冷冲压模具设计实例
冷冲压模具设计与制造实例汇总

该工件包括落料、冲孔两个基本工序,可有以下三种工艺方案:
方案一:先落料,后冲孔。采用单工序模生产。
方案二:落料-冲孔复合冲压。采用复合模生产。
方案三:冲孔-落料级进冲压。采用级进模生产。
方案一模具结构简单,但需两道工序两副模具,成本高而生产效率低,难以满足中批量生产要求。方案二只需一副模具,工件的精度及生产效率都较高,但工件最小壁厚3.5mm接近凸凹模许用最小壁厚3.2mm,模具强度较差,制造难度大,并且冲压后成品件留在模具上,在清理模具上的物料时会影响冲压速度,操作不方便。方案三也只需一副模具,生产效率高,操作方便,工件精度也能满足要求。通过对上述三种方案的分析比较,该件的冲压生产采用方案三为佳。
4.模具总体设计
(1)模具类型的选择
由冲压工艺分析可知,采用级进冲压,所以模具类型为级进模。
(2)定位方式的选择
因为该模具采用的是条料,控制条料的送进方向采用导料板,无侧压装置。控制条料的送进步距采用挡料销初定距,导正销精定距。而第一件的冲压位置因为条料长度有一定余量,可以靠操作工目测来定。
(3)卸料、出件方式的选择
取凹模厚度H=30mm,凹模壁厚c=45mm,
凹模宽度B=b+2c=(127+2×45)mm=217mm
凹模长度L取195mm(送料方向)
凹模轮廓尺寸为195mm×217mm×30mm,结构如图8.2.4(c)所示。
(2)定位零件的设计
落料凸模下部设置两个导正销,分别借用工件上φ5mm和φ8mm两个孔作导正孔。φ8mm导正孔的导正销的结构如图8.2.5所示。导正应在卸料板压紧板料之前完成导正,考虑料厚和装配后卸料板下平面超出凸模端面lmm,所以导正销直线部分的长度为1.8mm。导正销采用H7/r6安装在落料凸模端面,导正销导正部分与导正孔采用H7/h6配合。
冷冲模设计与制造实例

DT3 (15.865 0.072) 0 0.013 mm 15.7930 0.013 mm
DA4 50 0.75 0.24 00.019 mm 49.82000.019 mm ( )
冷冲模设计与制造实例 高职高专 ppt 课件
书名:冷冲模设计与制造实例 ISBN: 978-7-111-27278-6 作者:王嘉 出版社:机械工业出版社 本书配有电子课件
冷冲模设计与制造实例 高职高专 ppt 课件
冷冲压模具设计与制造实例
主编:王嘉
冷冲模设计与制造实例 高职高专 ppt 课件
第一部分 冷冲压模具设计步骤
FX K X F 0.05 72.6N 3.63kN
FT NK T F 5 0.055 72.6N 20kN
则零件所需的冲压力为
F总 F FX FT (72.6 3.63 20)kN 96.23kN
初选设备为开式压力机J23—16。
4.压力中心计算
DT4 (49.820 0.072) 0 0.013 mm 49.7480 0.013 mm
2200.52 mm (2)磨损后变小的尺寸: ,尺寸的精度等级为 IT14,磨损系数X取0.5。磨损后变小尺寸的基本计算公 式 0 DA (Dmin XΔ)
A
DT ( DA Z min ) 0 T
y5 8
y9 1
y6 14
1
l7 11 y7 20 l8 19 y8 10.5
l9 11
2
4
3
代入压力中心计算公式得
冷冲压模具设计与制造实例[2]汇总
![冷冲压模具设计与制造实例[2]汇总](https://img.taocdn.com/s3/m/bd988345be23482fb4da4c5a.png)
