材料成形原理1、2、3章
华科 材料成型原理 第1章绪论及第2章金属塑性变形的物理本质
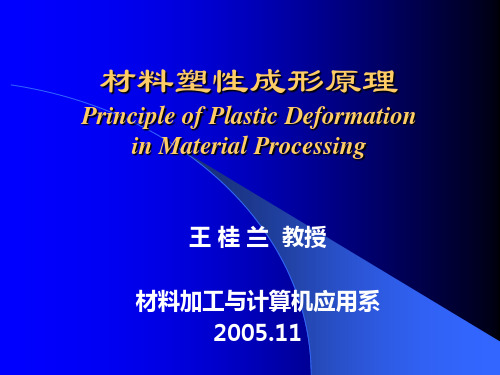
11~16
150
294~315
LY11
11~16
150
340~350
LY11
31
65
308
3.变形程度 4.应力状态
σ1-σ2
大
σ1-σ2
大
气
气
压
压
图5-20 脆性材料的各向压缩曲线 (a)大理石;(b)红砂石; —轴向压力; —侧向压力
5.变形状态
图5-24 主变形图对金属中缺陷形状的影响
(a)未变形的情况;(b)经两向压缩—向延伸变形后的情况; (c)经—向压缩两向延伸后的情况
Nabarro
蠕变
弹性区
(N扩ab散ar流ro蠕变变)
变形机制图
(a)纯银和(b)锗给出不同变形机制起控制作用的应力-温度区间, 两种材料的晶粒尺寸皆为32μm
以10-8/s的应变速率来确定弹性边界
§2. 2 塑性加工中金属的 组织与性能
2. 2. 1 冷变形 2. 2. 2 热变形 2. 2. 3 塑性变形对固态相变的影响
➢ 塑性映材料抵抗变形的能力。
塑性与柔软性的对立统一
➢铅---------------塑性好,变形抗力小
➢不锈钢--------塑性好,但变形抗力高 ➢白口铸铁----塑性差,变形抗力高
➢ 结论:塑性与柔软性不是同一概念
为什么要研究金属的塑性?
塑性变形—影响大(加工硬化、晶粒 细化、位错密度增加、形成织构等) ➢ 变形机理:弹性变形—原子间距的变化;
塑性变形—位错运动为主 ➢ 弹塑性共存:整体变形中包含弹性变形和塑性变形;塑性变
形的发生必先经历弹性变形;在材料加工过程中,工件的塑
性变形与工模具的弹性变形共存。
材料成形原理1、2、3章

毛细管现象:
将内径很细的玻璃管,插入能润湿玻璃管的液体中,则管内液面上升,且呈凹面状;...
产生部位:
狭窄管口,裂缝和细孔
浇铸薄小铸件时必须提高浇注温度和压力,以克服附加压力的阻碍。
金属凝固后期,枝晶间存在的微小液膜小至微米时,表面张力对铸件的凝固过程的补缩状况对金属是否出现热裂缺陷具有重大影响。
或:
液态成形是液态金属充满型腔并凝固后获得符合要求的毛坯或零件的工艺技术。
液态金属的充型能力首先取决于液态金属本身的流动能力,同时又与外界条件密切相关,是各种因素的综合反映,充型能力可以通过改变外界条件提高。
液态金属本身的流动能力称为流动性,是由金属的成分、温度、杂质含量决定的,可认为是确定条件下的充型能力。流动性越好,气体和杂质越易于上浮,使金属得以净化,良好的流动性有利于防止缩孔缩松热裂等缺陷。流动性越好,充型能力越强。
充型压头:
增加金属静压头的方法提高充型能力,也可采用压力铸造、低压铸造、真空吸铸。
浇注系统的结构:
结构越复杂,流动阻力越大,在静压头相同的情况下充型能力越差。
设计浇注系统时,要合理安排内浇道在铸件上位置,选择恰当的浇注系统结构和组件的断面积。
4.铸件结构方面的因素:
铸件的折算厚度:
铸件壁越薄,折算厚度越小,越不容易被充满。垂直壁易充满,要正确选择浇注位置。
铸件的凝固时间是指液态金属充满铸型时刻至凝固完毕所需要的时间。
凝固速度:
单位时间凝固层增长的厚度。
xx定律:
铸件凝固层厚度与凝固时间的平方根成正比。
金属型的凝固系数一般较大。
折算厚度法则考虑到了铸件形状这个因素,因而它更接近实际,是对平方根定律的修订和发展。
液态金属的凝固形核及生长方式
材料成型基本原理-第三章PPT课件

-
28
本章小结与习题讨论课
4 液态金属凝固时需要过冷,那么固态金属熔化时是否需要过热? 为什么?
