瓦楞纸质量不良现象及原因
瓦楞纸板不良原因分析

瓦楞纸板不良原因分析瓦楞纸板是由瓦楞纸板芯和面纸组成的一种多层结构材料。
它主要用于包装和运输行业,承载能力强,便于加工和加工。
然而,在实际生产和使用过程中,我们经常会遇到各种瓦楞纸板的不良问题,这直接影响了其使用效果和质量。
以下是对瓦楞纸板不良原因进行分析的一些常见问题。
1.压痕和划痕:瓦楞纸板在生产过程中可能会出现压痕和划痕的问题。
这可能是由于设备不当调整或操作不规范导致的。
例如,如果压痕辊的间距不正确,或者生产速度过快,纸板受到了太大的力,就会出现压痕。
而划痕则可能是由于切割工具不锋利或切割速度过快而导致的。
2.破裂和撕裂:瓦楞纸板在运输和使用过程中容易出现破裂和撕裂的问题。
这可能是由于纸板的强度不足造成的,可能是由于纸板芯的纸张质量不好,或者纸张的厚度不足。
此外,如果瓦楞纸板在存储或运输过程中受到了湿气或温度变化的影响,也会导致纸板的强度减小,容易发生破裂和撕裂。
3.潞水和水印:潞水是指瓦楞纸板表面出现水印痕迹,给纸板的外观质量带来影响。
潞水可能是由于纸张表面平整度不好,或者纸张吸水性能不佳导致的。
此外,如果生产过程中的湿度控制不当,或者纸板表面存在杂质或污染物,也会导致潞水问题的出现。
4.尺寸不一致:瓦楞纸板的尺寸一致性是其质量的重要指标之一、如果纸板的尺寸不一致,可能会导致包装箱的组合困难,影响使用效果。
尺寸不一致的原因可能是由于生产过程中的设备调整不准确或操作不规范,或者纸板芯的厚度不一致,造成纸板的尺寸差异。
5.外观缺陷:瓦楞纸板的外观缺陷可能是指纸板芯表面的起泡、蜂窝状,或者面纸的褶皱、异常颜色等问题。
这些缺陷可能是由于纸张质量不佳、生产过程中的设备故障或不良操作导致的。
例如,如果纸张含水量不均匀,或者设备温度过高,就会导致瓦楞纸板表面起泡或蜂窝状。
综上所述,瓦楞纸板的不良问题可能是由于生产过程中的设备故障、操作不良、纸张质量不佳等因素导致的。
为了解决这些问题,生产厂家应该加强对设备的维护和调整,确保操作人员的培训和规范。
瓦楞纸板不良原因分析

瓦楞纸板不良原因分析瓦楞纸板是一种由多层纸板互相粘合而成的材料,具有良好的抗压性能和缓冲性能,广泛应用于各个行业的包装中。
然而,在生产和使用过程中,瓦楞纸板可能会出现一些不良现象,影响其使用效果和寿命。
下面将分析一些可能导致瓦楞纸板不良的原因。
1.原材料质量不良:瓦楞纸板的质量主要受原材料的影响,如果原材料质量不好,会直接影响到瓦楞纸板的质量。
比如,纸张的纤维长度不足、杂质过多、含湿率过高等都会导致瓦楞纸板的强度下降和易碎性增加。
2.生产过程不规范:瓦楞纸板的生产过程包括纸张的加工、糊合、干燥等环节,如果操作不规范或控制不当,会导致质量不良。
比如,糊合时糊胶的浓度不合适、温度控制不好、糊胶的均匀性不好等都会影响瓦楞纸板的强度和质量稳定性。
3.设备老化或损坏:生产瓦楞纸板需要使用一系列的设备,如纸张预处理机、糊合机、干燥机等。
如果这些设备老化或损坏,就会影响生产过程的正常进行,进而导致瓦楞纸板的质量下降。
4.储存条件不好:瓦楞纸板在生产出来后需要进行储存,如果储存条件不好,比如温度过高或者潮湿,会导致纸张变形、发霉,进而影响瓦楞纸板的强度和质量。
5.运输和包装不当:瓦楞纸板在运输和包装过程中也容易遭受挤压、湿泡等不良影响,特别是在长途运输或者储存时间较长的情况下,容易出现不均匀应力分布,导致瓦楞纸板强度下降或出现划痕、弯曲等问题。
