过程控制和过程能力
控制图与过程能力

控制图与过程能力控制图与过程能力控制图是一种统计工具,用于检测过程是否稳定,并通过监控过程中的变异性来实现过程的稳定控制。
过程能力则用来评估过程的稳定性及其是否满足规定的要求。
在质量管理中,控制图和过程能力是常用的管理工具,可以帮助企业分析和改进生产过程,提高产品质量。
首先,控制图是由过程数据统计而得出的,其核心思想是通过收集并分析过程数据,判断过程是否处于可控状态,从而及时发现问题,采取相应的纠正措施。
控制图通常由中心线、控制限和数据点构成。
中心线表示过程数据的平均值,控制限则表示过程数据的变异性,通常分为控制上限和控制下限。
数据点则是通过统计过程数据得出的。
控制图可分为平均控制图和范围控制图两种。
平均控制图主要用于分析过程的平均水平是否稳定,常用的平均控制图有均值图和移动平均图。
均值图通过比较样本平均值与中心线的差异来判断过程的稳定性;移动平均图则将样本平均数按照一定的周期进行平均,从而降低随机变异的影响。
范围控制图主要用于分析过程的变异性是否稳定,常用的范围控制图有范围图和标准差图。
范围图通过比较样本范围与控制限的差异来判断过程的稳定性;标准差图则是将样本标准差按照一定的周期进行计算,从而判断过程的稳定性。
控制图的构建需要确定样本的大小和采样间隔,样本的大小一般取决于过程的稳定性和潜在的变异性,采样间隔则取决于对过程的监控程度。
通过不断地收集和分析过程数据,可以根据实际情况进行调整和改进。
过程能力则是对过程进行综合评价的指标,用于衡量过程的稳定性和能够满足规定要求的能力。
过程能力通常由过程能力指数(Cp)和过程能力指数偏差(Cpk)来表示。
Cp表示过程的能力指数,计算公式为 Cp = (USL-LSL)/(6σ),其中USL和LSL分别为规定的上限和下限,σ为过程的标准差。
Cpk表示过程能力指数偏差,表示过程确保产品能够满足要求的能力。
过程能力的评估通常需要先确定经验指标和相关标准。
常用的经验指标有6σ、4σ和3σ,表示过程的准确性和精度。
过程能力控制
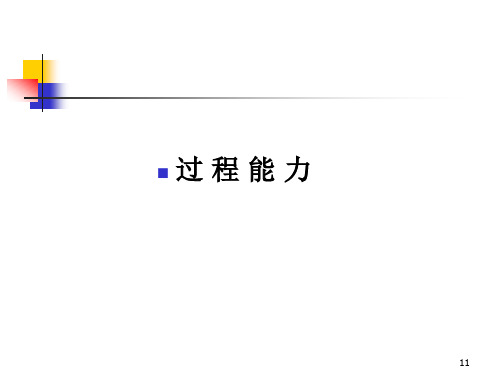
ppk
Ppk 的计算公式和cpk的一样,只是ó 值不一样
201
Ppk和Cpk的联合应用
一般情况下,ppk ≤cpk,但如果ppk远远 小于cpk时,说明实际的过程能力低于固有的 能力,过程没有达到稳态,过程中异常坏的特 殊因素,应该马上寻找原因,加以消除,把过 程绩效指数提高到过程能力指数的水平。 当ppk远远大于cpk时,说明实际的过程 能力高于过程的固有能力,说明有异常好的特 殊因素存在。应该将这种异常好的特殊因素找 到,并将它纳入作业指导书,以大幅度提高过 程能力指数
131
制程能力指数CpK :
CpK
1.33≤CpK 1.00≤CpK<1.33 0.67≤CpK<1.00 CpK <0.67
偏离度K(%)
︱K︱≤12.5 12.5<︱K︱≤25 25<︱K︱≤50 50<︱K︱
建议的措施
不必调整 密切关注,必要 时采取措施 应予以调整 采取纠正措施或 停止生产
31
3、过程能力的作用:
1)掌握生产过程中的质量水 平,预防不合格品的产生; 2)为制定标准、进行质量分 析提供依据。
41
4、过程能力的用途:
1)向领导汇报质量情况; 2)在QC小组活动中用于课 题选择、现状调查、原因分 析等。
51
二、过程能力应用的程序
141
