饲料--膨化料的优缺点
膨化料的优缺点(精选多篇)

膨化料的优缺点(精选多篇)第一篇:膨化料的优缺点膨化料的优缺点膨化加工是一项饲料加工新技术,饲料在挤压腔内膨化实际上是一个高温瞬时的过程:混和物处于高温(110-200 ℃)、高压(25-lOOkg / cm2)、以及高剪切力、高水分(10 %-20 %甚至 30 %)的环境中,通过连续混和、调质、升温增压、熟化、挤出模孔和骤然降压后形成一种膨松多孔的饲料。
1 膨化饲料的优点. 1 提高饲料的利用率膨化过程中的热、湿、压力和各种机械作用,使淀粉分子内 1,4 —糖苷键断裂而生成葡萄糖、麦芽糖、麦芽三糖及麦芽糊精等低分子量产物,膨化加工可使淀粉糊化度提高,纤维结构的细胞壁部分被破坏和软化,释放出部分被包围、结合的可消化物质,同时脂肪从颗粒内部渗透到表面,使饲料具有特殊的香味,提高了适口性,因而摄食率提高。
另外,植物性蛋白饲料中的蛋白质,经过适度热处理可钝化某些蛋白酶抑制剂如抗胰蛋白酶、脲酶等,并使蛋白质中的氢键和其他次级键遭到破坏,引起多肽链原有空间构象发生改变,致使蛋白质变性,变性后的蛋白质分子成纤维状,肽链伸展疏松,分子表面积增加,流动阻滞,增加了与动物体内酶的接触,因而有利于水产动物的消化吸收,可提高营养成分消化利用率 10 %-35 %。
. 2 降低对环境的污染膨化浮性鱼饲料在水中稳定性能好。
以挤压膨化加工而成的饲料颗粒,是靠饲料内部的淀粉糊化和蛋白质组织化而使产品有一定的黏结或结合力,其稳定性一般达 12h 以上,最长可达 36h,故可减少饲料营养成分在水中的溶解及沉淀损失。
有数据表明,一般采用膨化浮性鱼饲料比粉状或颗粒饲料可节约 5 %-10 %,并能避免饲料在水中残留,减少水体污染。
. 3 减少病害的发生饲料原料中常含有害微生物,如好气性生物、嗜中性细菌、大肠杆菌、霉菌、沙门氏菌等,动物性饲料原料中的含量相对较多。
而膨化的高温、高湿、高压作用可将绝大部分有害微生物杀死。
有资料显示,每克原料中大肠杆菌数达10 000 个,膨化后仅剩不到10 个,沙门氏菌在经85 ℃ 以上高温膨化后,基本能被杀死,这就有助于保持水质和减少水产养殖不利的环境因素,同时达到 0 . 4,这相当于水分含量在 8 %-10 %,更好地提高丁饲料的贮存稳定性。
膨化饲料
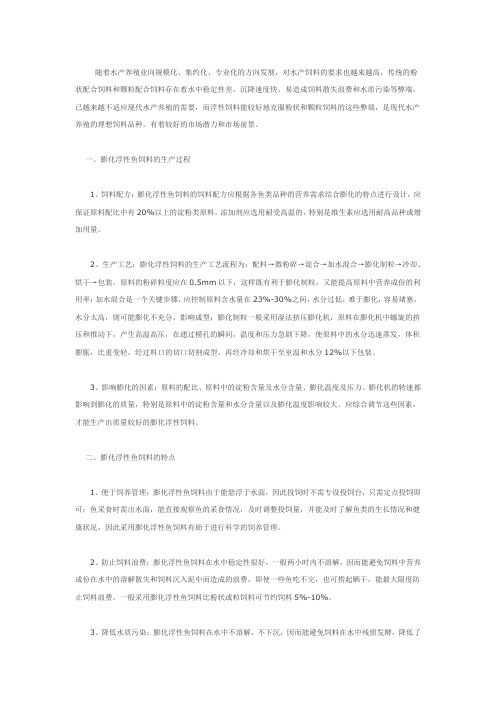
随着水产养殖业向规模化、集约化、专业化的方向发展,对水产饲料的要求也越来越高,传统的粉状配合饲料和颗粒配合饲料存在着水中稳定性差,沉降速度快,易造成饲料散失浪费和水质污染等弊端,已越来越不适应现代水产养殖的需要,而浮性饲料能较好地克服粉状和颗粒饲料的这些弊端,是现代水产养殖的理想饲料品种,有着较好的市场潜力和市场前景。
一、膨化浮性鱼饲料的生产过程1、饲料配方:膨化浮性鱼饲料的饲料配方应根据各鱼类品种的营养需求结合膨化的特点进行设计,应保证原料配比中有20%以上的淀粉类原料,添加剂应选用耐受高温的,特别是维生素应选用耐高品种或增加用量。