6.设计不合理:瓦楞纸板在使用过程中有时受到外力的作用,特别是在堆叠、挤压等情况下,如果设计不合理,纸板可能容易变形、产生断裂、划痕等不良现象。
综上所述,瓦楞纸板不良的原因多种多样,涉及到原材料、生产过程、设备、储存和运输等多个方面。
为了提高瓦楞纸板的质量,减少不良现象的发生,需要从原材料的选择和质量控制、生产过程的改善和规范、设备的维护和更新、储存和运输条件的优化以及设计的合理性等方面进行改进和管理。
只有全面有效地把控这些方面,才能保证瓦楞纸板的质量和可靠性,满足各个行业对包装的需求。
瓦楞纸板各种常见纸病的解决方案
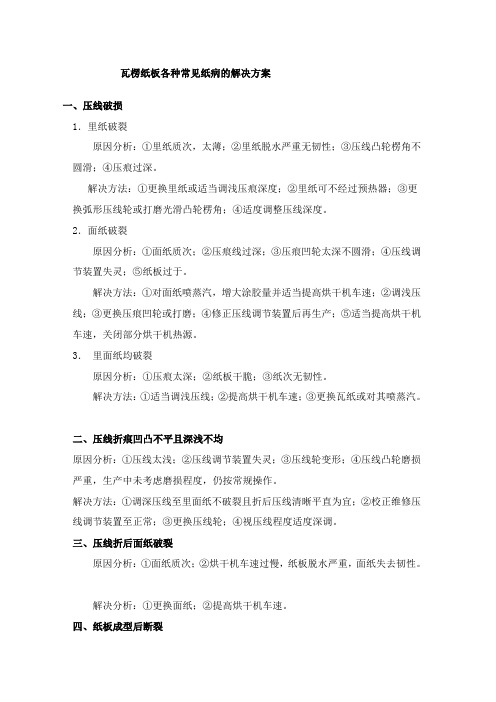
瓦楞纸板各种常见纸病的解决方案一、压线破损1.里纸破裂原因分析:①里纸质次,太薄;②里纸脱水严重无韧性;③压线凸轮楞角不圆滑;④压痕过深。
解决方法:①更换里纸或适当调浅压痕深度;②里纸可不经过预热器;③更换弧形压线轮或打磨光滑凸轮楞角;④适度调整压线深度。
2.面纸破裂原因分析:①面纸质次;②压痕线过深;③压痕凹轮太深不圆滑;④压线调节装置失灵;⑤纸板过于。
解决方法:①对面纸喷蒸汽,增大涂胶量并适当提高烘干机车速;②调浅压线;③更换压痕凹轮或打磨;④修正压线调节装置后再生产;⑤适当提高烘干机车速,关闭部分烘干机热源。
3.里面纸均破裂原因分析:①压痕太深;②纸板干脆;③纸次无韧性。
解决方法:①适当调浅压线;②提高烘干机车速;③更换瓦纸或对其喷蒸汽。
二、压线折痕凹凸不平且深浅不均原因分析:①压线太浅;②压线调节装置失灵;③压线轮变形;④压线凸轮磨损严重,生产中未考虑磨损程度,仍按常规操作。
解决方法:①调深压线至里面纸不破裂且折后压线清晰平直为宜;②校正维修压线调节装置至正常;③更换压线轮;④视压线程度适度深调。
三、压线折后面纸破裂原因分析:①面纸质次;②烘干机车速过慢,纸板脱水严重,面纸失去韧性。
解决分析:①更换面纸;②提高烘干机车速。
四、纸板成型后断裂原因分析:①瓦纸质次;②纸板过分干燥;③成型工序设备调节不当;④压线太浅,瓦楞未压扁或成型后折叠摇盖时高强瓦楞将面纸撑破,瓦楞随之断裂。
解决方法:①更换瓦纸;②保证纸板含水量在10±3左右;③注意成形各工序的设备调节并调至最佳状态;④烘干机加速并加大涂胶量,压线调深。
五、纵切毛边原因分析:①分纸刀已钝或刀刃有缺口;②上下刀咬合过深;③上下刀之间有间隙。
解决方法:①打磨或更换新刀;②调节上下刀重合至最佳状态;③将上下两刀靠紧,用手转动刀轮,灵活不伤刀为宜。
六、横切纸板拖尾原因分析:①横刀已钝;②横切刀上下两片咬合不正,纸板切不断的部位在机械力作用下带起撕裂的面瓦纸;③横切机瞬时加速调节不当,引起阻纸。
瓦楞纸板常见质量问题和产生原因及解决办法

修正瓦楞辊的贴合间隙 清理瓦楞表面异物
瓦楞辊贴合间隙大
• 修正瓦楞辊的贴合间隙
瓦画辊贴合间隙不平衡 •
导纸板位置不正、磨损或带
脏
瓦楞原纸含水水均衡
•
瓦楞原纸的张力太小
•
检查并修正或更换导纸 板
加大予热包角 适当调整张力控制
瓦楞纸板常见质量问题和产生原因及 解决办法
质量问题
平行度
• 瓦楞辊表面带脏
• 清理瓦楞辊,保持干净
• 导纸板位置不正,、带脏或磨损 • 检查、修正、清理或更换导
纸板
• 涂胶辊、浮动辊间隙不当