制程能力指数CpK :单边规格
没有规格下限:Cp=CpU=CpK 没有规格上限:Cp=CpL=CpK
151Leabharlann 过程绩效(process performance): 定义: 是从过程总波动的角度反应过程的实际加工能 力,此时不需要考虑过程是否受控,也不要求 过程输出的质量特性一定要服从某个正态分布。 如果说过程能力反映的是过程的固有属性, 那么过程绩效反映的就是过程的实际属性。 过程绩效是过程的总变差O的6倍,即pp=6o. O通常用所有测量值计算出来的标准差s来估计。
统计过程控制(SPC)之过程控制过程能力过程性能和过程指数

统计过程控制(SPC)之过程控制过程能⼒过程性能和过程指数
统计过程控制(SPC)之过程控制/过程能⼒/过程性能和过程指数定义/说明/要求/⽬的:
能⼒是指:⼀个稳定过程中固有变差的总范围。
过程控制是指:分析某⼀过程或其输出,以便采取适当的措施来达到⼀种统计受控的状态,这种控制是对过程进⾏的控制,⽽不是事后的⾏为。
过程能⼒是指:⼀个稳定过程固有的变差的总范围,⼀般为过程固有变差的6?σ范围;对于计量型σ,对于计数型数据,通常为不合格品或不合格的平均⽐例或⽐率。
数据,其被定义为6?
c
过程能⼒指数是指:过程能⼒满⾜产品质量标准要求(规格范围等)的程度。
分布是指:描述具有稳定系统变差的⼀种输出⽅式,其中单个值是不可预测的,但⼀组单值就可形成⼀种图形,并可⽤位置、分布宽度和形状这些术语来描述。
过程控制系统的⽬的是对过程当前和将来的状态作出预测,以便对影响过程的措施做出经济合理的决定。
采⽤的总体标准差的估计⽅法的不同导致过程能⼒和过程性能之间的不同。
理解过程控制/过程能⼒/过程性能和过程指数才能最终⽐较“过程的声⾳”和“顾客的声⾳”。
检查表:。
SPC基本知识

受控
不受控
可接受
1类
3类
不可接受
2类
4类
2类过程虽然受控,但因为普通原因造成过大的变差而不能满足规范要求。
3类过程可接受,但存在变差的特殊原因,一般情况下要设法找出原因并消除之。
4类过程既不受控,又不可接受。应减少变差的普通原因和特殊原因。
在某些情况下,顾客允许3类过程运行。例如特殊原因已查明,具有一定的稳定性,采取措施所发生的成本比顾客获得的利益大等。
3.四类过程
过程能力与规范无关。顾客更关心的是过程的输出是否满足规范的要求。满足则可接受,否则不可接受。(关于能力与规范的关系可以用能力指数描述,以后再介绍)。
过程是否受控和是否满足规范要求是两个不同的问题。下面将过程按此分成4类(见表3-1):
1类过程是理想的,它受控且满足
规范要求。
表3-1
是否受控
二、收集数据
1.选择子组容量、频率、子组数
合理子组的确定将决定控制图的效果
①在 -R控制图中,子组的容量是恒定的。在过程研究初期n取4~5,通常取2~5件连续生产的产品。这样的子组反映的是在很短时间内、非常相似的生产条件下生产出来的产品,因此,子组内的变差主要应是普通原因造成的。这些条件不满足,就不能有效地区分出变差的特殊原因。
2.计量型数据控制图分类
表3-2列出计量型数据控制图的种类及其应用范围。
表3-2
类型
优点
应用
均值-极差图 -R
较简便,对子组内特殊原因较敏感
广泛
均值-标准差图 -S
S较R更准确有效,尤其在大样本容量时
计算机实时记录样本容量大
中位数图 -R
用 代替 ,直接描点,不用计算,最为简便
过程能力
