭受较大的温度变化
熔胶在模腔内流动不连续
A.浇口要对称
B.再定浇口位置
C.保持模温均匀
D.尽量使制品切面厚薄均匀
缺乏外润滑剂
加硬脂酸锌(每100磅胶料加15.5克);通常需要翻磨
外润滑剂和塑料的混合不均匀
胶料在模腔内流动不良
A.再设计交口或模塑品
B.加长低压持续时间
3.胶粒未能全部熔胶
熔胶筒温度过低
A.提高熔胶筒温度
B.增加螺杆背压
模塑周期过快,使熔胶筒内胶料供应不足
延长模塑周期
熔胶筒加料量无法控制
改用有调节塑料流量的射嘴
4.翘曲(变形)
塑胶制品于太热时脱模
A.降低塑胶温度
B.降低工模温度
C.延长工模闭合时间
注射压力过大
降低注射压力
射胶时的保压时间过长
用最少的注射时间和保压时间
前后工模温度变化过大
使前后工模温度一致
浇口熔胶凝结慢
减少浇口尺码
退火温度不当
试选用最高的退火温度直至热扭变温度轻微或无增加为止
塑件切面厚度不均
尽可能保持切面厚度均匀
工模温度过低
增高模温
机筒温度与模温不配合
选择适当的机筒温度和模温
进料过多
提高锁模压,如已不能提高时必须换较大机械
模具不良
整修模具
12.射嘴漏胶
胶料太热
降低加热缸或射嘴温度
射嘴不合适
更换适合的射嘴
背压太高
降低背压或松退
13.凹痕(缩水)
模腔胶料不足,引致收缩。
A.塑品切面厚,或厚薄不均匀
B.入料不足
C.注射压力太小
D.注射时间太短
E.浇口不对称
F.注射速度太慢
A.修改工模或增加注射压力
A.首先减少射嘴、鱼雷头分流梭温度,然后是熔胶筒温度
B.延长模塑周期或选用有较大发热量的注塑机
C.预热材料或安装料斗干燥器以保持材料固定的温度
胶粒中混入少量空气
A.降低机筒后段(近料斗处)温度和避免用翻磨料或柱塞或注塑机
B.柱塞向前推尽后,缓冲垫要少
C.增加螺杆注塑机的前段(入料区)
修改工模
顶针或环定位不当
再安装顶针俾能顺利将塑件顶出工模
21.胶品尺寸性改变
模塑情况不稳定
A.调节操作情况,直至得到最大的平稳操作
B.啤塑工人视乎各种情况而决定啤塑时间长短
今次啤塑与上次情况不同
A.改正跟上次不同之处
B.检查胶料温度、胶料压力、工模温度、模塑周期时候、入料、电压、温度调节表、压力系统和放入料斗材料温度
A.工模排气要改好
B.再设计工模或塑件
C.再定浇口(Gate)位置
D.增加或减少熔胶筒和工模温度,以改变胶料在模内的流动形态
E.减低射胶压力或速度
17.黑色条纹
(Black Streaks)
冷胶粒互相摩擦或与机筒壁摩擦时烧焦
A.加入有外润滑剂的塑胶
B.翻磨料加入润滑剂
C.增加机筒后端温度
因柱塞或螺杆的中心有偏差,发生柱塞与机筒壁面摩擦,烧焦溶胶
保持工模温度均一
过多废料在浇口周围
A.调整注射时间
B.减少或增加浇口尺码
5.填模不足
注射压力太低
增大压力
加热缸温度低
延长注射周期或慢慢提高温度
模温过低
模具水量调小,提高模具温度
排气不良
改良模具通气坑
包风
改良模具射口或增加射口点
射速太慢
增快射出
6.顶出困难
工模冷却不足
加大水量或延长工模冷却时间
工模斜度不够
保持固定开模时间。如有需要,可用计时器
工模内壁光洁不够
模腔壁再次抛光
模蕊产生位移
重新装好模蕊
29.塑件表面出现微弱或明显的熔合线
胶料过冷
A.增加熔胶筒和工模温度
B.增加注射压力
C.减少柱塞(泵心)的熔胶缓冲垫