例8.2.1冲裁模设计与制造实例工件名称:手柄工件简图:如图8.2.1所示。
生产批量:中批量材料:Q235-A钢1.冲压件工艺性分析此工件只有落料和冲孔两个工序。
材料为Q235-A钢,具有良好的冲压性能,适合冲裁。
工件结构相对简单,有一个φ8mm的孔和5个φ5mm的孔;孔与孔、孔与边缘之间的距离也满足要求,最小壁厚为3.5mm(大端4个φ5mm的孔与φ8mm孔、φ5mm的孔与R16mm外圆之间的壁厚。
工件的尺寸全部为自由公差,可看作IT14级,尺寸精度较低,普通冲裁完全能满足要求。
2.冲压工艺方案的确定该工件包括落料、冲孔两个基本工序,方案一:先落料,后冲孔。
采用单工序模生产。
方案二:落料-冲孔复合冲压。
采用复合模生产。
方案三:冲孔-落料级进冲压。
采用级进模生产。
方案一模具结构简单,但需两道工序两副模具,成本高而生产效率低,难以满足中批量生产要求。
方案二只需一副模具,工件的精度及生产效率都较高,但工件最小壁厚3.5mm接近凸凹模许用最小壁厚3.2mm,模具强度较差,制造难度大,并且冲压后成品件留在模具上,在清理模具上的物料时会影响冲压速度,操作不方便。
方案三也只需一副模具,生产效率高,操作方便,工件精度也能满足要求。
通过对上述三种方案的分析比较,该件的冲压生产采用方案三为佳。
3.主要设计计算(1)排样方式的确定及其计算设计级进模,首先要设计条料排样图。
手柄的形状具有一头大一头小的特点,直排时材料利用率低,应采用直对排,如图8.2.2所示的排样方法,设计成隔位冲压,可显著地减少废料。
隔位冲压就是将第一遍冲压以后的条料水平方向旋转180°,再冲第二遍,在第一次冲裁的间隔中冲裁出第二部分工件。
搭边值取2.5mm和3.5mm,条料宽度为135mm,步距离为53 mm,一个步距的材料利用率为78%(计算见表8.2.1)。
查板材标准,宜选950mm×1500mm的钢板,每张钢板可剪裁为7张条料(135mm×1500mm),每张条料可冲56个工件,故每张钢板的材料利用率为76%。
冷冲压模具改进设计实例分析

冷冲压模具改进设计实例分析冷冲压模具是一种用于制造金属零件的工具,它通过在金属表面施加压力使其变形,同时具备一定的冷却功能。
冷冲压模具的设计直接影响到产品的质量和生产效率。
本文将以一款汽车零部件模具为例,对其进行改进设计分析。
首先,我们需要对原有的冷冲压模具进行分析,并识别出存在的问题和改进的空间。
该模具用于制造汽车车门锁芯零件,主要问题如下:1.模具使用寿命较短:由于该模具在长时间使用后容易出现磨损,并且需要定期更换,这导致了生产效率的下降和成本的增加。
2.产品变形和尺寸不准确:由于金属材料的收缩和热变形,以及模具本身的精度问题,导致制成的零件存在一定的变形和尺寸不准确性,影响了产品的质量。
3.制造周期长:该模具需要多道工序进行制造,且每道工序之间的处理时间较长,导致整个制造周期过长,无法满足快速交付的需求。
基于以上问题,我们可以提出以下改进设计方案:1.优化材料选择:选择更耐磨、抗拉力更强的材料制作模具。
优化后的模具材料能够增加使用寿命,减少更换次数,提高生产效率和降低成本。
2.设计增加辅助冷却系统:在模具设计中增加冷却孔和冷却水道,通过冷却水的流动来降低模具温度,以减缓模具和金属材料的热变形,从而改善零件的尺寸准确性。
3.采用多道工序一体化加工:通过模具设计的一体化,将原本需要多次装配和加工的工序合并在一个模具中完成。