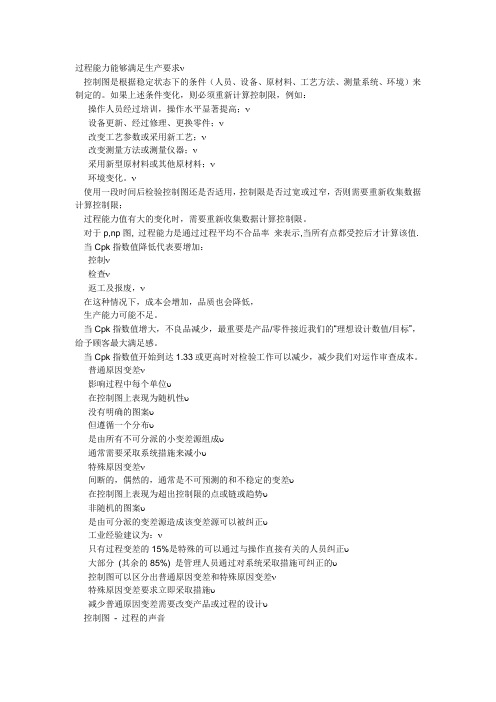
过程能力能够满足生产要求ν控制图是根据稳定状态下的条件(人员、设备、原材料、工艺方法、测量系统、环境)来制定的。
如果上述条件变化,则必须重新计算控制限,例如:操作人员经过培训,操作水平显著提高;ν设备更新、经过修理、更换零件;ν改变工艺参数或采用新工艺;ν改变测量方法或测量仪器;ν采用新型原材料或其他原材料;ν环境变化。
ν使用一段时间后检验控制图还是否适用,控制限是否过宽或过窄,否则需要重新收集数据计算控制限;过程能力值有大的变化时,需要重新收集数据计算控制限。
对于p,np图, 过程能力是通过过程平均不合品率来表示,当所有点都受控后才计算该值. 当Cpk指数值降低代表要增加:控制ν检查ν返工及报废,ν在这种情况下,成本会增加,品质也会降低,生产能力可能不足。
当Cpk指数值增大,不良品减少,最重要是产品/零件接近我们的“理想设计数值/目标”,给予顾客最大满足感。
当Cpk指数值开始到达1.33或更高时对检验工作可以减少,减少我们对运作审查成本。
普通原因变差ν影响过程中每个单位υ在控制图上表现为随机性υ没有明确的图案υ但遵循一个分布υ是由所有不可分派的小变差源组成υ通常需要采取系统措施来减小υ特殊原因变差ν间断的,偶然的,通常是不可预测的和不稳定的变差υ在控制图上表现为超出控制限的点或链或趋势υ非随机的图案υ是由可分派的变差源造成该变差源可以被纠正υ工业经验建议为:ν只有过程变差的15%是特殊的可以通过与操作直接有关的人员纠正υ大部分(其余的85%) 是管理人员通过对系统采取措施可纠正的υ控制图可以区分出普通原因变差和特殊原因变差ν特殊原因变差要求立即采取措施υ减少普通原因变差需要改变产品或过程的设计υ控制图- 过程的声音试图通过持续调整过程参数来固定住普通原因变差,称为过度调整,结果会导致更大的过程变差造成客户满意度下降υ试图通过改变设计来减小特殊原因变差可能解决不了问题,会造成时间和金钱的浪费υ控制图可以给我们提供出出现了哪种类型的变差的线索,供我们采取相应的措施υ能力指数的计算基于以下假设条件:ν过程处于统计稳定状态υ每个测量单值遵循正态分布υ规格的上、下限是基于客户的要求υ测量系统能力充分υ如果理解关满足了这些假设后,能力指数的数值越大,潜在的客户满意度越高ν过程能力分析的用途-设计部门可参考目前之制程能力,以设计出可制造的产品-评估人员、设备、材料与工作方法的适当性-根据规格公差设定设备的管制界限-决定最经济的作业方式过程控制和过程能力◎目标:过程控制系统目标,是对影响过程的措施作出经济合理的决定, 避免过度控制与控制不足◎过程能力讨论:必需注意二个观念○由造成变差的普通原因来确定○内外部顾客开心过程的输出及与他们的要求的关系如何。
5 过程控制与过程能力

• 假定为了控制螺丝的质量,每隔一个小时随机抽取1个车 假定为了控制螺丝的质量,每隔一个小时随机抽取1 好的螺丝,测量其直径,将结果描点画图如下(共取了4 好的螺丝,测量其直径,将结果描点画图如下(共取了4个 螺丝): 螺丝):
直 径
3σ 均值 3σ
为什么会出现 超出的现象呢? 超出的现象呢? 可能的原因: 可能的原因: 过程正常, A:过程正常,点出限 的概率为1‰左右; 1‰左右 的概率为1‰左右; B:车刀磨损,点出限 车刀磨损, 的概率是1‰的几十倍 的概率是1‰的几十倍 1‰ 甚至是几百倍。 甚至是几百倍。 您更相信那种原因? 您更相信那种原因?