• 调整二者的贴合间隙
• 粘合剂质量不好
• 检查并重新制作粘合剂
• 瓦楞原纸含水不均衡张力小 • 适当予热并加大张力控制
• 过纸天桥张力不均衡
瓦楞纸板常见质量问题和产生原因及 解决办法
1. 面纸予热包角太大 2. 里纸予热包角太小 3. 过纸天桥堆积过多 4. 单面机涂胶量过大
5.涂胶仙涂胶量偏少
6.车速太低
7.双面机热板温度高
8.重量辊施加压力过大
解决办法
• 减少包角、降低予热 • 增大包角、加强予热 • 减少过纸天桥的堆积 • 适当控制单面机的着胶
量 • 适当增大涂胶机的着胶
7.双面机热板温度高 8.重量辊施加压力过大
解决办法
• 减少包角、降低予热
• 增大包角、加强予热 • 减少过纸天桥的堆积 • 适当控制单面机的着胶
量 • 适当增大涂胶机的着胶
量 • 根据实际运行质量,适
当提高车速
• 提高车速或人为降低热 板
• 适当投放重量辊
PPT文档演模板
瓦楞纸板常见质量问题和产生原因及 解决办法
瓦楞纸板搓板状及粘合不良的解决方案

瓦楞纸板搓板状及粘合不良的解决方案世界瓦楞纸板市场以每年2.8%的速度增长,预计到2010年,市场需求量将达1.25亿吨。
中国加入WTO以后,包装纸板行业应主动迎接挑战。
我国大部分的纸板企业市场主要在国内,从国内范围来看,纸板的需求呈自给自足的状态,将市场从国内向国外拓展已成为一个方向。
在此方向下,质量是企业要抓的首要问题,纸板质量是由多方面因素造成的。
如:板搓板状现象、纸板翘曲不平、抗戳穿强度不达要求等问题。
有些问题较直观,有些则隐蔽复杂。
因为有些问题的影响因素往往并存,互相牵制交织在一起。
这就需要对有些质量问题进行理论研究。
1瓦楞纸板搓板状现象的研究及对策瓦楞纸板是由夹芯纸、芯纸和面纸、底纸组合而成的。
原纸质量的好坏,对于瓦楞纸板成型质量起着举足轻重的作用。
作为纸箱生产厂不仅应选购合格的原纸,还应在生产中观察不同的生产情形,随时加以控制调节,否则仍会出现因生产控制不当导致纸板搓板状等质量问题。
1.1原纸含水量的影响当纸板出现搓板状现象时,一般首先考虑到的是,操作工是否按要求去调节好各个关键点的主要参数。
如:纸板的张力控制、单面机上蒸汽喷雾对瓦楞纸的干湿程度调节与控制等问题。
而往往忽略了很重要的因素——原纸的含水率。
常常以为含水率略高或略低都无大碍,只要原纸能上机生产,不致出现纸板脱胶就行了。
其实不然,由于纸张的伸缩率问题在很大程度上取决于纸张本身所含水分的高低。
就合格的原纸而言,瓦楞纸必须严格控制在(8±2)%之间。
箱板纸控制在(9±2)%之间。
过高的含水率必将使纸张纤维因过度吸入水分而膨胀伸长;而过低的含水率又不利于纸张的粘合与成型,这一点在使用低定量原纸上特别明显。
由于低定量的瓦楞纸板具有质轻价低的优点,在目前面临国际性纸浆行情不断上涨的今天,正备受广大纸箱生产商的倡导和推广。
然而由于原纸定量偏低,纸张偏薄,给瓦楞纸板的制造带来一定难度。
往往会因为生产调节不当而造成纸板表面呈搓板状或起泡。
瓦楞纸板及印刷不良问题产生的原因及解决办法(PPT54页)

二
双面机加热板温度不够
部
车速太快
分
脱
原纸含水量太高
胶
胶黏剂质量不好
胶黏剂附着量小
解决办法
检查冷凝水排放装置和 供水气压是否符合要求 检查供气部分是否有故障
适当降低车速 加大预热或换纸
修正胶黏剂质量 加大胶黏剂附着量