这样可以减少制造时间和人力资源的浪费,缩短制造周期,提高生产效率。
4.优化模具结构和形状:通过对模具结构和形状的优化,减少零件变形的可能性。
例如,采用适当的辅助结构和强度加固设计,以及减小模具开缝的尺寸,从而提高模具的准确度和稳定性。
5.引入模具设计软件和先进制造工艺:利用模具设计软件进行模拟和仿真,对模具进行优化设计。
同时,引入先进的制造工艺,如数控加工和电脉冲成型等,以确保模具的精度和稳定性。
经过以上的改进设计方案,我们预计可以得到以下改进结果:1.提高模具使用寿命:通过优化材料选择和增加冷却系统,降低模具磨损和温度变形的可能性,从而提高模具的使用寿命。
冷冲压工艺制定及模具设计实例冲压与模具15640
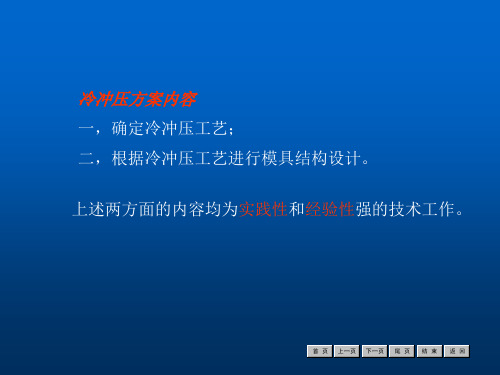
具体内容包括冲压工艺规程卡片(如表8-4所示)、冲 压工序卡片、工艺路线明细表等。在大批量生产中,需要 制定每个零件的工艺过程卡和工序卡;成批生产中,一般 需要制定工艺过程卡;小批量生产一般只需要填写工艺路 线明细表。
对于重要的冲压件工艺制定和模具设计,往往还需要 编制计算说明书。计算说明书的内容包括:1冲压件工艺性 分析;2毛坯尺寸计算;3排样及剪板;4工序次数及工序件 形状和尺寸;5工艺方案的技术、经济性分析比较;6模具 结构形式分析;7模具主要零件结构、材料、公差、技术要 求等;8凸、凹模工作部分尺寸与公差确定;9模具主要零 件强度计算、压力中心、弹性元件选用和核算;10设备类 型、吨位、主参数等。
主要根据确定的冲压工艺和冲压件形状特点、精度 要求、生产批量、模具加工条件、操作是否方便与安全 等要求,以及利用现有通用机械化、自动化装置的可能 性等,选定冲模类型及结构形式。
此外还需要进行必要的计算,包括模具零件强度计 算、压力中心计算、弹性元件选用和核算,再进行模具 总装配图设计、列出模具零件明细表,设计模具凸、凹 模等工作零件以及非标准零件的技术图纸。
8.1.2 分析冲压件的工艺性
汽车前大灯外壳
连接件
8.1.3 冲压工艺方案的确定
1.确定工序性质
翻边零件图
翻边件的工序安排
直接翻边成形
一次拉深成形:采用落料并冲Ф11孔、拉深、冲Ф23孔 的工艺方案,使凸缘保持为弱区,则可以一次拉深成形。
不能采用:落料、拉深、冲Ф23孔的工艺方案 。
变形减轻孔的应用
8.1.3 冲压工艺方案的确定
2.工序数的确定 3.工序顺序的确定
弯曲前冲孔
多孔拉深件拉深后冲孔
4.工序的合并
冷冲压模具设计过程

A 47 2 94 28 mm 2 9572mm 2
计算毛坯的面积A:
二、冷冲压模具设计实例
按表查得最小搭边值:a=2mm,a1=1.5mm 条料宽度:B 2R 28 2 a 2 47 28 2 2 126mm 进距: c 2R a1 2 47 1.5 95.5mm 一个进距的材料利用率:
5) 安装、紧固零件,如模柄、上下模座的结构型式的选择等。
一、冷冲压模具设计的一般步骤
6.选定冲压设备
冲压设备的选择是工序设计和模具设计的一项重要内
容,合理地选用设备对工件质量的保证、生产率的提高, 操作时的安全都有重大影响,也为模具设计带来方便,冲 压设备的选择主要决定其类型和规格。 冲压设备类型的选定,主要取决于工艺要求和生产批 量。 冲压设备规格的确定,主要取决于工艺参数及冲模结 构尺寸,对于曲柄压力机来说,必须满足以下要求:
以便放入毛坯和取出工件; 4) 压力机的台面尺寸必须大于模具下模座的外形尺寸,并要 留有固定模具的位置;一般每边应大出 50~70mm以上,压 力机台面上的漏料孔尺寸必须大于工件(或废料)的尺寸。
一、冷冲压模具设计的一般步骤
7.绘制模具总图
一、冷冲压模具设计的一般步骤图上应注明全部尺寸、公差与配合、形位公 差、表面光洁度、所用材料、热处理要求以及其它各 项技术要求。
二、冷冲压模具设计实例
查表2—13得磨损系数: R470 0.62 mm x=0. 5 0.26 28 x=0. 75 0.26 mm 据表4-14参考,查得拉深凸模的制造公差:δp=0.04mm, δd=0.07mm 落料凹模刃口尺寸的计算:
Dd Dmax x 0d
0.04 Rd Rmax x 0d (47 0.5 0.62)0 46.690.04 0 mm
冷冲压模具设计实例和编写说明书

冷冲压模具设计实例和编写说明书一、冲裁模如图1所示工件为22型客车车门垫板。
每辆车数量为6个,材料为Q235,厚度t=4mm.图1 车门垫板1.零件的工艺分析零件尺寸公差无特殊要求,按ITl4级选取,利用普通冲裁方式可达到图样要求.由于该件外形简单,形状规则,适于冲裁加工。
材料为Q235钢板,2.确定工艺方案零件属于大批生产,工艺性较好。
但不宜采用复合模.因为最窄处A的距离为6.5mm(图1),而复合模的凸凹模最小壁厚需要8.5mm(见表2—27),所以不能采用复合模.如果采用落料以后再冲孔,则效率太低,而且质量不易保证。
由于该件批量较大,因此确定零件的工艺方案为冲孔—切断级进模较好,并考虑凹模刃口强度,其中间还需留一空步,排样如图2所示。
图2 排样图.工艺与设计计算(1)冲裁力的计算根据式(2—4),冲孔力切断力根据式(2-5),冲孔部分及切断部分的卸料力二、弯曲模如图6-10所示零件为汽车上的塑料闸瓦钢背,每辆车16个。
材料为Q235,厚度t=3mm.图6—10 塑料闸瓦钢背本工序简图设计步骤:1.分析零件的冲压工艺性并确定工艺方案弯曲模没有固定的结构型式,有可能设计得很简单,也可能设计得很复杂,这需要根据工件的材料性能、形状、精度要求和产量进行综合分析,确定模具结构型式。
本工件的断面是燕尾形的,其表面还要翻出两种尺寸的若干梅花形孔,确定工艺方案为弯曲一翻边一修边三个工序.本工序主要完成弯曲工艺,达到如图6—10所示的燕尾形工件.这种燕尾形一般分两次弯成,先弯成四个直角槽形件,然后再侧弯成燕尾形,这就需要两套模具,生产效率低。
考虑该工件的批量较大,因此应该尽量设计一种效率较高的模具,本方案就是采用了能一次成形的转轴式压弯模。
2.进行必要的计算(1)毛坯尺寸计算毛坯尺寸分析如图6,11所示三、拉深模及翻边模如图6—19所示工件,为180柴油机通风口座子,每台车用数量4个.材料为08酸洗钢板,厚度t=1.5mm。
冷冲压工艺模具设计实例
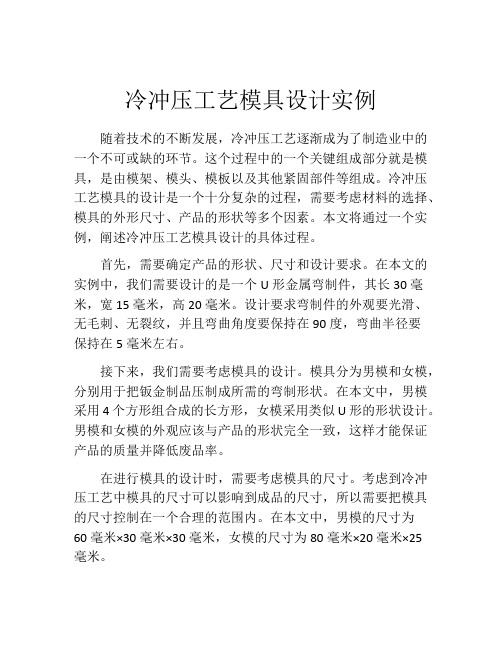
冷冲压工艺模具设计实例随着技术的不断发展,冷冲压工艺逐渐成为了制造业中的一个不可或缺的环节。
这个过程中的一个关键组成部分就是模具,是由模架、模头、模板以及其他紧固部件等组成。
冷冲压工艺模具的设计是一个十分复杂的过程,需要考虑材料的选择、模具的外形尺寸、产品的形状等多个因素。
本文将通过一个实例,阐述冷冲压工艺模具设计的具体过程。
首先,需要确定产品的形状、尺寸和设计要求。
在本文的实例中,我们需要设计的是一个U形金属弯制件,其长30毫米,宽15毫米,高20毫米。