5 假设凝固时的临界晶核为立方体形状,求临界形核功。分析在同样过 冷度下均匀形核时,球形晶核和立方晶核哪一个更容易成?
-
29
12
第三节 晶核的形成
2 非均匀形核 (3)临界形核功 计算时利用球冠体积、表面积表达式,结合平衡关系 σlw=σsw+σslcosθ 计算能量变化和临界形核功。 △Gk非/△Gk=(2-3cosθ+cos3θ)/4 a θ=0时,△Gk非=0,杂质本身即为晶核; b 180>θ>0时, △Gk非<△Gk, 杂质促进形核; cθ=180时,△Gk非=△Gk, 杂质不起作用。
19
第四节 晶核的长大
3 液体中温度梯度与晶体的长大形态 (2)负温度梯度(液体中距液固界面越远,温度越低) 粗糙界面:树枝状。 光滑界面:树枝状-多面体—台阶状。
-
20
第四节 晶核的长大
3 液体中温度梯度与晶体的长大形态 (2)负温度梯度(液体中距液固界面越远,温度越低)
©2003 Brooks/Cole, a division of Thomson Learning, Inc. Thomson Learning™ is a trademark used herein under license.
-
26
第六节 凝固理论的应用
4 急冷凝固技术 (1)非晶金属与合金 (2)微晶合金。 (3)准晶合金。
-
27
本章小结与习题讨论课
1 试述结晶相变的热力学条件、动力学条件、能量及结构条件。 2 在液态金属中,凡是涌现出的小于临界晶核半径的晶胚都不能成核。
材料成型原理

材料成型原理第1章液态金属的结构与性质物相由界面包围的具有一定成分和结构的均匀体组织物相的机械混合物润湿性是指存在两种互不相溶液体,液体首先润湿固相表面的能力,即一种液体在一种固体表面铺展的能力或倾向性压力差物体两侧所受压力的差值现代晶体学表明,晶体的原子一定方式周期排列在三维空间的晶格结点上,表现出平移对称性特征,同时原子以某种模式在平衡位置上作热振动,相对于晶体这种原子有序排列,气体的分子原子,不停的做无规律运动。
液体表现出长程无序特征,液体结构表现出局域范围内的近程有序。
偶分布函数的物理意义:距某一参考粒子r处找到另一个粒子的概率。
晶态固体因原子以特定方式周期排列,其偶分布函数以相应的规律呈分立的若干尖锐峰,液体的g(r)出现若干衰减的钝化峰,直至几个原子间距后趋于直线g(r)等于1。
由于能量起伏,液体中大量不停游动着的局域有序原子团簇,时聚时散,此起彼伏,而存在结构起伏,实际金属的现象,还要复杂的多,除了能量起伏及结构起伏,还同时存在着浓度起伏。
长程有序:液体的原子相对于周期有序的晶体固态是不规则的,液体结构宏观上不具有平移、对称性。
黏度是液体内摩擦阻力大小的标志,黏度的物理意义可以视为:作用于液体表面的应力与垂直于该平面方向上的速度梯度的比例系数。
表面活性元素使液体黏度降低,非表面活性杂质的存在使黏度提高。
黏度的意义:黏度影响金属液的流动性进而影响铸件轮廓的清晰程度。
影响钢铁材料的脱硫,脱磷,扩散脱氧。