产生原因
单面机涂胶量过小
涂胶机涂胶量过大
一
双面机加热温度不够
横
向
面纸预热包角太小 、里纸预热包角太大
原因
滚筒压力不足 墨层太厚
油墨黏度太高
解决办法
适量调高滚筒之间的压力 调薄墨层
适当稀释油墨
四 印面油 墨粉化 ,摩擦 后容易 脱落, 墨色浑 浊
原因
油墨过稀 油墨变质
解决办法
减少稀释溶剂,增加油墨浓度 给油墨增添树脂剂量,增强 油墨黏性和粘接附着性能
换掉变质的油墨
原因
五
印
印版上有旧墨堆积
上
翘
输送桥架纸板过多堆积
输送桥架输出瓦 楞纸板张力过大
解决办法
适当加大张力系 统的控制力度
适当预热 检查、修整传动装 置,保证运转正常
减少堆积量
适当减少纸板输出张力控制
产生原因
传送带运行压力不够
四
纵
输送桥架输出瓦 楞纸板张力不够
向
向
下
面纸含水量不均衡
翘
面纸张力太大
解决办法
适当加大张力系 统的控制力度
调整前色干燥速度、尽 量在后一色印刷前干燥
问题
供墨系统清洁不彻底
七 墨 杠
水墨本身含有未完 全溶解的颜料颗粒
解决办法
更换产品时将供墨系统彻底 清洁干净,注意避免前后两 种产品颜色相差很远且使用 同一印刷色组的大面积印刷
瓦楞纸板脱胶原因及改善措施
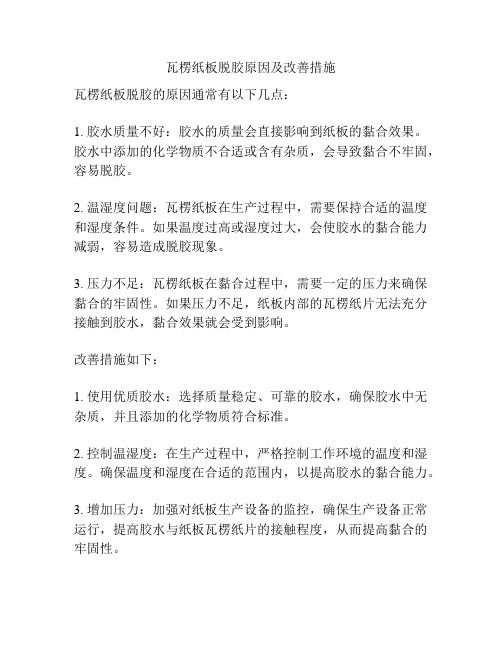
瓦楞纸板脱胶原因及改善措施
瓦楞纸板脱胶的原因通常有以下几点:
1. 胶水质量不好:胶水的质量会直接影响到纸板的黏合效果。
胶水中添加的化学物质不合适或含有杂质,会导致黏合不牢固,容易脱胶。
2. 温湿度问题:瓦楞纸板在生产过程中,需要保持合适的温度和湿度条件。
如果温度过高或湿度过大,会使胶水的黏合能力减弱,容易造成脱胶现象。
3. 压力不足:瓦楞纸板在黏合过程中,需要一定的压力来确保黏合的牢固性。
如果压力不足,纸板内部的瓦楞纸片无法充分接触到胶水,黏合效果就会受到影响。
改善措施如下:
1. 使用优质胶水:选择质量稳定、可靠的胶水,确保胶水中无杂质,并且添加的化学物质符合标准。
2. 控制温湿度:在生产过程中,严格控制工作环境的温度和湿度。
确保温度和湿度在合适的范围内,以提高胶水的黏合能力。
3. 增加压力:加强对纸板生产设备的监控,确保生产设备正常运行,提高胶水与纸板瓦楞纸片的接触程度,从而提高黏合的牢固性。
4. 定期检查和维护设备:对生产设备进行定期维护和检查,确保设备运行正常,避免设备问题导致黏合不牢固。
5. 加强员工培训:提高生产操作人员的技术水平和质量意识,确保生产过程中的操作规范,减少操作失误和质量问题的发生。
瓦楞纸箱缺陷及产生原因

5
1
原纸 原纸纸色差异
5
1
1
1:水墨上机时混进太 多水,成膜效果差 2:送出的水墨粘度 低,成膜效果差
1:水墨上机时操作员准确判定水排干 净后才将水墨进入循环 2:加新墨提高粘度
5
1:水墨快干度没有按 需要调整
1:按季节调整水墨干燥速度: 2:生产时按需要在机上调整 3:调整生产速度改善
1:趁纸板热时生产,提高水墨干燥速
制作色卡严格按标准色对照,符合要求 才可使用
印刷 样箱保存不当
5
3
印刷 油墨号错误
5
0
1:样箱未避光保存
1:不用样箱用色卡 2:样箱避光保存
0
1:未认真对照号码拿 1:按指定的标准颜色号码对照取
墨
墨:2:首检对色
检测 设备
检测光源问题
5
0
色差
印刷 印刷速度不适合 5
1
0 1:非标准光源