设计要求弯制件的外观要光滑、无毛刺、无裂纹,并且弯曲角度要保持在90度,弯曲半径要保持在5毫米左右。
接下来,我们需要考虑模具的设计。
模具分为男模和女模,分别用于把钣金制品压制成所需的弯制形状。
在本文中,男模采用4个方形组合成的长方形,女模采用类似U形的形状设计。
男模和女模的外观应该与产品的形状完全一致,这样才能保证产品的质量并降低废品率。
在进行模具的设计时,需要考虑模具的尺寸。
考虑到冷冲压工艺中模具的尺寸可以影响到成品的尺寸,所以需要把模具的尺寸控制在一个合理的范围内。
在本文中,男模的尺寸为60毫米×30毫米×30毫米,女模的尺寸为80毫米×20毫米×25毫米。
与此同时,还需要考虑模具的材料。
可以采用碳钢、合金钢、特殊合金或者硬质合金等材料制作模具。
考虑到我们所需制作的弯制件是一种广泛用于各种交通运输车辆中的金属制品,需要考虑其强度、硬度、韧性、耐热性等方面的要求。
在本文中,我们采用了高速钢作为模具材料,其硬度和韧性都比较适中,并且其制作成本相对较低。
最后,还需要考虑一些其它因素,如模具的制造成本、制作周期、精度等。
在本文中,我们选择了传统的数控加工技术,制作周期为2周左右,精度误差控制范围在0.1毫米左右。
总之,冷冲压工艺模具设计是一个高度精密的过程,需要专业的设计人员根据具体的产品形态、尺寸、工艺要求等因素进行综合考虑,并且需要结合经验进行实际操作才能获得最终的理想产品。
- 1、下载文档前请自行甄别文档内容的完整性,平台不提供额外的编辑、内容补充、找答案等附加服务。
- 2、"仅部分预览"的文档,不可在线预览部分如存在完整性等问题,可反馈申请退款(可完整预览的文档不适用该条件!)。
- 3、如文档侵犯您的权益,请联系客服反馈,我们会尽快为您处理(人工客服工作时间:9:00-18:30)。
A冷冲压模具设计实例工件名称:手柄工件简图:生产批量:中批量材料:Q235-A钢材料厚度:1.2mm1、冲压件工艺性分析此工件只有落料和冲孔两个工序。
材料为Q235-A钢,具有良好的冲压性能,适合冲裁。
工件结构相对简单,有一个φ8mm的孔和5个φ5mm的孔;孔与孔、孔与边缘之间的距离也满足要求,最小壁厚为3.5mm(大端4个φ5mm的孔与φ8mm孔、φ5mm的孔与R16mm外圆之间的壁厚)。
工件的尺寸全部为自由公差,可看作IT14级,尺寸精度较低,普通冲裁完全能满足要求。
2、冲压工艺方案的确定该工件包括落料、冲孔两个基本工序,可有以下三种工艺方案:方案一:先落料,后冲孔。
采用单工序模生产。
方案二:落料-冲孔复合冲压。
采用复合模生产。
方案三:冲孔—落料级进冲压。
采用级进模生产。
方案一模具结构简单,但需两道工序两副模具,成本高而生产效率低,难以满足中批量生产要求。
方案二只需一副模具,工件的精度及生产效率都较高,但工件最小壁厚 3.5mm 接近凸凹模许用最小壁厚3.2mm,模具强度较差,制造难度大,并且冲压后成品件留在模具上,在清理模具上的物料时会影响冲压速度,操作不方便。
方案三也只需一副模具,生产效率高,操作方便,工件精度也能满足要求。
通过对上述三种方案的分析比较,该件的冲压生产采用方案三为佳。
3、主要设计计算(1)排样方式的确定及其计算设计级进模,首先要设计条料排样图。
手柄的形状具有一头大一头小的特点,直排时材料利用率低,应采用直对排,如图8.2.2手柄排样图所示的排样方法,设计成隔位冲压,可显著地减少废料。
隔位冲压就是将第一遍冲压以后的条料水平方向旋转180°,再冲第二遍,在第一次冲裁的间隔中冲裁出第二部分工件。