变异是产品和过程的固有特性 过程和产品的变异是有统计规律性的
变异的分类及质量管理对策 变异 分类
随机变异/普通原因 随机变异/ 异常变异/特殊原因 异常变异/
对策
运用 质量改进 技术降低 再降低
运用 SPC控制 控制 技术及时 发现并纠正
常用的质量管理工具,包括直方图,鱼刺图,散布图, 常用的质量管理工具,包括直方图,鱼刺图,散布图, 抽样等等都是对“过去”情况的分析和解释。 抽样等等都是对“过去”情况的分析和解释。
普通原因: 普通原因:
• • • • • • • 打字过程中手的动作的变化; 打字过程中手的动作的变化; 打字过程中的心理变化; 打字过程中的心理变化; 被录入文字的变化; 被录入文字的变化; 某个时间突然身体不适; 某个时间突然身体不适; 环境温度的突然变化; 环境温度的突然变化; 某个时间稍事休息或喝水; 某个时间稍事休息或喝水; 在某个时间间断打字如接电话, 在某个时间间断打字如接电话,复印文件等
控制图与过程能力分析

控制图与过程能力分析控制图是一种用于监控过程稳定性和一致性的工具,它通过监控产品或过程的变异性来确保产品质量以及生产效率。
在工业生产中,控制图被广泛应用于监控制造过程中的变异性,以便及时发现和纠正问题,从而确保产品的稳定性和一致性。
与此同时,过程能力分析则是用于评估制造过程的稳定性和一致性的工具,它可以帮助企业确定其生产过程是否能够满足产品质量要求。
因此,控制图与过程能力分析在生产管理中扮演着至关重要的角色。
控制图的原理和类型控制图是一种通过统计方法来监控过程稳定性的工具,它可以帮助生产者及时发现和纠正生产过程中的问题。
控制图的原理是将生产过程中的数据进行分类,然后根据统计学方法对数据进行分析,以便确定过程是否处于稳定状态。
控制图的基本原理是将数据按照时间顺序绘制在图表上,并根据统计学规则来判断生产过程的稳定性。
常见的控制图类型包括X-bar图、R 图、P图和C图等,每种类型的控制图都有着不同的应用范围和适用条件。
X-bar图是一种用于监控过程平均值的控制图,它可以帮助生产者了解生产过程的变异情况。
R图则是用于监控过程变异性的控制图,它可以帮助生产者了解生产过程的一致性。
P图和C图则是用于监控不合格品率的控制图,它们可以帮助生产者了解生产过程的品质情况。
通过绘制这些不同类型的控制图,生产者可以全面了解生产过程的稳定性和一致性,从而及时发现和纠正生产过程中的问题。
过程能力分析的原理和方法过程能力分析是一种用于评估生产过程稳定性和一致性的工具,它可以帮助企业确定其生产过程是否能够满足产品质量要求。
过程能力分析的原理是通过统计方法对生产过程的数据进行分析,以便评估过程的稳定性和一致性。
常见的过程能力指标包括过程能力指数(Cp)、过程能力指数(Cpk)以及过程性能指数(Pp)和过程性能指数(Ppk)等,它们可以帮助企业全面了解生产过程的稳定性和一致性。
通过计算这些过程能力指标,企业可以全面了解生产过程的稳定性和一致性,从而确定生产过程是否能够满足产品质量要求。
过程能力指数分析

长期过程能力。是指由偶因和异因之和所引起的总
变异,它实际上反映了“长期”变异,也称实绩变
异。
二、过程能力指数
1.过程能力指数
定义:表示过程能力满足过程质量标准要求程度的量 值。过程质量要求的范围(公差)和过程能力的比值。
公式:
无偏时双向公差过程能力指数计算
Pp与Ppk