2、生产工艺:膨化浮性饲料的生产工艺流程为:配料→微粉碎→混合→加水混合→膨化制粒→冷却、烘干→包装。
原料的粉碎粒度应在0.5mm以下,这样既有利于膨化制粒,又能提高原料中营养成份的利用率;加水混合是一个关键步骤,应控制原料含水量在23%-30%之间,水分过低,难于膨化,容易堵塞,水分太高,则可能膨化不充分,影响成型;膨化制粒一般采用湿法挤压膨化机,原料在膨化机中螺旋的挤压和推动下,产生高温高压,在通过模孔的瞬间,温度和压力急剧下降,使原料中的水分迅速蒸发,体积膨胀,比重变轻,经过料口的切口切割成型,再经冷却和烘干至室温和水分12%以下包装。
3、影响膨化的因素:原料的配比、原料中的淀粉含量及水分含量、膨化温度及压力、膨化机的转速都影响到膨化的质量,特别是原料中的淀粉含量和水分含量以及膨化温度影响较大。
应综合调节这些因素,才能生产出质量较好的膨化浮性饲料。
二、膨化浮性鱼饲料的特点1、便于饲养管理:膨化浮性鱼饲料由于能悬浮于水面,因此投饲时不需专设投饲台,只需定点投饲即可;鱼采食时需出水面,能直接观察鱼的采食情况,及时调整投饲量,并能及时了解鱼类的生长情况和健康状况,因此采用膨化浮性鱼饲料有助于进行科学的饲养管理。
2、防止饲料浪费:膨化浮性鱼饲料在水中稳定性很好,一般两小时内不溶解,因而能避免饲料中营养成份在水中的溶解散失和饲料沉入泥中而造成的浪费,即使一些鱼吃不完,也可捞起晒干,能最大限度防止饲料浪费。
水产养殖中使用膨化饲料的优势?

水产养殖中使用膨化饲料的优势?膨化饲料,也被称为浮性饲料,其在膨化过程中由于热、湿、压力和各种机械作用,能使饲料中的淀粉充分糊化,破坏和软化纤维的细胞壁部分,释放营养,使蛋白质变性,脂肪稳定,有利于消化吸收,提高饲料的消化率和利用率。
与传统的颗粒饲料相比,膨化饲料消化性能好,水稳定性强,热敏抗营养素低,投喂管理方便,加之其特殊的工艺使得饲料具有特殊的香味,有利提升采食。
因此,虽然成本相对较高,但近年来,膨化饲料在水产养殖中日益受到养殖户的青睐,膨化饲料的饲用范围也从初始的高档水产养殖中逐渐扩散至中低档水产品饲养。
膨化饲料到底有哪些优点:1、提高饲料原料利用率颗粒饲料的调制温度在80~90°C之间,而膨化料的调制温度在100~110°C之间,膨化料的调制温度更高,可以提高饲料中淀粉的熟化程度,更容易被吸收。
颗粒料的淀粉糊化度最高不过30%,而膨化料的淀粉糊化度可以达到80%~99%。
2、水中稳定性较好,减少饲料浪费颗粒料在投喂时容易溃散,造成饲料的浪费,还会进一步导致水体溶氧量下降和残饵对水质的污染。
而膨化饲料在水中不下沉,且在水中的稳定性比较好,饲养鱼类可以有充裕的时间摄食,从而有效减少饲料浪费,避免水质污染。
而且,膨化饲料可以通过密度控制,适应不同的饲喂对象和不同的饲喂环境。
3、饲料适口性较好膨化饲料的结构疏松、多孔,具有独特的香味和篷松感。
此外,与颗粒饲料受生产工艺限制很难提高油脂添加量的劣势相比,膨化饲料可以采用后添加方式,提高饲料脂肪含量,在提高饲料能量水平的同时也提高了适口性,更充分满足水产动物快速生长的需求。