搭边值取 2.5mm和 3.5mm,条料宽度为135mm,步距离为53 mm,一个步距的材料利用率为78%(计算见表8.2.1)。
查板材标准,宜选950mm×1500mm的钢板,每张钢板可剪裁为7张条料(135mm×1500mm),每张条料可冲56个工件,故每张钢板的材料利用率为76%。
图8.2.2 手柄排样图(2)冲压力的计算该模具采用级进模,拟选择弹性卸料、下出件。
冲压力的相关计算见表8.2.1。
根据计算结果,冲压设备拟选J23-25。
(3)压力中心的确定及相关计算计算压力中心时,先画出凹模型口图,如图8.2.3所示。
在图中将xoy坐标系建立在图示的对称中心线上,将冲裁轮廓线按几何图形分解成L1~L6共6组基本线段,用解析法求得该模具的压力中心C点的坐标(13.57,11.64)。
有关计算如表8.2.2所示。
由以上计算结果可以看出,该工件冲裁力不大,压力中心偏移坐标原点O较小,为了便于模具的加工和装配,模具中心仍选在坐标原点O。
若选用J23-25冲床,C点仍在压力机模柄孔投影面积范围内,满足要求。
(4)工作零件刃口尺寸计算在确定工作零件刃口尺寸计算方法之前,首先要考虑工作零件的加工方法及模具装配方法。
结合该模具的特点,工作零件的形状相对较简单,适宜采用线切割机床分别加工落料凸模、凹模、凸模固定板以及卸料板,这种加工方法可以保证这些零件各个孔的同轴度,使装配工作简化。
因此工作零件刃口尺寸计算就按分开加工的方法来计算,具体计算见表8.2.3所示。
(5)卸料橡胶的设计卸料橡胶的设计计算见表8.2.4。
选用的四块橡胶板的厚度务必一致,不然会造成受力不均匀,运动产生歪斜,影响模具的正常工作。
4、模具总体设计(1)模具类型的选择由冲压工艺分析可知,采用级进冲压,所以模具类型为级进模。
(2)定位方式的选择因为该模具采用的是条料,控制条料的送进方向采用导料板,无侧压装置。
控制条料的送进步距采用挡料销初定距,导正销精定距。
而第一件的冲压位置因为条料长度有一定余量,可以靠操作工目测来定。
(3)卸料、出件方式的选择因为工件料厚为1.2mm,相对较薄,卸料力也比较小,故可采用弹性卸料。
又因为是级进模生产,所以采用下出件比较便于操作与提高生产效率。
(4)导向方式的选择为了提高模具寿命和工件质量,方便安装调整,该级进模采用中间导柱的导向方式。
5、主要零部件设计(1)工作零件的结构设计①落料凸模结合工件外形并考虑加工,将落料凸模设计成直通式,采用线切割机床加工,2个M8螺钉固定在垫板上,与凸模固定板的配合按H6/m5。
其总长L可按公式2.9.2计算:L =20+14+1.2+28.8=64mm具体结构可参见图8.2.4(a)所示。
②冲孔凸模因为所冲的孔均为圆形,而且都不属于需要特别保护的小凸模,所以冲孔凸模采用台阶式,一方面加工简单,另一方面又便于装配与更换。
其中冲5个φ5的圆形凸模可选用标准件BⅡ型式(尺寸为5.15×64)。
冲φ8mm孔的凸模结构如图8.2.4(b)所示。
③凹模凹模采用整体凹模,各冲裁的凹模孔均采用线切割机床加工,安排凹模在模架上的位置时,要依据计算压力中心的数据,将压力中心与模柄中心重合。
其轮廓尺寸可按公式2.9.3、2.9.4计算:凹模厚度H=kb=0.2×127mm=25.4mm(查表2.9.5得k=0.2)凹模壁厚c=(1.5~2)H=38~50.8mm取凹模厚度H=30mm,凹模壁厚c=45mm,凹模宽度B=b+2c=(127+2×45)mm=217mm凹模长度L取195mm(送料方向)凹模轮廓尺寸为195mm×217mm×30mm,结构如图8.2.4(c)所示。