美国三大汽车公司(福特、通用、克 莱斯勒)在QS9000标准中对于统计 方法的应用提出的更高要求。 称为过程性能指数,过程实绩指数或 者长期过程能力指数。 它反映的是生产系统当前实际状况的 过程能力,而不是在稳态的条件下。
Pp与Ppk的比较
PpK min( PpU , PPL ) PpK (1 K ) Pp ˆ ST PPK C pK ˆ LT
p pU pL 2 [3Cp (1 K )] [3Cp (1 K )]
当K较大时, PL接近于零,可略去,故
p pU 1 [3C p (1 K )]
当分布中心向规范下限TL偏移时
同理可求得:
p pU pL 2 [3Cp (1 K )] [3Cp (1 K )]
举例
例1:某零件的屈服强度界限界限设计要求为 480-520MPa,从100个样品中测得样本标准 差(S)为6.2MPa,求过程能力指数。 解:当过程处于稳定状态,而样本大小n=100 也足够大时,可以用S估计 的过程能力指数
520 480 Cp 1.075 6 6.2
同理
T TL ( ) X TL 2 ] PL P[ X TL ] P[ ] P[Z T (1 k ) P[ Z 2 ] P[ Z 3C p (1 K )] [3C p (1 K )]
- 1、下载文档前请自行甄别文档内容的完整性,平台不提供额外的编辑、内容补充、找答案等附加服务。
- 2、"仅部分预览"的文档,不可在线预览部分如存在完整性等问题,可反馈申请退款(可完整预览的文档不适用该条件!)。
- 3、如文档侵犯您的权益,请联系客服反馈,我们会尽快为您处理(人工客服工作时间:9:00-18:30)。
过程控制和过程能力
过程控制系统的目标是对影响过程的措施作出经济合理的决定。
也就是说,平衡不需控制时采取了措施(过度控制或擅自改变)和需要控制时未采取措施(控制不足)的后果。
必须前面提到的变差的两种原因——特殊原因和普通原因的关系下处理好这些风险。
(见图3)过程在统控制下运行指的是仅存在造成变差的普通原因。
这样,过程控制系统的一个作用是当出现变差的特殊原因时提供统计信号,并且当不存在特殊原因时避免错误信息。
从而对这些特殊原因采取适当的措施(或是消除它们,或是如果有用,永久地保留它们)。
讨论过程能力时,需考虑两个在一定程度上相对的概念:
•过程能力由造成变差的普通原因来确定,通常代表过程本身的最佳性能(例如分布宽度最小),在处于统计控制状态下的运行过程,数据收集到后就能证明过程能力,而不考虑规范相对于过程分布的位置和/或宽度的状况如何;
•然而,内外部的顾客更关注过程的输出以及与他们的要求(定义为规范)的关系如何,而不考虑过程的变差如何。
一般说来,由于受统计控制的过程服从可预测的分布,从该分布中便可以估计出符合规范的产品的比例。
只要过程保持受统计控制状态并且其中分布的位置、分布宽度及形状不变化,就可以继续生产相同分布的符合规范的产品。
对过程采取的第一个措施就是将过程定位在其目标值上。
如果过程的分布宽度是不可接受的,该策略则允许生产最小量不符合规范的产品。
通常要求用对系统采取措施从而减少产生变差的变通原因的方法来改进过程的能力(以及其输出),从而始终符合规范。
为了进一步具体了解过程能力、过程性能以及与之相关的假设,参见第2章第5节。
简言之,首先应通过检查并消除变差的特殊原因使用权过程处于受统计控制状态,那么性能是可预测的,变可评定其满足顾客期望的
能力。
这是持续改进的基础。
每个过程可以根据其能力是否受控进行分类,过程可分成4类,如下表所示:
控制
一个可接受的过程必须是处于受控统计控制状态的且其固有变差(能力)必须小于图纸的公差。