4、利于饲养管理和疫病防治膨化饲料浮于水面,在投喂时可以直接观察鱼类的摄食情况,及时调整投饲量,同时也可了解到鱼类的生长情况和健康状态。
鱼类膨化饲料工艺及优缺点浅析

鱼类膨化饲料工艺及优缺点浅析作者:廖建华来源:《好日子(下旬)》2017年第11期摘要:饲料业是我国农业中工业化程度最高的产业,是联系种植业、养殖业、畜产品加工业等产业的纽带,在农业中占有举足轻重的作用。
在饲料工业中,膨化水产饲料的生产工艺与传统的畜禽饲料的加工工艺有很大的不同。
根据水产饲料品种多、原料变化大、粉碎细度要求高和物料流动性差等特点,生产工艺的设计一般采用二次粉碎与二次配料混合来完成对粉状原料的加工;粉状原料经膨化机压制成型,再经过烘干、油脂喷涂和冷却筛选等工序来完成对膨化饲料的加工进入成品包装系统。
关键词:饲料;工艺在饲料行业中,人们把用来喂养动物的食物统称为饲料,饲料包括大豆、豆粕、玉米、鱼粉、氨基酸、棉粕、添加剂、乳清粉、油脂、肉骨粉、谷物、甜高粱等十余个品种的饲料原料。
原料是饲料的基础,不同的加工方法就会做出功能各异的饲料。
而这里所讲到的膨化饲料是一种专门适用于水产动物类(如图1-1)、幼畜、观赏动物等生长的饲料。
一般饲料的加工是一个多步骤,多工序的过程,通常要经过原料的接受与清理,再进行粉碎,混合,制粒等。
而膨化饲料膨化饲料是一项饲料加工新技术,饲料在挤压腔内膨化实际上是一个高温瞬时的过程:即饲料处于高温(110 -200 ℃)、高压(25-100kg/cm2)以及高剪切力、高水分(10 % -20 %甚至 30 %)的环境中,通过连续混和、调质、升温、增压、熟化、挤出模孔和骤然降压后形成一种膨松多孔的饲料。
饲料经膨化后,形成“爆米花”的状态,不但外形等物理状态有所改变,而且内部有机物分子结构也有改变,使淀粉更易消化,蛋白更易利用。
1 膨化饲料的加工工艺内容膨化饲料的加工工艺一般包含以下内容:(1)原料的接受与清理(2)原料的粉碎(3)原料粉碎后的配比与混合(4)混合后大颗粒料的微粉碎(5)二次配料以及二次混合(6)混合料的筛理(7)加水,蒸汽调质(8)湿法膨化制(9)后续的烘干,油脂喷涂以及冷却(10)最后的鉴定分级包装2 膨化饲料的优点及缺点一、膨化饲料的优点:(1)提高饲料的利用。
【新提醒】饲料用膨化玉米介绍
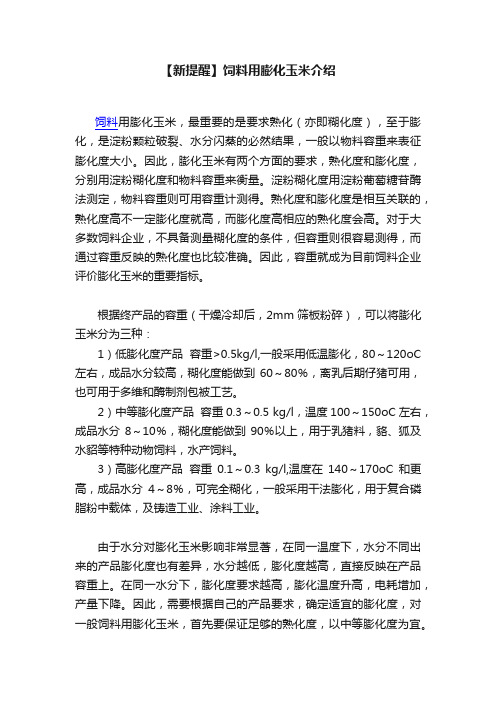
【新提醒】饲料用膨化玉米介绍饲料用膨化玉米,最重要的是要求熟化(亦即糊化度),至于膨化,是淀粉颗粒破裂、水分闪蒸的必然结果,一般以物料容重来表征膨化度大小。
因此,膨化玉米有两个方面的要求,熟化度和膨化度,分别用淀粉糊化度和物料容重来衡量。
淀粉糊化度用淀粉葡萄糖苷酶法测定,物料容重则可用容重计测得。
熟化度和膨化度是相互关联的,熟化度高不一定膨化度就高,而膨化度高相应的熟化度会高。
对于大多数饲料企业,不具备测量糊化度的条件,但容重则很容易测得,而通过容重反映的熟化度也比较准确。
因此,容重就成为目前饲料企业评价膨化玉米的重要指标。