(2)定位零件的设计落料凸模下部设置两个导正销,分别借用工件上φ5mm和φ8mm两个孔作导正孔。
φ8mm导正孔的导正销的结构如图8.2.5所示。
导正应在卸料板压紧板料之前完成导正,考虑料厚和装配后卸料板下平面超出凸模端面lmm ,所以导正销直线部分的长度为1.8mm。
导正销采用H7/r6安装在落料凸模端面,导正销导正部分与导正孔采用H7/h6配合。
起粗定距的活动挡料销、弹簧和螺塞选用标准件,规格为8×16。
(3)导料板的设计导料板的内侧与条料接触,外侧与凹模齐平,导料板与条料之间的间隙取1mm,这样就可确定了导料板的宽度,导料板的厚度按表2.9.7选择。
导料板采用45钢制作,热处理硬度为40~45HRC,用螺钉和销钉固定在凹模上。
导料板的进料端安装有承料板。
(4)卸料部件的设计①卸料板的设计卸料板的周界尺寸与凹模的周界尺寸相同,厚度为14mm。
卸料板采用45钢制造,淬火硬度为40~45HRC。
②卸料螺钉的选用卸料板上设置4个卸料螺钉,公称直径为12mm,螺纹部分为M10×10mm。
卸料钉尾部应留有足够的行程空间。
卸料螺钉拧紧后,应使卸料板超出凸模端面lmm,有误差时通过在螺钉与卸料板之间安装垫片来调整。
(5)模架及其它零部件设计该模具采用中间导柱模架,这种模架的导柱在模具中间位置,冲压时可防止由于偏心力矩而引起的模具歪斜。
以凹模周界尺寸为依据,选择模架规格。
导柱d/mm×L/mm分别为φ28×160,φ32×160;导套d/mm×L/mm×D/mm分别为φ28×115×42,φ32×115×45。
上模座厚度H上模取45mm,上模垫板厚度H垫取10mm,固定板厚度H固取20mm,下模座厚度H下模取50mm,那么,该模具的闭合高度:H闭=H上模+H垫+L+H +H下模-h2 =(45+10+64+30+50-2)mm=197mm 式中L——凸模长度,L=64 mm;H——凹模厚度,H=30mm;h2——凸模冲裁后进入凹模的深度,h2=2mm。
可见该模具闭合高度小于所选压力机J23-25的最大装模高度(220mm),可以使用。
6、模具总装图通过以上设计,可得到如图8.2.6所示的模具总装图。
模具上模部分主要由上模板、垫板、凸模(7个)、凸模固定板及卸料板等组成。
卸料方式采用弹性卸料,以橡胶为弹性元件。
下模部分由下模座、凹模板、导料板等组成。
冲孔废料和成品件均由漏料孔漏出。
条料送进时采用活动挡料销13作为粗定距,在落料凸模上安装两个导正销4,利用条料上φ5mm和φ8孔作导正销孔进行导正,以此作为条料送进的精确定距。
操作时完成第一步冲压后,把条料抬起向前移动,用落料孔套在活动挡料销13上,并向前推紧,冲压时凸模上的导正销4再作精确定距。
活动挡料销位置的设定比理想的几何位置向前偏移0.2mm,冲压过程中粗定位完成以后,当用导正销作精确定位时,由导正销上圆锥形斜面再将条料向后拉回约0.2mm而完成精确定距。
用这种方法定距,精度可达到0.02mm。
7、冲压设备的选定通过校核,选择开式双柱可倾压力机J23-25能满足使用要求。
其主要技术参数如下:公称压力:250KN滑块行程:65mm最大闭合高度:270mm最大装模高度:220mm工作台尺寸(前后×左右):370mm×560mm 垫板尺寸(厚度×孔径):50mm×200mm 模柄孔尺寸:φ40mm×60mm 最大倾斜角度:30°。