熔渣及金属液粘度降低对合金元素的过渡是有利的。
影响铸件内部缩孔或缩松、热裂的形成倾向。
影响精炼效果,夹杂、气孔的形成。
表面张力是表面上平行于表面切线方向且各方向大小相等的张力。
表面张力是由于物体在表面上的质点受力不均所致。
表面是产生新的单位面积表面时系统自由能的增量。
表面与界面的差别在于后者泛指两相之间的交界面,前者指液体或固体与气体之间的交界面。
原子间结合力越大,表面内能越大,因此表面自由能越大,表面张力也就越大。
材料成型概论第二章材料成型的基础220110427资料

挤压模具
结构钢—工程结构钢、机械结构钢
工程结构钢:大多规定了钢的最低抗拉强度、最低屈 服强度,使钢具有一定的综合力学性能,保证材料设计 和使用中结构部件的最低安全要求。 工程结构钢分为: 1.通用工程结构钢—碳素结构钢、低合金高强度结构钢 2.专用工程结构钢—压力容器用钢、锅炉用钢、桥梁用 钢;焊接用钢、汽车大梁用钢;地质钻探钢管用钢、 钢轨、铆螺钢;船用钢、管线钢、锚链钢等。
金属压力加工产品标准和技术要求
内容包括: 3 验收试验标准—验收规则、做试验时的取样部位、
试样形状和尺寸、试验条件和试验方法。 4 交货标准—钢材交货时的包装和标志方法,以及资
料证明书内容等。
2.2.1 钢铁材料的种类及编号
工程上常采用的分类方法主要有:
按主要性能及用途分类 按化学成分分类 按合金元素种类分类 按质量等级分类 按冶炼方法分类 按金相组织分类
材料成型概论
第一章 材料成型概述 第二章 材料塑性成型的基础 第三章 轧制成型 第四章 挤压成型 第五章 拉拔成型 第六章 锻造成型 第七章 冲压成型 第八章 陶瓷成型
2.2 金属材料的种类及编号
2.2.1 钢铁材料的种类及编号 2.2.2 铝 铝合金及铜 铜合金 2.2.3 钛及钛合金
高级优质钢 ≤0.030 ≤0.030 ≤0.025 ≤0.025
特级优质钢 ≤0.025 ≤0.020 ≤0.025 ≤0.015
3. 钢材按用途分类
工程用钢 建筑、桥梁、船舶、车辆
结构钢
滚动轴承钢
刃具钢
工 具 钢 模具钢
量具钢
特 殊 性 不锈钢 能 钢 耐热钢
耐磨钢
2.钢材按质量分类
钢的质量是以磷、硫的含量来划分的。
材料成型基本原理完整版

第一章:液态金属的结构与性质1雷诺数Re:当Re>2300时为紊流,Re<2300时为层流。
Re=Du/v=Duρ/η,D为直径,u 为流动速度,v为运动粘度=动力粘度η/密度ρ。
层流比紊流消耗能量大。
2表面张力:表面张力是表面上平行于切线方向且各方向大小相同等的张力。
润湿角:接触角为锐角时为润湿,钝角时为不润湿。
3压力差:当表面具有一定的曲度时,表面张力将使表面的两侧产生压力差,该压力差值的大小与曲率半径成反比,曲率半径越小,表面张力的作用越显著。
4充型能力:充型过程中,液态金属充满铸型型腔,获得形状完整轮廓清晰的铸件的能力,即液态金属充型能力。
5长程无序、近程有序:液体的原子分布相对于周期有序的晶态固体是不规则的,液体结构宏观上不具备平移、对称性,表现出长程无序特征;而相对于完全无序的气体,液体中存在着许多不停游荡着的局域有序的原子集团,液体结构表现出局域范围内的近程有序。