根据终产品的容重(干燥冷却后,2mm筛板粉碎),可以将膨化玉米分为三种:1)低膨化度产品容重>0.5kg/l,一般采用低温膨化,80~120oC 左右,成品水分较高,糊化度能做到60~80%,离乳后期仔猪可用,也可用于多维和酶制剂包被工艺。
2)中等膨化度产品容重0.3~0.5 kg/l,温度100~150oC左右,成品水分8~10%,糊化度能做到90%以上,用于乳猪料,貉、狐及水貂等特种动物饲料,水产饲料。
3)高膨化度产品容重0.1~0.3 kg/l,温度在140~170oC和更高,成品水分4~8%,可完全糊化,一般采用干法膨化,用于复合磷脂粉中载体,及铸造工业、涂料工业。
由于水分对膨化玉米影响非常显著,在同一温度下,水分不同出来的产品膨化度也有差异,水分越低,膨化度越高,直接反映在产品容重上。
在同一水分下,膨化度要求越高,膨化温度升高,电耗增加,产量下降。
因此,需要根据自己的产品要求,确定适宜的膨化度,对一般饲料用膨化玉米,首先要保证足够的熟化度,以中等膨化度为宜。
过度膨化,不仅导致设备效率低下,还会产生一些抗酶消化的类似木质素的新键物质,使得膨化产品的淀粉含量下降或膳食纤维量上升,从而降低动物对淀粉的消化吸收。
膨化料
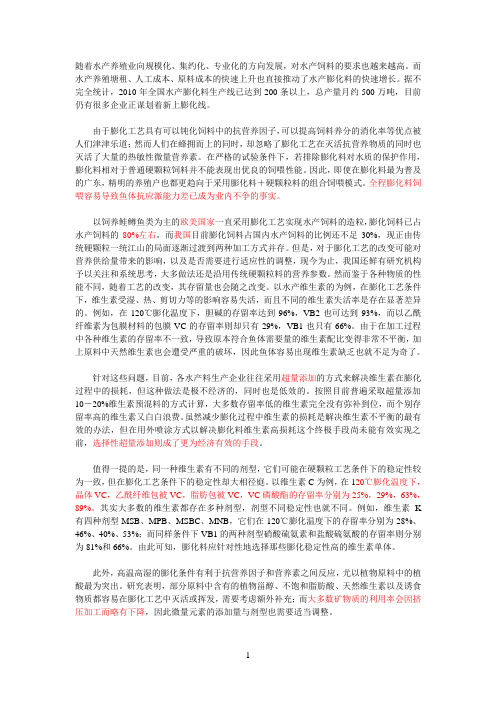
随着水产养殖业向规模化、集约化、专业化的方向发展,对水产饲料的要求也越来越高。
而水产养殖塘租、人工成本、原料成本的快速上升也直接推动了水产膨化料的快速增长。
据不完全统计,2010年全国水产膨化料生产线已达到200条以上,总产量月约500万吨,目前仍有很多企业正谋划着新上膨化线。
由于膨化工艺具有可以钝化饲料中的抗营养因子,可以提高饲料养分的消化率等优点被人们津津乐道;然而人们在蜂拥而上的同时,却忽略了膨化工艺在灭活抗营养物质的同时也灭活了大量的热敏性微量营养素。
在严格的试验条件下,若排除膨化料对水质的保护作用,膨化料相对于普通硬颗粒饲料并不能表现出优良的饲喂性能。
因此,即使在膨化料最为普及的广东,精明的养殖户也都更趋向于采用膨化料+硬颗粒料的组合饲喂模式。
全程膨化料饲喂容易导致鱼体抗应激能力差已成为业内不争的事实。
以饲养鲑鳟鱼类为主的欧美国家一直采用膨化工艺实现水产饲料的造粒,膨化饲料已占水产饲料的80%左右。
而我国目前膨化饲料占国内水产饲料的比例还不足30%,现正由传统硬颗粒一统江山的局面逐渐过渡到两种加工方式并存。
但是,对于膨化工艺的改变可能对营养供给量带来的影响,以及是否需要进行适应性的调整,现今为止,我国还鲜有研究机构予以关注和系统思考,大多做法还是沿用传统硬颗粒料的营养参数。
然而鉴于各种物质的性能不同,随着工艺的改变,其存留量也会随之改变。
以水产维生素的为例,在膨化工艺条件下,维生素受湿、热、剪切力等的影响容易失活,而且不同的维生素失活率是存在显著差异的。
例如,在120℃膨化温度下,胆碱的存留率达到96%,VB2也可达到93%,而以乙酰纤维素为包膜材料的包膜VC的存留率则却只有29%,VB1也只有66%。