用标准光源
1:印刷时速度不稳 1:用稳定速度和固定粘度生产
油墨原因
1
0
0
印刷
纸屑、灰尘等异 物
1
6
6
1:纸板线横切刀及飞 边刀不利产生纸尘 2: 纸板边沿有纸屑 3:没有及时擦版
1:定期检查和保养横切刀及飞边刀 2:生产纸板时发现纸屑多影响印刷, 通知磨刀或换刀. 3:印刷机生产时发现纸屑及时擦板
露白
缺墨
1
1
1:水墨管堵塞上不上
墨
1:停机及时清洗管道,定期清理水墨
时调整水墨
首检
1:操作员未按标准要
印刷
调机不良品未剔 除
5
3
15
求隔离调机品 2:操作员没有养成规
- 1、下载文档前请自行甄别文档内容的完整性,平台不提供额外的编辑、内容补充、找答案等附加服务。
- 2、"仅部分预览"的文档,不可在线预览部分如存在完整性等问题,可反馈申请退款(可完整预览的文档不适用该条件!)。
- 3、如文档侵犯您的权益,请联系客服反馈,我们会尽快为您处理(人工客服工作时间:9:00-18:30)。
瓦楞纸质量不良现象及原因
露楞:指在纸面上能明显看见坑纹的楞高。
一般厂家生产的纸板的底纸均有露楞现象,此属正常,但露楞不能超过3mm且面纸不得露楞缺材:指纸板的宽度不够。
引起缺材的原因可能是原纸不足度,原纸经加热后缩水,错边(也叫纸边不齐),引起这些原因是可能驳纸未对齐,纸架走位,原纸筒端面不平整。
此外,还与面纸,底纸,见坑纸在运行中的张紧度有关。
露坑:指纸面上能明显看见坑纹,由面纸或底纸缺材引起。
塌楞:指坑纸的峰楞受到超过其承受能力的压力而被压塌。
引起塌楞的原因可能是坑机运转,调机不正常(原则上每天应试机),双面机内有杂物也与见坑纸所受的压力大小有关(如浆糊轮压不到位可压辊不平衡)。
脱坑:指纸板的各层纸黏合不良。
检验脱坑的方法有三种:(1)将纸板长度的一边靠近地面约成60度,用手掌在纸面上推动;(2)拿住纸板幅宽的两边,用适当的力向中间挤压;(3)剥离法,如黏合处的纸张纤维未受到破坏,则说明纸黏合不良。
脱坑产生的原因可能是施胶量小,异物阻塞浆糊管道,浆位调试不当,浆糊黏度较小,受热时间与温度不合要求;纸板胀缩比例悬殊;面纸,底纸,见坑纸受压不当。
起泡:一般出现在面纸或底纸,原因有以下几个方面:(1)原纸所含水分大;(2)原纸的质量差(厚度不均,杂质较多);(3)施胶量不合要求;(4)浆糊水分蒸发慢,在纸板内形成空膜;(5)温度控制不
当,主要为热板;(6)压力不当,如浆糊轮压不到位。
油污,斑点:纸板内外不得有油污,面纸不得有斑点
破损:纸板中间不能破损,纸板边沿破损以不影响外观为准。
折皱:指纸板面纸或底纸有明显皱纹,引起原因是以下几个方面:(1)原纸来料折皱;(2)生产中未将纸面舒张舒张平整;(3)张力控制器没有控制好面纸与底纸的张紧度;(4)面纸与底纸的张紧不协调
弯曲:弯曲度是指纸板弯曲后水平面之间的最高高度与纸板方向的长度的百分比,分为横向弯曲(坑纹方向)和纵向弯曲(纸板长度方向)两种,一般横向弯曲情况比较多。
原因有以下几个方面:(1)水分(构成纸板的各层原料的含水量或浆糊中的含水量及施胶量);(2)张力;(3)面,底,支架上的控制器的张力调试;(4)原纸的热胀冷缩跟纸板各层纸产生的热胀冷缩比例失衡;(5)预热器,加热辊等。
硬度:纸板硬度主要由组成纸板的各层原纸的硬度(特别是坑纸的硬度)决定它受坑机以及楞型的影响。
色差:指同一款纸板的面纸或底纸有明显色差。