拓扑短程序:Sn Ge Ga Si等固态具有共价键的单组元液体,原子间的共价键并未完全消失,存在着与固体结构中对应的四面体局域拓扑有序结构。
化学短程序:Li-Pb Cs-Au Mg-Bi Mg-Zn Mg-Sn Cu-Ti Cu-Sn Al-Mg Al-Fe等固态具有金属间化合物的二元熔体中均有化学短程序的存在。
6实际液态金属结构:实际金属和合金的液体由大量时聚时散、此起彼伏游动着的原子团簇空穴所组成,同时也含有各种固态液态和气态杂质或化合物,而且还表现出能量结构及浓度三种起伏特征,其结构相对复杂。
能量起伏:液态金属中处于热运动的原子的能量有高有低,同一原子的能量也在随时间不停的变化,时高时低,这种现象成为能量起伏。
结构起伏:由于能量起伏,液体中大量不停游动的局域有序原子团簇时聚时散,此起彼伏而存在结构起伏。
浓度起伏:游动原子团簇之间存在着成分差异,而且这种局域成分的不均匀性随原子热运动在不时发生着变化,这一现象成为浓度起伏。
材料成型原理
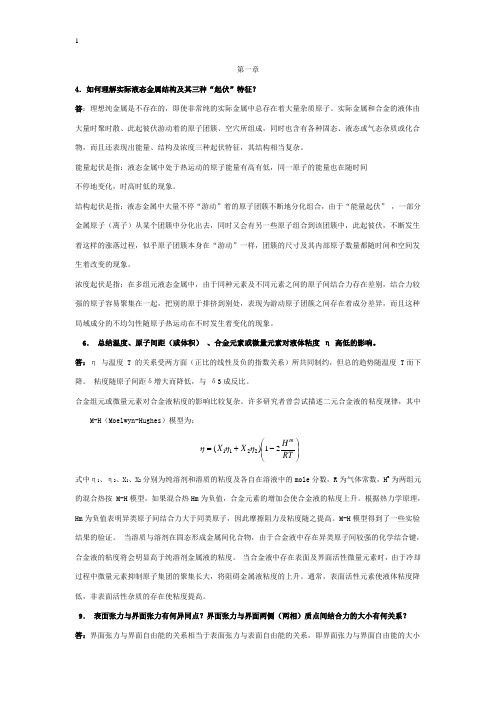
第一章4.如何理解实际液态金属结构及其三种“起伏”特征?答:理想纯金属是不存在的,即使非常纯的实际金属中总存在着大量杂质原子。
实际金属和合金的液体由大量时聚时散、此起彼伏游动着的原子团簇、空穴所组成,同时也含有各种固态、液态或气态杂质或化合物,而且还表现出能量、结构及浓度三种起伏特征,其结构相当复杂。
能量起伏是指:液态金属中处于热运动的原子能量有高有低,同一原子的能量也在随时间 不停地变化,时高时低的现象。
结构起伏是指:液态金属中大量不停“游动”着的原子团簇不断地分化组合,由于“能量起伏” ,一部分金属原子(离子)从某个团簇中分化出去,同时又会有另一些原子组合到该团簇中,此起彼伏,不断发生着这样的涨落过程,似乎原子团簇本身在“游动”一样,团簇的尺寸及其内部原子数量都随时间和空间发生着改变的现象。
浓度起伏是指:在多组元液态金属中,由于同种元素及不同元素之间的原子间结合力存在差别,结合力较强的原子容易聚集在一起,把别的原于排挤到别处,表现为游动原子团簇之间存在着成分差异,而且这种局域成分的不均匀性随原子热运动在不时发生着变化的现象。
6. 总结温度、原子间距(或体积) 、合金元素或微量元素对液体粘度 η 高低的影响。
答:η 与温度 T 的关系受两方面(正比的线性及负的指数关系)所共同制约,但总的趋势随温度 T 而下降。
粘度随原子间距δ增大而降低,与 δ3成反比。
合金组元或微量元素对合金液粘度的影响比较复杂。
许多研究者曾尝试描述二元合金液的粘度规律,其中M-H (Moelwyn-Hughes )模型为:⎪⎪⎭⎫ ⎝⎛-+=RT H X X m 21)(2211ηηη 式中η1、η2、X 1、X 2 分别为纯溶剂和溶质的粘度及各自在溶液中的mole 分数,R 为气体常数,H m为两组元的混合热按 M-H 模型,如果混合热Hm 为负值,合金元素的增加会使合金液的粘度上升。