由于在加工过程中各种维生素的存留率不一致,导致原本符合鱼体需要量的维生素配比变得非常不平衡,加上原料中天然维生素也会遭受严重的破坏,因此鱼体容易出现维生素缺乏也就不足为奇了。
针对这些问题,目前,各水产料生产企业往往采用超量添加的方式来解决维生素在膨化过程中的损耗,但这种做法是极不经济的,同时也是低效的。
挤压膨化对水产饲料营养价值的影响
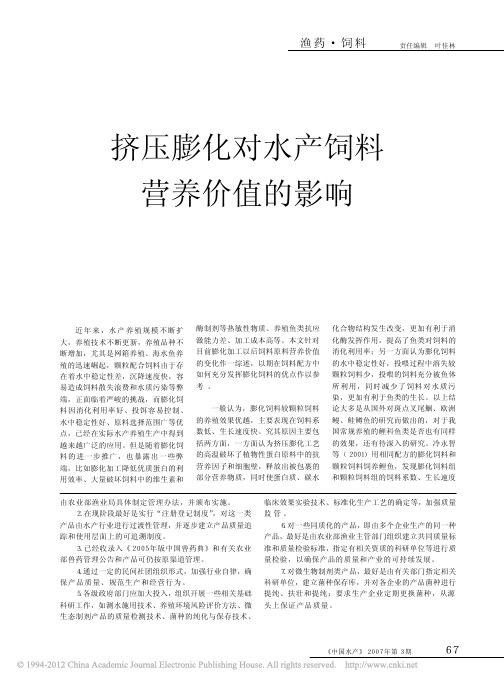
责任编辑 叶佳林挤压膨化对水产饲料营养价值的影响胡学峰 北京昕大洋科技发展有限公司 100081近年来,水产养殖规模不断扩大,养殖技术不断更新,养殖品种不断增加,尤其是网箱养殖、海水鱼养殖的迅速崛起,颗粒配合饲料由于存在着水中稳定性差,沉降速度快,容易造成饲料散失浪费和水质污染等弊端,正面临着严峻的挑战,而膨化饲料因消化利用率好、投饵容易控制、水中稳定性好、原料选择范围广等优点,已经在实际水产养殖生产中得到越来越广泛的应用。
但是随着膨化饲料的进一步推广,也暴露出一些弊端,比如膨化加工降低优质蛋白的利用效率、大量破坏饲料中的维生素和酶制剂等热敏性物质、养殖鱼类抗应激能力差、加工成本高等。
本文针对目前膨化加工以后饲料原料营养价值的变化作一综述,以期在饲料配方中如何充分发挥膨化饲料的优点作以参考。
一、膨化饲料的特点一般认为,膨化饲料较颗粒饲料的养殖效果优越,主要表现在饲料系数低、生长速度快。
究其原因主要包括两方面,一方面认为挤压膨化工艺的高温破坏了植物性蛋白原料中的抗营养因子和细胞壁,释放出被包裹的部分营养物质,同时使蛋白质、碳水化合物结构发生改变,更加有利于消化酶发挥作用,提高了鱼类对饲料的消化利用率;另一方面认为膨化饲料的水中稳定性好,投喂过程中溶失较颗粒饲料少,投喂的饲料充分被鱼体所利用,同时减少了饲料对水质污染,更加有利于鱼类的生长。
以上结论大多是从国外对斑点叉尾鮰、欧洲鳗、鲑鳟鱼的研究而做出的,对于我国常规养殖的鲤科鱼类是否也有同样的效果,还有待深入的研究。
冷永智等(2001)用相同配方的膨化饲料和颗粒饲料饲养鲤鱼,发现膨化饲料组和颗粒饲料组的饲料系数、生长速度渔药・饲料由农业部渔业局具体制定管理办法,并颁布实施。
2.在现阶段最好是实行“注册登记制度”,对这一类产品由水产行业进行过渡性管理,并逐步建立产品质量追踪和使用层面上的可追溯制度。
3.已经收录入《2005年版中国兽药典》和有关农业部兽药管理公告和产品可仍按原渠道管理。
08第八章 膨化工艺
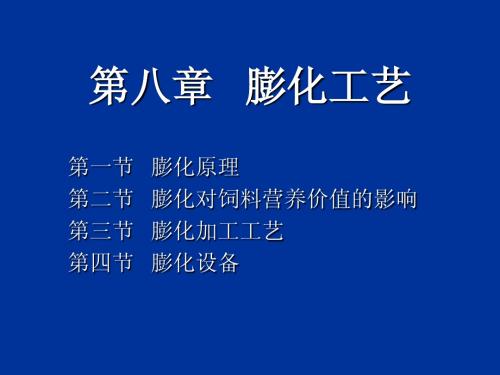
二、膨化工艺参数对饲料营养价值的影响
挤压机结构 物料粒度对挤压效果的影响 物料水分对UA及产量的影响 物料温度对挤压效果的影响 原料处理对大豆膨化效果的影响
第三节 膨化加工工艺
膨化饲料的生产有间歇膨化和连续膨化两 种工艺. 连续膨化使用较多,主要有三种形式:气流连 续膨化工艺,流动层式连续膨化工艺和挤压 式膨化工艺. 间歇膨化工艺生产周期长,生产效率低,因而 其应用受到限制.