D.增加模塑周期
模腔壁涂脱模剂过多
A.抹赶工模壁,重新涂上小量脱模剂
B.在需要时才用脱模剂
熔合线离开浇口太远
32.塑件面呈银纹
塑胶温度过高
A.由喷嘴温度开始,减少机筒温度
B.降低螺杆旋转速度俾螺杆所受的背压也能减少
粗胶粒和幼胶粒(如翻磨料)的混合
避免用这类材料,或可经过筛选,得到粗细均一的胶粒
塑胶温度不均一。引致原因是:
A.射嘴、鱼雷头分流梭或熔胶筒温度过高
B.超过注塑机的塑化容量(磅/小时)
C.胶粒放入料斗时本身温度有变化
A.减少入料,如有可能量准每次的入料量
B.调节螺杆的加料位置
28.塑件粘模
注射压力或熔胶筒温度过高
A.降低注射压力或机筒温度
B.降低螺杆的旋转速度或螺杆背压
进料太多
减少入料
注射时间过长
减少注射胶料时间
工模内有倒扣位
除去倒扣位,打磨抛光,增加脱模部分的斜度
模腔深入部分空气压力小
设立适宜的排气道
开模时间变动不定
减少入料
制品脱模时依然过热
冷却工模,或马上将制品浸入水,或延长冷却时间
14.直浇道黏模
压力过大
降低注射压力或枕压时间
塑胶过热
降低塑胶温度
浇道过大
减少直浇道之尺寸;延长射嘴和用短浇道衬套
制品脱模锥度够
增大锥度
直浇道衬套和射嘴嵌接不适当
射嘴孔尺码应比直浇道衬套小
有倒扣位或模腔壁粗糙
去除倒扣位和模壁再抛光
在工模过热部分增加冷却
26.啤胶周期需时过长
胶料温度高
A.降低温度
B.减少螺杆旋转速度或背压
工模温度过高
降低模温
模塑时间不稳定
用记时表,管制工模开合时间
供热量不够
改换较大注塑机或将胶料预热
塑件较厚处,冷却不足
A.改变模内冷却水道位置
B.用快冷浴
过多漏胶需要修边
参看『23.漏胶』的补救办法
27.热扭变温度比实际应用时的温度范围低
延长混合时间增加小量润滑剂
注射速度太快
A.工模设排气孔
B.减少注射压力
C.降低机筒温度
D.减少注射速度
E.降低螺杆旋转速度或背压
模温过低
增高模温
注射压力过大
降低注射压力
2.表面不完整
材料冷
提高熔胶筒温度
工模冷
提高工模温度
注射缓慢
A.增加注射温度
B.加大注射压力
胶料在各浇口及横浇道的流动情况不一样
尽量使横浇口对称
螺杆、止逆圈不干净
清理加热缸,螺杆止逆圈硬铬处理
9.塑件变脆
废料加太多
少用或不用
加热不均
加长成型周期
尼龙成型不久
应用热水煮过
10.塑件内空洞
塑料太湿
把塑料烘干
射速太快,造成包风
速度缓慢
射压太低
提高射压
模具设计不良
重新设计模具
11.成品毛边
塑料太热
把加热缸和工模温度降低
注射压力太高
降低注射压力
闭模压力不足
入料不稳定
检查进料系统
23.漏胶
(Flash)
胶料太热
A.降低胶料温度
B.降低工模温度
C.减少螺杆旋转速度或螺杆背压
注射压力过高
A.降低压力
B.减少枕压时间(Booster time)
入料过多
减少入料
入料不稳定
泵心机要保持定量胶料落入柱塞前头
工模的凸凹两面接触线不良
再次打磨凸凹面的接触线
模塑周期不稳定
B.增加入料
C.增加注射压力
D.增加注射时间
E.限制熔胶全部流入最近直浇道浇口,俾使熔胶流入其它浇口
F.增加注射速度
G.增大浇口尺码
塑胶过热
A.降低机筒温度
B.适当控制工模温度过热的部分
注射塞(泵心)前熔胶缓冲垫
A.增加入料
B.保持泵心前熔胶垫层压力稳定