根据热力学原理,Hm 为负值表明异类原子间结合力大于同类原子,因此摩擦阻力及粘度随之提高。
材料成型原理
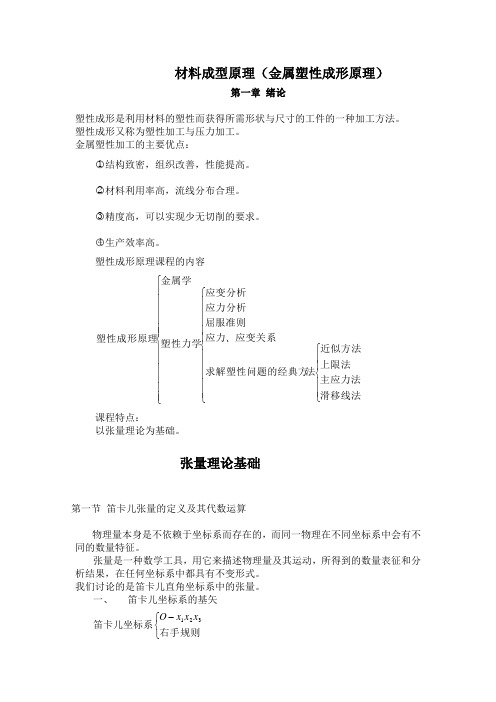
材料成型原理(金属塑性成形原理)第一章 绪论塑性成形是利用材料的塑性而获得所需形状与尺寸的工件的一种加工方法。
塑性成形又称为塑性加工与压力加工。
金属塑性加工的主要优点:○1结构致密,组织改善,性能提高。
○2材料利用率高,流线分布合理。
○3精度高,可以实现少无切削的要求。
○4生产效率高。
塑性成形原理课程的内容⎪⎪⎪⎪⎪⎪⎩⎪⎪⎪⎪⎪⎪⎨⎧⎪⎪⎪⎪⎪⎩⎪⎪⎪⎪⎪⎨⎧⎪⎪⎩⎪⎪⎨⎧滑移线法主应力法上限法近似方法法求解塑性问题的经典方应变关系应力屈服准则应力分析应变分析塑性力学金属学塑性成形原理、课程特点:以张量理论为基础。
张量理论基础第一节 笛卡儿张量的定义及其代数运算物理量本身是不依赖于坐标系而存在的,而同一物理在不同坐标系中会有不同的数量特征。
张量是一种数学工具,用它来描述物理量及其运动,所得到的数量表征和分析结果,在任何坐标系中都具有不变形式。
我们讨论的是笛卡儿直角坐标系中的张量。
一、 笛卡儿坐标系的基矢笛卡儿坐标系⎩⎨⎧-右手规则321x x x O设e k (k=1、2、3)沿Ox k 轴的单位矢量,称为基矢量或基矢。
定义基矢的点积或标量积:⎩⎨⎧≠==∙lk lk e e kl k .0.11δ kl δ为Kronecker 克氏符号。
定义基矢的叉积或矢量积为:k ijk j i e e e =∈⨯ ijk ∈为置换符号。
⎪⎩⎪⎨⎧-=∈,其它的奇数排列、、为、、,的偶数排列、、为、、,032113211k j i k j i ijk指标ijk 的原始排列顺序为1、2、3,如果将排列中的任意一对相邻指标互换,则称为指标的一次置换。
例如1 2 3给一次置换就成为1 3 2或2 1 3。
如果再互换一对指标,就称为二次置换。
依次类推可以定义指标排列的几次置换。
当几次为奇数时,称为奇置换。
而几为偶数时,称为偶置换。
二、 求和约定任一矢量 i i e e e e μμμμμ=++=332211 ij ij i j ij ij υμυμ=∑∑==3131在三维的欧矢空间内,如果某一指标在同一项中重复出现,就表示要对这个指标从1到3求和。
- 1、下载文档前请自行甄别文档内容的完整性,平台不提供额外的编辑、内容补充、找答案等附加服务。
- 2、"仅部分预览"的文档,不可在线预览部分如存在完整性等问题,可反馈申请退款(可完整预览的文档不适用该条件!)。
- 3、如文档侵犯您的权益,请联系客服反馈,我们会尽快为您处理(人工客服工作时间:9:00-18:30)。
形核:
亚稳态的液态金属通过起伏作用在某些微观小区域内形成稳定存在的晶态小质点的过程。
表面张力意义:
毛细管现象:
将内径很细的玻璃管,插入能润湿玻璃管的液体中,则管内液面上升,且呈凹面状;...