一、间歇膨化工艺
物料装罐后密封,再加热是罐内温
度达到膨化所需压力,这时便可以 一开盖,开盖后物料会迅速膨化, 并自动流出。
二、气流式连续膨化工艺
包括两个系统:一是加热蒸气产生和输送 系统,二是进料和膨化系统。
来自锅炉的饱和蒸气,由高压风机压送至 蒸气加热器,变成过热蒸气,再输入物料 加热管。物料加热管有三个通管,其中一 个管口与离心分离器进风管相连,另一个 与旋转供料器相连,从而形成循环的热风。
第八章 膨化工艺
第一节 第二节 第三节 第四节 膨化原理 膨化对饲料营养价值的影响 膨化加工工艺 膨化设备
第一节 膨化原理
膨化指含有一定淀粉比例(20%以上)和一定 水分的原料,经高温高压处理后,淀粉糊化,蛋 白质分层,水分呈过热状态,再在短时间内(约 10s左右)降为常压,温度骤降,在温差、压差 的作用下,饲料体积迅速膨胀,水分迅速蒸发 而形成质地结构疏松的饲料,即膨化饲料。
湿法膨化营养成分损失小,适口性好,利 于动物消化吸收,能耗低,产量高,因而 适于大豆,粉料等原料的连续膨化过程。
湿法膨化的特点
增设蒸气等预处理有助于饲料异味的挥发 和祛除,使所有颗粒成为均匀的不可逆的 和连结的分散体。 提高膨化生产率。比干法高70—80%。 降低原料损失。干法损失5—6%,湿法损失 仅2%。 湿挤压膨化,延长易损件使用寿命22—50%。
- 1、下载文档前请自行甄别文档内容的完整性,平台不提供额外的编辑、内容补充、找答案等附加服务。
- 2、"仅部分预览"的文档,不可在线预览部分如存在完整性等问题,可反馈申请退款(可完整预览的文档不适用该条件!)。
- 3、如文档侵犯您的权益,请联系客服反馈,我们会尽快为您处理(人工客服工作时间:9:00-18:30)。
膨化料的优缺点
膨化加工是一项饲料加工新技术,饲料在挤压腔内膨化实际上是一个高温瞬时的过程:混和物处于高温 (110 -200 ℃ ) 、高压 (25-lOOkg / cm2) 、以及高剪切力、高水分 (10 % -20 %甚至 30 % ) 的环境中,通过连续混和、调质、升温增压、熟化、挤出模孔和骤然降压后形成一种膨松多孔的饲料。
1 膨化饲料的优点
1 .1 提高饲料的利用率膨化过程中的热、湿、压力和各种机械作用,使淀粉分子内 1 , 4 —糖苷键断裂而生成葡萄糖、麦芽糖、麦芽三糖及麦芽糊精等低分子量产物,膨化加工可使淀粉糊化度提高,纤维结构的细胞壁部分被破坏和软化,释放出部分被包围、结合的可消化物质,同时脂肪从颗粒内部渗透到表面,使饲料具有特殊的香味,提高了适口性,因而摄食率提高。
另外,植物性蛋白饲料中的蛋白质,经过适度热处理可钝化某些蛋白酶抑制剂如抗胰蛋白酶、脲酶等,并使蛋白质中的氢键和其他次级键遭到破坏,引起多肽链原有空间构象发生改变,致使蛋白质变性,变性后的蛋白质分子成纤维状,肽链伸展疏松,分子表面积增加,流动阻滞,增加了与动物体内酶的接触,因而有利于水产动物的消化吸收,可提高营养成分消化利用率10 %-35 %。
1 .