理想的情况是具有1类过程,该过程受统计控制且有能力满足要求,是可接受的。
2类过程是受控过程但存在因普通原因造成的过大的必须减少的变差。
3类过程符合要求,可接受,但不是受控过程,需要识别变差的特殊原因并消除它。
4类过程即不是受控过程又不可接受,必须减少变差的特殊原因和变通原因。
在有些情况下,顾客也许允许制造商运行一个3类过程,这些情况包括:
•顾客对规范要求之内的变差不敏感(见第2章第5节所讨论的损失函数;
•对特殊原因采取措施所发生的成本比任何所有顾客得到的利益大,因成本原因可允许存在的特殊原因包括刀具磨损、刀具重磨、周期的(季节的)变化等;
•特殊原因已被识别,其记录表明具有一致性和可预见性。
在这些情况下,顾客可能会有以下要求:
•该过程是成熟的,例如,该过程已经过几个循环的持续改进;
•允许存在的特殊原因在已知一段时间内表现出产生稳定的后果;
•过程控制计划有效运行。
可确保所有的过程输出符合规范并能防止出现别的特殊原因或与允许存在的特殊原因不稳定的其它原因。
在汽车工业中可接受的作法是一个过程被证明处于统计控制状态后才计算其过程能力。
过程能力是作为利用从过程中得到的统计数据来进行过程性能预测的基础。
利用从过程中得到的一定时间的不稳定或不重复的数据来进行预测是没有什么价值的。
特殊原因是造成分布的形态、分布宽度或位置改变的原因,因此会很快使过程能力预测失效。
用来计算不同的能力指数或比值所要求的数据是从处于统计控制状态的过程获得的。
能力指数可分成两类:长期的和短期的。
短期能力的研究是以从一个操作循环中获取的测量为基础的。
这些数据用控制图分析后作为判定该过程是否在统计控制状态下运行的依据。
如果没有发现特殊原因,可以计算短期能力指数。
如果过程不是处于受控状态,就要求采取解决变差的特殊原因的措施。
这种研究通常用于验证由顾客提出的过程中生产出来的首批产品。
另一个用途,有时也叫机器能力研究,是用来验证一个新的或经过修改的过程实际性能是否符合工程参数。
如果一个过程是稳定的并且能符合短期的要求。
紧接应进行另一种型式的研究。
长期能力研究包括通过很长一段时间内所进行的测量应在足够长的时间内收集数据,同时这些数据应能包括所有能预计到的变差的原因,很多变差原因可能在短期研究时还没有观察到。
当收集到足够的数据后,将这些数据画在控制图上,如果没有发现变差的特殊原因,便可以计算长期的能力和性能指数。
这种研究的一个用途是用来描述一个过程在很长的一个时期内包括很多可能变差原因出现后能否满足顾客的要求的能力——例如:量化过程性能。
几个不同的指数已被提出。
因为1)没有一个单独的指数可以万能地适用于所有过程;且2)没有一个给定的过程可能通过一个单独的指数完整地来描述。
例如:推荐同时使用Cp和Cpk(见第II章第5
节),并与图表技术一起使用,可以更好地理解估计的分岂有此理和规范界限的关系。
在某种意义上说就是比较(并且努力使两者一致)“过程的呼声”和“顾客的呼声”(参见参考文献22)。
所有的指数都有不足之处且可能产生误导。
任何从计算的指数中得到的推断,可以从计算这些指数的数据中找到合适的解释。
有关汽车公司已经确定了对过程能力固定的要求。
读者有责任与他们的顾客联系从而确定使用哪些指数。
在有些情况下,可能最好是什么指数都不合适,或不是基于顾客的要求,努力使过程来符合这些规范浪费大量时间和精力。
第II章第5节描述的是能力和性能指数的选择以及在使用这些指数时的注意事项。