产生部位:
狭窄管口,裂缝和细孔
浇铸薄小铸件时必须提高浇注温度和压力,以克服附加压力的阻碍。
金属凝固后期,枝晶间存在的微小液膜小至微米时,表面张力对铸件的凝固过程的补缩状况对金属是否出现热裂缺陷具有重大影响。
熔焊过程中,熔渣和合金液两相应不润湿,否则不易将其从合金液去除,导致焊缝处夹渣缺陷的产生。
晶体的形核及生长、缩松、热裂、夹杂及气泡等铸造缺陷都与表面张力联系密切。
液态成形中的流动与传热
液态成形是将熔化的金属或合金在重力或其他外力作用下注入铸型的型腔中,待其冷却凝固后获得与型腔形状相同的铸件的一种成形方法
高能态区:
固态晶粒与液态间的界面。
生核或晶体的长大,是液态中的原子不断晶面向固态晶粒堆积的过程,是固液界面不断的向前推进的过程。
热力学能障与动力学能障都与界面状态密切相关。热力学能障是由被迫处于高自由能过渡状态的界面原子产生的,它能直接影响到系统自由能的大小,界面自由能即属于这种情况;动力学能障是由金属原子穿越界面过程引起的,它与结晶驱动力无关,仅取决于界面的结构和性质,激活自由能即属于这种情况。液态金属在成分、温度、能量上是不均匀的,正是由于存在这三个起伏,才能克服凝固过程中的两个能障,使凝固过程不断的进行下去。液态金属在一定的过冷度下,临界晶核必由相起伏提供,临界形核功由能量起伏提供。
原子在固态的规则排列熔化后紊乱程度不大,液态金属原子间结合键只破坏了一部分,液态金属的结构应接近固态金属而远离气态金属(熔点和过热度不大时)。
纯金属的液态结构是由原子集团、游离原子和空穴组成的。
结构起伏:
原子集团和空穴的变化现象。
实际合金熔体的结构是极其复杂的,包含各种化学成分的原子集团、游离原子、空穴、夹杂物及气泡等,是一种混浊的液体。液态金属中存在温度起伏、相起伏和浓度起伏。
温度差和浓度差产生的浮力,是液态合金对流的驱动力,粘度越大,对流强度越小。
表面张力:
一小部分的液体在大气中单独存在时,力图保持球形状态,说明总有一个力使其趋向球状
表面张力的实质是质点间的作用力,是由质点间的作用力不平衡引起的,指向液体内部的合力是表面张力产生的根源。
表面自由能即单位面积自由能,表面能或表面张力是界面能或界面张力的一个特例,对于液体来说,表面张力和表面能大小相等,只是单位不同,体现为从不同角度来描述同一现象。
形核的首要条件是系统必须处于亚稳态以提供相变驱动力,其次,要通过起伏作用克服能障才能形成稳定存在的晶核并确保其进一步生长。
均质形核:
在没有任何外来界面的均匀熔体中的形核过程。晶核的全部固液界面都由形核过程产生,因此热力学能障打,所需驱动力也较大。
异质形核:
在不均匀的熔体中依靠外来杂质或型壁界面提供的衬底进行形核的过程。
金属的比热容、密度、热导率:
比热容和密度大的合金,因本身含有较多的热量,在相同的过热度下保持液态的时间较长,流动性好;热导率小的合金,热量散失慢,同时,凝固期间液固两相并存的两相区小,流动阻力小,流动性好。金属中加入合金元素后,一般都使热导率明显下降,流动性上升。
粘度
表面张力:
对薄壁铸件、铸件的细薄部分、棱角的成形有影响,为克服附加压力的阻碍,必须在正常压头上增加一个附加压头h。
异质形核影响因素:
过冷度:
过冷度越大形核速率越大
界面:
若夹杂物基底与晶核润湿,则形核速率大
液态金属的过热及持续时间的影响:
当液态金属的过热温度接近或超过异质核心的熔点时,异质核心将会熔化或其表面活性消失,失去了夹杂物应有特性,从而减少了活性夹杂物数量,形核速率降低。
宏观长大是讨论固液界面所具有的形态,微观长大是讨论液相中的原子向固液界面堆积的方式。
界面固相一侧的点阵位置只有50%左右被固相原子所占据,这些原子散乱的随机分布在界面上,形成一个坑坑洼洼凸凹不平的界面层
平整界面:
固相表面的点阵位置几乎全部被固相原子锁占据,只留下少数空位,或者在充满固相原子的界面上存在有少数不稳定的、孤立的固相原子,从而形成了一个总体上是平整光滑的界面。
显微尺度下,粗糙界面由于其原子散乱分布的统计均匀性反而显得比较光滑,平整界面则由一些轮廓分明的小平面构成,粗糙界面的生长方式成为非小平面生长方式,平整界面以小平面生长。
充型压头:
增加金属静压头的方法提高充型能力,也可采用压力铸造、低压铸造、真空吸铸。
浇注系统的结构:
结构越复杂,流动阻力越大,在静压头相同的情况下充型能力越差。
设计浇注系统时,要合理安排内浇道在铸件上位置,选择恰当的浇注系统结构和组件的断面积。
4.铸件结构方面的因素:
铸件的折算厚度:
铸件壁越薄,折算厚度越小,越不容易被充满。垂直壁易充满,要正确选择浇注位置。
由于结构高度紊乱的液相具有更高的熵值,液相自由能将以更大的速率随着温度的升高而降低。
对于给定金属,结晶潜热与平衡结晶温度是定值,故自由能差仅与过冷度有关,因此液态金属的凝固过程的驱动力是由过冷度提供的,过冷度越大,驱动力也越大。
晶核的形成和长大是同时进行的,即在晶核长大的同时又会产生新的结晶核心。
凝固过程总的来说是由于体系自由能减低自发进行的,但在形核时,体系自由能的变化是由体积自由能的降低和界面自由能的升高组成的,当能量以降低为主时,就发生凝固现象。
影响表面张力的因素:
熔点、温度和溶质元素。
金属微粒的熔点随其尺寸减小而降低,熔点越高,表面张力越大。
表面活性元素:
使表面张力降低的元素
正吸附:
溶质在界面层的浓度大于在溶液内部的浓度
加入溶质改变表面张力的原理在于它改变了表面层质点的力场分布不对称程度。正负吸附的原理在于自然界中系统的自由能总是自发降低
动态凝固曲线的水平距离很小或等于零时,这时铸件的凝固区很小或者没有,称这种凝固方式为层状凝固方式。
一般的,具有层状凝固方式的铸件,凝固过程容易补缩,组织致密,性能好;具有体积凝固方式的铸件,不易补缩,易产生缩松、夹杂、开裂等缺陷,铸件的性能差。
影响凝固方式的因素是合金的化学成分和铸件断面的温度梯度。
晶体的宏观长大方式取决于固液界面前方液体中的温度分布,即温度梯度。
正温度梯度:
液相温度高于界面温度
平面方式xx:
固液界面前方液体过冷区域及过冷度极小,晶体生长时凝固潜热的析出方向与晶体生长方向相反,一旦某一晶体生长伸入液相区就会被重新熔化,导致晶体以平面状生长。