2 降低对环境的污染膨化浮性鱼饲料在水中稳定性能好。
以挤压膨化加工而成的饲料颗粒,是靠饲料内部的淀粉糊化和蛋白质组织化而使产品有一定的黏结或结合力,其稳定性一般达12h 以上,最长可达36h ,故可减少饲料营养成分在水中的溶解及沉淀损失。
有数据表明,一般采用膨化浮性鱼饲料比粉状或颗粒饲料可节约 5 %-10 %,并能避免饲料在水中残留,减少水体污染。
1 .3 减少病害的发生饲料原料中常含有害微生物,如好气性生物、嗜中性细菌、大肠杆菌、霉菌、沙门氏菌等,动物性饲料原料中的含量相对较多。
而膨化的高温、高湿、高压作用可将绝大部分有害微生物杀死。
有资料显示,每克原料中大肠杆菌数达10 000 个,膨化后仅剩不到10 个,沙门氏菌在经85 ℃以上高温膨化后,基本能被杀死,这就有助于保持水质和减少水产养殖不利的环境因素,同时降低水产动物的死亡率。
1.4提高养殖密度
在人工养殖条件下,养殖密度的提高,就意味着养殖者所得到的回报率越高。
当单位水体的养殖密度提高后,鱼类在养殖水体中的空间缩小了,对水质的要求也就要大大高于自然环境的水平。
因为使用膨化配合饲料能降低饲料系数,使排入水体中的残饵和排泄物大大降低,便有可能使养殖密度大幅度提高。
1.5延长饲料贮藏期
挤压膨化加工通过降低细菌含量和氧化作用,从而使原料稳定性提高。
挤压膨化产品干燥、冷却时,已将饲料水活性(AW)降低到0.6,甚至达到0.4,这相当于水分含量在8%~10%,更好地提高了饲料的贮存稳定性。
1 . 6 投饲管理方便水产膨化饲料能较长时间悬浮于水面 ( 水中 ) ,投饲时不需专设投饲台,只需定点投饲即可。
鱼摄食时需浮十水面,能直接观察鱼
的吃食情况,及时调整投饲量,并能及时了解鱼类的生长和健康状况。
因此,采用水产膨化饲料有助于进行科学的饲养管理,既节约大量时间,又能提;高劳动生产率。
1 .7 可以满足不同摄食习性的动物需要膨化饲料根据加工工艺的不同可分为漂浮性、缓慢沉降性、迅速沉降性 3 种类型。
目前,约80 %的鱼饲料为沉降饲料,如虾、大麻哈鱼、鲑、黄尾金枪鱼都喜欢沉降饲料,而鲇鱼、罗非鱼、鳗、大部分鱼类的幼鱼则喜欢漂浮饲料,鲇鱼、罗非鱼对沉降饲料和漂浮饲料同等喜好。
此外,膨化饲料还能满足一些特殊的要求,如低水分饲料、高纤维饲料等。
2 膨化饲料的缺点
2 .1 维生素的损失温度、压力、摩擦和水分都会导致维生素的损失。
美国学者报道,在膨化饲料中,V A 、VD ,、叶酸损失1l %,单硝酸硫铵素与盐酸硫铵素的损失率分别为11 %与17 %,VK 与VC 的损失率为50 %,而同样在硬颗粒饲料中损失则减半。
冷永智等在完全没有天然食料的条件下,用膨化料喂养鲤鱼,鱼群有少数个体出现鳃流血现象,估计与饲料加工过程中热敏维生素的破坏有关。
2 .2 酶制剂的损失酶的最适温度在35 -40 ℃,最高不超过50 ℃。
但膨化制粒过程中的温度达到120 -150 ℃,并伴有高湿( 引起饲料中较高的水分活度) 、高压( 改变酶蛋白的空间多维结构而变性) ,在这样的条件下,大多数酶制剂的活性都将损失殆尽。
据Coman 报道,未经处理的葡聚糖酶经70 ℃制粒后在饲料中的存活率仅为10 %;处理后的葡聚糖酶在料温为75 ℃时调质30s ,其存活率为64 %,而再经90 ℃的制粒其存活率仅为19 %,植酸酶经70- 90 ℃制粒后活力下降也在50 %以上。
2 .
3 微生物制剂的损失目前,饲料中应用较多的微生物制剂主要有乳酸杆菌、链球菌、酵母、芽孢杆菌等,这些微生物制剂对温度尤为敏感,当膨化制粒温度超过85 ℃时其活性将全部丧失。
2.4 蛋白质和氨基酸的损失
膨化过程中的高温使原料中的一部分还原糖与游离的氨基酸发生美拉德反应,
降低了部分蛋白质的利用率。
另外, 蛋白质在碱性条件下经过高温可形成赖氨基丙氨酸, 加热过度, 特别是在pH 值较高的情况下, 可使部分氨基酸消旋而产生D- 型氨基酸, 这都使蛋白质的消化率大幅度降低。
加热最易受损失的是赖氨酸, 其次是精氨酸和组氨酸。
采用离体研究方法, 王琳等测定了草鱼、罗莉测定了异育银鲫肠道对7 种饲料原料膨化前后的酶解动力学, 证明膨化对饲料原料的蛋
量低而淀粉含量高的饲料原料起到了积极的作用,而对蛋白质含量高的产生了不
利影响( 羽毛粉除外)。
因此, 在鱼的配合饲料中不宜将豆粕、鱼粉、肉骨粉膨化后使用。
2.5 生产成本较高
膨化饲料的工艺比一般颗粒饲料复杂、设备投入多、电耗高、产量低, 因而成本较高, 一般比颗粒饲料的成本要高20%左右。
3 对弊端的现有改良方案
3.1 改变挤压工艺条件减少蛋白质和氨基酸的损失
不同的挤压条件对蛋白质品质的影响取决于挤压过程中有效赖氨酸的损失。
当原料水分低于15%、挤压温度高于180℃时, 挤压时水分越低、温度越高, 赖氨酸的损失就越大, 蛋白质的生物学效价就越低, 降低饲料中葡萄糖、乳糖等还原糖含量、提高原料水分含量等可有效减少美拉德反应的发生。
Dahlin(1993) 等通过不同条件下对玉米、小麦、黑麦、高粱等8 种谷物的处理结果表明: 在原料水分为15%, 挤压温度为150℃, 转速为100r/min 的条件下挤压, 产品蛋白质的生物学效价与未处理原料相比得到显著提高。
3.2 利用后添加方法减少热敏性物质的损失
后添加方法通常有两种, 一种是直接将热敏性成分或含有热敏性成分的组分与饲料进行混合。
这种方法一般是将后添加成分同某些黏性胶体先均匀混合成泥状物或悬浮液, 然后再将这种混合物与颗粒饲料混合。
Kvanta(1987) 报道了可将含有少量生物活性的物质( 包括维生素、激素、酶、细菌等或其中的某一种) 结合到加工过的食
物或动物饲料中, 将含有生物活性的物质, 先与一种惰性载体混合成泥状, 这时是不可溶的, 然后形成均匀的悬浮液, 悬浮液再通过一种设备转化为一种可作用于粒料的形态, 形成均匀的一层薄膜, 覆盖于粒料的表面。
另一种是喷雾法, 该法是在高精度计量泵定量的前提下, 使添加的液态物料通过一个特殊的压力喷嘴, 喷出雾化液滴使其被饲料吸附。
Chevita(1998)发明了一种新的喷涂应用系统, 它能够同时在加工过的饲料上喷涂多达 4 种的液体或胶体添加物, 喷涂的剂量为0.1~5kg/t 饲料。
然而后添加组分集中于颗粒表面容易受外界因素, 如包装、运输、温度、光、氧气及湿度等影响, 从而导致在贮藏过程中这些组分的损失比普通料中的损失更快。
因此, 后添加采用的液体至关重要。
液体的选择除了考虑后添加组分能够均匀稳定地分散在其中外, 还需考虑其同饲料颗粒的黏结能力及受环境因子的影响大小。
另外, 亦有采用包埋、衍生化、载体吸附等手段对热敏性物质进行前处理, 以提高这些物质的热稳定性, 如果将药物等改为后添加还可以减少药物的交叉污染, 提高产品的质量, 英国的Tmuw有限公司将粉料通过一种糖浆包裹到颗粒饲料上, 不但降低颗粒饲料的粉尘污染, 还因糖浆掩盖药
为加工设备。
油脂喷涂要求物料温度在30~38℃, 这可使油脂均匀分散在饲料中, 提高饲料能量, 颗粒表面也比较光滑、匀称, 外观大为改善。
油脂的来源对膨化度的影响也不一样, 饲料原料中自身含有的油脂对膨化度的影响要小于外加的纯油脂, 因此,选择含油脂高的原料以提高饲料的油脂水平更有利于膨化饲料的生产。
4 膨化饲料的改进设想
针对膨化饲料目前存在的问题, 有人提出通过改变饲料加工工艺来提高饲料的品质, 但这种方法机械磨损大、操作不稳定、产量低、成本高。
通过上述分析可以看出, 膨化技术对含淀粉较高的饲料原料如次粉、玉米等能显著提高其可消化利用性, 而对豆粕、鱼粉等总体上降低了其可消化利用性。
其破坏抗营养因子等积极作用通过硬颗粒饲料加工技术也能解决。
因此,完全可以设想将膨化技术和硬颗粒饲料加工技术进行嫁接, 只对次粉、玉米等适合膨化的原料进行膨化, 也可以通过购买得到, 然后和不适合膨化的原料混合, 用硬颗粒饲料加工机组加工,这样, 就可以尽可能地扬长避短, 充分发挥饲料效率, 同时也能大大降低饲料加工成本。