树枝晶xx方式:
固液界面前过冷区域较大,离界面越远的区域过冷度越大,晶体生长时凝固潜热析出方向与晶体生长方向一致,界面上凸起的晶体将快速伸入过冷液中,成为树枝状晶生长方式。粗糙界面:
具有最大溶解度的合金,其流动性最小。在液态金属前面析出15%~20%液相时,液态金属就停止流动。
影响充型能力的因素:
1.金属性质方面的因素。这类因素是内因,决定了金属本身的流动能力—流动性。
合金的成分:
纯金属和共晶成分的地方出现最大值,即流动性最好。
结晶潜热:
约占液态金属含热量的85%--90%,其余为过热量。纯金属和共晶成分合金凝固过程释放的潜热越多,凝固过程进行的越缓慢,流动性越好。
铸件的凝固时间是指液态金属充满铸型时刻至凝固完毕所需要的时间。
凝固速度:
单位时间凝固层增长的厚度。
xx定律:
铸件凝固层厚度与凝固时间的平方根成正比。
金属型的凝固系数一般较大。
折算厚度法则考虑到了铸件形状这个因素,因而它更接近实际,是对平方根定律的修订和发展。
液态金属的凝固形核及生长方式
液态金属的凝固过程决定着凝固后的显微组织,并影响随后冷却过程中的相变、过饱和相的析出、铸件的热处理过程及凝固过程中的偏析、气体析出、补缩过程和裂纹形成等,对铸件的质量、性能以及工艺过程都有极其重要的作用。
枝晶间的液体流动就是在糊状区的补缩流动,宽结晶温度范围的合金,树枝晶发达,凝固过程最后的补缩往往得不到液流的补充,而形成缩松。
凝固过程中的热量传输,传导传热、对流换热、辐射换热。热传导为主要方式。
铸件冷却凝固过程实质上是铸件内部过热热量和潜热不断向外散失的过程。
测温法测温度场是通过向被测件内安放热电偶实现的,主要技术是放置热电偶的位置的选择和数据的处理。
绪论
材料成形:
将材料加工成具有一定形状、尺寸和性能要求的零部件或毛坯的工艺方法。
材料成形主要方法:
除去加工法、连接加工法、变形加工法、液态及粉末成形加工法。
液态金属的结构和性质
在熔点附近,空穴数目可以达到原子总数的1%
金属由固态变为液态,体积膨胀为3%·5%
熔化潜热:
在熔点温度的固态,变为同温度下的液态,金属要吸收大量的热量
液态金属的粘度:
粘度的本质是原子间的结合力。
影响粘度的因素:
化学成分、温度和夹杂物。
化学成分:
难溶化合物的液体粘度较高,而熔点低的共晶成分的合金粘度低,对于共晶成分的合金,异类原子之间不发生结合,而同类原子聚合时,由于异类原子的存在而使它的聚合缓慢,晶坯的形成拖后,故粘度较非共晶成分低。
非金属夹杂物:
晶体的长大机制是指在结晶过程中晶体结晶面的生长方式。
连续生长机制:
固液界面在原子尺度呈粗糙结构时,界面上的空位构成了晶体生长所必需的台阶,使得液相原子能够连续的往上堆砌,并随机的受到固相中较多近邻原子的键合。界面的粗糙使原子的堆砌变得容易,另外,固相与液相之间在结构和键合能方面的差别较小,容易在界面过渡层内得到调节,因此动力学能障小,不需要很大的过冷度来驱动原子进入晶体,并能得到较大的生长速率。